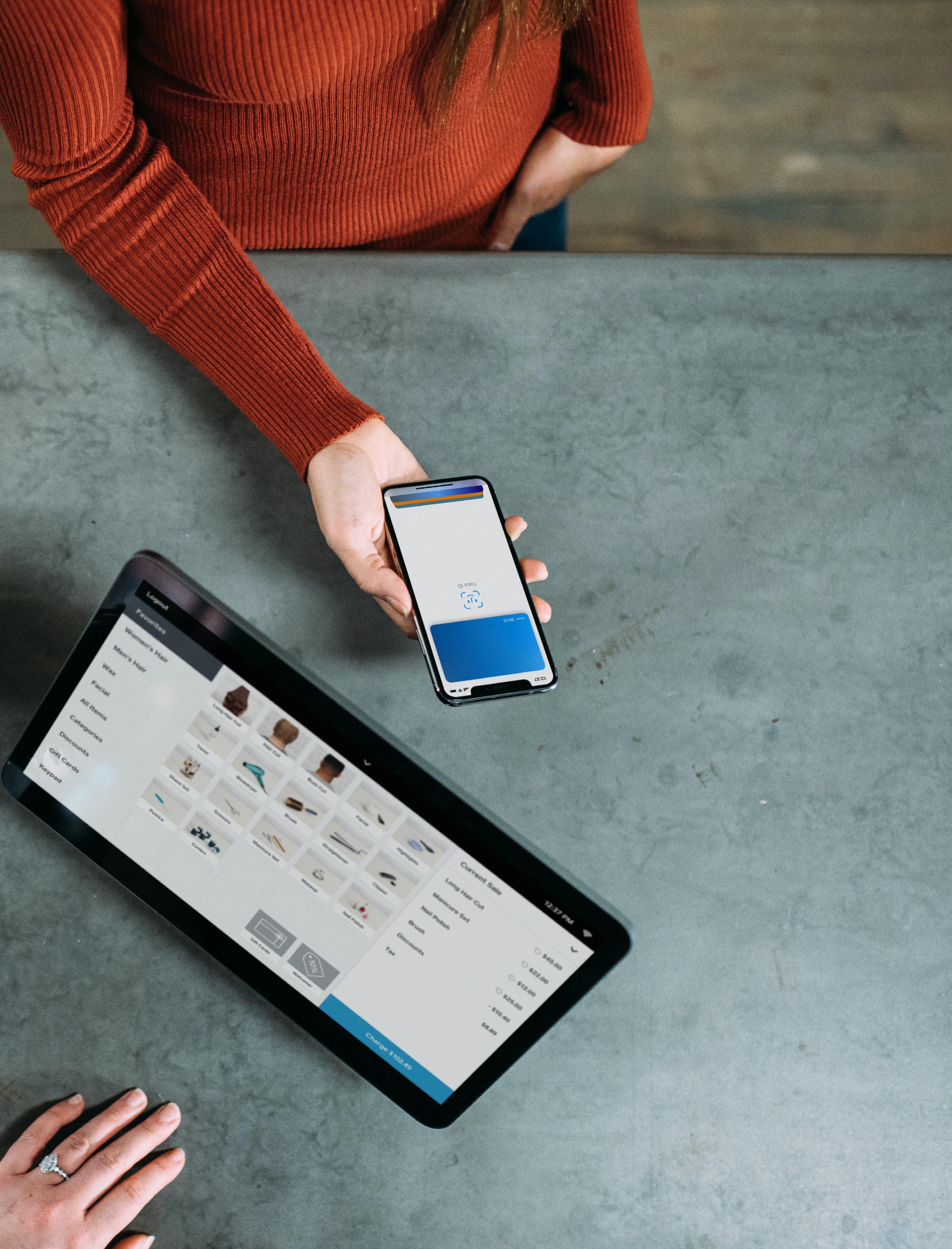
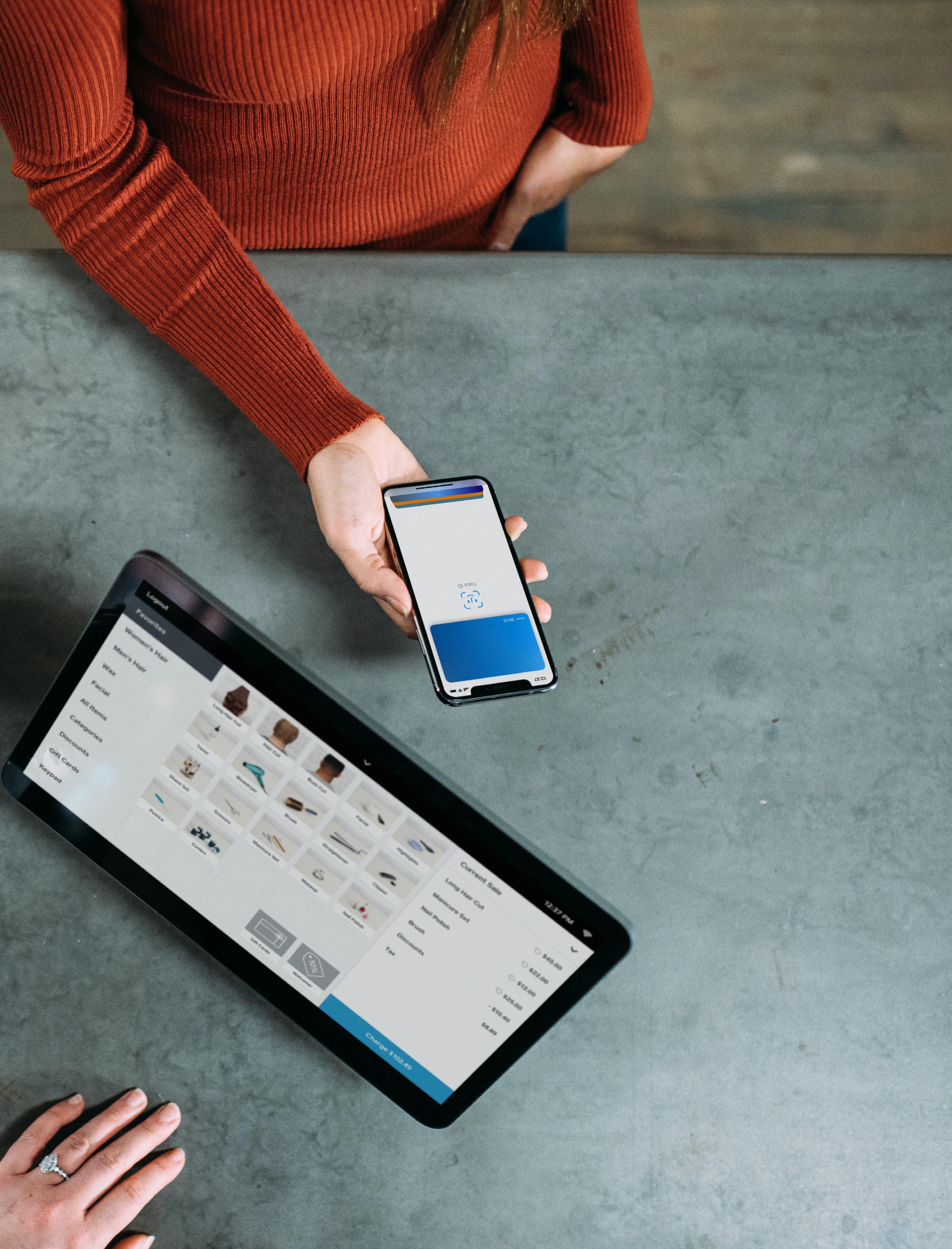
Welcome
About The Magazine
Published quarterly to a circulation of 20,000 + industry professionals across Australia, New Zealand and the wider Asia-Pacific region, Supply Chain Insights Magazine is focused on helping you solve the complexities of today's supply chain. The digital magazine highlights the latest trends, operational strategies, technology advancements and best practice within the supply chain and logistics industry.
In this edition, our features editor Mel Stark looks at the issue of “how the customer experience is transforming supply chains”. Today’s consumers are placing increasingly higher expectations on the companies they choose to do business with. With a new breed of buyer comes a new battleground: the customer experience. In this edition, we explore the symbiotic relationship between supply chain management and delivering a great customer experience.
We take a look at how TMX is helping Kmart to open a new 40,000 sqm distribution centre in New Zealand, how Manhattan Associates have deployed their WMS software at a 70,000 sqm facility in China for Puma, and Google discusses how they accelerated logistics services for
Kings Transport.
In more news, Zebra Technologies have released findings from their 2027 Warehouse Vision Study, eStore Logistics, focusing on how supply chain operations can impact customer perception, and SOTI take a look at how technology can help build resilience into your logistics network.

This edition also includes insights from FourKites on how to optimise last mile deliveries, and Bastian Consulting looks at how supply chain talent can impact on customer experience, while low-code specialists Appian highlights how digital technologies can improve supply chain flexibility.
We hope that you enjoy this edition of our magazine and look forward to hearing your feedback!
Welcome to Supply Chain Insights Magazineyour primary source of industry news, focused on innovation, technology and knowledge-sharing in the logistics sector.
In This
News & Insights
Puma Deploys Manhattan Associates WMS at its 70,000-Square Meter Distribution Centre in China
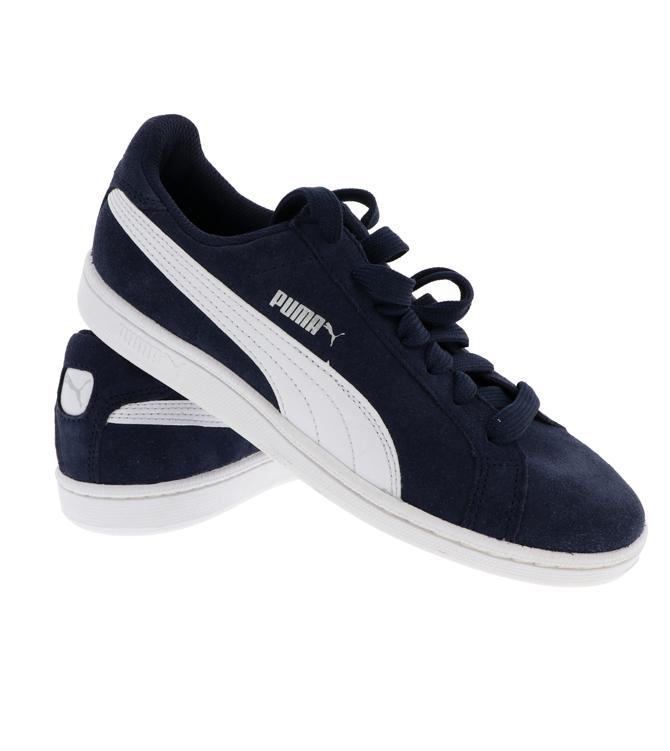
Manhattan Associates has announced that Puma has deployed its Warehouse Management System (WMS) at its 70,000-square meter distribution centre in Taicang, China. This implementation is part of an ongoing project aimed at significantly improving the flow of goods and warehouse efficiency by optimising its inventory, labour resources and warehousing space more effectively.
As one of the world's leading sports brands, Puma boasts more than 16,000 employees worldwide and has a market presence in more than 120 countries.
Following growing business momentum in recent years, coupled with the impact of the COVID-19 pandemic, Puma realized the need to address heightened requirements around labour shortages in its warehouse, storage and distribution facilities.
“Manhattan Associates has the expertise and rich experience in similar projects all over the world, and its WMS has complimented and synchronised well with our business operations since its launch in May,” Mr. Andy Sheng, Head of IT Puma China Limited, commented.
“With the help of the new WMS, the operational efficiency of Puma’s inventory, labour and overall warehouse management have all been improved, and we are very pleased with the service and solutions it has provided. The successful deployment of Manhattan WMS has significantly improved our efficiency in the Taicang distribution centre, proving that Manhattan Associates is a trusted and reliable partner,” Sheng finished.
Stone Chen, General Manager of Manhattan Associates for Greater China, commented on the collaboration with Puma:
Given Manhattan’s deep experience and market-leading position in the warehouse management space, introducing its flexible, advanced WMS was identified as a way to solve Puma’s warehouse and distribution centre challenges at the giant Taicang site.
“Manhattan Associates has operated in China for 18 years, and we feel honoured to serve this world-renowned sports brand. Despite the challenges presented by another wave of Coronavirus hitting China halfway through the project, our team ensured the execution of the implementation went smoothly and was delivered on time, thanks to our ‘always on’ blend of remote and onsite assistance,” Chen ended. ●
Zebra Technologies Releases 2027 Warehouse Vision Study
Zebra Technologies recently conducted a new global Warehousing Vision Study to explore the trends and sentiments driving operational decisions and spend in warehouses. The findings deliver encouraging news: warehouse operators are making significant investments to fulfil the needs of both customers and workers better and make it easier to fill open jobs.
Nearly nine in 10 warehouse operators agree they must implement new technology to be competitive in the on-demand economy, with 80% confirming the pandemic has prompted them to evolve and modernise more quickly. They’re turning their focus and spending most heavily on technologies supporting workforce augmentation and workflow automation.
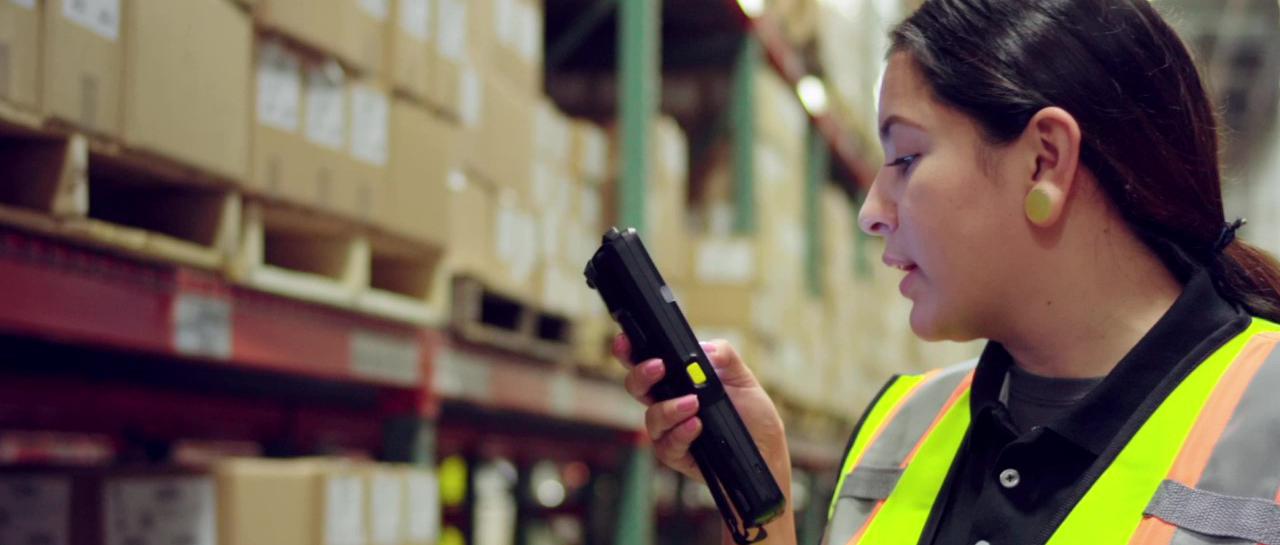
For example, the use of wearables, mobile printers and rugged tablets will
TMX Supports Kmart in Securing Hot Property in Hamilton, New Zealand
Kmart New Zealand has announced it will open a new 40,000 sqm distribution centre at the Ruakura Superhub in Hamilton, following a planned move from its distribution centre in Wiri, South Auckland.
The new distribution centre is scheduled to be operational in late 2023 and will service the long-term needs of Kmart’s New Zealand stores and many customers on the North Island.
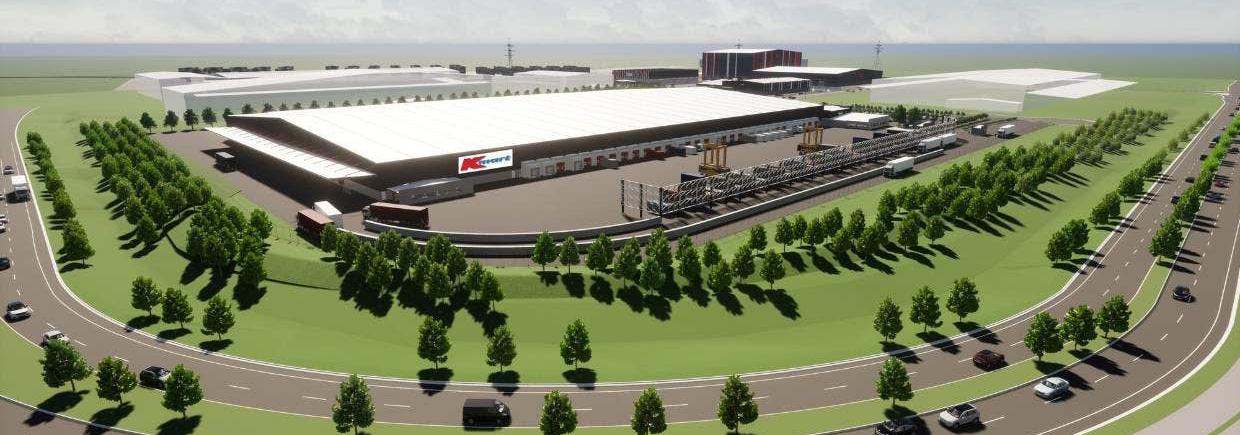
Kmart engaged TMX to lead the procurement of a new facility, and via a competitive tender process, the development was awarded to Tainui Group Holdings, who are developing the Superhub, to build and lease back the distribution centre.
The new facility, located on nine hectares, will include warehousing, distribution, storage, a container yard, and an office facility. The site will benefit from direct access to the Ruakura Inland Port, which will provide rail access to the Port of Tauranga, minimising road transport costs and reducing carbon emissions.
increase in the next few years, along with mobile dimensioning software that automates parcel and carton measurements. Additionally, 27% of warehouse operators have already deployed some form of autonomous mobile robots (AMR) today. Within five years, that number is expected to grow to 90%.
“Most decision-makers believe investments in automation far outweigh the risk of doing nothing, and they are becoming more comfortable integrating all sorts of new technologies into their current operations and infrastructure”, said Mark
TMX partnered with Kmart to lead the strategy, design, automation and property procurement and will also provide ongoing project management for the development of the DC.
Sustainability is a key feature of the new distribution centre, which has been developed in line with the Greenstar 4 rating. Sustainability features will include solar panels generating up to 300kW of power, rainwater harvesting, onsite stormwater treatment, electronic vehicle charging stations, bike racks, and end of trip facilities. Construction of the facility will include low VOC (volatile organic compound) paints, LED lighting, double glazing, and HVAC (heating, ventilation and air conditioning) systems that use low emission refrigerants. Close to 20% of the overall site will be landscaped.
TMX has an enduring relationship with Kmart, having supported the company develop its distribution centres in Australia
Wheeler, Director of Supply Chain Solutions, Zebra Technologies.
An overwhelming 92% of warehouse associates agree on some level that technology advancements will make the warehouse environment more attractive to workers, even in times like these when supply chains are strained, demand is surging, and there’s increasing pressure to meet tighter deadlines. ●
more than ten years ago.
TMX Co-Founder and CEO Travis Erridge said, “We’ve worked with Kmart for over ten years, helping the business to develop optimised supply chain networks and bespoke distribution centres, in Australia and New Zealand. We’re proud to continue to partner with Kmart and support them as they develop this new facility that will enable them to meet the growing demand in eCommerce, now and in the future”.
TMX Director of Property, New Zealand, Sam Smith, said,” We were pleased to help Kmart secure this sought-after location. The facility will incorporate cutting-edge technology, including autonomous mobile robot (AMR) technology. With the retailing landscape changing due to Covid-19 and evolving consumer preferences, the investment in a new, bespoke warehouse will enable Kmart to distribute products via multiple channels and efficiently handle their dynamic range of inventory”. ●
Download the full study here.The Australian Supply Chain & Logistics Awards
The Supply Chain and Logistics Association (SCLAA) is holding its annual Australian Supply Chain and Logistics Awards (ASCLA) on November 4 at the Park Hyatt in Melbourne. These awards are industry’s oldest and most prestigious awards and will celebrate its 60th anniversary in 2022.
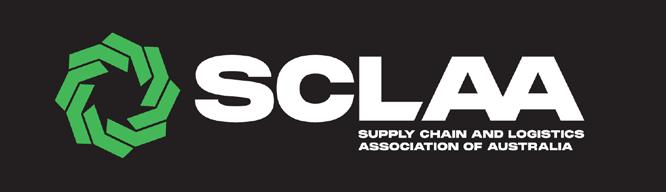
Industry best-practice will be recognised in the following categories:
Prestigious Industry award presented to an outstanding individual who has had an impact across the industry or an impact benefitting the industry as a whole and/or across time.
ASCL Supply Chain Management Award
Supply Chain Management (SCM) is the oversight of materials, information, and finances as they move in a process from supplier to manufacturer to wholesaler to retailer to consumer. This award recognises an organisation that can demonstrate significant achievement or improvement within a section or across their entire supply chain.
ASCL Future Leaders Award
This award provides an incentive and recognition to an outstanding Supply Chain Industry Future Leader and to encourage and support leadership across the industry.
ASCL Automation, Robotics or Emerging Technology Award
The supply chain world is changing quickly, and physical technology is making a huge impact. This award recognises that in addition to data management, significant impacts are occurring through devices, robotics, automation, wearables, and other emerging physical technologies.
ASCL Training, Education & Development Award
Training, education, and development remains a vital part of allowing knowledge to be utilised for new ideas and supply chain improvements to be discovered and then implemented. This award will be presented to a company that can best demonstrate its commitment, application, and results of providing training, education, and development of its people.
ASCL International Supply Chain Award
In recognition of global supply chains, the ASCL International Supply Chain Award is given to a company, institution or an individual that operates internationally. Either an Australian entity with international impact, an international entity with impact on the supply chain industry in Australia, or an Australian company impacting supply chain internationally.
ASCL Environmental Excellence Award
ASCL Environmental Excellence Award recognises corporate leadership or projects within our industry contributing to environmental corporate responsibility, the circular economy and/or protecting the environment.
