
4 minute read
SMACNA and SMART Building Boston Together
SMACNA and SMART Building Boston Together
By / Sheralyn Belyeu
Wayne A. Greenwood, president of JEC Service Company in Boston, Massachusetts, built his business on a simple idea. “He believes that if people are looking out for each other on the job, they can do anything,” says Sean O’Keeffe, JEC project manager. “When he’s hiring, Wayne isn’t looking for superstars. He wants employees who will do the right thing when no one is watching, people who are organized and have a sense of ownership. He looks for people who are respectful of others and professional, people who act like ladies and gentlemen.”
Local 17 Executive Board Member Mike Mathews is a field foreman for JEC. Mathews keeps an eye out for apprentices who fit Greenwood’s vision. “Wayne is picking a team that works well together and with other trades. That’s more important to him than being the most technically polished,” Mathews says. “He wants people who are going to help each other out in a pinch.”
“Our contractors are always in control of their workforce needs,” says Bob Butler, business manager for Local 17. “They can choose the employees they want.”
Hiring through the Local guarantees that every single craftsperson has the technical skills needed for success. “In the building trades, union sites are nearly five times more productive than non-union sites,” Butler says. “Our training program plays a big role in these partnerships. Local 17’s five year U.S. Department of Labor-certified training program gives workers expertise in every aspect of sheet metal fabrication and installation, from stainless steel to the fabrication and installation of heavy metals and tanks. We also provide ongoing skills training for journeypersons at no cost to contractors.”
Training begins in JATC classrooms and continues on site. “The experienced craftspersons give apprentices a little leeway in the field as they show them how to do the harder things,” says O’Keeffe. He sees mentoring each apprentice as an investment in the future.
