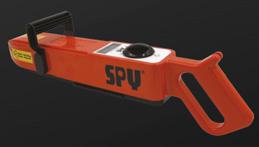
11 minute read
AIM: the next generation
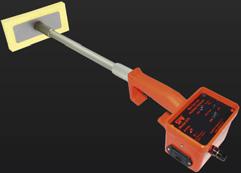
They will alert the operator of the need for further ‘quantitative’ inspection being required in that location to obtain accurate wall thickness measurements for further analysis. The focus of screening is therefore often on providing assurance that the inspection identifies the most severe degradation, or at least regions representative thereof.
The inspection planning process for unpiggable pipelines has the aim of identifying the most effective approach for each situation and ensuring the inspection meets the integrity requirements.
The bespoke Sonomatic MAG-ST crawler (Figure 3) has been utilised on recent campaigns to deploy screening techniques such as EMAT/Multiskip, on multiple pipelines at <1000 m water depth. These lines were not designed for inline inspection and had been in service for many years, therefore an assessment of their condition was necessary. The inspection to assess their condition had to be performed using external direct assessment methods.
Differing diameters and external coating types can result in the inspection being challenging and may require the need for both screening techniques depending on the pipeline specifics. Typically, in one 24 hr offshore period, approximately 320 m of pipeline can be screened with these techniques, resulting in a total of approximately 10 km of pipeline inspection on a two to three week offshore inspection campaign.