ASCL Big Data, IT & Business Intelligence (BI) Award
This award focuses on digital innovations that improves or offers a new way of delivering value to the supply chain using Big Data, IT and BI. Award nominees will demonstrate where applying use of existing or new digital technologies, methodologies or frameworks have provided significant improvements to their management of information and/or their supply chain processes.
ASCL Start-Up Award
ASCL recognises that any start-up company faces a tough road. This award recognises those tenacious individuals and companies who push through from inception to success.
ASCL Industry Excellence AwardASCL Awards Gala Dinner
The annual ASCL Awards gala dinner recognises the outstanding achievements of supply chain and logistics professionals and organisations across Australia, celebrating industry excellence and championing collaboration, innovation, and success. Nearly (400) people attended the last ASCLA event earlier in 2022. The SCLAA encourages industry professionals, companies, and associates to join again, in what is expected to be another stellar evening.
Ticket registrations open: Supply Chain and Logistics Association of Australia Ltd - ASCLA 2022 (sclaa.com.au)
Awards Night: November 4, 2022
ASCL Awards Sponsorship Opportunities
Showcase your organisation, strengthen brand awareness to industry leaders, and be an Ambassador of Excellence by recognising its highest achievers. Partnerships of Strength allows sponsors to invite their valued clients or associate companies to become a co-sponsor.
Sponsorship opportunities: The Australian Supply Chain & Logistics Awards - ASCLA Sponsorship For all enquiries: please contact the SCLAA Secretary on secretary@sclaa.com.au or 1300 364 160.
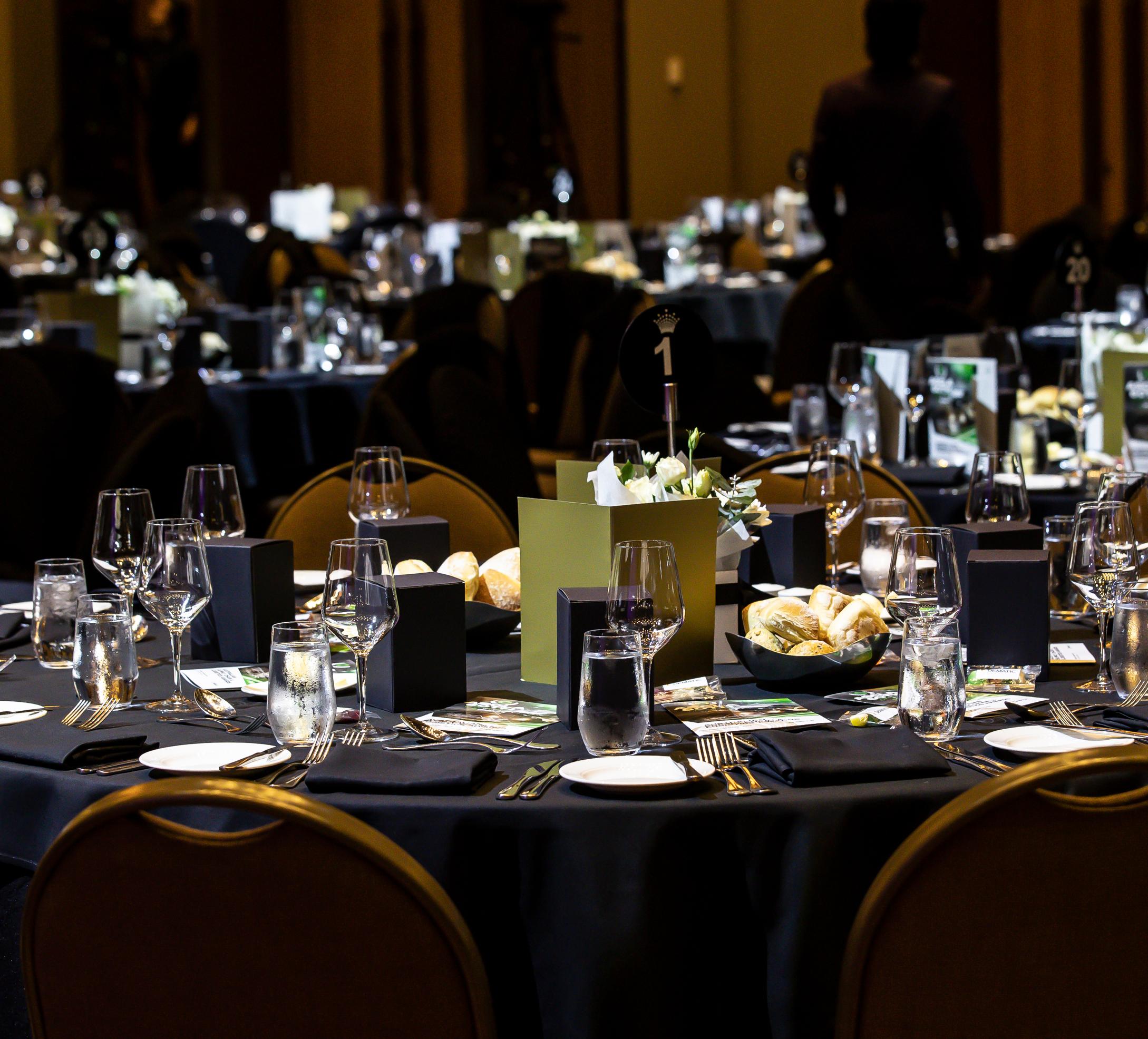
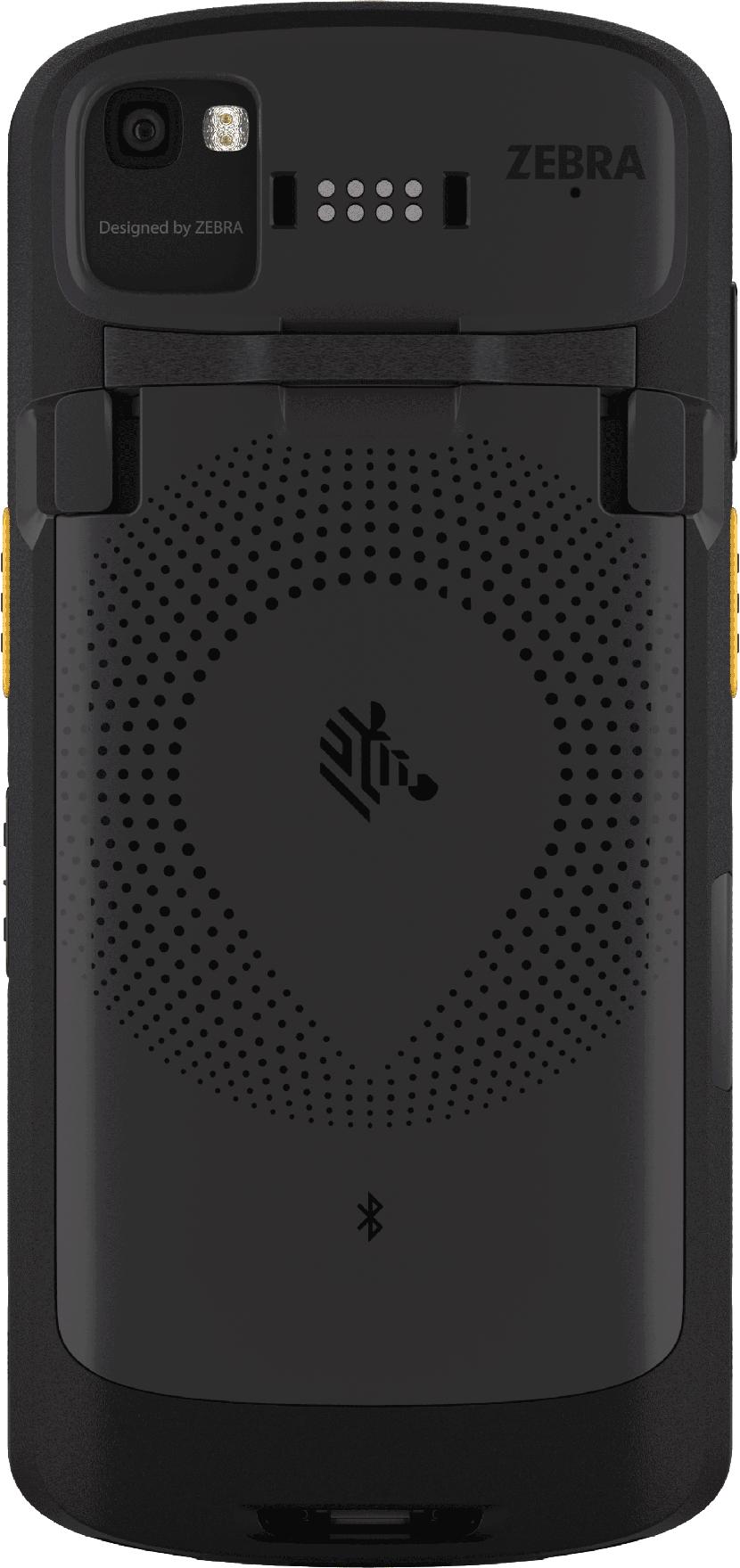
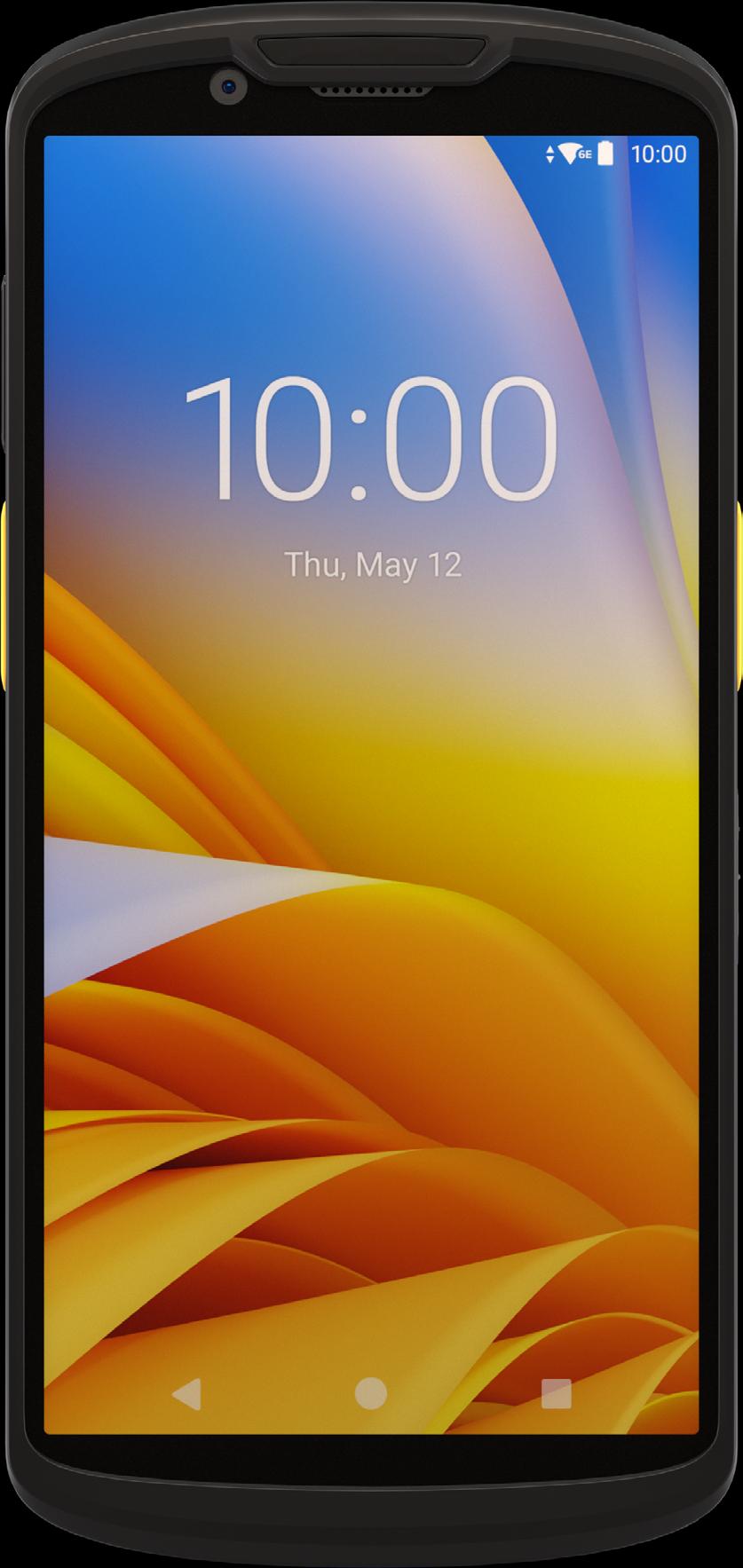
Customer Demand Drives Focus on Supply Chain Sustainability
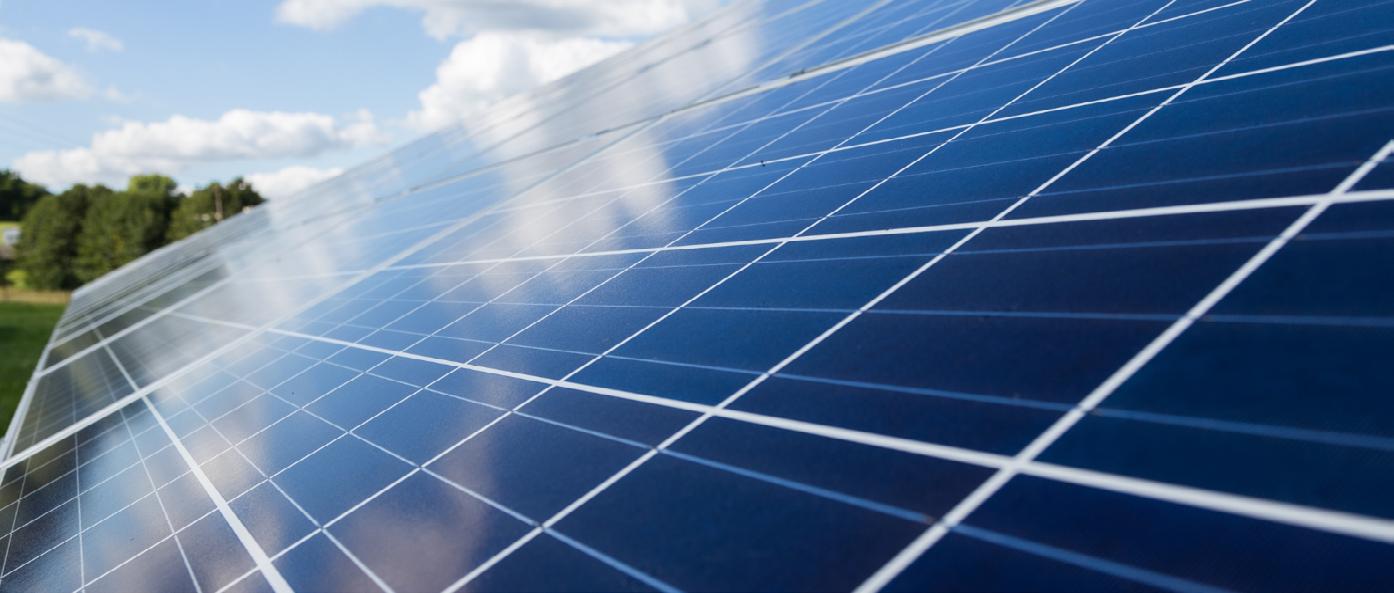
An incorporated sustainability focus is on the rise in freight and logistics as businesses respond to increasing customer demand for more environmentally friendly supply chains.
Increasingly, customers are choosing to buy from businesses that demonstrate leadership and embed social responsibility goals within their operations. There is also increasing awareness across the FMCG sector that sustainable supply chains are not just good corporate governance and a driver of operational savings. They are also a tool to attract or retain environmentally conscious customers who choose businesses based on their green credentials.
According to a report by Australia Post, the key concerns for online shoppers are sustainable packaging and delivery, returns policies and processes and additional costs such as shipping, taxes and duties. Almost half of the respondents want recyclable packaging, and nearly 30 per cent prefer carbon-neutral delivery. Some 28 per cent are willing to wait longer for delivery to reduce environmental impact.
This push for sustainability has coincided with an e-Commerce boom, with customers driven online and the rise of next-day delivery changing how businesses interact with them. It has also changed consumers’ buying experiences, shifting the retail landscape.
In response, the uptake of green warehousing has been rapid, with many businesses installing solar panels and water recycling plants to reduce carbon initiatives. The focus has now shifted to the last mile, with businesses ramping up their efforts to 'green' their operations from warehouse dispatch to delivery on the doorstep in response to heightened customer expectations.
So how can you meet the demands of environmentally conscious customers?
Reviewing the configuration of your network design to ensure that the distribution centres and fulfilment centres are configured in a way that reduces travel is a good starting point. Going a step further and developing a comprehensive network strategy that outlines current and future infrastructure and transport routes, location of physical stores, fulfilment centres and dark sites, plus identifying where customer demand is coming from is even
better and should be a priority for businesses serious about sustainability.
Businesses should also understand the cost to service their logistics profile by expanding from a large warehouse into multiple smaller ones to deliver on time, as Amazon in the US has done. Another option is to look at the current delivery vehicle fleet and consider whether electric or hybrid vehicles can be adopted.
Businesses should consider implementing robust order management systems (OMS), which serve the dual purpose of improving customer experience while driving sustainability. OMS combines inventory, booking and route systems to use despatch points, delivery addresses and flexible timeslots to supply customers with ultra-convenient but cost-effective solutions from the right place to the right place without splitting orders. Hybrid operating models can enhance customer experience and optimise your fleet and transport modes, reducing cost and carbon emissions. Importantly, talk to your customers and let them know if a delay can be expected.
Finally, who you choose as your freight and logistics provider can make all the difference in achieving a greener 'last mile'. Using the procurement process to identify providers who focus on sustainability and who demonstrate their green credentials and making sustainability a key objective of procurement contracts can also ensure your last mile is as green as possible.
Making tangible efforts to implement a more sustainable supply chain should be a focus for businesses, especially those in the B2C market, with customer expectations around sustainability only likely to grow.
As businesses shift away from sustainability initiatives within physical infrastructure ‘greening’ the last mile should be next on the to-do list. Communicating these efforts to customers should follow as a priority. ●
As retailers benefit from strong consumer demand and a colossal increase in e-Commerce orders, the focus for many businesses is now on controlling emissions within the supply chain.For more information, click here.
How Supply Chain Operations Can Impact Customer Perception
WRITTEN BY LEIGH WILLIAMS FOUNDER & MANAGING DIRECTOR OF ESTORE LOGISTICSTo deliver an exceptional customer experience, businesses need to provide reliable, flexible and reasonably-priced delivery options for customers. At the same time, the organisation must also have a unified view of customer demand, balance supply and demand, and identify and respond to any disruptions or deviations.
A modern, digitised and resilient supply chain is critical to achieving this. By understanding customer and supplier behaviour and optimising inventory and production, companies can reduce stockouts and improve the proportion of orders delivered on time and in full, leading to high revenue and customer retention.
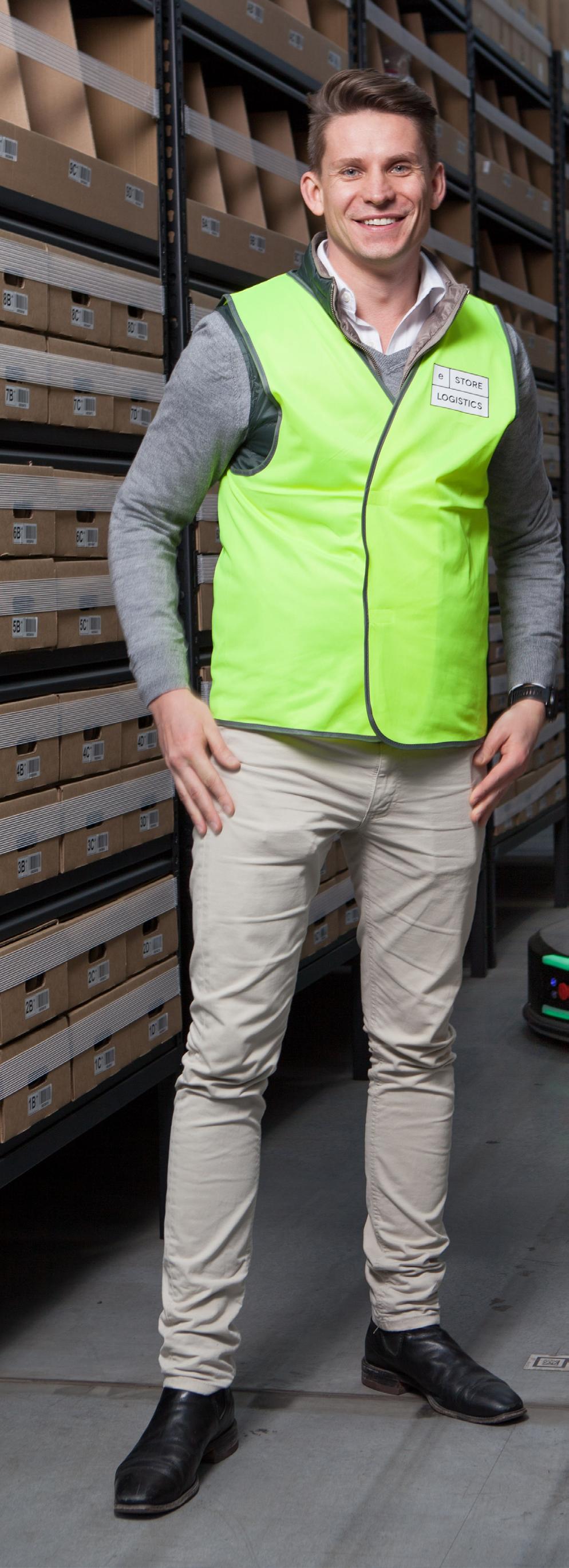
Retail sector headwinds to be aware of
In the past, supply chains have focused primarily on minimising cost and increasing speed. Now, with the ubiquity of customer data such as cart abandonment
and pricing data, as well as third-party data such as weather, companies can better understand changes in customer behaviour to inform forecasts and logistics.
