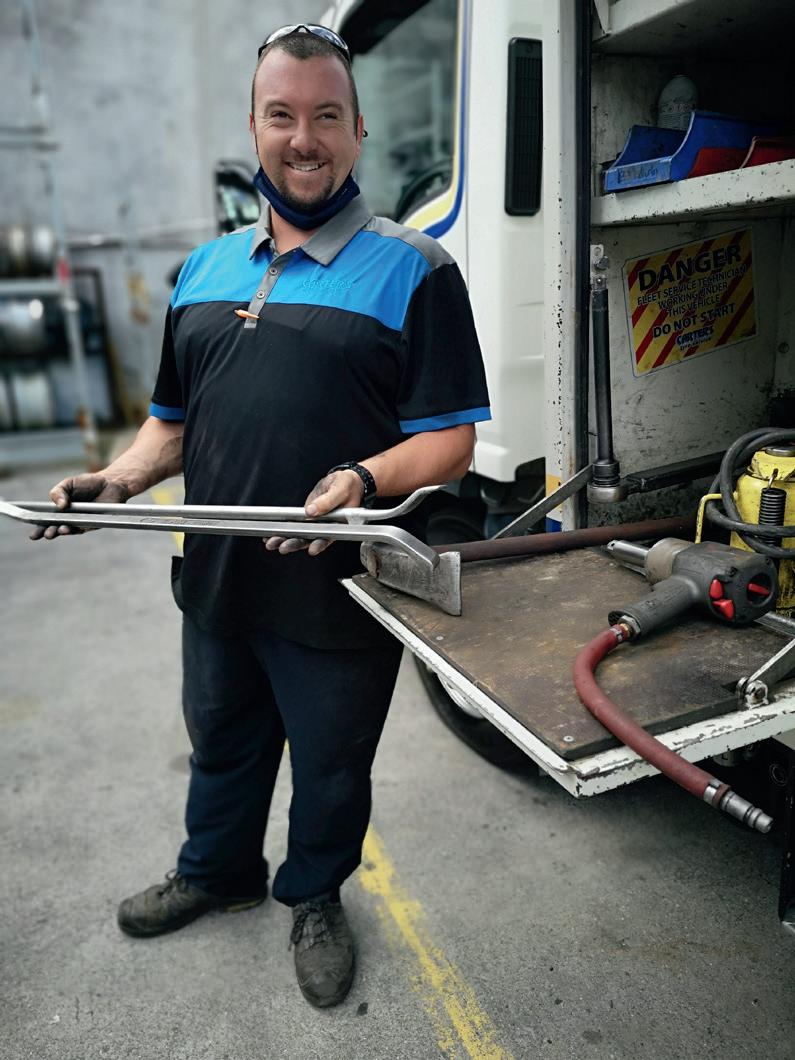
5 minute read
New mobile truck tyre machine 1 and
from Auto Channel 42
by Via Media
even thought it would take longer, and it meant getting a class 2 driver’s licence for the new trucks which have increased in size from six to nine metres, as they also carry 24 tyres. The first five new Tyrebox equipped vehicles, including a van, are going to Carter’s best and most experienced staff who work late shifts. The main challenge now is that everyone will want one.
Importers Century Distributors’ general manager Todd Jenkins says the Tyrebox is an off-the-shelf solution and all components are built into one simple-to-install package. Developed by Guernet Compressors, the diesel engine, tyre changer, and compressor in the Guernet Tyrebox are all designed to work together.
Advertisement
ALL HYDRAULIC
All of the tyre changing operations, including clamping unit rotation, are hydraulically driven and it is currently the only fully hydraulic option in the market. This compressed air-driven hydraulic solution provides more torque, more reliability, and as it’s diesel powered, it can be mounted anywhere outside without the need for a power supply to an electric motor.
A 17hp Lombardini diesel engine drives a piston compressor and 120L reserve air tank. Being a simple diesel engine, the maintenance requirement is low and servicing can be carried out by any diesel mechanic. No special parts or tools are required.
