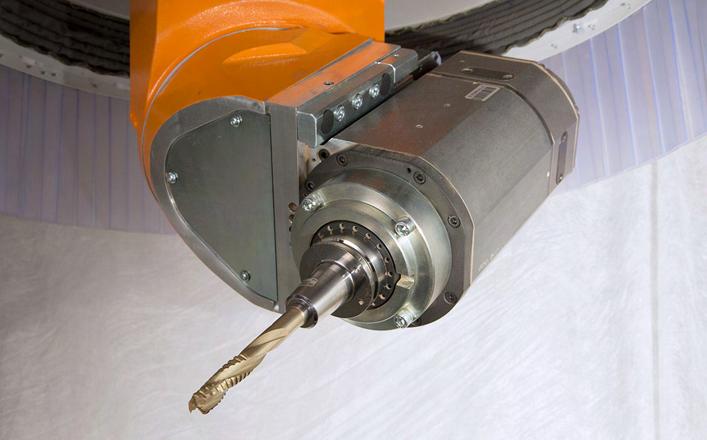
1 minute read
CASE STUDY
Its cutting and drilling accuracy has also slashed installation time on-site and reduced material waste throughout the production process. “We allow over-length on the machine but we can minimise this on each component we cut. Engineered wood lengths are also very accommodating which, when teamed with the CNC, have helped us reduce waste considerably. It’s this, plus the ProMaster’s speed, that has helped us see a return on our investment within eight months. It has given us the confidence to take on more orders and remain competitively priced.”
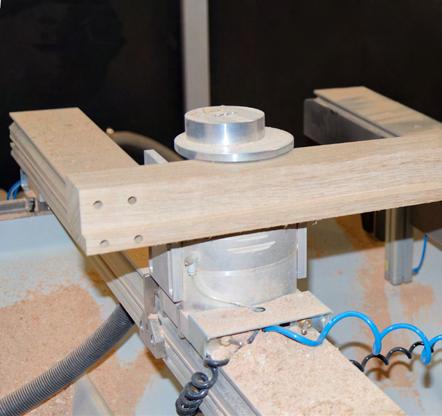
Advertisement
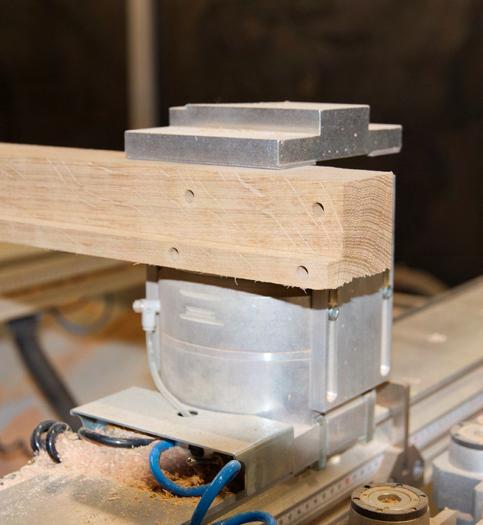
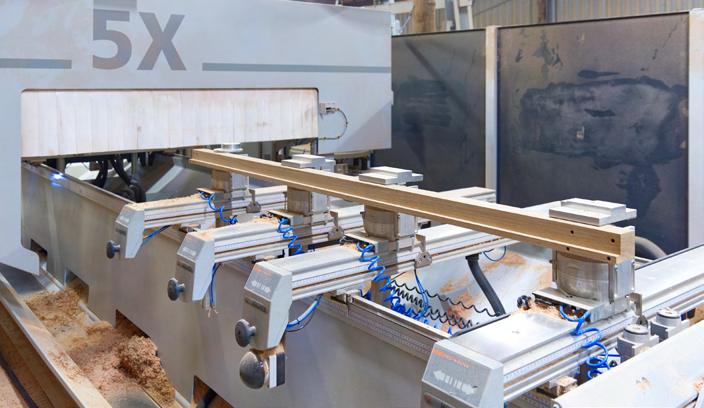
But the benefits of the Pro-Master are not just in the present day, as the forward-thinking company continues to explore new ways to grow and diversify. “Later this month, we’re set to launch a brand-new e-commerce door company which will allow us to maximise the machine’s running capacity. We’re also looking at some commercial projects too. It’s certainly a long way from where we were in 2020 when we were faced with a staffing shortage. Without making the leap and modernising our production methods, I’m certain we wouldn’t be in business today. At best, we’d have been running at a seriously reduced rate. Now, we’re pumped to see what the future will hold as we continue our ambitious five-year growth plan. One thing is for certain though, we couldn’t have achieved any of this without the guidance and support of Weinig UK’s team and we couldn’t produce our range of solid and engineered wood products at this level without our robust ProMaster CNC. For those people looking to take the next step, talk to Weinig. Their advice really was a game-changer for us and I couldn’t recommend them more highly.”
From the raw material being cut to the parts being assembled, Chris’ team can now have a door completed in 1.5 hours instead of the two days it would have taken before the ProMaster arrived
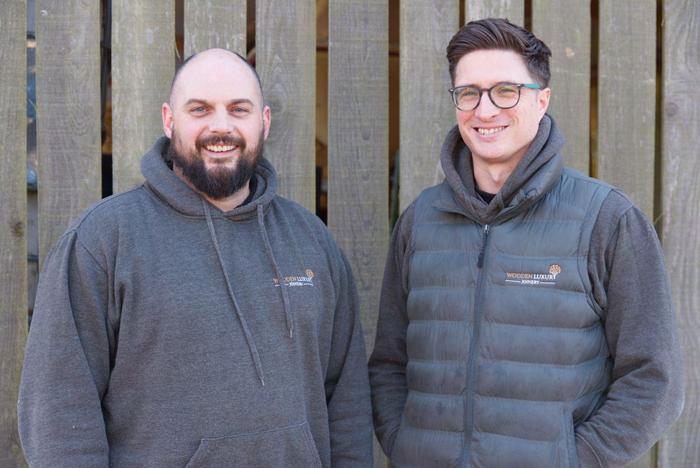