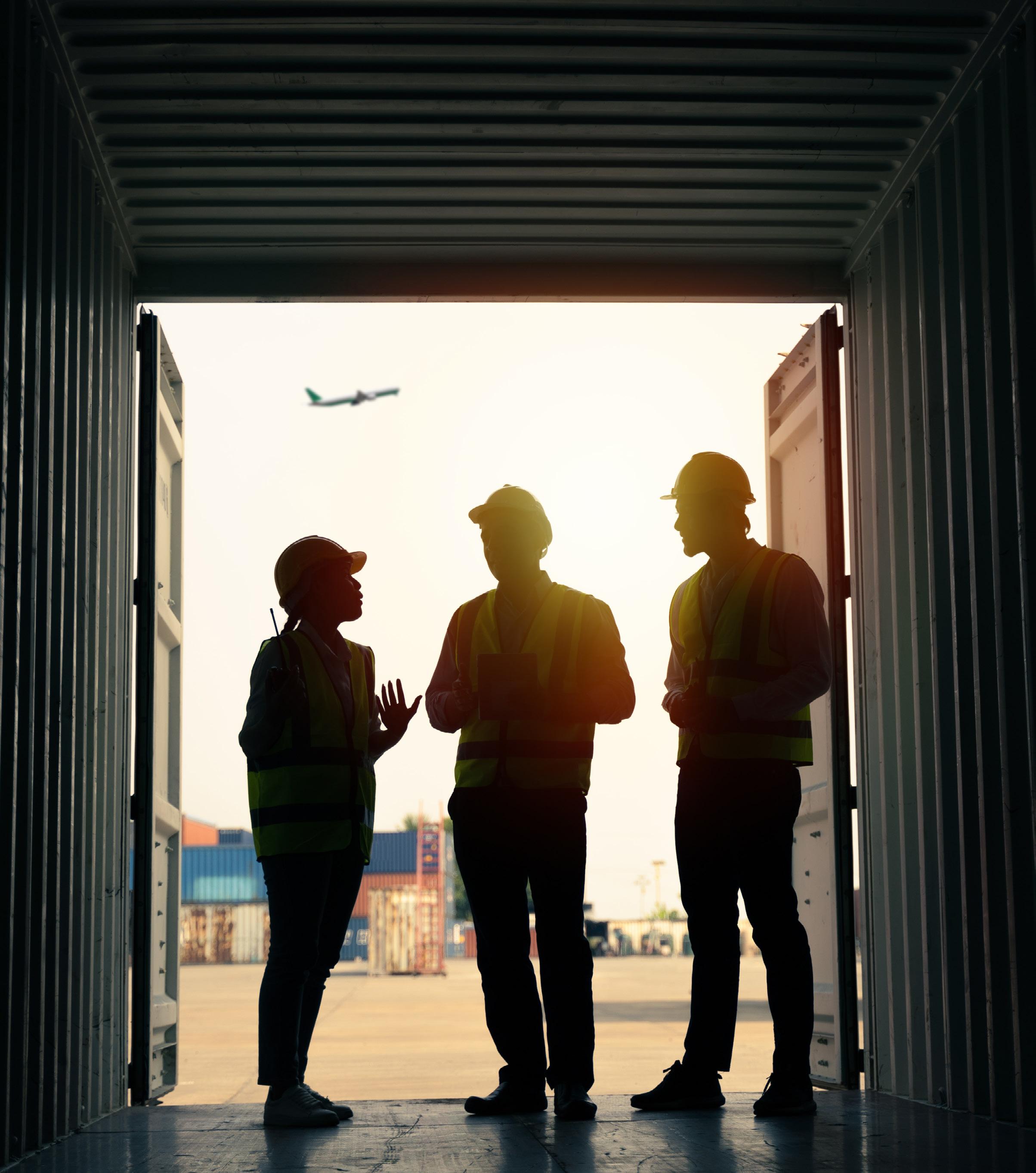
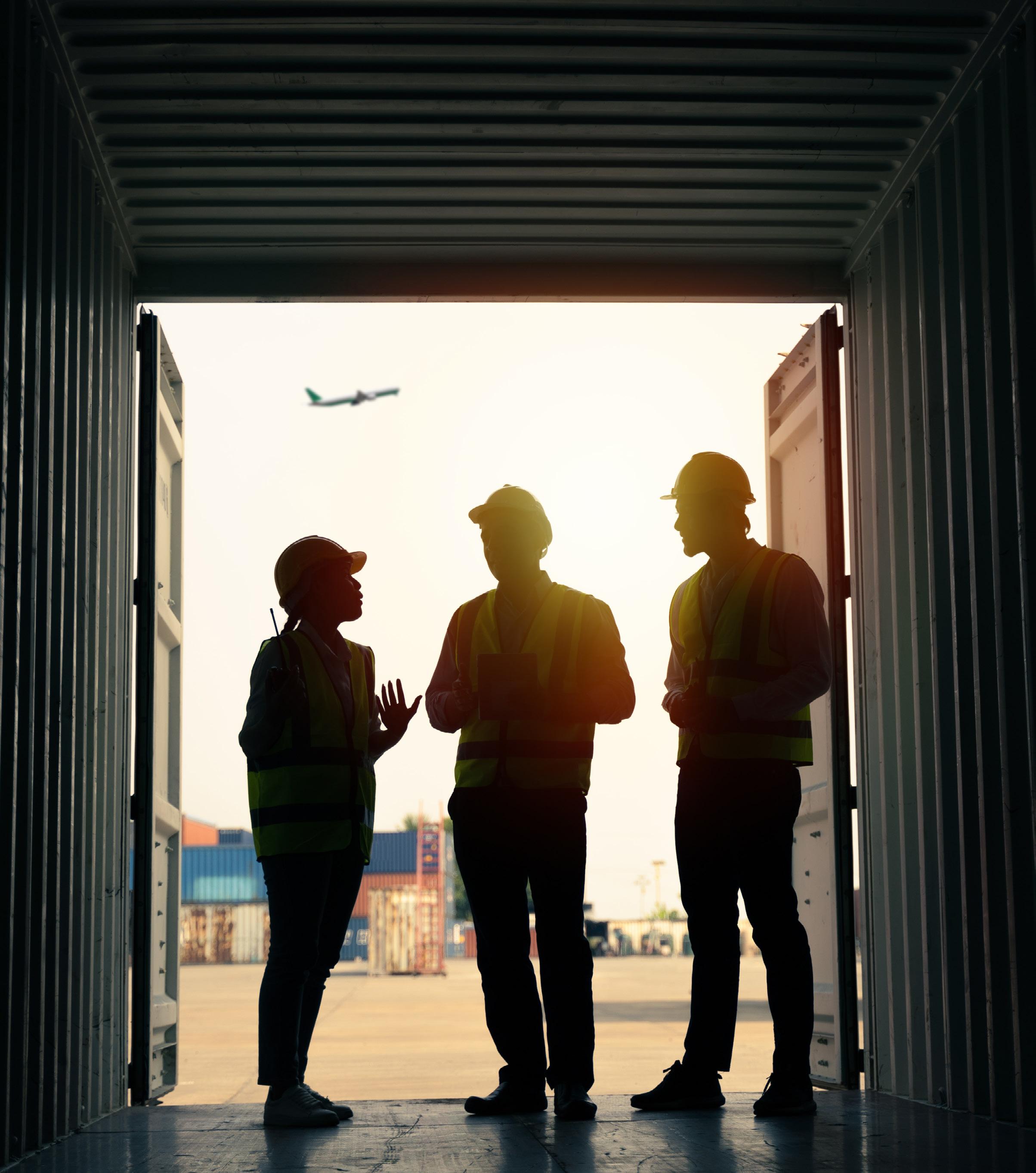
Welcome
About The Magazine
Published quarterly to a circulation of 20,000 + industry professionals across Australia, New Zealand and the wider Asia-Pacific region, Supply Chain Insights Magazine is focused on helping you solve the complexities of today's supply chain. The digital magazine highlights the latest trends, operational strategies, technology advancements and best practice within the supply chain and logistics industry.
Welcome to Supply Chain Insights Magazineyour primary source of industry news, focused on innovation, technology and knowledge-sharing in the logistics sector.
In this edition, we explore how retailers are preparing for the holiday season amidst rising interest rates and economic challenges. Supply Chain Insights investigates how strategic investments in technology, workforce management, and adaptive planning can help businesses tackle short-term pressures while setting up for long-term success. Features editor Mel Stark writes, Navigating the Peak: What to Expect and How to Prepare for This Year’s Seasonal Spike, delving into expert insights on consumer demand forecasting and supply chain resilience.
We also feature insights from George Pecchiar, Executive Director of Peacock Bros.,
offering solutions for managing warehouse workforce challenges with equipment rentals and advanced tools. Gordon Maddock, Regional VP at Appian APAC, discusses how data accessibility issues are disrupting Australian supply chains, while Michael Dyson, VP at SOTI, explores the inefficiencies and opportunities of mobile technology in transport and logistics. Additionally, Tony Richter, Partner at Bastian, examines the "second wave" of supply chain transformation, focusing on automation, advanced analytics, and geopolitical risk management.
We hope you enjoy this edition and look forward to your feedback!
For more information or story suggestions, please contact: editor@supplychain-insights.media
For advertising enquiries, please contact: advertising@supplychain-insights.media
Visit our website: www.supplychain-insights.media
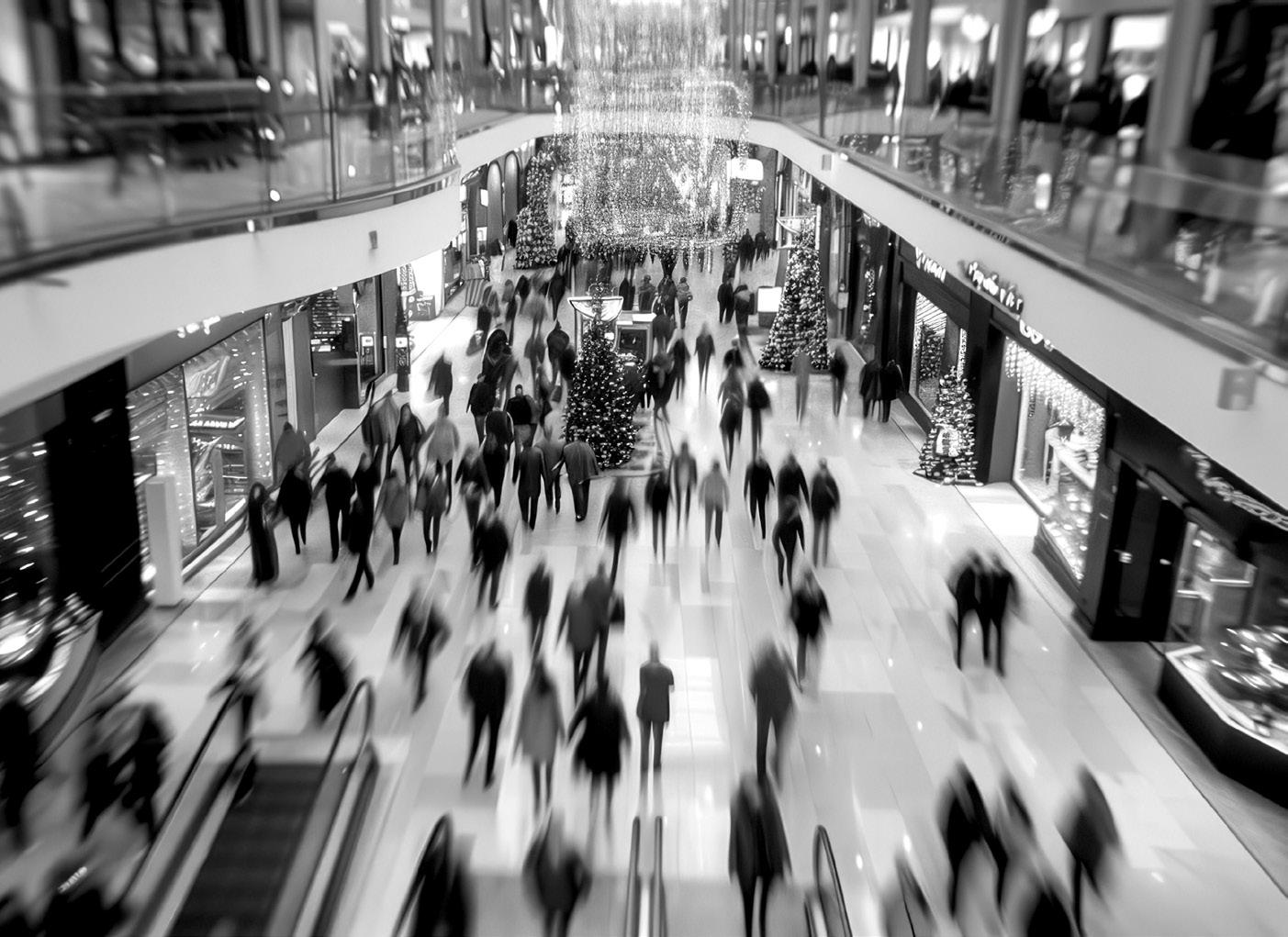
News & Insights
Construction Begins on API’s New Distribution Centre in Cairns
Construction has commenced on a new medication distribution centre in Cairns, Queensland.
Wesfarmers Health’s subsidiary Australian Pharmaceutical Industries (API) is establishing a new fulfilment centre in Portsmith that will be three times larger than its existing building in Bentley Park.
The new centre will supply more than 120 pharmacies from Cairns to as far north as Weipa and inland to Mount Isa, improving reliability and access to medication for Queenslanders.
A ceremonial groundbreaking marked the construction commencement on September 17.
“The new fulfilment centre will increase product, boast updated technology in the warehouse and will feature solar panels to
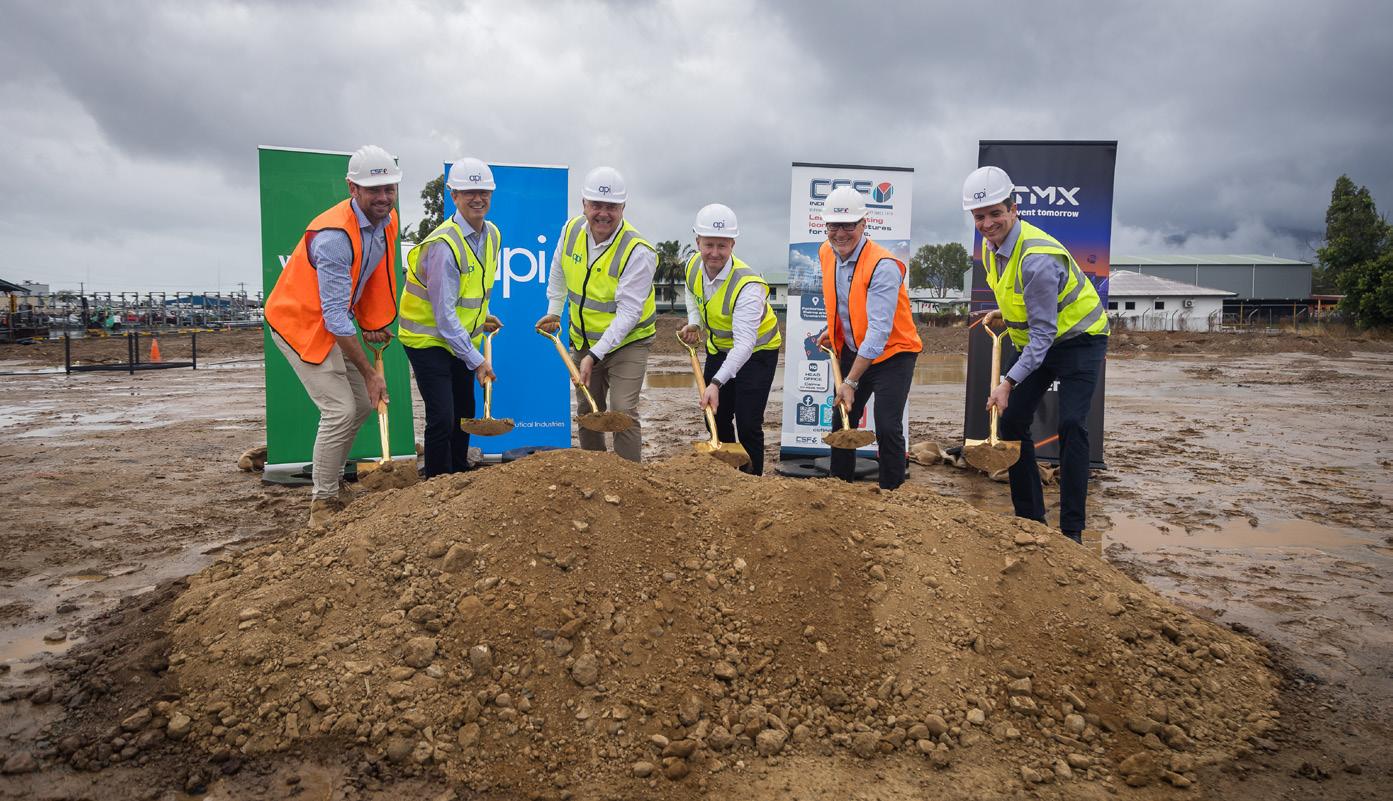
drive our Net Zero sustainability goals,” API’s General Executive Manager Doug Swan said.
CSF Industries will construct the facility.
TMX Transform worked on the concept design, property procurement, and is managing construction with the works now underway.
“This strategically located site in Cairns consolidates existing facilities into a new bespoke distribution centre, which will enable API to plan for and accommodate product and volume growth and to continue supplying critical deliverables for regional Australians,” TMX Transform’s Executive Director of Project Services Angus Perry said. “This
is the third major project on which API has partnered with TMX, and our partnership has deepened our joint expertise in positioning API for growth and supply chain resilience.”
Hundreds of Cairns locals will be employed during the construction phase, with new, permanent jobs also created once the site opens. The new facility is expected to open October 2025. ●
Staff Retention, Tech Gaps, and Multi-Channel Complexity Put Warehouse Operations in the Spotlight
Manhattan Associates Inc. (NASDAQ: MANH) as released its 2024 'State of Warehouse Operations' research, conducted in partnership with Vanson Bourne, highlighting critical issues that Australian businesses must address to stay competitive. Amid economic and geopolitical disruptions, local procurement and supply chain leaders are under increased pressure to manage staff retention challenges, modernise outdated technology, and streamline complex multichannel operations.
The study found that 93% of Australian warehouse professionals are facing ongoing difficulties with staff retention, a challenge that threatens operational
stability. Compounding this issue, 79% of respondents reported a significant surge in goods passing through their warehouses over the last year. As warehouses become busier, nearly all respondents (98%) believe their current IT infrastructure is insufficient and urgently needs modernisation to manage these growing volumes effectively.
Global disruptions, combined with changing consumer expectations, are reshaping the supply chain landscape. Warehouse professionals must navigate labour shortages, supply chain disruptions, and increasing demand across both digital and physical sales channels. According to the research, senior management from industries including manufacturing, logistics, pharmaceuticals, retail, automotive, and consumer packaged goods (CPG) pinpointed outdated technology, workforce shortages, and multi-channel order complexity as their biggest operational hurdles.
Optimism Through Emerging Technologies
Despite these challenges, Australian businesses remain optimistic about the potential for emerging technologies to improve warehouse operations. The research

revealed that 68% of respondents believe Generative AI will significantly improve job satisfaction and productivity by automating manual tasks, while 72% expect robotics to enhance operational efficiency by reducing bottlenecks in workflow processes.
Raghav Sibal, Managing Director for Australia and New Zealand at Manhattan Associates emphasised the importance of embracing new technologies: “High turnover and low morale disrupt operations, drive up costs, and damage service quality. Addressing these issues with advanced technologies like AI and robotics will not only help businesses meet rising demand but also support staff engagement and satisfaction.”
Technology Gaps Pose Operational Risks
The study also highlighted that 28% of businesses see outdated IT systems as their most pressing challenge, with financial and operational inefficiencies resulting from reliance on legacy technology. These inefficiencies are especially concerning in a landscape where 22% of respondents struggle to manage orders across multiple channels, and 20% find it difficult to meet growing consumer expectations for faster delivery times.
“Warehouses are the backbone of a unified supply chain. Optimising operations with modern technology is vital for businesses to stay competitive,” said Sibal. “By adopting innovations like microservices and Generative AI, businesses can future-proof their supply chains, turning them into key drivers of revenue growth and customer satisfaction.”
The Future of Warehousing
The report highlights the growing importance of continuous innovation in supply chain operations. As businesses adapt to rising demand and rapid technological advancements, a cohesive strategy that integrates advanced technologies will not only boost efficiency but also promote economic and environmental sustainability.
“A unified supply chain strategy enables businesses to improve productivity and efficiency while supporting sustainability efforts. By integrating advanced technologies, businesses can boost their profit margins and contribute positively to the planet,” Sibal concluded. ●
To read the full 2024 'State of Warehouse Operations' report, click here.
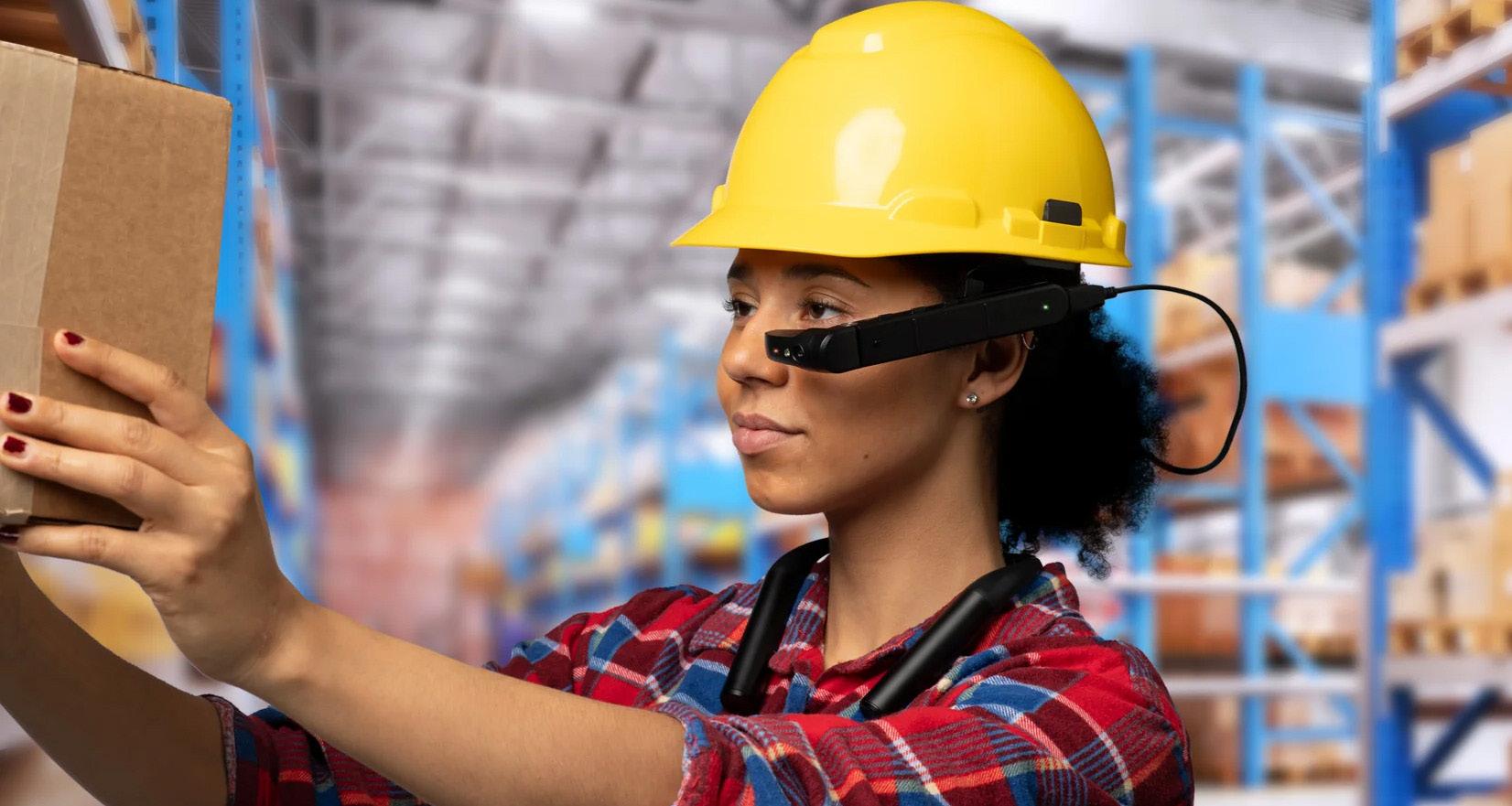
Dematic Launches New Vision Picking Solution to the Australian and New Zealand Supply Chain Industries
Dematic, a leading global supplier of integrated supply chain and warehouse automation technologies, software, and services, is excited to announce the launch of its innovative Vision Picking Solution in Australia and New Zealand.