Across the world, the retail sector is facing headwinds of rapidly changing customer needs and behaviours, rising operating costs and heightened demand for last-mile delivery.
The demand for immediacy through express delivery, more flexible return policies and endconsumers using subscription or rent models is significantly changing supply chain logistics and inventory flows across channels. Companies now need to stitch together the customer journey across their front, middle and back operations and ecosystems of suppliers and partners to meet new customer demands and expectations.
How supply chain operations can impact on customer perception
There is no point in having a great buying experience, if your supply chain processes are not designed to deliver on the promise.
If a customer places an online order in two minutes, they expect the same level of response in delivery - two hours or two days, not six weeks. It’s important to have a supply chain that is aligned with the customer expectations that can offer fast, reliable and cost-efficient fulfilment and delivery.
Supply issues and available stock can also affect the customer experience. For eCommerce operations, it can be very easy to overlook inventory levels when fast fulfilment is a number one priority. This can lead to issues managing reverse flows such as new items and customer returns and, in turn, product availability.
How automation can support supply chain operations
At eStore Logistics, our customer promise is that orders made by 4 pm are fulfilled on the same day. We can meet these fast delivery standards for online stores of all sizes as we have deployed a fleet of autonomous mobile robots (AMRs) to work alongside our human workforce at our warehouses distributed across the country.
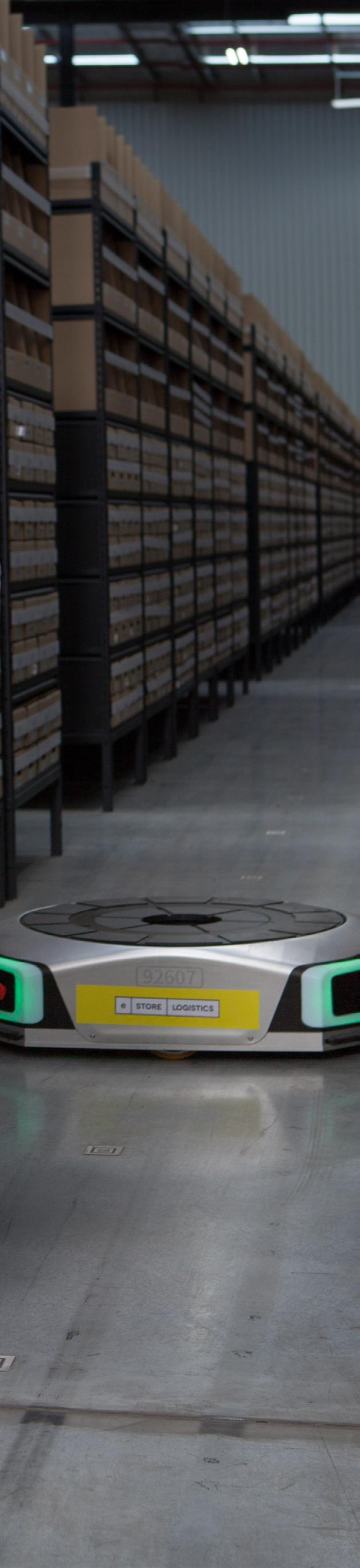
It also allows manual workers to be placed in positions of higher value rather than physically demanding jobs.
The role of supply chain leaders today
Supply chain strategies are intrinsic to business strategies; an integrated supply chain can lead to financial and operational gains, a greater competitive advantage and increased customer retention. For example, more accurate sales order forecasts can translate into a more effective supply plan, which reduces lost sales.
The role of the supply chain leader has evolved in recent years to keep pace with customer expectations for service and personalisation and new customer purchasing behaviours. With the ongoing pressures of the COVID-19 pandemic, including global supply chain disruptions, labour shortages and rising inflation, supply chain leaders are getting a seat in the boardroom to support the customer experience and meet market demand. ●
For more information, please click here.
There are greater expectations for frictionless buying experiences; customers expect anytime, anywhere delivery with inbuilt flexibility.
Against a backdrop of labour shortages, using AMRs and other automated warehouse solutions can enable retailers to keep pace with growing eCommerce demands and maximise order fulfilment.
Industry-First: Capture Parcel Dimensions and Shipping Costs with the Press of a Button
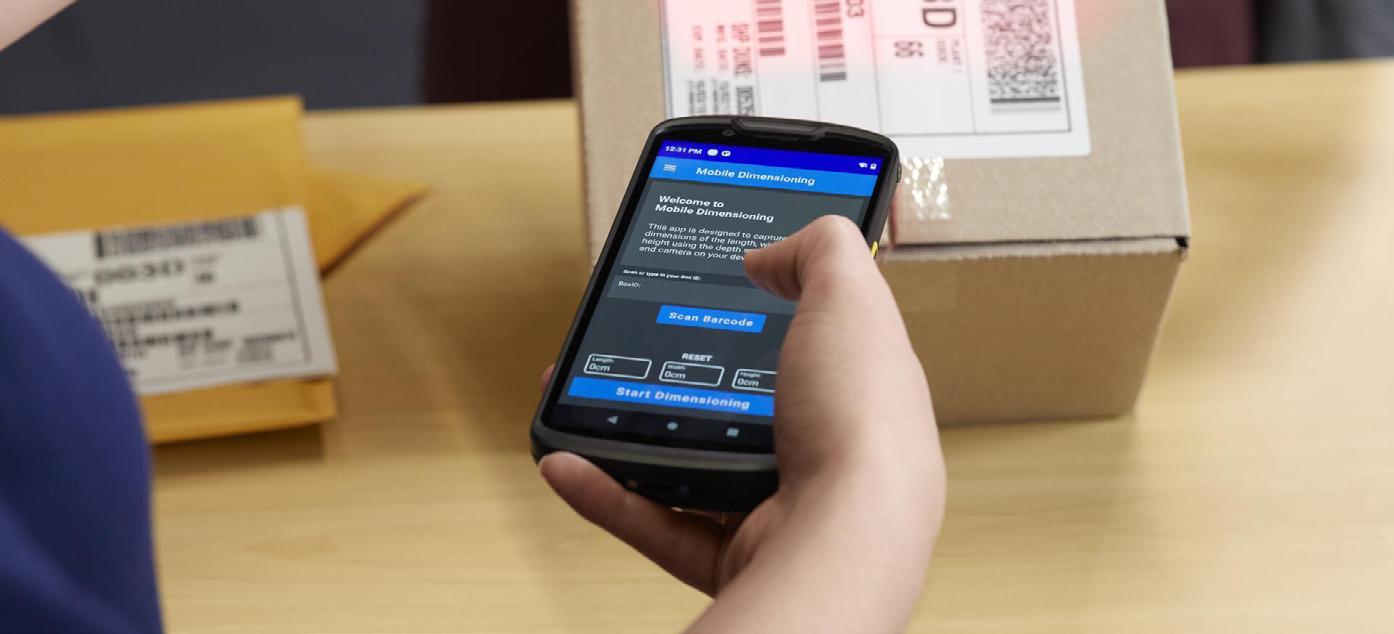
Supply challenges are currently at an all-time high. Today’s on-demand economy, coupled with heightened customer expectations, skyrocketing labour costs, and globalisation are heavily impacting transport and logistics businesses around the world.
For these reasons, quick, accurate and easy parcel dimension calculation is key at both a parcel’s pick-up and drop-off points. But capturing dimensions manually via a tape measure inserts lengthy time into the already-complex shipment process, reduces workforce productivity, and invites errors. Miscalculations can lead to undercharging, loss of revenue, reduced profitability and costly disputes that ultimately erode customer service quality, satisfaction and retention. In the warehouse, inaccuracies can also lead to costly underutilisation of warehouse space, reduced load efficiencies and increased transport costs.
The stakes are high. By accurately recording the dimensions of parcels and understanding the total volume they will take up in a delivery truck, businesses can more effectively use vital space in a shipment, ensuring every truck is used to full capacity.
improved visibility, enabling businesses to better plan their fleet loads and warehouse space requirements. Ultimately, this fully mobile solution allows businesses to capture dimensions anywhere in their operations – doorstep collection at homes and businesses, parcel drop-off locations, warehouses, depots and hubs.
Businesses can rapidly capture the dimensions of practically any parcel – with box dimensions ranging from 10cm to 1m per side. It doesn’t matter whether boxes are plain, wrapped or printed with graphics and whether they are placed on a counter or the floor. Zebra Dimensioning allows busy frontline staff to capture information in virtually any environment and lighting conditions.
Zebra’s TC53 and TC58 mobile computers are powered by the Zebra Dimensioning software, designed to add a new level of operational efficiency and workforce productivity.
Introducing a new solution, Zebra Dimensioning, which helps Transport & Logistics business make the most of their precious time and space. The solution is certified by Australia’s National Measurement Institute and other international regulators, offering a fully integrated handheld mobile dimensioning solution businesses can rely on.
The solution captures accurate parcel dimensions and calculates shipping charges with the press of a button. It also provides
What makes these devices so different? With all the latest wireless technologies, workers are given faster and more reliable access to information they need to get the job done — including 5G and Wi-Fi 6E. A class-leading 6-inch screen lets workers see more, do more — and scroll less, while an ultra-rugged, sleek design has made the TC53 / TC58 thinner and more durable.
Businesses can also choose the scanner that best fits their workers’ needs — either
the standard scan engine or the advanced range scan engine with IntelliFocus™ technology, which delivers an extraordinary scanning range. A 16 MP rear colour camera offers the maximum resolution in this class, while three microphones and two speakers deliver outstanding audio clarity. Furthermore, the device’s battery is the largest in this class, with the extended battery option offering 50%+ more power than competitive devices.
The result? A new generation of data collection. A new level of operational efficiency. And a new level of workforce productivity.
The TC53/TC58 — together with Zebra Dimensioning software — is driving new possibilities into the world of mobility.
Zebra mobile computers are ready to start capturing dimensions straight out of the box — the Time of Flight sensor is integrated, and the Zebra Dimensioning is pre-installed. All you need to do is integrate the dimension capture into your backend enterprise systems — and the Zebra Mobile Dimensioning Application Programming Interface (API) makes that as easy as integrating your barcode application. ●
There has never been an application that has achieved certification by international weights and measures regulators – until now.Click here to learn more about Zebra Dimensioning and the TC53/TC58 mobile computers.

Safety Stock: What Is It and How Can It Be Optimised?
WRITTEN BY TOM FITZ-WALTER EXECUTIVE DIRECTOR, SUPPLY CHAIN AT TMXWith severe disruption still prevalent across global supply chains today, it’s time to rethink the role of safety stock.
Recent data from Adobe revealed that stockouts were up 250% in October 2021 compared to prepandemic levels.
However, the concept of safety stock is often surprisingly misunderstood and can have very real consequences when it’s applied in a way that doesn’t align with the wider business strategy or fit in with the physical constraints of a given network.
What is safety stock?
Safety stock, sometimes referred to as buffer stock, is extra inventory held to prevent stockouts in case of an issue in the supply chain, an increase in demand or to mitigate the risk of uncertainties such as supplier delays, financial constraints, inaccurate forecasts, or failure to place timely reorders.
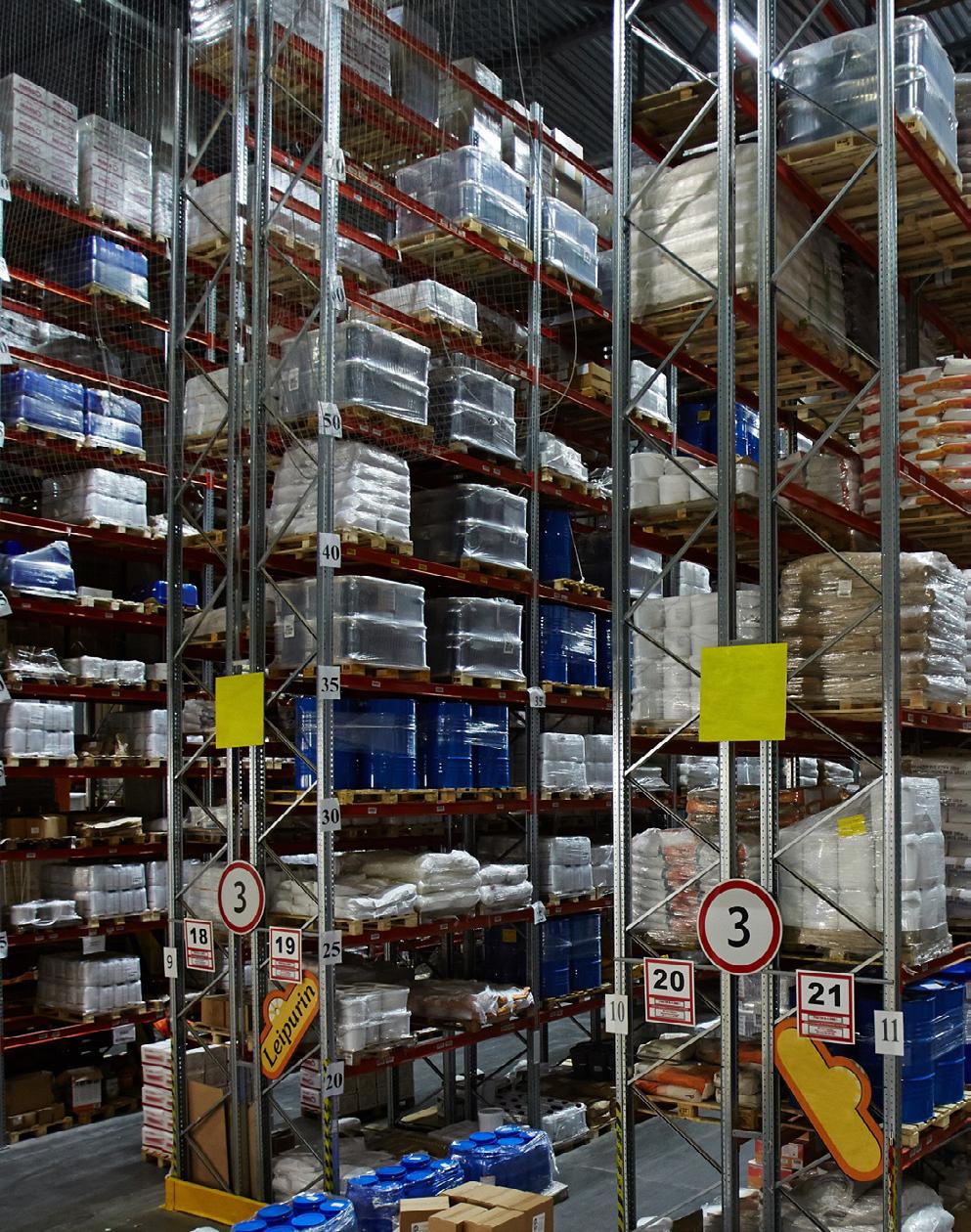
Strategies concerning safety stock are largely employed by businesses to primarily protect themselves from future unknowns. These can range from the trivial, for example selling more than forecasted over a certain time period, through to the more significant – for example geographic lockdowns or force of nature events.
With major fluctuations in demand, due to unpredictable consumer behaviour during COVID-19, geopolitical events and the rapid rise of e-commerce – there’s been major swings in demand volatility, making predictions around inventory management and safety stock extremely challenging.
Moving into the middle of this year, we are still dealing with container equipment and vessel space shortages which are continuing to expose weak links in the end-to-end supply chain. As a result, there’s never been an area of inventory management that’s as critical as safety stock.
While running low on stock is a regular occurrence for many retailers in the current climate, safety stock can ensure that a supply chain runs smoothly and stockouts are minimised.
With the rise of e-commerce, the negative impact of stockouts can be crippling for retailers. It’s now far too easy for online shoppers to find a product on a competitor’s site.
But the consequences can be more than a missed sale, stockouts can also impact long-term relationships with customers, and even reduce brand loyalty.
It’s no surprise that the past two years have seen businesses place more importance and emphasis on safety stock than ever before.
How should you calculate safety stock?
Supply chain and inventory teams of today are left with a number of key questions regarding safety stock and how to manage it. These questions tend to be centred around how to mitigate for supply risk and how to ensure any safety stock strategy supports this. Questions are also asked around how much safety stock to hold and where to hold it.
But when considering safety stock strategies, it’s important to understand specifically what problem it is you’re attempting to solve and build a strategy accordingly.
Namely, safety stock is the contingency stock that is held at a location that is used to absorb unforeseen demand as a result of variation in:
1. Demand - what is the customer demand on this product between now and when I can next replenish this location
2. Supply - the volume of this product due into the location
3. Lead-time - when are future drops of this product planned into this location
Fashion retail: an example
Let’s take a simple example of a pair of jeans. If a retailer plans to sell 20 pairs of jeans from a store over the next week and their lead time is seven days (from between now when they order it to when it is delivered) there are many approaches to solving how to prevent this location from running out of stock, without filling it with excessive amounts of safety stock.
However, when thinking through safety stock strategies, an issue we often see is that businesses establish their strategy as a purely theoretical exercise.
Meaning that a safety stock value is calculated based on input variables like demand variability, lead-time variability, or even worse, simply as a days or weeks of stock value.
While these strategies succeed in placing additional inventory in locations, they fall short of achieving the optimal scenario for a supply chain operation and in many cases cause additional handling challenges.
Optimising safety stock strategies
By approaching the problem of safety stock with the view of optimisation across both the physical supply chain and the more theoretically driven inventory function together, different solutions become apparent very quickly.
As with the example above, the jeans safety stock is used to mitigate variability over the lead-time, but instead a concerted effort should be made to shorten the lead-time. This then reduces the level of uncertainty and therefore enables the organisation to hold less stock at the location without the incremental risk of sell-out (assuming the reduced lead-time can be reliably met).
Even where this tactic would add some cost, a cost benefit analysis should be performed on the incremental processing which enables the shorter lead-time against the cost of inventory that needs to be held to mitigate the current lead-time as well as the potential double handling that occurs as a result.
While this example might seem relatively obvious, it demonstrates how achieving a local optimum can leave a far greater opportunity unrecognised despite all teams having the best intentions at heart.
Post pandemic, many businesses are now more comfortable with holding excess stock, but significantly increasing stock levels is a costly endeavour when you consider the rising cost and scarcity of industrial property in Australia.
Furthermore, businesses are starting to feel the strain of tied up capital sitting in inventory, and need to adapt a more flexible approach and strategy to move back towards profitability.
Leveraging the digital supply chain
The more connected a supply chain is, the greater the opportunity for getting safety stock levels right.
Nowadays, there’s more inventory management software options in the market than ever before and modules such as demand planning, inventory planning, replenishment planning and product planning all play their part in optimising inventory and analysing safety stock requirements.
At TMX, we partner with a number of global tech leaders in this space to find opportunities to analyse, optimise and manage inventory. Our team of experts in this field have a deep understanding of implementing new inventory management systems at some of Asia Pacific’s largest retailers and logistics providers.
Inventory management services are also increasingly available in a Software as a Service (SaaS) model – enabling for rapid and cost-effective improvements to safety stock and inventory management processes.
With digital supply chain solutions a major focus for TMX and our clients, we ensure that all inventory management systems seamlessly integrate with our digital solutions – including IBP, TMS, WMS and MRP. ●
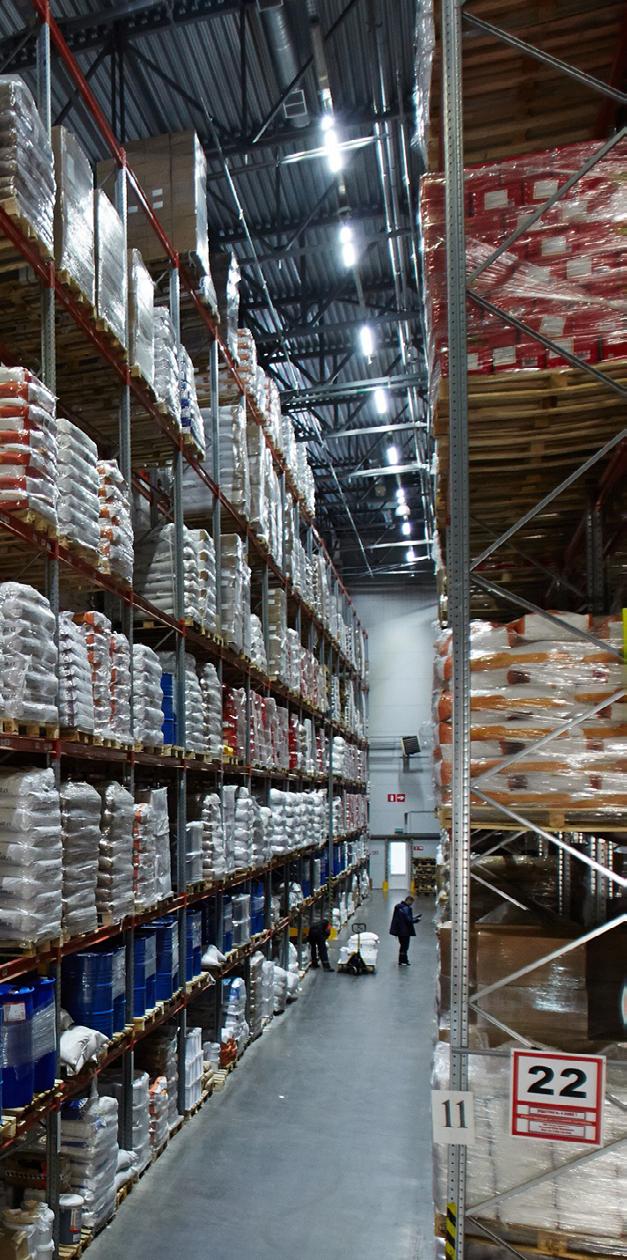
At TMX, our view is that innovating and optimising processes and lead times is now a better option than simply holding an abundance of safety stock.
To find out more about how TMX can help with your safety stock strategy, tmx.global/
Close Gaps in Communication, Information and Technology with Zebra Workforce Connect
The need to close information and communication gaps
Workforce Connect enables warehouse managers to consolidate critical workflows into one fully connected platform – giving their frontline workforce a complete solution. It covers the entire spectrum of frontline needs, from communication to collaboration, from information to safety, all in one connected platform.
Offering strong analytics and reporting capabilities, Workforce Connect can be used to determine powerful insights and improve productivity. It also enhances workflow and location visibility via automated safety measures which protect frontline staff.
