
8 minute read
Power To The People




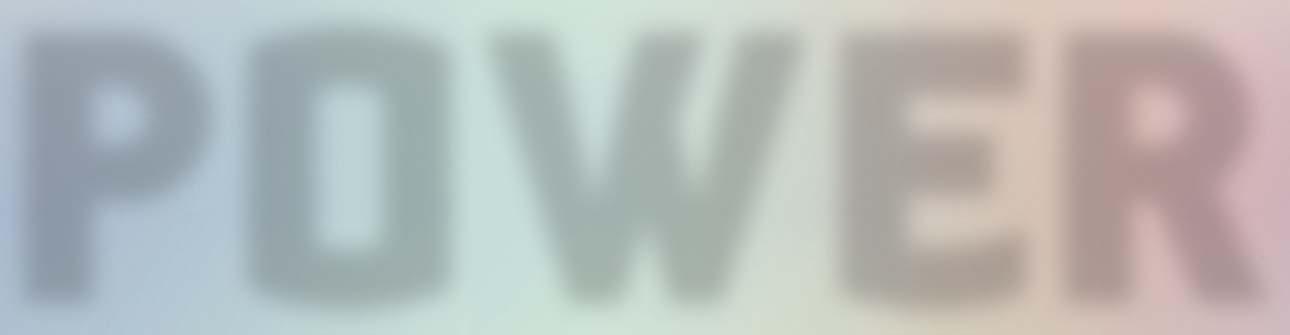

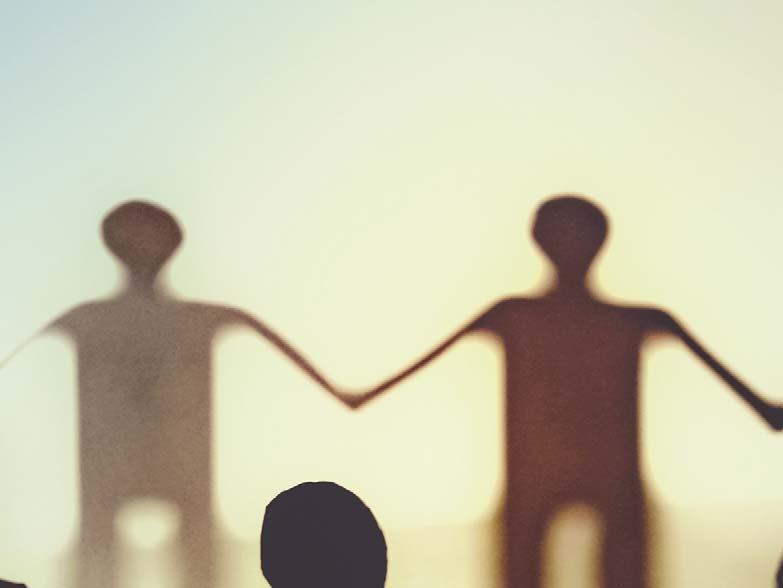
POWER
TO THE PEOPLE TOTHEPEOPLE
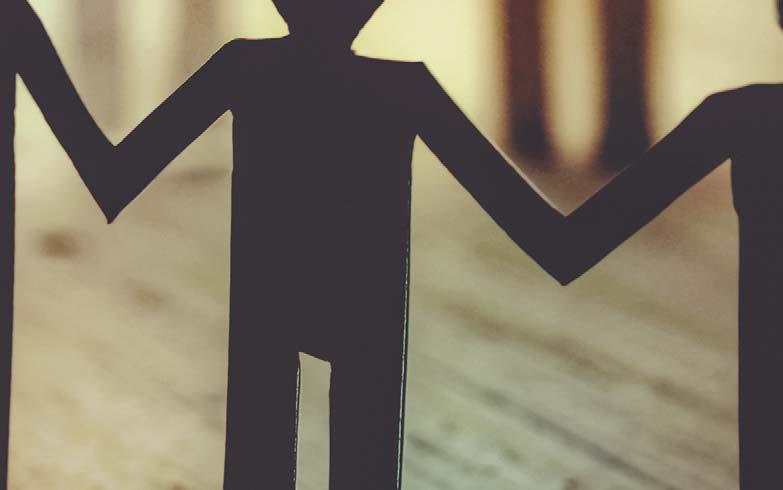
Diego De La Sotta, Parsable, considers how people-centric technologies, like connected worker solutions, could be the key to successful cement plant digitalisation.
