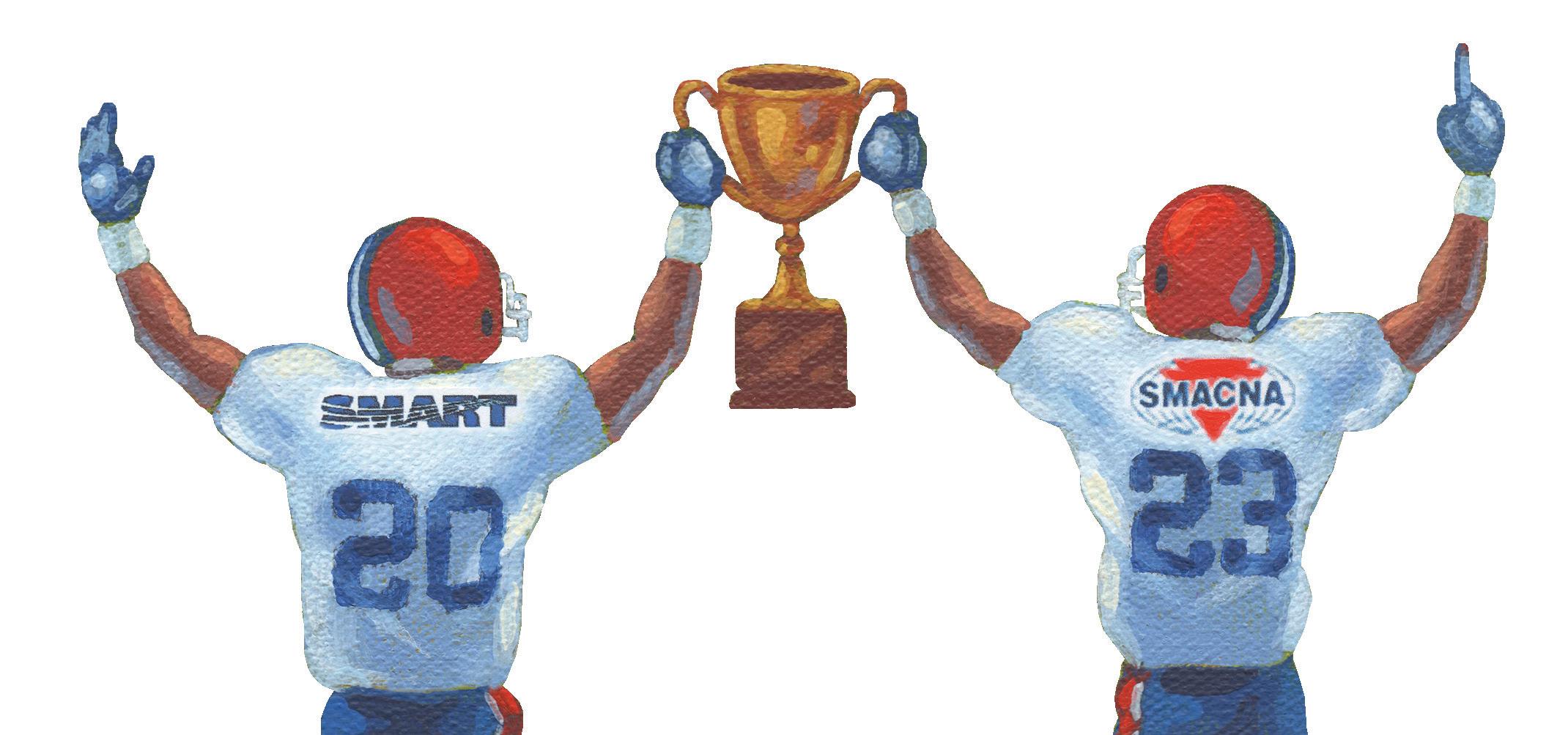
6 minute read
PLAYING THE LONG GAME
By / Robin Brunet
In this post-pandemic climate of pent-up demand, and despite inflation and supply chain issues, stadium projects are big business in many jurisdictions of the United States and Canada. Indeed, they are a boon for SMACNA contractors and the SMART workforce.
