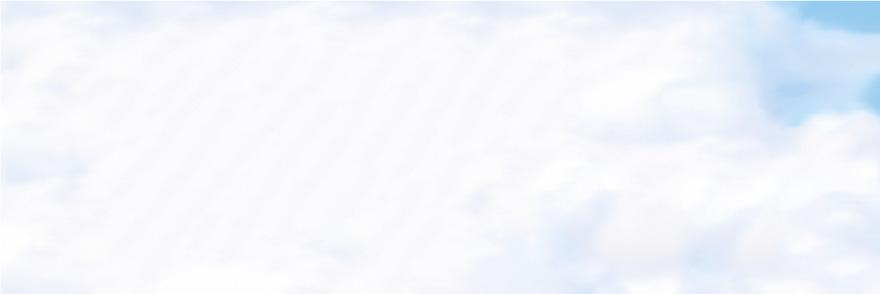
11 minute read
All aboard the blue train
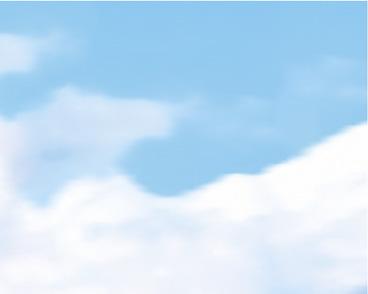
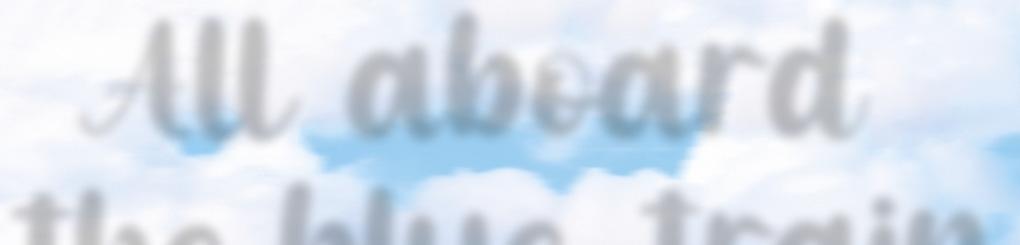
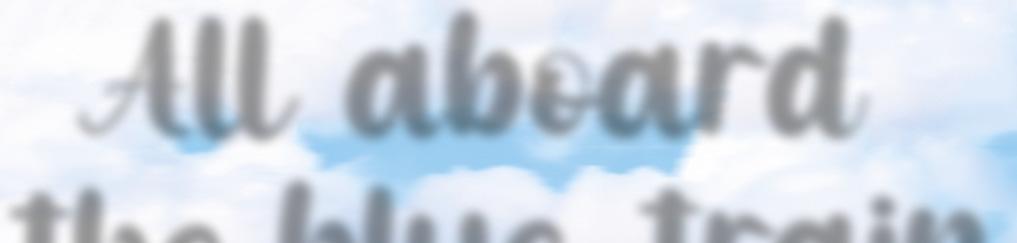

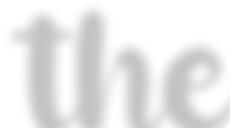

Nim Gnanendran Ph.D., NimblEng Energy Consultants, Australia, explains why mid scale LNG trains are an ideal size for the development of blue LNG concepts.
