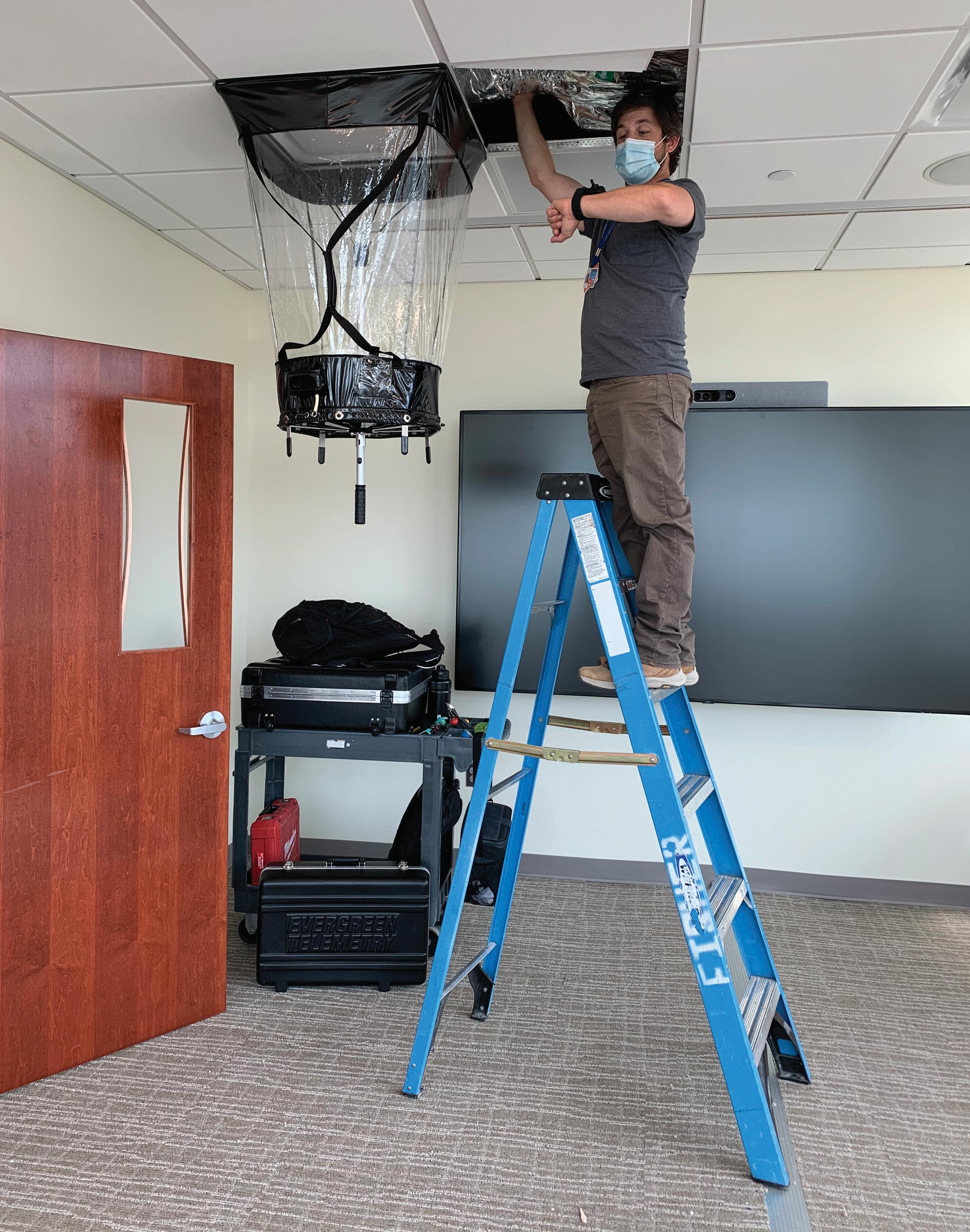
6 minute read
TAB IN THE PANDEMIC
The Sheet Metal Industry Steps up to the Plate
By Deb Draper Photos courtesy of Fisher Balancing
It is critical in any healthcare space to maintain safe, clean air, the pressure in every room precisely balanced to prevent contamination of patients and healthcare professionals. This is the work that testing and balancing (TAB) contractors perform with precision every day of the year, but in early 2020 with the COVID-19 virus sweeping across the globe, they were suddenly working around the clock to flip regular hospital rooms into negative air pressure isolation rooms in preparation for the anticipated surge of infected patients.
