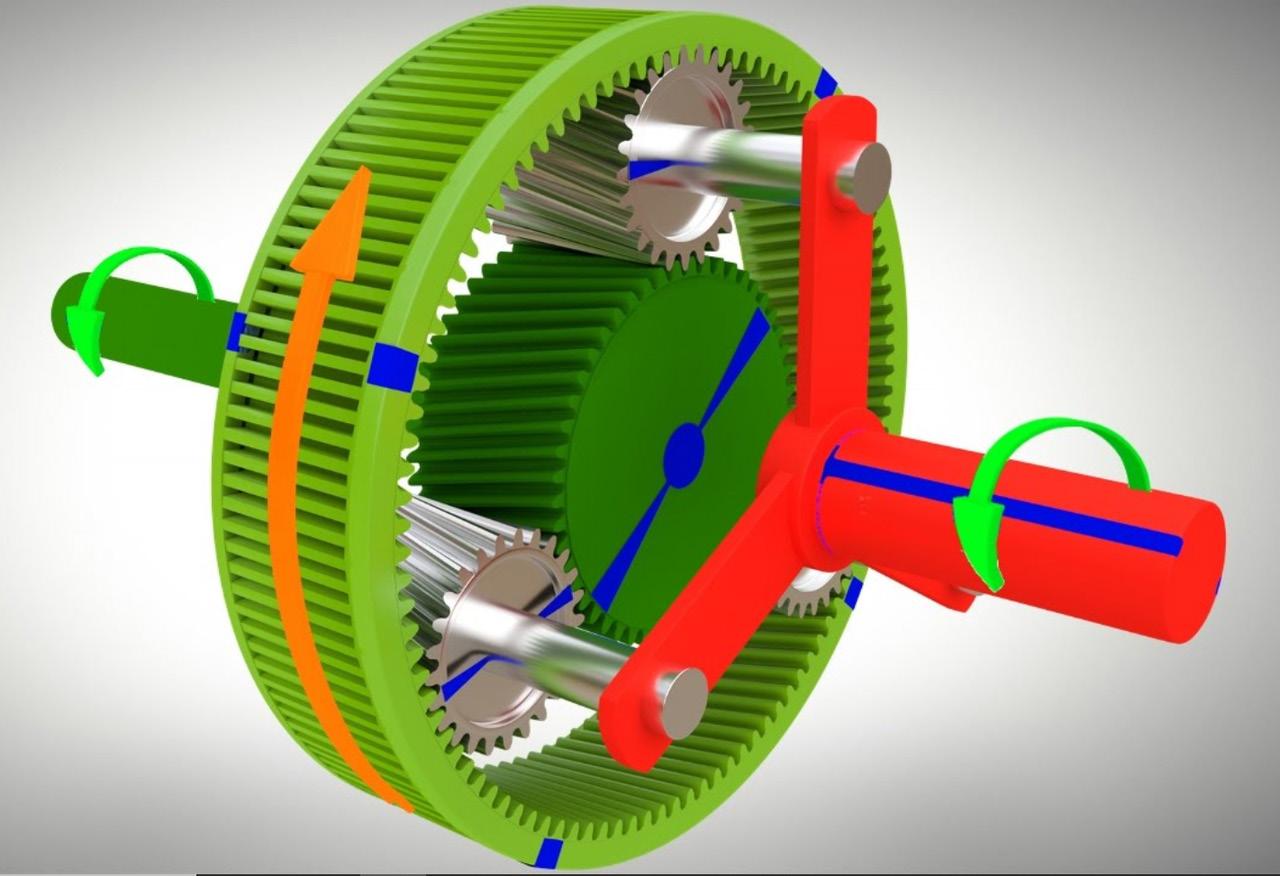
9 minute read
Petrol guy opens doors to hybrids
from Auto Channel 38
by Via Media
This kind of planetary gear set — a compound drive unit — connects the ICE with the MGs to allow a series-parallel operation and the ability to create positive or negative torque, driving the vehicle down the road or charging the battery through regenerative braking
Taking on a hybrid
Advertisement
THERE ARE SOME FUNDAMENTALLY DIFFERENT TECHNOLOGIES IN A HYBRID CAR, BUT THEY MUST ALL BOW TO A TRADITIONAL APPROACH TO UNDERSTANDING AND MASTERING AUTOMOTIVE SYSTEMS
It’s no secret that the automotive world is changing as governments drive towards lower emissions. We can run, but we can’t hide. Hybrids, plug-in hybrids, and battery-electric vehicles (BEVs) are here to stay, and as carmakers around the world are switching wholesale to the new technology, we all need to get on board with it. It need not be traumatic, and a traditional approach to workshop work can help us navigate this technology, which is also based on well-known and well-understood principles.
