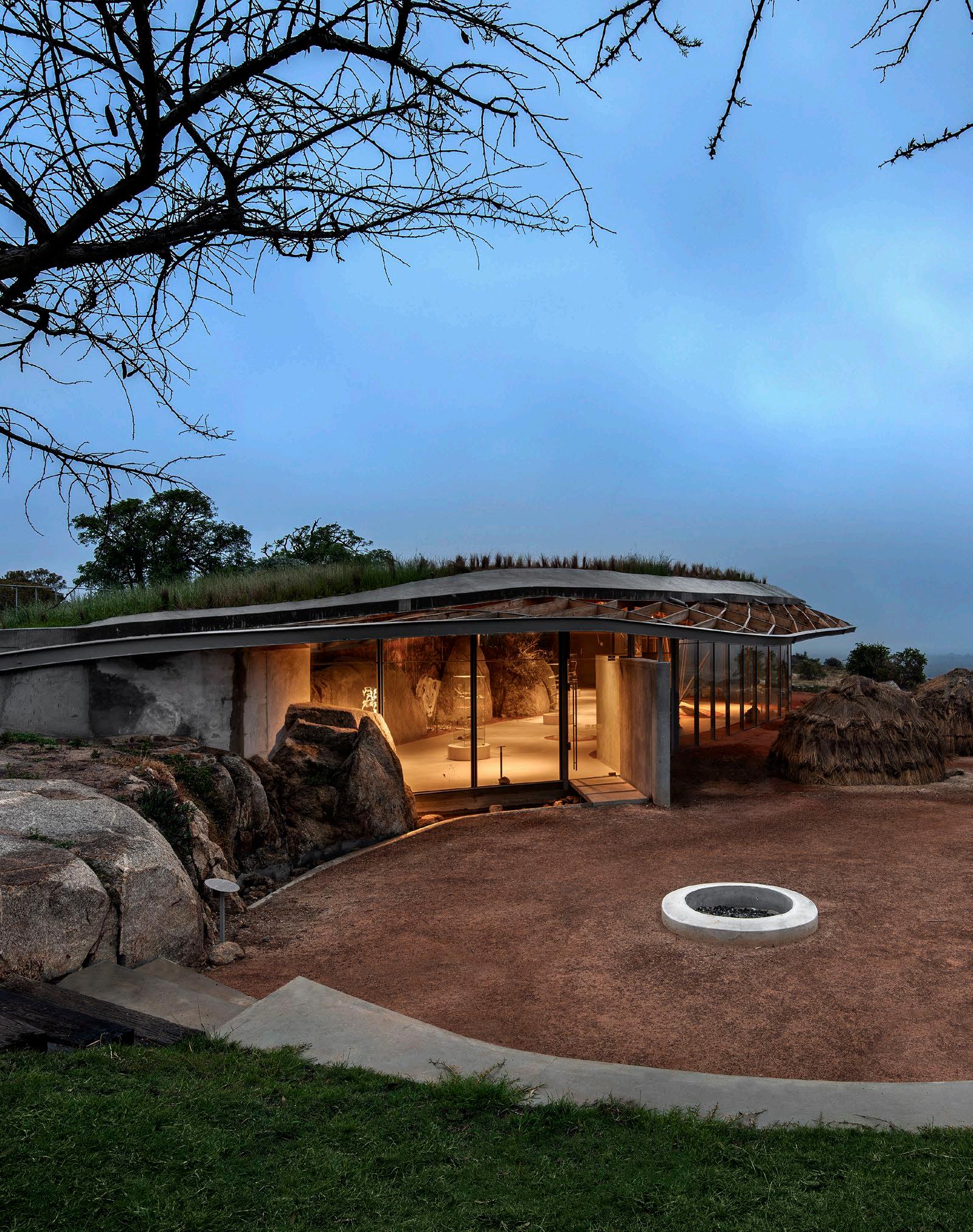
6 minute read
Khwa ttu San Heritage Centre
Completed: 2019 Size: 265m 2 Location: Yzerfontein, West Coast, Western Cape
In 1998, the Working Group for Indigenous Minorities in Southern Africa (WIMSA) decided to assist the San in unlocking potential tourism opportunities and showcasing the San culture to the world. WIMSA turned to Swiss anthropologist Irene Staehelin, who agreed to help. In 1999, guided by her own vision, and inspired by heritage centres in the USA and Canada, Irene bought an 850 hectare wheat farm, north of Cape Town on the West Coast of South Africa for the !Khwa ttu project. She subsequently set up the Ubuntu Foundation in Switzerland, to help guide and support the project. !Khwa ttu opened to the public in 2006. In the following decade, inside the now restored farm buildings, it steadily developed its tourism offering and San training capabilities. Outside, the land was carefully rehabilitated and wildlife reintroduced.