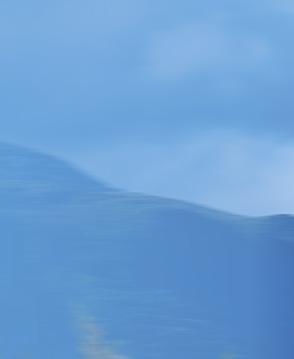
Natural gas – being a low-carbon fossil fuel – continues to play a key role in displacing coal in the power generation sector. However, falling solar and wind power generation costs and changing global attitudes towards fossil fuel-based energy systems has seen the natural advantage of gas waning ever so quickly. With global energy markets in transition towards low-carbon energy, there is a growing scrutiny of the carbon intensity of LNG produced from various sources and an appetite for sourcing lower carbon LNG. For the purpose of this article, blue LNG is defined as LNG produced with more than 90% of carbon associated with the production, liquefaction, and
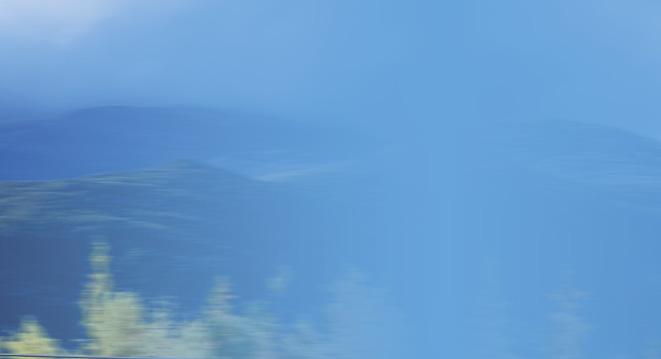
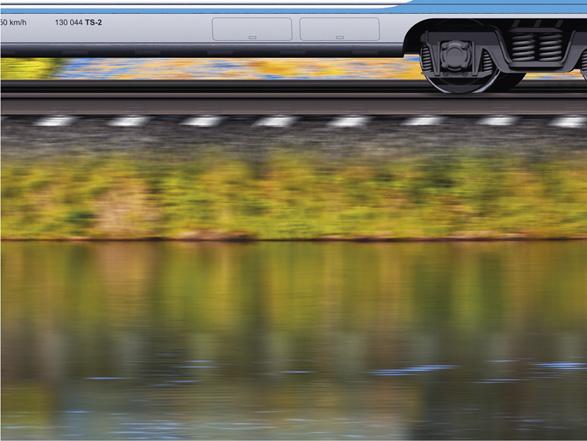
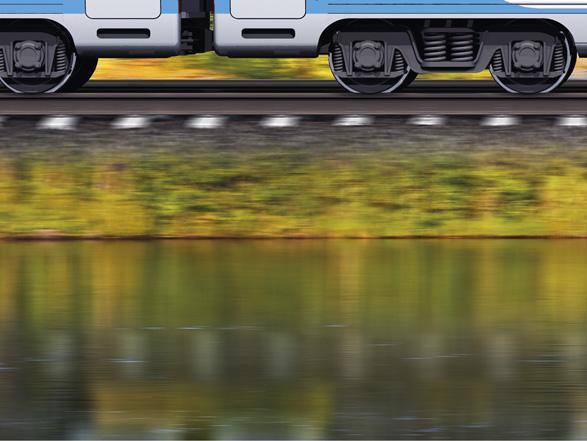
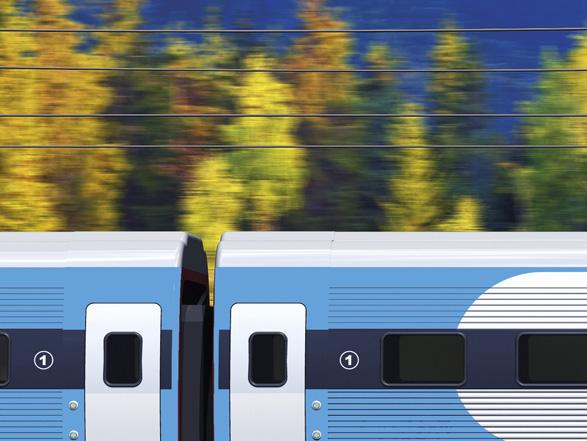
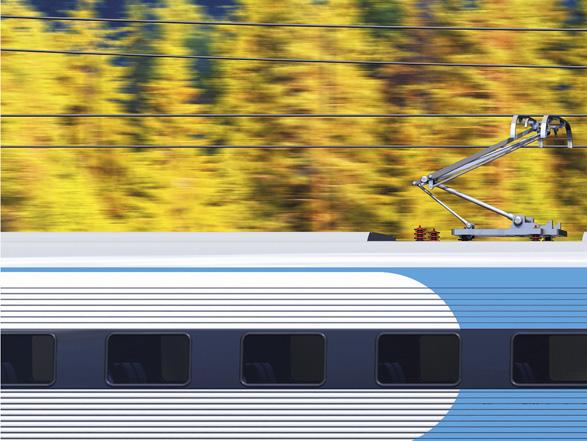
transportation being captured and stored. This is analogous to blue hydrogen, where hydrogen is produced from natural gas with carbon capture and storage (CCS). The greenhouse gas (GHG) emission intensities of LNG supply chains into central Europe are shown in Figure 1, where it can be seen that liquefaction contributes to 30 - 40% of GHG emissions. CCS in LNG projects is inevitable as they provide direct means of emissions reductions. At present, carbon-neutral LNG cargoes can be procured where the associated carbon emissions with the production and delivery of the cargo is offset through the purchase of carbon credits. This seems a short-term measure to suit a small volume of trade while the debate continues around the veracity of such carbon credit schemes. A more prudent alternative for the industry is to fast-track the implementation of CCS projects within its operations to produce low-carbon petroleum commodities, including LNG, where there is already a growing market. The knowhow within the oil and gas industry in CCS technologies such as separating CO2 from gases, compressing it to higher pressures, identifying suitable geological locations for CO2 storage, constructing CO2 wells, injecting pressurised CO2, and monitoring CO2 in storage needs to be capitalised to ensure CCS is widely adapted. This article provides technical and commercial reasoning for mid scale trains to be used for implementing CCS in LNG trains along with a conceptual design of a mid scale blue LNG train.