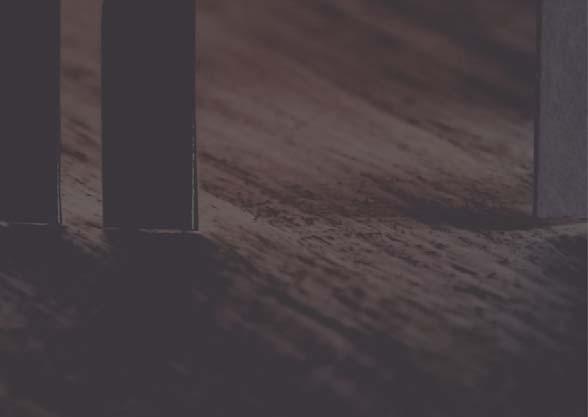
Even before the COVID-19 pandemic, digitalisation and modernising operations in the cement industry were key management priorities. The lessons quickly learned during this historic global disruption have made going ‘digital’ even more urgent. Specifi cally, there is now no doubt that technology is essential to agility and the ability to respond rapidly to any unexpected stress, which is clearly required for any company to stay competitive.


Digital transformation efforts often allude to more futuristic scenarios, like humanoid robots, wearable devices at scale, advanced machine learning, and artifi cial intelligence, but the urgency of providing digital access for the current human workforce cannot be overlooked.
Humans still perform 72% of tasks in factories1 , according to research by A.T. Kearney, a global consulting fi rm. Elon Musk famously remarked, “Humans are underrated,” when Tesla was initially unable to meet its Model 3 automobile production goals.2
People, not machines, are the driving force behind cement production. While automation is a critical component of a well-run cement plant, it works best when it enhances human capabilities. Machines bring predictability to production, but people bring critical thinking and decision-making every day.
How can the industry marry the best of what its people have to offer – particularly its frontline operators – with vision-driven Industry 4.0 initiatives? A pragmatic approach with tangible business and operational gains, along with a clear path to scale, are essential.
Digitalisation objectives in cement
It is no surprise that the cement industry is increasingly challenged with improving productivity, ensuring safety, and complying with changing stricter regulatory and environmental protection policies. Plant managers and executive teams alike are turning to digitalisation to achieve critical business and operational goals, including: Keeping plants running and producing at the expected levels and speeds. Demand will remain very unpredictable, at least through 2021. In the United States, the
PCA (Portland Cement Association) Market
Intelligence now expects cement consumption to grow by nearly 1% in 20213,primarily fuelled by residential construction; this is a revision to a previous forecast last autumn of a modest decrease in consumption in 2021. How can operational and supply chain leaders leverage
digital technologies to be able to change production and output at a moment’s notice to leverage these opportunities? Ensuring safety and ESG compliance (environmental, social, and corporate governance compliance). The risk of non-compliance is vast, and not just on the fi nancial front. Stricter safety protocols on the plant fl oor, particularly as a result of COVID-19, mean that up-to-date, accurate instructions for adherence – and the automatic recording of such adherence – are critically important to help prevent outbreaks and other safety and employee welfare issues that can quickly snowball out of control. Meeting sustainability goals and reducing waste.
Cement is the second most-used material in the world. More than ever, cement manufacturers are under intense scrutiny over their sustainability efforts, and sustainability is now being seen as a C-suite objective that is increasingly of equal stature to revenue and profi t. How can digital technology accelerate the needle forward in reducing waste and energy consumption, including material waste caused by ineffi cient, sub-optimal production processes on the frontlines?
The critical role of connected worker technologies
A recent survey of more than 1000 frontline manufacturing workers commissioned by Parsable, a connected worker platform, found that 79% of workers still primarily relied on paper to track work4 , resulting in lost visibility and lost opportunities to improve productivity, quality, and safety at scale. Connected worker technologies help frontline employees better execute work through a digital approach and mobile devices. They connect workers to the people, information, systems, and machines to help them do their jobs more safely and more effectively. Instead of large binders full of SOPs (standard operating procedures) on paper, connected worker platforms digitise these SOPs so that workers have immediate, easy access to them as they execute their day-to-day tasks. Digitised SOPs offer step-by-step real-time, interactive, and multimedia instructions on how to perform the work accurately. Connected work provides a prescriptive, data-driven feedback loop that drives On the back-end, continuous improvement across operations. these platforms create

a digital, accessible record of the work performed for compliance and accountability purposes. Subject matter experts can make changes to SOPs at any time so that the most up-to-date procedures and steps are integrated into the work itself. This is critically important as policies and regulations are revised; those updates can be immediately pushed out to – and executed – by the team, the plant, and across many sites in different regions or even continents.