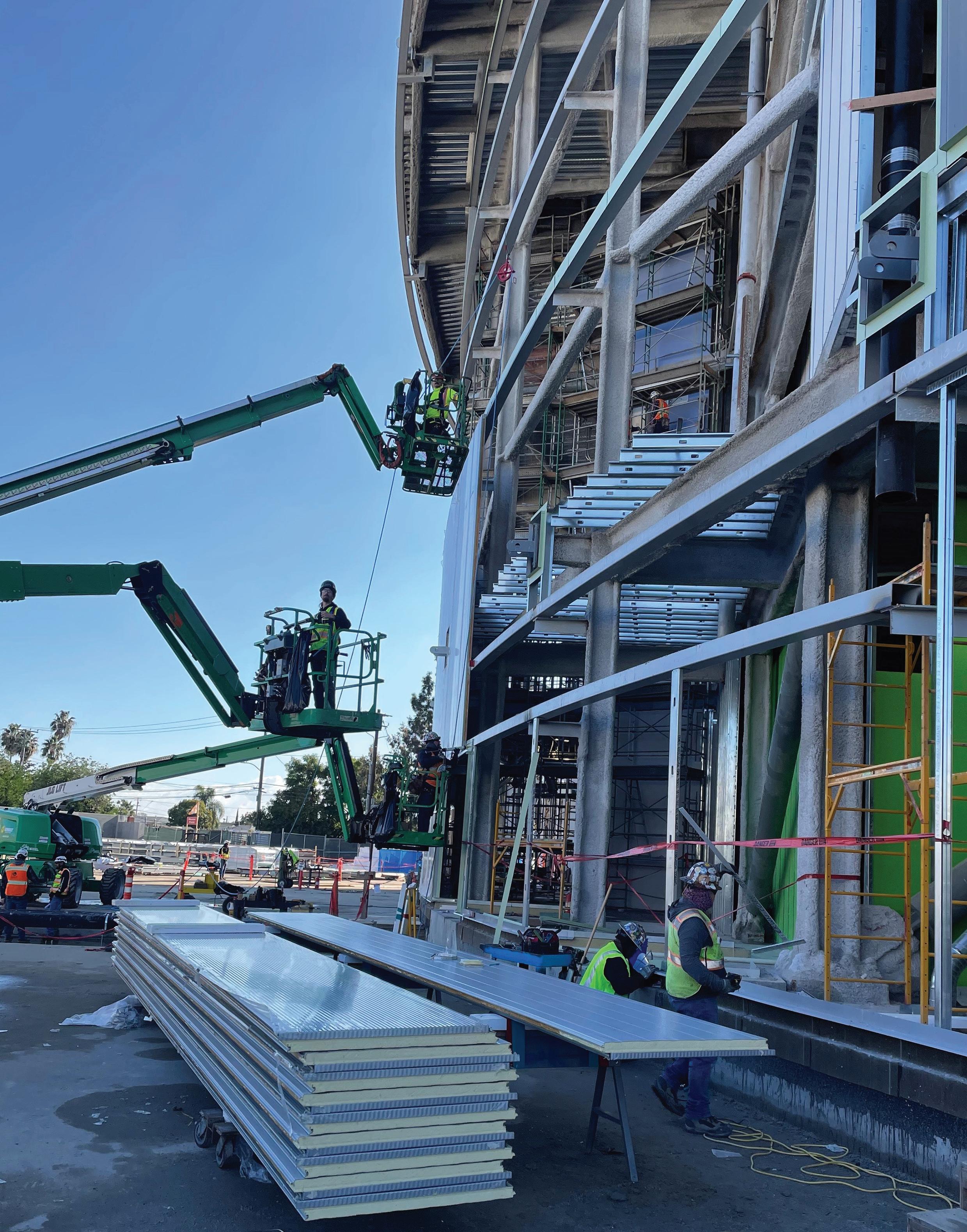
Steve Hinson, business manager/president of Local 105, which serves various Southern California counties, including Los Angeles, says,“Our members have been involved in at least five major projects during the past five years, including SoFi Stadium in Inglewood and, more recently, the adjacent Intuit Dome, which broke ground in 2021. Whenever we hear of stadiums builds, we get right in front of the decision makers to make sure the appropriate humanpower is deployed.”
L. William Zahner, president and CEO of A. Zahner Co., says that stadiums mean long-term employment for both architectural and mechanical sheet metal crews. “Securing these projects takes effort and can be frustrating, but it’s well worth it,” he says. He adds that the high-profile nature of stadiums allow the sheet metal trade to show the world what it can do.
ACCO Engineered Systems sales manager Matt Taylor agrees that stadium projects—including SoFi, the Stub Hub Center, and the Crypto.com Arena—are essential for his company’s success. “Work at SoFi began in 2017, lasted three years, and enabled us to use some of our most experienced people, as well as hire locally,” he says.
That 70,000-seat stadium was designed by HKS Architects, is covered by a canopy of translucent ETFE membrane and 34,789 unique, perforated panels courtesy of A. Zahner Co., and includes a 5,000-ton central plant, over 1.7 million pounds of sheet metal ductwork, and 4,000 tons of VRF systems from ACCO.