“We hope these apprentices will stay with us and work their way up through the company. They do a good job.”
JEC isn’t the only company that recognizes the value that Local 17 labor brings to the industry.
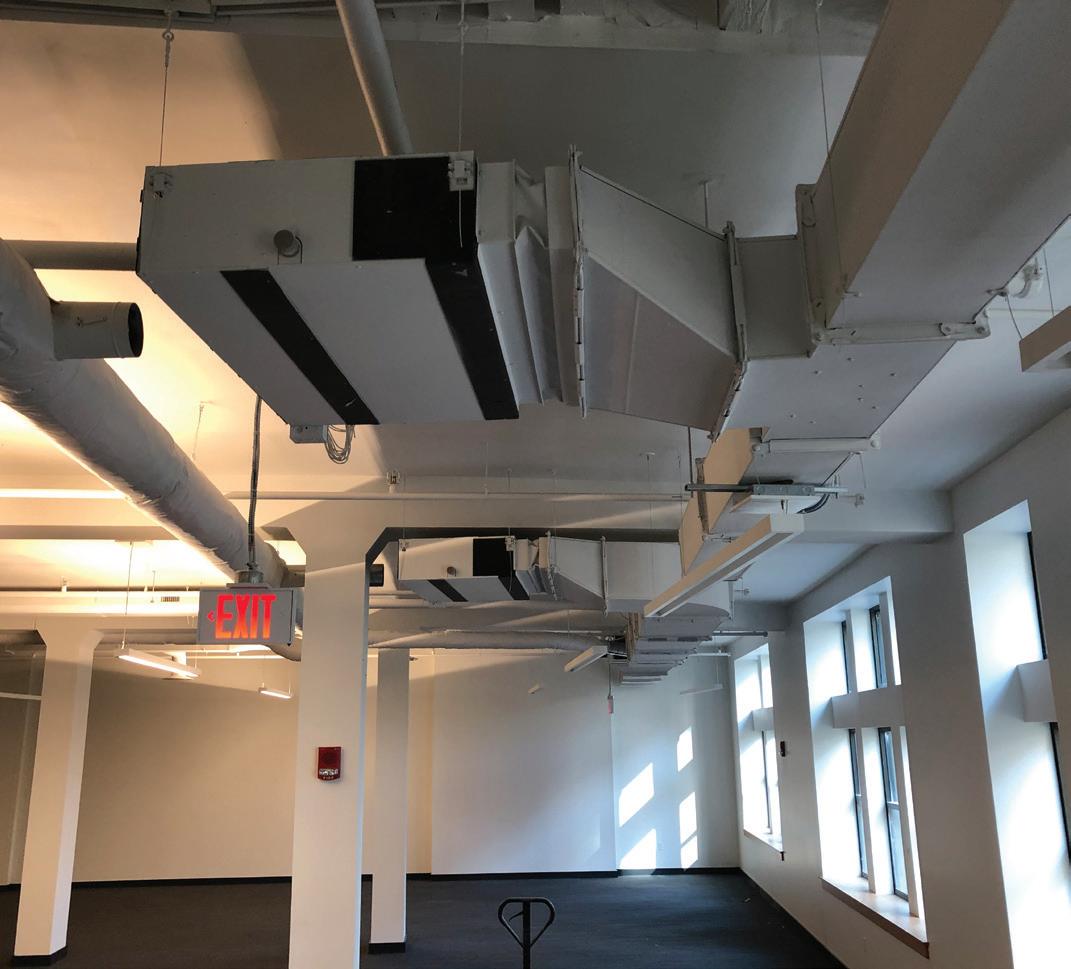
“Our partnership with SMACNA Boston has won and built some of the most competitive jobs in the region, including the Harvard University Science Center, Fenway Park, Gillette Stadium, Massachusetts General Hospital, and Boston Convention and Exhibition Center,” Butler says. “Industry-leading wages and benefits support a highly-skilled workforce. That means the job gets done right the first time, which saves contractors money, increases efficiency, and helps the bottom line.”
Boston is one of the oldest cities in the United States and also has the fastest job growth in the country. Young adults are flooding into the region in pursuit of education and work opportunities. This growth brings unique challenges as modern businesses move into historic buildings. “Our current project is in a building with a wooden frame made of timbers,” says Mathews. The demolition uncovered lumberyard markings that are about 150 years old. “We still don’t know the intended purpose for some of the structures we found, like the round metal pillars on the roof.” The unfamiliar construction techniques and materials demanded a fresh approach. “We’re used to concrete and steel construction, so we had to think through every step.”
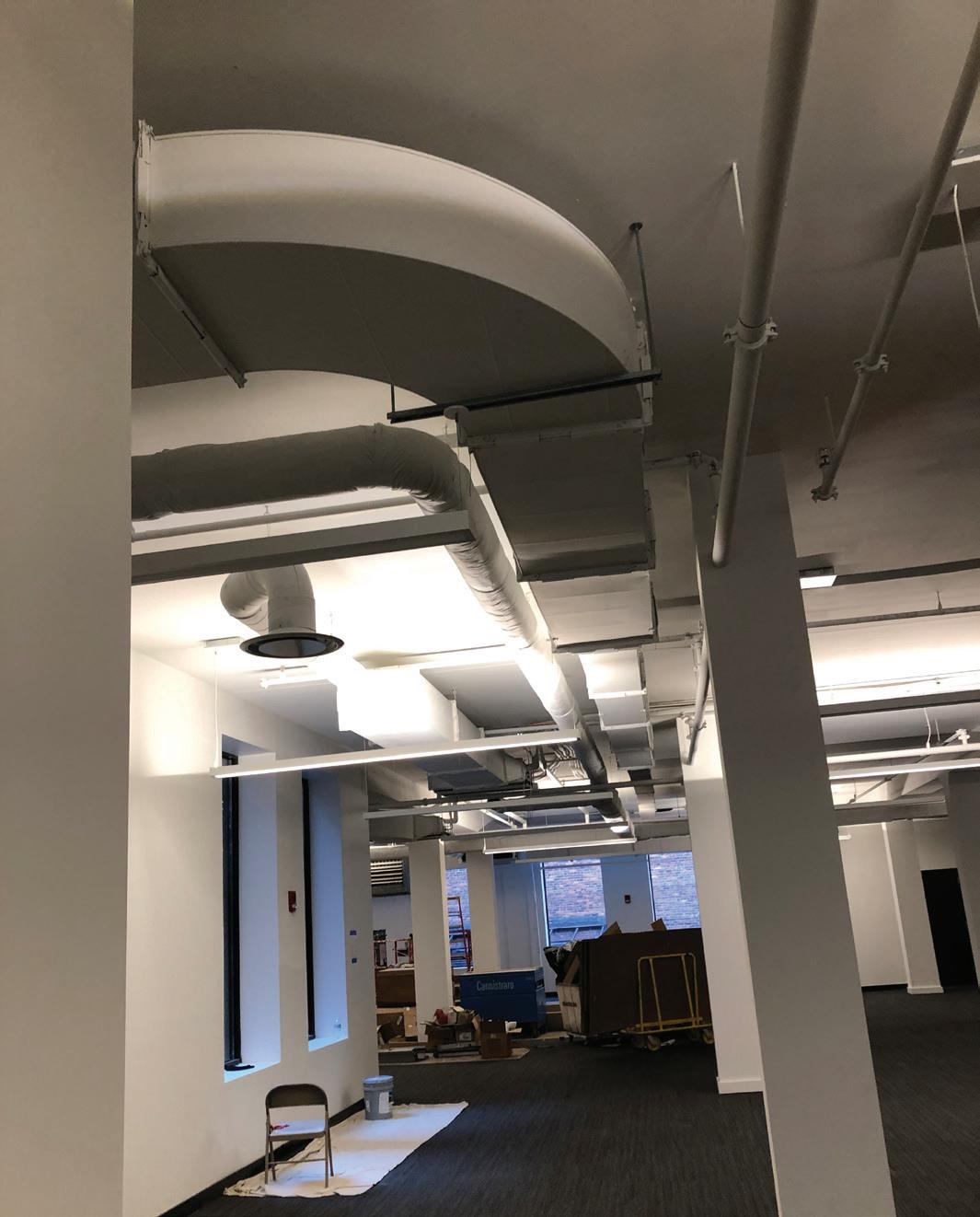
The wood brought another complication; to reduce the risk of fire, Boston fire codes require drywall throughout the interior of all-wood buildings. “The drywall makes the job tougher because we have to layout earlier in the process,” says O’Keeffe. “Accurate planning and measuring are even more important than usual. We make sure we do it right the first time, because we can’t do it twice.”