This advanced solution is designed to optimise warehouse worker productivity and enhance supply chain processes by integrating vision-assisted picking with realtime logistics solutions.
“In today’s fast-paced supply chain environment, it is vital to always know where your stock, orders, people, and equipment are. Dematic’s mobility and productivity solutions empower supply chain operators with key information whenever and wherever it is needed. This leads to enhanced decision-making, optimised service levels, and reduced costs,” says Lee Koutsos, Director of Real Time Logistics and Colby Storage Solutions ANZ at Dematic.
The Dematic Vision Picking Solution
incorporates a small heads-up display (HUD) that improves the warehouse picking process by providing visual confirmation of instructions. This hands-free technology works seamlessly with vision-picking software, which can be applied to any vision glasses technology and can also work in tandem with voice-picking technology. By displaying the items to be picked (including images for fast identification) along with their quantities and locations (including check digits to ensure the right location is selected), the solution ensures smoother and more accurate picking.
The Dematic Vision Picking Solution offers numerous key benefits, including:
• Enhanced efficiency: Hands-free picking and better spatial awareness.
• Increased Accuracy: Visual confirmation reduces picking errors.
• Reduced Training Times: Intuitive design simplifies onboarding.
• Improved visibility: Real-time data provides up-to-date information on stock and asset traceability as well as stocktake.
• Optimised Workflows: Improves overall warehouse operations.
“The Dematic Vision Picking Solution addresses key challenges currently faced by the supply chain industry, including the high
cost of labour, labour shortages and turnover, and the need for faster order fulfilment. By integrating advanced technologies into warehouse operations, Dematic is helping businesses overcome these challenges, improve accuracy, and enhance overall efficiency,” continues Koutsos.
The solution is ideal for various warehouse applications such as picking cases from pallet racking, picking eaches from cartons in shelving, replenishment, stocktaking, and maintenance and inspection tasks. The solution is also ideal in temperature-controlled environments (where staff typically wear gloves) and supports multiple languages, making it suitable for a diverse workforce.
To further boost productivity, the Dematic Vision Picking Solution includes gamification features. Staff can engage in competitive activities and achieve targets, with rewards for meeting activity-based goals.
“The new Dematic Vision Picking Solution is available through our Real Time Logistics division in Australia and New Zealand. It was developed from our deep global experience and rigorous in-house testing, and it is supported by our large Australian team of engineers, project managers, and software developers. We provide ongoing support from a large customer service team with a 24/7 contact centre and in-house repair centre,” concludes Koutsos. ●
Ingram Micro Australia Improves Warehouse Operational Efficiency with Zebra Technologies
Ingram Micro Australia is improving its operational efficiency using Zebra Technologies’ solutions at its 42,000-squaremetre warehouse at Eastern Creek, NSW.
Ingram Micro is Australia’s largest technology and supply chain services distributor that represents more than 250 vendors to a network of 11,000 Australian resellers.
The solution implemented by Ingram Micro is Zebra’s intelligent cabinet which offers adaptable device storage, software automation, and security applications as well as ongoing support. Prior to deploying the intelligent cabinet solution, Ingram Micro’s front-line staff wasted valuable time every day searching for their mobile computers before they could begin their work in the warehouse. They have since eliminated this delay while enjoying realtime visibility and better tracking of devices returned to the intelligent cabinets at the end of each workday.
“The introduction of Zebra’s intelligent
cabinet has significantly reduced the combined time spent by our front-line staff in searching for the tools they need to perform their daily tasks,” said Aaron Kumar, Director of Operations, Australia and New Zealand, Ingram Micro. “Zebra enables us to empower our front-line staff with greater efficiency and the ability to deliver better results through digitalisation.”
With Australia’s logistics and warehousing industry forecast to grow from a 4.7% economic contribution in 2023 to around 6% by 2026, “it is important that warehouse operators equip themselves with the right technology to increase collaboration between workers as well as boost productivity and effectiveness,” said Peter Pollari, Regional Distribution Manager ANZ, Zebra Technologies. ●
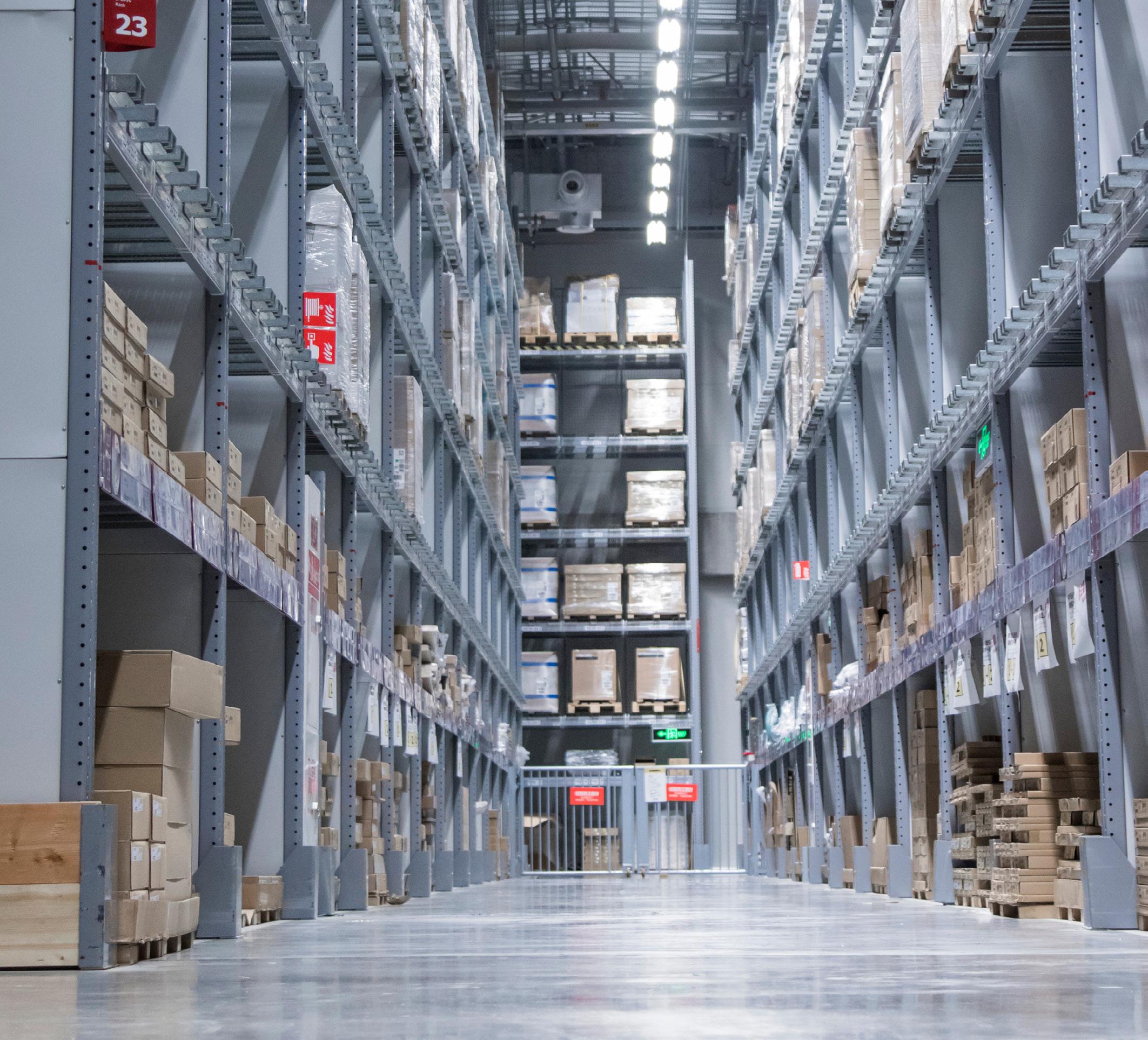
Electrifying Delivery Fleets: Inside Origin 360 EV’s Bespoke Charging Strategy for Long-Time Player ANC
One of Australia’s oldest delivery companies, ANC, is just weeks away from the rollout of its EV charging strategy that will see more than 120 chargers installed at driver homes and select ANC depots by the end of 2025.
Origin 360 EV is facilitating the deployment of the EV chargers and plans to have the first tranche of 34 chargers installed in the near future, with the first six chargers arriving at driver homes in the coming weeks.
To effectively and successfully integrate EVs into the business fleet, Origin 360 EV worked with ANC to develop and implement a bespoke charging strategy tailored to ANC’s unique operational requirements.
David Helmy, Head of Sales at Origin 360 EV emphasised that delivering to ANC’s operational requirements played a pivotal role in the development of ANC’s tailored charging solution. This approach supports a comprehensive charging network, including the installation of charging infrastructure at fleet drivers' homes.
"When developing a charging strategy tailored to a business' fleet requirements, it's essential to focus on data that reveals vehicle usage patterns and potential charging locations. Ensuring that the charging solution developed provides our customers with a seamless operational outcome is a key focus for us," said Helmy.
"Electric vehicle adoption is becoming a central component to a company's decarbonisation strategy, particularly as we become more aware of the efficiencies,
usability, and cost-saving benefits EVs provide."
Mo Abbas, Chief Growth & Sustainability Officer at ANC, shared, “ANC has a commitment to reducing our environmental impact and overcoming the barriers to a sustainable energy future. We're thrilled to work with Origin to accelerate our journey towards zero emissions and provide our drivers with the best possible EV charging experience.”
Origin 360 EV will deliver the charging infrastructure and assist ANC with the payment model, ensuring drivers can reconcile charging costs and get the most out of their at-home charging facility.
The bespoke charging strategy will streamline ANC's EV uptake and provide long-term charging solutions to strengthen ties with clients, including Temple & Webster, IKEA, Bunnings, and JB Hi-FI. ●


Welcome to supply chain commerce
Unify ware h ouse manageme nt, t ransportation management and o rder management
With all your sup p ly chain a pplications on a s ingle p latform, you can b reak down silos, unlock efficie n cies, boost p rofitability and transform execution. Set your most a mbitious goals, Ma n hattan will make them poss ible.
To learn more, visi t m anh.co m.au
WATCH ON DEMAND
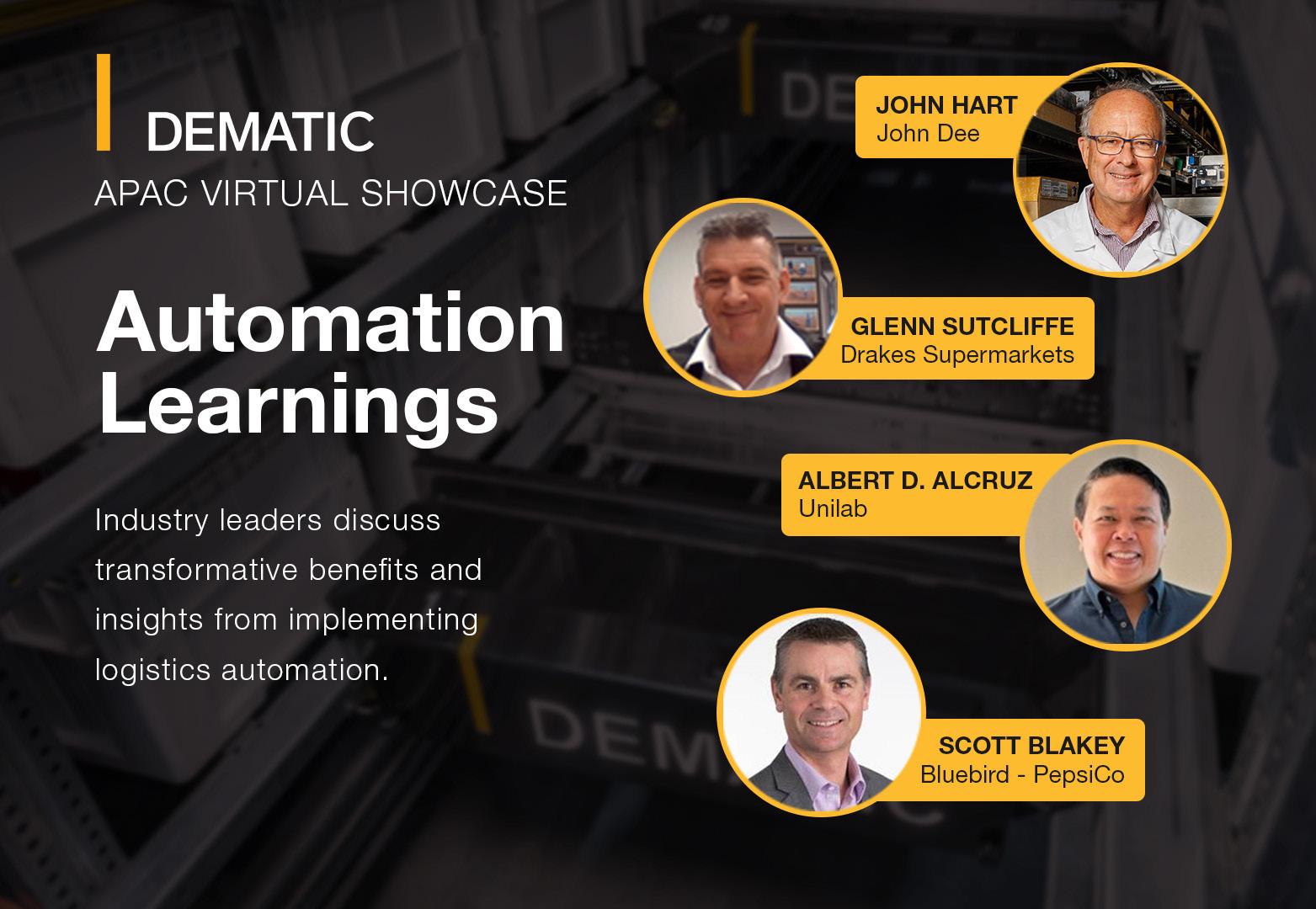
Dematic Virtual Showcase 2024
Dematic’s latest Virtual Showcase delves into the transformative impact of automation on supply chains, highlighting the operational benefits being realised by businesses, such as increased productivity, enhanced customer satisfaction, and improved organisational flexibility.
Join industry leaders from Bluebird Foods –PepsiCo, Drakes Supermarkets, Unilab Pharmacy, and John Dee, as they discuss how their automation projects were meticulously evaluated, implemented, and optimised to meet specific supply chain needs.

Scan to access on-demand
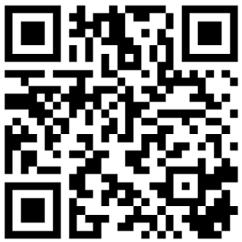
Watch to gain insights into:
• Business cases for automation
• Strategic factors and influences
• Planning for success and change management
• Integration and adoption experiences
• Results, benefits, and key learnings.
Watch on-demand today!
Technology is a Key Driver For Growth in Supply Chains, But Lack of Understanding Across Leaders is Holding Back Progress – Research Reveals
A new research report has revealed a contradiction in supply chain technology adoption, with 62% of supply chain decision makers citing technology as a key driver for business growth, yet 45% are struggling to effectively implement these solutions in daily operations.
This gap between recognising technology’s potential and practically implementing it to boost efficiency and drive business growth was identified in the Attitudes to Innovation report, commissioned by end-to-end supply chain consultancy TMX Transform.
The research surveyed more than 250 global supply chain and logistics decision-makers and provides insights into the awareness, attitudes, and uptake of innovative supply chain technology such as AI, predictive analytics, automation and simulation among industry leaders.
Of the business leaders questioned (including business owners, C-Suite executives, and management professionals) the majority are on board with technology in the supply chain. Three quarters have implemented innovative technology within their organisation and of these, four in five (80%) say their organisation is set for growth in the upcoming year, compared with just under 3 in 5 (59%) who have not implemented new technology.
The most implemented tech solutions are predictive analytics (62%), sustainable tech to reduce carbon footprints (59%), and the Internet of Things (52%). According to the data, predictive analysis has had the greatest impact on businesses, with 94% citing the technology has had a positive impact on their business.
When asked about the technologies that organisations have not implemented, but plan to, simulation/digital twins was the most common response, with 44% of respondents planning on adding the solution to their supply chain capability.
Yet nearly a quarter of respondents (24%) are unsure about AI/Machine Learning capabilities, while 60% are
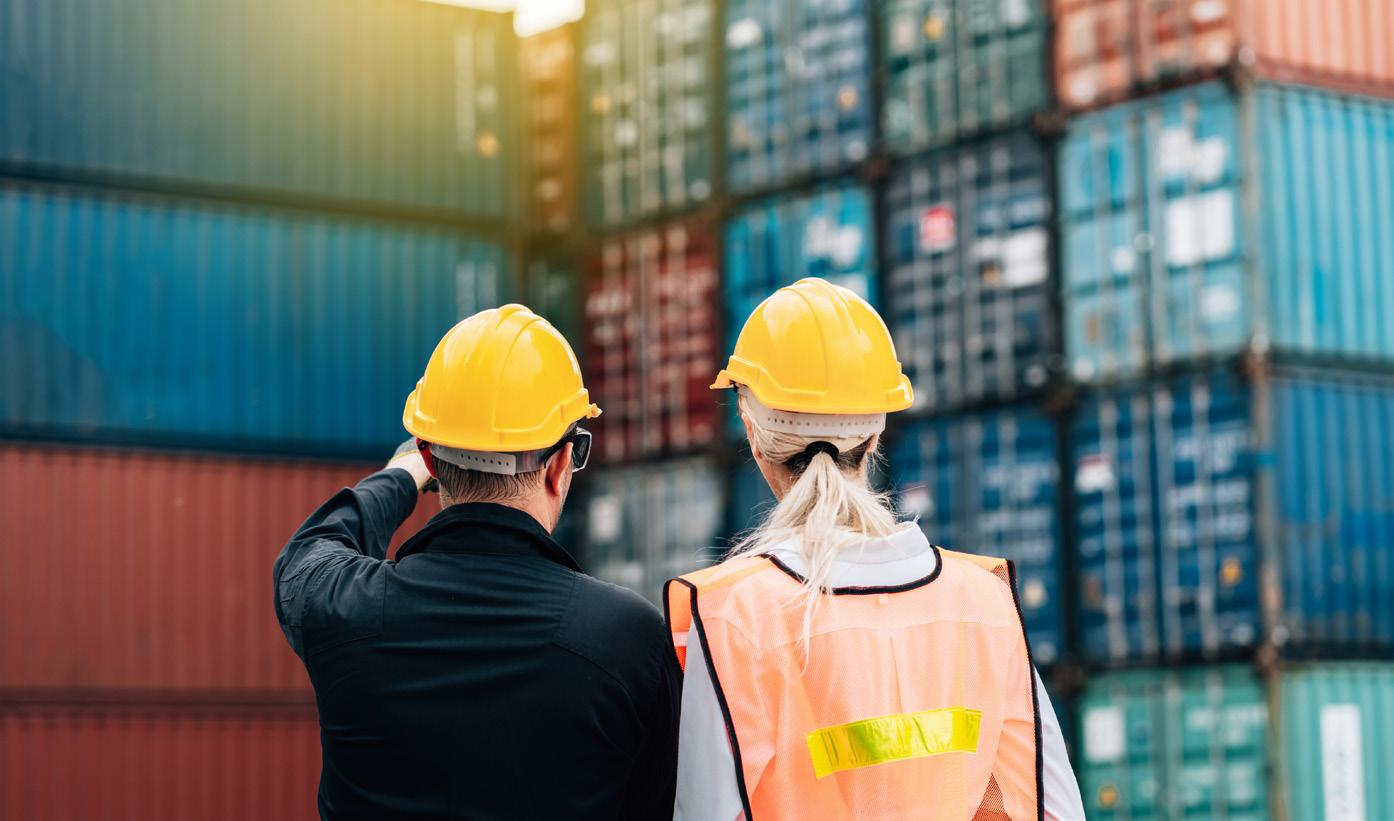
uncertain about what simulation/digital twins technology is, or does.
Cost-savings and improved efficiency was the most common benefit that respondents attributed to technology investment, ahead of reduction in human error and manual processes, and the ability to react quickly to changing consumer expectations and demand.
Travis Erridge, TMX Transform CEO:
“Today's consumers expect instant access to global products. The results of this research demonstrate that technology is paramount in adapting to this new reality, where supply chain becomes a strategic business advantage to unlock customer satisfaction. It is encouraging to see the positivity around innovation in the supply chain, but this report demonstrates the need for better education and support in adopting different solutions.”
“In the last few years, global conflicts, environmental crises, major trade disruptions and a pandemic have starkly
revealed how vital a resilient supply chain is for business continuity. The companies who have been able to plan ahead, think progressively and be open to change have thrived, while those holding on to old processes have been left behind.”
Tom Fitz-Walter, TMX Transform Executive Director - Supply Chain:
“Automation and technology are crucial in addressing the pressing issue of labor shortages in supply chains. However, experiencing the biggest benefits of technology hinges more on people than the technology itself. As organizations face challenges like high staff turnover and a lack of experienced leaders, nurturing and retaining skilled personnel becomes essential to successfully implementing technology solutions and driving innovation.” ●
Transforming Regional Healthcare Logistics: How Dematic Helped South West Healthcare Meet Growing Demands
South West Healthcare, based in Warrnambool, Victoria, is a key provider of healthcare services to communities across Southwest Victoria.
As a major healthcare hub, the organisation operates several campuses, including the Warrnambool Base Hospital, as well as smaller facilities in Camperdown, Lismore, Hamilton, and Portland. Serving this expansive area requires a sophisticated logistics network capable of ensuring timely delivery of essential medical supplies, linen, food, and equipment to 13 hospitals in the region.
“We provide more than 150 medical, nursing, mental health, allied health and community health services to the 110,000 people who live across the Southwest of Victoria and in Warrnambool, one of the fastest-growing regional cities in Victoria,” said Michael Farley, Construction Project Manager at South West Healthcare. “We are also the region’s largest employer, with 2,158 people working for South West Healthcare across various locations.”
The increasing population in the region, coupled with aging infrastructure at the Warrnambool Base Hospital, created an urgent need for a modernised logistics system that could handle the demands of today, while being flexible enough to accommodate future growth.
South West Healthcare recognised that its Regional Logistics Distribution Centre (RLDC) in

Warrnambool required a significant upgrade to address these challenges.
Faced with growing demand, the need for more storage capacity, and the constraints of outdated facilities, South West Healthcare embarked on a project to build a state-of-the-art RLDC. The organisation turned to Dematic for a solution that would not only meet the region’s immediate supply chain needs, but would also future-proof operations for years to come.
The new RLDC, constructed in 2023, allowed for South West Health’s laundry and supply and logistics services to move from their original location at the Warrnambool Base hospital campus to make way for the Victorian Government funded Warrnambool Base Hospital redevelopment project. This project freed up space for vital health services within a brand new multi-storey clinical services building at the existing hospital site.
The Challenge: Space Limitations and Operational Inefficiencies
At the core of the challenge for South West Healthcare was a lack of space. The distribution centre’s existing facilities were limited in size, resulting in frequent reordering of supplies and excessive stock handling.