Support technologies are required for follow up inspections at areas of degradation of concern as identified by the screening inspection. These follow up techniques have the ability to quantify the depth and characteristics of the degradation in detail, supporting the CRA process and allowing fitness for service assessment to be performed. Ultrasonic corrosion maps, or C-scans (Figure 1) can be exported in .csv file format directly to a finite element model for stress distribution analysis. Sonomatic utilises the ROV-iT scanner (Figure 4) for such inspections where quantitative results are required from a specific location. The ROV-iT has been utilised extensively since 2012 for subsea inspection of un-piggable pipelines down to water depths of 1750 m to date (pressure tested to 3000 m). The scanners have the capacity to inspect pipelines with outer diameters from 6 in. up to 30 in. The two smaller units are deployed over the side of the ROVSV or through the moonpool, attached to the front of most modern work class ROVs. However, the larger ROV-iT 30 must be deployed subsea in a work basket, and the ROV will ‘hot stab’ into the scanner for power and comms operations. Inspectanycoated metal surface For over 65 years SPY® has been an industry leader in coating inspection equipment. We offer a full line of portable and in-plant holiday detectors for pipes, tanks, or any coated metal surface in the field or in a manufacturing facility. wetsponge wet sponge in-plantholiday holiday detectors detector systems • Lightweight and ergonomic • Extremely versatile for design automatic or manual inspection • Accurate, reliable and easy • No batteries required, to use operates on 120 VAC • Audible and visual alerts • Multiple accessories • Available in basic kit or available to meet any plant full inspection kit line configuration portable holiday detectors • Easy to use, no trigger to hold while inspecting • Tough, ergonomic and reliable • Infinite voltage settings • 3 different voltage ranges available