SoFi and similar projects demonstrate that stadiums demand the absolute best sheet metal design, fabrication, and installation. “Not only are they massive, but also they are enormously complex,” says SMACNA Western Washington Executive Director Julie Muller-Neff. “Plus, as energy efficiency takes on new levels of meaning in the construction sector, the standards to which stadiums are built are rapidly evolving. Climate Pledge Arena in Seattle is a prime example.” The 740,000-square-foot, multipurpose facility completed in 2021 is the world’s first International Living Future Institute certified zero carbon arena.
SMACNA-Western Washington’s Hermanson was the mechanical contractor, using Local 66 crews to help create a stadium powered exclusively by renewable energy, including on-site and off-site solar. Plumbing, fitting, and sheet metal requirements—including installation of 1 million pounds of sheet metal and 200,000 linear feet of pipe—had to be fulfilled in an existing arena that was completely gutted except for the roof.
With the coming surge in the renovation and construction of sporting venues—including Highmark Stadium in New York, the Rogers Centre in Toronto, and stadiums in Kansas, Nashville, and St. Louis—what is the recipe for procurement of these projects and their construction success?
“In the context of sheet metal, it is vital to have skilled labor available,” Zahner says. “Since I can state confidently that my company has the skills and the volume to get big jobs done on time, I get my foot in the door.” Another advantage Zahner offers is that the company manufactures everything it installs.
“ACCO has helped build major sport facilities along the West Coast by working with trade partners and engineering groups to bring flexibility into the mix, which is crucial because these facilities have diverse systems and frequent sequence changes,” Taylor says.
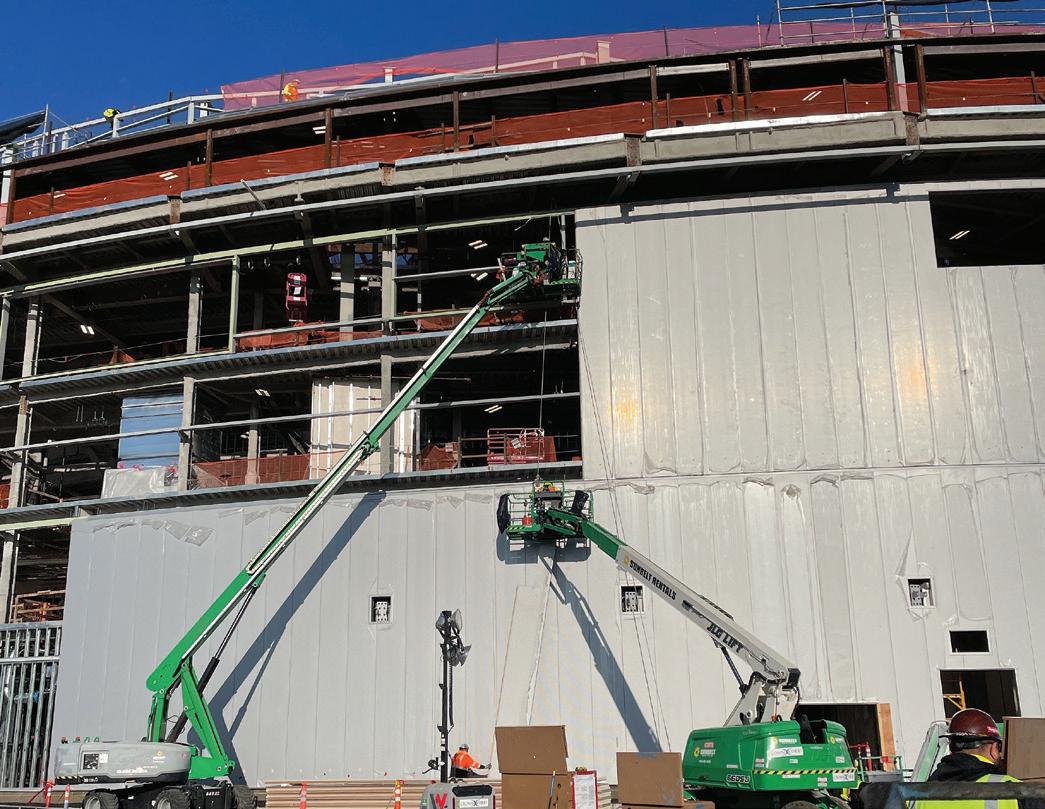
Maintaining well-trained crews is another important part of the procurement process, Zahner emphasizes. “The number one consideration is safety training, as a lot of work is conducted at great heights—and any construction manager will be scrupulous about this,” he says. “OSHA certification lays the groundwork. SoFi crews were trained to either OSHA 10 or 30 standards, but it’s also indispensable to have ITI training for crane work, rigging, lift planning, and more.”
