
1 minute read
Innovation solving part availability issues
from Auto Channel 56
by Via Media
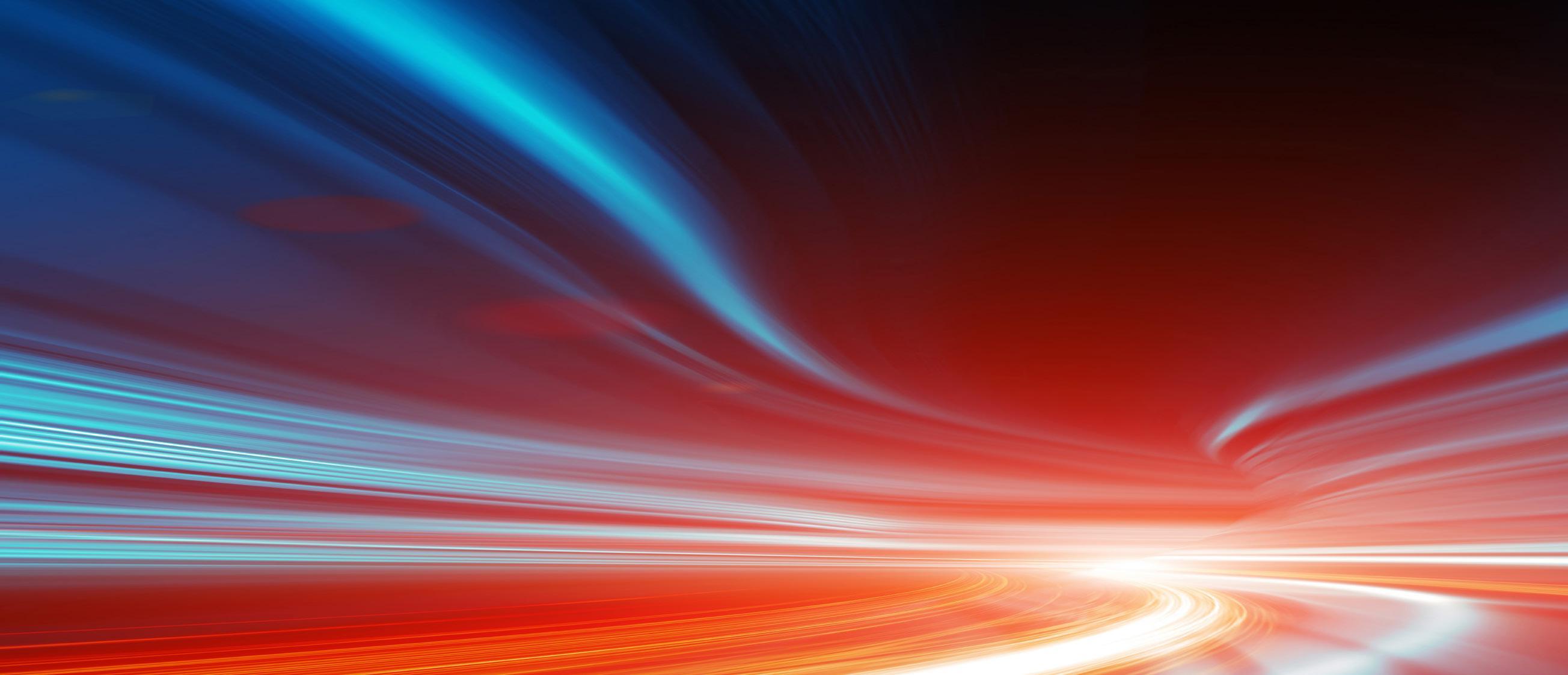
CLUTCH INDUSTRIES’ RESEARCH AND DEVELOPMENT DIVISION HAS A FUTURE THINKING PHILOSOPHY AND HAS BEEN PROACTIVELY APPROACHING THE CHALLENGE OF HOW TO ENSURE WORKSHOPS HAVE IMMEDIATE ACCESS TO THE PARTS THEY NEED IN THE COMPLEX AND SIGNIFICANT CATEGORY OF THE CLUTCH
Advertisement
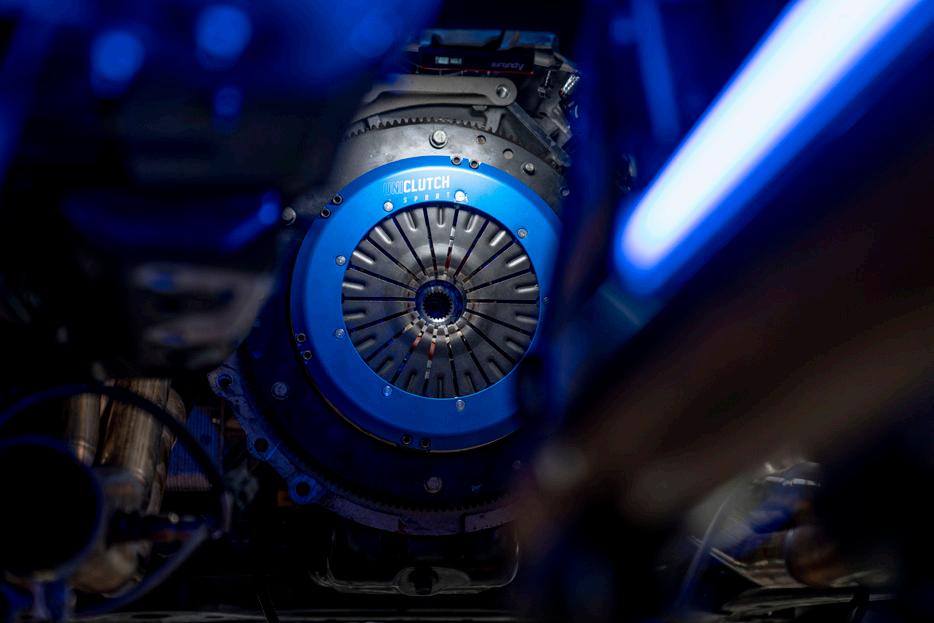
In 2018 a dedicated engineering team at Clutch Industries embarked on a project to decrease clutch SKU complexity (ie. increase car parc coverage with less parts), and reduce installation time for mechanics, while also looking at enhancing performance and quality compared with typical OEM clutches. What they created is a clutch system that replaces thousands of different clutch kits with 20 products. The system is called UniClutch.
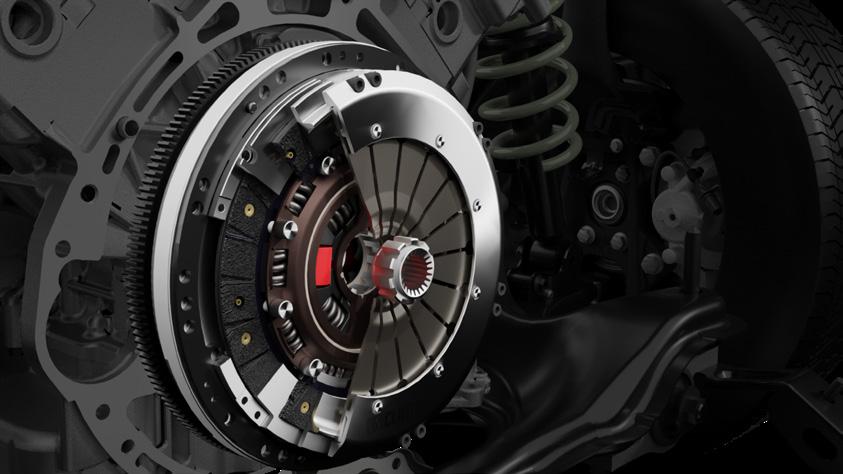
UniClutch works by taking the fitment complexity out of the clutch and consolidating the mechanical interfaces into a fitment kit, which contains its patented multi-fit flywheel mount and patented interchangeable splines. This system allows the sealed pre-assembled clutch to be adapted to various makes and models where traditionally a different clutch would be required for each vehicle.
Justin Batten, Clutch Industries’ general manager of sales, says the clutch system has been in beta testing all through 2022 with the system being fitted to over 50 vehicles in that time. “We’ve been focusing testing on the enthusiast market which has meant we’re not only testing on different vehicles but also testing with different drivers and environments, from tuned street machines to off-road beasts.”
With the development and testing stages of the project now complete, Clutch Industries has started production of the system in their Melbourne manufacturing facility. “In preparation to manufacture the UniClutch inhouse, our Melbourne facility has had a massive upgrade, which included the commissioning of a fully autonomous production line,” Justin says. “In addition to the autonomous production line, we have commissioned a quality control system which is revolutionary in the industry. Every clutch is tested for clamp, bearing load, lift, release, finger evenness, and finger height. All this information is saved to our server and a unique QR code is engraved on each clutch which allows the purchaser to access the specific test results for their clutch. In all, we’ve spent over $1 million modernising our Melbourne manufacturing facility, ensuring that we can efficiently produce the UniClutch inhouse.”
The UniClutch will be officially launched in mid2023 and will be available through Repco and NAPA Auto Parts. For more information, visit uniclutch.com.