According to Farley, the RLDC was becoming
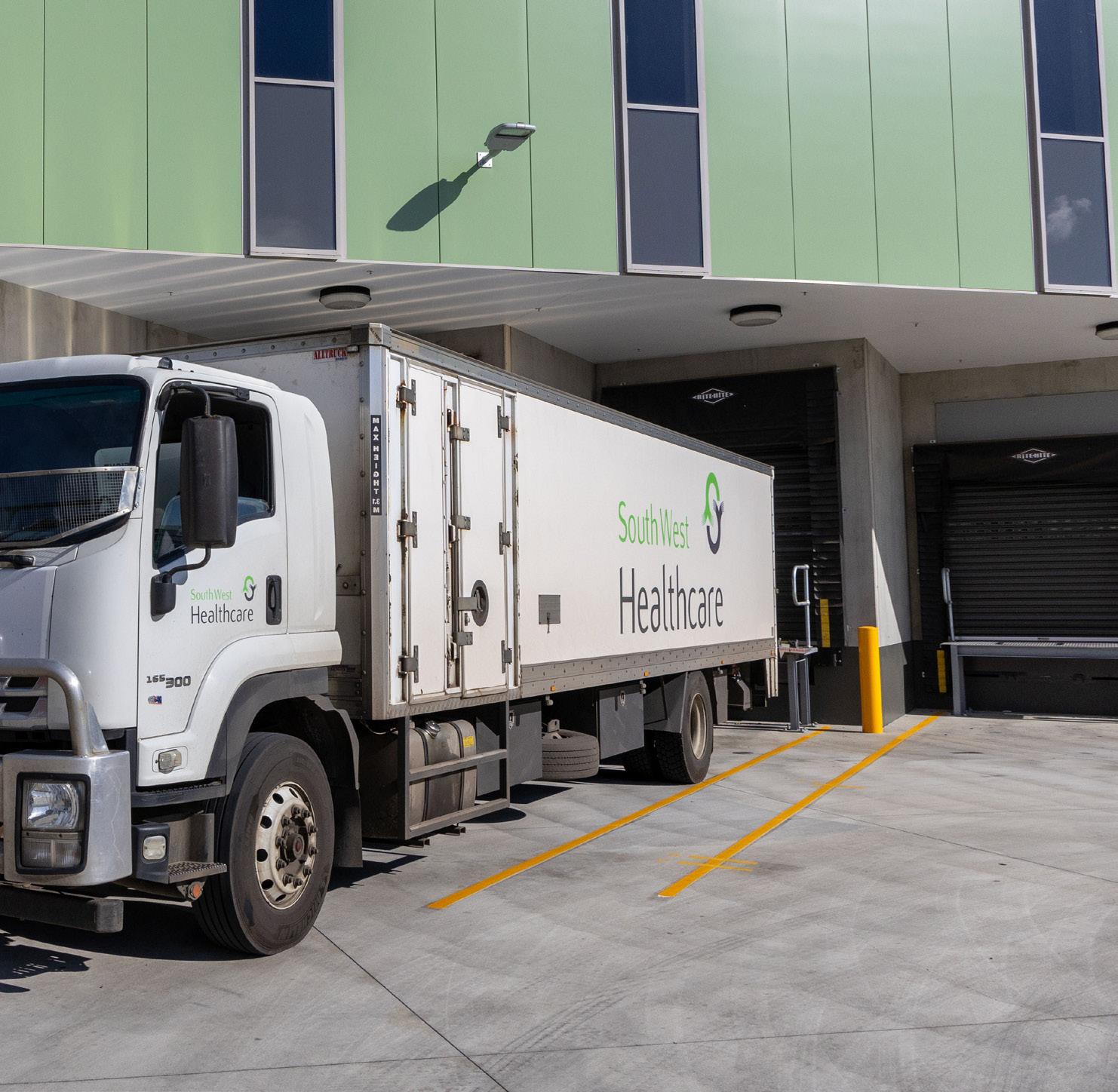
increasingly stretched as the healthcare needs of the region continued to grow.
“Warrnambool and the surrounding region are growing rapidly,” said Farley. “Our logistics facility, which once met our needs, was simply no longer large enough to handle the increased demand. We needed to build a larger warehouse and adopt a more modern approach to logistics to keep up with the region’s growth.”
Previously, the logistics team had to place frequent orders for high-usage items, which not only created inefficiencies in procurement but also increased the risk of stock shortages. The warehouse operated with traditional shelving and manual picking systems, which were not equipped to handle the high volume of orders and stock rotations necessary to support 13 hospitals across the region.
“Our old facility couldn’t store more than a week’s worth of stock for many high-usage items,” said Shane Grundy, Warehouse Logistics Manager at South West Healthcare. “This meant we had to reorder frequently and handle the same goods multiple times, increasing the workload for our staff and the chance of errors.”
Compounding these space and operational challenges was the need for the RLDC to serve as a critical part of the redevelopment plan for the Warrnambool Base Hospital. The RLDC needed to act as a logistics hub, supporting the base hospital and other regional facilities while new clinical service buildings, including emergency departments and operating theatres, were being constructed.
The Solution: Choosing Dematic’s AutoStore GTP System
To address these challenges, South West Healthcare sought a solution that could significantly increase storage capacity, improve order accuracy, and reduce the time spent handling stock. After a comprehensive evaluation process, Dematic’s AutoStore™ goods-toperson (GTP) system emerged as the clear choice for the RLDC’s modernisation efforts.
“Once we understood that AutoStore was the right solution for our needs, Dematic’s presentation really stood out,” said Farley. “Their ability to service regional Victoria and their commitment to a five-year maintenance contract gave us confidence that they were the right partner for this project.”
The Dematic solution requires up to 80% less space than a traditional manual racking layout, which needs wide aisles for forklifts and personnel. AutoStore totes stack vertically, eliminating the need for clear aisles.
The AutoStore solution is a high-density storage system that maximises the use of vertical space, allowing more goods to be stored in a smaller footprint. It utilises robots that move through a storage grid to retrieve totes and deliver them to ergonomic pick stations.
Items required to fulfil orders arrive from the AutoStore storage system to the GTP workstations precisely when they are needed. Operators then build orders at the ergonomically designed, high-rate workstations efficiency and safely.
This automation eliminates the need for manual stock handling, reduces the risk of errors, and significantly increases efficiency.
“One of the key benefits of the AutoStore system is its ability to store more items in a much smaller space,” explained Terry Jamieson, Business Development Manager at Dematic. “For South West Healthcare, this was critical. The laundry services at the RLDC needed to expand, so reducing the footprint of the storage facility was essential to making space for other functions.”
The AutoStore GTP system’s modular design also provides flexibility for future expansion, allowing South West Healthcare to easily add more robots and pick stations, or increase the size of the modular storage grid as demand grows.
South West Healthcare also chose Dematic’s selective pallet racking, ColbyRACK, for storing bulky items that weren’t suitable for the AutoStore GTP system. Designed, engineered, and manufactured by Dematic’s Australian team, ColbyRACK meets rigorous Australian standards.
Implementation: A Seamless Installation Process
Installing the AutoStore GTP system was a complex process, particularly due to its integration with South West Healthcare’s existing Oracle-based ordering system. However, Dematic’s project team worked closely with South West Healthcare to ensure that the installation was as seamless as possible.
“The biggest challenge we faced during the installation was integrating the AutoStore system with our Oracle ordering system,” said Farley.
“It was a highly complex task, but Dematic’s Software Engineering team worked diligently to ensure that the integration was smooth and effective.”
Despite these technical challenges, the overall installation process was completed on schedule, and Dematic provided extensive training to ensure that South West Healthcare’s staff could operate the system efficiently.
“The training provided by Dematic was topnotch,” said Grundy. “Our team was excited to learn the new system, and they adapted to it quickly.
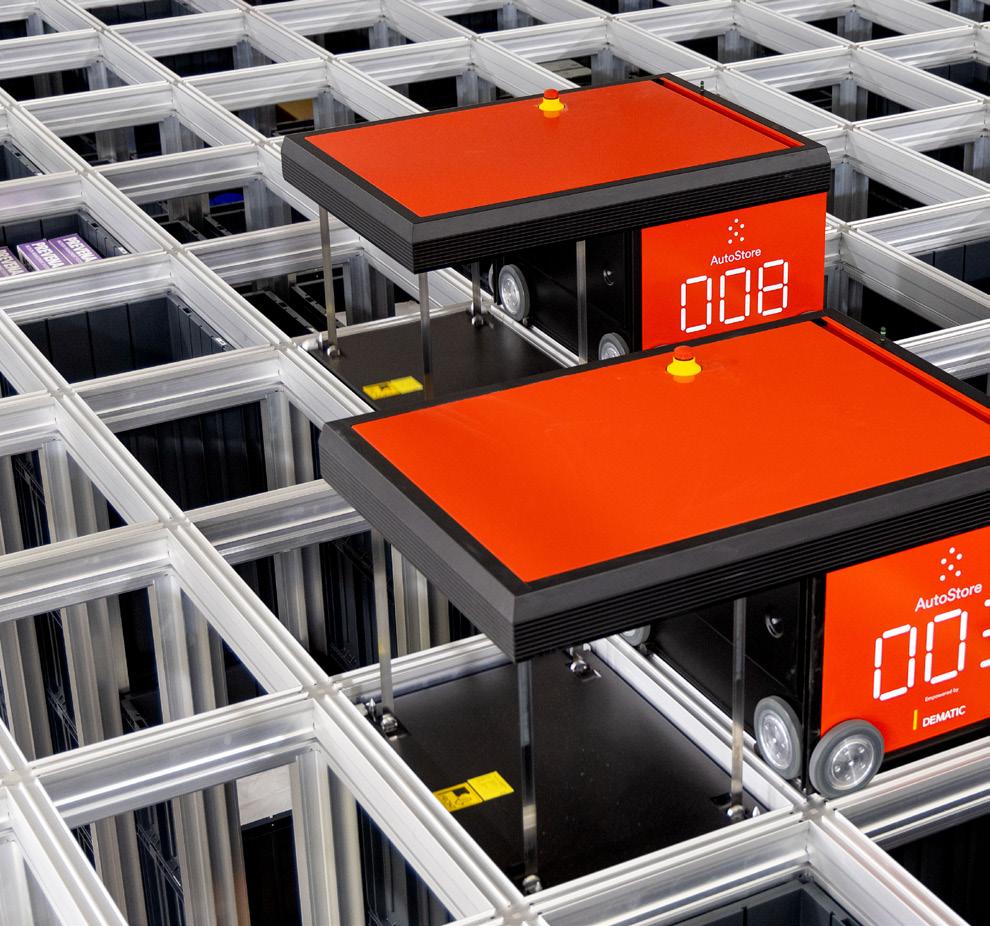
The AutoStore system has not only improved our operations but has also provided an opportunity for staff development as they get to work with cuttingedge technology.”
The Benefits: Increased Capacity, Accuracy, and Efficiency
Since the implementation of the AutoStore GTP system, South West Healthcare has seen significant improvements in its supply chain operations. The system has provided a range of benefits, including:
• Dramatically Increased Storage Capacity: One of the most immediate benefits of the AutoStore GTP system was the increase in storage capacity. The RLDC now holds up to 6,500 totes, allowing South West Healthcare to store six to eight weeks’ worth of stock for high-usage items, compared to the one-week capacity in the previous facility. This increase in capacity has reduced the need for frequent reordering and has allowed the warehouse team to focus on more value-added tasks. “We’ve increased our stock holdings by nearly $200,000,” said Grundy. “That means our purchasing team can focus on strategic tasks rather than spending time reordering the same products every week. We’ve also been able to reduce backorders and improve our service levels across the region.”
• Improved Accuracy and Reduced Errors: The AutoStore GTP system has greatly improved order accuracy by automating the picking process. In the previous system, staff manually picked items from shelves using paper-based picking slips, which created the potential for errors. With AutoStore, the correct product is automatically delivered to the pick station, reducing the chance of human error. “The system has virtually eliminated picking errors,” explained Grundy. “Now, the right product comes directly to the operator, which has significantly improved the accuracy of our orders and made the entire picking process much more efficient.”

• Optimised Space Utilisation: The high-density design of the AutoStore GTP system has allowed South West Healthcare to maximise the use of available space, freeing up room for the expansion of other critical services. By consolidating storage into a smaller footprint, the RLDC has been able to accommodate the growing needs of its laundry services, which are essential for supporting hospitals in the region. “One of the major benefits of the AutoStore system is that it reduced the footprint required for storage,” said Jamieson. “This allowed South West Healthcare to allocate more space to other essential functions, such as the laundry, which is critical to the operation of hospitals in the region.”
• Futureproofed and Scalable: The modular design of the AutoStore GTP system ensures South West Healthcare can easily expand the system in the future as demand increases. The RLDC has the option to add more robots, increase the size of the storage grid, or add additional pick or replenishment stations as needed. “The system is designed to grow with us,” said Grundy. “While we’re not planning any immediate expansions, it’s comforting to know that we have the flexibility to increase capacity if the demand continues to grow in the coming years.”
• Faster Turnaround Times and Improved Service: The streamlined operations provided by the AutoStore GTP system have enabled South West Healthcare to improve its service levels. Orders from regional healthcare facilities are now processed and delivered more quickly, with same day delivery for Warrnambool Base Hospital and next-day delivery for other regional campuses becoming the norm for most items.
“We’ve seen a significant improvement in our order fulfilment times,” said Grundy. “The system processes orders much more efficiently, allowing us to get supplies to our hospitals faster. This has been a huge benefit for the region, particularly in emergencies when time is of the essence.”
Support and Ongoing Partnership with Dematic
The partnership between South West Healthcare and Dematic has been a key factor in the success of the project. Dematic provided ongoing support throughout the installation and continues to deliver maintenance and remote IT support to ensure the system operates smoothly.
“Dematic’s commitment to supporting regional Victoria was a big reason we chose them as our partner,” said Farley. “Their team has been fantastic to work with, and their ongoing support has been instrumental in ensuring that the system continues to run efficiently.”
Dematic’s Victoria-based service team provides regular maintenance visits every three months, checking the system to ensure it is functioning as expected. Additionally, remote IT support is available 24/7 to address any issues that arise, allowing the RLDC to operate with minimal downtime.
“Dematic’s support has been excellent,” added Grundy. “Whenever we’ve had an issue, they’ve responded quickly.”
A Future-Ready Logistics Hub for South West Healthcare
The implementation of Dematic's AutoStore GTP system has successfully transformed South West Healthcare’s RLDC into a modern, efficient, and future-proof operation. By overcoming space constraints, improving accuracy, and streamlining processes, the new system has enabled South West Healthcare to meet the increasing demands of the region’s healthcare facilities while ensuring longterm scalability.
"Our partnership with South West Healthcare demonstrates how automation can be tailored to meet specific needs and challenges. We’re proud to have delivered a solution that not only meets today’s demands but is also ready to scale for the future," said Jamieson.
Looking ahead, South West Healthcare is wellpositioned to continue providing exceptional service to its healthcare partners across the region, supported by a robust and flexible supply chain infrastructure.
"The AutoStore system has been a game-changer for our operations. The technology is cutting-edge, the support has been excellent, and our staff are excited to work with such a modern system. We’re better equipped than ever to meet the demands of our region," explained Grundy.
Dematic’s AutoStore GTP system has proven to be the ideal solution, offering both immediate improvements and longterm sustainability, ensuring that South West Healthcare can continue to deliver vital services efficiently and reliably.
As the region continues to grow, South West Healthcare's RLDC will continue to highlight the benefits of strategic automation in the healthcare logistics space.
"We needed a solution that would allow us to manage today’s needs while preparing for the future. Dematic’s AutoStore system has exceeded our expectations in terms of efficiency, scalability, and service, allowing us to provide the best possible care for the region's healthcare facilities," Farley concluded. ●
Supercharging Logistics with Wearables, Machine Vision, and Artificial Intelligence (AI)
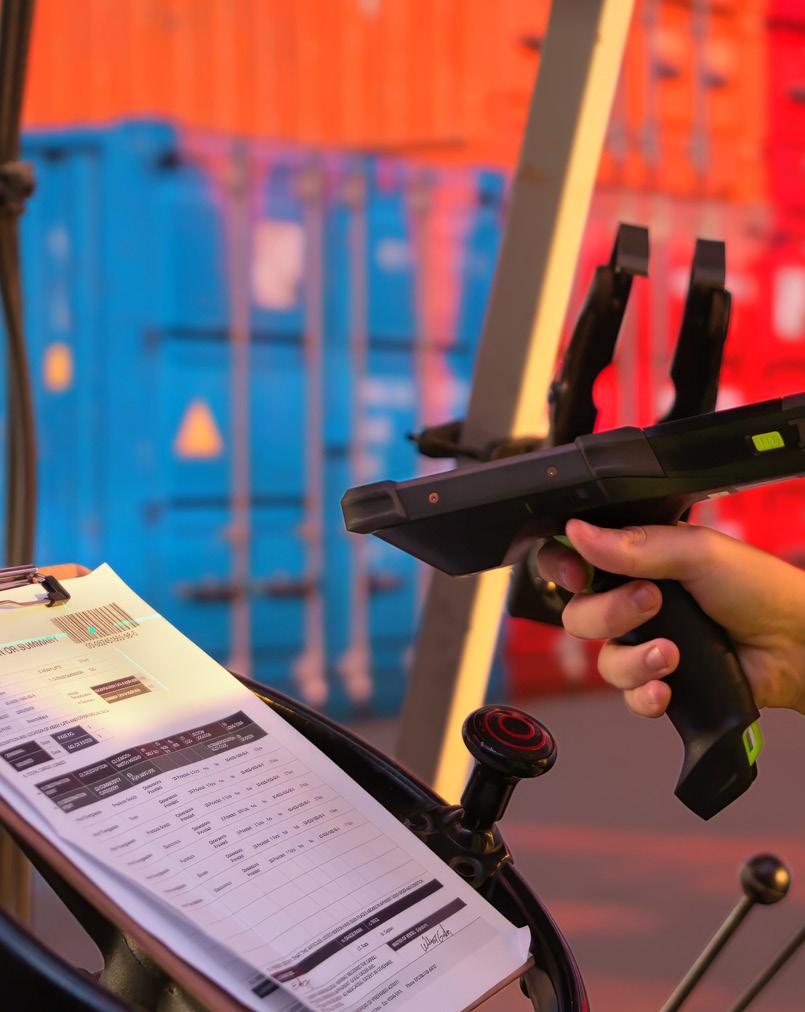
WRITTEN BY VIVIEN TAY, APAC MARKETING LEADER FOR WAREHOUSE & DISTRIBUTION, ZEBRA TECHNOLOGIES
The transportation and logistics industry serves as the lifeblood of Asia Pacific’s thriving economic landscape, helping businesses worldwide operate smoothly and efficiently.
However, the industry continues to battle immense waves of disruption, from the rise of new business models and evolving consumer behaviours to labour shortages and black swan events like COVID-19.
These events have driven demand for fast, reliable, and affordable logistics to new heights, stretching operators to their limits. For example, the retail sector faces skyrocketing demand for deliveries, driven by booming omnichannel e-commerce and an evolving returns culture—spiking demand for accelerated last-mile and reverse logistics services. According to Zebra Technologies’ 2023 Global Warehousing Vision Study, 40% of warehouse decision-makers in APAC cited returns management as their top operational challenge.
As costs rise and trade landscapes continue to shift, retailers and businesses across industries are under greater pressure to ramp up productivity in logistics. The same Zebra Study found that 75% of warehouse decision-makers in APAC are under pressure to improve performance while adjusting to shifting consumer e-commerce demands.
How can logistics operators overcome these issues while they face mounting challenges, like tightening budgets and labour shortages? The answer lies in next-generation technologies.
Enhance Front-line Efficiency
with a New Generation of Wearables and Devices
Logistics workforces have long relied on connected devices, like mobile computers and scanners, to help warehouse workers complete tasks faster and more accurately. However, a new generation of humancentric technologies, like wearables, presents an opportunity for businesses to supercharge efficiency.
These devices can direct users to the right pick locations and verify their picks, improving accuracy, accelerating task times, and reducing ramp-up times. Purpose-built wearables offer superior ergonomics and efficiency compared to mobile computer applications. Head-mounted displays, for example, can provide warehouse workers with the most relevant contextual information through augmented reality to complete their tasks. Wearables can be particularly effective, as they are ruggedized to withstand heavy physical use and function optimally in direct sunlight, cold conditions, or dusty environments—making them perfect for warehouse settings.
Businesses can equip front-line workers with wearable scanners to enhance efficiency even further. For example, delivery workers out in the field can use hand-mounted scanners to quickly process goods on the go. The hands-free ergonomic design
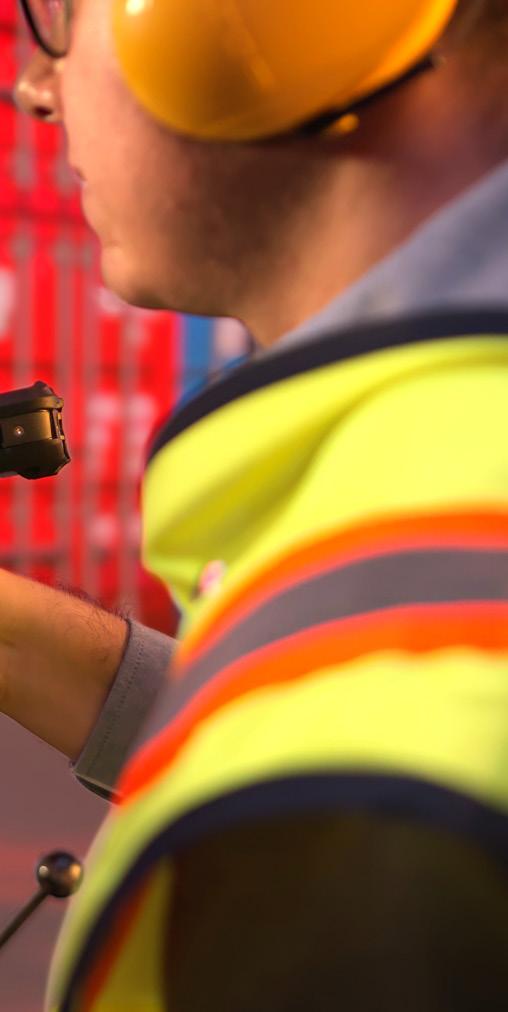
and low profile of these scanners gives workers the flexibility to better handle goods—especially when dealing with numerous boxes in confined spaces, like a fully-loaded truck.
One of Vietnam’s leading express delivery companies recently integrated finger-mounted scanners and other visibility technologies into their operations, which increased operational efficiency by 15%, reduced costs by 5%, and enhanced employee satisfaction and retention. More businesses are looking to empower their front-line employees with human-centric technologies— with 94% of decision-makers globally planning to deploy wearables to support their workforce by 2028, up from 43% in 2023.
Enhancing Productivity and Visibility with Machine Vision and Automation
Logistics operators can also turn to machine vision (MV) solutions to enhance visibility and productivity across the supply chain. MV uses a combination of hardware, software, and electronics to enable computers to ‘see’ items in the real world, analyse them, and make decisions based on that analysis. In a warehouse or industrial setting, MV solutions enable businesses to perform automated inspection, process control, and operational guidance based on image analysis—enhancing accuracy and efficiency throughout the supply chain.
For example, in a warehouse, fixed industrial scanners mounted overhead or by a conveyor belt (scan tunnels) enable rapid automatic scanning and tracking of goods as they pass through the hands of workers and throughout the supply chain. The capability of MV solutions to recognize elements in an image also enables businesses to read shipping labels with high accuracy, confirm label presence and placement on packages, and even check if they are correctly and accurately placed via these scan tunnels, giving clear visibility over every item wherever it may be in the supply chain.
This automation reduces manual labour, minimises delays from misreads, and enhances the overall productivity and quality of service in logistics operations.
Businesses can also use the data from such MV solutions to glean actionable insights and optimise processes across environments—enabling better quality control, cost reductions, and increased operational flexibility on a larger scale.
One leading logistics provider in Germany recently implemented MV solutions to improve its handling of goods, given it was dealing with very high volumes and rapid turnovers of inventories. To enhance productivity, the group installed fixed
industrial scanners at inbound and outbound gates at their warehouse, which automatically scanned shipping labels on goods—even poorly printed, faded, or damaged ones. This autonomous system enabled the logistics provider to process packages much faster, generating over 50% time-savings for the logistics provider.
Helping Workers Do More with Less Through Generative AI
Generative artificial intelligence (GenAI) solutions can also be used as a catalyst to help businesses boost productivity and visibility at scale.
These solutions, powered by large language models like ChatGPT, have the capability to analyse vast amounts of data across the enterprise and provide personalised, actionable insights in an easily understandable format. With the ability to understand nuances in natural language and conversation, GenAI solutions enable workers to obtain answers to specific questions in intuitive ways—like asking a human coworker.
By training GenAI models on standard protocols, operational insights, and leading practices—and providing staff access to these solutions, logistics operators can accelerate onboarding and training of workers to achieve full productivity, especially useful during periods of high demand. Fifty-four percent of decision-makers globally believe the onboarding takes too long, according to the same Zebra Study.
In Europe, one supermarket chain is already piloting GenAI with Zebra Technologies’ mobile computers. By empowering employees with these computers and feeding the GenAI-enabled models their entire SOP library, the business saved time, accelerated training, elevated customer interactions, improved worker autonomy and enhanced employee satisfaction.
Deliver Success Today with the Technologies of Tomorrow
Embracing innovations in the fields of wearable technology, MV, and GenAI, is crucial for businesses seeking to stay ahead of evolving challenges. These next-generation technologies have the potential to enhance organisational efficiency, productivity and visibility—all while helping companies better close manpower gaps and develop a more engaged workforce. While implementing new technology may seem daunting, businesses can realise tremendous benefits by starting with something as small as equipping workers with wearable computers.
As stakeholders become more comfortable with these technologies, companies can gradually scale to use more advanced solutions—enabling the organisation to tackle bigger logistics challenges and stay competitive in the long run. ●
Read Zebra’s Warehouse Vision Study here.