There’s disruption on the frontline. Employees in transportation and logistics face a disconnected workplace with gaps in communication, information and technology.
One major problem is the decentralised work environment, which makes it difficult for organisations to track the location of employees, equipment and orders in real-time.
As a result, frontline workers are buried in tasks and burdened by inefficiencies, from juggling multiple devices to managing disjointed workflows. They also face increasing pressure to deliver optimal customer service. This directly leads to inefficient delivery and dispatch operations and worker safety concerns.
Without a unified digital workplace solution that fosters collaboration, increased engagement and information sharing, communication and information gaps will continue to grow — and frontline morale will continue to decline. So how do you do this?
The key is to shift frontline workers’ focus from transactional tasks to high-value interactions. When information flows freely, and collaboration happens naturally, workers move away from task-oriented work and break out of their silos. Organisations must empower workers with the digital tools to solve problems on the spot and apply their cognitive skills to serve customers better.
Take the following scenario as an example: In many logistics companies, delivery drivers do not take the same mobile device at the start of every shift because the business operates a shared device model. While this means businesses don’t have to purchase as many devices, it also presents a new challenge: when a delivery driver needs to be contacted, tracking them down can be a lengthy process.
This becomes a problem when a customer requests an urgent update on their delivery status, requiring the customer service team to find and contact the appropriate delivery driver. Delays can lead to a negative customer experience and lengthy call times for customer service assistants, taking their attention away from other important issues.
That’s where Workforce Connect can help! The software enables central teams such as customer service to view the exact location of mobile workers on a map and instantly communicate with them using a push-to-talk application. This means delivery drivers can easily report where they are on their journey, customer queries can be answered quickly, and call times are reduced for customer service contact centres.
There is an easy way to do this, thanks to Zebra Workforce Connect.
This fosters collaboration, increases productivity and raises customer service to new heights.
In an ideal world, each delivery driver would have their own mobile device, but this is often not an economically viable option.
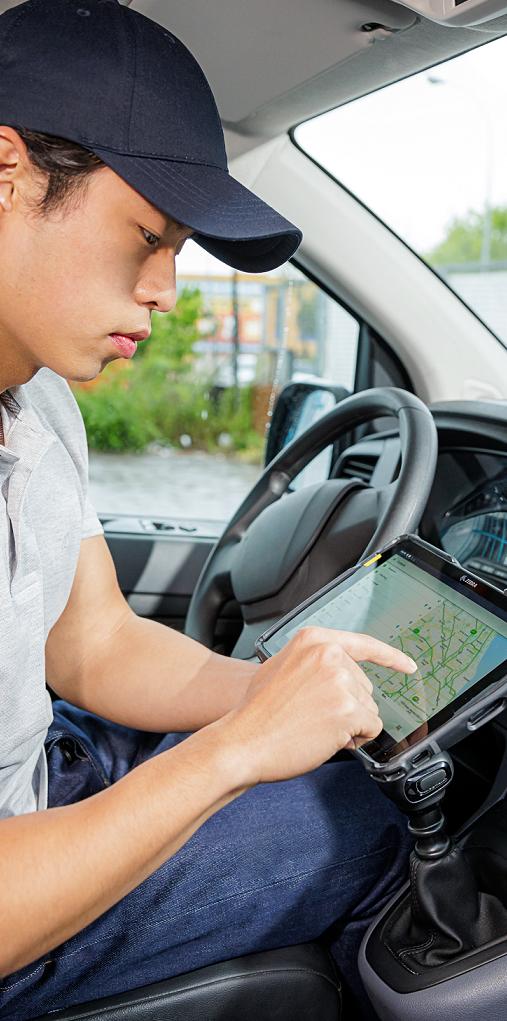
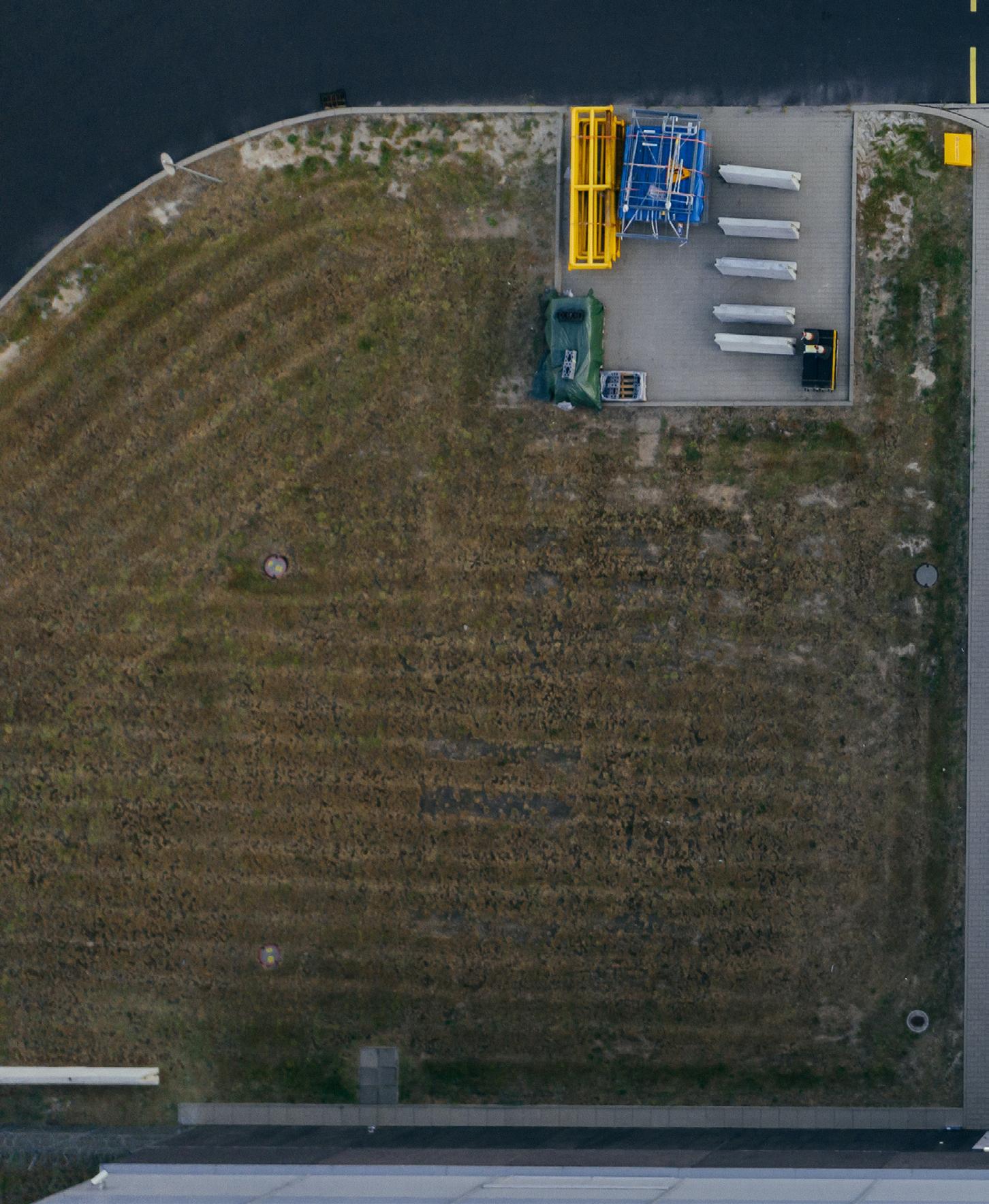
Today’s consumers are placing increasingly higher expectations on the companies they choose to do business with. With a new breed of buyer comes a new battleground: the customer experience. In this edition of Supply Chain Insights, we explore the symbiotic relationship between supply chain management and delivering a great customer experience.
Today’s consumer engages with brands through multiple digital touchpoints: social media, online shopping, apps, emails, live chat, SMS updates, online ads and more. We’re constantly connected to the places we shop.
Customers now place incredibly high expectations on the brands they choose to do business with, and they are largely putting the customer experience at the heart of their decision-making. This enhanced connectivity has led to many marketing experts declaring this period: the age of the consumer.
In the age of the consumer, customer experience is king. According to US-based customer experience and social media marketing platform Emplifi, 86% of consumers would leave a brand after as few as two poor experiences. Furthermore, 61% of consumers
will pay at least 5% more if they know they will get a good customer experience. A recent survey from PwC also found that 65% of all consumers find a positive experience with a brand to be more influential than great advertising.
For Travis Erridge, Co-Founder and CEO at TMX, experience is everything. “There’s nothing worse than an order taking too long or the wrong item turning up. It kills the customer experience immediately, and getting this right is the bare minimum when it comes to delivering a good customer experience,” he says.
Yet delivering a good customer experience is becoming increasingly challenging in today’s turbulent environment, says Raghav Sibal, Managing Director in Australia & New Zealand at Manhattan Associates.
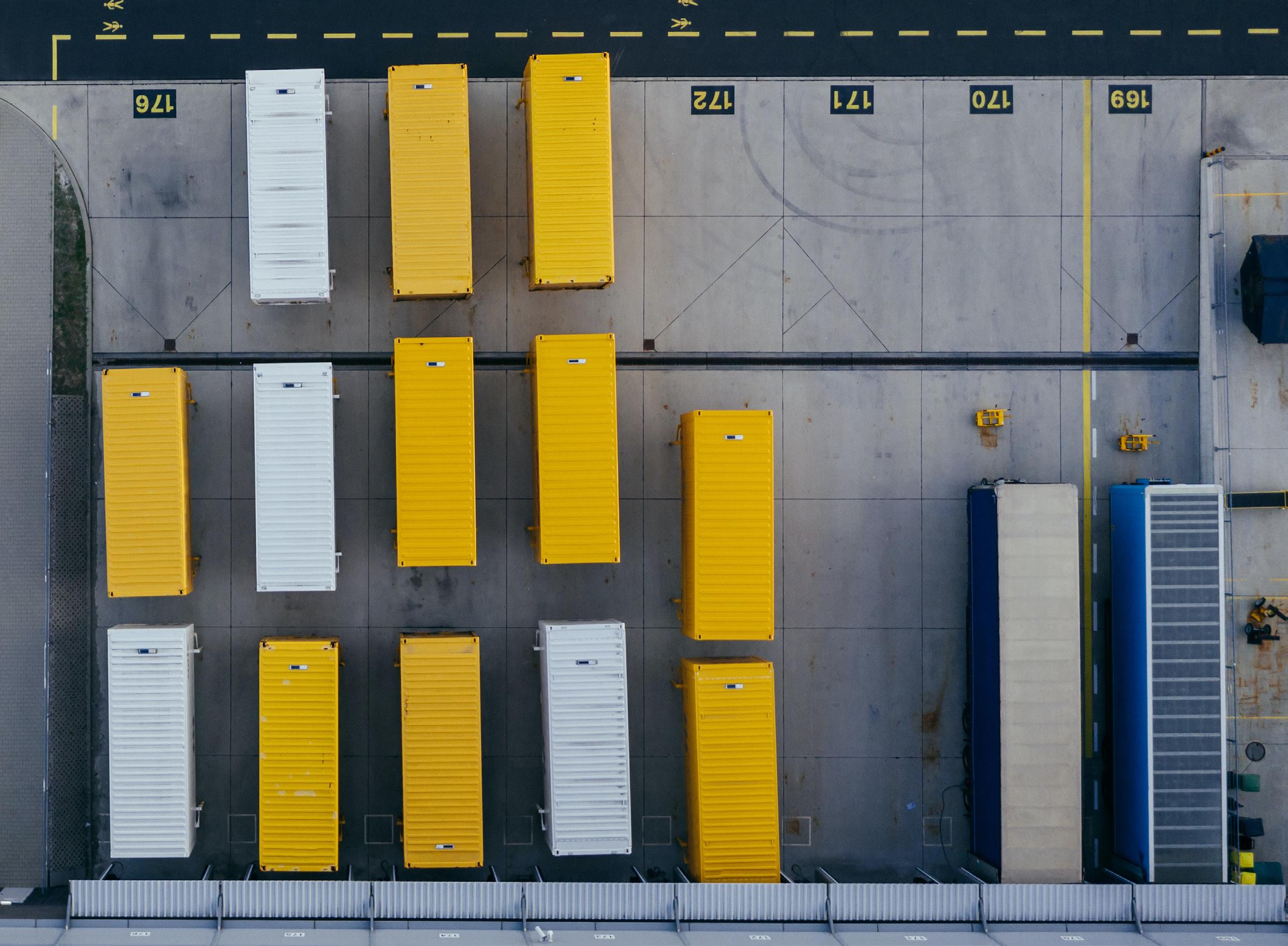
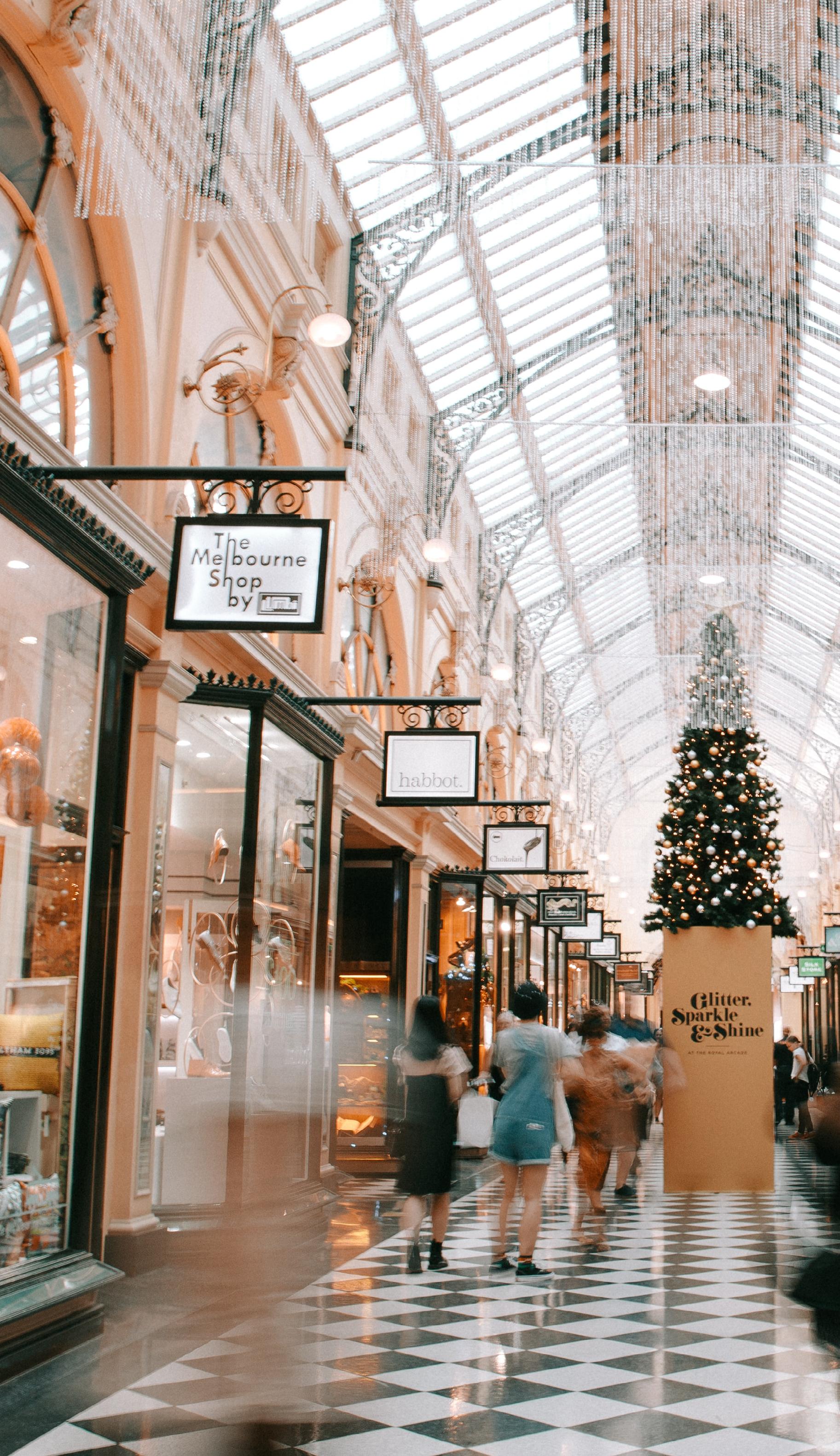
“We’re still battling major supply chain disruption, and it’s certainly making delivering a great customer experience more difficult. But it’s absolutely critical to everything, and we’re seeing more organisations place this at the centre of any decision making.”
Businesses are investing a lot of time and resources into improving their customer experience – and supply chain plays a crucial role here.
Experience is everything
For TMX’s Travis Erridge, supply chain has always been linked to the customer experience.
“If you think about supply chains, they’ve either got an internal or external customer. The internal customer is putting stock on the shelves of a store, and the external customer is the person receiving the end product. In this process, customer experience has always been a key part.”
But the rise of e-Commerce has emphasised the importance of customer experience in supply chain operations. “Retailers now need to provide the same customer experience whatever channel their customer chooses to buy from – a marketplace, a physical shop, an online store – the experience has to be the same,” Travis says.
Royston Phua, Zebra Technologies’ APAC Supply Chain Vertical Practice Lead, says that while the rise of e-Commerce is making an impact, there’s even more at play here. “What we are looking at from the business perspective today is not just e-commerce but omnichannel fulfilment, which combines B2B and B2C fulfilment models and is very challenging to get right.”
Closing the gap between the customer experience promised and the customer experience delivered is high on the corporate agenda, which according to Royston, is exactly where it should be.
Furthermore, the organisations that do deliver a great customer experience are the ones who hold on to their customers. “Customer experience is always a lead indicator for repeat business,” TMX’s Travis Erridge says.
“Historically, retailers could avoid investing in online customer experience if e-commerce only made up 5% of total sales. But now we’re talking 15% upwards, it’s really important. In today’s online world, it’s too easy to lose a customer – if they don’t feel part of a community, receive a good service and a great experience, then they will find someone else that provides this,” Travis says.

A wave of digital investment
Some of the largest businesses are investing record amounts of capital in their supply chains to enhance and improve the customer experience – with digitisation at the core.
Global fashion retailer H&M recently partnered with Google Cloud to enhance its customer experience and supply chain operations. The fashion retailer will collaborate with Google to develop an enterprise data backbone that includes a core data platform, data product and advanced artificial intelligence and machine learning capabilities.
Sports giant Nike also recently announced it would be overhauling its ERP in a bid for better supply chain speed and agility. Nike, like many retailers, has been facing extended lead times and delivery delays and sees this new technology system as instrumental in tackling these issues.
Described by Nike CFO Matthew Friend as the company’s “biggest investment in digital transformation”, the ERP system will be crucial to increasing inventory visibility and productivity.
Like Nike, H&M and many of the world’s largest organisations – businesses throughout the APAC region are looking to digitise their supply chain to help deliver the very best customer experience.
But according to TMX’s Travis, there is still a long way to go in this space.
"It’s not just about being able to provide an extended range of products and services – it’s also about the ability to proactively understand the customer’s preferred shopping habits, tastes, and preferences and commit to the agreed fulfilment service levels with a high level of visibility,” he says.
“A lot of the problems we are seeing today in retail supply chain are caused by a lack of connectivity and integration across systems and processes. There is often a disconnect between store sales data, store inventory data, warehouse management systems and transport management systems.
“We must recognise the fact that consumers of today have more choices. They're more discerning and more demanding.”
“In the future, to get customer experience right, we'll see these systems become increasingly connected and we will also start seeing increased utilisation of big data and predictive analytics to ensure that inventory is in the right place, at the right time and at the right location to provide the ultimate customer experience,” Travis says.
According to Zebra Technologies’ Royston, buzzwords like agility and resilience have moved into the mainstream.
As with all supply chain technology, data must be in a usable format to be meaningful.
On the rise of the digital supply chain and its vital role in delivering a great customer experience, TMX’s Travis Erridge says it’s about utilising as much legacy data as possible and adding new data to it to improve it.
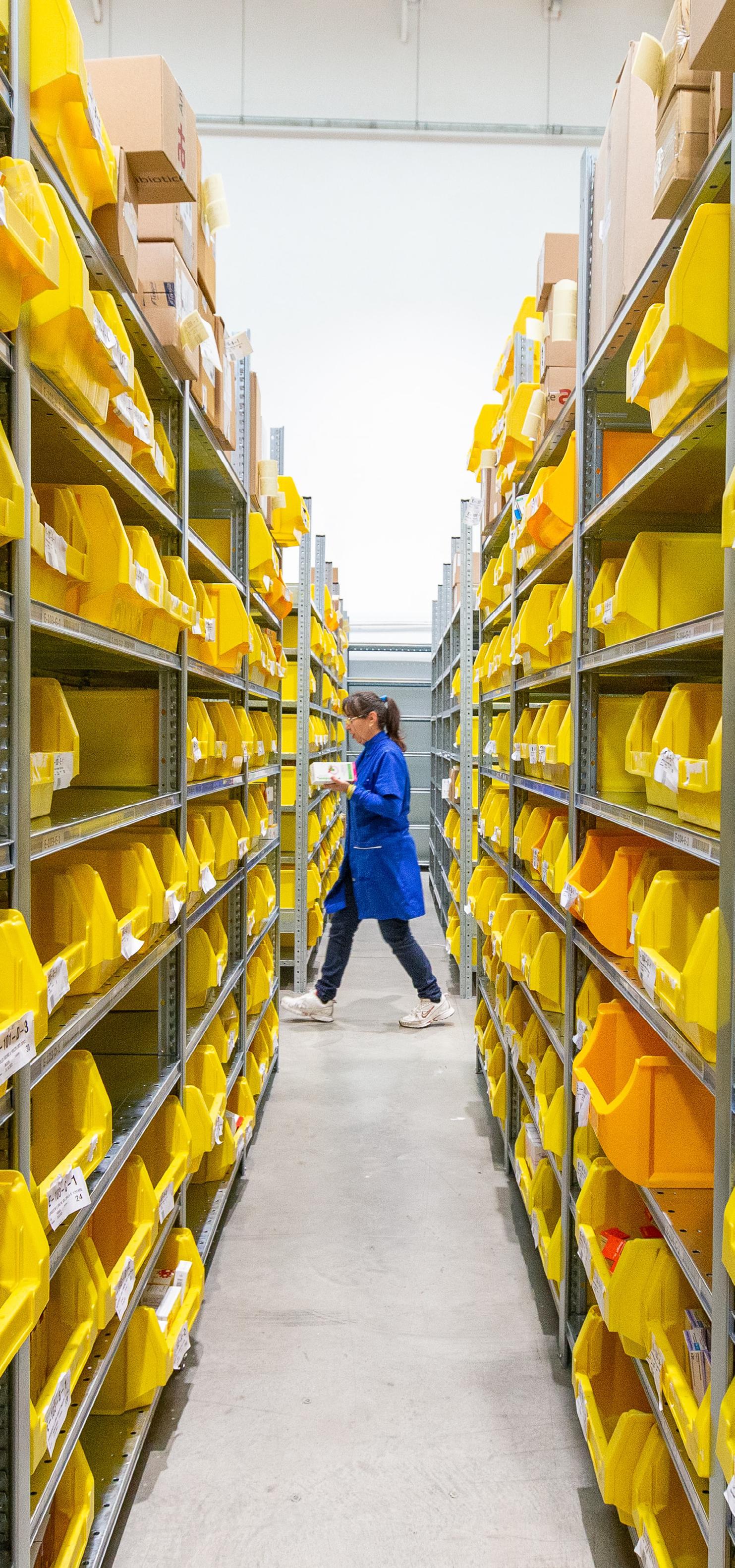
“With this approach, you can make quick and meaningful decisions about your supply chain in a much more accurate and speedy way than using traditional methods. The digital supply chain takes historical data and predictive analytics to allow you to look forward, whereas most data will only allow you to look backwards. By combining these two methods, you can use trend mapping to predict more accurately what will happen in the next two weeks – this is incredibly powerful when the consumer is demanding more from your brand,” he says.