Taylor echoes Muller-Neff’s observation that training must address stadium design that is evolving to accommodate more sustainable systems. “For example, a lot of new arenas require flexible duct ‘socks’ that wrap around the entire perimeter of the facility,” he says.
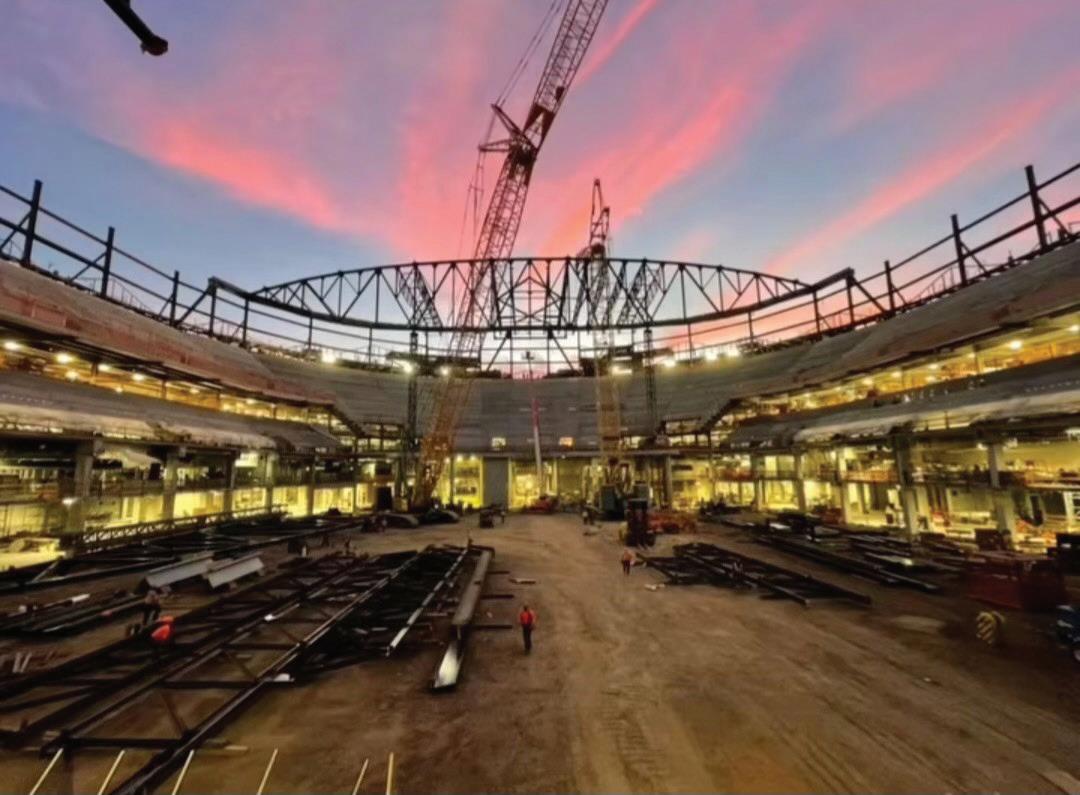
“As more and more stadiums are built to the standards of Climate Pledge Arena the more intensively crews will have to be trained in order to secure such work…Goals—such as net zero carbon—affect everything from mechanical overall down to the fasteners of building envelopes,” says Western Washington Sheet Metal JATC’s executive administrator Jeff Reinhardt. “Fortunately, organizations such as ours contribute to our workforce being one of the best trained in the industry.”
However, according to Zahner, even the most experienced sheet metal company with the most thoroughly trained crews will not prevail without productive labor-management relations. “Good union relationships enable me to get crews at size in any jurisdiction, not just my home base of Kansas City,” he says. “Locals want projects to succeed, and this enthusiasm disseminates into the workforce.”
Muller-Neff agrees. “Good relations are essential in stadium work because these projects have all sorts of rules and regulations that require the expertise of both parties to find solutions—and to pivot quickly when required,” she says.
There’s no magic to fostering great relationships, just the requirement of forthrightness. “Open and honest communication between the two parties is important,” Hinson says. “At Local 105, my predecessor Luthor Medina pushed for it very hard, and we continue to emphasize it because we’re well aware that to get anything done we need to be on the same page.”
The Local 66 JATC is a testament to the benefits of labormanagement cooperation. “Our mission statement is to bring both parties together for the development of a highly skilled and competitive workforce for our evolving sheet metal industry,” Reinhardt explains. “With six members from labor and six from management governing our activities, we’re able to continue providing training that is specific to many areas of industry, such as lift certifications for stadiums.”