LNG projects in the capacity range of 1 - 2 million tpy were considered for monetising smaller stranded gas reserves with relatively short distance markets targeting integrated power projects in Southeast Asia in the early part of the 2000s. Several project developers using simple liquefaction technologies began to explore this niche market, when large scale LNG projects were serving the high volume, high value, lucrative North Asian markets. Mid scale LNG, by definition, is a niche market, where ideally the compelling features of large scale LNG, such as efficiency and lower dollar/tonne cost can be combined with the attractive features of small scale LNG, such as simplicity and lower capital costs. The arrival of the US shale gas boom and LNG projects based on take-or-pay tolling contracts saw the advantages of mid scale trainbased LNG projects where project developers used standardised modular mid scale trains as viable alternatives. These projects used mid scale trains to better support multiple, small volume, short-term and mediumterm LNG sales contracts, offering flexibility, lower capital costs, and better overall project economics. In the recent past, mid scale LNG trains have also shown to be ideal for floating LNG (FLNG) applications. Golar LNG and Petronasled projects showed that 1 - 2 million tpy mid scale FLNG is ideally suited for commercialising stranded gas fields, while the large scale, complex Shell Prelude FLNG project has continued to be plagued with technical issues and delays. The success of mid scale LNG trains in FLNG applications also provides a pathway for adapting CCS in offshore applications, where deep sea floor carbon storage options can be utilised when geological carbon storage is not viable. A mid scale LNG project in many cases will produce first LNG four to five years earlier than large scale LNG projects, considering the entire project development cycle.2 Mid scale LNG also provides an ideal size to develop innovative low-carbon solutions such as combined cycle LNG.3 A mid scale LNG project with 1.0 - 2.0 million tpy capacity could provide an ideal scale for developing blue LNG value chains based on the CCS of LNG liquefaction plants.