THE THREE-LEGGED STOOL APPROACH
Picture an automotive technician perched on a three-legged stool. He or she is supported by three pillars: • fundamental knowledge • reliable service information • proper tooling.
The first is developed over years of experience dealing with the components and interactions that make up virtually all systems in almost every vehicle. Experience with how these devices function becomes second nature to us. This must include thorough understanding Ohm’s law, the operation of DC motors, and other inductive devices like relays and solenoids found in almost everything we see daily. We should have them mastered, and that means we don’t have to research their functionality every time we come across them.
Reliable service information includes the wiring diagram — the roadmap for the electric current powering the devices. The wiring diagram allows us to see how any function is carried out on the specific vehicle we are faced with.
Equally as important as the wiring diagram is a solid description and theory of operation about the system you are working on and the components that make up the systems. These are both crucial to the successful and efficient diagnosis and repair of the vehicle.
Finally, we need proper tooling. Having the tools necessary to evaluate the systems or components is the first step, but understanding the limitations of the tools or tests you are performing is also a must. If we don’t know what to anticipate or learn from the outcome of a test, the data we gather are pointless.
This three-legged-stool approach applies to hybrids as well as any other operating system. All three of the stool’s legs must be rigid and supportive to apply this approach. We may be low on some elements of understanding on new systems, and that is OK. It simply means that we need the training to reinforce the strength of that fundamentalknowledge stool leg.
HYBRID BASICS
Let’s fill in some gaps. First we need to acknowledge that a hybrid uses more than one source of propulsion. Some hybrids are configured as parallel hybrids, like that of Honda’s earlier systems (known as ‘Integrated Motor Assist’, or ‘IMA’, systems) in which a three-phase AC-motor stator is confined within the bell housing of the engine and transmission. The motor’s rotor is attached to the crankshaft (where a torque convertor typically rests). The very small displacement internalcombustion engine (ICE) will continue to run as the vehicle is propelled down the road. However, when necessary, the onboard engine control units (ECUs) will allow the IMA motor to produce torque. This allows the vehicle’s small ICE to produce far fewer emissions, yet still require torque output to perform adequately. It’s referred to as a ‘parallel hybrid’ because both propulsion systems (IMA and ICE) operate alongside one another. The IMA motor is also used to start the ICE.
THE SERIES-PARALLEL HYBRID
The other configuration of the hybrid is now more common. This ‘series-parallel’ hybrid configuration is used in the Toyota Prius. In this configuration, the ICE serves multiple purposes that will be discussed shortly. The electrified propulsion system has two three-phase AC motor generators (or three, if
all-wheel drive). They’re referred to as ‘MGs’. They serve to operate a bit differently (they too will be discussed shortly). In the heart of the hybrid propulsion system is a device called a ‘compound gear unit’. This device is a planetary gear set that allows for simultaneous or individualised operation of an MG and/or ICE. By holding one of the three planetary gear-set major components still and driving another, the third component’s output speed and direction are forced, enabling the planetary gear set to have many different modes of output. This is why it’s referred to as a ‘series parallel’.
Both the electrified propulsion and charging systems are connected by a compound drive unit — a planetary gear set (main picture) which distributes power in different ways as follows: • The ICE is connected to the planetary gear set’s carrier. This allows torque from the ICE to be carried to the transaxle. • MG1 torque is sent to the ICE during start-up, by way of the sun gear as it is connected to MG1’s rotor. MG1 is also used to control engine gearing (when it is operated simultaneously with MG2) and provide charging to the hybrid battery pack, dependent on operating conditions. • MG2 is what propels the vehicle down the road. It is connected to the ring gear of the planetary gear set, which is part of the transaxle’s final drive. • Regenerative braking is achieved when MG2 functions as a generator and charges the hybrid battery pack. MG2 is used as a generator to slow the vehicle and charge the HV battery pack.