The hydraulics deliver a massive 25,000 Newtons of bead breaking force — that is the equivalent of the Sice S45A in-store tyre changer, and 5500 Newtons more than the nearest competitor.
The Tyrebox comes with two 20m hose reels — one for inflation and one for air tools — however, the unit is still 100kg lighter than the nearest competitor, at 739kgs for the complete unit, an equivalent of two extra tyres in weight saving.
Mike Guard with the traditional tools — levers
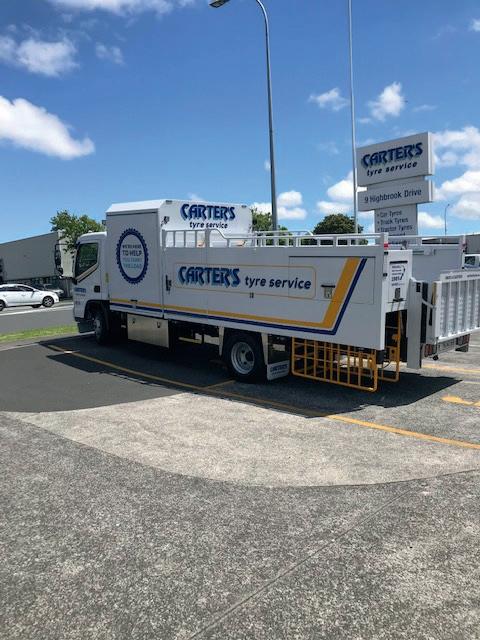
The tyre machine folds out from the truck
PISTONS VS SCREWS
The key strength of the Guernet Tyrebox is the piston-type compressor, which offers greater reliability in mobile use. The alternative screwtype compressors are designed to run in industrial applications where they have 18-24 hours continuous use.
In a mobile tyre unit, screw compressors suffer premature wear of the screw due to cold starts and water emulsion in the oil. Screw compressor starts will dramatically increase water emulsification in oil, which can be carried from the sump and forced through the air lines. Mike confirms the screw-type compressors on their other trucks need frequent maintenance and rebuilds.
A piston compressor, on the other hand, is designed to be run intermittently, optimally at 60 percent use and turned on and off as required — a most suitable match for the mobile tyre changing environment.
The Guernet Tyrebox will run consistently between 105 and 170 Psi and never drop lower than the pressure required to inflate a truck tyre, which is the largest demand in the tyre change cycle.
For more information on the Guernet Tyrebox, contact Century Distributors on 04 567 1405.

Mike checks tread depth digitally