Advertisement
In September 2016 Ubuntu committed a substantial portion of the funding needed to build !Khwa ttu’s San Heritage Centre. This paved the way to fulfilling the dreams of many, and launched the next exciting stage of !Khwa ttu’s development. This San Heritage Centre project was headed by KLG Architects, with environmental work being taken on by Vula Environmental Services.
At the outset of planning the new San Heritage Centre at !Khwa ttu, it was decided that the project should have a low ecological impact, that it should be sensitively scaled in order for it not to overshadow the natural environment and that it should serve as a backdrop for its content and allow people to converse and share relevant information within a revelatory environment.
It displays the San ‘way of life’, not like a traditional museum, but with the building conceived as an organic landscape with an emphasis on sustainable and ethical design. The undulating structure is embedded within the landscape along a granite ridge overlooking vistas towards the Atlantic Ocean, close to Yzerfontein on the West Coast.
The proposed museum had to address not only the challenge of integrating into the natural landscape but also that of incorporating natural site features into the interior as part of an exhibition. This called for an innovative approach through the use of built form, local materials and inventive construction.
Concrete was chosen as one of the principal building materials for its plasticity of form, austerity in aesthetic quality, strength, durability and economy. An undulating multilayered green roof is supported on a very thin 80mm reinforced concrete layer which works in composite action with curved steel roof beams.
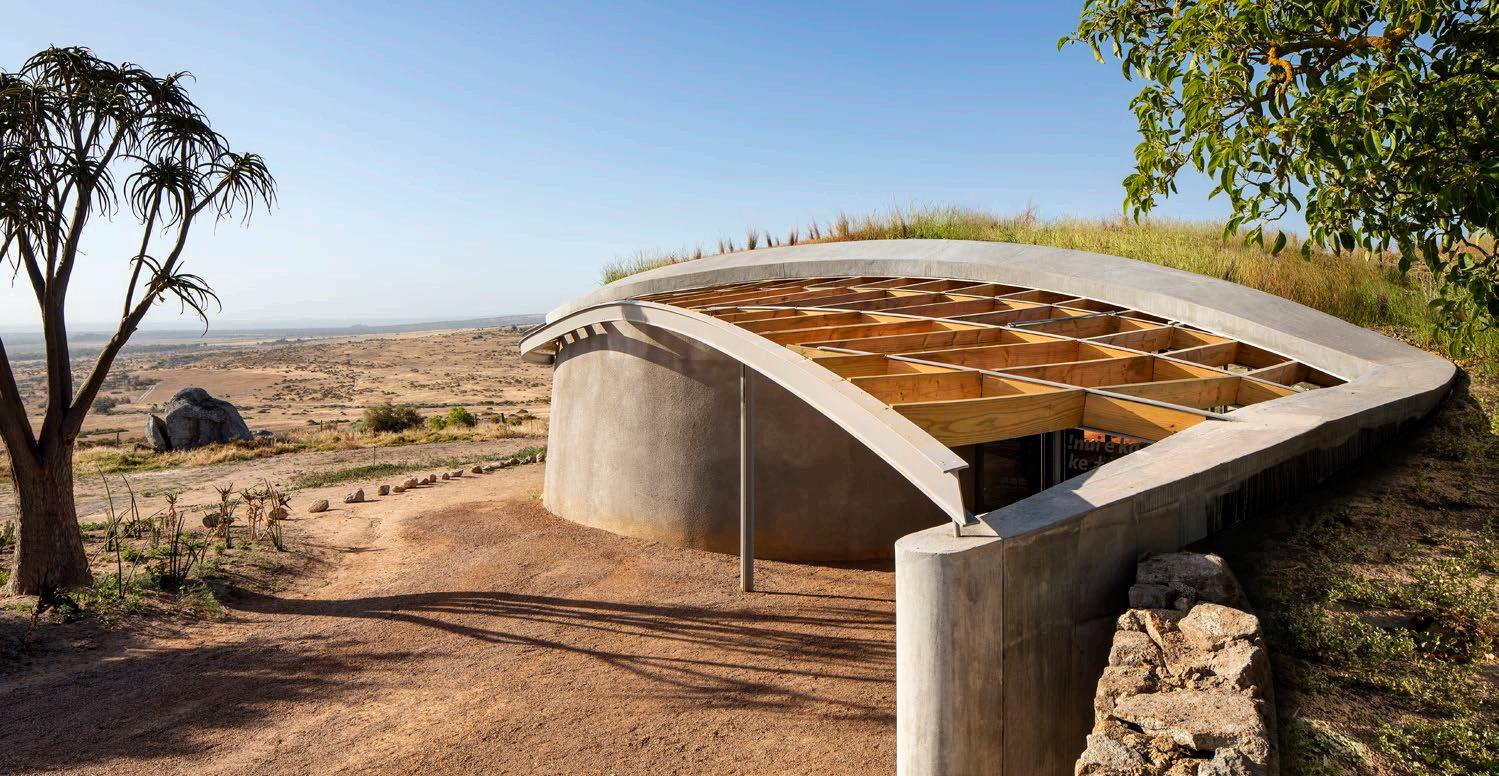
I-beams are cut in half and used as the main structural members. The resulting upside-down T-sections forming the beam soffits are easily bent to the correct varying degree of roof curvatures. The top half of the beam is made up out of a steel plate, held in position by a series of vertical flat sections with gaps in-between. This fabricated beam is much lighter than a conventional full depth beam, which would have been required if the concrete at the top was not used as a compression flange. The concrete has to be a very specific consistency in order to make the various falls of the roof possible.
A benefit of this method of concrete construction is that extra reinforcing steel can be introduced in specific zones where it is actually required. This technique allows for considerable savings in cost, material and overall roof load.
Permanent shutter boards on timber rafters are used to span between individual roof beams to form the unique curve of the roof and also acts as a ceiling internally. This dual functionality results in time and material savings on site. Indigenous self-seeding grass species are planted on top of the roof to deal with the harsh coastal climatic conditions. The green roof has thermal mass and natural thermal insulation qualities, which further assist with keeping the interior sheltered and cool during the hot summer months.
