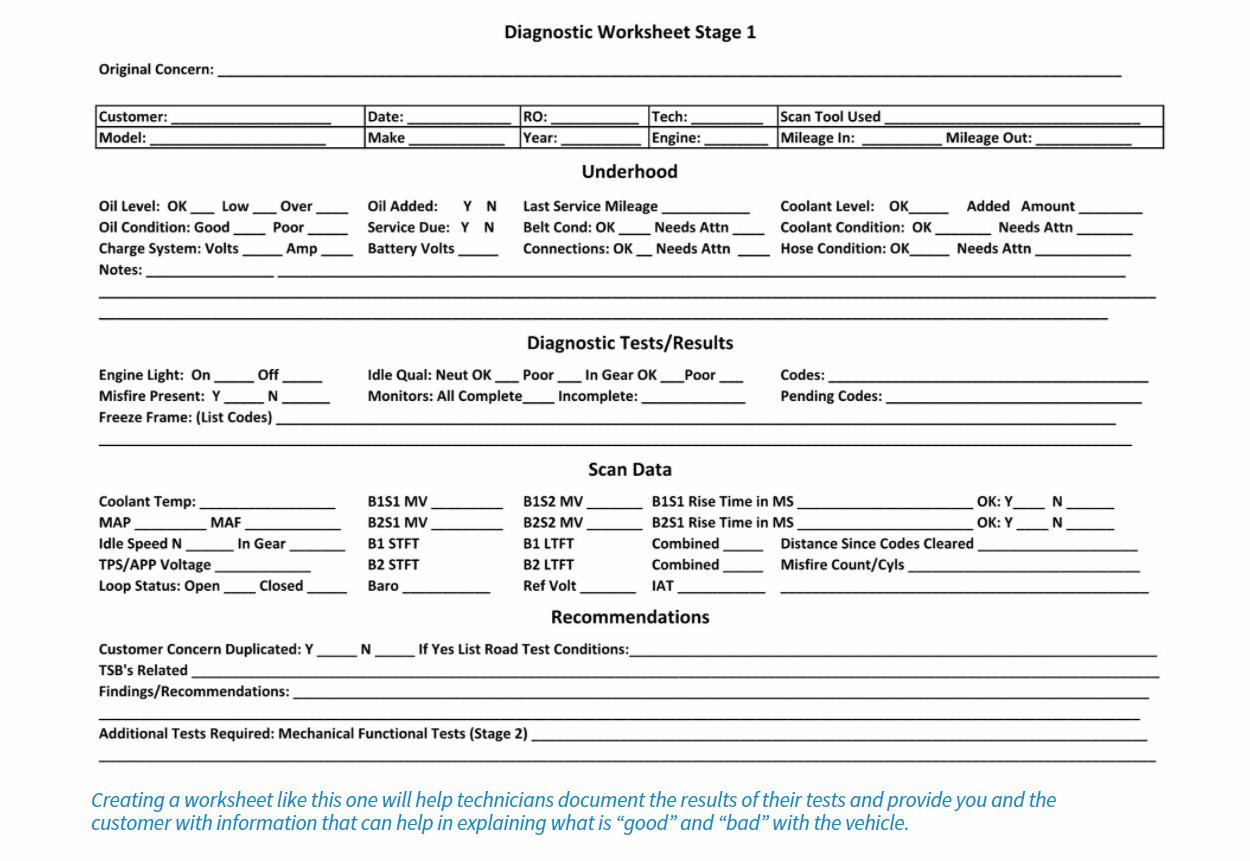
4 minute read
Leverage your team’s diagnostic nous
from Auto Channel 38
by Via Media
Build a diagnostic process step-by-step
IMPLEMENTING A FORMAL PROCESS IMPROVES CONSISTENCY AND OFFERS BENEFITS TO CUSTOMERS
Advertisement
Most technicians think the beginning of a diagnostic process is breaking out the scan tool, but that’s not always the case. A good diagnostic process will encompass many tools, but it also involves getting the right information.
A good diagnostic process will improve profit through efficiency, leverage the expertise in your workshop, and show customers the value of paying you for the diagnosis. It will result in fewer misdiagnoses and fewer comebacks.
DUPLICATE THE CUSTOMER’S CONCERN
Many workshops will have similar stories, like the customer who left a car at a workshop with a spare key. It had a rough idle but the carburettor mixture could not be adjusted to clear up the rough idle. A carburettor overhaul appeared to fix the fault, until the customer picked up the car and reported the same problem. The workshop made a minor adjustment to the choke, and it ran fine again.
The customer picked up the vehicle and five minutes later they were back to complain that the car had stalled. The technician went for a ride with the owner to duplicate the problem and noticed their key was on a long lanyard with at least 20 keys and gadgets on it. The weight of all those keys swinging about shut off the ignition.
And surely we’ve all heard about the customer whose car always ran rough until a drive with her revealed she always pulled out the choke to hang her handbag from it … Or the customer who complained of a noise when driving on the motorway. The workshop found no issue until the owner took the mechanic for a drive and they ran the car up to 120kph, when the roof rack started to drum — not something a workshop sticking to the speed limit would discover.
Hand in hand with duplicating the problem is asking enough of the right questions to make sure you have sufficient information to duplicate the issue.
ALWAYS CHECK THE BASICS
A technician was tasked with diagnosing a checkengine light. This car, a Mustang, had a code for a faulty manifold absolute pressure (MAP) sensor. The technician replaced the sensor, then said the new sensor was defective and needed another one. As this technician was right much more than he was wrong, the workshop ordered another sensor. When the new sensor came, he installed it, then said the car needed a new power-train control module (PCM).
Now, computers are very reliable and, in most cases, issues are caused by other factors. I went to confirm the need for the PCM when I heard a popping sound coming from the exhaust. The technician said that he hadn’t checked the vacuum with a vacuum gauge. He had assumed it was OK. A vacuum gauge was installed on the manifold and it showed that the vacuum was jumping between 15 and 25 inches (38 and 63cm), indicating a broken valve spring. MAP sensors had read the engine vacuum and reported it to the PCM. As the vacuum reading was fluctuating so much, the computer assumed the sensor was faulty and sent a code.
THREE-STAGE PROCESS
three-stage process. Stage one is a system check, including the basics. Stage two will normally involve performing some intrusive tests when necessary, such as compression testing or timingbelt alignment. If the diagnosis is not clear after stages one and two, stage three is required, when you would perform specific pier-to-pier or pinpoint tests from the computer to individual components.
Using this approach will make it much easier to set a price and explain to the customer what is involved when the workshop provides the results of a diagnostic test to them. It also means that every technician can be trained to perform the process so that every vehicle is tested in the same manner.
To set up a similar process, get together with your technicians and ask them how they approach a diagnostic problem. Document these steps, then discuss them with your technicians to make sure they are on board with a new, formal process. Once they are on board with this approach, create a step-by-step worksheet for diagnoses. Documenting the results of their tests will provide you and the customer with information that can be useful in not only diagnosing the issue but also explaining what is ‘good’ and ‘bad’ with the vehicle and deciding the next steps.
The good and bad can also assist you in showing the value of the service you have just performed and in charging a reasonable fee for the diagnosis.
BENEFITS
Having an agreed set of steps to follow for each vehicle reduces some of the worry for technicians about missing clues and misdiagnosis. It also allows the technician to be more thorough and less concerned with being fast or right the first time, and helps them to focus more on finding the issue. It also decreases the likelihood of a comeback or unresolved vehicle problem.
That will mean a more efficient workshop and increased driver or customer satisfaction. A standardised process can also help management set pricing for both vehicle diagnostics and repairs.