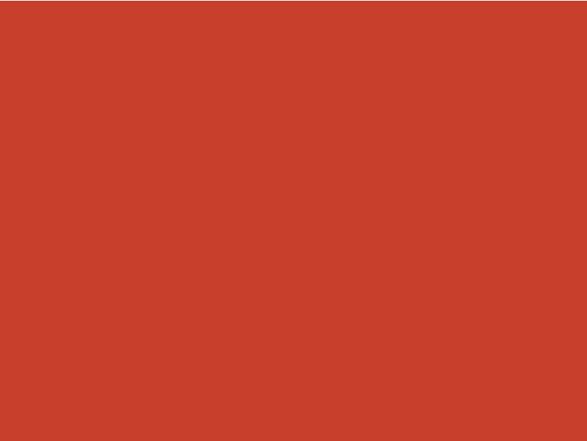
10 minute read
The hitchhiker's guide to MAOP
Tad Nowicki, Christopher DeLeon, and Rhett Dotson, ROSEN USA, explain how new US regulations have changed requirements for assessing the maximum allowable operating pressure of pipelines.
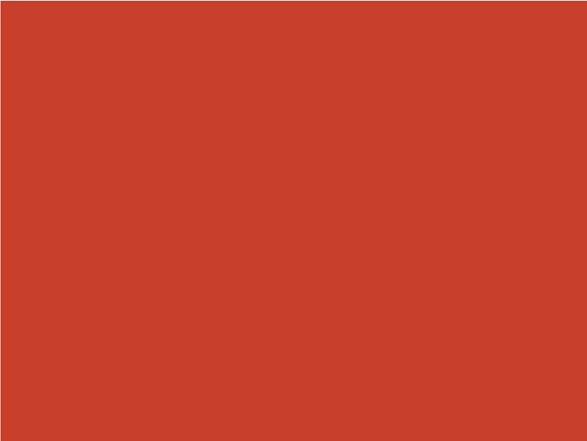
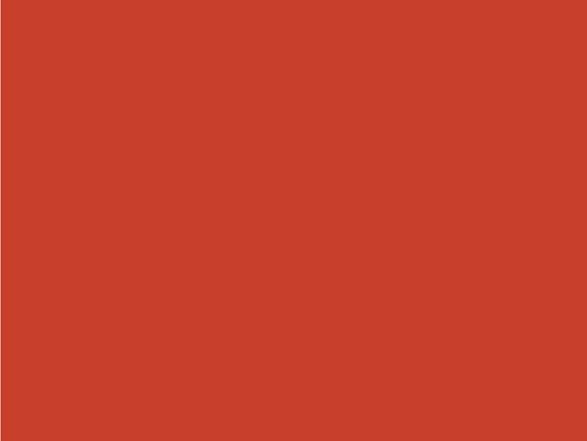