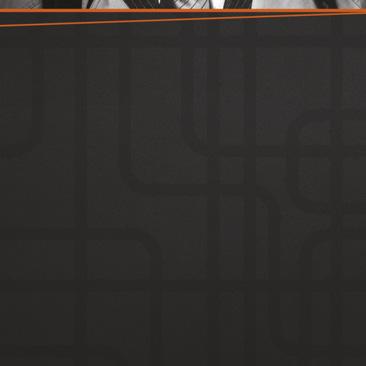

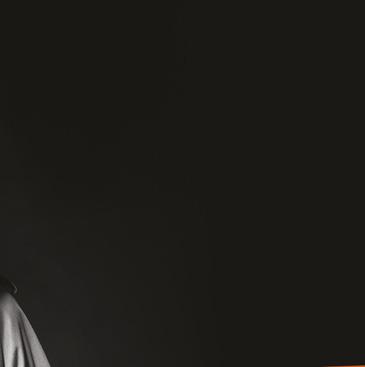

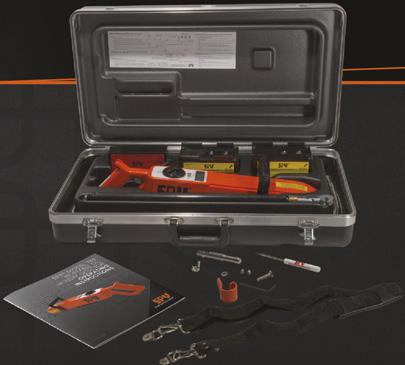
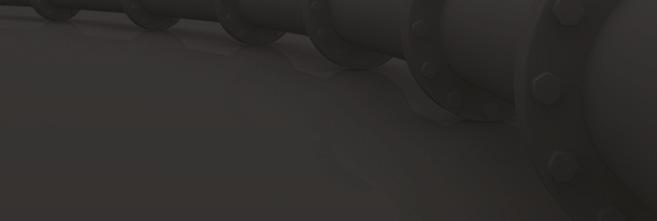
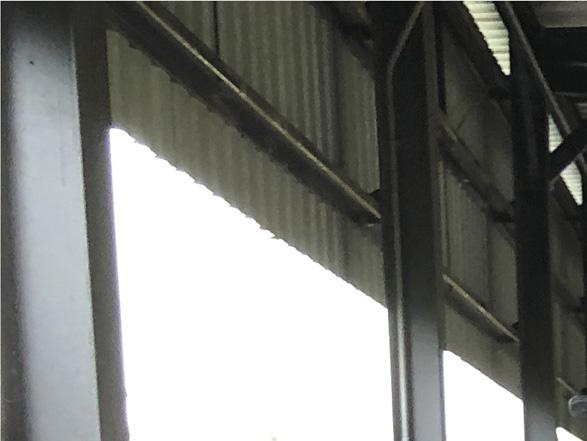
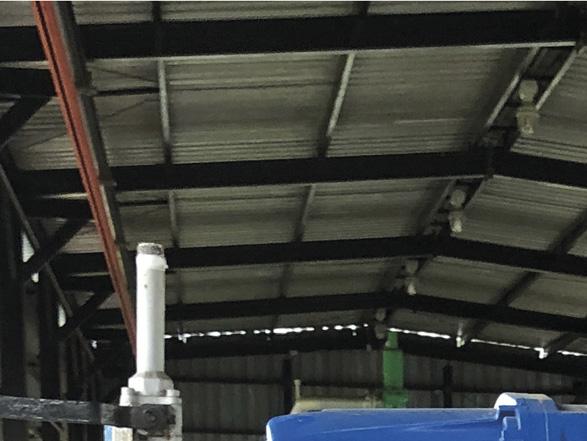
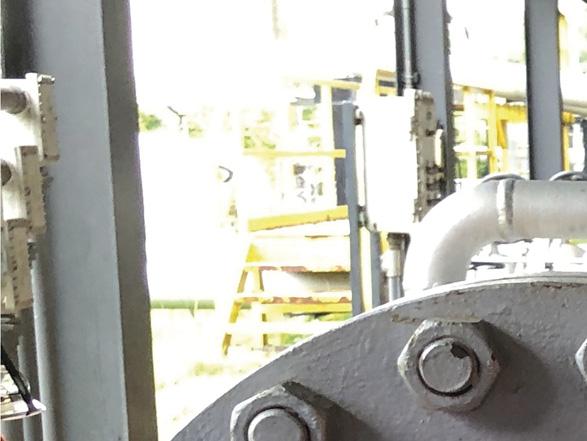
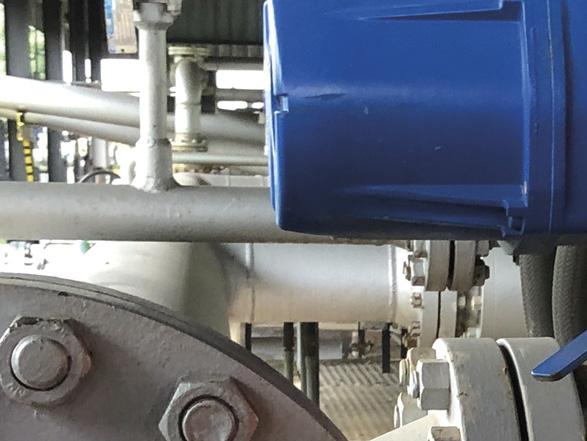

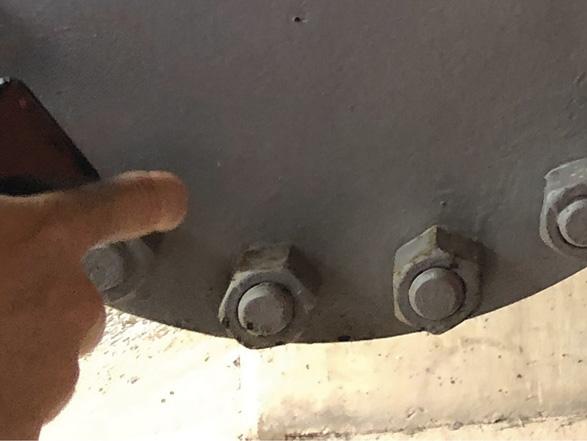
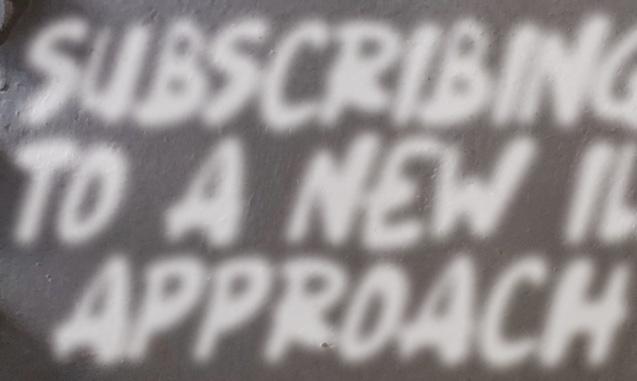
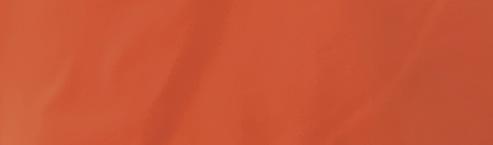
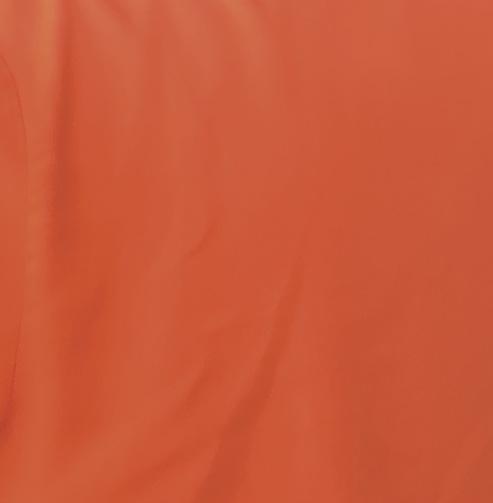
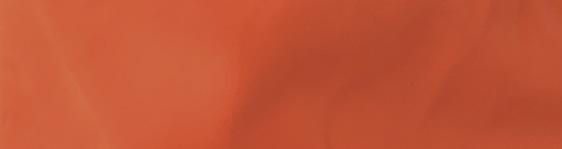
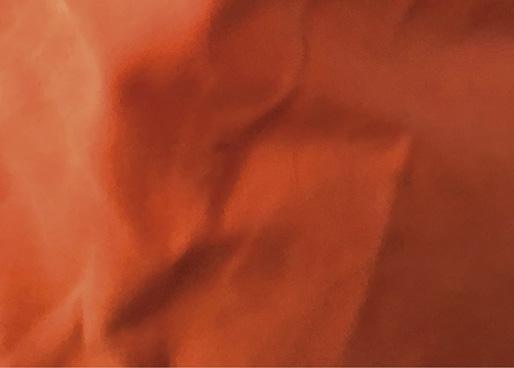
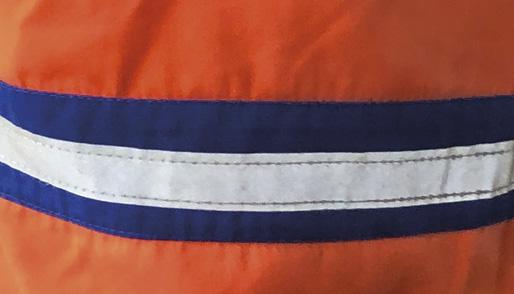
The subject of data seems to dominate every business discussion today. Yet, too often, there are few pointed questions about the ultimate value of the information being presented and, most critically, how accumulating data can best be applied in support of operational planning, asset management, and sound business decision-making.
From day one at INGU, we have challenged ourselves on the fundamentals of business value – even before we understood the full importance of our work as physicists, data scientists, and machine learning experts. We dedicated ourselves to improving pipeline performance and safety, and in doing so, we have come to a deep understanding of the business needs of those tasked with managing these critical energy assets.
Four qualities that give data its business value There are four critically important qualities that give data its business value: quality, reliability, timeliness, and affordability. If data has these qualities, those using it will not only be able to know things they didn’t know before, but they will be empowered to effectively manage their business operations, making decisions that will deliver a measurable return on investment.