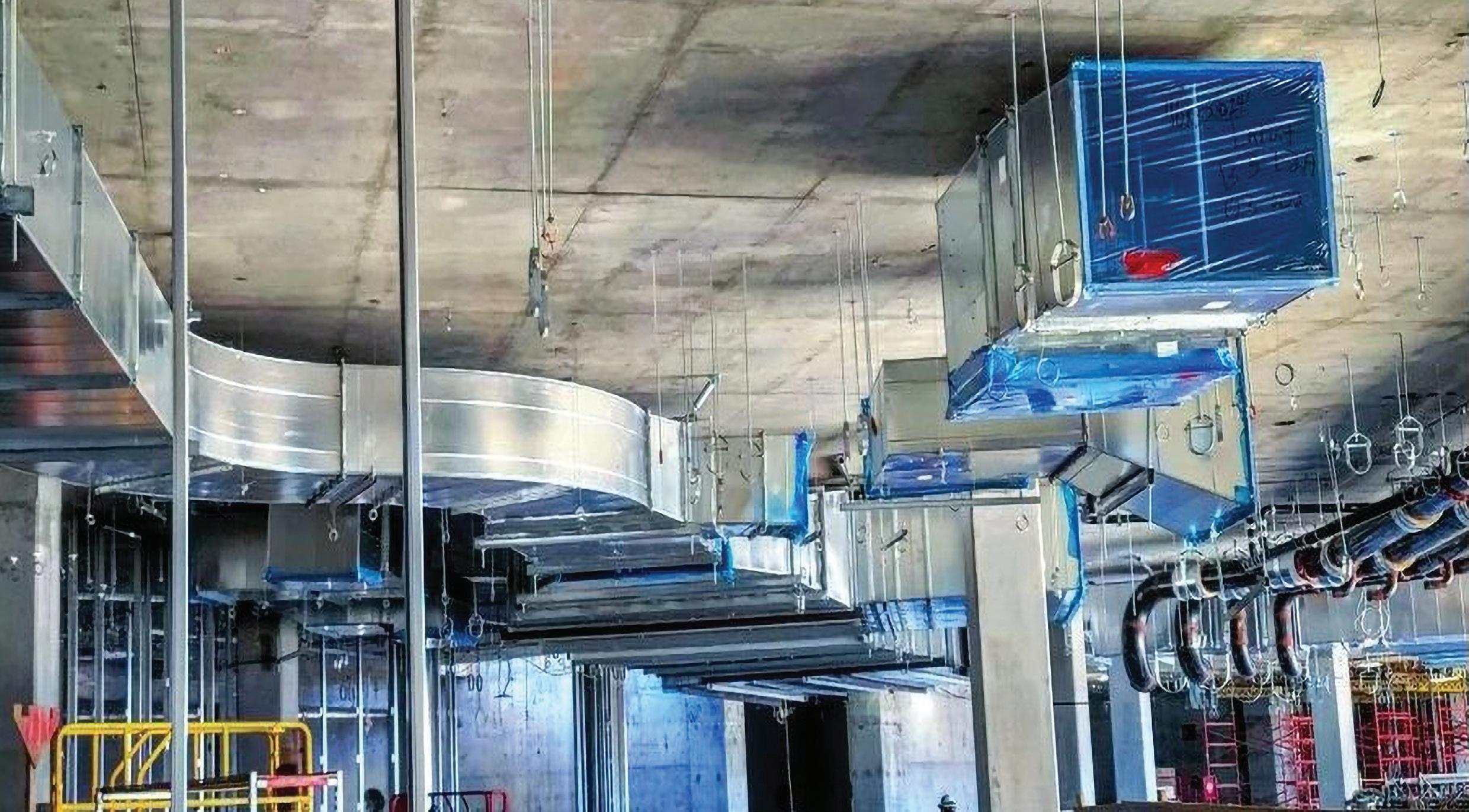
Zahner echoes the sentiments of his colleagues. “When all the elements are in place, stadium work fulfills a lot of objectives,” he says. “It’s a showcase for sheet metal specialists. It gives young talent considerable training and on the job experience, and it’s a great way for labor and management to come together.”
“And last but not least, the fact that our work will be admired by stadium patrons for decades to come is enormously fulfilling and will compel us to continue seeking such work, well into the future.” ▪
Robin Brunet’s journalism has been published in over 150 magazines, newspapers, websites, and other media across Canada and the United States since 1982. He is also the best-selling author of two books: Red Robinson: The Last Deejay and Let’s Get Frank, as well as the upcoming The Last Broadcast.