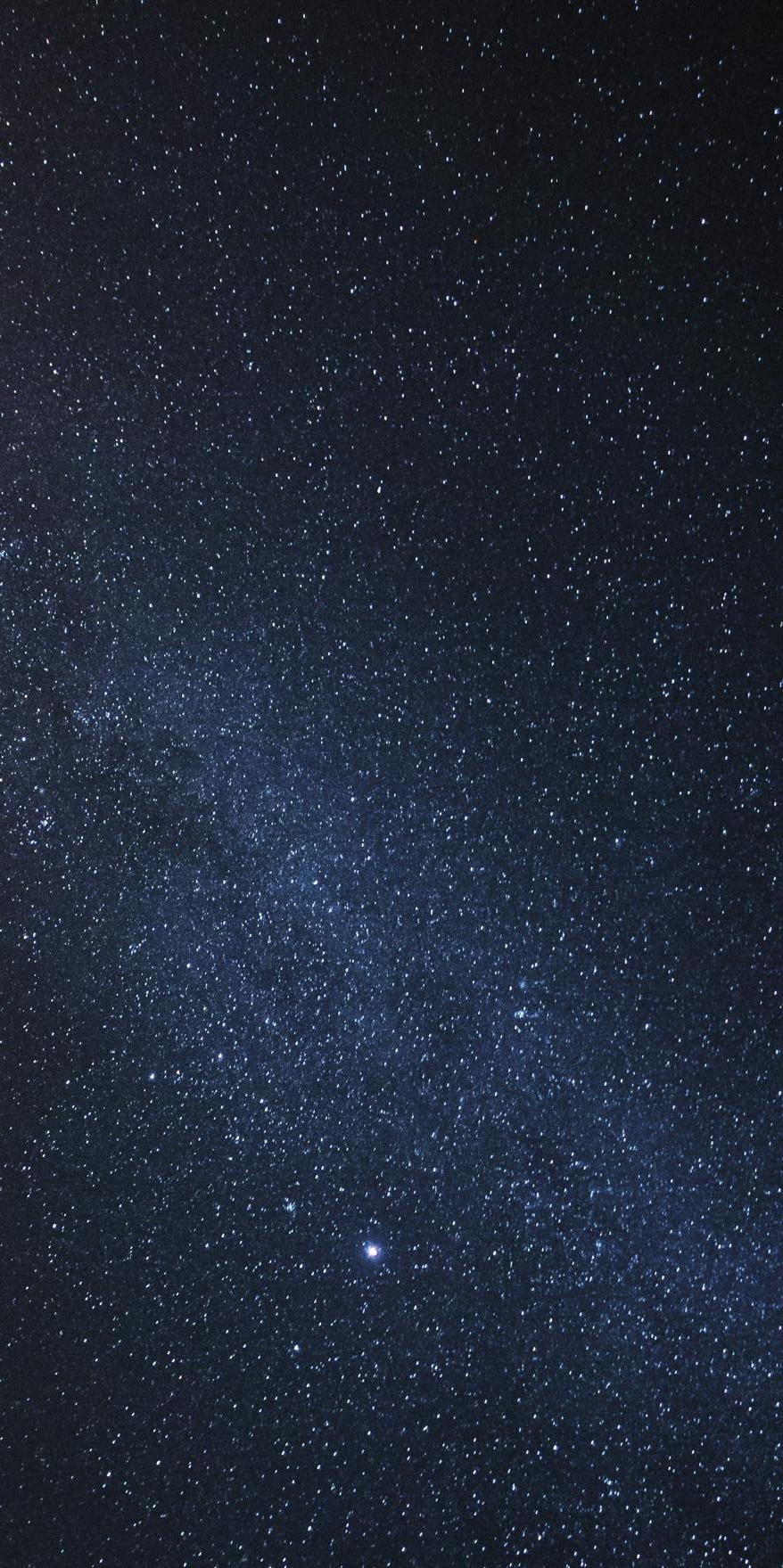
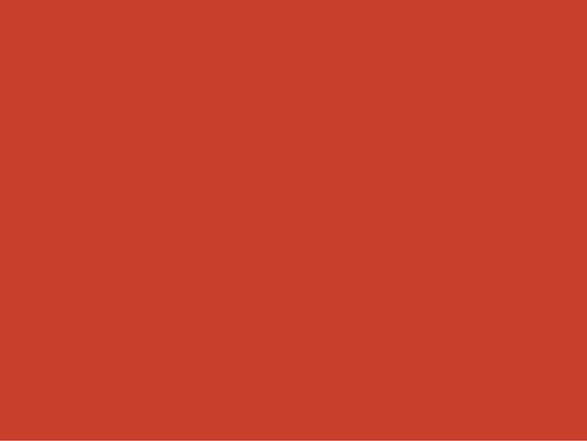
This article is focused on a non-technical review of the new onshore gas pipeline regulations in the US, specifically how the maximum allowable operating pressure (MAOP) of applicable transmission pipelines is required to be reconfirmed.