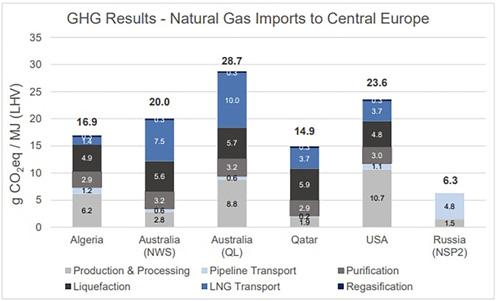
Figure 1. LNG supply chain carbon emissions.1
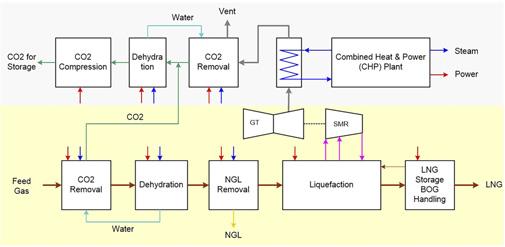
Figure 2. A mid scale blue LNG process schematic.
LNG and CCS
The petroleum industry of the future would be required to abate their Scope 1 and Scope 2 carbon emissions in a sustainable manner, other than look at offsets with tree planting schemes. While several measures are undertaken to reduce upstream methane emissions, it is prudent for industry to look at midstream and downstream emissions and act now rather than attract further scrutiny. LNG production is one of the most carbon intensive midstream processes within the industry, hence the adoption of CCS in LNG liquefaction facilities should remain a primary focus. The lessons from the coal industry failures in not investing in research in CCS technologies is proof, as the global energy transition threatens the immediate viability of that industry. The oil and gas industry needs to show visionary leadership in developing CCS projects now, beginning with reinjecting reservoir CO2 separated from feed gas in existing operations.
The new phase of the Qatar LNG expansion with approximately 37 million tpy LNG capacity will include sequestration of the CO2 separated from the feed gas, thus setting a new benchmark for new LNG projects. LNG projects such as Gorgon LNG and Snøhvit LNG with higher CO2 content in the feed gas have been reinjecting CO2 separated from the feed gas in geological storage formations for a number of years. These CCS projects have
faced several challenges including equipment failure due to corrosion and injection pressure management issues in CO2 wells, but have continued to provide vital learnings for the CCS industry. These learnings are critical for establishing CCS as a viable technology, not only for the oil and gas industry but for decarbonising the power sector and other energy intensive industries such as steel, cement, and chemical manufacturing. The CCS expertise gained by the oil and gas industry will also enable the establishment of CCS hubs, where industrial CO2 emissions can be collected, processed, and sequestered in depleted reservoirs which could also enable a new business stream for the industry in a low-carbon world. Further, the growth of the CCS industry will reduce the cost of blue hydrogen, i.e. hydrogen produced from natural gas using the steam-methane reforming (SMR) process with CCS, opening long-term markets for the gas industry in the hydrogen economy.
A mid scale blue LNG plant concept
Carbon emissions from an LNG plant are associated with two main sources: CO2 separated from feed gas. Post-combustion CO2 associated with gas/power turbines in the plant.
Smaller amounts of emissions are also associated with emergency flares and other fugitive emissions which are difficult to capture but can be managed by good engineering design and proactive operations and maintenance practices. Chemical solvents such as amines and physical solvents such as selexol have been used to remove CO2 from natural gas with up to 15 vol% to near zero levels as part of LNG production. The amine solution is contacted with the natural gas in an absorber column flowing in a counter-current manner to selectively absorb CO2 from the natural gas. The CO2 rich amine is then treated in a rectification column at higher temperatures to separate the CO2 and produce lean amine to be returned to the absorber column. The rectification column operates with a reflux drum, and the CO2 leaving the unit is water saturated and is at near atmospheric pressure. For postcombustion CO2 removal, several chemical and physical solvent-based plants with a similar configuration to natural gas CO2 removal plants are used. Typical flue gas from gas turbines contains 8 - 10 vol% CO2, 18 - 20 vol% H2O, 2 - 3 vol% O2, and 67 - 72 vol% N2. The CO2 content to be removed from the flue gas is typically five to seven times more than CO2 removed from feed gas in an LNG plant. Hence the energy requirements for a CO2 removal unit along with dehydration of the CO2 stream prior to compressing it to 70 - 100 bar to suit geological sequestration is significantly high. The CCS plant could add an overall energy efficiency penalty of a further 3 - 5% on top of the typical energy efficiency penalty of LNG plants of 10 - 12% operating with open cycle gas turbines.