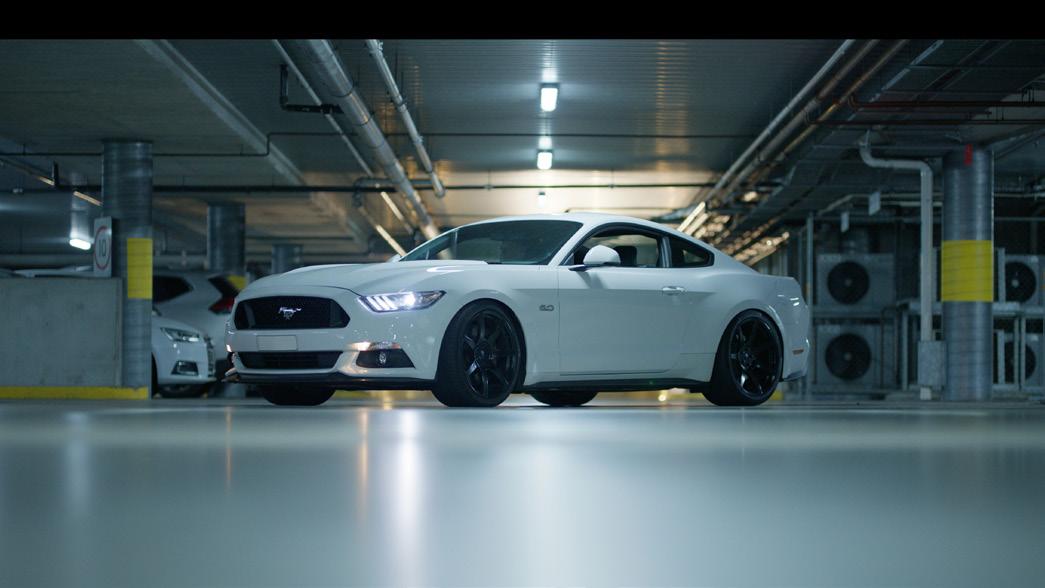
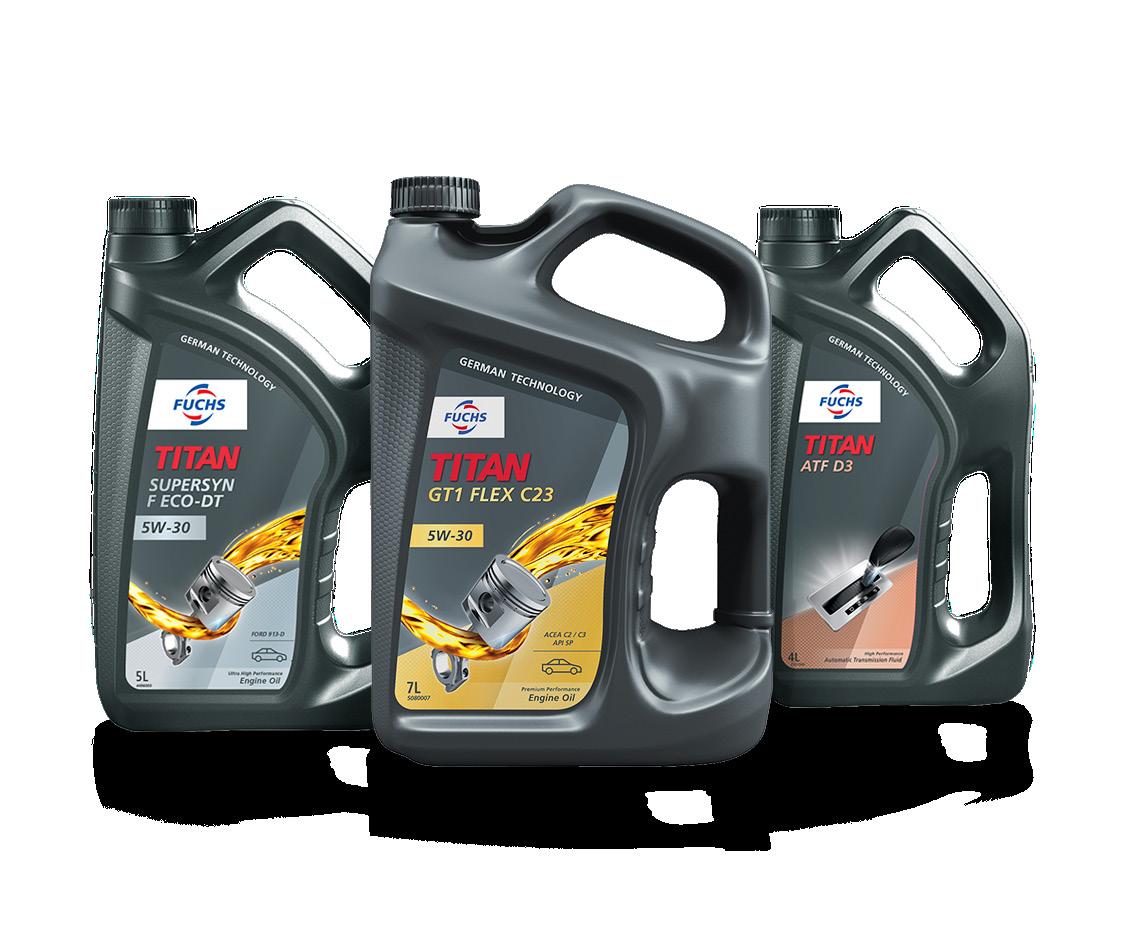