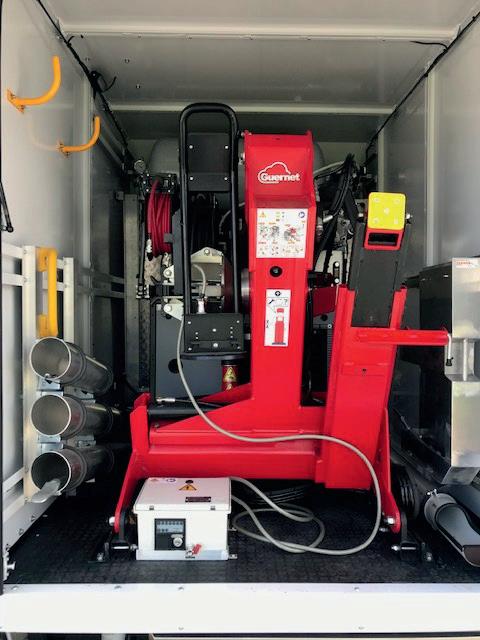
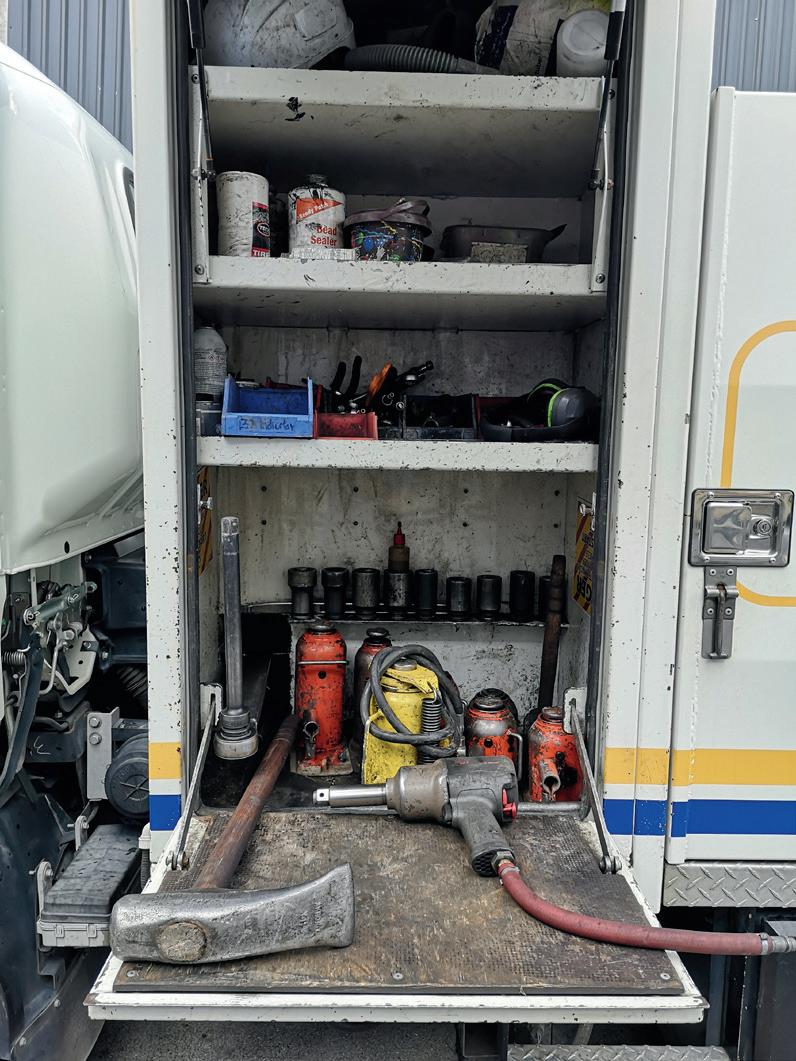
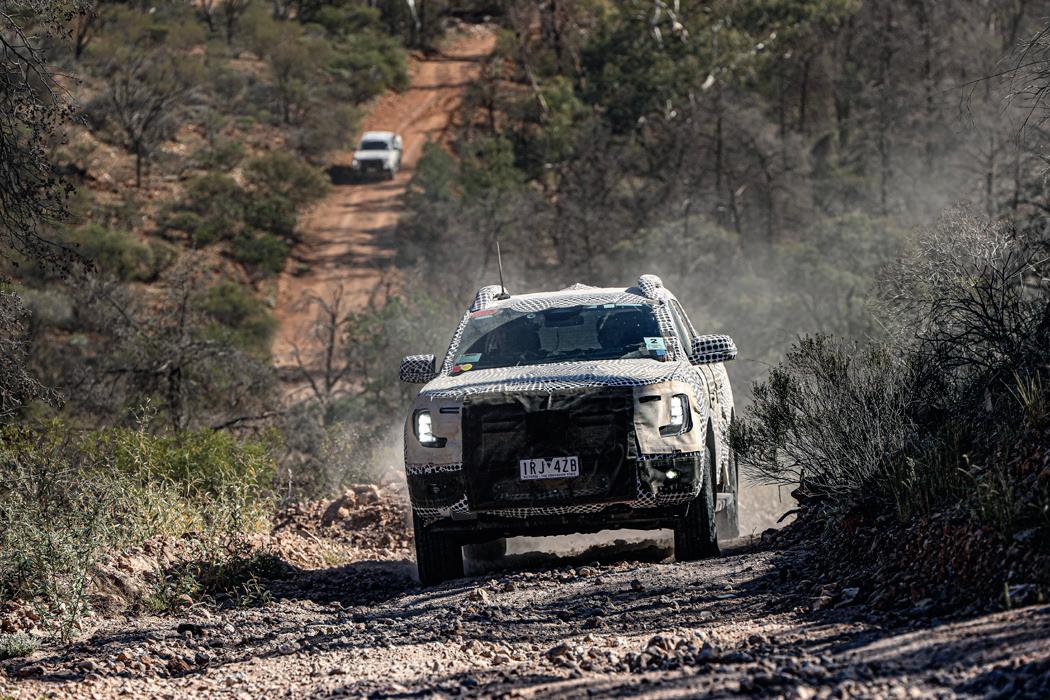
Tested to extremes — the next-gen Ranger’s punishing path to customers
TESTING A ROAD CAR IS RIGOROUS. TESTING A VEHICLE DESIGNED TO ALSO HANDLE OFF-ROAD CONDITIONS, FROM THE MUDDIEST JUNGLE AND ROCKIEST MOUNTAIN TRACKS TO BAKING DESERT OR FREEZING TUNDRA, CALLS FOR NEXT-LEVEL CHALLENGES
Ford’s global team of development engineers doesn’t pull any punches when it comes to testing the next-generation Ranger’s toughness and durability. After all, they need to deliver a truly global pick-up that is up for the challenge across 180 markets.
Built from the ground up to be the toughest, smartest, most versatile, and most capable Ranger ever, the truck is being subjected to more physical and virtual testing than ever before. The next-generation truck will be an all-new model based on the new Ford Bronco platform. It had yet to debut as this issue went to press, but Ford Europe was due to reveal the new model in late November.
“Earning a Built Ford Tough status is not something we take lightly,” says John Willems, Ford Ranger’s chief programme engineer. “Every part of the next-generation Ranger was tested to the same standards that we demand of every Ford vehicle.”
The next-gen Ford Ranger is being put through its paces on some of the toughest terrain around the world to not only ensure it’s capable and customer ready, but that it also meets Ford’s own quality, reliability, and durability standards.
“It’s important that our customers are able to rely on Ranger to deliver years of dependable service,” says Willems. “So we’ve gone to great lengths to subject next-gen Ranger to extreme tests — stressing it much more than a typical consumer would — to help ensure it is ready to face everything life throws at it.
“Whether it’s tackling muddy bush tracks, coping with the rigours of extreme tropical weather, towing over alpine passes, or enduring temperatures of more than 50°C, Ranger has to do it all.”
So far, next-generation Ranger testing has covered around 10,000km of desert driving — the equivalent of 1,250,000km of customer driving — and the equivalent of 625,000km of off-road testing at maximum load capacity. Testing is continuing around the world. But even before the road and off-road testing, Ford’s engineers subjected nextgen Ranger to thousands of hours of computer simulations and thousands more physical simulations in labs, covering aerodynamics as well as component and structure durability.
“Computer simulations have helped us speed up development, while lab testing has helped us refine and test specific components, but there really is no replacement for real-world testing to really see how it stands up to years of customer use,” Willems says.
This rigorous testing mimics a variety of realworld scenarios customers might put their pick-up through and it takes place at Ford facilities across the world to ensure next-gen Ford Ranger meets the needs of customers in more than 180 markets.
Packing a lifetime’s use into a test time frame means some of these tests are deemed too rigorous for humans to endure. In those cases, computer simulations and robotics take the place of people in tests that include the extreme ‘squeak and rattle’ rig in which the pick-up’s suspension and whole body is exposed to punishing test cycles that are repeated 24/7.