An efficient plant design is essential to overcome the increase in energy requirements with an LNG + CCS plant. One such option is to utilise a deep waste heat recovery system, such as in a combined heat and power (CHP) plant, where high-pressure steam is generated from the gas turbine flue gas to produce sufficient heat to meet re-boiler loads in amine and dehydration units and to power a steam turbine generator to supply plant electrical power requirements, as shown in Figure 2. An auxiliar boiler, not shown in Figure 2, can be used in part of the CHP plant for start-up. A typical combined cycle power plant can improve the power plant efficiency to approximately 55 - 60% compared to an open cycle gas turbine plant that operates at 35 - 40% efficiency. Configuring the blue LNG plant around an efficient gas turbine such as GE LM2500+G4, Siemens SGT-750, or GE LM6000, with a rated capacity ranging from 35 - 45 MW, allows the gas turbine and CHP plant to be highly integrated in an LNG train with a capacity of 1 - 2 million tpy and a CCS plant. A two-in-one unit with two parallel gas turbines and liquefaction trains with common pre-treatment, a CHP plant, and a post-combustion CO2 removal unit can also be used to improve overall plant reliability and availability.
As an example, a 40 MW gas turbine operating at 40% efficiency and using a fuel gas with a low heating value of 50 MJ/kg has an annual CO2 emissions rate of 0.21 million tpy. A further 0.04 - 0.05 million tpy will be associated with the CO2 removed from a typical low CO2 content feed gas. This volume can be supported using a single CO2 injection well, and is a manageable volume for geological site selection and monitoring over a 25-year project life. As a comparison, the Gorgon LNG CO2 injection system is designed for 3.5 - 4.0 million tpy of CO2. The 40 MW turbine, when used to drive a single mixed refrigeration process with a refrigeration efficiency of 14 kW/tpd of LNG, can produce 1 million tpy of LNG. A waste recovery unit capable of recovering 17 - 18% of the energy from the turbine exhaust can power a CHP plant capable of supporting 13 - 14 MW of heat load and 2.5 - 3.5 MW electrical power, hence meeting all heat and power loads of the LNG train and the CCS plant. Similarly, other blue LNG plant concepts can be developed to utilise waste heat from gas turbines in the LNG train to supply heat and power for the CCS and LNG plants.
Key takeaways
The oil and gas sector needs to lead the development of CCS technologies and CCS applications to reduce its carbon emissions while also ensuring the longevity of the industry in a low-carbon world. The cost of CCS must reduce significantly, similar to solar, wind, and battery systems, for its wider adaption. Mid scale LNG trains with 1 - 2 million tpy have proven scale to develop novel LNG applications in the past and would be an ideal scale for efficiently adopting CCS in LNG applications with compact, modular trains based on deep waste heat recovery systems. In the longer-term, lowering the cost of CCS is essential for the viability of the gas industry during this era of energy transition and increases the competitiveness of blue hydrogen in the hydrogen economy. The investments in blue LNG supply chains today will pave the path to blue hydrogen supply chains in the future.
References
1. Nord Stream 2, thinkstep AG, ‘GHG Intensity of Natural Gas
Transport’ (March 2017). 2. Linde Engineering, ‘Mid-Scale is Scaling Out’ (June 2019). 3. GNANENDRAN, N., and BAGULEY, J., ‘Optimising mid scale
LNG’, LNG Industry (January 2020).