“We have a number of experienced TAB contractors in our area that have been out there doing the work in these dangerous times,” says Pete Jenkins, executive director for SMACNA Philadelphia. “Fisher Balancing Company especially has risen to the challenge, having previously worked in many local hospitals and being familiar with their systems.
Matthew Sano, the man behind Fisher Balancing in Williamstown, New Jersey, entered the sheet metal industry 40 years ago as an apprentice in Local 19. “I worked at various shops serving my apprenticeship, and later as a journeyman, taking balancing through the union’s technical school,” he says. “I worked for some good companies, gaining experience in balancing whenever I could.”
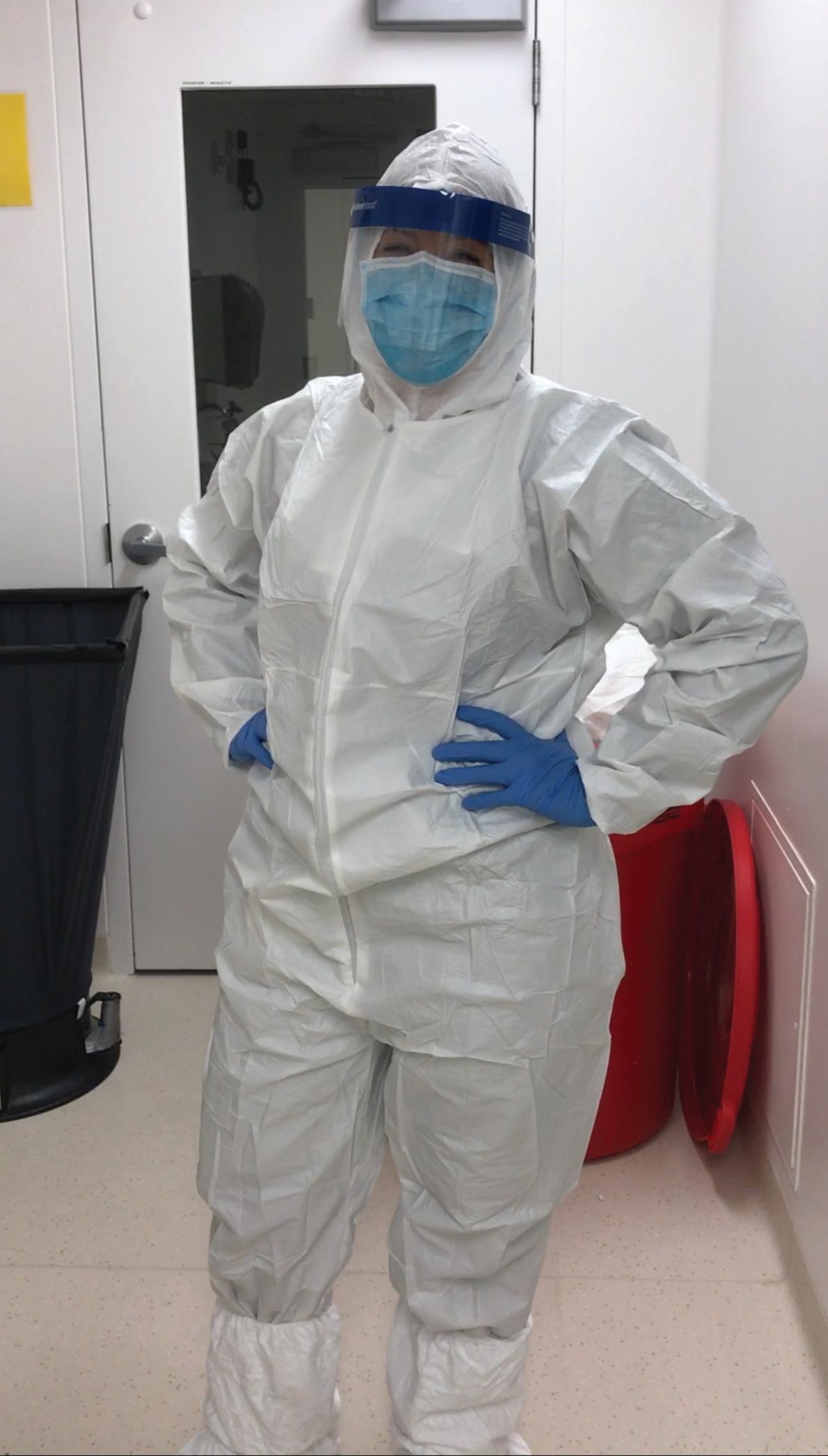
Photo courtesy of Fisher Balancing.
