
6 minute read
From Compliance to Care
Signatory contractor ACCO Engineering Systems and Local 105 commit to an ongoing safety revolution
By / Robin Brunet
Even for a company of ACCO Engineered Systems’ capabilities, the new Inglewood Stadium (aka the SoFi Stadium), three miles from Los Angles International Airport, was a construction project with huge logistics that required an unwavering commitment to onsite safety. Clearly, it needed more than the usual checklists and procedures.It was not a problem because the company’s safety culture has evolved from compliance to care thanks to its ongoing partnership with Local 105.
Altogether, the $5-billion facility for 70,240 spectators required 2.1 million pounds of ductwork, and at peak, 120 signatory sheet metal workers were on site. Because SoFi is under LAX’s flight path, two-thirds of the facility was constructed below grade, requiring crews to install 46 different air handlers and numerous split systems in a moat-like perimeter.
Donovan Seeber, ACCO’s vice president of corporate safety, recalls, “SoFi, which commenced construction in 2016, was huge and challenging, and we were still actively working on site when COVID hit. This obliged us to quickly add another layer of safety to protect our crews and allow work to continue with minimal disruption.”
Ultimately, two full-time onsite safety experts and 22 full-time safety professionals available by phone helped ensure that virus protocols were strictly followed, and that the 250,000 personhours spent on the project overall were without incident.
With over 4,300 employees in 30 offices and four fabrication plants, Pasadena-based ACCO is the largest mechanical contractor in the western United States and the biggest employer of sheet metal workers on the United States west coast.
It could be argued that everything ACCO does is big, including its approach to safety. But it hardly operates in a vacuum: Seeber credits Local 105 for an on-going collaboration that has helped evolve ACCO’s safety culture in a fundamental way.
“We’ve gone from being a company with a solid culture of compliance to a culture of care, which makes us far more capable of sending our work crews safely home to their families at the end of every day,” he says. “That’s because instead of just following regulations, every one of our staff is a self-motivated safety champion.”
As for ACCO’s relationship with Local 105, Seeber says, “We regularly discuss training issues, how to better prep people, consult with them before making corporate changes, and work together on projects like SoFi Stadium. It’s a great partnership.”
It’s also one with a long history. “ACCO, our Local, and Local 104 go back 80-plus years, and today it represents a large portion of our 6,800-strong membership, so we share their concerns and goals,” says Local 105 President Luther Medina. “Considering ACCO has such a large workforce, it has always been ahead of the curve in safety, and the SoFi project is a good example. When COVID hit, ACCO was one of the very first companies in California to distribute face coverings to its crews—so fast, in fact, that it became a union issue, with us telling each other, ‘We’ve got to match that speed.’”
Medina laughs at the memory of scrambling to source masks. “You could say we inspire each other,” he says. “ACCO’s safety programs dovetail and complement ours, and it’s not uncommon for one party to incorporate measures that the other has developed.”
Seeber loves discussing the particulars of safety, and his passion is understandable. He began his career as a medic in the oil and gas sector and dealt first-hand with more than his fair share of onsite accidents. “During that time, I was introduced to occupational health and safety, which I never knew existed and was fascinated by,” he recalls. “I quickly devoted myself to ‘the cause,’ so to speak.”
Seeber was recruited by ACCO to develop a separate safety program for its oil and gas division, and this led to him kicking the company’s overall program into high gear in 2010 with a robust investment into safety teams and resources. Today, ACCO’s safety provisions are delivered by directors for the company’s north and south regions, 20 safety professionals in management, and 10 site-specific professionals.
But the intent wasn’t restricted to beefing up infrastructure. “When I joined the company, there was definitely an impressive safety culture, but like so many other companies it was focused on teaching compliance,” Seeber says. “Given that we had all the components in place, I felt there was an opportunity to develop further into a culture of care. In other words, instead of work crews simply following orders, they would be motivated to be safety champions. And this would very much tie into the Locals’ philosophy of brothers and sisters looking out for one another.”
The shared goal was to ensure each member of either organization would come to work viewing everything through the lens of safety. “It’s a great approach that, in addition to its obvious benefits, boosts productivity and keeps workers’ comp rates down,” Medina says.
Seeber concedes there was no magic recipe for developing the culture of care—just lots of work over a long time-period. “It takes years and starts with management adopting a leadership attitude rather than a punitive attitude,” he says. “For example, instead of managers quoting clauses and subsections to work crews, they engage everyone in a discussion about specific site conditions and how the crew can get through the day safely.
“With this approach, checklists are also simplified, and instead of berating someone for violating a regulation, managers explain why the regulation is important and the hazards that can result from not following it.”
The shift from compliance to care has been painstaking and must be constantly reinforced. Safety inspectors typically visit a site, not with a clipboard in hand, but to roam around and engage in friendly conversation. “Our crews know all the rules, and our inspectors are there to learn the specifics of what’s going on and determine if anything further can be done to make the job go even more smoothly and safely,” Seeber explains.
