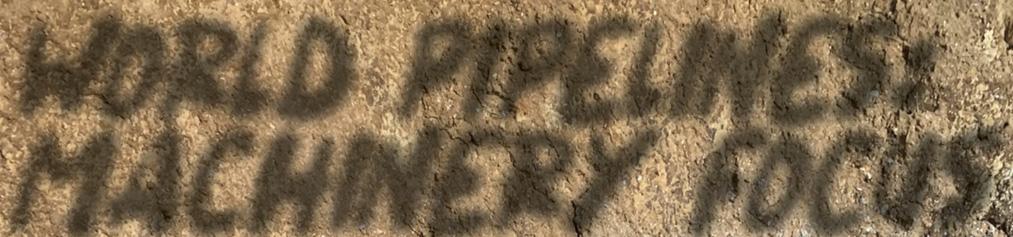
4 minute read
Machinery focus: Barbco
Thomas W. Schmidt, Barbco, Inc., and Drake Barbera, AccuLine Underground, USA, discuss a challenging guided auger bore project completed in Tennessee.
In February 2021, the AccuLine team was called on a 36 in., solid rock crossing in Dayton, Tennessee. AccuLine was notified that another contractor was set to attempt the crossing with a disc cutter head, but was not able to, by the time the jacking pit was completed. The overall project had no more time to wait, and became a rush to start. When reviewing the project details, the team was informed of the necessity that the bore was completed on the line and grade of the engineered plans, 0.15%, with no tolerance permitted. The AccuLine team made the decision to install a line-of-sight pilot throughout the crossing to maintain grade and to determine the ground conditions throughout the crossing, changing a rock SBU crossing to a Guided Auger Bore. The team, which included Drake Barbera, Clay Gillilan, and Joshua Knotts, set up AccuLine’s

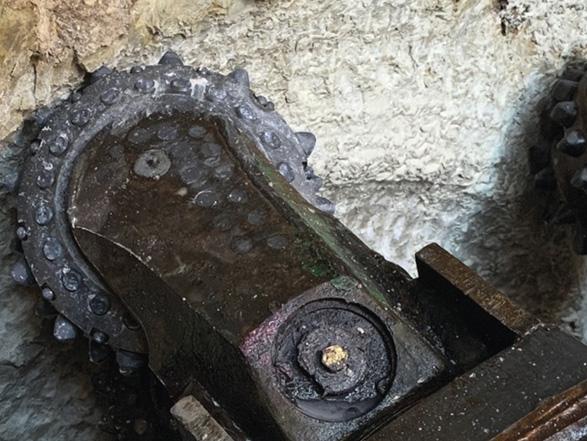

Figure 1. Close-up of AccuLine’s custom designed Pioneer One Hammer Tool.
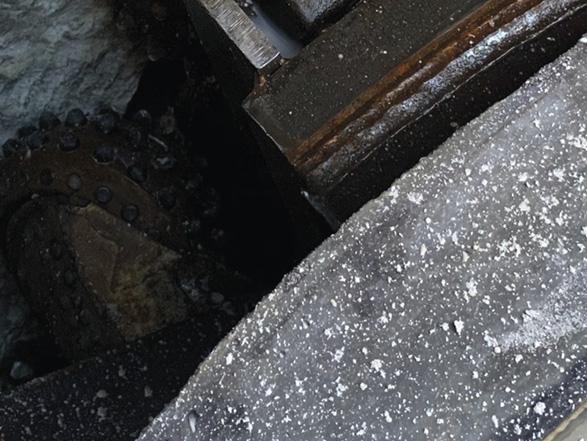
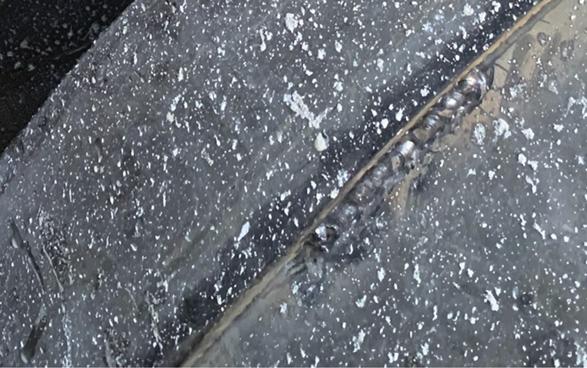