Shippit Launches International Solution to Tackle Cross-Border Shipping Challenges for Australian Retailers
WRITTEN BY
JOHN-DAVID KLAUSNER, VICE PRESIDENT OF BUSINESS DEVELOPMENT & STRATEGIC ALLIANCES, LOOP
Shippit, the industry-defining commerce delivery platform that powers hundreds of millions of deliveries for 4,000 retailers across Australia, New Zealand, and Southeast Asia, has announced the launch of Shippit International.
The solution is poised to meet the growing demand for international expansion, as highlighted by Shippit’s latest State of Shipping Report which reveals that 66% of retailers view global expansion as a critical objective for the next 12 months. Shippit International is designed to make cross-border shipping less expensive and complex.
International shipping has been a persistent challenge for Australian retailers, with rising costs and complex regulations stifling global growth opportunities. Over the past year, international parcel delivery costs have risen by nearly 5%, forcing retailers to navigate long transit times and high expenses with existing providers. Furthermore, nearly 60% of global consumers have reported poor international delivery experiences, with unexpected customs duties prompting 75% of them to reconsider future purchases from the same brand.
“International shipping is pivotal to our growth as we expand into global markets," said Christopher
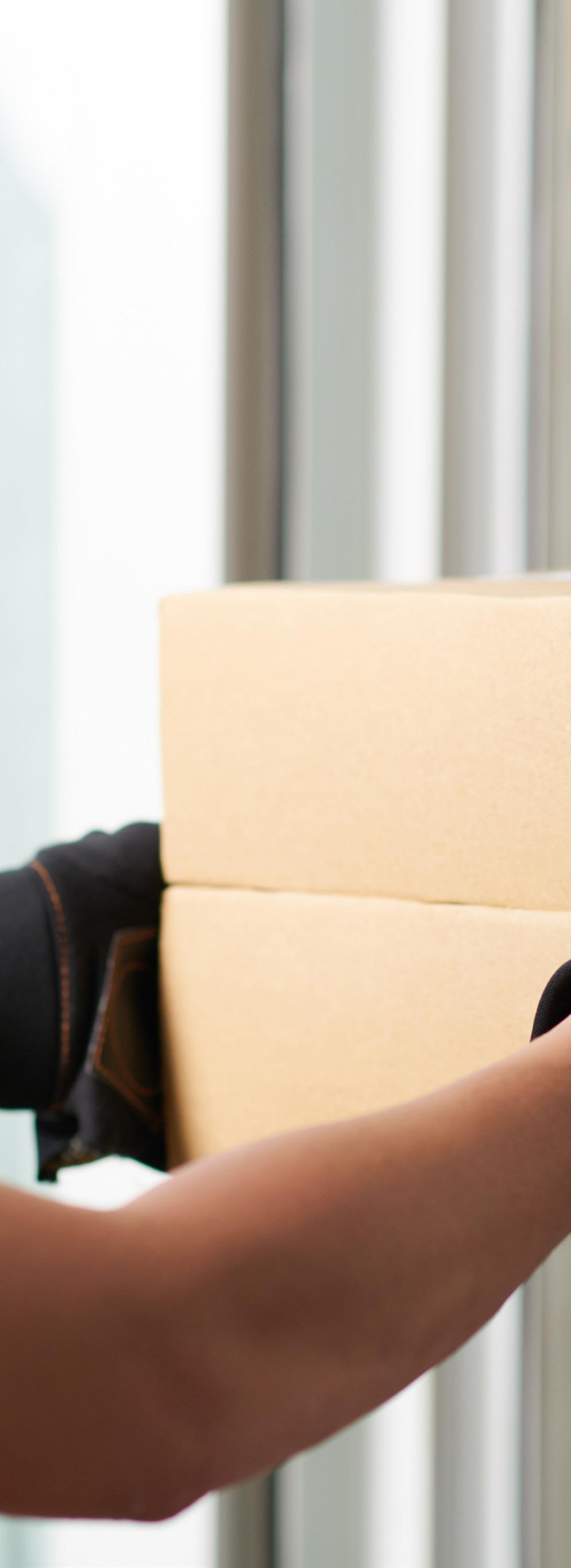
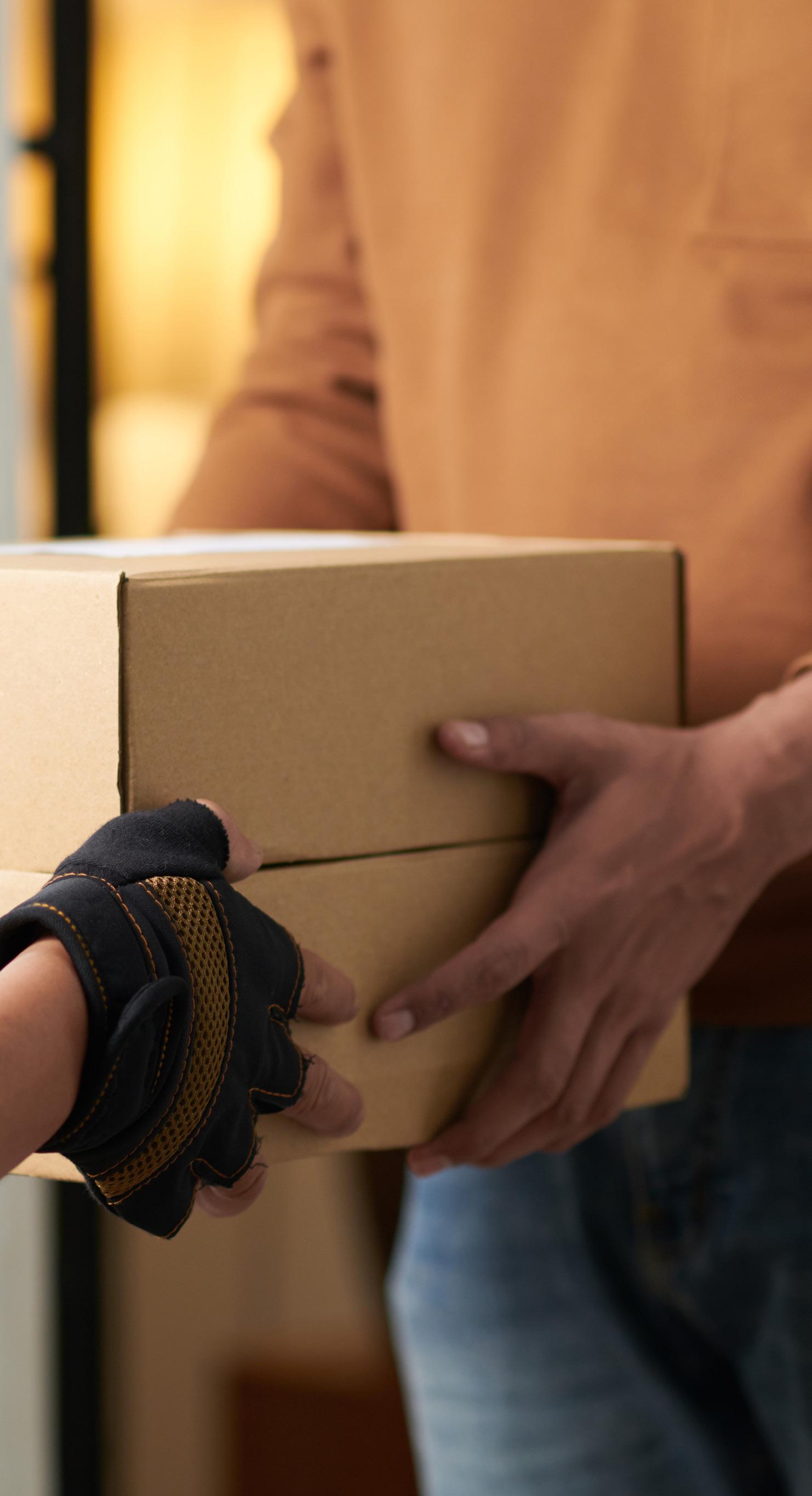
Lockwood at City Beach Australia. “To sustain high customer satisfaction and meet the needs of international consumers, we require streamlined and cost-effective shipping solutions. Reliable and affordable shipping options are crucial for reaching new audiences and driving our business forward.”
Shippit International directly addresses these issues by providing Australian retailers with access to global markets through a flexible, multi-carrier solution that addresses rising costs and poor customer experiences. By leveraging Shippit’s Smart Routing service and securing competitive rates with key carriers like FedEx, Shippit offers a flexible, cost-effective alternative to traditional shipping providers. This approach simplifies global expansion for retailers, ensuring efficient transit times and competitive pricing.
“eCommerce has opened up the world, but for too long, Australian retailers have struggled to access global markets," said Inga Latham, Chief Product Officer at Shippit. “Shippit International is designed to meet these needs by providing reliable, costeffective international shipping. It enables retailers to tap into new markets, which is essential as Australian consumers face cost-of-living pressures that are impacting discretionary spending. With only 6% of global buyers shopping from Australian retailers, this solution offers a significant growth opportunity. Our goal is to empower retailers to expand their reach with confidence, knowing they have the tools to deliver a seamless experience to customers worldwide.”
Key services offered by Shippit International include simplified global expansion, which provides easy access to international delivery services without lock-in contracts.
The solution features automated calculations for duties and taxes, ensuring a straightforward cross-border shipping process backed by a landed cost guarantee.
Additionally, Shippit’s Smart Routing International service offers market-leading rates, delivering costeffective and reliable shipping solutions to major eCommerce markets such as North America, New Zealand, and the United Kingdom. Retailers can also benefit from fast and reliable transit times through Shippit’s partnership with FedEx, which provides exclusive rates for FedEx’s express International Priority service. This allows Australian retailers to leverage 1-2 day transit times to the United States, ensuring prompt and dependable deliveries, particularly during peak periods like the holiday season. FedEx's 7-day delivery option enhances retailers' capacity to meet holiday shipping deadlines. ●
Insights from CeMAT Singapore and Australia: Top APAC Supply Chain Challenges Revealed
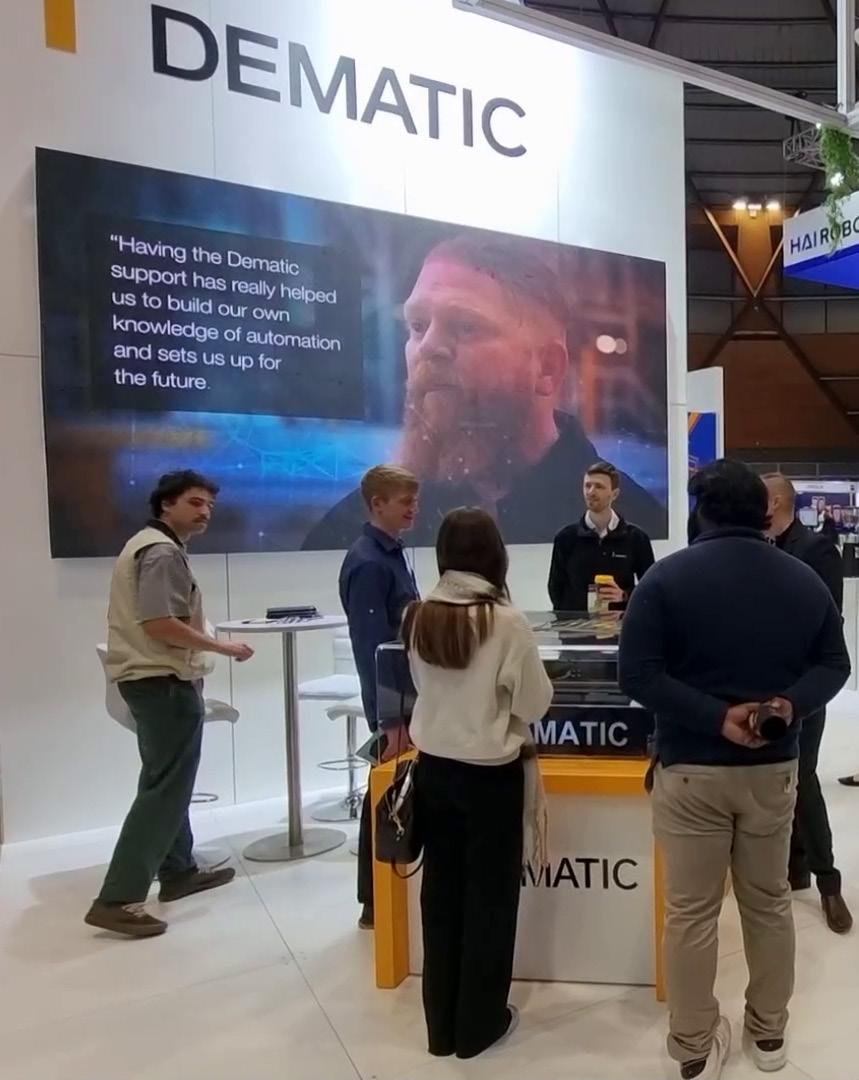
At the recent CeMAT Singapore and Australia events, Dematic conducted surveys to identify the biggest supply chain challenges faced by industry professionals across the APAC region. This survey provides valuable insights into the priorities and obstacles currently shaping the supply chain landscape. With supply chains being the backbone of global commerce, understanding these challenges is crucial for developing strategies to enhance efficiency and resilience.
Supply chain professionals are constantly navigating a complex array of issues, from cost management and labour shortages to sustainability and
technological integration. The survey results offer a clear picture of where the APAC industry is feeling the most pressure and where opportunities for improvement lie. As companies strive to adapt to rapidly changing market conditions and consumer expectations, these insights will be instrumental in guiding future innovations and solutions.
Key Findings
1. Labour Costs and Availability (28%): The most significant challenge identified by respondents was labour costs and availability, cited by 28% of participants. The supply chain sector is heavily dependent on skilled labour for various operations, from warehousing and transportation to data analysis and customer service. However, the industry is currently facing a shortage of qualified workers, exacerbated by factors such as aging populations, changing workforce expectations, and the competitive job market. High labour costs, driven by the need to attract and retain talent, are putting additional strain on supply chain budgets. Addressing this challenge requires a multifaceted approach, including investment in automation and technology to reduce dependency on human labour, as well as initiatives to upskill existing employees and make supply chain careers more attractive.
2. Overall Rising Costs (18%): Overall rising costs were highlighted by 18% of respondents as a major challenge. This encompasses a wide range
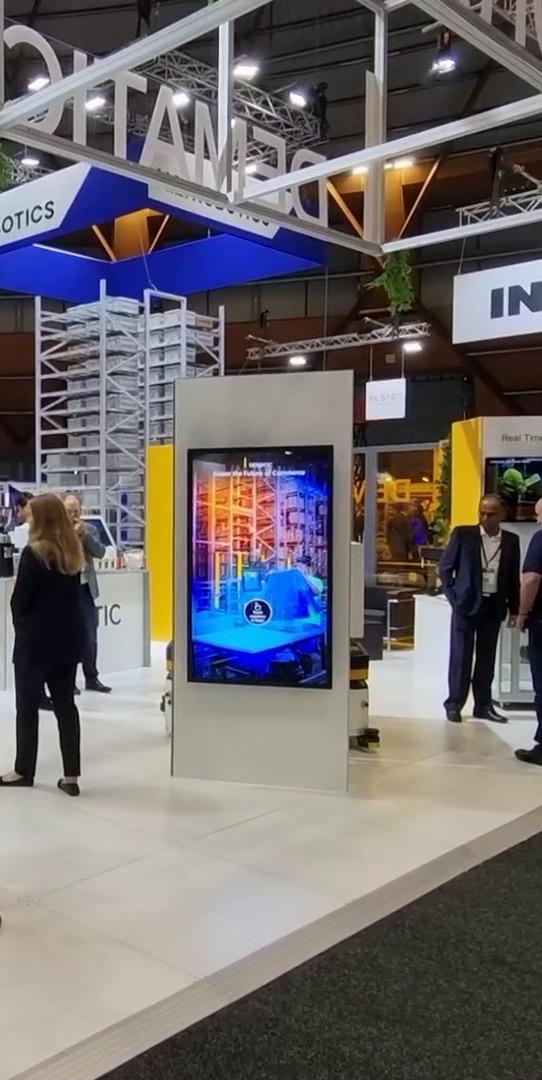
of expenses, including raw materials, energy, transportation, and compliance with regulatory requirements. Global economic conditions, such as inflation and trade tariffs, are contributing to these increased costs, squeezing profit margins for supply chain operators. To mitigate this issue, companies are exploring cost-saving measures such as optimising supply chain networks, improving energy efficiency, negotiating better terms with suppliers and using intelligent software and technology to optimise packing and use of transport cube. Additionally, leveraging data analytics can help identify inefficiencies and areas where costs can be reduced without compromising service quality.
3. Use of Space (14%): Effective use of space was highlighted by 14% of participants as a critical challenge. As companies strive to optimise their operations, maximising warehouse and storage efficiency is crucial. Space constraints can lead to inefficiencies, higher operational costs, and limitations in inventory management. To address this, businesses are adopting innovative storage solutions such as high-bay warehousing and automated storage and retrieval systems (AS/ RS). These technologies enable better utilisation of available space, reduce handling times, and improve overall warehouse productivity. Additionally, strategic location planning for distribution centres can help minimise transportation costs and improve delivery times.
4. Sustainability Concerns (13%): Sustainability emerged as the fourth most important challenge, with 13% of respondents prioritising it. There is growing pressure on companies to adopt environmentally responsible practices, driven by regulatory requirements, consumer demand, and corporate social responsibility initiatives. This includes reducing carbon emissions, minimising waste, and sourcing materials ethically. For supply chain operations, this means rethinking logistics strategies to reduce environmental impact, investing in sustainable technologies, and adopting circular economy principles. While these initiatives can involve significant upfront costs, they also offer long-term benefits in terms of brand reputation, regulatory compliance, and operational efficiency.
5. Delivering Quickly (8%): Speed of delivery is a critical factor, with 8% of respondents indicating it as a major challenge. In today’s competitive market, meeting customer expectations for rapid delivery times is essential. This is particularly important in the e-commerce sector, where sameday and next-day delivery options are becoming the norm. To achieve faster delivery times, companies are investing in advanced logistics solutions, including automation, technology and intelligent real-time tracking and optimisation software. Additionally, building a network of strategically located fulfilment centres can help reduce transit times and improve service levels. Balancing speed with cost efficiency remains a key challenge for supply chain professionals.
6. Other Challenges: Other notable challenges identified in the survey include:
• Visibility of Data (5%): Having real-time visibility into supply chain operations is essential for making informed decisions. Companies are adopting integrated software solutions that provide end-to-end visibility and facilitate data sharing across the supply chain ecosystem.
• Product Security (4%): Protecting products from theft, damage, and counterfeiting is vital for maintaining supply chain integrity. Implementing security measures such as tamper-evident packaging, secure transportation, and surveillance systems can help mitigate these risks.
• Fulfilment Accuracy (4%): Ensuring accurate order fulfilment is crucial for customer satisfaction and operational efficiency. Companies are investing in technologies such as barcode scanning, RFID, and warehouse management systems (WMS) to reduce errors and improve accuracy.
• Increasing Product Range (4%): Managing a wider product range requires robust inventory management and demand forecasting capabilities. Companies are leveraging advanced analytics and AI to predict consumer demand and optimise stock levels.
Supporting an Intelligent Automated Supply Chain Future
The survey results from CeMAT Singapore and Australia provide valuable insights into the current landscape of supply chain challenges across the APAC region. While labour costs and overall rising costs dominate the concerns, sustainability is also rapidly gaining importance, reflecting a shift towards more environmentally conscious practices. Addressing these challenges will be key for supply chain professionals as they navigate an increasingly complex and dynamic industry landscape.
By understanding these priorities, companies can better strategise and implement solutions to enhance their supply chain operations, ensuring they remain competitive and responsive to market demands.
Dematic works closely with customers to help them address these challenges, offering innovative automation solutions and unmatched implementation expertise to help businesses successfully navigate this ever-evolving landscape. Dematic designs, builds, and supports intelligent automated supply chain and logistics solutions powering the future of commerce for its customers in manufacturing, warehousing, and distribution. With engineering, manufacturing, and service centres in more than 35 countries, the Dematic global network has helped achieve successful installations for some of the world’s leading brands. ●
How Victoria’s Foreign Owner Surcharge is Hurting Industrial Tenants
The Added Cost of Doing Business in Victoria
Rapidly rising taxes in Victoria are hitting industrial tenants hard.
For the 2024 land tax year, the state government increased the absentee owner surcharge (also known as the ‘foreign owner surcharge’) from two to four percent from the 2024 land tax year onwards.
The surcharge exists to discourage underutilised property and applies to absentee individuals, corporations, or trusts, that own property in Victoria but reside or operate primarily outside of Australia.
Introduced in 2016, the initial surcharge began at 0.5 percent, increased to 1.5 percent for the 20172019 land tax years, and to two percent for the 2020-2023 land tax years. As of 2024, this has now increased to four percent.
With Victoria facing exponential debt in 2024 of over AUD $135 billion in the face of post-pandemic spending, the state government is using land tax changes as one way to recover debt.

But the impact across residential and commercial land holdings is becoming evident and disproportionately impacts industrial land.
Office buildings require significantly less land than industrial, and the cost is spread over multiple tenants over multiple floors. But a single tenant usually occupies industrial property, which requires significant land holdings.
The Outgoings Provision – a New Loophole?
The state government introduced the surcharge in 2016, but rising land values, land tax, and surcharge rates mean the impact on cost is now far higher.
Although the tax targets foreign owners, Victorian businesses that lease premises where landlords are subject to the tax are the ones absorbing these surcharges.
The Retail Lease Act restricts absentee landlords from passing on the land tax to retail tenants. But most tenants within industrial fall outside of this act, meaning landlords can recover land tax from tenants through the outgoings provision of a lease. As such, we are seeing the surcharge become a key factor for tenants during renewal of lease or new lease discussions. During a recent review of outgoings for a TMX customer, the land tax surcharge equated to an additional expense of AUD $350,000 per annum and when combined with the land tax equates to
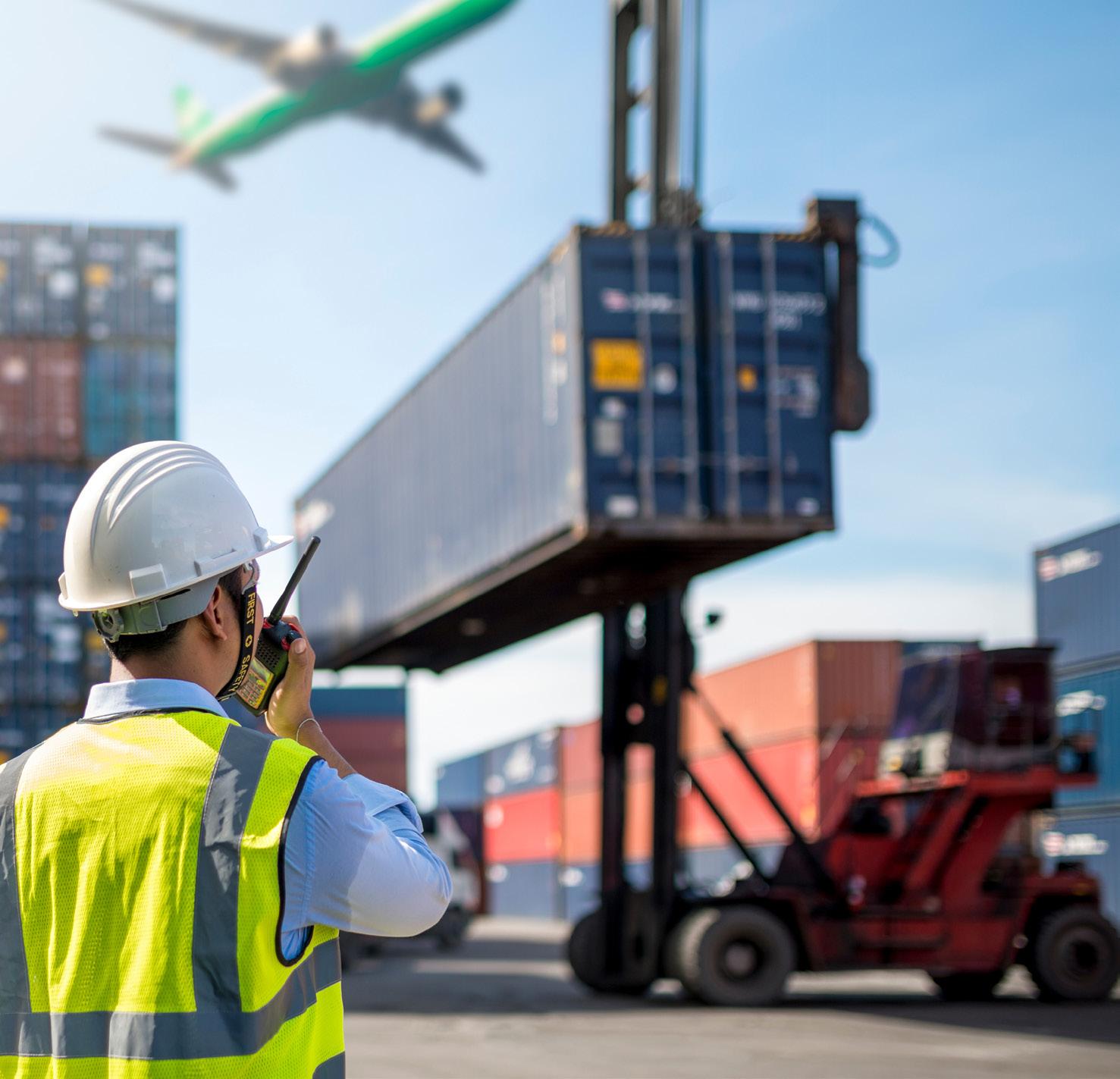
$500,000. To put this into perspective, the annual rent for the customer is AUD $1,000,000.