The data gathered by these technologies can be measured and analysed to provide new visibility into specifi c standardised processes and to identify opportunities for improvement. In the cement industry, a few examples of these processes span across: Safety (e.g., unsafe acts/near misses, workplace inspections, hot/not hot work permits). Environment (e.g., method 22/9, SPCC, solid waste inspections, discharge monitoring). Maintenance (e.g., autonomous maintenance, tags, rounds, lube routes). Production (e.g., routine inspections for dust collectors, raw mill separators, preheat tower, crusher dryer, cooler fl oor, etc.). Logistics (e.g., inbound and outbound truck checks).
Having this level of data, measurement and insight can help managers better iterate and improve workfl ows and keep production moving at the pace it needs to, and with the required quality, to meet quota and customer expectations.
Next steps: A practical guide to digitalisation
Improving environmental compliance: Digital inspections with connected worker technology
The cement division of a global building materials company recently deployed a connected worker platform to increase effi ciency, specifi cally, to help eliminate environmental compliance deviations resulting from missing or lost paper-based inspection records. The company wanted a solution with: An easy-to-use interface that its frontline operators could quickly learn and adopt and a highly fl exible approach to creating digital inspection checklists. Real-time notifi cations when errors occurred, so corrective action could be performed quickly, and an easy way to export data to analyse and identify operational trends.
Operators estimated that the shift to digital inspections on the connected worker platform improved overall effi ciency by at least 30 minutes per inspection by reducing NPT (non-productive time). In addition to increased worker effi ciency, this digitalisation programme enhanced regulatory compliance, overall document control, and change management.
Digitalisation does not need to be a complicated process requiring big teams and big budgets. It is important to have a plan that focuses on minor, incremental improvements on the frontlines and showcasing wins backed by data, as the above case study illustrates. The following illustrates fi ve steps to get there: Find advocates. Success is more likely to happen with buy-in from stakeholders within a plant or organisation who share the same vision for digitalisation and belief that technology for frontline operators will improve productivity, quality and safety at scale. Start smart. Think about which processes could be the easiest and quickest to digitise. Perhaps it is a LOTO (lock out/tag out) procedure or a routine maintenance round. Also, it is important to think about scalability: are there simple processes that are similarly carried out in multiple plants or sites? Set baseline metrics. Setting baselines helps measure the impact of digital- versus Turning paper-based work instructions into mobile-based, dynamic workfl ows is paper-based a foundational component of digitalisation and Industry 4.0 efforts. processes.

Metrics could be as simple as time spent on a specifi c procedure, or number of calls/notifi cations for assistance. Regularly evaluate performance. Gather feedback from frontline operators. The more visibility and data that can be analysed, the easier and more accurate it will be to fi nd the ineffi ciencies or bottlenecks, enabling the process to be improved continuously. Have a plan to scale. It is critical to measure and highlight the value of mobile-based software and digital tools for frontline workers early on, but also to have a plan to roll out a programme to additional sites and use cases.
Reach out to peers at other plants or factories, and share any success and learnings.
Conclusion
With human workers being an essential part of the cement industry, digitalisation efforts must support and empower them. People-centric technologies, like connected worker solutions, provide ‘quick win’ progress towards achieving the productivity, safety, compliance and sustainability goals pursued by every cement manufacturer. Companies that act now will have the agility and resiliency required to stay in an ever-increasing competitive world.
About the author
Diego De La Sotta is a Director at Parsable, a globally deployed enterprise platform for industrial companies that helps empower frontline workers with digital tools to improve productivity, quality and safety.
References
1. ‘The state of human factory analytics’ – https://www.kearney.com/digital-transformation/ the-state-of-human-factory-analytics – Accessed on 14 April 2021. 2. ‘Elon Musk admits humans are sometimes superior to robots, in a tweet about Tesla delays’ – https://www. cnbc.com/2018/04/13/elon-musk-admits-humans-aresometimes-superior-to-robots.html – Accessed on 14 April 2021. 3. ‘PCA Updates Forecast Risks to Upside’ – https:// www.cement.org/newsroom/2021/03/03/pcaupdates-forecast-risks-to-upside – Accessed on 14 April 2021. 4. ‘New Research: The State of Digital Transformation and Connected Work on the Manufacturing Frontlines’ – https://parsable.com/blog/new-researchthe-state-of-digital-transformation-and-connected-workon-the-manufacturing-frontlines – Accessed on 14 April 2021.