Figure 2. Close-up of the large cobble and loose material at the 40 ft bore mark.
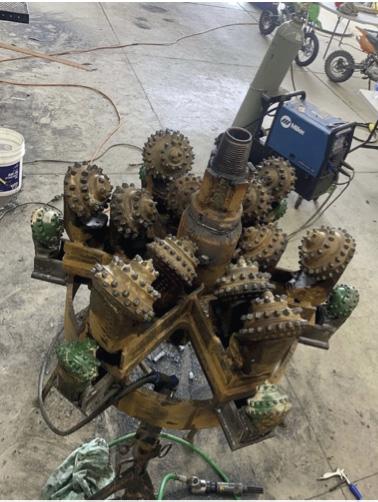
Figure 3. 36 in. Rollercone built to cut 48 in. Barbco Pathfinder 1000 and prepared to start the pilot phase. AccuLine utilised a Pioneer one hammer, with a custom hammer bit, built for their Pathfinder 1000. The crew piloted through 30 ft of solid limestone when they suddenly hit large cobble and loose material. As the team worked through roughly 8 ft of this material, line of sight became nearly impossible to maintain. This eventually caused a deviation in the pilot, resulting in the loss of line of sight. AccuLine then chose to stop work and evaluate the situation.
The crew made the decision to stop piloting. They began to install the 36 in. casing and open up the 30 ft section of solid rock, that maintained line and grade, with their in-house built roller cone cutting head. This decision was made to withhold multiple key factors of the crossing. First, opening the hole maintained the correct line and grade throughout the section of pilot that was acceptable. Secondly, having a cased hole, up to a section of extremely difficult ground, would allow the crew to safely support and stabilise pilot rod for reentry. Lastly, this decision would continue to push the overall crossing forward in progression. They then inserted an 8 in. casing, with pipe supports throughout the 30 ft cased hole, and set up to restart the pilot back on line and grade. AccuLine started the pilot into the 8 in. casing pipe and entered back into the ground, downhole, to continue the pilot phase. The crew would eventually finish, with line of sight, through various challenging ground conditions. After the pilot was pushed 2 ft into the exit pit, the team met with the engineering company on the project, to survey the pilot, and confirmed its successful completion.
AccuLine then began boring operations with their Barbco 54/60 boring machine. While pushing the 36 in. casing forward, attached to the redirected pilot, the pilot rod failed directly in front of the cutting head. The team then pulled the auger line and cutting head out to access the situation. After Joshua Knotts went in to find that the pilot rod snapped off of the head, the team regrouped and realised that the 36 in. casing would not be able to make the transition necessary to progress forward on line and grade. AccuLine then made the decision to back out of the hole and re-tool the cutting head in order to cut 48 in. This would allow for the 36 in. casing to progress forward through the transition and would later be filled with concrete. The team was able to redesign the 36 in. cutting head to cut 48 in. while being centralised by the original roller cones already on the head. The crew made the additions to the head and was successfully able to open the hole to 48 in.
Following the success of the hole opening, the team tripped out the cutting line once again. They were able to simply cut off the extra overcut roller cones and go back into the hole. AccuLine then welded supports onto the casing, in order to keep the 36 in. pipe centered, in the 48 in. hole. These supports would get ripped off after the first 10 ft of the casing made it past the transition. With these methods the 36 in. casing would easily make the transition and begin to make positive progress. The rest of the auger boring phase would include drilling 20 ft sections of 36 in. casing, and breaking out the pilot rod, in the exit pit, as they progressed. The team endured 3 months of extremely difficult auger boring, through various ground conditions, with 45 - 50 gpm of groundwater coming from downhole, and successfully entered the exit pit on line and grade. This crossing showed the vast capabilities of the AccuLine team, and the hard-work they bring to every jobsite.