The land tax and the surcharge add an additional 50 percent to the tenant’s cost. And that is before the balance of outgoings such as council rates and compliance or utility services such as power.
How Tenants are Paying the Price
Land value rates have increased steadily across the past decade and therefore baseline land tax has also climbed. If we take Melbourne’s west, for example, we have seen land values for sites sub-three hectares increase from AUD $250/sqm in 2018 to around $800/sqm in 2024.
This represents a 220% increase in land value over a six-year period.
A foreign landlord passing on land tax in 2018 would have seen a tenant charged AUD $55,975 for land tax on a one-hectare parcel of land. That same
parcel of land, with the increase in land value over the past six years together with the foreign ownership surcharge, would now have land tax passed on of AUD $484,000.
For clients with larger property portfolios and multiple sites leased from foreign owners, the compounding additional total cost across their portfolio is in the millions.
The foreign status of an owner is now forming a consideration for occupiers when entering new leases, with the lease structure negotiated to ensure a landlord’s ownership structure does not disadvantage a tenant.
For example, if an asset owner sells the property to an absentee owner, the tenant may become susceptible to paying the surcharge. But the question also arises – what are the tenant’s other options? Fit-for-purpose industrial land and premises are hard to find.
The Targets of the Tax
Property is Australia’s biggest employer, contributing $234bn+ to direct GDP. Who the state government considers a foreign owner may come as a surprise. Foreign owners are often large, institutional landlords who have a parent company or an owned fund sitting outside of Australia. They are large employers within Australia and contribute significantly to the economy, through job generation within the construction and property sectors.
For tenants and occupiers, outgoings previously were a low cost and a consistent rate from one site to the next.
But we are now seeing the disparity between sites at such significant levels that costs such as land tax is being scrutinised and factored into an occupier’s feasibility when considering sites. The difference could be as much as AUD $3M or $4M, over a ten-year period.
Additionally, while negotiating new or renewal leases, the ambiguity over which party will or should absorb the costs of the surcharge is creating additional uncertainty for landlords, tenants, and managing agents alike. Carve outs and clarification on pass-through costs are now starting to become a critical negotiation point.
If this is the added cost of doing business in Victoria, what are the consequences? Is the state disincentivising businesses from investing in Victorian property? Clear legislation on this surcharge is crucial. Industrial property is a crucial part of any company’s supply chain – meaning it is the consumer who will pay the ultimate price. ●
Navigating the peak: What to expect and how to prepare for this seasonalyear’s spike
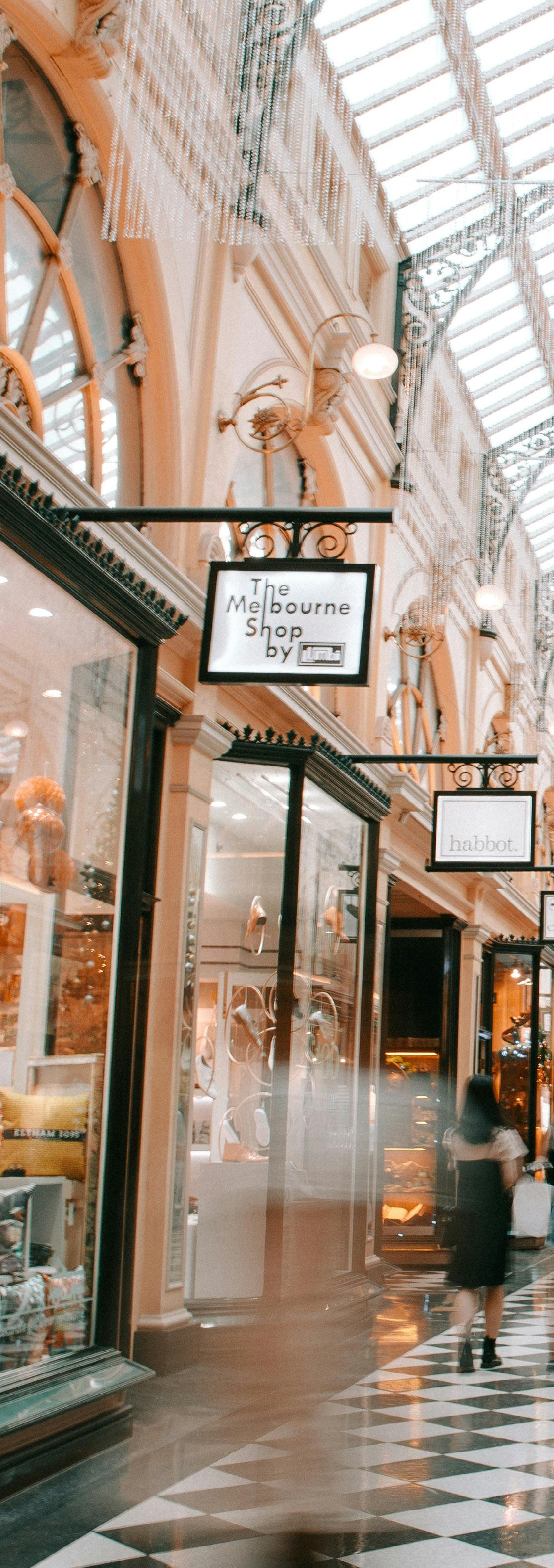
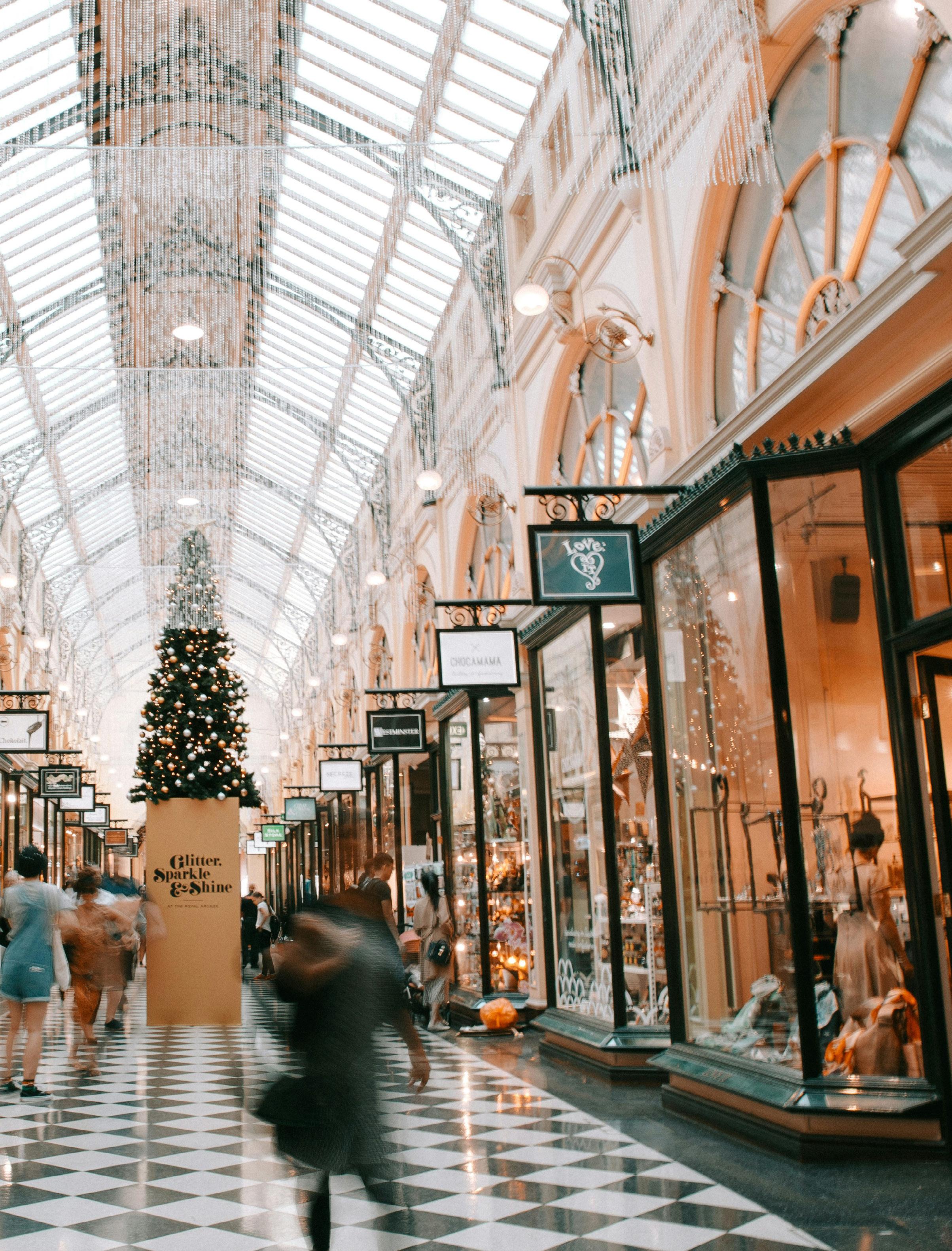
On the eve of the crucial holiday shopping period, retailers are bracing for the impact of interest rates and economic challenges on consumer spending.
Supply Chain Insights explores how strategic investments in technology, workforce management, and adaptive planning can help businesses weather the short-term challenges this peak season presents, while also setting up for long term success.
Shoppers around the country will soon visit their favourite retailers – mostly online – to start to fill their Christmas stockings. With interest rates casting a shadow over consumer spending, analysts are anticipating a challenging year for retail as customers are predicted to shop earlier this year during shopping events such as Black Friday to snap up heavily reduced items.
Glenn Barnes, Industry Manager Grocery & General Merchandise at Dematic, explains why a more cautious approach from consumers is expected this year.
"High interest rates are making consumers hold off on purchases, particularly discretionary items. There may be a bigger than normal trough-to-peak change in order volumes, and supply chain operations may need to be prepared for this, such as being ready to take on additional operators to handle the peak," Glenn says.
According to Glenn, much rests on messaging from the Reserve Bank of Australia (RBA) – hints at interest rates remaining high may temper consumer spending during the sales periods, but an interest rate cut before either or both periods could give a significant boost.
Bruce Herbert, Strategic Advisor at TMX Transform, echoes this sentiment of uncertainty.
"On the balance of probability, this peak holiday season will be a little more subdued because all the economic indicators are generally heading in the wrong direction. However, supply chain is about expecting the unexpected and avoiding broad generalisations, as different segments of the retail sector will experience different outcomes,” Bruce says.
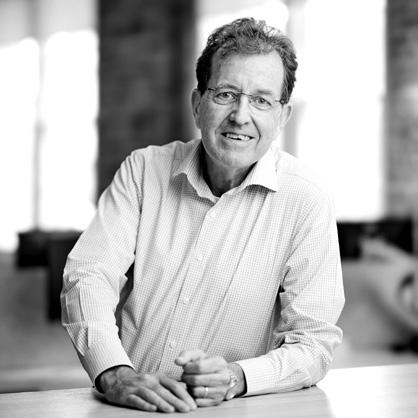
“Supply chain is about expecting the unexpected and avoiding broad generalisations, as different segments of the retail sector will experience different outcomes”
BRUCE HERBERT, STRATEGIC ADVISOR AT TMX TRANSFORM
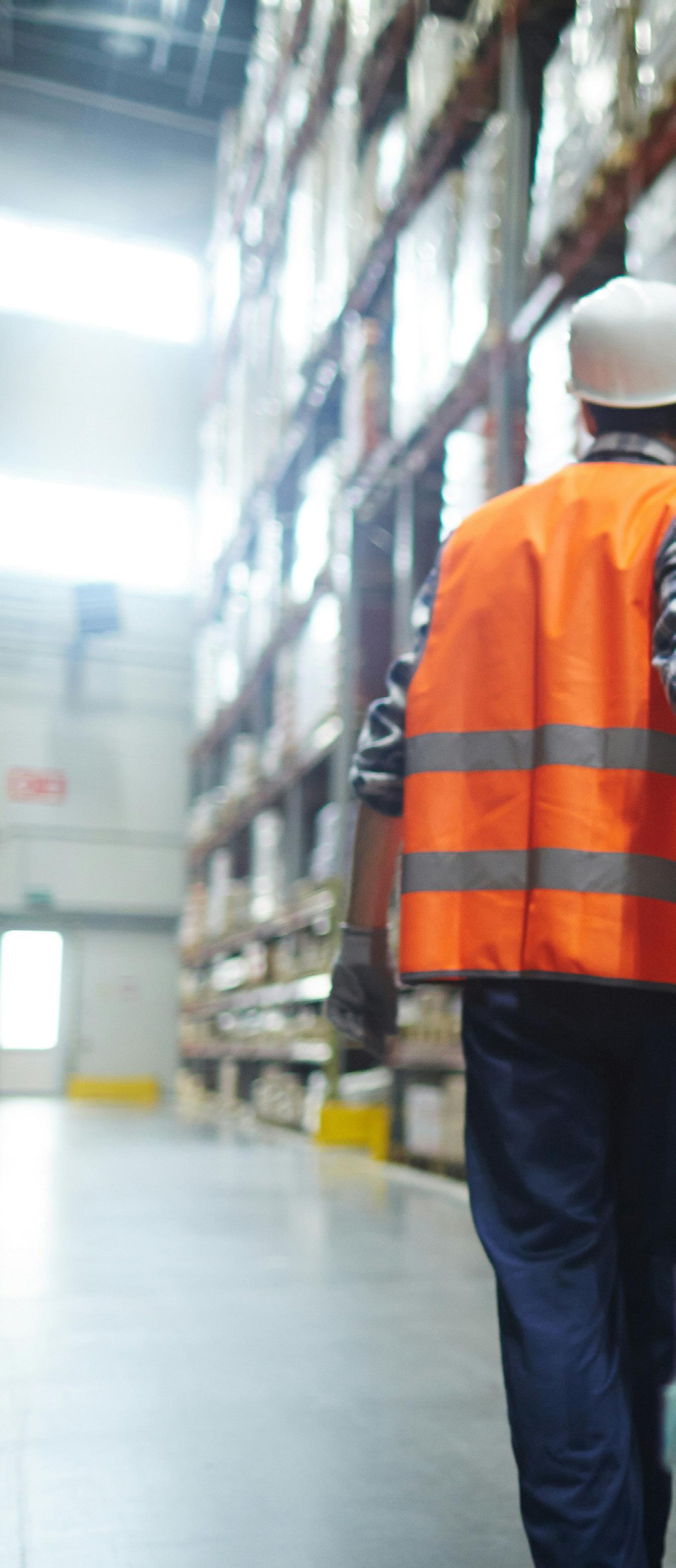
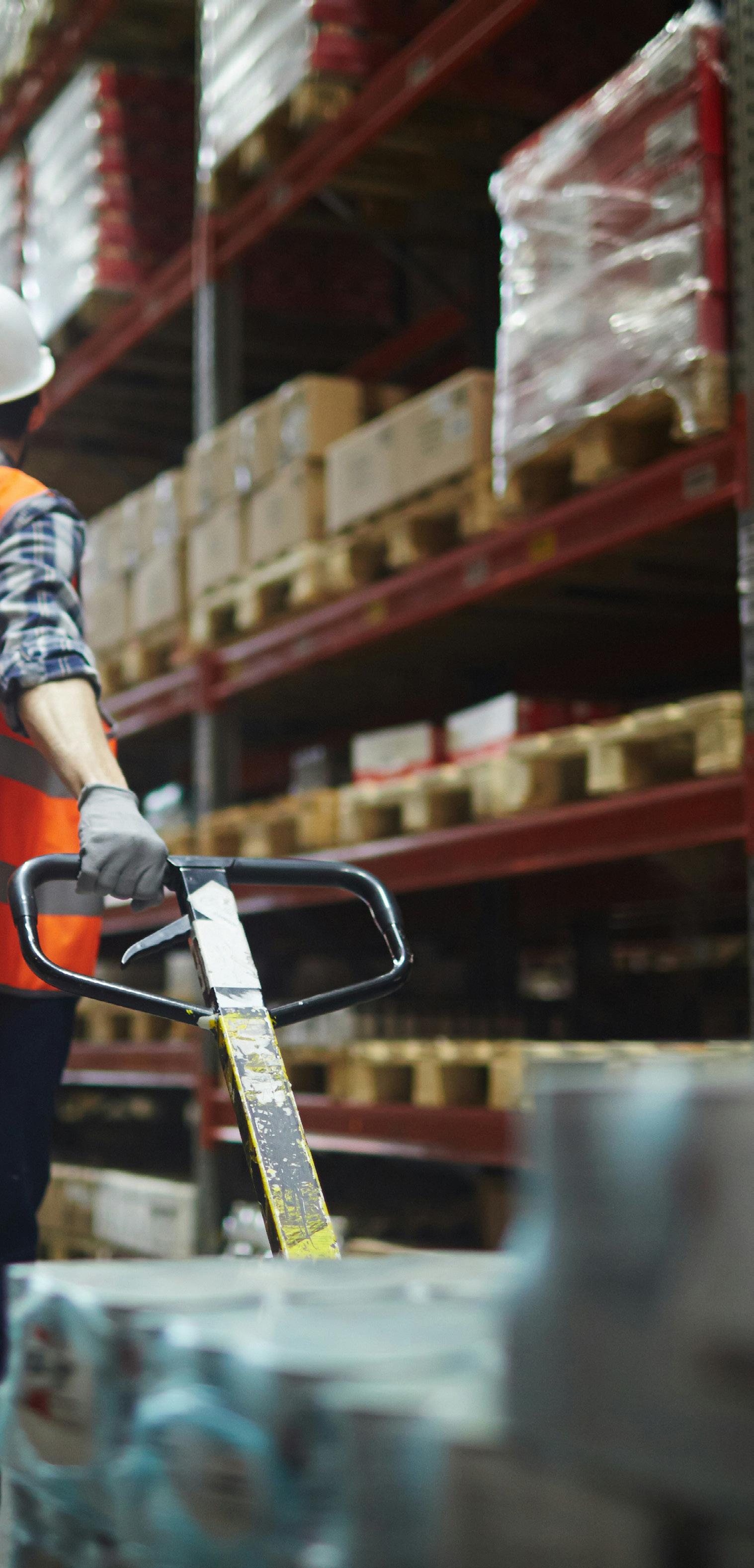
Regardless of what’s in store for retailers this holiday season, supply chains need to be prepared. Doing more with less has become a reality for many Australian organisations, and a reliable, resilient, and agile supply chain provides the groundwork for succeeding in this reality.
Forecasting in Uncertain Times
The ability to accurately predict consumer demand is the foundation for supply chain success in the retail industry. Data analytics software can predict looming shortages, identify supply chain vulnerabilities, and give managers actionable insights on how to respond to problems before they arise. Raghav Sibal, Managing Director ANZ at Manhattan Associates, highlights the complexity of this task.
"I think the biggest challenge is still predicting consumer demand,” Raghav says.
“All this planning starts months prior to peak season and relies on a combination of predictive analytics with historical data and algorithms to get a sense of demand.”
Raghav emphasises the importance of real-time data in making informed decisions.
"Real-time data is crucial in today's retail landscape. Information from point-of-sale systems, social media, and visibility tools gives instant insights into stock levels and in-transit inventory across different locations. Having this visibility and applying all these data elements to decision-making will be key to success."
This sentiment is echoed by TMX Transform’s Bruce Herbert, who points out the rapid advancements in forecasting technology.
"There used to be an ongoing debate about how to best forecast product demand. Which algorithm should we use? What factors should we consider - weather, economic activity, or other variables? The most advanced systems today sidestep this
debate by using multiple algorithms simultaneously and letting them compete against each other to determine the most accurate forecast.
"These advancements are exciting for companies investing in people and systems. However, for those not making these investments, it’s probably intimidating as they risk being left behind."
Royston Phua, Vertical Strategy Leader for Asia Pacific Supply Chains with Zebra Technologies, explains why the advancements in demand forecasting are more important than ever.
“Business leaders haven’t had to consider the impact of climate change until recently. There are more natural disasters affecting infrastructure, causing congestion and creating other issues throughout the supply chain. Organisations now have to consider three types of data: transactional, historical, and near real-time. In the past, we'd look at traditional data going back as far as five years. Today's retail environment changes so rapidly that even data from two years ago might be irrelevant, so that historical data isn’t as useful as it once was.”
Striking the Balance: Efficiency Meets Resilience
In the past, supply chain managers, executives, and researchers have viewed efficiency (low cost) and resilience (high flexibility and agility) as mutually exclusive. This perspective shaped the design of supply chains, with managers often prioritising short-term profits over long-term resilience and adaptability. As a result, numerous supply chains were primarily engineered to cut costs.
The disruptions and challenges thrown up in recent years have forced a re-evaluation of this approach. Bruce Herbert argues that resilience is a "two-way story – it's not just about overcoming interruptions, disasters or big spikes in demand. It’s also about building cost flexibility, so that if things do turn down, you're not caught with a whole bunch of fixed costs."
Bruce Herbert emphasised the importance of scalability in both directions.
"Building in cost flexibility allows you to either manage high volume without exploding your costs, or when the volume goes down, reduce your cost proportionally to protect your margins."
Visibility tools and data analytics help to reveal
safe cost-cutting opportunities involving sourcing, inventory, or capacity. Real-time information on potential bottlenecks reduces the risk involved in otherwise difficult decisions like adding suppliers, increasing safety stock, or ramping up capacity. In an era where consumer expectations are sky-high, visibility is paramount.
"In peak season, the consumer becomes more demanding. They want on-time arrival, accurate stock levels, and flexible fulfillment options like click and collect," Raghav Sibal says.
"Within the four walls of fulfillment, there needs to be more planning from a workforce and labour standpoint, building contingency plans to become more resilient."
These factors are coming into play for leaders who have to balance high customer service expectations with staying ahead of demand.”
Automation plays a big part in this pursuit for both efficiency and resiliency. Glenn Barnes particularly highlights the benefits of goods-toperson (GTP) systems, which "enable greater flexibility and adaptability to change order profiles, such as shifts in the balance between store and online orders and provide extra capacity in a compact footprint."
"Automation drives efficiencies through optimised storage, picking, dispatch as well as process enhancements. In reducing the reliance on labour, automation makes supply chains more resilient to labour challenges,” he says.