John van Pol, CEO, INGU, Canada, presents inline inspection as a service: an operating systems approach to pipeline integrity.


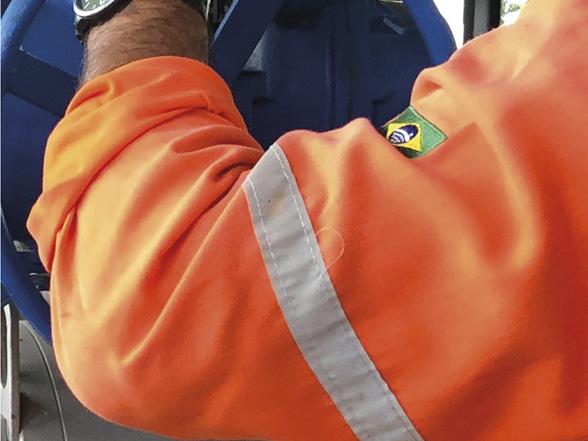
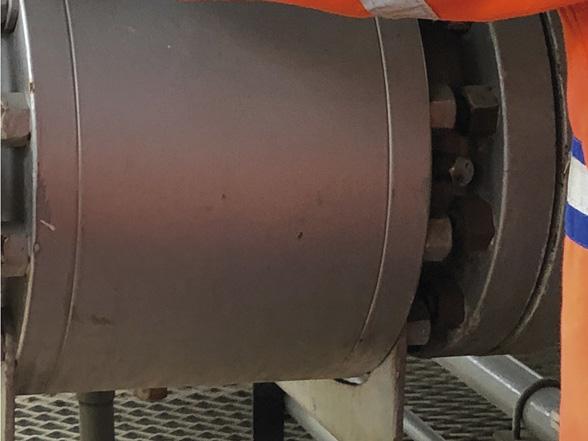
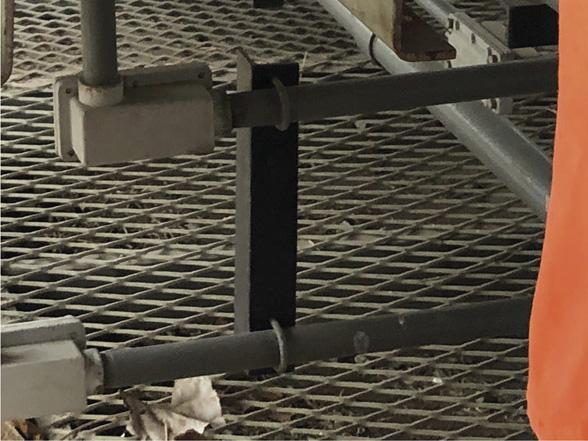
Pipeline operators have relied on smart pigs since they were introduced in 1964 to stay on top of pipeline condition and performance. As these solutions have evolved over the decades, the accuracy of their data has been second to none. Unfortunately, deploying this technology is infrequent, operationally disruptive, costly, and only applicable to about 60% of the world’s pipeline assets. This means smart pigs serve as an effective point solution but provide limited value as a business decision-making tool. The industry’s stop-start approach to inline inspection has left operators vulnerable and forced to act based on moments in time or calendar dates, rather than on insights gained through timely and complete access to their pipeline assets.
The operating system for pipeline integrity Our work at INGU revolves around the use of free-floating Pipers® and advanced data analytics to deliver optimal operational control and insight, while simultaneously reducing overall costs and downtime. In short, we are the operating system for pipeline integrity and management. As the first in our industry to offer inline inspection as a service, on a subscription basis, we provide complete, timely, accurate and affordable data. In business terms it means operators have greater visibility across all pipeline assets, whenever and wherever they want, regardless of location, material, configuration, or condition at a 10x cost advantage. The result is better planning, decision-making and overall financial control.