Getting it right
According to Manhattan Associates’ Raghav Sibal, organisations are now asking themselves how to build resilience and flexibility in their supply chain to improve customer experience.
“This is the norm now; you absolutely must be agile and resilient, and the way to do this is to invest in the digitisation of your supply chain.”
Reducing split shipments, cutting down delivery times and providing complete visibility and information to the consumer about order status is becoming critical. “It’s really about inventory optimisation and omni-channel retail coming together and working together – getting this right is going to be hugely powerful in driving further customer experience and satisfaction,” Raghav says.
For TMX’s Travis Erridge, order management systems are set to play an increasingly critical role in the fight to win the customer experience battle.
“Order management systems that utilise big data and predictive analytics to prioritise what stock you hold where and when will have a huge impact on customer experience – we’re seeing a lot of organisations looking at upgrading and enhancing their capabilities in this space.” Royston says whether an organisation is big or small, digital investment is now mandatory to survive and potentially thrive, and they must be prepared to invest. “Organisations have to understand that they need to start digitising now. You would be surprised how many businesses still use spreadsheets to forecast. investment in this space is not cheap, it has to be considered a long-term investment that will protect market share and promote customer retention.”
“Businesses are investing in how to optimise their inventory further. They’re looking at how much to buy, where to store it, how to manage it, in order to fulfil orders more efficiently to improve the experience for the end consumer.”
Kings Transport: Accelerating Logistics Services with Data-Driven Decisions on Google Cloud
According to the Australian Department of Infrastructure, Transport, Regional Development, and Communications, the freight and logistics industry accounts for approximately 8.6% of GDP.
With growing consumer demand for eCommerce, logistic providers are under pressure to attract and retain customers with faster service at lower costs.

To stay competitive, Kings Transport, which specialises in on-demand courier, taxi truck, and business fleet services, is on a transformation journey to improve its resource management systems so that it can provide a more cost-effective and streamlined service. The company wants to use real-time data to identify new revenue opportunities and optimise transport resources. Kings Transport generates daily data from job bookings, route planning, delivery notifications, invoicing, and much more. However, the aging on-premises data centre lacked the compute resources and analytics capabilities to derive insights from data.
“Our on-premises data centre was at the end of its life cycle. It became challenging to add new workloads, such as data analytics, without worrying about reduced performance and downtime,” says Travis Timms, General Manager of Technology at Kings Transport. “In comparison, Google Cloud
provides scalable computing on demand to extract data insights for our business users and customers.”
“Another reason we chose Google Cloud is its vast worldwide networks,” Travis adds.
Kings Transport runs its cloud resources in the Sydney Google Cloud region to comply with the Australia Privacy Act and minimize latency for customers in the region. It uses Cloud Hybrid Connectivity to connect to a Melbourne data centre provider for data backup and disaster recovery.
“The robust global network of Google Cloud provides high availability connectivity to keep our services running without disruption, even if a machine or a data centre fails.”
“Cloud Interconnect gives us high bandwidth access to Google Cloud to keep data secure, without going over the public internet,” says Travis. “Virtual Private Cloud (VPC) gives us a redundant connection in a failover scenario.”
“Protecting our customer data is a top priority,” Travis adds. “We adopt rigorous Cloud Identity and Access Management to control access to data. Google Cloud provides an additional layer of cloud security by encrypting data at rest and in transit.”
Google Cloud Partner Oreta provided in-depth cloud expertise to Kings Transport during the twelvemonth migration process. The team took a mindful approach to cloud migration by reviewing what legacy applications to migrate or modernize. Kings Transport replicated mission-critical workloads such as its transport management system to a “bubble” test environment to make sure everything works well together on Google Cloud.
Scaling power to run queries on Compute Engine and App Engine
Google Cloud Compute Engine provides Kings Transport with a range of virtual machines optimised for different workloads, including its transport management system that requires 20 TB of storage. Most employees interact with this platform daily for job bookings, job despatching and monitoring, job viewing on a customer-based website portal, GPS, invoice management, and more.
Logistic providers like Kings Transport typically experience peak demand for delivery before Christmas and returns just after Christmas. On the legacy infrastructure, scaling was a laborious process that required setting up servers and configuring hardware. To handle such traffic spikes, Compute Engine seamlessly scales up to handle more user requests and scales back down when resources are no longer required.
Over the years, Kings Transport expanded its business and service offerings through organic growth and acquisitions. As a result, the company offers more than 500 service codes on the transport management system. The job booking process is complicated since customers have to select from the vast catalogue and quote the relevant one to schedule a pick-up.
To improve customer experience, the project transformation team plans to reduce the number of services by reviewing sales volume and profitability. This project involves an analysis of data from the transport management system.
“In the legacy environment, we needed at least a day to access and analyze data from our transport management system,” says Travis. “We can run the same workload on Google Cloud in under an hour.”
The IT team clones the transport management system in a bubble environment so other users on the platform won’t be affected. Once the project transformation team can access and analyse the data, IT shuts down the instance, so it’s not running round the clock.
“Compared to our on-premises server environment, pay-as-you-go billing on Compute
Engine lets us scale up or down VMs without having to worry about hardware provisioning or additional licensing,” says Travis.
Kings Transport also uses App Engine to host internal applications such as its various internally developed applications in a fully managed, serverless environment. App Engine automatically provisions servers and scales cloud instances up and down as traffic load increases or decreases. The IT team can focus on business demands instead of maintaining the infrastructure.
Robust reporting and analytics with BigQuery and Google Data Studio
The technology team at Kings Transport used to spend up to 80 hours a month running reports for colleagues in business development, account management, and operations. IT had to export data from the transport management system into spreadsheets and then manipulate it to meet reporting requirements.
For example, the Sales and Operations team looks at KPIs, such as delivery in full on time, account balances, and demurrage costs to track performance and identify issues.
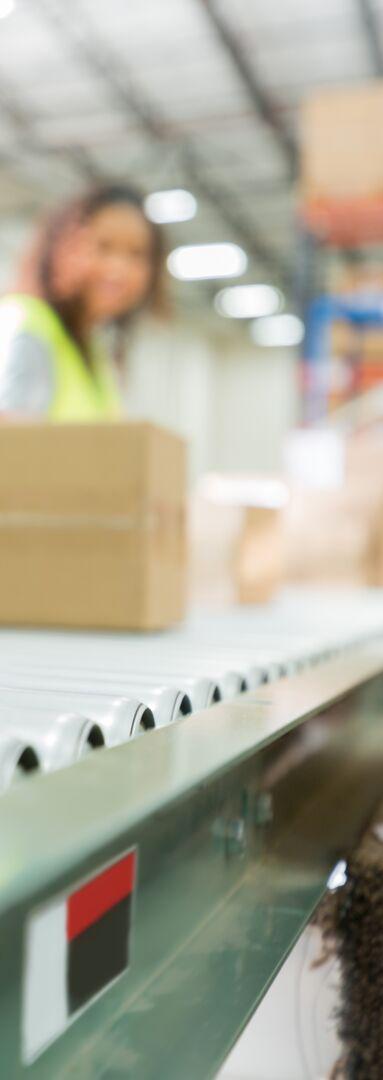
IT created an interactive dashboard by analysing enterprise data with BigQuery and connecting the results to Google Data Studio. Visualising data with Google Data Studio makes it easier for Kings Transport to view and analyse patterns and trends pertinent to the business. The dashboard refreshes BigQuery data regularly so the business users can see up-to-date results.
“Google Data Studio fills a massive gap that we had in the business, a reporting tool that makes data accessible for anyone in the organization,” says Travis. “Powered by BigQuery, Google Data Studio increases data visibility to improve business planning.”
Business users can easily create and share custom reports with Google Data Studio by adding KPI relevant to their reporting needs. For example, team leaders can analyse historical and current data to forecast trends and determine whether to scale up trucks and staffing. Kings Transport also utilizes Google Data Studio for lead and lag safety performance indicators which can be analysed at a Group level down to client operational sites, ensuring safety remains the utmost priority.
“Google Data Studio makes it easy for clients to access account performance at any time,” says Travis. “We build better relationships with our clients by being transparent about our service level. Internally and externally, we’re measuring and reporting the same metrics.”
“Our focus this year is to create an Enterprise Data Warehouse to accelerate transformation with datadriven insights,” he adds. “Using BigQuery on Google Cloud, we get high-speed analysis of data at scale without worrying about hardware constraints.” ●
Supply Chain Crisis Management: How Technology Can Help Build Resilience into Your Logistics Network
WRITTEN BY MICHAEL DYSON VP OF SALES, APAC AT SOTITraditional supply chains are struggling to keep up with heightened customer expectations, increased regulations, and outside influences on the market — including how to pivot operations in response to global pandemics.
A successful post-pandemic supply chain can be summarised in two words: diversity and resilience. Supply chain diversity means having multiple suppliers to choose from when procuring raw materials, manufacturing, warehouse storage and shipping. Meanwhile, supply chain resilience is the ability to bounce back when a disruption occurs.
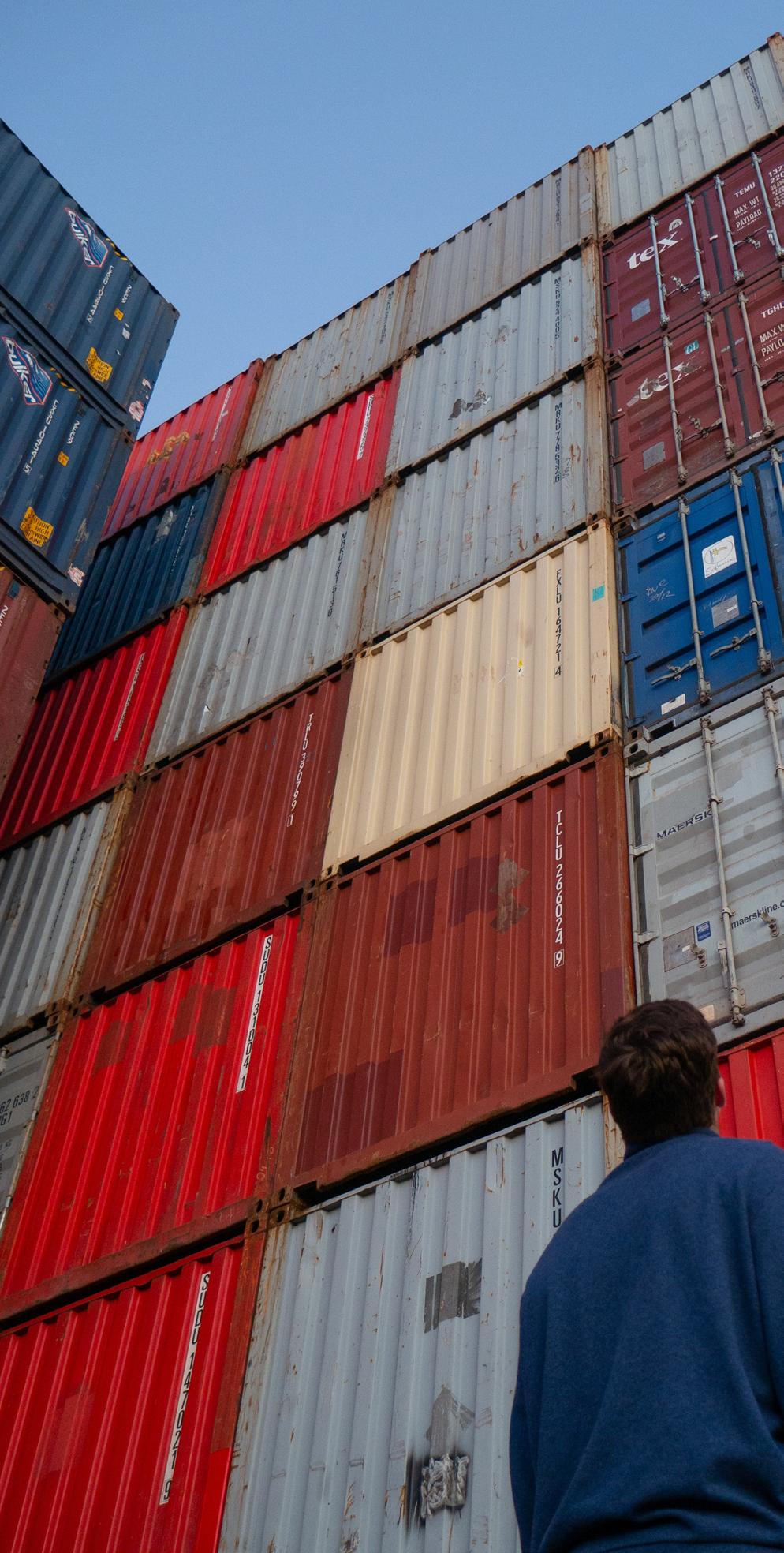
If you think of the supply chain literally, you might picture a linked chain with a beginning and an end. It goes in one direction, and everything is connected. The current global supply chain crisis broke some of those links, preventing goods from moving smoothly along the chain.
A successful post-pandemic supply chain is like a networked web with different access points, meaning if one route is unavailable, another one is open. For example, if one microchip supplier is experiencing a
delay or shortage, an organisation can easily pivot to an alternative supplier without disrupting operations.
Mobile Technology and Digitisation Can Support Your Supply Chain Operations
If diversity and resilience are the destination endpoints for the post-pandemic supply chain, mobile technology and digitisation can help companies get there.
Even before the pandemic, the shift toward digitisation was underway globally. As far back as 2016, 70% of executives had already started the digital transformation of their supply chains. COVID-19 magnified the importance of the digital supply chain. Even when companies were shuttered
and revenues dried up, 92% of businesses did not halt technology investments in the supply chain.
So, how can mobile technology help support an effective supply chain?
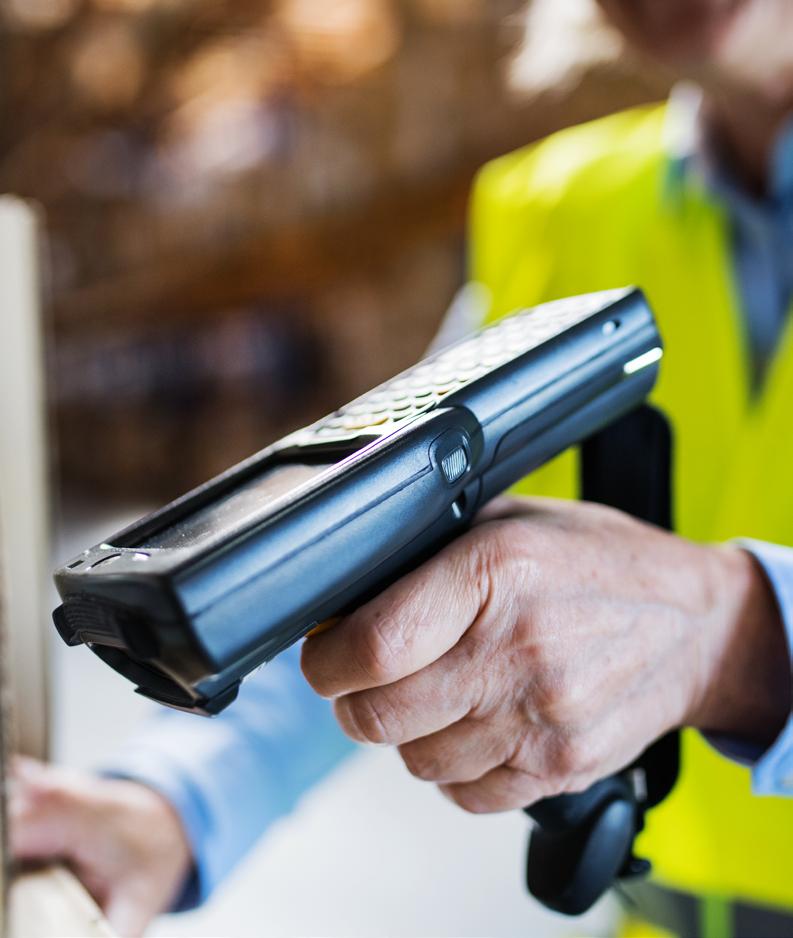
• Forecasting: At the outset of the pandemic, there was a 186% spike in toilet paper purchases. Then a spike in hobby items. All this is to say consumer behaviour is unpredictable and leveraging historical trends to predict future ones is not always reliable. Artificial Intelligence (AI) and machine learning can help direct companies on everything from inventory recommendations to distribution strategies. In fact, 90% of supply chain professionals believe AI will transform the supply chain by 2025.
• Quickly onboarding talent: Australian supply chain professionals are aware of the staff shortages across trucking, warehouse and delivery services. Technology can be used to attract and retain talent. Because of the supply chain crisis, management and human resources (HR) departments want to onboard new workers as quickly as possible. Technology can help by making learning content accessible through remote devices via an Enterprise Mobility Management (EMM) solution or apps rather than in-class instruction.
• Mobile barcoding: In global supply chain crisis management, mobile barcoding has numerous benefits. First, it digitises the pen-and-paper processes 55% of supply chain organisations still employ. This ensures data is captured accurately and shared quickly. Second, it eliminates hand-tohand paper transfers and typing into a common workstation, giving peace of mind to workers mindful of social distancing.
Supply Chain Efficiency and Transparency are Key to Customer Satisfaction
The disruption experienced through the pandemic highlighted complexities in the supply chain and the struggles the sector faces in delivering against fluctuating demand. The rise in transport costs, shortages of materials, breaks in the supply chain, and surges in demand created a chaotic period of adjustment. Now, transportation and logistics (T&L) organisations need more agile day-by-day operations and must also ensure customer expectations are met. Research shows that 57% of customers are frustrated by the shipping/delivery/returns aspects of ordering online.
Today, logistics is not just concerned with the delivery of goods on time but also with the visibility of data throughout the supply chain, effective communication and setting expectations throughout the logistics chain. Keeping customers informed along this path is crucial, and companies need
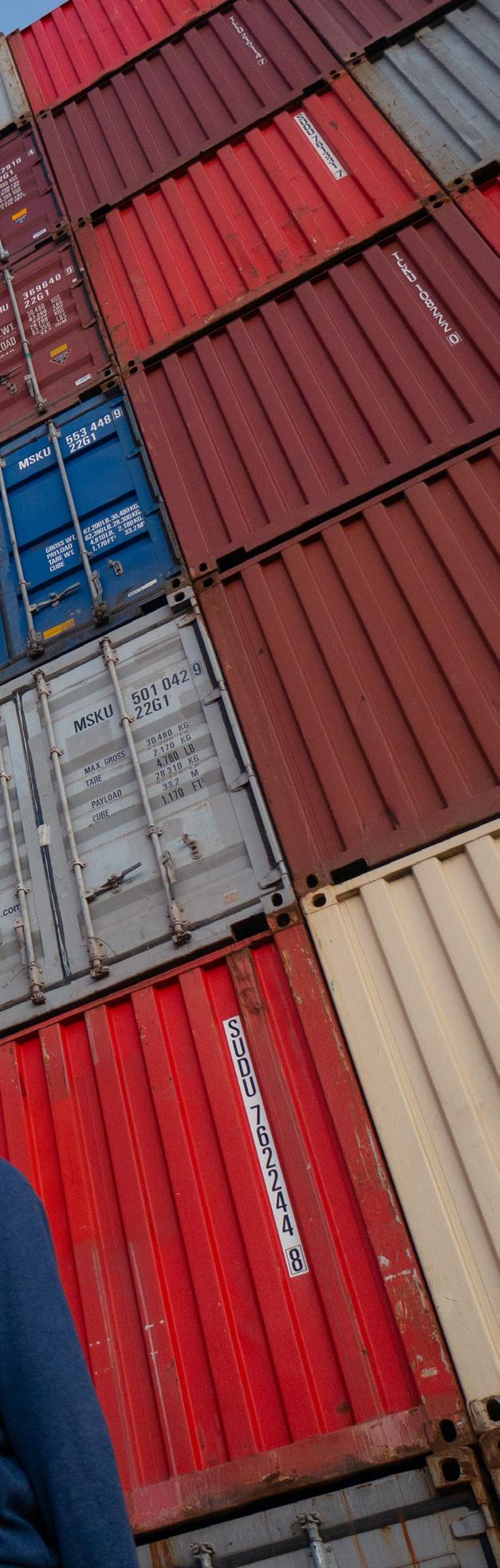
strong, reliable, usable and real-time data to meet customer expectations. By improving the efficiency of product delivery, supply chain traceability and customer communication, businesses can create a loyal customer base and better predict demand.