Workforce Management in High-Stress Periods
The peak season inevitably brings increased stress for supply chain workers at all levels. In a national labour shortage, retaining staff is becoming more crucial for organisations, who can’t afford a slowdown in efficiency due to a lack of staff. Leaked documents in

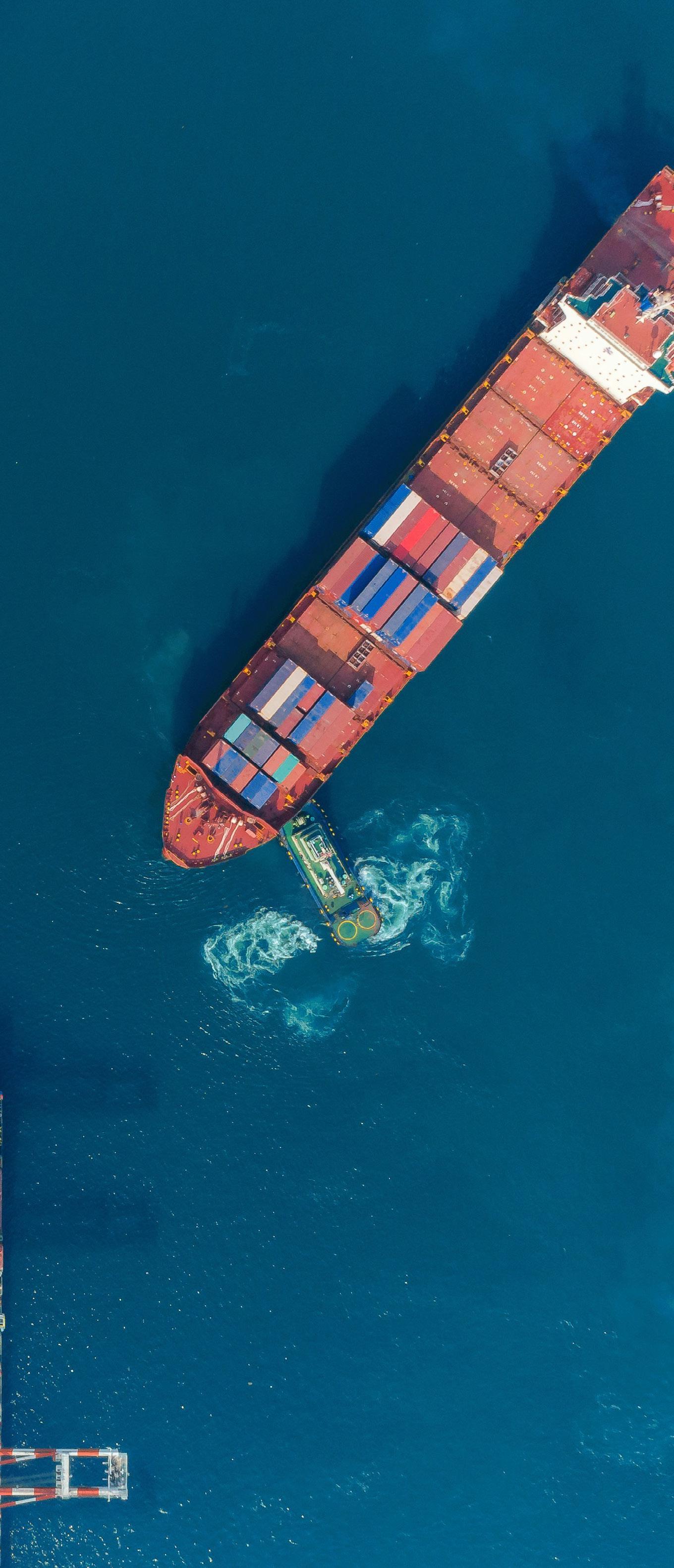
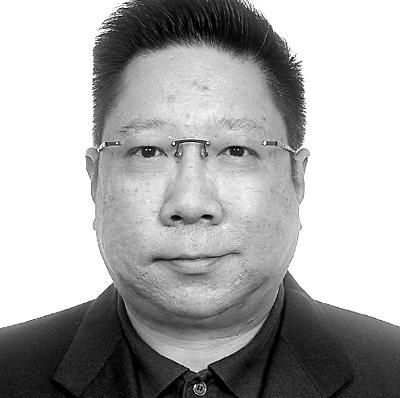
“Today's retail environment changes so rapidly that even data from two years ago might be irrelevant, so that historical data isn’t as useful as it once was”
ROYSTON PHUA, VERTICAL STRATEGY LEADER APAC SUPPLY CHAIN AT ZEBRA TECHNOLOGIES
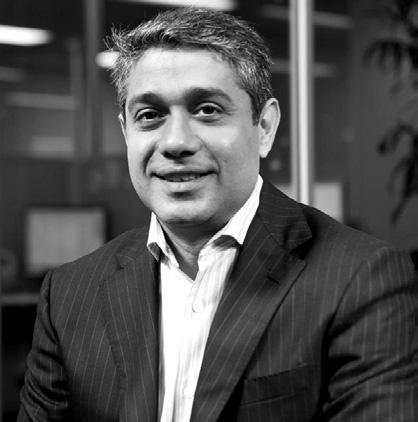
“Technology solutions that monitor performance and prompt breaks when needed will grow in popularity.”
RAGHAV SIBAL, MANAGING DIRECTOR ANZ AT MANHATTAN ASSOCIATES
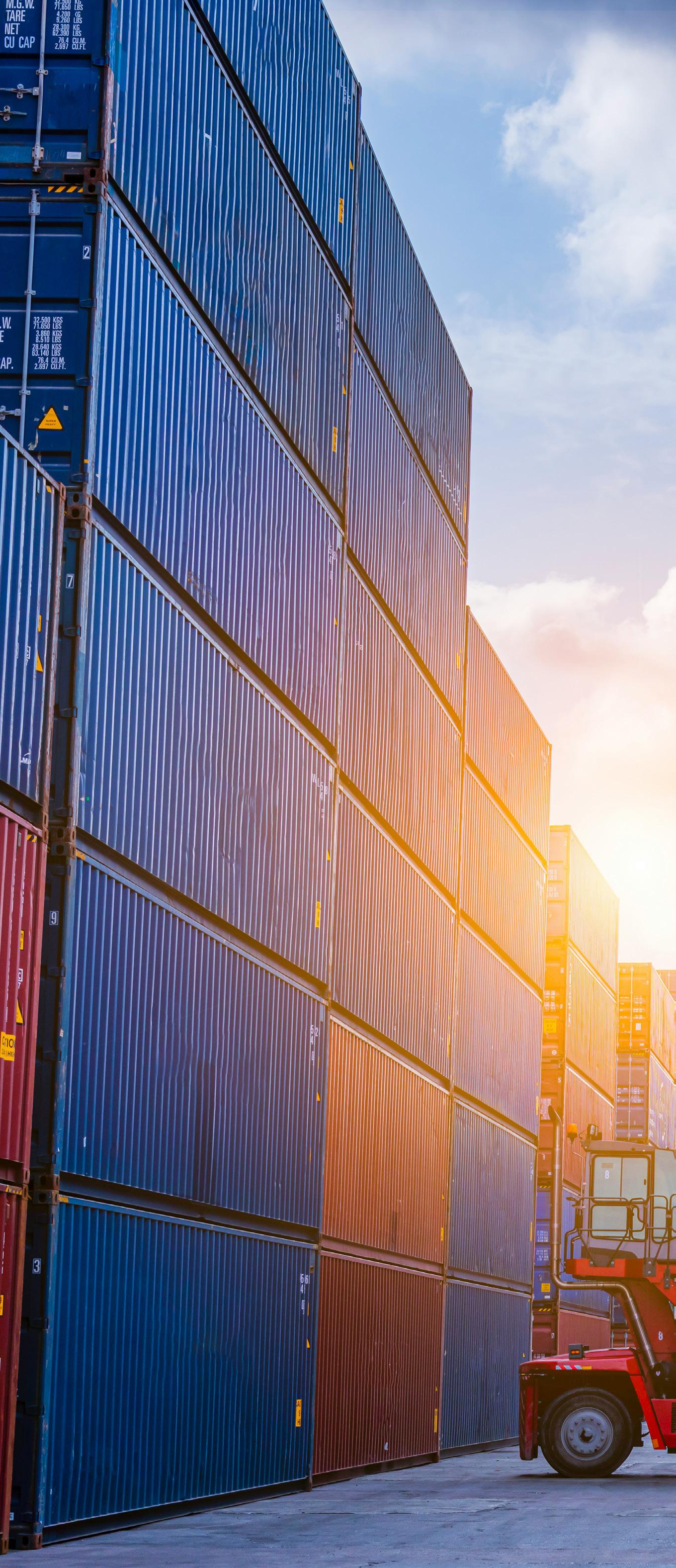

2022 revealed Amazon has an annual employee turnover rate of 150% –double the industry average – costing the company and its shareholders $8 billion annually.
In 2024, Ikea Australia has moved to close the gender pay gap, revising super payments on unpaid parental leave and offering retail store workers to be on a fixed roster – all in a bid to retain its employees. Bloomberg reported Ikea’s workers were previously quitting in large numbers in the US, while in the UK and Ireland, half of all new hires were leaving before their first anniversary.
By 2022, more than 62,000 employees were departing each year. Globally, each departure cost Ikea AUD $7,521 to replace.
Raghav Sibal suggests innovative approaches to manage and motivate staff, where technology works to better staff wellbeing.
"Technology solutions that monitor performance and prompt breaks when needed will grow in popularity. For example, the system might notify a worker who's been maintaining high productivity for several hours and provide an unscheduled break,” he says. "Some of our customers have introduced creative incentives for high performance, such as top performers earning a prime parking spot next to the Managing Director for a month. It's a simple but effective way to recognise and reward exceptional work."
Dematic’s Glenn Barnes points out that automation can also contribute to a less physically and mentally demanding work environment.
"Automation provides for a less stressful working environment, as operators work in ergonomically and safety-optimised stations at consistent, comfortable speeds. Warehouse workers aren’t reliant on others for maintaining high performance and accuracy is assured, which alleviates stress levels as volumes increase.”
On top of this, automation can help address the issue of labour availability, which is particularly challenging during peak periods.
Automation reduces dependence on casual labour pools, which is especially relevant in Australia, where labour is becoming increasingly scarce, particularly in regional areas.
Technology is fundamental to challenge perceptions of warehouses being dull and dirty environments and tackle
labour shortages. However, people remain at the heart of the issue.
Bruce Herbert emphasises the importance of leadership during these high-stress peak periods.
"Good leaders have always prepared their teams for peak seasons by being realistic and honest about the challenges ahead,” he says, “They encourage their staff to take holidays and rest beforehand, treating the busy period like athletes preparing for a major event –you don't perform at that intense level all year round. If overwork creeps in the best leaders don’t turn a blind eye to it and check in with their staff.”
Royston Phua suggests that four key supply chain principles need to be in place to deal well with stressful periods.
"It sounds cliché, but the key to managing peak season stress starts with a clear vision and mission. Retailers need to define what they aspire to achieve for their customers and for themselves. From there, they should examine their supply chains, focusing on four basic tenets: people, processes, systems, and automation – in that order. Many companies make the mistake of jumping straight to technology or automation without considering their people and processes first. This can lead to costly investments in technology that don't align with their workflows. By getting the fundamentals right and leveraging appropriate technology, retailers can better manage the stress of peak seasons."
The Key to Peak Season Success
Royston advises retailers, regardless of size, to prioritise digitisation and modernisation.
"If you’re a small to mediumsized business, you don't need to invent everything yourself, you can subscribe to platforms that digitise your supply chain,” he says.
"Retailers should explore partnerships with larger players for crowdsourcing arrangements, especially in areas like transport and inventory management. There are numerous SaaS programs available in
Australia and New Zealand that can optimise these processes – the goal should be to start digitising your supply chain with a medium-term view of two to three years."
While investing in automation now will not address the challenges of this coming peak season, retailers looking to invest will be ready for next year's peak seasons, according to Glen Barnes.
"When implementing automation, it's crucial to have a deep understanding of your businessand ensure your supplier does too. This includes your warehousing operations, data, supply chain requirements, business strategy, and growth plans to avoid overcapitalisation on automation. Design a system that includes manual overflow capabilities and room for future expansion, so your investment remains justifiable and adaptable," he says.
Bruce Herbert says it's challenging to provide generic advice about peak seasons because each retailer is unique. Rather than focusing on specific events from the previous year, retailers should be ready to expect the unexpected.
While it's impossible to plan for every potential situation, organisations need to develop a flexible approach that can adapt to various challenges, rather than assuming that history will repeat itself.
“Resilience during peak season isn't just about physical capacity to handle products; it's also about financial management. Effective automation should be sized for peak capacity or close to it, rather than based on average volumes to avoid having systems that are too large during off-seasons and inadequate during peak times,” Bruce says.
As retailers and supply chain professionals in Australia prepare for the upcoming peak season, success will depend on a combination of accurate forecasting, strategic use of technology and efficient workforce management. Those who can balance these necessities will be in the best position not only this year, but for many Christmases to come. ●
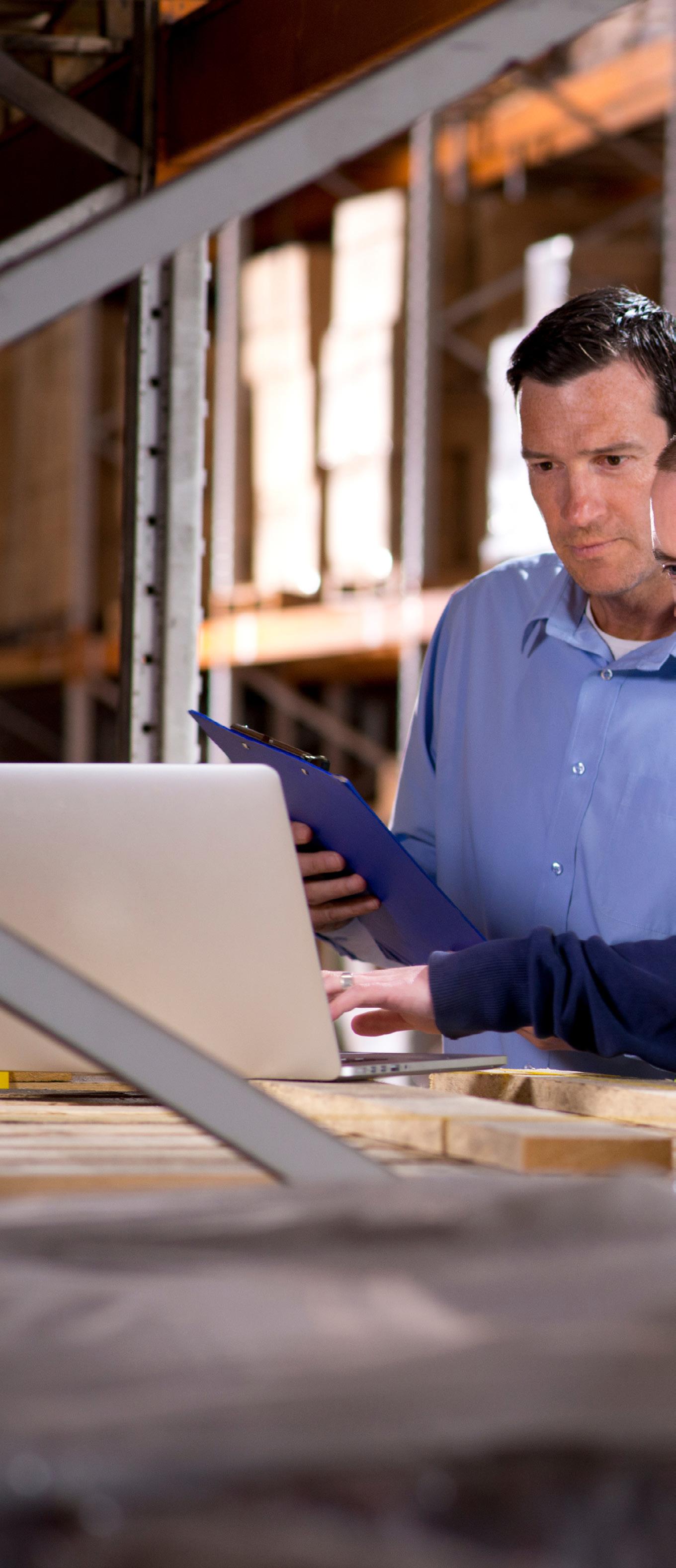
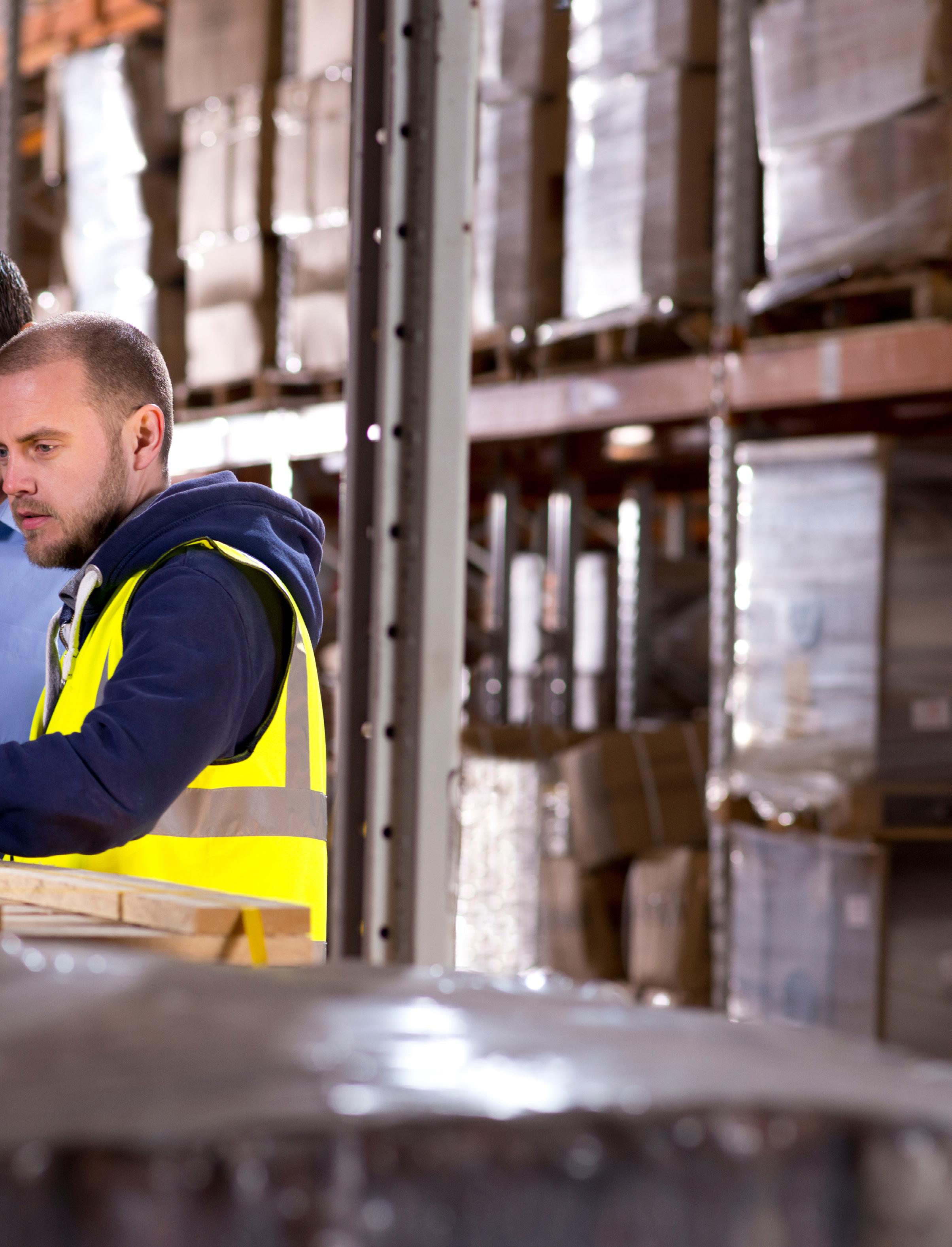
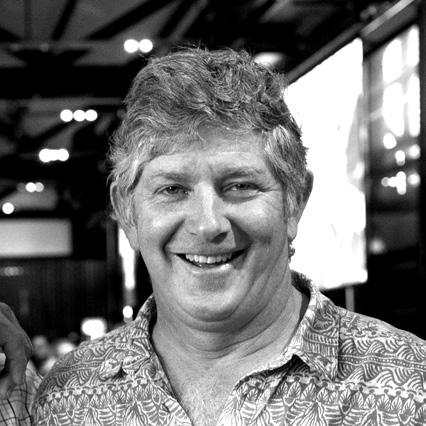
“Design a system that includes manual overflow capabilities and room for future expansion, so your investment remains justifiable and adaptable”
GLENN BARNES, INDUSTRY MANAGER GROCERY & GENERAL MERCHANDISE AT DEMATIC
The most versatile rugged Android and Windows business tablets
Two di erent operating systems with unique class-leading features.
