
5 minute read
Obtuse Angle
PROJECT PROFILE
Evidence that HVRF works can be drawn aplenty from
Advertisement

Sirus Group has offices in Cork and Dublin and has been providing services to the HVAC, electrical and controls industry since 1988. It has grown considerably since those early days and now employs over 120 staff specialising in the delivery of critical environments to the pharma, biotech and data centre sectors. It also provides turnkey, maintenance and FM services across a wide range of equipment and a diverse customer base including industry, education, retail, hospitality, healthcare, life sciences, airports, etc.
When considering the deep retrofit and renovation of an old industrial unit in Citywest approximately four years ago, Sirus set out to establish The Well, a comfortable and healthy environment for workers that would also enhance their sense of well-being.
Constructed in the late 1990s, the challenge was to bring The Well to life as a state-of-the art, Class 1, smart, comfortable working environment. Expert sources, such as CIBSE Guide A: Environmental Design, helped shape a holistic approach to the retrofit ensuring a sustainable and low energy building would be possible, while not compromising on occupant comfort and wellbeing.
The design team specified the most energy efficient and low environmental impact building technologies. A vaulted open ceiling with very innovative triple- glazed bespoke window units to direct natural light into every section of the first floor was designed to fit into an airtight insulated ceiling beneath the warehouse roof panels. The poor building fabric insulation of the 1990s made way to high-density, airtight insulation and pumped insulation up to 400mm throughout the building cavity.
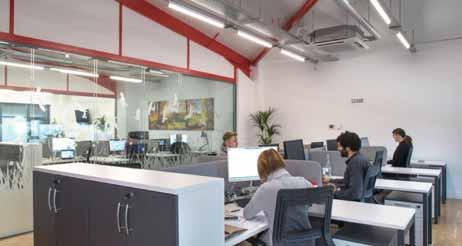
The primary objective was to create a pleasant environment for staff at The Well through a combination of a state- of-the-art building management system providing clean fresh air with internal insulation ensuring optimal thermal comfort for employees. Noise levels are minimimised through acoustic design and natural materials were used to reduce volatile organic compounds in the air.
Having carefully considered what indoor air quality/comfort equipment to use, the Sirus design team concluded that the Mitsubishi Electric HVRF (hybrid variable refrigerant Flow) system was the ideal solution. Four years later this decision to use a then relatively new technology as the main source of
sustainable energy has been fully vindicated.
The Mitsubishi Electric HVRF system uses heat pump technology with a full heat recovery system. Critically, the refrigerant gas is circulated outside the building into a heat exchanger which transfers heat/cool between the outdoor unit to the water used in the indoor units. This means there is no refrigerant in occupied spaces. It also minimises leaks and is therefore beneficial to the environment. Furthermore, it reduces the F Gas charge by 75%, future proofing the building system as regulations drive costs higher.
As a complementary sustainable element Sirus also installed a Mitsubishi Electric Lossnay fresh air heat recovery unit. This is capable of supplying and extracting up to 2,000 m3/h of fresh air, and has a temperature exchange efficiency up to 84%. This significantly reduces the amount of heating needed for the fresh air supply in each zone.
Four years on, The Well demonstrates how innovative thinking can re-purpose a building by creating an energy efficient, healthy and comfortable environment for employees. It is now an established exemplar building that highlights how even older premises can be re-purposed to deliver a healthy environment for staff through a combination of innovative equipment and a state-of-the-art building management system.
Evidence-based data collated over four years indicates that, due to the sustainable technologies, the building’s energy usage is now about 50% of what it originally would have been. What is even more encouraging is that the predicted energy savings were conservative. In reality, the gains are far greater than expected.
There have been other unexpected benefits, flexibility in the use of space being one. For instance, moving office or sub-dividing a larger space into new configurations is problem-free. There is no need to decommission the entire system, or to drain it down. It is also a simple process to upgrade the filters in the Lossnay system, a feature that is now more critical than ever given the
Schematic showing hybrid branch controller at the heart of the Mitsubishi Electric HVRF.
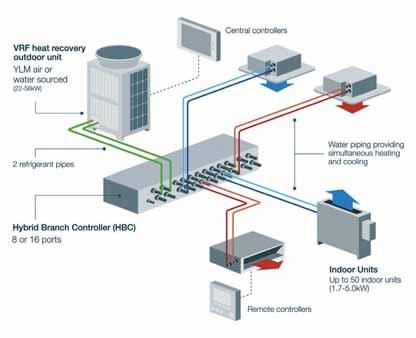
renewed focus on indoor air quality because of the Covid-19 pandemic.
Since the installation of the Mitsubishi Electric HVRF system on The Well project further advancements have taken place with the technology. Stronger legislation is impacting on the use of energy in the built environment (as evidenced the recent publication of the EU Renovation Wave Initiative), while there is a determination to look for new refrigerants to mitigate any harm to the environment.
A new approach to delivering energy efficient heating and cooling to buildings is needed and Mitsubishi Electric’s R32 Hybrid VRF system is a case in point. It uses R32 as refrigerant and operates without using refrigerant in occupied spaces, removing the need for leak detection equipment and allowing more properties to take advantage of manageable phased installation through the system’s modular two-pipe design.
This unique air conditioning system delivers levels of comfort normally associated with chiller technology, while also providing the flexibility and efficiencies of refrigerant based air conditioning. Hybrid VRF therefore offers an additional solution to traditional VRF or chiller systems. Put simply, Hybrid VRF is a 2-pipe heat recovery VRF with water between the hybrid branch controller (HBC) and indoor units. The system can be designed and installed as as VRF while enjoying the features of a chiller system. It delivers a complete solution for office buildings, hotels, medical centres, schools, high rise buildings, shopping centres and other commercial premises.
Hybrid VRF is quick, easy and flexible to design and install using the same control and network as VRF systems. Furthermore, the decentralised system means phased installation is possible with the same high levels of seasonal efficiency expected with VRF. With water at the indoor units, Hybrid VRF provides comfortable and stable air temperature control with no refrigerant in occupied spaces, meaning simple regularity compliance and removing the need for leak detection.
Getting back to The Well project, and bearing in mind that it was conceived at a time when knock-andrebuild was considered the easy option, it is an exemplary display of sustainability. This is evident in the re-use and re-imagination of the internal building space, and many of the core materials used within it. The finished product is an emphatic representation of what can be achieved when the occupant and their comfort and wellbeing are placed the at the core of building design. The entire open design has the added benefit of being a living educational facility, not just for building engineering students, but for all involved in the sector.