Manage Mobile Devices to Avoid Downtime and Disruption
While it is clear mobile technologies can enable Australian supply chains, these devices must be managed properly. When devices are in the field, companies do not have visibility into them. They are unable to hold or touch the device to remediate issues. Without remote access and monitoring software, companies do not know when issues are occurring, what’s causing costly device downtime, and how to solve the problem and improve future device performance.
To get the most from your mobile investments and gain a significant return on investment (ROI), supply chain organisations can use a diagnostic intelligence solution, like SOTI XSight, to reduce costly downtime.
SOTI XSight allows organisations to pull critical data, such as battery health, and accurately determine the right time to replace batteries. Users can closely monitor device performance through app usage, data usage and signal strength analytics. IT managers responsible for mobile devices across trucking fleets can even set up watchlist parameters for battery drainage, data consumption and physical damage. When devices exceed those established parameters, they are instantly notified and can take proactive action to address the issue quickly. If an issue arises, SOTI XSight provides instant access to device logs, profiles, statistics and configurations to troubleshoot mobile issues occurring in the field. ●
For more information, please click here.
Late-Stage Order Cancellation Improves Customer Experience & Environmental Impact of eCommerce
Online shopping returns are a growing challenge for retailers around the world, accounting for over $400 billion in lost sales for U.S. retailers in the year 2020 alone, according to the National Retail Federation. Many Australian retailers are also seeing a significant portion of their online sales being returned by customers after shipping.
With late-stage order cancellations becoming a growing issue for Australian retailers trying to balance customer demands against the capabilities of current systems, Manhattan Associates’ new latestage order cancellation solution means orders can be cancelled up to the point of manifested/loaded status.
"Customers often change their minds. It is part of doing business. How a company wishes to react should be a business decision, not simply constrained by a retailer’s system capabilities," said Raghav Sibal, Managing Director, ANZ, Manhattan Associates.
"Previously, when customers decided to cancel an order, they might not be able to depending on how quickly the order was dropped to the warehouse. In most cases, the order could not be cancelled once it was allocated, limiting the timeframe customers could change their mind before an unwanted shipment was sent on its way," Sibal continued.
Manhattan’s new late-stage order cancellation capability allows retailers to amend and cancel orders right up to the moment the truck leaves. This gives retailers more flexibility in handling latestage cancellations, enhances the customer experience and negates the costly carbon footprint often associated with returns processes.
"Retail systems should not restrict consumer behaviour, so we’ve introduced the ability to cancel orders in our Warehouse Management System (WMS) much later in the fulfilment lifecycle. Not only does that improve customer satisfaction, but it also reduces shipping waste and the unwanted carbon footprint associated returns," Sibal added.

The new late-stage order cancellation capabilities build on Manhattan Associates’ existing digital self-service capabilities,
which allow customers to cancel items being shipped to their address from a distribution centre (DC) or a store without reaching out to a contact centre.
"We’ve all been in a position where we’d like to be able to amend or cancel an online order, but the ‘point of no return’ or ‘remorse period’ has been reached. When these situations occur, it causes friction and frustration for the customer who has to return the item, not to mention the time and cost for the retailer, who will often have to absorb the shipping, handling and environmental costs of the return.
“With Manhattan’s latest order cancellation capabilities, all these issues can be resolved at source, making for happier customers, better margins for the retailer and lesser impact on the environment – a triple threat of benefits that everyone can get behind,” finished Sibal. ●
This process allows brands to offer an extended window of opportunity for customer cancellation, preventing unwanted shipments and costly returns, both financially, and environmentally.
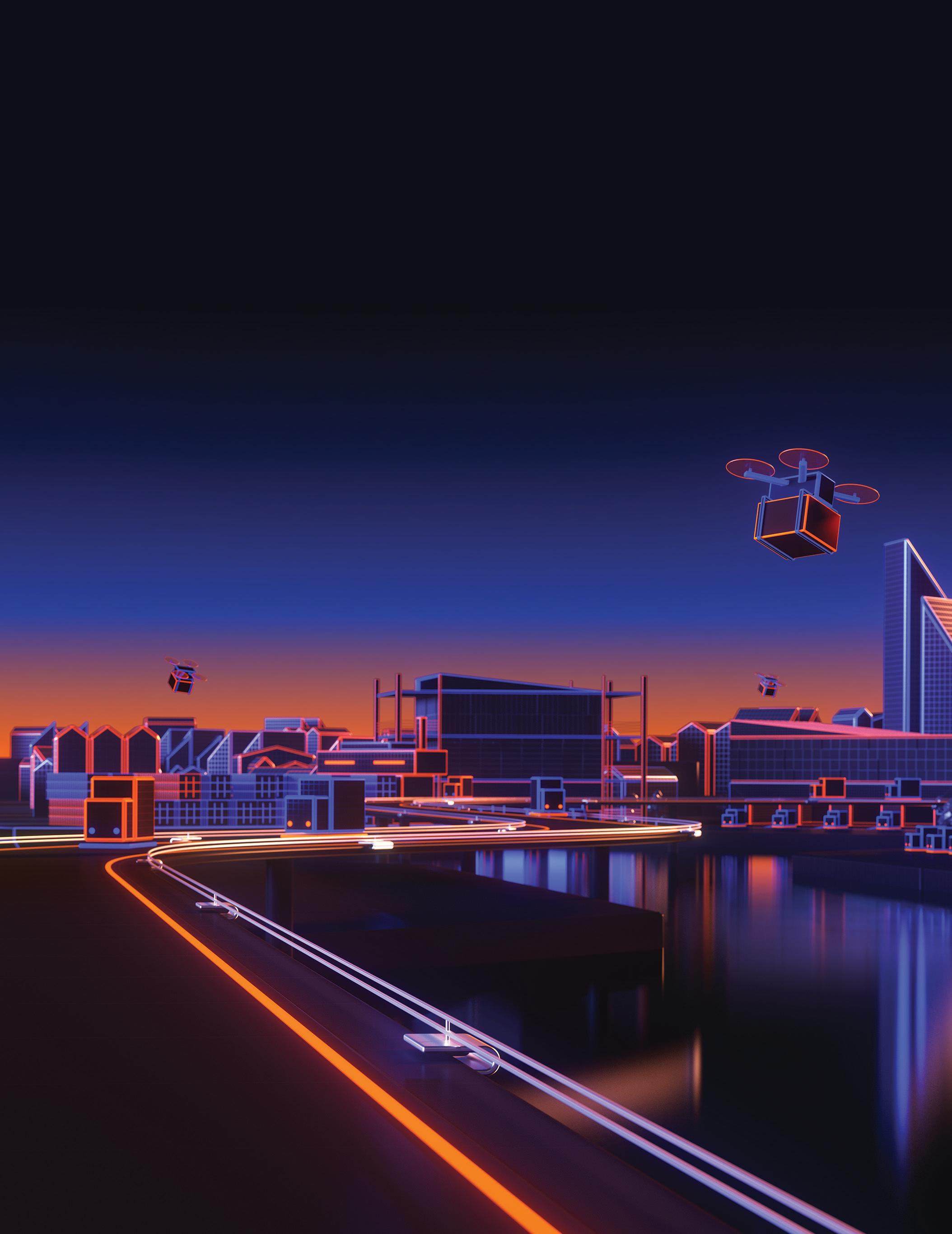

How LowCode Helps Organisations Address Supply Chain Challenges
WRITTEN BY LUKE THOMAS AREA VICE PRESIDENT, ASIA PACIFIC, APPIANThe Covid-19 pandemic dramatically exposed the fragility of global supply chains. Extended lockdowns disrupted supply, demand, and logistics, with customers and communities experiencing widespread shortages and frustrating delays.
As businesses recover from the pandemic, the flow of raw materials and finished goods remains an ongoing challenge for the global economy.
An Ernst & Young (EY) survey of 200 senior supply chain executives from large companies showed that 60 per cent of respondents believe the supply chain has increased in strategic importance. The survey also revealed that organisations are seeking ways to make their supply chains more resilient, collaborative, and networked.
Many companies experience supply chain disruptions because they still use manual processes, inflexible legacy systems and spreadsheet tracking for asset management. This creates silos and limits enterprise-wide visibility across high-priority assets such as equipment, machinery, vehicles, and factories. A lack of control and visibility impacts not only performance, production and service delivery but, ultimately, customer satisfaction.
Digital increases responsiveness
Digital supply chains can help organisations navigate disruptive forces and respond faster to volatile international supply and demand.
Sixty-four per cent of supply chain executives surveyed in the EY survey predicted that the pandemic would accelerate digital transformation. Fifty-two per cent said that autonomous supply chain, including automated planning, is either already here or will be by 2025.
A wide range of complex but repeatable tasks require large amounts of data at all stages along the supply chain. Automation can help transform key aspects of supply chain management, including automating workflows, more effectively leveraging asset data, and improving operational visibility.
However, simply utilising digital technologies does not create a digitised, autonomous supply chain. This requires connected supply chain technologies across planning, procurement, manufacturing, and logistics that work beyond a company’s four walls.
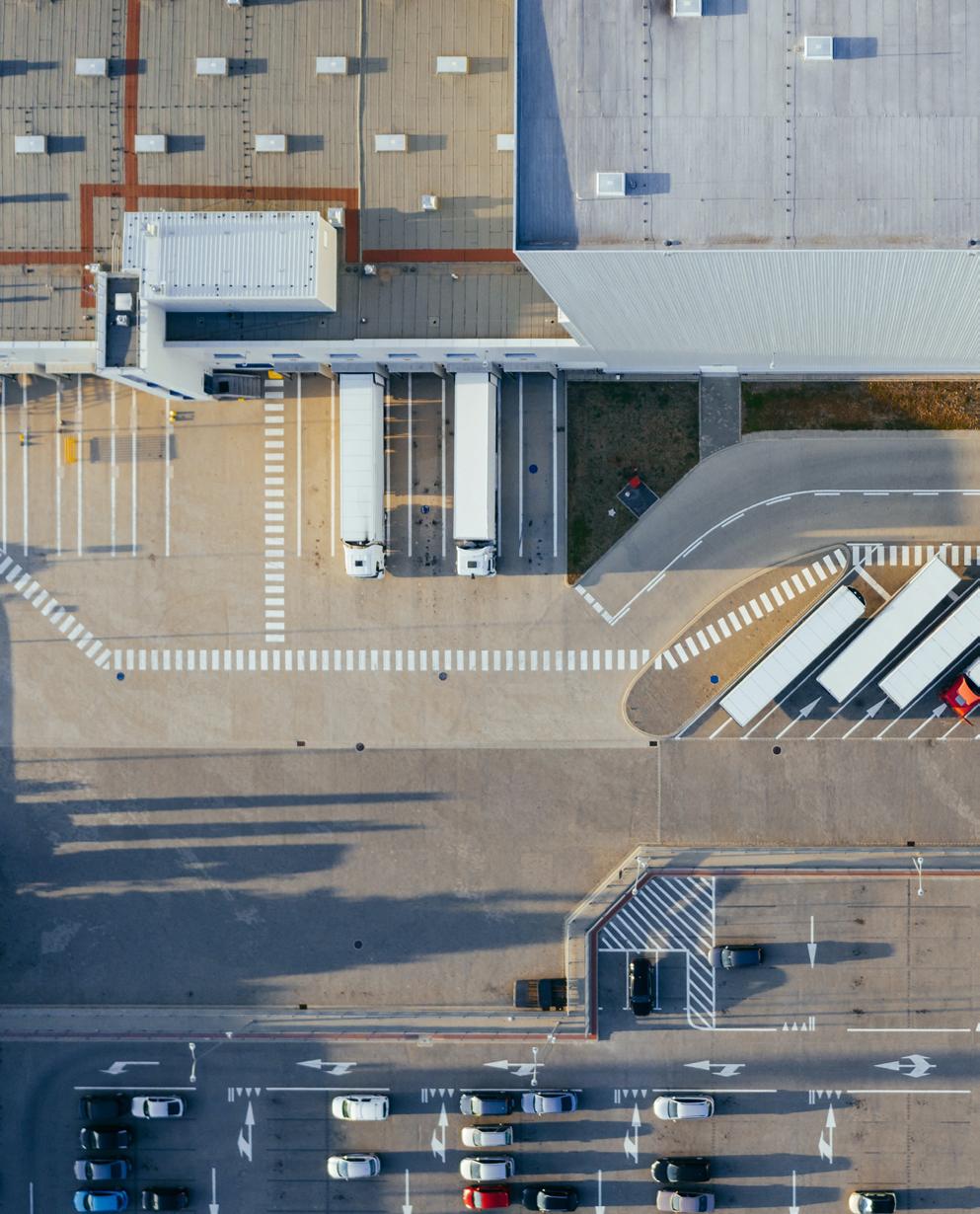
How low-code improves supply chain management flexibility
Low-code allows companies to optimise supply chain management and mitigate risk by using a flexible, unified development platform that allows them to build and customise software to meet evolving market needs.
Supply chain management is complicated and challenging, but low-code solutions excel at tackling
complex problems. The most effective platforms combine multiple automation tools such as robotic process automation, artificial intelligence, business rules, and intelligent document processing. This combination provides the right tools for a diversity of tasks, from automating communication to integrating data with legacy systems.
The advantages of low-code for supply chain include:
Increase visibility and connectivity
The EY survey found that supply chain visibility will become the respondents’ number one priority over the next three years. It also found that with the need for increased visibility across hundreds or thousands of suppliers, there is already a shift from linear supply chains to more integrated networks connecting various players.
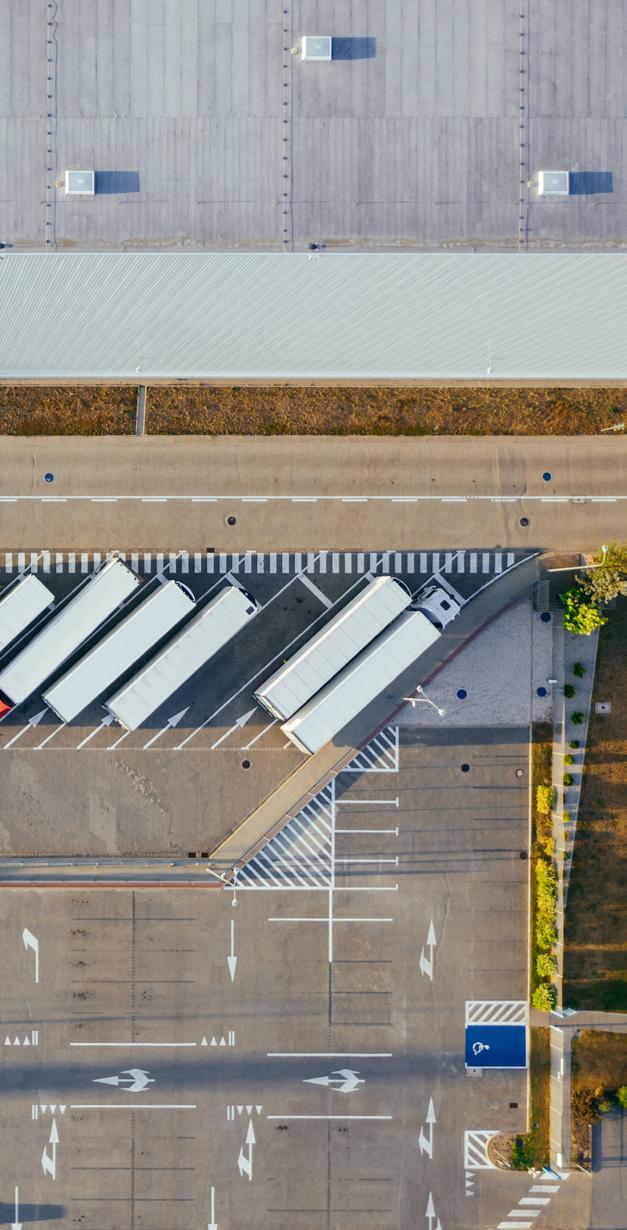
Many companies still rely on multiple systems such as enterprise resource planning (ERP), warehouse management, transportation management, and sometimes manual systems. Low-code makes it easier to connect disparate technology solutions, even if they lack modern APIs. It also lets you connect and share data with supplier and customer systems and helps teams make decisions faster.
Providing workers with mobility as they go about their daily tasks can further increase operational efficiencies. Look for a platform that can create mobile-native applications and ensure off-line access in remote or hard-to-connect-to areas.
Improves customer communications
The explosion in online shopping during the pandemic increased customer expectations. People now demand a seamless customer journey and delivery times that rival behemoths like Amazon.
At a time when customer service teams are experiencing unprecedented pressure, low-code platforms empower customers to solve their issues with self-service options.
Web portals allow customers to find information on their order and delivery status. Automation features like bots and business logic can automatically craft and send notifications to customers when scheduled deliveries are missed. Combining these features lets teams proactively notify customers via email when shipping may be delayed, then lets them follow delivery status via portals.
A low-code platform also allows companies to improve communication and collaboration with suppliers by connecting with supplier systems. Teams can learn about delays or shortages and plan accordingly.
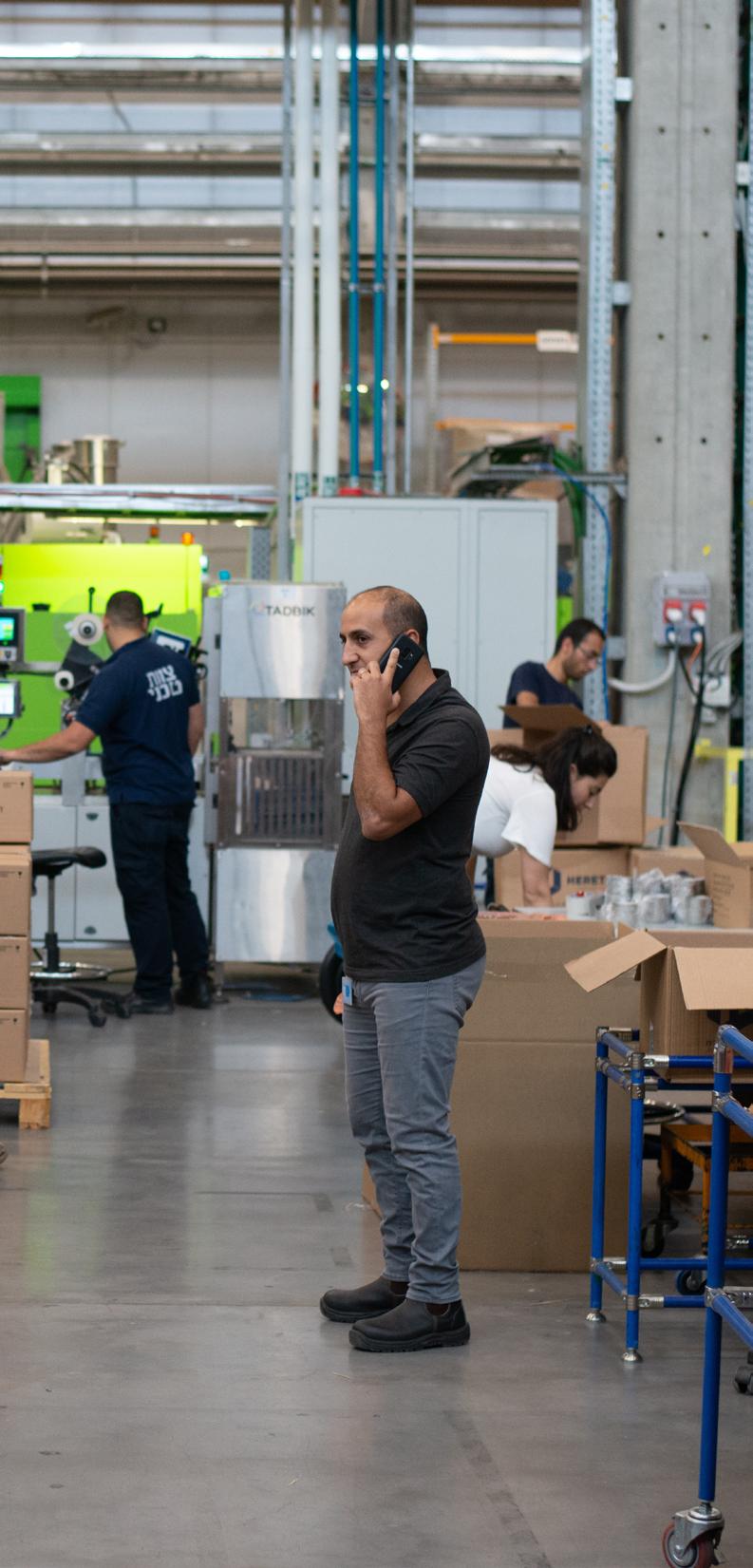
Other transformation opportunities include vendor onboarding, inbound supply management and supply chain planning that encompasses sales, marketing, demand management, production, inventory management, and new product introduction.
Discovering process inefficiencies is key.
Unlike other low-code platforms, Appian has process mining tools that help uncover and address workflow bottlenecks and deviations.
Process mining is a critical component of business transformation because organisations often don’t understand how their work is carried out at an operational level. Process mining allows businesses to solve process challenges and inefficiencies based on data rather than assumptions and intuition.
Appian’s process mining tools are an essential first step to digital transformation. The tools are supported by workflow design capabilities that allow the platform to build powerful applications to orchestrate processes and automation. The benefits include internal cost and time savings, an empowered workforce, increased transparency, and a supply chain consistently delivering a superior customer experience. ●
For more information, please click here.
How Automation Can Help Optimise Your Distribution Processes Today

Businesses face increasing supply chain pressures associated with shorter lead times, competitive pricing and heightened consumer delivery expectations.
For online orders, customers want the cheapest price, fast deliveries, up-to-date information on stock availability, access to the real-time status of their orders and seamless return options.
Additionally, businesses continue to contend with increasing labour costs (let alone finding and keeping workers) and rising land costs (especially finding land where they need it). There are further pressures from increased regulation and safety requirements and supply chain disruptions, be they from pandemics, natural disasters or geopolitical tensions.
The booming growth of e-Commerce, the recent supply chain disruptions exacerbated by the pandemic, and other recent developments have only amplified these challenges around labour, land and meeting customer expectations. However, there is a way businesses can ease these impacts. As this new age of retail and e-Commerce coerces the supply chain to work faster and harder than ever, warehouse optimisation and automated technologies introduce scalability, resilience and agility into their operations and are proving to be effective in helping businesses to streamline their processes.