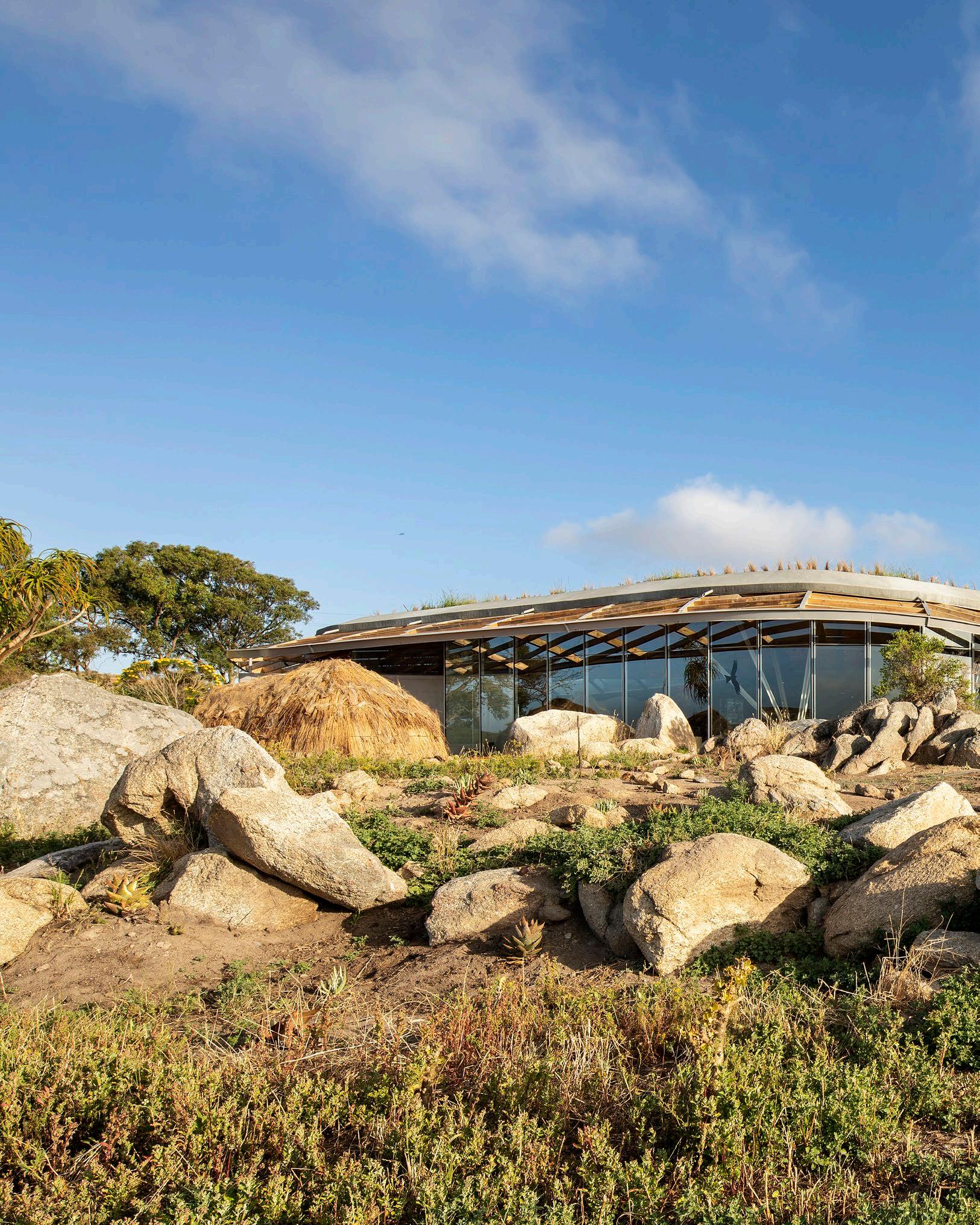
Architects
KLG Architects
Landscape contractors
Vula Environmental Services
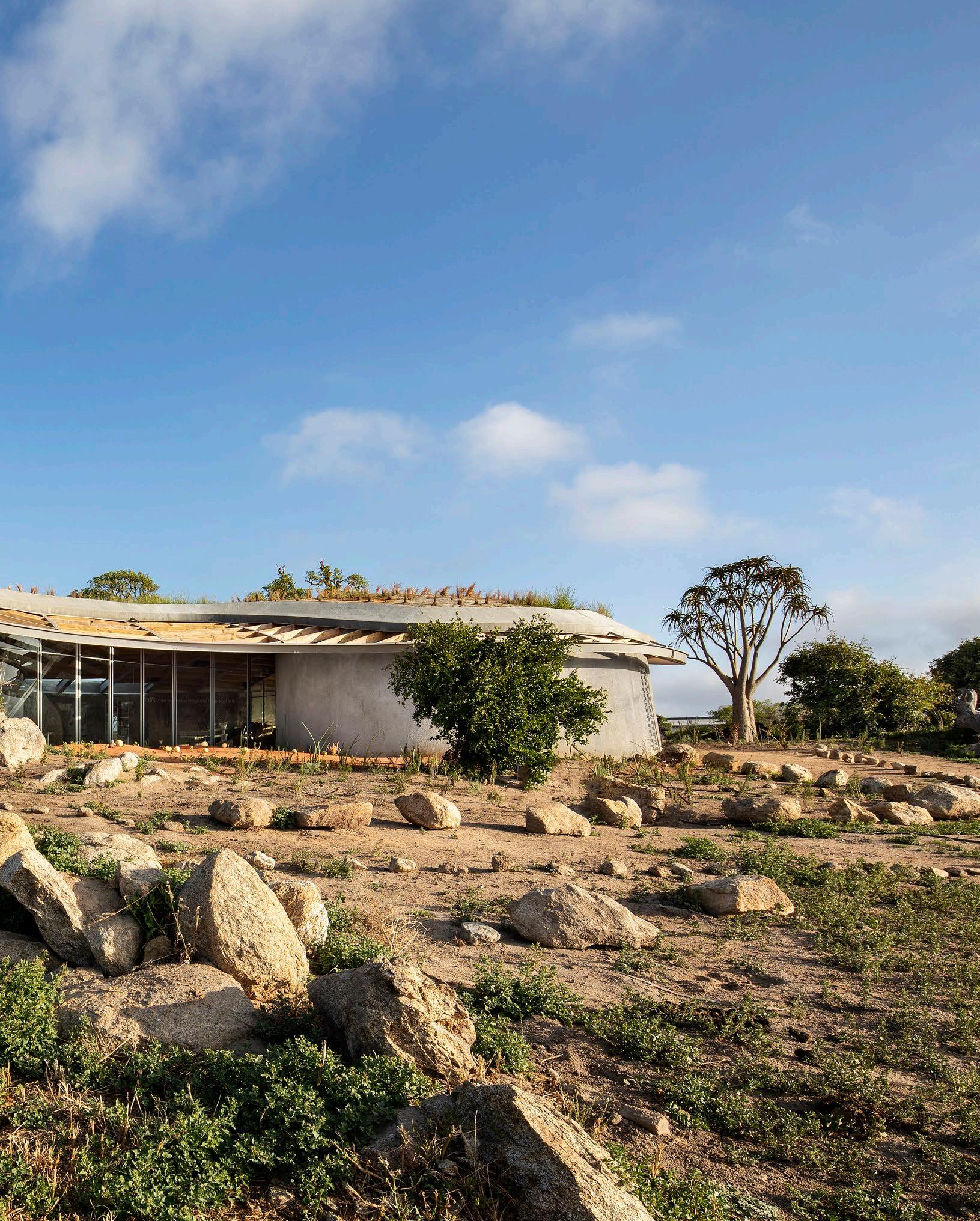
Images
Adam Letch - adamletch.com
It also seamlessly integrates the building into the landscape, minimising the building’s visual footprint.
Internally, the exposed granite rocks become an integral part of an exhibition wall.
The concrete roof edge parapets are hand moulded and shaped to the various curvatures and tied back into a retaining wall. The retaining wall is built as an undulating curve set in-between granite ridges which are expressed in an unadorned manner as part of the museum interior. The wall consists of two parts – a reinforced concrete load bearing retaining wall and a cavity with an internal dry-skin of brickwork.
This mitigates any possible moisture bridge between the water collected behind the wall or between the granite boulder cavities and the interior wall surface. Moisture is transferred down within the wall cavity into a sub-base of no-fines foundation pads to naturally dissipate.
The uniquely cast floor is shaped around the natural site features and celebrates rocky outcrops within the floor. This method of building displays a sensitivity and respect towards the context. The museum interior is envisaged as a landscape set below an abstract roof canopy which contains information and activity. For the floor, a special Lafarge concrete mix was used to emulate the colours of the Kalahari San environment. A granite stone aggregate from a local quarry was added to the mix and the surface was ground down to a finely textured ‘salt & pepper’ finish, which delicately exposes the aggregate. The floor was cast and shaped around the exhibition floor surface. This demonstrates the fluidity of material to adjust sensitively towards its context, ultimately translating the space into a rich and authentic expression between the natural and the built fabric.