Greenwood started by sitting down with Mathews, O’Keeffe, the pipefitters, and a few people from the office to share ideas. “To succeed, include the team you have available,” advises Mathews. “That means the office, the apprentices, and the journeymen. Brainstorm together when you hit problems. Troy Anderson is a third year apprentice. He was there for the initial demolition and layout, and he had some very good ideas. Mark Zalis joined us when it was time to install the manifolding, and he also offered good ideas.”
Based on input from the entire team and experience from a prior renovation, Greenwood determined that the solution was to install steel supports for the ductwork before the drywall went in and to clip on afterward. “The whole job is hanging off of eyebolts,” Mathews says.
Tight coordination between the field foreman and the office continues now that the project is underway. “I see Sean O’Keeffe every Tuesday and once or twice during the week,” Mathews says. “He often attends our job-site meetings and will pop over before the meeting if he has a schedule conflict. He’s always available when I want him.”
“Mike has everything under control on the site,” O’Keeffe explains. “He doesn’t need me to run job-site meetings, but he might require more people, materials, or equipment. Sometimes questions come up about ship dates, dimensions, or gas locations.” Mathews and O’Keeffe coordinate details through Procore. “We talk about the project every day. Mike and one of the foremen in the shop are also testing a new app to manage trucking and shop time. We are always trying out new platforms that might improve communication.”
Mathews attributes JEC’s success to the culture Greenwood has created. “We all work as a team,” he says. “I came to JEC for a company that values the employees. I’ve been in sheet metal for 30 years, and this is the best working situation I’ve ever had.” ▪
A Colorado native, Sheralyn Belyeu lives and writes deep in the woods of Alabama. When she’s not writing, she grows organic blueberries and collects misspellings of her name.