WRITTENThe imperative to optimise
Whether your business is feeling the pressures of a changing market and consumer landscape or looking to adopt leaner processes to help with operational speed, efficiency, and costs – optimising supply chains and distribution has never been as important as it is now.
In today’s retail environment, it is the consumer who has all of the power. If you don’t have what they want in the right size, the right colour, or at the right price and in the right place, that sale will almost certainly be lost. With the current uptake in online shopping, it has become seemingly easy for consumers to find what they want – though, who’s to say that they will turn to your store and not your competitors who are just a web search away? While online shopping is not a new concept to retailers, the pandemic gave consumers an accelerated nudge in that direction. In fact, in just the first eight weeks of the pandemic, e-Commerce spending grew significantly, with some major retailers announcing an 80% growth in online orders during that period.
This trend is still going strong. In 2022, global sales made from online purchases are expected to reach 21%, representing a 17.9% increase in e-Commerce market share over the past two years. And that growth is expected to continue throughout this year and beyond, predicted to reach an increase of 24.5% by 2025. So, what can retailers do to prepare themselves and leap ahead of the competition?
The answer to preparing and succeeding in whatever the future market holds is adopting a strategy to optimise operations. This must be built to meet and exceed consumer expectations, ensure product availability, minimise costs, provide the fastest delivery, eliminate errors and product damage, and offer seamless returns.
Optimisation falls into three broad categories: processes, human efficiency, and inventory management.
Optimised processes make for streamlined operations
Processes provide the structure for supply chains to function, and companies must continuously review and optimise processes as a way of increasing productivity by removing non-value adding activities, reducing errors, and increasing the speed of operations. This also includes streamlining processes to eliminate touches (the number of times workers need to handle a product), reducing operator travel (a major non-valueadding task in manual picking operations), combining processes (such as batch picking products for multiple orders or doing stock take checks while picking), and introducing checks and balances. New technologies and software can then take productivity to the next level when processes are optimised.
While streamlining processes does improve the human factor – particularly by reducing non-value adding activities like travel – operations should also look to optimise worker activities to use their time better and increase their speed and accuracy.
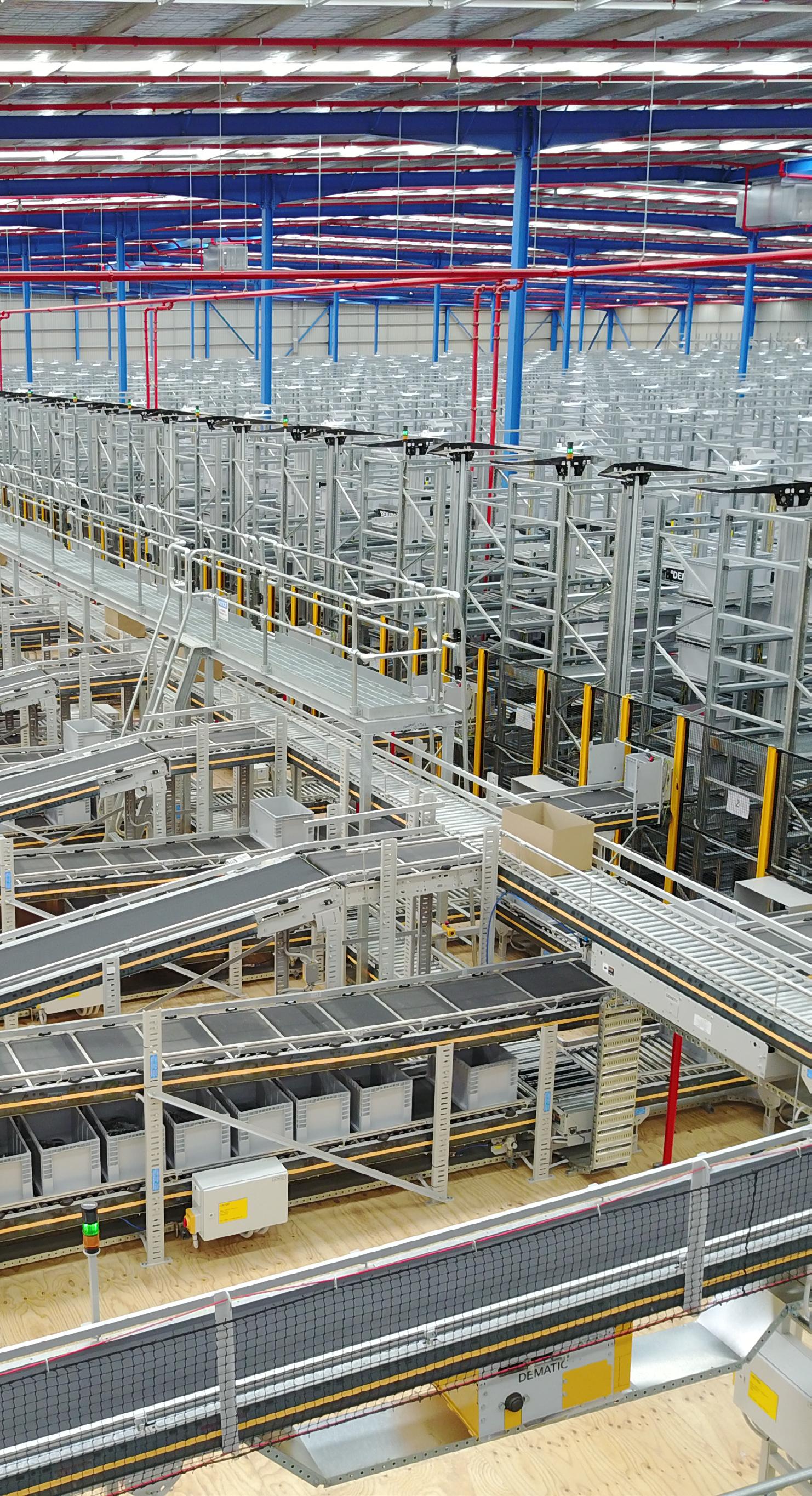
Human Efficiency
Opportunities for optimisation become available when you know how, when, and how often tasks are performed. From here, you can streamline operations, reduce repetition, limit the number of touches, improve operator ergonomics, reduce training time for new users, and improve the overall worker environment.
Optimising tasks for workers often include providing real-time instructions via a mobile computer or audio headsets, which has the added benefit of increased speed, having workers confirm actions in real-time to improve accuracy, operational visibility, and labour management, and optimising ergonomics for improved safety and speed.
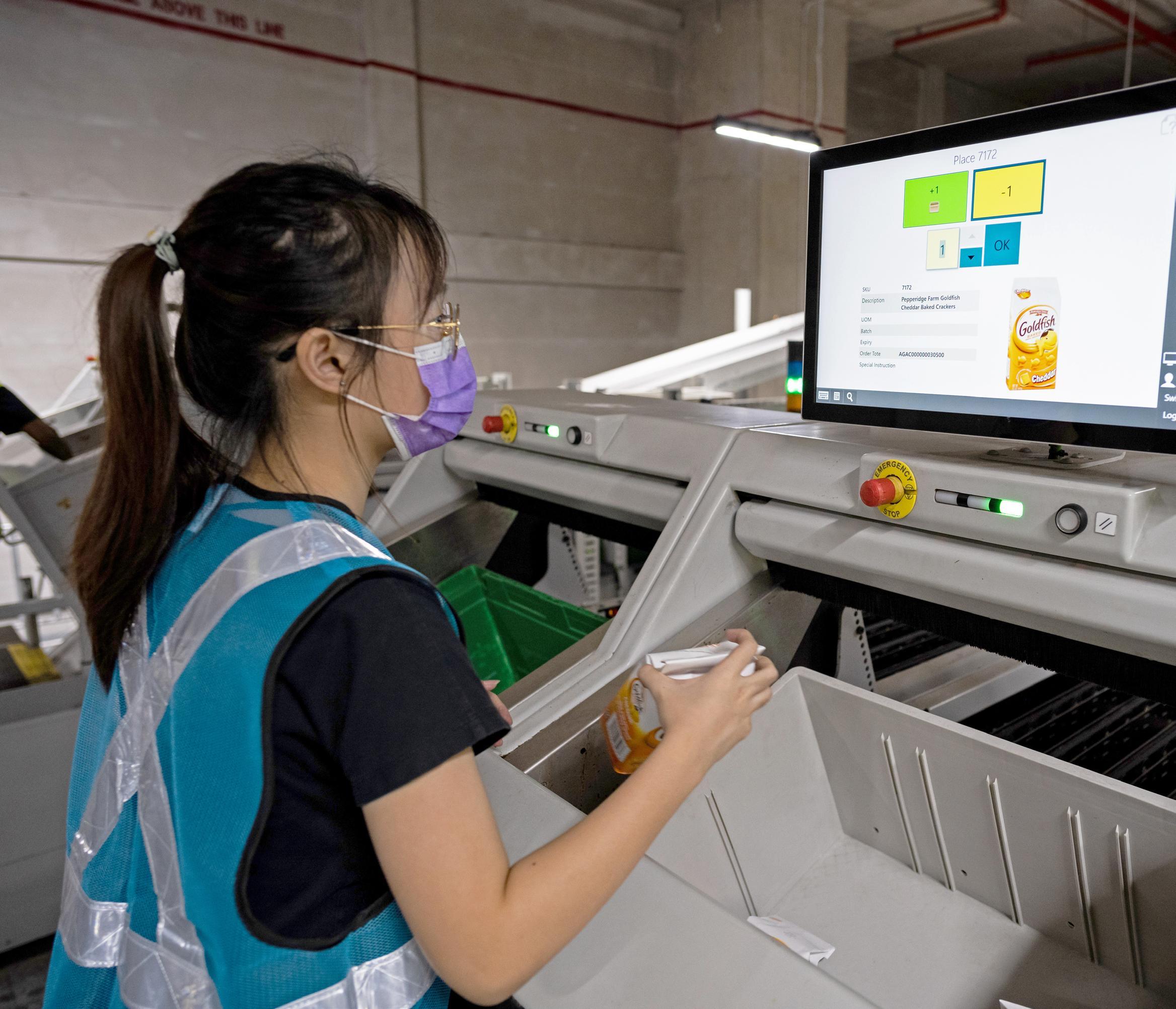
Inventory management is key
Inventory storage is constantly changing, and efficiencies of space and movement must be continuously reviewed. Storage has moved on from a simple static operation to dynamic storage, which provides further optimisation benefits. Carton and/or tote storage and buffering technology like Dematic’s Multishuttle or Autostore systems are increasingly being used to manage inventory in distribution centres (DCs) to maximise capacity and stock accessibility. Additionally, Automated Guided Vehicles (AGVs) and mobile robotic and shuttle systems have become dynamic storage solutions that maximise reliability, agility and accuracy when managing inventory in the warehouse.
Real-time and operation-wide data provides further potential for optimising inventory. Optimising inventory and its management can maximise storage capacity (e.g., by increasing storage density and more effectively using headroom), optimise stock accessibility and the speed at which a product is transported between applications, centralise inventory to get efficiencies in scale and reduce the required level of safety stock, and locate inventory close to consumers to improve delivery speeds.
Make your workers more effective
One of the most effective strategies for distribution logistics success uses a concept where travel is eliminated altogether in a DC. Goods-to-Person (GTP) takes advantage of the power of data combined with high-efficiency buffering and sequencing systems such as the Dematic Multishuttle or the highly compact Autostore system. In high-volume item picking operations, items for orders can be stored, sequenced, and delivered to workers in the order in which they need them.
In a GTP system, workers stay in ergonomically designed high-rate workstations that optimise productivity, efficiency, and safety. The orders and items required to fulfil the orders arrive at the workstation precisely when needed. Workstations can facilitate discrete or batch picking and can be configured to fulfil one or more open orders at a time, depending on order processing needs – for example, whether for a store, online order fulfilment, or both.
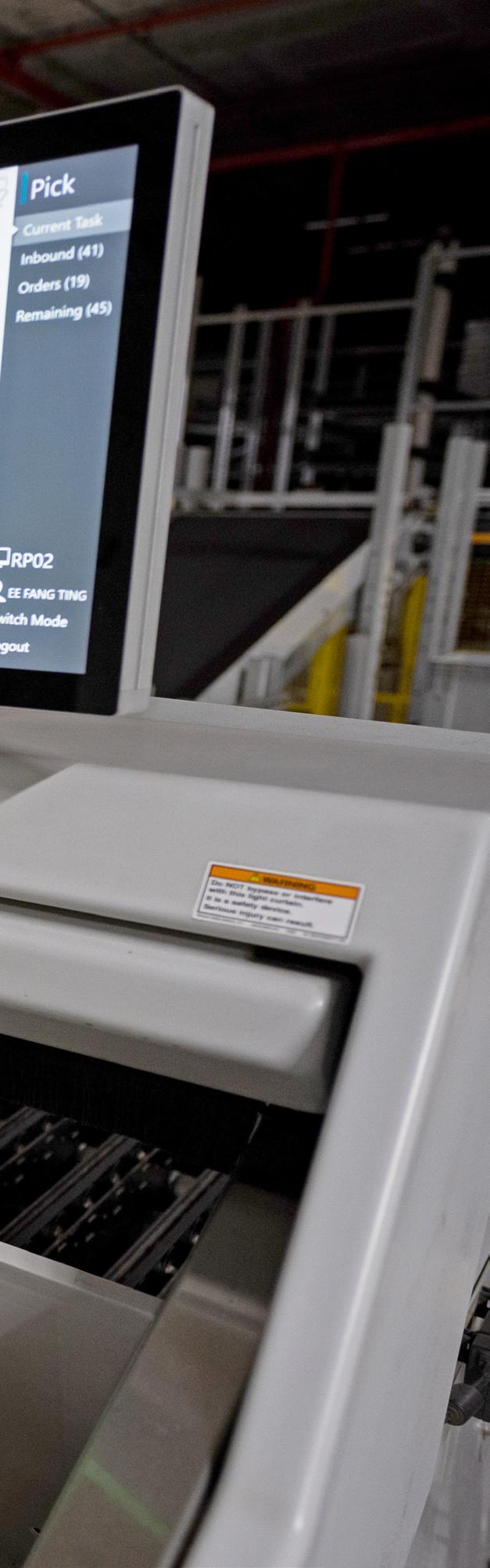
Case Study: Toll’s advanced retail & e-Commerce fulfilment centre
In collaboration with Dematic, Toll Group enhanced its retail operations by constructing a new facility for a major apparel retailer. The 32,00 square metre DC now has 15,600 square metres worth of automation equipment, which picks, processes and packs up to 375,000 items per day – significantly reducing delivery timeframes from days to hours.
Together with a fleet of 10 AGVs and a GTP picking solution, Toll’s investment in the new optimised facility helped its customers adapt to the new retail environment. The facility was equipped with advanced automation technology so retailers could deliver their e-Commerce orders faster, and in a much more economical way. The facility was also designed to handle 170,000 units per day and is scalable to cater for seasonality and growth, and to provide the high flexibility needed in a 3PL.
As a result, retailers benefit from the ability
to deliver goods to their stores and directly to customers faster and more cost-effectively, with customers also enjoying flexible order times and faster order processing, receiving their purchases within hours instead of days or weeks.
Optimisation with information
Optimisation occurs when we analyse information relating to processes, human factors, and inventory. Analysis and analytics tools provide a continuous improvement environment to reduce waste such as non-value adding tasks, unnecessary space, and costly mistakes. Industry 4.0 capabilities provide a seamless interface between humans, products, automation, robotics, big data and operational visibility, thereby maximising performance and responsiveness to operational and customer demands.
By having a robust and real-time integration between software platforms across the supply chain linked to key automation technologies like AGVs, AS/RS and GTP systems, businesses can optimise their supply chains and improve worker efficiency, operational processes, and inventory management. These steps can enable businesses to effectively safeguard themselves from future disruptions or demand peaks and thrive in the future retail market.
Dematic has worked with a consultive approach on thousands of projects with many of the world’s most successful businesses and can provide unique global insights by focusing on optimising processes, human activities, and inventory. ●
For more information, please click here.
Even retail stores have become dynamic warehouses in the e-Commerce world, similar to how trucks have become warehouses on the road.
Knowing which strategies to apply as well as knowing where and when to apply them is key to your business success. There is no onesize-fits-all solution – every supply chain is different, so each solution and strategy is unique. Addressing distribution challenges requires gathering information and using insights to assess multiple strategies to see how they might apply to your particular facility.
Why ACRs Should Lead Your Warehouse Automation Project
WRITTEN BY JULIAN BRANCACCIO NATIONAL DIRECTOR OF SALES ANZ FOR HAI ROBOTICSNever before has the competition for warehouse and fulfilment labour been so fierce, strongly driven by sustained growth in B2C channels. In the short term, businesses are having to offer higher wages, bonuses and flexible working conditions to attract staff. But the long-term implications of increased reliance on labour and manual processes are clear: automation in warehousing is no longer just nice to have but an imperative for sustainable growth. In such an environment, ACR systems allow DCs to meet demand in a flexible and highly efficient manner. Business operators can drastically elevate warehouse throughput by adding ACRs or highspeed loading and unloading workstations without refitting existing facilities. And unlike traditional automation solutions that require months-long planning and year-long implementation, the ACR systems can be easily deployed in several weeks, bringing little disruption to ongoing operations.
Higher pick rate with huge SKUs
Huge and ever-changing SKUs are common with e-commerce and retail orders, making piece-picking a heavy and laborious duty in warehouses. ACRs that move totes/cartons instead of a whole rack are adept at order fulfilment in such scenarios. By planning efficient picking routes to reduce travel time and establishing organized picking processes, the ACR systems enable more efficient order fulfilment with less human intervention and fewer human errors.
Higher space utilisation
ACRs boast a picking height of up to 10 meters, meaning that almost every inch under the ceiling of a 10-meter warehouse can be used for storage. This feature sets ACR systems apart from rack-moving systems that generally cover a space of no higher than 4 meters. Meanwhile, a greater storage density can be achieved with the same shelf height when using the
ACR systems. The slim ACR chassis design allows narrower aisle width, and precise picking supported by AI algorithms permits more efficient use of shelf space.
How ACRs have helped Booktopia to increase capacity and improve fulfilment
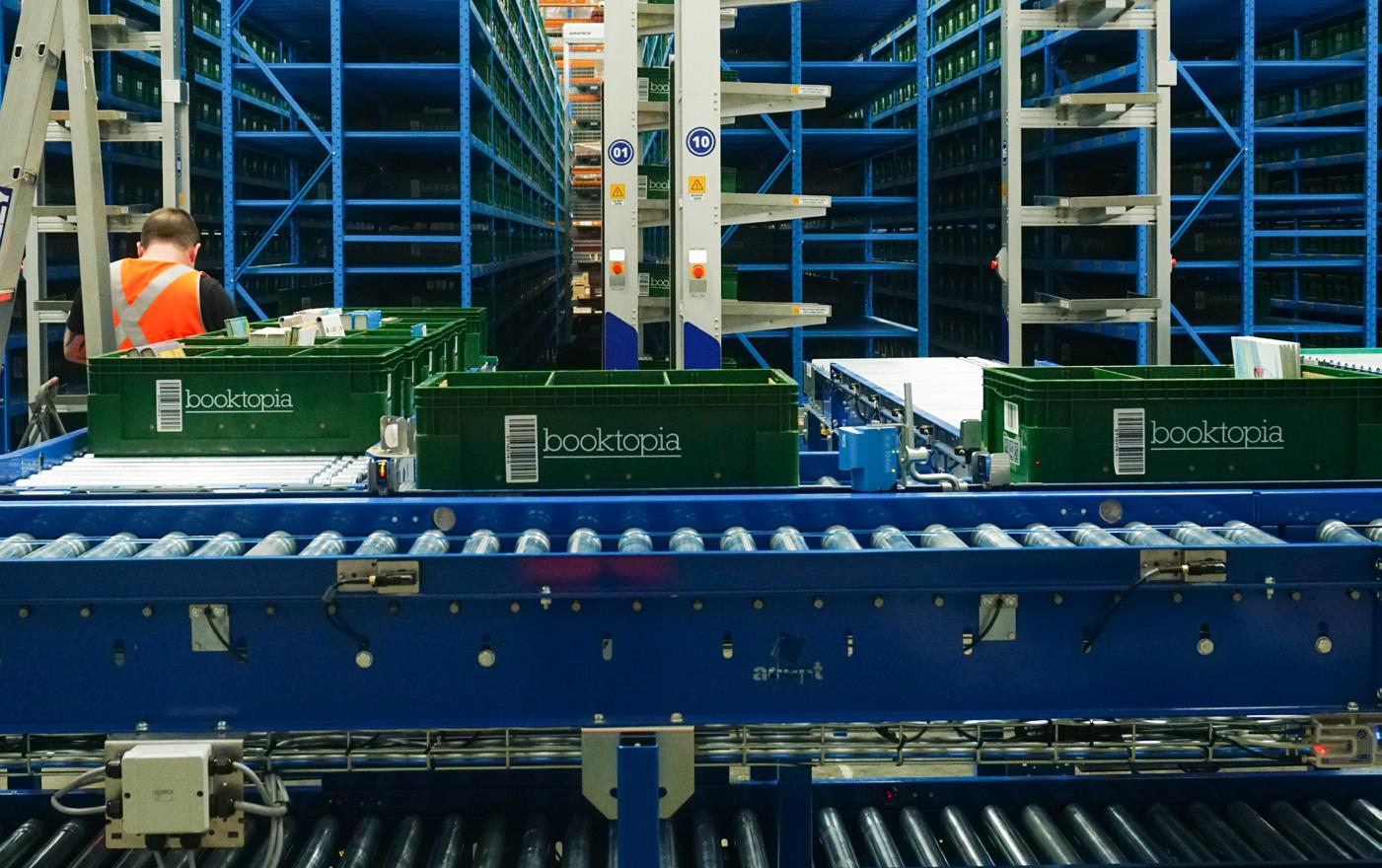
Australia's largest online bookstore Booktopia deployed ACR technology to increase capacity and improve fulfilment and putaway rates at its national distribution centre (DC) in Lidcombe, NSW. For the past seven years, Booktopia has been exploring ways to add storage and packing capacity to its existing DC. While capacity was the key driving factor for the project, the efficiency improvements for picking and putaway also gave Booktopia further opportunities to improve the customer experience.