On 1 October 2019, the US Department of Transportation’s (DOT) Pipeline and Hazardous Material Safety Administration (PHMSA) issued the first of three final rules to improve the safety of onshore gas pipelines. This rule focused specifically on gas transmission pipelines by addressing US congressional mandates in the Pipeline Safety, Regulatory Certainty, and Job Creation Act of 2011 (2011 Pipeline Safety Act) as well as recommendations made by the National Transportation Safety Board (NTSB) as a result of its investigation of the 2010 pipeline incident in San Bruno, California.1
In anticipation of this final rule, in 2011 PHMSA published an Advanced Notice of Proposed Rule Making (ANPRM), which identified 16 major areas of regulatory reform.2 This first of three final rules, also called “RIN 1 of the New Gas Rules”, addresses several of these major topics focused on improving the safety of pipelines that operate with incomplete or inaccurate pipeline records. This rule requires onshore gas transmission pipeline operators to reconfirm the MAOP of segments that operate with previously untested pipe, commonly referred to as “grandfathered pipelines.” These pipelines typically do not have a traceable, verifiable, and complete (TVC) pressure test or adequate material property records indicating the pipeline’s diameter, wall thickness, specified minimum yield strength (SMYS) and construction method.
Several other newly implemented requirements demand that pipeline operators create and implement written procedures for achieving MAOP reconfirmation in accordance with Section §192.624 of PHMSA’s Part 49 of the Code of Federal Regulation (CFR). Pipeline operators will also be required to determine, gather and report all pipeline mileage requiring

MAOP reconfirmation to PHMSA as part of the 2021 annual report due 15 March 2022. The annual report also includes additional reporting requirements associated with other changes in the new gas pipeline regulations.1
Maximum allowable operating pressure The MAOP of a pipeline is limited by 49 CFR §192.619, which consist of three primary elements: construction records, physical and mechanical strength testing, and an understanding of the pipeline’s assigned Class Location. PHMSA defines the Class Location process in §192.5, with resulting values ranging from 1 to 4. A Class 1 segment represents the lowest density of buildings intended for human occupancy near the pipeline, with Class 2, 3 and 4 each progressively increasing population density.
A pipeline’s Class Location directly correlates to the maximum operating stress the pipeline may be subject to. It is reduced, as a percent of the specified minimum yield strength (SMYS), as the Class increases from 1, up to 4. This reduction creates an incremental safety factor that limits the pipeline’s maximum operating pressure. For example, a Class 1 pipeline can operate at a maximum of 72% SMYS, whereas a Class 4 Pipeline can only operate at 40% SMYS.
Mechanical strength testing is performed through hydrostatic pressure testing in accordance with Subpart J. A pressure test is required to validate that the pipeline is capable of holding the pressure required to substantiate the desired MAOP. Different test multipliers are used; they increase in severity as the Class Location increases. Until recently, Class 1 pipelines only had to test to 1.1 times the desired MAOP to be considered valid. Now, pressure testing in a Class 1 location requires a pressure of 1.25 times MAOP to establish the desired MAOP. These records are to be traceable to the specific pipeline, verifiable with a complementary record and complete with the signature of an appropriate person. PHMSA provides more information on TVC records in the Preamble of RIN 1.1
If the mechanical strength test record is not TVC or not conducted via hydrostatic testing in accordance with Subpart J of Part 192 of the CFR, the pipeline must have its MAOP reconfirmed in accordance with §192.624. This section of code was added as part of the new gas pipeline regulation within Part 192 of the CFR. Construction records are used to establish the MAOP by evaluating the physical pipeline characteristics and their pressure limitations. These characteristics are used in the steel pipe design formula listed in §192.105 (a); this requires data inputs for the pipeline’s SMYS, wall thickness (WT) and outer diameter (OD) along with safety factors associated with construction seam type, operating temperature and Class Location.
It is important to recognise that the established MAOP has levels of conservatism: maximum operating stress as a percentage of SMYS based on the Class Location and the safety factors explicit in the design formula for steel pipe in §192.105. Effectively, when the construction records that indicate the material properties and attributes are not TVC, pipe for which documentation is inadequate to support the MAOP in accordance with §192.619 (a) and §192.517 (a), pipeline material properties and attributes must be verified in accordance with §192.607.