Provision is made for a hydronic underfloor heating system on top of a rigid insulation layer which forms part of an ‘active’ thermal mass design approach for heat radiation during cooler winter months, whilst the inherent thermal mass of the concrete slab is also utilised as a heat sink.
The media centre is shaped as a nonsymmetrical eclipse and has a rock store built within the tapering mass of its walls. Air is funneled through the walls from an underground

concrete plenum below the floor level. The wall cavity is divided into different chambers with transverse walls to tie the tapering masonry walls together. The wall ‘chambers’ are hand packed with local granite rocks on top of precast concrete lintels above the underground plenum. Air is drawn up through the gaps between the lintels to cool the rocks at night. During the day, air flowing over the rocks can therefore be cooled down before being discharged at the highpoint of the wall into the media centre’s interior.
These sustainable approaches allow for a climatically stabilised internal environment while also reducing the need for conventional heating and cooling services and their associated energy demands.
The structure consciously demonstrates a balance between the context, materials and design philosophy through a combination of passive environmental strategies and contemporary technologies.
SUPPLIERS
Lighting:
Megalite – 021 797 8487
Concrete works:
Melt-Wahl – 021 946 1334
Timber:
Prinro - 022 772 2334
Concrete sealing & waterproofing:
Crete Color - 021 823 0000


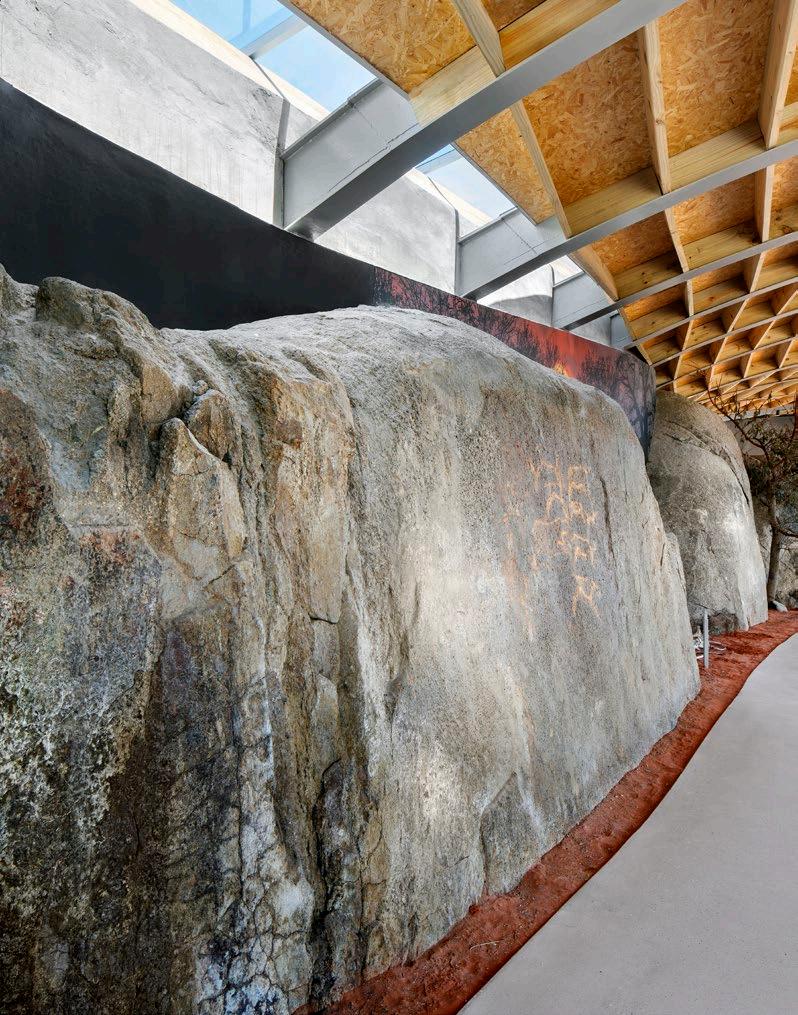