AC TO DC RECTIFICATION; SURE … BUT DC TO AC SYNTHESIS?
But we are not done yet. It still takes the appropriate training to gain the level of understanding we need regarding the electric and electronic controls. These allow those mechanical functions to happen.
Communication systems exist on all of today’s vehicle platforms. These systems serve to reduce cost as well as weight. These virtual systems provide the same functionality as hard-wired systems but much more efficiently. We should already be familiar with them and understand that they exist in hybrid vehicles as well. This allows for the sharing of data from ECU to ECU and from system to system.
What you will find different is that the hybrid system operates at a much higher voltage level than the conventional charging system voltages we are accustomed to. That being said, there is no need for a conventional charging system or an alternator. The typical system operating voltage we see will be derived from the highvoltage (HV) DC side of the vehicle. A device called a ‘DC-DC converter’ takes the HV from the HV battery pack and steps it down to the 12V–14V we are used to seeing.
Early on, I mentioned AC motor generators. They can’t be supplied DC voltage and be expected to operate. So, how does the available DC voltage make its way to the MGs as AC voltage? It is through a device called an ‘inverter’ that takes the HV DC and synthesizes it to AC voltage.
Internal to the inverter are very fast operating electronic switching devices called ‘insulated-gate bipolar transistors’ (IGBTs). When operating, they allow current to flow, and when at rest, current flow ceases. The takeaway is that they operate so swiftly that the current amplitude can be controlled by controlling the frequency at which they operate. This effectively synthesises the AC waveform using DC voltage.
The inverter also contains high-voltage diodes. They serve as a way to rectify the AC voltage from the MGs back to DC (like a conventional alternator), so it can replenish the HV battery packs and allow the functionality of the components found on the conventional system voltage side.
The three-legged stool
PROPER TOOLING
As with any other system we’ve encountered in
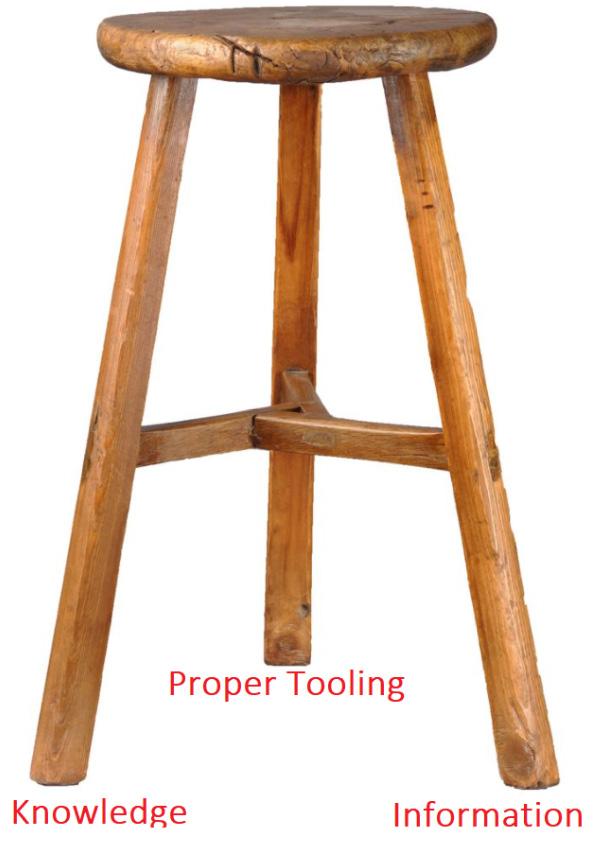


An AC sine wave (left) and a synthesised sine wave derived from rapidly cycled DC voltage supplied by the inverter’s IGBTs, which allows MGs to operate
Honda's Integrated Motor Assist (IMA) system shows the rotor and stator assembly that supplements the internal combustion engine (ICE)
the past, proper tools and familiarity with them are what it takes to get the job done right the first time. First and foremost is a need for safety. When dealing with high-voltage systems, we could see voltages near 40V and upwards of nearly 600V. It takes very little amperage to really injure or even kill you. Safety is of the utmost importance. Be sure to always follow the recommended service procedures and to always take the prescribed necessary precautions when working on or around HV vehicles and their components.