MAOP reconfirmation The new MAOP reconfirmation requirements are mostly targeted at pipelines with an MAOP established through §192.619 (c). These pipelines are called “grandfathered” because they were constructed and put into operation prior to the pressure testing requirements that are imposed on modern pipelines. Because post-construction pressure testing was not a code requirement when these pipelines were built, reestablishing their MAOP based on the maximum operating pressure they experienced in the five years prior to an applicable date listed in PHMSA regulations was allowed.
When these pipelines require MAOP reconfirmation, an operator can choose from one of six newly listed methods. One of these methods, Method 3: engineering critical assessment (ECA), is described in Section §192.632. While the term “ECA” is a well-known and understood engineering assessment, PHMSA describes the expectations and requirements of an ECA in §192.632. PHMSA included the use of an ECA to reconfirm the MAOP as one of the methods available to operators because it directly addresses the congressional mandate for PHMSA to consider other safetytesting methodologies – including inline inspection (ILI) – that are determined to be of equal or greater effectiveness than a Subpart J pressure test.1
Increasing the utilisation of ILI was also a recommendation by the NTSB as a result of the San Bruno California pipeline incident. This incident is attributed to an incomplete understanding of the pipeline characteristics, which could have been identified through an ILI.3 Therefore, PHMSA developed this ECA methodology as a way to validate a pipeline’s MAOP.
PHMSA based the methodology on experience gained since the implementation of integrity management, which typically uses ILI, and real-world examples from special permits that allow an operator to deviate from the prescribed requirements in CFR Part 192. The American Society of Mechanical Engineers (ASME) reported that an ECA can be
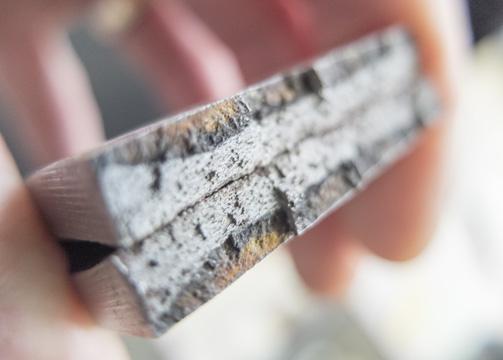
Figure 1. Validation testing, both in the ditch as well as destructive testing, can greatly benefit an ECA.
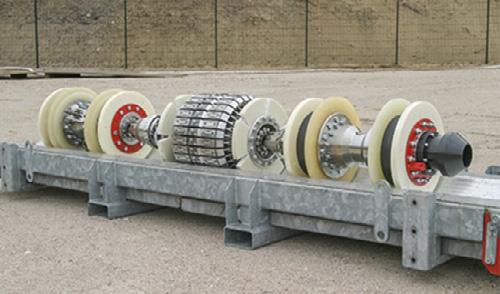
Figure 2. Using ILI to perform an ECA to reconfirm a pipeline’s MAOP can achieve equal or better results than a pressure test.
reliably used even if seam weld cracking is present on the pipeline. This research was sponsored by PHMSA.1
Sound data enables good decisions The MAOP reconfirmation process described in §192.624 requires that all applicable pipelines satisfy this new requirement within 15 years from the effective date of this new rule, namely by 2 July 2035. The expectation is that 50% of the total pipeline mileage is reconfirmed within 8 years of the effective date of the rule, with the remaining 50% completed by 2 July 2035. PHMSA deemed that the 15-year timeline was an appropriate window for completion of MAOP reconfirmation because it correlates to – and allows operators to utilise one of two – seven-year assessment intervals as prescribed in their integrity management programme. An operator’s integrity management programme, described in Subpart O, outlines a variety of methods for carrying out an assessment, including a Subpart J pressure test. It serves the purpose of both: ) Failing any flaw in the pipe not capable of holding the pressure required for MAOP.
) Proving that any flaws remaining in the pipe are strong enough to hold the pressure required for MAOP without leaking.
Section §192.632 outlines the process for conducting an ECA. Section §192.632 (a) indicates that an operator must integrate, analyse and account for all tests, assessments and information available on the pipeline segment, as well as consider any unknowns such as material properties and attributes. The results of an ECA, and therefore the ability to confidently act upon the results, is dependent upon the quality of the data utilised in the analysis as well as the knowledge and experience of the individual performing the assessment.