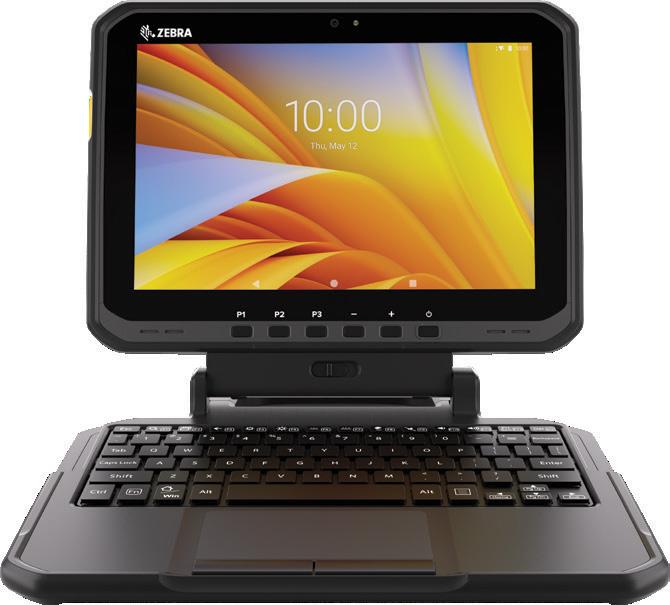
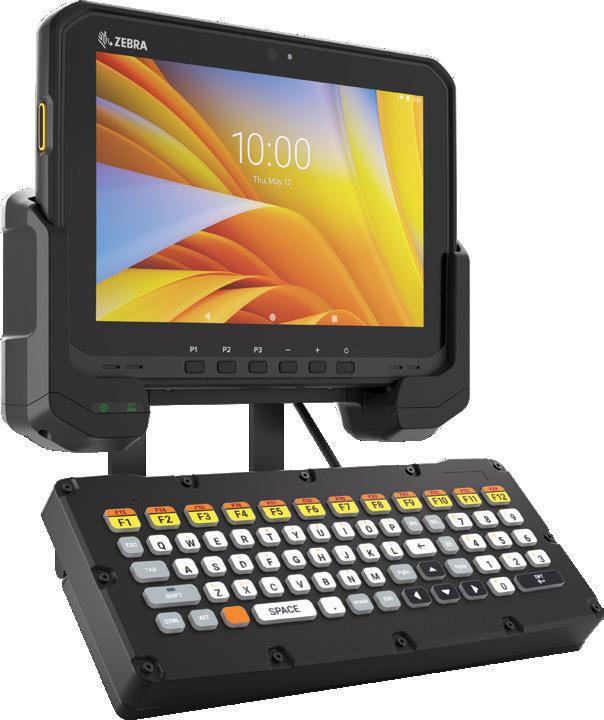
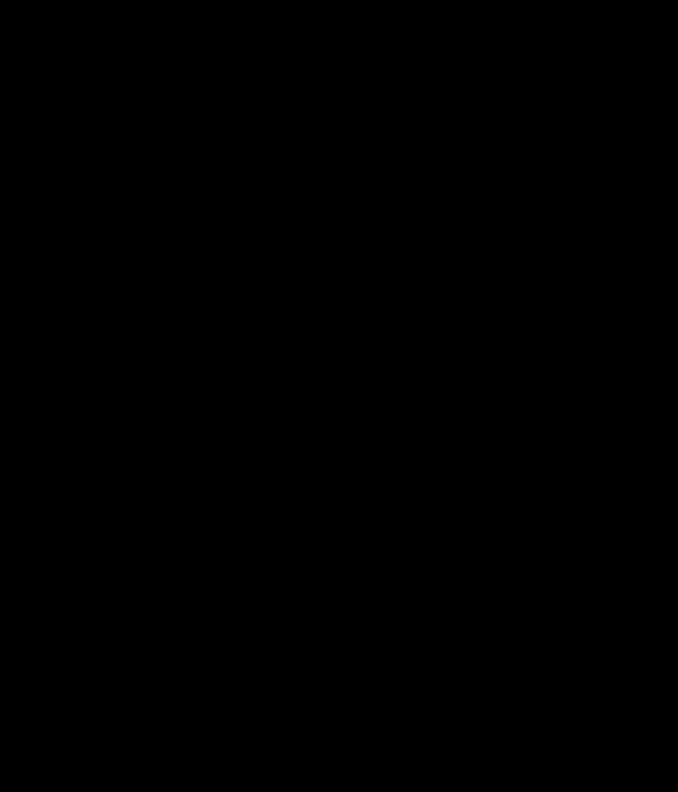

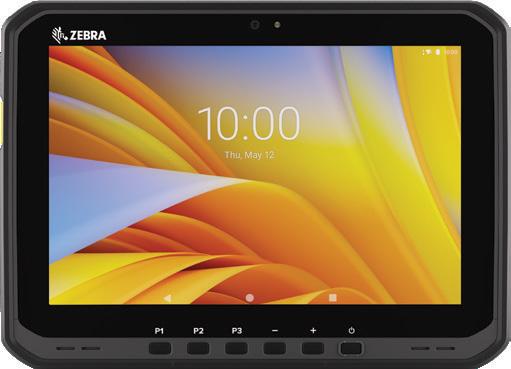
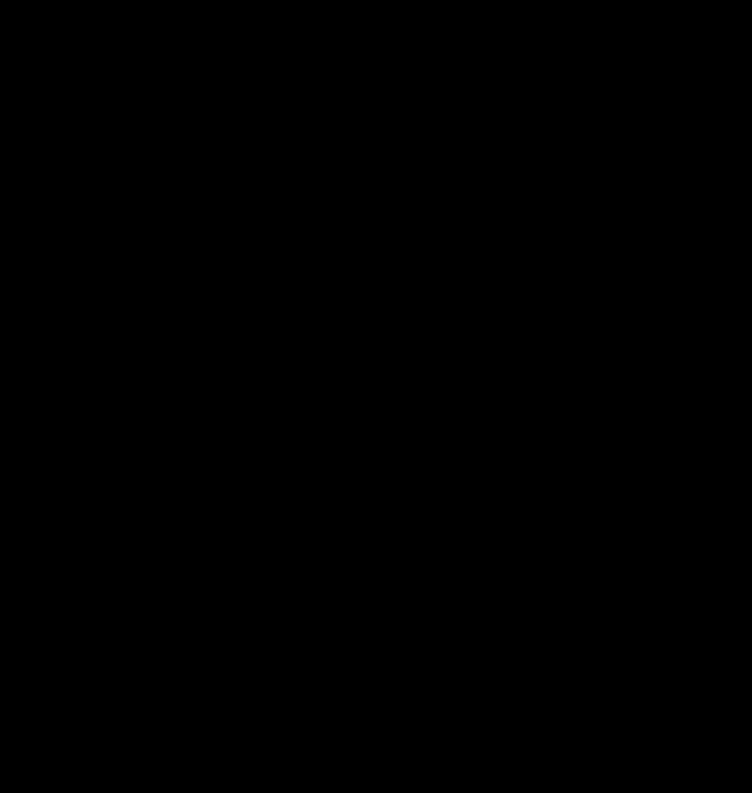
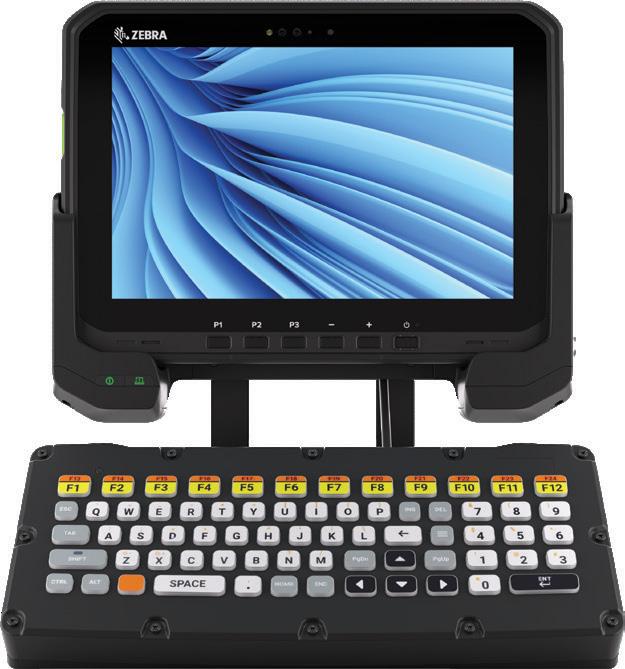
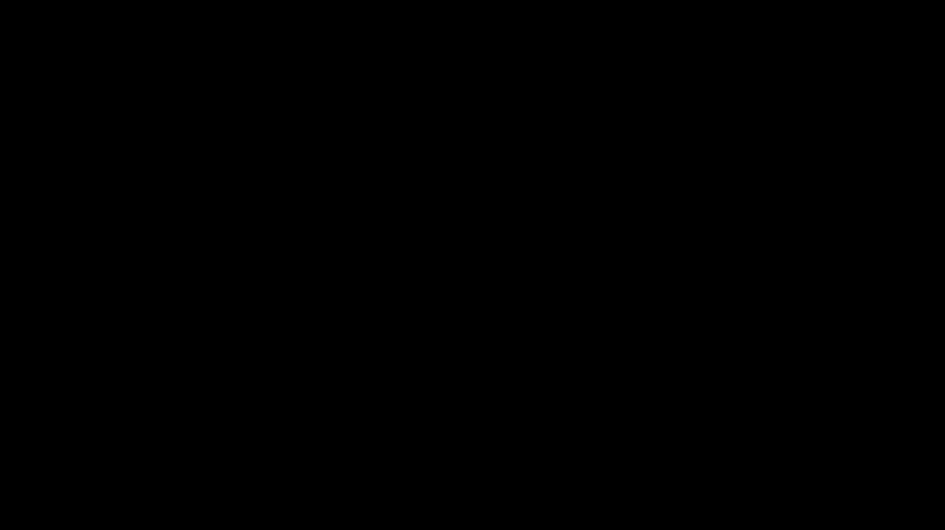
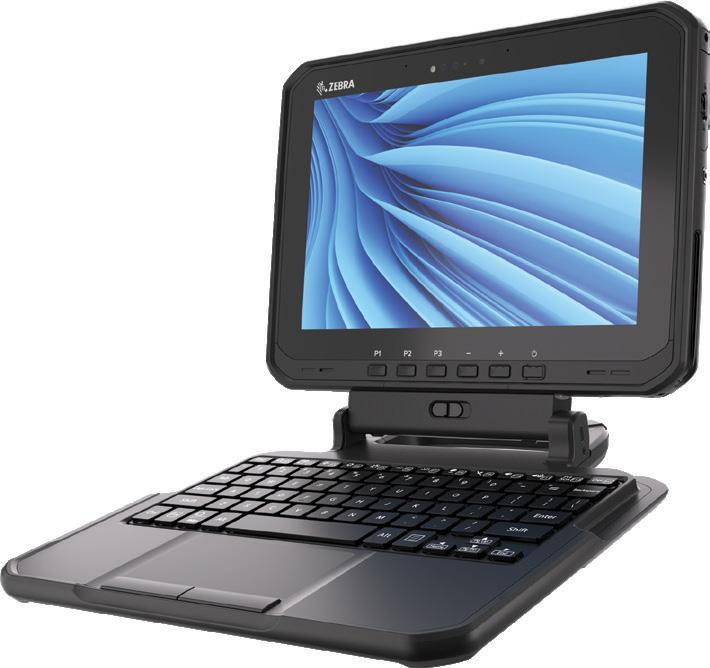
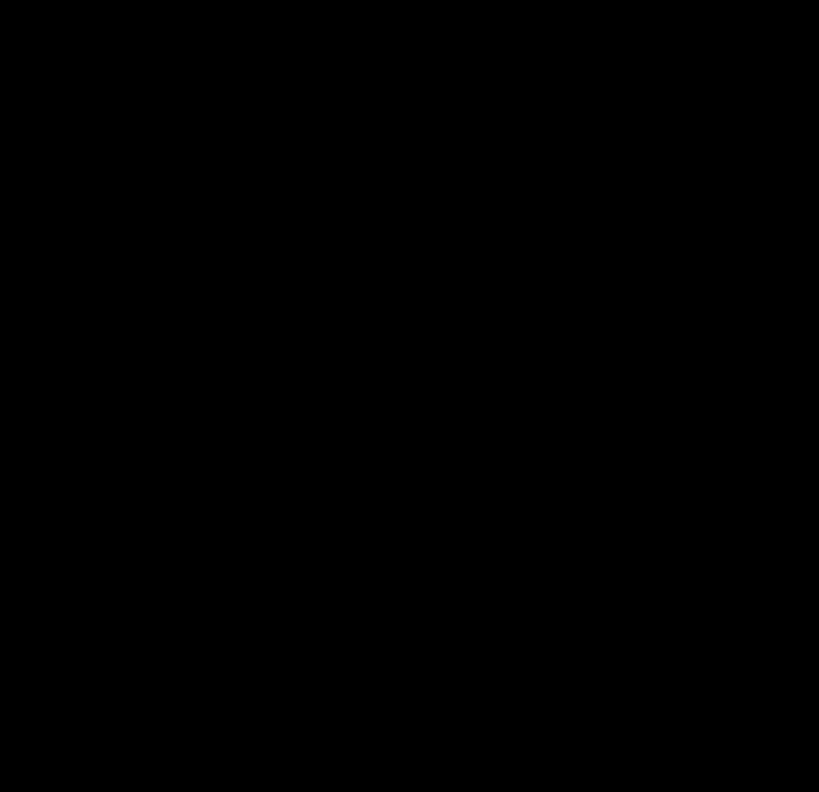

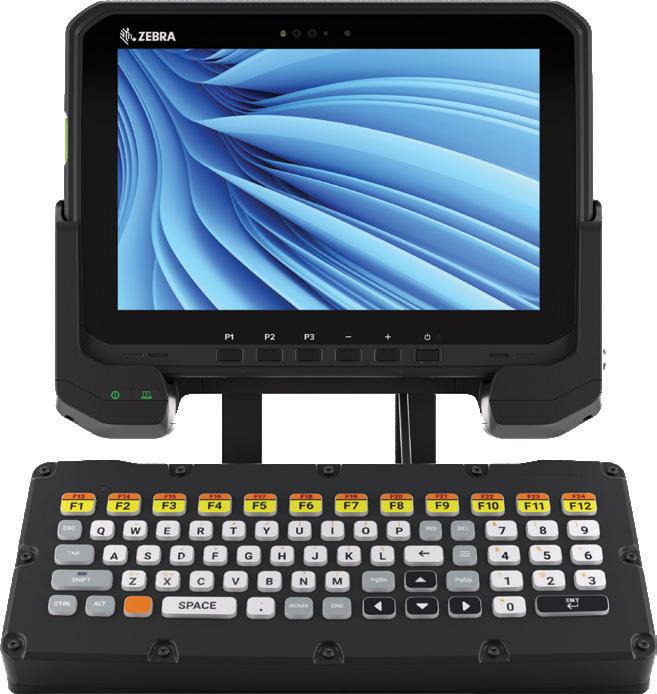
Survives constant pounding / water exposure
Easy viewing in any environment
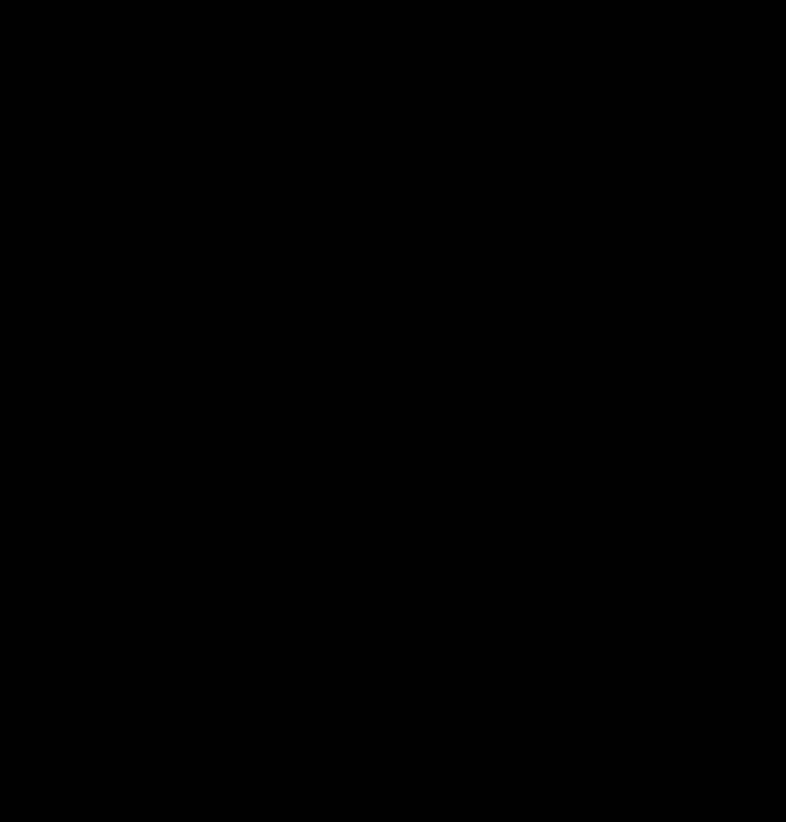
Latest wireless / 5G connectivity
AI-enabled touchscreen and audio (Windows only)
Optional no battery configurations
Supports your legacy operations
Ready for the freezer (Android only)
Iconic Australian Athletic Brand 2XU Partners with Pattern for International Repositioning
Leading global ecommerce and marketplace accelerator, Pattern, today announced it has supported iconic Australian athletic wear brand 2XU to pivot its international business, solidifying its position as a leading specialist technical athletic brand in key markets, including North America. This strategic partnership has enabled 2XU to achieve an 80% full-price sales rate and increase its average selling price by 25% to $200.
With pre-existing operations in North America through wholesale, D2C, and Amazon channels, 2XU identified the need to reimagine its sales strategy to regain control of its brand and product positioning.
The shift was motivated by recognising that the brand’s complex distribution model and the practice of uploading a wide range of seasonal end-of-life products to Amazon had diluted the brand’s premium image.
Marc Boelen, CEO at 2XU, explained, “The international sportswear market is very crowded and highly competitive. As a premium technical brand, we needed to take control and differentiate ourselves. This meant simplifying our distribution to focus on our unique selling point (USP) as a technical compression and triathlon brand, which 2XU is well known for and consumers are willing to pay a premium for. Our data further supported this, showing that content from 2XU’s athletes and ambassadors focused on the technical benefits of our range outperformed other products and content in the US.”
Previously, 2XU’s distribution model into markets like North America included
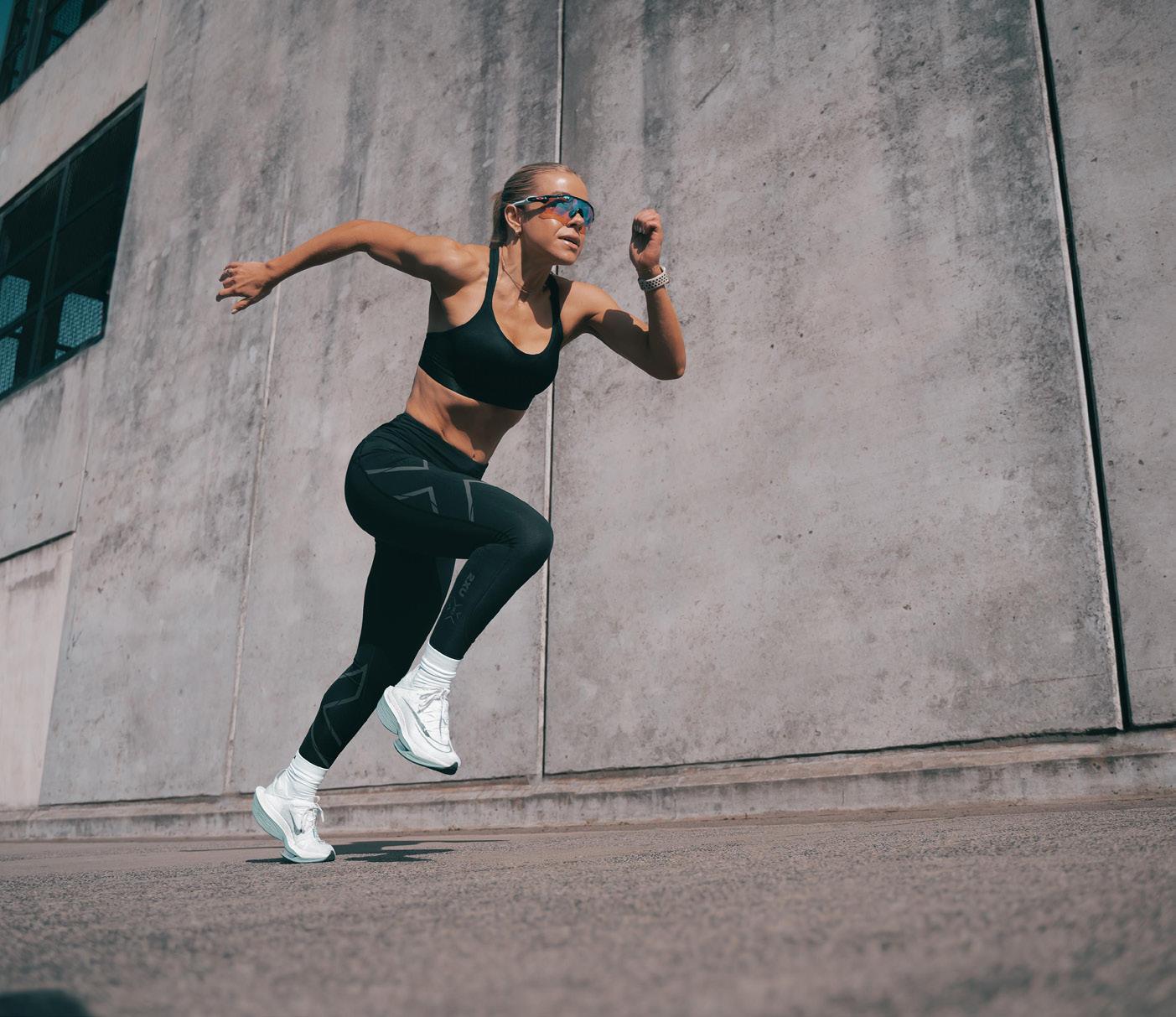
multiple channels, creating inconsistencies in pricing and brand perception. The strategy of uploading a wide range of endof-life products exclusively to Amazon was intended to reduce channel conflicts and maintain stock keeping unit (SKU) continuity. However, this strategy negatively impacted 2XU’s brand perception
The decision to overhaul 2XU’s Amazon strategy was driven by the fact that in 2024, over half (56%) of US consumers start their product search on Amazon, rather than other search platforms like Google. This meant that for many US consumers, their first encounter with 2XU would be through Amazon, making this channel crucial in shaping their perceptions of the brand.
“Moving from a multi-channel distribution model to a direct-to-consumer (DTC) model is
a major strategic change. As a brand, we saw a critical need to build out our international DTC business, even if it meant accepting a short-term impact on sales, to achieve longterm control over pricing and positioning,” said Lindsay Swaik, VP of Digital, 2XU. “Given Amazon’s dominance among US consumers, we felt it was necessary to showcase leading content and a smaller range of our bestselling premium products on Amazon as a first brand impression. This was crucial in enhancing our brand story and positioning us as the leading technical performance brand and the world leader in compression.”
How Seamless Shopping Journeys Are Reviving Physical Retail Stores
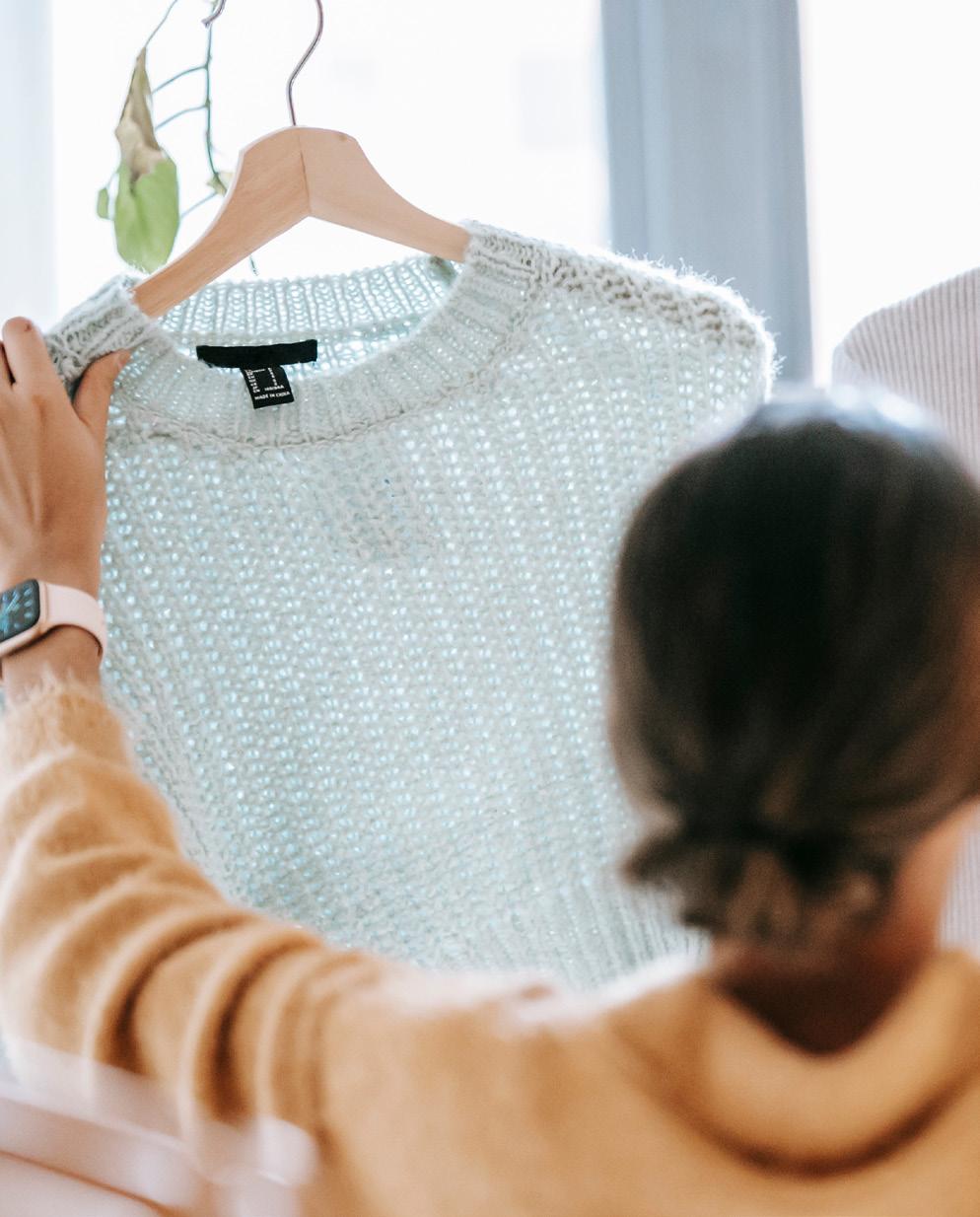
With ecommerce projected to capture 41% of global retail sales by 2027, it might seem counterintuitive for retailers to continue investing in new and existing physical stores.
Yet, retailers like Fujifilm, Sketchers, and North Face are not only maintaining their brick-andmortar presence but actively innovating with new store concepts to better serve modern shoppers and stand out in a competitive market.
Rather than signalling the decline of physical stores, the rise of ecommerce is actually fuelling the revival of retail spaces, where fresh, exciting store concepts are drawing in consumers. This trend highlights the evolving behaviours and preferences of today’s shoppers. Retailers recognise that modern consumers engage with multiple sales channels during their buying journey, and in fact, 73% of shoppers prefer to combine online and in-store experiences.
This omnichannel approach underscores the enduring importance of physical stores in a digitally driven retail landscape.
Flexible Payments
In today's omnichannel digital age, offering flexible payment solutions is essential. According to Manhattan’s Unified Commerce Benchmark Singapore, 31% of ecommerce consumers will not retry if they must re-enter their payment details at checkout. Modern shoppers expect to pay using their preferred method, whether it's a credit card, digital wallet, contactless payment, cash, or pay-by-link— regardless of the shopping channel they choose.
By providing a range of payment options, physical stores can better meet the flexibility and convenience expectations of modern shoppers. Offering popular alternative payment methods not only increases the likelihood of attracting new customers but also encourages repeat visits from those who find their preferred payment options available. Satisfying these preferences is key to fostering customer loyalty.