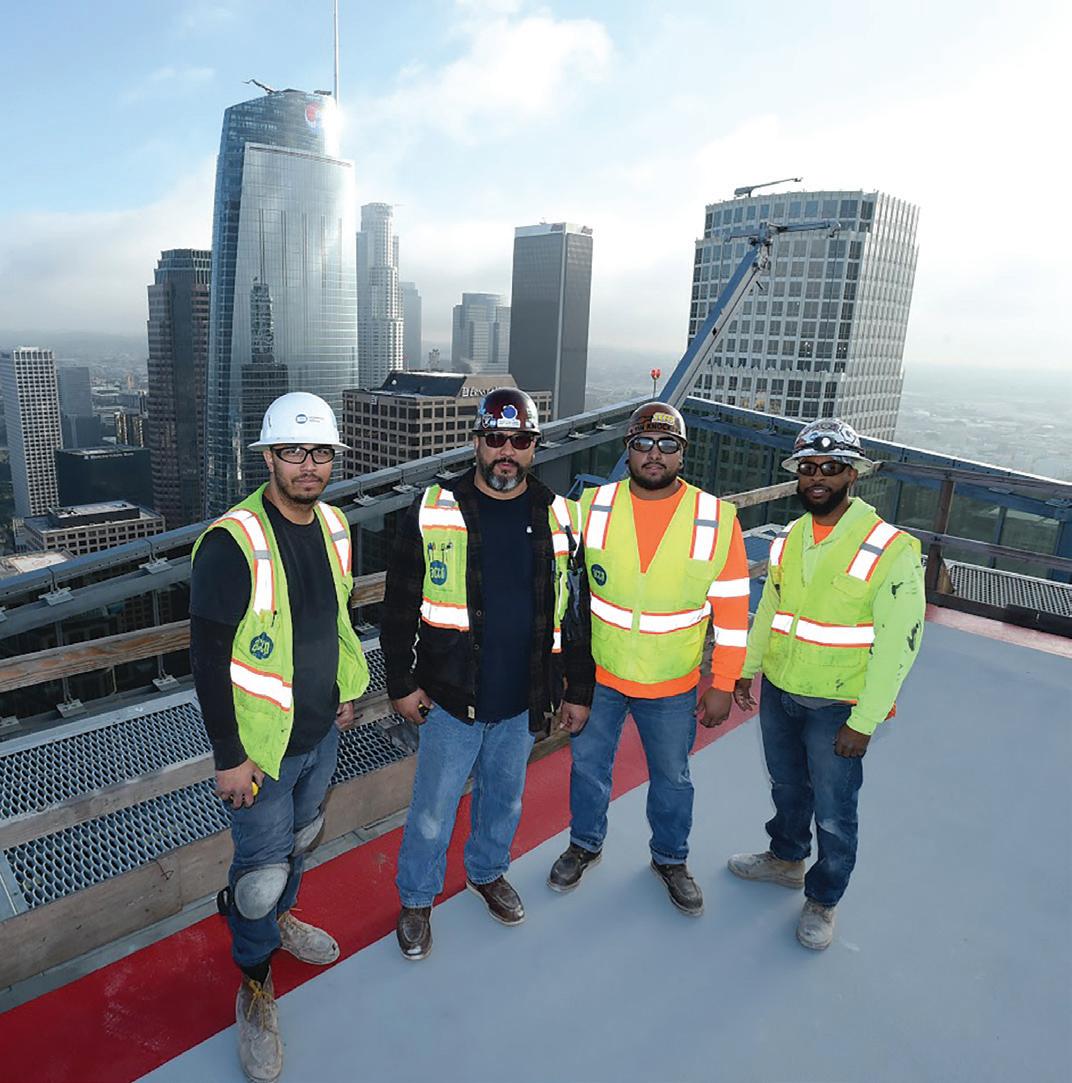
This culture of care has yielded impressive results. For the past five years, ACCO’s Experience Modification Rate (EMR, the rate used by insurance companies to gauge the cost of past injuries and future chance of risk in order to calculate worker compensation rates) has been below .5—anything below the average rate of 1 is an impressive achievement by industry standards.
The question is, can safety in the future go beyond a culture of care? “In a way, yes,” Seeber says. “We recently embarked on making our shared culture of care an integral part of our leadership program, of building it into every component of this company and our workforce rather than restricting it to a standalone department. While this is a multi-year task, we really think it’s a model of what safety in the workplace could be.”
For his part, Medina is excited about ACCO’s ongoing evolution. “It’s gratifying to see Seeber and his colleagues create healthy environments,” he says. “They’re very much part of the industry shift of safety practices being perceived as a strength instead of a burden.”
One thing is assured: Local 105 will continue to help ACCO achieve its goals.
“Local 105’s doors are always open to us, as ours are to them, and we’re always crossing through them whether it’s with an idea to share or a situation to resolve,” Seeber says. “We really are partners in the most productive sense of the word.” ▪
Robin Brunet’s journalism has been published in over 150 magazines, newspapers, websites, and other media across Canada and the United States since 1982. He is also the best-selling author of two books: Red Robinson: The Last Deejay and Let’s Get Frank.