Robust ILI systems can provide the fundamental data required as input into the ECA analysis. The intent of an ECA is to establish the same level of confidence in the pipe’s strength as that of a Subpart J pressure test. This assessment is performed by calculating the predicted burst pressure of all ILI reported features in the line and ensuring these pressures are greater than the pressure necessary to establish the MAOP. Safety factors are incorporated into the burst pressure calculations according to risk. ILI can detect and size the relevant flaws needed to evaluate the pipeline’s fitness for service and integrity.
The particular ILI systems deployed must have the appropriate measurement principal onboard and associated performance specifications to detect, identify and size the critical flaw sizes according to the pipeline’s material and operating stress. ILI-reported features such as metal loss (manufacturing, gouging and corrosion), deformation (dents, buckles wrinkles), and crack-like and hard spots are then evaluated to a threshold, and potential remediation requirements are added.
This process is focused on achieving similar results to how a pressure test would fail imperfections in the pipeline above a determined critical stress. PHMSA added Section §192.712 to prescribe how the results of an ILI are assessed using various fracture mechanics models and establish conservative mechanical pipe properties to use when material records are not TVC. In the absence of reliable data for key parameters, such as fracture toughness, PHMSA allows the use of conservative pipeline material assumptions. These conservative assumptions have a direct impact on the fracture mechanics model used to assess the reported features. Section 192.712 also requires that a subject matter expert (SME) reviews the assessment in order to ensure the calculations are performed competently. The SME plays an important role in ensuring the calculations are realistic and not overly conservative. FAQ 3 by PHMSA provides guidance on defining an SME.4
Using ILI to perform an ECA to reconfirm a pipeline’s MAOP and achieving equal or better results than a pressure test is both achievable and highly beneficial. The data requirements are intense, but the use of ILI and historical information provide the foundation for completing the process in a resource-conscience manor without compromising safety. While Section §192.632 outlines a process for conducting an ECA, the operator may submit an alternate process through §192.18 if the same or better results can be achieved. Recent projects have demonstrated that an ECA will benefit greatly from validation testing, both in the ditch and through destructive testing.
References
1. Pipeline and Hazardous Materials Safety Administration (PHMSA), Department of Transportation (DOT). (2019, October 1). Pipeline Safety: Safety of Gas Transmission Pipelines: MAOP Reconfirmation, Expansion of Assessment Requirements, and Other Related Amendments. Federal Register. https:// www.federalregister.gov/documents/2019/10/01/2019-20306/pipelinesafety-safety-of-gas-transmission-pipelines-maop-reconfirmation-expansionof-assessment. 2. Pipeline and Hazardous Materials Safety Administration (PHMSA), Department of Transportation (DOT). (2011, August 25). Pipeline Safety: Safety of Gas Transmission Pipelines. Federal Register. https://www.federalregister.gov/ documents/2011/08/25/2011-21753/pipeline-safety-safety-of-gas-transmissionpipelines. 3. National Transportation Safety Board (NTSB). (2011, August 30). Pacific Gas and Electric Company Natural Gas Transmission Pipeline Rupture and Fire San Bruno, California. September 9, 2010 Accident Report. https://www.ntsb.gov/ investigations/AccidentReports/Pages/PAR1101.aspx. 4. Pipeline and Hazardous Materials Safety Administration (PHMSA), Department of Transportation (DOT). (2020, September 15). Batch 1 Frequently Asked Questions (FAQs) on Gas Transmission Final Rule 9-15-20. Regulations.gov. (2020, September 15). https://www.regulations.gov/document/PHMSA-2019-02250028. 5. SLATER, S., DAVIES, C., BURKINSHAW, O., CLYDE, P., & GRIFFIN, J. (n.d.). MAOP Reconfirmation for a 20 Inch Gas Pipeline Using the ECA Method and Enhanced ILI. Paper presentation, International Pipeline Conference 2020.