Proper precautions mean wearing or using the appropriately rated personal-protection equipment (PPE). This includes insulated gloves rated at Class-0 or up to 1000VAC. These gloves should be field inspected and tested before and after each use. They are also required to be certified (sent out for evaluation) every six months. Blow a lungful of air into them to make sure there are no leaks. It’s always wise to ensure that your hands are dry by using glove dust and also covering the gloves for protection, using leather gloves over top of the PPE. This will ensure that your PPE is protected from damage and you are properly insulated from electrical shock. Insulated hand tools are also recommended to further protect you and those around you.
Venturing into hybrid-vehicle diagnosis and repair will probably introduce you to some unfamiliar tooling such as the megohmmeter, commonly known as a ‘megger’. This device is like an ohmmeter on steroids. It’s used to determine a breakdown in HV component insulation. It functions by driving very HV (500V or more) into a component and measures resistance accurately, even up to billions of ohms. Its operation is designed to detect a short circuit or continuity between an HV component and chassis ground.
Another new device could be the milliohmmeter. This functions at the opposite end of the spectrum. Its operation is designed to detect even very minor shorts between the three stator windings of an MG.
TRAINING AND CERTIFICATION
Finally, where can one go to get the proper training to be a qualified hybrid- and electric-vehicle technician? There are several reliable sources of training information, but you will want to do your research and determine what is best for you and your workshop when it comes to certification.
Going ‘hybrid’ is more of a mindset than a skillset. Acquire the proper knowledge, invest in the appropriate tooling, and provide yourself with adequate service information. That way, you will not only understand how the hybrid propulsion (and supportive systems) functions in general, but you will also quickly become familiar with the vehicles that will soon be common in our workshops.

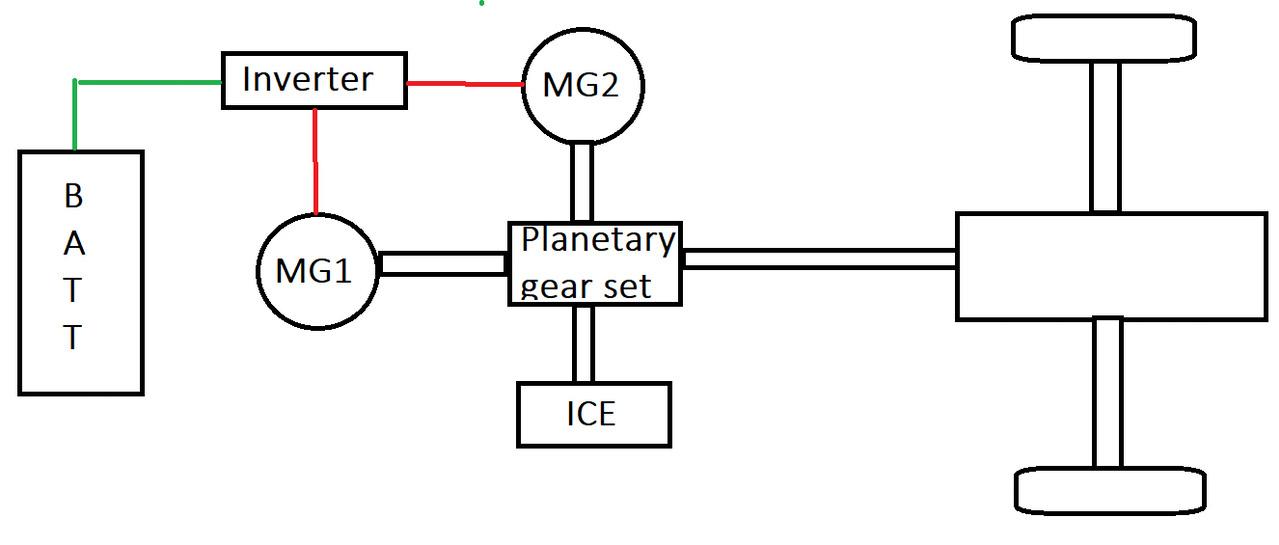