We can achieve this because of a unique, self-serve solution that uses free-floating, micro sensor technology designed to work under operational conditions. This approach translates into 100% uptime and the ability to act where and when it’s required. There are no third parties required on-site – including INGU – and operators can deploy our solution on a moment’s notice.
Pipers data is highly repeatable making it ideal for monitoring for changes in pipeline condition, keeping operators on top of leaks, deposits, wall condition, and damage or tampering to their pipelines.
When it comes to troubleshooting, Pipers are always in scope and readily at hand. Equipped with a magnetometer, accelerometer, gyroscope, acoustic sensor, and pressure sensor on board, they can deliver leak, deposit, and wall condition insights in a single run. Even when timing is tight, the INGU team can turn around client data as fast as 24 hours.
INGU’s data science team has the unique advantage of access to a growing library containing learnings from small, mid- and large scale operators across four continents. This provides rich contextual analysis and the ability to continuously improve our work.
A recent case in point Success is always measured by how challenges that come within the last mile are handled. For our client, a private refinery and a pioneer in the efficient production of fuels, the last mile means
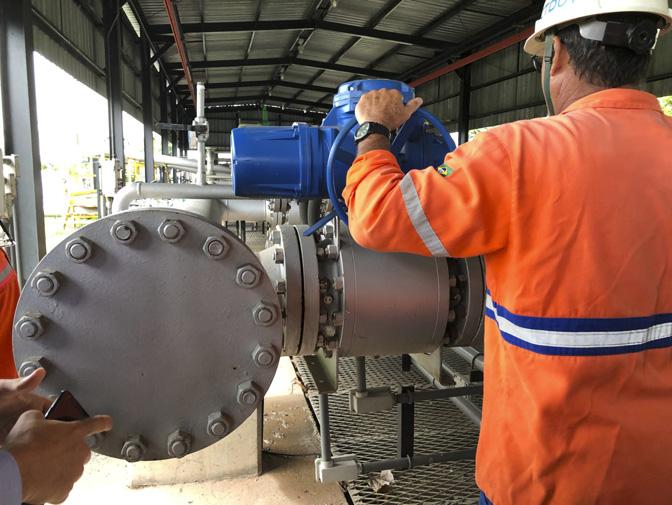
Figure 1. Onsite launch location.