In business now for 21 years, Fisher Balancing delivers accurately balanced HVAC systems, working with building owners, maintenance personnel, engineers, construction managers, and mechanical contractors across a broad spectrum of clients and industries, including medical facilities and hospitals. It relies on the skilled tradespeople at Local 19 for expertise in ensuring every stringent guideline and requirement is met.
Previous relationships with the systems of many health care facilities enabled the company to get everything done in the frantic pandemic timeline with its regular nine-member field team, long hours, and a lot of hard work.
“We were declared an essential service, and although we had to work longer hours, we didn’t miss a beat,” Sano says. “Ours is a very dedicated crew, only taking a day off here and there when necessary to decompress. It was pretty high pressure stuff. In fact, all sheet metal workers across the nation went above and beyond, stepping up to what needed to be done, providing a lot of support to everyone involved in the health service.”
Jennifer Lohr is part of the Fisher team, a Local 19 member, and a sheet metal journeyperson with 13 years of training and experience in testing and balancing.

Photo courtesy of Fisher Balancing.
“This was an emergency situation,” Lohr says. “Your adrenaline is rushing as you use all your skills to get things done, sometimes working 24 hours nonstop. Patients were coming through the health facility presumptive positive, and we had to create negative pressure suites where they waited for test results. If positive, they moved over to the tower where we were also working. At the height of it, we needed to flip a lot of rooms at once, and so it was work until we got it all done.”
Throughout all those hours, Lohr worked with a control contractor to ensure everything operated together. At most times, there was a patient in the isolation rooms where Fisher’s team was working, but they took all the necessary precautions for working in health facilities. “We used face shields and gloves, were constantly cleaning, and following a specific procedure before contact with family at home,” Lohr says.
At Local 19, COVID-19 safety measures suggested by the Center for Disease Control and Prevention (CDC) are stressed for every job site, notes Gary Masino, president and business manager. “We all follow social distancing practices, use hand sanitizers, sometimes wear face shields or even full tie-back suits in workplaces like health care with high exposure risks,” he says.
Sano estimates that during the height of the action, the Fisher Balancing team worked in about 15 different hospitals and converted about 1,500 patient rooms, and although the emergency rush is off, there is more work to be done.
“Now we’re converting rooms back to where they were,” Sano says. “In most of the major systems, we probably had twice as many rooms ready as they ended up needing, but because that work has been done, hospitals can now decide how to be ready for the next crisis. They may decide to have
more rooms prepared for negative pressure to facilitate an easier, quicker response time. With the proper duct and control systems in place, different control commands can more readily make negative spaces available.”
Since many elective surgeries are now reopening and the CDC has recommendations about how that should be done, Fisher Balancing and its skilled Local 19 workforce is busy gathering data on airflow/changes to help facilities understand ventilation and occupancy, time needed between patients, and how much cleaning of the air has taken place. Using that information, facilities can better understand when improvements on existing equipment are necessary.
Jenkins believes balancing and testing is going to be crucial in terms of making sure health, retail, and educational buildings are safe moving forward. “One lesson we’ve learned is that these kinds of public spaces are going to need newer, more effective air filtration systems—especially the negative pressure rooms, being able to switch them back and forth,” he says. “The balancers are a fairly specialized group, and I think there will be much more demand for their skills in the near future.”
Masino agrees that sheet metal will be one of the few trades that will see work opportunities coming out of the pandemic. “Maybe it will be putting ultraviolet lights inside the units, or developing portable systems to depressurize rooms quickly,” he says. “There are many new ideas out there, and a lot of talk about how to better tackle the whole clean air situation.”
Universities and schools are looking for information about ventilation and for data based on occupancy and spacing, Sano explains. “We’re also partnering with the casino industry. Everyone is looking at how to be better prepared, not only for now, but in the future. It’s a big challenge.”
Lohr anticipates new ways of approaching building design in the future. “There was a big push for LEED, but with COVID, we had to transition a lot of systems from being economical and efficient to 100% air, 100% exhaust, all outside air,” she says. “How do we create a LEED building that can transition to higher energy use to keep the virus out of the building? It’s going to be interesting.”
Lohr feels TAB is sometimes overlooked as part of the sheet metal industry. Ductwork and air systems are visible, but few think about how the ductwork is set and tested and balanced after the fact.
“It is rewarding work, and I am extremely proud of what I do,” Lohr says. “This is a great career, and I recommend it to anyone considering coming into the trades who wants to be a problem-solver and a trouble shooter making the air safe, more comfortable, and more efficient.” ▪
From her desk in Calgary, Alberta, Deb Smith writes for trade and business publications across North America, specializing in profiles and stories within the hospitality, food service, mining, recreation, and construction industries.