“Our job as engineers is to translate the customer experience insights into a clear product definition brief for the engineering group, which becomes the absolute reference for engineers. This is particularly important for the Ranger, given we are developing it to be sold across the globe,” says Willems.
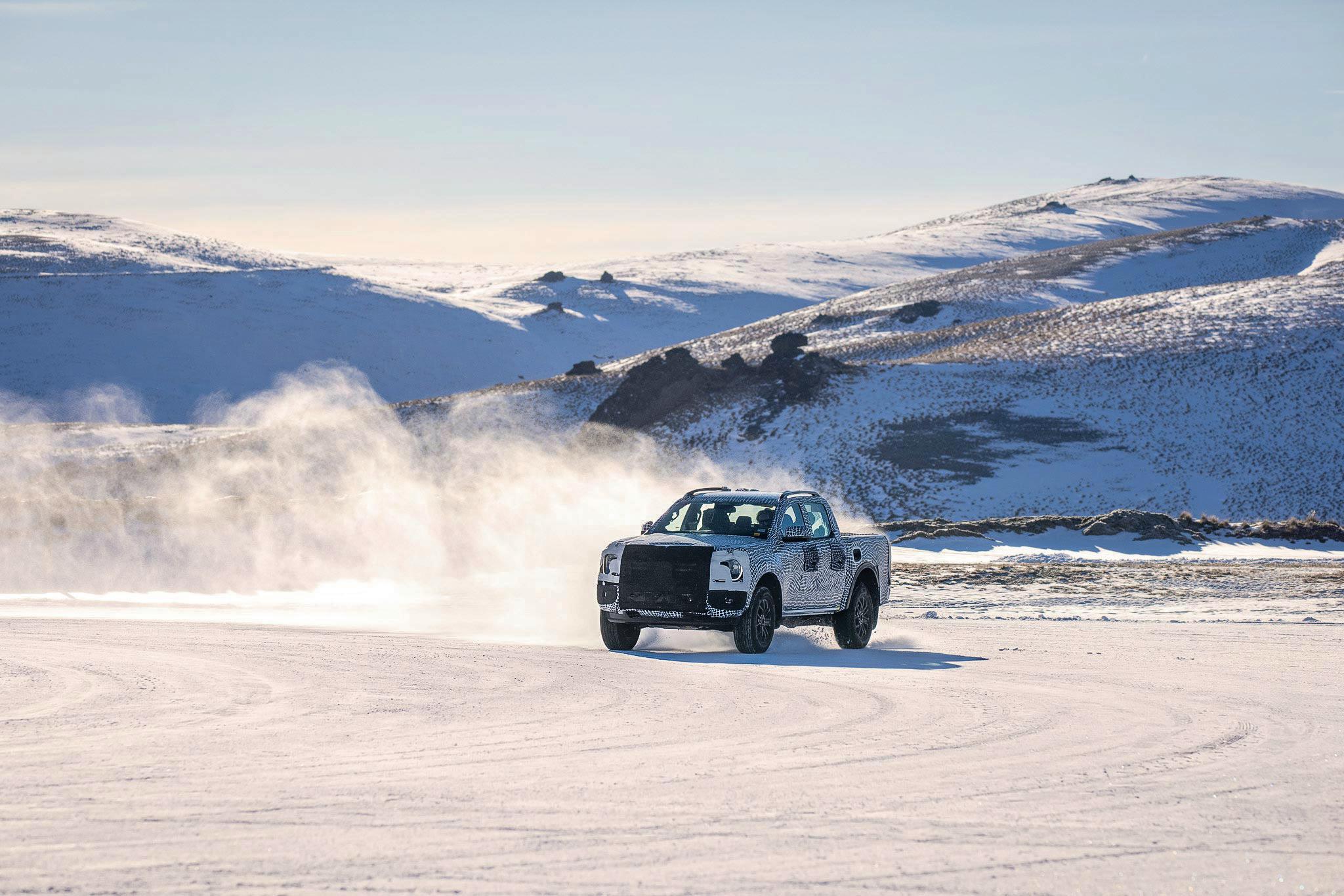
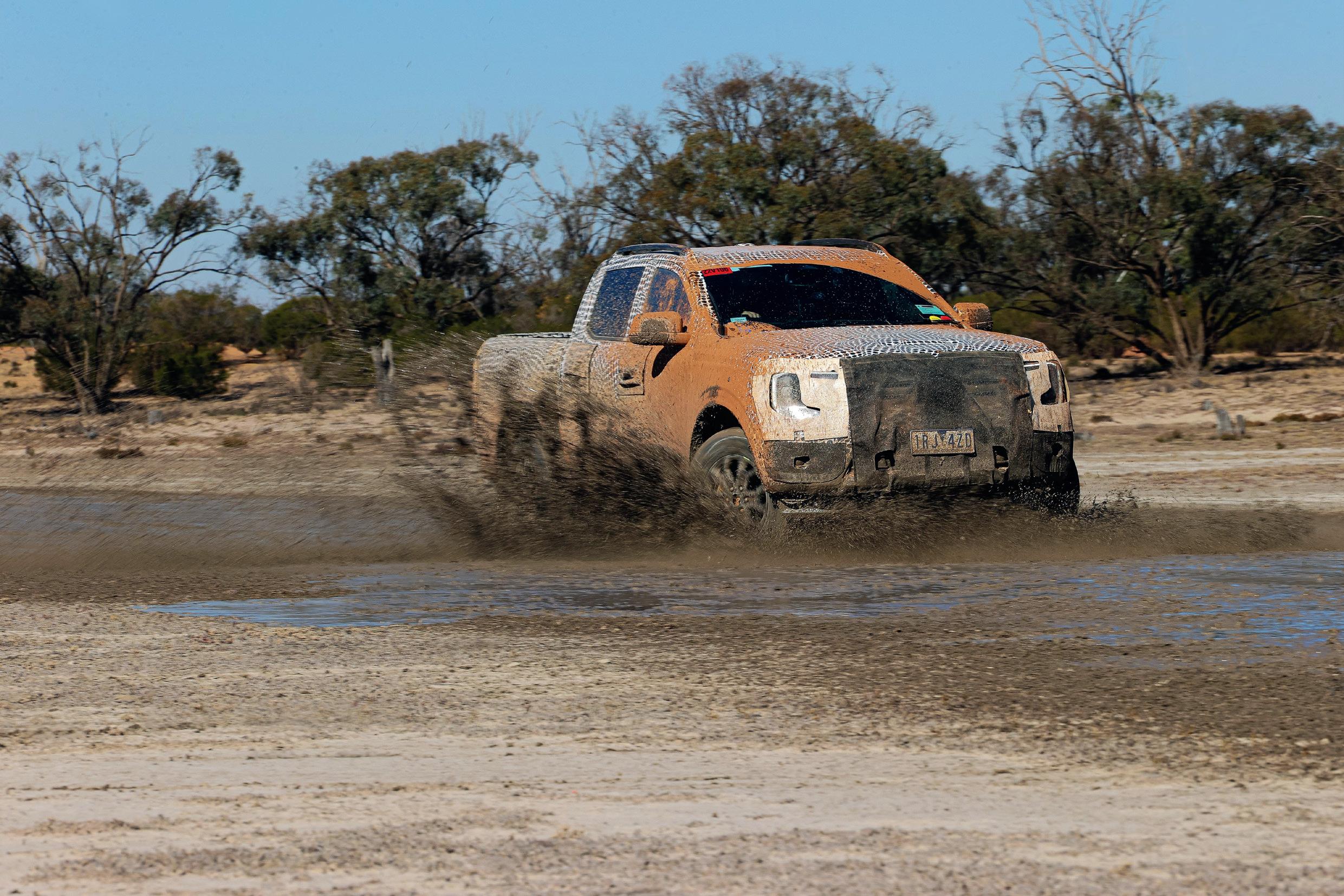