Figure 2. Pipers with microsensors onboard.

successfully transferring oil resources from arriving tankers to its modern port facility. There, resources are processed efficiently with attention paid to every detail.
In October 2020, the refinery ran Pipers as part of its risk management efforts to assess the condition of a primary pipeline used to transfer products from ship to port. This initial assessment established a baseline for continued monitoring of this critical asset. In late April 2021, a leak was suspected and Pipers, already in stock with our local agent, were immediately deployed to find the leak location. A tanker was on its way and any necessary repairs to the pipeline would need to be done within days.
The Pipers data was uploaded after deployment to INGU for analysis, and within 24 hours the location of the leak was identified. The area was excavated and the hole in the pipeline was discovered within 1 m of the location isolated by the INGU team. Repairs were made that morning and the company was safely back in operation in just two days from actioning the problem.
Pipers technology is exceptional at leak detection because these free-floating micro sensor devices travel with the liquid through pipelines with limited to no background noise, making them extremely sensitive to the sounds associated with leaks.
The refinery subscribes to Pipers as a service, ensuring they have condition baselines for all assets which allows for fine grain financial and operational planning, as well as the ability to confidently troubleshoot any issues that may arise.
Data that works It is estimated that conventional inline inspection methods are not suitable for 40% of the world’s pipeline assets. Our goal is to open the doors to all pipelines – independent of diameter, fluid, and pipeline material.
Many pipeline assets have a poorly documented or lost history. They may also be in unknown condition and difficult to inspect. These pipelines present a significant risk from an integrity perspective.
The advantage of repeatability allows Pipers to establish a baseline through an initial run. Our clients have the ability to use each subsequent run to gain a clear, comparative picture of the state of their pipeline assets and monitor changes over time. This also gives our team the ability to observe trends and perform quantitative assessments using different sensor data sets.
Maintaining a regular inline presence across all assets allows users to plan, decide, and act with certainty. As seen with the refinery case study above, INGU was able to provide the location of the leak identified within 48 hours. The accuracy of the data allowed excavators to discover the hole in the pipeline within one meter of the location via Pipers data.
Pipers are putting power and control into the hands of pipeline operators and ensuring integrity management programs are running as efficiently as possible, with data that is complete, timely, reliable and affordable.
A look ‘under the hood’ What we have developed is not a better inline inspection data tool. Rather, it is a powerful business decision-making and planning solution, offering benefits that this industry has not seen. Self-serve system ) Provides maximum control, while eliminating the need for third parties onsite.
Universal pipeline access ) Easy access to pipeline assets no matter the material, diameter, or configuration.
Multi sensor capabilities ) Investigate leaks, deposits, and changes in wall condition in a single run.
100% uptime ) Designed for use under operational conditions.
Cost advantage ) Affordability and ease of use means more visibility, more often.
Rich datasets ) Leverage historical data for unprecedented analysis.
Pipers® 2.8 ) For the largest diameter pipelines (up to 48 inches) and specialized conditions such as offshore.
) Pressures up to 20 000 kPa/2900 psi.
) Temperature range -20˚C to 60˚C/-4 to 140˚F.
) Runtime up to 24 hours.1
Pipers® 2.2 ) The standard for piggable and unpiggable lines.
) Pressures up to 10 000 kPa /1450 psi.1
) Temperature range -20˚C to 60˚C/-4 to 140˚F.
) Runtime up to 24 hours.2
Pipers® 1.5 ) For unpiggable small diameter pipelines down to 2 in.
) Pressures up to 3000 kPa/435 psi.1
) Temperature range -20˚C to 60˚C/-4 to 140˚F.
) Runtime up to 2 hours.2
Notes
1. Maximum pressure rating is at 20˚C. 2. Given runtime is for storage and operation at 20˚C.