Global coverage of the cement industry
• International cement news • Regional reports • Market analysis • Event previews and reviews • In-depth technical articles • In-depth regional analysis by key players in the industry • Comprehensive technical reviews on all aspects of cement production, from the quarry face to despatch
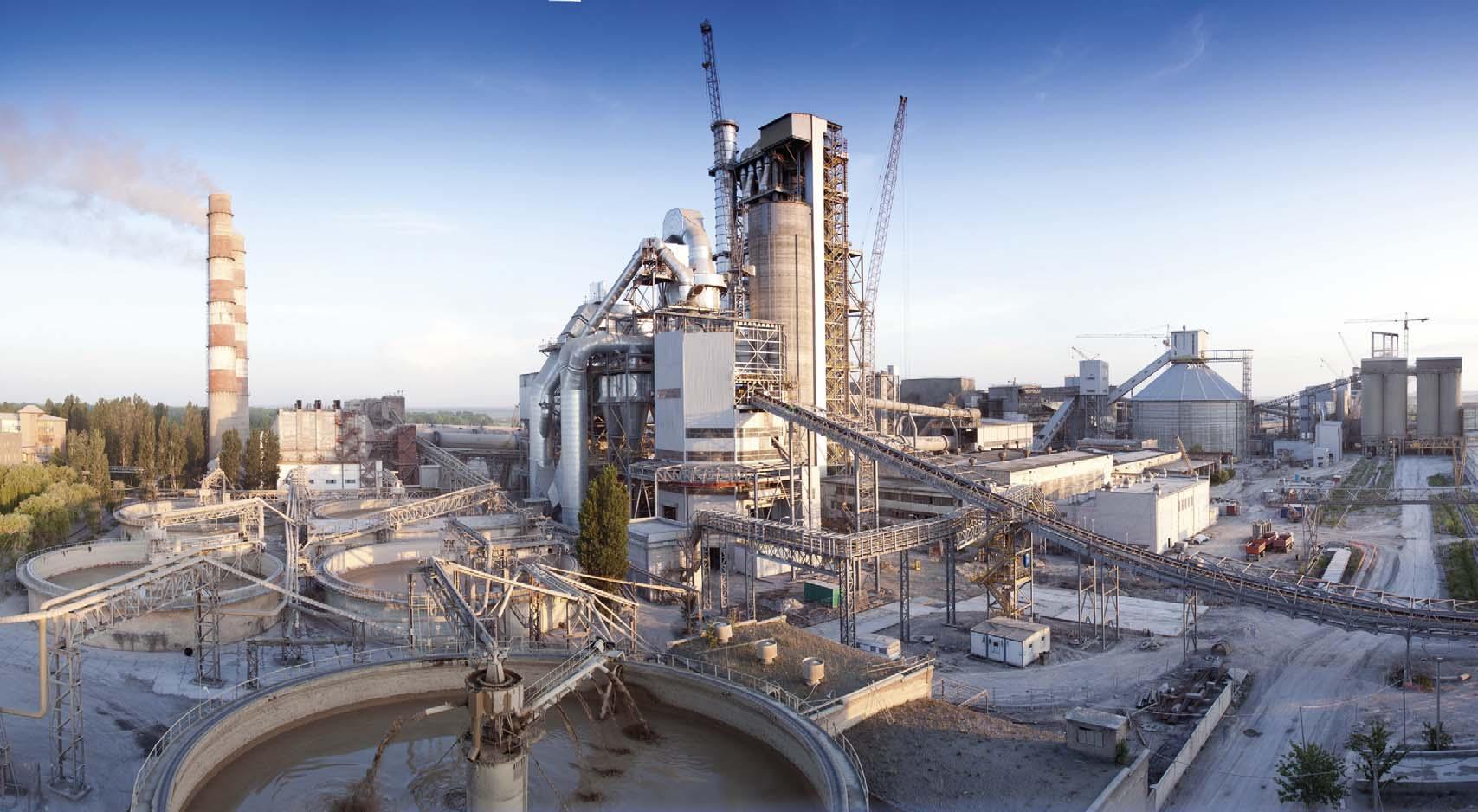