ACR technology from Hai Robotics allowed Booktopia to improve its putaway rates by an impressive 800 %. The robots use 3D visual recognition technology to identify goods without codes, resulting in faster inventory counts through shelf scanning. It supports multi-size cartons and tote picking and can be applied to multiple business needs. Furthermore, the robots use artificial intelligence technology to establish which SKUs are in demand and will re-organize the inventory accordingly, resulting in further efficiencies.
"For example, our dock is now much more efficient as we can put away so much faster so we can ingest stock more quickly."
●
Wayne Baskin, CTO at Booktopia, said: "With this solution, the efficiencies we get from pick and putaway drive efficiencies in other areas of the business.
How Supply Chain Talent Can Impact the Customer Experience – the Bastian Consulting Perspective
WRITTEN BY STEPHANIE MARTINEZ AND TONY RICHTER PARTNERS AT BASTIAN CONSULTINGConsumer behaviour has changed the retail paradigm. To meet customer needs and to discover untapped revenue, modern retailers are rapidly investing in their supply chain capabilities to stay ahead of the curve. By managing supply chains effectively, businesses can stay ahead of competitors and directly dictate two key parts of customer satisfaction – price and delivery.
Customers expect to be able to get in touch with businesses quickly and easily to get issues resolved.
They also have heightened expectations of product availability, ranges, delivery options (including price and speed) which are all major factors when making a purchase.
Customers want to make an order knowing that stock level availability is in real-time. In Australia especially, we’re seeing a lack of skills around digital and order management systems (OMS.) Many businesses are still using Excel spreadsheets to manage their inventory, which just doesn't work anymore. Businesses need to have real-time visibility into their inventory levels to ensure they always have enough product to meet customer demand. Adopting automated systems to improve order and inventory management is a must.
We’ve also seen a rise in the number of roles in the warehousing space. You can have the best technology in the world available, but if you don’t have the people to manage fulfilment or get your order delivered on time, this will negatively affect the company and the brand.

On the employment website SEEK, there are more than 32,000 unfilled vacancies
(July 2022) which is a big challenge for us as an industry to solve.
The warehousing sector is crying out for talent, and the widening gap is causing salaries in this space to increase exponentially. In fact, not long-ago general warehousing staff salaries were around $65,000 plus superannuation on average. Right now, it’s very common to see these same roles being advertised for $75,000$85,000, if not higher.
Skills such as Warehouse Management System (WMS) integration, OMS configuration, and knowledge of working with robotics and automation can make or break your supply chain right now, directly resulting in a customer experience that strengthens or weakens your brand.
In 2010 industry talk focused on the
issue of the “perfect order” and being able to track and measure all the links in the chain. Today the focus is on the customer, their experience, the perceived value in your service, the digital feedback they provide and whether or not they come back.
Ensuring you have a positive impact on your customer experience through effective supply chain management requires careful planning, coordination, and execution. Having the right people in place to manage this ensures a smooth experience and repeat business. ●
For more information on how your business can attract workers in a talent crunch, please click here.
From Plenty to None: What Can Supply Chain Leaders Learn from Australia’s Current Grapple with Product Shortages
WRITTEN BY RAGHAV SIBAL MANAGING DIRECTOR, ANZ, MANHATTAN ASSOCIATESSince the pandemic, supply chains have been no stranger to product shortages. From the toilet paper saga that saw supermarket shelves laid bare in mid-2020 to the latest shortage of lettuce –of all things – it has become a recurring theme that shortages happen more often than consumers and retailers, think.
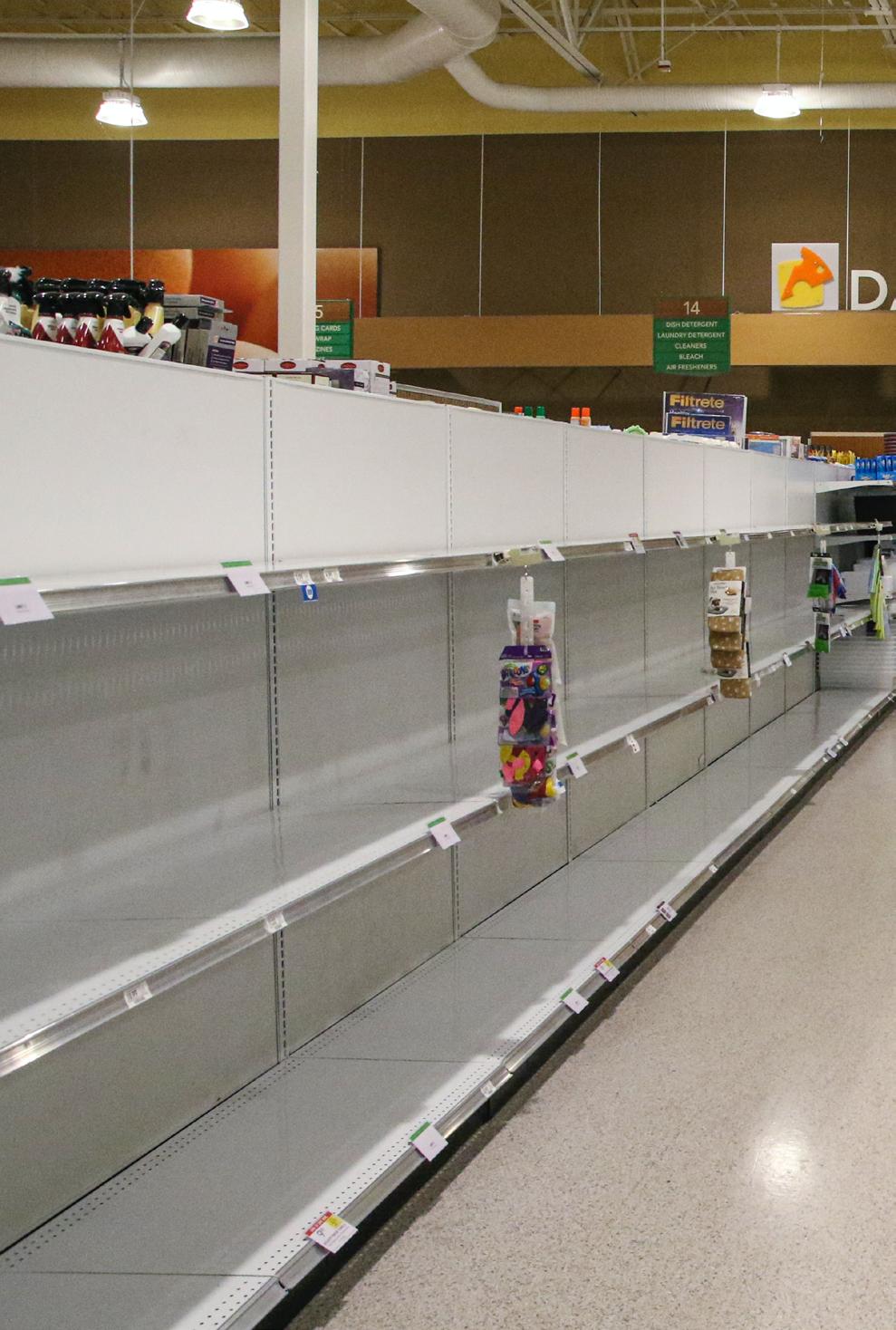
A case in point is KFC’s debatable act of serving their burgers with cabbage – due to a lack of lettuce – raised public awareness of (and with no shortage of outcry) around just how quickly food shortages can result from supply chain issues.
So, what can supply chain leaders, retailers, wholesalers and grocery chains learn from this? And how can they learn to prepare themselves for inevitably more supply interferences in the future?
A rethink of supply chain continuity
Issues such as food shortages, the climate crisis, worldwide pandemics, and, more recently, military conflicts in Eastern Europe, have created significant disruptions to global production, shipping and logistics processes. However, in an unexpected turn of fortune, these events present an opportunity to ‘rethink’ the approaches that facilitated overly lean supply chains without any inbuilt resilience.
In due course, this crucial rethink could spur brands and governments to kickstart a stronger supply chain, all whilst promoting a sustainable, green revolution in manufacturing, supply chain, and retailing approaches. As both brands and governments look to allay future supply chain disruptions and the genuine knock-on effects inflation is having on businesses and individuals, the topic of onshoring and all its potential long-term consumer and environmental benefits is gathering momentum.
A case beyond just pure economics
Increased flexibility, access to larger workforces and reduced operational expenses are just three of the most commonly cited reasons that have seen tens of thousands of Australian organisations moving significant business operations overseas. And while
expansive global supply chains gained prominence over the past decade, they have also introduced a level of fragility that, until recent events, was not entirely understood.
stock in their local DC network as a buffer against supply chain disruption. This is because it has a significant impact on short-term cash positions for retailers and carrying large amounts of seasonal inventory means that working capital is constrained. Additionally, due to a business holding more stock, retailers are sometimes forced to mark-down prices to move goods and face challenges around where to hold stock and when. Many retailers are still unsure about the split between eCommerce and brick-andmortar, so they often find their inventory is in the wrong place.
The ‘onshoring’ movement of entire manufacturing processes and supply chain networks offers a tantalising opportunity for brands to reimagine and reinvent their entire approach to shortages, interferences, and sustainable practices.
Having your inventory in the right places
From a retail perspective, companies have traditionally been reluctant to hold large amounts of
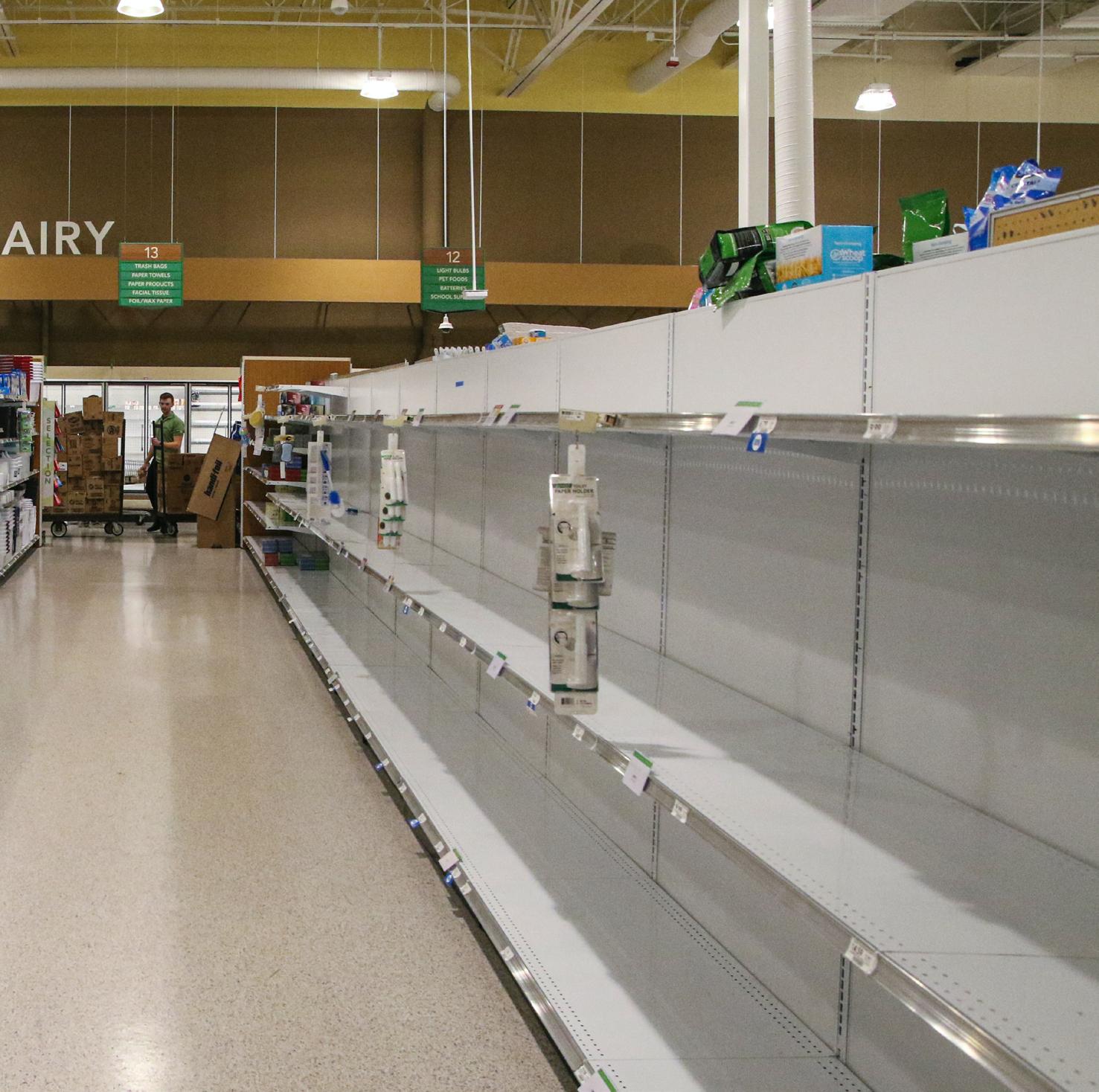
To gain these insights, solutions like a Warehouse Management System (WMS), which integrate all sales and distribution channels into one place are required. With innovations like a WMS, retailers have absolute transparency around their goods. They can review the rules of stock allocation, temporarily giving priority to in-store stock over warehouse stock, thus, freeing up any trapped inventory confined within closed stores.
In addition, retailers should consider adopting a micro-fulfilment strategy that involves moving out of large singular DCs to smaller and more local and convenient hubs. By expediting the fulfilment process, micro-fulfilment allows brands to house their inventory close to the point of demand, enabling them to get goods to their customers quickly and provide convenient collection point for consumers who want to click and collect. With the adoption of this kind of smart fulfilment method, retailers can get their goods to consumers faster, cheaper, and more efficiently.
Building a supply chain fit for the future
Global events and local production issues continue to have a profound and lasting impact on Australian supply chains. As brands and the federal government look to mitigate against ‘the next’ significant event, moving manufacturing processes, goods, and distribution networks closer to home and to consumers is becoming a more important tool than ever to execute supply chain resilience and continuity.
The key to success for this new strategy rests on the ability of brands to continue to innovate at a supply chain level and deliver networks and solutions that are not only resilient and reliable but also agile and responsive enough to deal with shortages, disruptions, and changing consumer and environmental needs in the future. ●
For more information, please click here.
Nevertheless, there is far more to like about the potential for bringing supply chain and manufacturing processes closer to the consumer than simply economic and security incentives.
In this environment, operational visibility and forward planning are critical to ensuring stock is where it needs to be to meet demand.
How to Optimise Last Mile Deliveries
WRITTEN BY MARK DELANEY VP, RETAIL INDUSTRY STRATEGY FOR FOURKITESLast-mile delivery is hard to get right. Home deliveries are labour and fuel-intensive, and they’re difficult to predict. But this final stage in the delivery process significantly impacts customer satisfaction and customer loyalty.
Such is the interest in this space that Crunchbase currently lists more than 400 organisations trying to address the issues that come with leaving a package on consumers’ doorsteps.
The last-mile logistics pie is growing rapidly. But it poses one of the more challenging logistics puzzles to solve. Why is last-mile delivery so challenging? Well, it can cost… a lot! As the number of final-mile deliveries grows, shippers’ expenses will balloon. According to Capgemini, the last mile accounts for 41% of total supply chain costs. Scaling your fleet of drivers and equipment – not to mention skyrocketing gas prices – creates high fixed costs that can erode profitability. Route and labour optimisation become paramount for a cost-effective last-mile delivery strategy.
According to a report from UPS Capital, “69% – the vast majority of shoppers – are willing to pay for the ability to personalise, control and uplevel their shipping experience. They are looking for new services from merchants including guaranteed
delivery timelines, real-time tracking, replacement of lost/stolen/damaged packages, and pre-order or special deal opportunities.” In other words, shoppers want to know with certainty what they’re getting, when they’re getting it and how it’s getting there. For shippers and supply chain leaders, these expectations are in direct conflict with the shipper’s other desire for flexibility: the ability to put the package on a different truck or deliver at a different time of day if conditions have changed and it’s more efficient to do so.

How Can You Improve Last-Mile Deliveries Today?
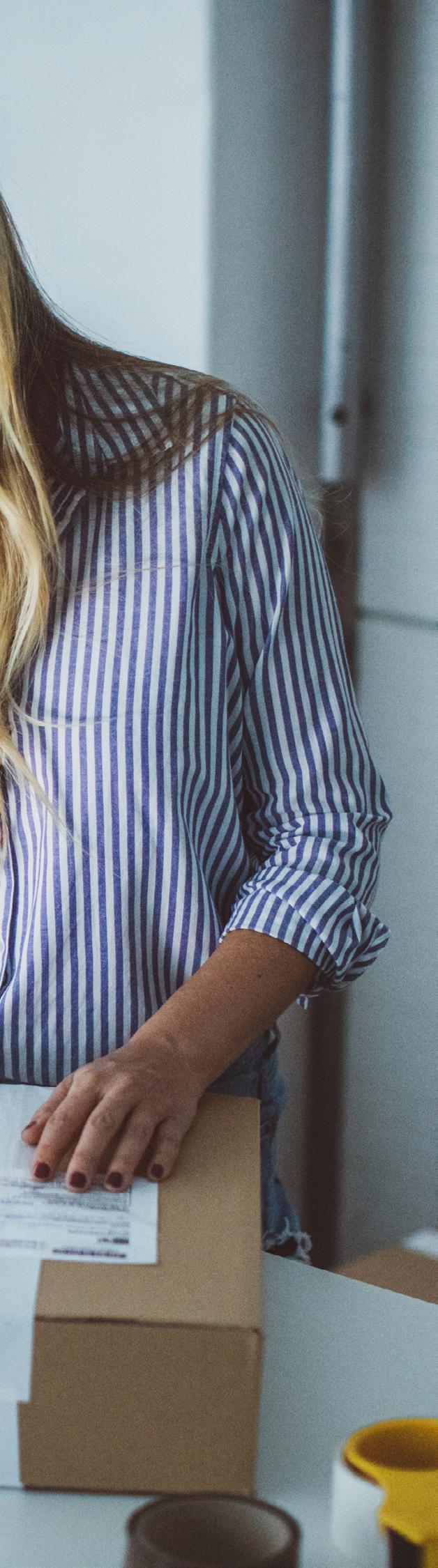
So, where can shippers start? How can they overcome the challenges of the final mile? While a handful of the 400+ last-mile companies show promise of solving these problems, it’s not sufficient to simply outsource the solution. Here are some practical steps that can be taken today to tackle the final mile.
Assess Your Network
The pendulum is shifting back in favour of shippers. With more available capacity, rationalising your network to work with the providers that make the right impact is wise. Commodity-specific providers can help make a difference in your last-mile delivery customer experience, especially with white glove and “deluxe” capabilities. Developing a universal provider scorecard that considers the cost-to-quality ratio can help you fine-tune your delivery experience, reduce costs and improve customer retention. Identifying how your network will handle your plans for micro-fulfilment and omni-channel distribution is also critical.
The pandemic forced the industry to adopt truly revolutionary channels for fulfilment. Now, with more retail space available for localised fulfilment models, there’s a precedent for moving inventory deeper into population centres, reducing your time to consumer and improving your ability to compete with last-mile delivery juggernauts.
Improve Collaboration Across Your Supply Chain
Collaboration – both within and among supply chain organisations – can help companies make significant strides in eliminating waste, maximising profits and promoting sustainability. Poor communication is often one of the biggest hurdles to effective supply chain collaboration.
The logistics industry has a long history of decentralisation – proprietary workflows, processes and systems that are largely unknown or unintelligible to those outside an organisation or department. Believe it or not, many companies still operate out of spreadsheets and emails to manage their supply chain. These workflow chokepoints can be overcome by implementing dedicated, shared systems that enable efficient communication with supply chain networks, partners and outside stakeholders.
Data is critical to any effective supply chain collaboration. For organisations of all shapes and sizes, good data is the foundation of strong decision-making. It facilitates efficient performance not only among individual team members, but across entire organisations. Without good data, the best anyone can do is make an educated guess – and for shippers under constant pressure to succeed, that’s simply not good enough. Start improving collaboration across your supply chain to optimise your entire delivery process.
Implement Real-Time Visibility
Optimising last-mile delivery and improving your supply chain starts with better data, collaboration and network enablement. Supply chain visibility platforms are a good place to start to improve across the board. The last mile is hard and expensive to perfect. Retailers and logistics service providers (LSPs) who gain efficiencies elsewhere in their supply chain – like optimising labour, inventory, and transportation – can make the investments necessary to conquer the final mile.
What can real-time visibility do? Imagine empowering employees to be more productive by eliminating manual processes and leveraging real-time ETAs to ensure people are in the right place at the right time. Or having more accurate cycle time calculations and tighter inbound shipping tolerances that enable you to operate with less excess safety stock. Or gaining the power to quickly adapt to rapidly changing consumer demand by knowing where popular products are in their journey from plant to warehouse.
This supply chain agility requires real-time visibility across all modes, including inbound visibility into vendor-managed shipments and the ability to facilitate handoffs between modes and legs. But visibility is not a one-size-fits-all approach; each shipper or LSP has unique operating processes, suppliers and carrier networks. An interoperable real-time visibility platform is key.
Real-Time Visibility and Optimising Last-Mile Deliveries
It’s a tough journey to reach a consumer’s doorstep efficiently, but leveraging real-time supply chain visibility to optimise your network, collaborate and proactively communicate can make the ride much smoother and more cost-effective. Plus, a realtime visibility solution that integrates with last-mile software gives shippers and customers visibility across the supply chain – from the manufacturer to the front door.
Managing the increasing expectations and demands of shoppers can create all sorts of chaos for last-mile delivery. A bad delivery experience can cause customers to jump ship. Perfecting the delivery experience can seem like an impossible task, but shippers who can master last-mile delivery and meet consumers’ increasingly complex demands – expectations like deliveries arriving in two days or less – will satisfy and win loyal customers. In short, optimising last-mile delivery empowers shippers to enhance their delivery experience, delight their customers and retain a base of loyal customers. ●
For more information, please click here.