Omnichannel Promotions
Retailers plan and execute promotions to boost sales, attract new customers, and enhance brand
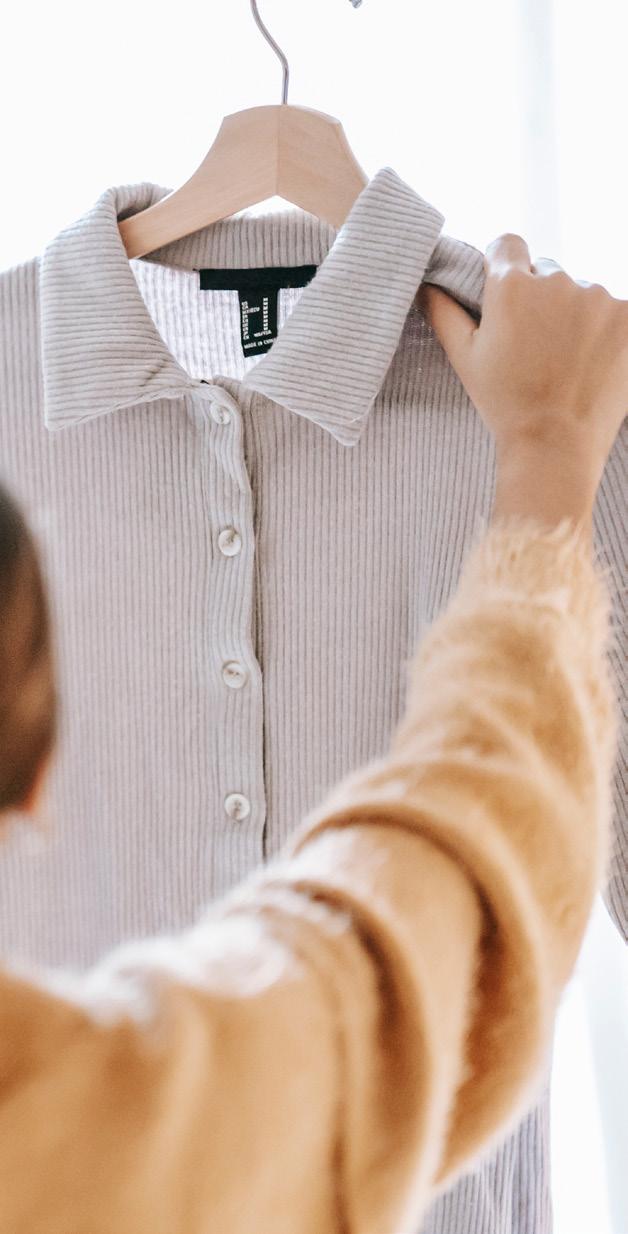
awareness. However, without the right technology in place, promotions can negatively impact already narrow margins. It’s essential for retailers to focus on promotional effectiveness, ensuring these initiatives deliver the desired financial results and customer satisfaction.
Seamless integration across all sales channels is critical, as promotions should be defined once and shared consistently with unified targeting, qualification, and calculation logic. If a customer is eligible for a promotion online, that same offer should be available in stores and at the contact centre, unless it is an exclusive online deal. Yet, executing promotions consistently in-store remains a significant challenge due to the fast-paced environment.
An omnichannel promotions engine can address this challenge by providing a single source of truth for promotion logic, ensuring consistency across all sales channels. Effective omnichannel promotions are well-planned, targeted to the right customers, and executed consistently, playing a crucial role in the modern retail brand experience.
Clienteling
Modern shoppers highly value personalised shopping experiences, especially in retail segments like highend luxury goods, where personalisation is expected. According to McKinsey, companies that excel in personalisation can potentially generate 40% more revenue, highlighting its significant impact.
For brick-and-mortar retailers, personalised one-on-one shopping experiences provide a unique advantage over digital-only competitors. By incorporating clienteling capabilities, such as Mobile Clienteling, stores can seamlessly connect all sales and service functions, empowering store associates with rich customer data to enhance interactions throughout the store.
Virtual clienteling is also emerging as a powerful tool, allowing store associates to maintain customer engagement beyond the store. Whether it's responding to product inquiries via phone, text, or email, or providing additional information to assist with purchase decisions, virtual clienteling extends the personalised shopping experience beyond the store’s physical boundaries.
In 2024, the key to effective clienteling lies in enabling store associates to quickly access and utilise customer purchase history, engagement history, and preferences. This allows for personalised interactions and tailored recommendations that resonate with customers, whether in-store or through virtual channels.
Store Order Fulfilment
Modern shoppers appreciate the convenience, immediacy, and cost savings of buying online and picking up in-store (BOPIS), driving increased demand for this fulfilment service. Simultaneously, retailers are increasingly leveraging their stores to ship orders, reducing shipping costs and speeding up delivery times.
To meet customer expectations while maintaining
profitability, modern stores must excel in fulfilment efficiency, scalability, and accuracy. BOPIS not only caters to shoppers’ desire for convenience but also drives additional foot traffic and sales in stores.
According to a survey by the International Council of Shopping Centres, 67% of BOPIS users buy additional items when picking up their orders.
Physical stores have evolved into multifunctional hubs within the omnichannel retail ecosystem, offering retailers a strategic way to meet growing shopper demands for speed and convenience. When optimised to handle increasing volumes and rising customer expectations, store fulfilment can significantly boost sales and enhance customer satisfaction.
Unified Returns and Exchanges
In 2022, returns cost retailers a staggering $817 billion, with 78% of shoppers finding the returns and exchanges process inconvenient, and 41% considering it time-consuming.
Beyond the financial impact, returns significantly contribute to CO2 emissions and landfill waste. A March 2023 report by the British Fashion Council’s Institute of Positive Fashion, Solving Fashion’s Product Returns, revealed that in the UK, 3% of returned items are not resold—50% of which end up in landfills, 25% are incinerated, and only 25% are recycled, underscoring the environmental toll. Unified returns and exchanges enable modern shoppers to return or exchange any item at a store, regardless of the original sales channel, including online purchases. This approach offers customers the convenience of a straightforward return or exchange process, with the immediate satisfaction of an instant refund or a new item.
By implementing unified returns and exchanges, retailers not only meet the needs of today’s shoppers in this crucial area of customer service but also reduce both business and environmental costs by minimising the need to ship returns. ●
For more information: https://www.manh.com/en-sg
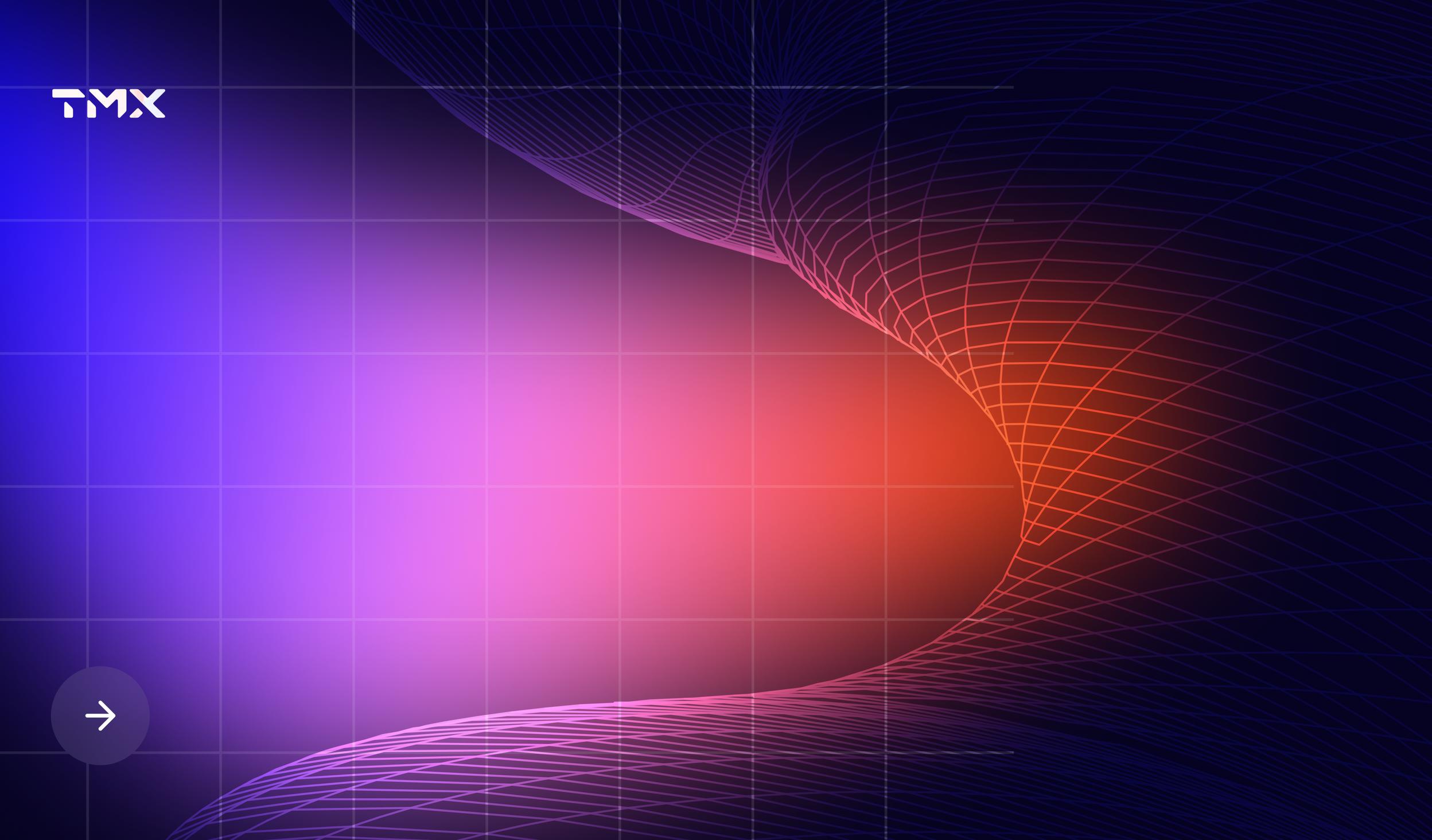
Building Supply Chain Resiliency Through Warehouse Modernisation
Warehouse leaders are under constant pressure to do more in less time without compromising on accuracy.
By increasing data visibility and analytics, warehouse operators can dynamically respond to challenges or peaks in demand while optimising productivity. Zebra Technologies commissioned a global research study among decision-makers and associates to analyse the latest trends and technologies transforming warehouse operations.
Overall, 73% of decision-makers will accelerate the timelines of their warehouse modernisation projects this year. Their top three priority areas for modernisation include labour optimisation, streamlining processes, and moving to cloud-based systems.
In terms of technology investment, 91% of decision-makers will invest in visibility across the supply chain and supplier management, while 89% will invest in digital twin technology and 87% will invest in robotics.
Putting Supply Chains to the Test
Global disruption has exposed the vulnerabilities of traditional supply chain operations and forced businesses of all sizes to embrace change and enhance resiliency. Despite the push for innovation, it’s hard to keep up with the speed of transformation. The world continues to move online, accelerating shifts in consumer demand and putting more demands on global distribution networks.
As e-commerce grows, so too does the demand for inventory traceability and reverse logistics. These changes put even more pressure on warehousing operations to move from siloed and reactionary to more predictive and adaptive. 77% of warehouse decision-makers and associates agree that out-of-stocks and inventory inaccuracy challenge productivity.
Forward-thinking enterprises are investing in solutions that enable real-time
visibility and traceability in warehouses, such as RFID, 3D sensors and machine vision, which have revolutionised the way warehouses capture data.
However, warehouse operations also need advanced analytics to make the most of all this data gathered across the supply chain. 71% of decision-makers are investing in software and automating analytics and decision-making, which can help them gain instant insights into inventory levels, demand patterns and operational performance, empowering swift decision-making and enabling agile responses to unforeseen disruptions.
Warehousing Modernisation in Action
As a warehouse reaches higher maturity levels, integrating inventory visibility with other supply chain processes becomes a cornerstone of success, enabling seamless coordination and collaboration with suppliers, distributors and customers. Customer expectations for real-time updates and transparent delivery experiences make visibility indispensable for meeting evolving demands.
Warehouse decision-makers are increasingly turning to sensor technology to
meet these demands. By the end of 2024, most plan to deploy RFID tags and sensors with strong growth expected for RFID printers and encoders. Over the next five years, however, the highest growth is seen in 3D sensors, active RFID tags, computer vision, fixed RFID readers, machine vision and fixed industrial scanning.
Transforming Tomorrow’s Supply Chain
Warehouse visibility remains an essential component for a thriving supply chain ecosystem. The demand for efficiency and cost reduction in today’s competitive landscape is motivating warehouse leaders to optimise their operations, identify bottlenecks and streamline processes. As warehouse technology and automation continue to evolve and standards of operational excellence also rise, businesses will lean on solutions that enable them to track the real-time location of all assets and inventory through each step of the supply chain. ●
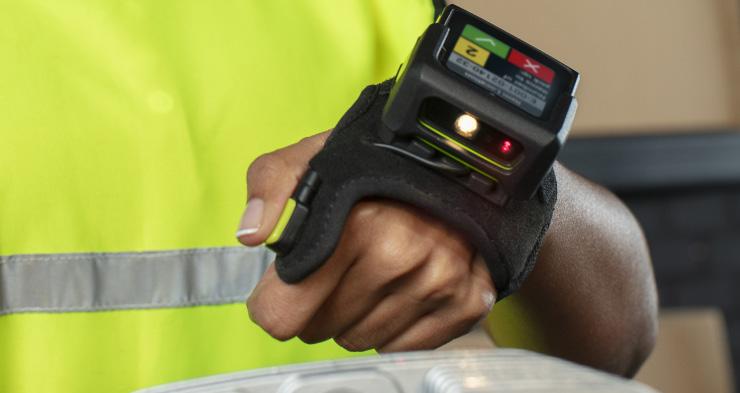
To read Zebra’s Warehousing Vision Study, click here.
Bridging the Data Gap: How Inaccessible Information is Impacting Australia's Supply Chains
WRITTEN BY GORDON MADDOCK, REGIONAL VICE PRESIDENT, BROAD MARKETS
Australian supply chains are facing significant disruptions due to widespread data accessibility issues. According to new research from Appian, 66% of supply chain employees report struggling with incomplete or inaccessible data, impacting their ability to operate efficiently and meet demands.
The study, which surveyed 300 supply chain workers across the shipping, distribution, and transportation sectors, highlights persistent data-related obstacles despite ongoing digital advancements in the industry. The lack of unified data significantly affects inbound visibility, creating challenges in predicting what, when, and how much inventory will arrive at distribution centres or factories.
The research found that for approximately 41% of supply chain professionals, maintaining operational efficiency is compromised by poor data accessibility. Similarly, 31% of the workforce expressed difficulties completing essential inventory management tasks. This uncertainty around the availability of parts and
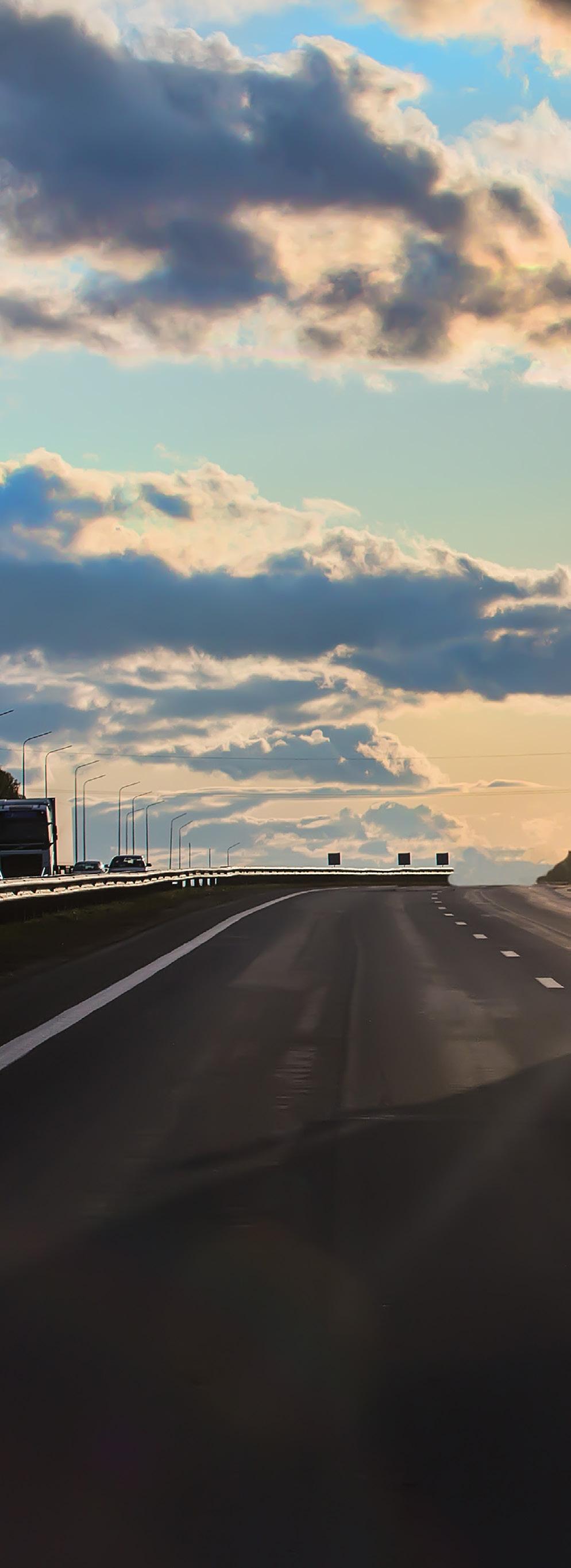
APPIAN APAC
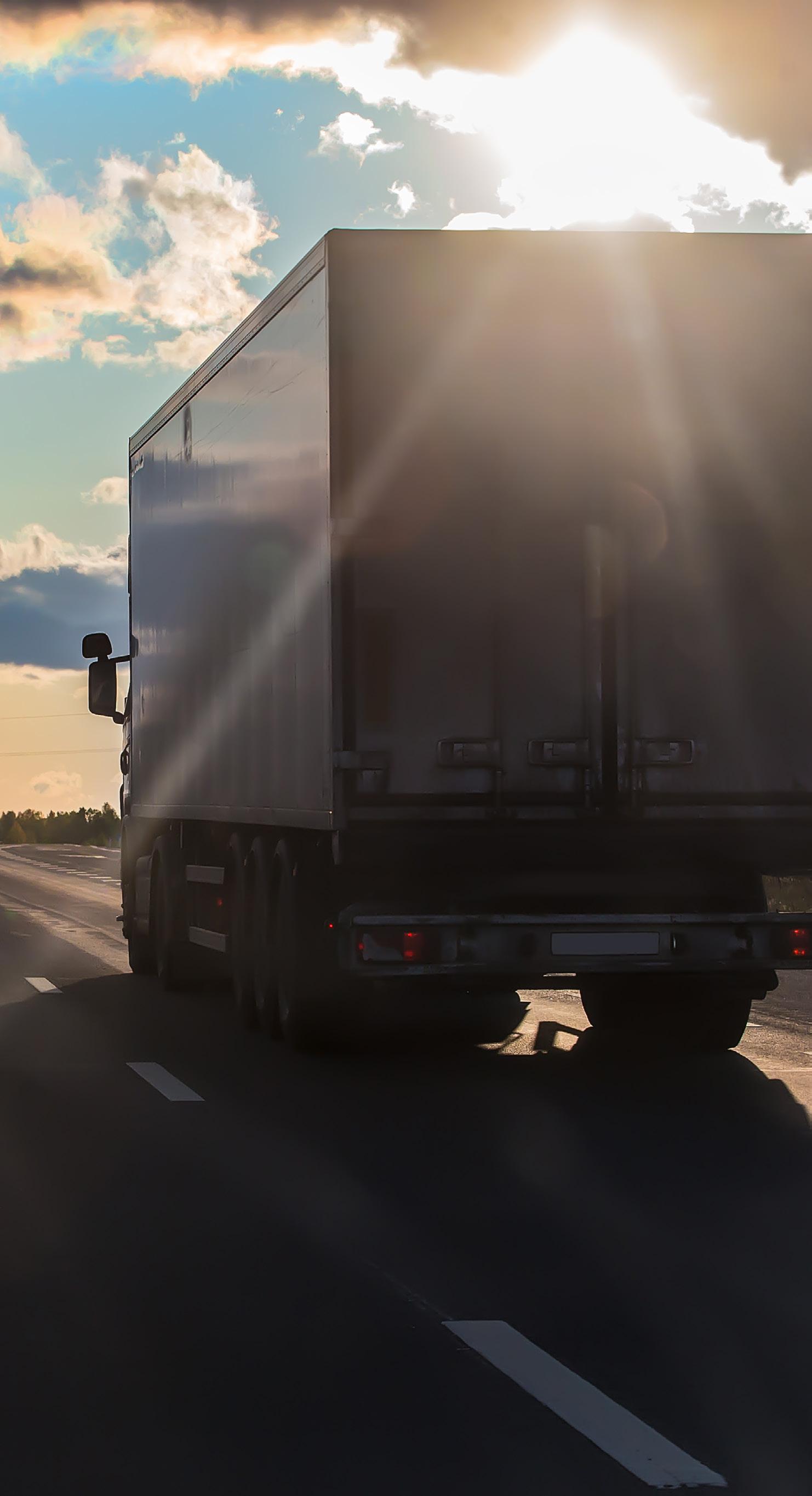
materials hinders future operational capabilities, impacting production planning and decisions on adjusting output levels.
Australian supply chains rely on digital processes and accurate data to function. Yet, research shows that they are asking their workers to operate with incomplete or inadequate information to manage complex, and often disconnected operations across critical areas such as logistics management, shipment tracking, and schedule coordination.
Fragmented, inconsistent or unavailable data creates a lack of real-time visibility. This impacts key functions within the supply chain including inbound visibility, which can have knock-on effects on efficient staffing and warehouse operations.
The Need for Enhanced Data Access and Visibility in the Supply Chain
For stronger business outcomes, supply chain organisations need greater data access and visibility. Many organisations still rely on manual processes and spreadsheet tracking, limiting enterprise-wide visibility across their operations and high priority assets including equipment, machinery, vehicles and infrastructure.
Automating track-and-trace operations in supply chains can also provide new levels of insight for smarter business decisions, as it allows businesses to collect and analyse real-time data at every step of the supply chain. By implementing digital solutions like IoT sensors, RFID tags, and advanced analytics platforms, companies can gain granular visibility into the movement of goods, inventory levels, and potential bottlenecks.
This enhanced transparency enables quicker responses to disruptions, optimises resource allocation, and reduces operational inefficiencies. Moreover, integrating machine learning and AI into these digital systems can more accurately forecast demand, assess supplier reliability, and predict potential risks before they materialise, driving more informed, proactive decisionmaking. In Australia, where supply chains are vast and often challenged by distance and remote delivery locations, digitisation can be the key to maintaining resilience and ensuring long-term sustainability. The ability to track goods across remote regions in realtime offers businesses a critical competitive advantage, streamlining processes and fostering stronger partnerships throughout the supply chain.


The Risk of Inaccessible Data
While major digital transformation projects are ongoing in the Australian supply chain sector with 78% of respondents noting their organisations had adopted new digital initiatives within the last five years, data usability has not kept pace.
Currently, 43% of workers identify data accessibility as their biggest challenge. A significant portion also highlighted data overload—having abundant data but lacking effective tools to analyse and utilise it—as a major issue.
When information is inaccessible or unable to be analysed accurately, it complicates decision-making processes and heightens the risk of operational errors and ongoing inefficiencies across supply chain operations.
To address these challenges, organisations should consider the strategic implementation of a modern process automation platform enhanced by a data fabric. A data fabric is an architectural layer and toolkit that seamlessly integrates data across disparate systems, whether on-premises or in the cloud. By creating a centralised, unified view, it substantially enhances operational efficiency.
Data Challenges Impact Customer and Employee Experiences
Appian research also highlighted the impact of poor data accessibility on the overall customer and employee experience. It found that approximately 39% of workers encountered obstacles in meeting customer service expectations directly due to complications arising from inadequate data access.
Compounding the issue, 33% of those surveyed reported that such data-related challenges adversely affect the employee experience.
This dissatisfaction is particularly problematic for Australian supply chain organisations facing skilled worker shortages, where maintaining a satisfied and efficient workforce is crucial to prevent increased turnover, knowledge loss and to ensure workforce stability.
Lacking unified and visible data needed to forecast productivity fluctuations renders proactive staffing decisions impossible. This leads to inefficient labour management, with employers struggling to optimise both, casual and full-time labour. Consequently, this impacts the overall experience of staff and the service output for their customers.
AI: Low Adoption, High Potential
Despite the growing adoption of digital transformation strategies, the integration of Artificial Intelligence (AI) in supply chain operations remains low, with only 3.67% of workers regularly using AI-powered systems.
This slow uptake highlights significant opportunities to enhance supply chain efficiency and responsiveness through advanced technologies. AI has the potential to transform supply chain management by automating repetitive tasks, improving demand forecasting, optimising inventory management, and enhancing decision-making across the entire supply chain.
Low AI adoption rates can be attributed to several factors, including the complexity of integrating AI into legacy systems, a lack of digital skills within the workforce, and concerns over the upfront implementation costs. However, as the benefits of AI become more apparent, especially in areas like predictive analytics and real-time optimisation, the case for adoption grows stronger. AI can sift through massive amounts of data to identify patterns and trends, enabling businesses to anticipate disruptions, streamline logistics, and improve overall operational agility.
Embracing AI, alongside sophisticated data management tools, can revolutionise the way organisations approach supply chain operations. By connecting and streamlining access to data across various touchpoints, companies can transform logistical challenges into growth opportunities.
AI can enable end-to-end visibility and predict issues before they escalate, fostering a more responsive and resilient supply chain ecosystem. ●
For more information, please visit: appian.com/industries/broad-markets/ supply-chain-orchestration
The Second Wave of Supply Chain Transformation: What’s Coming Next?
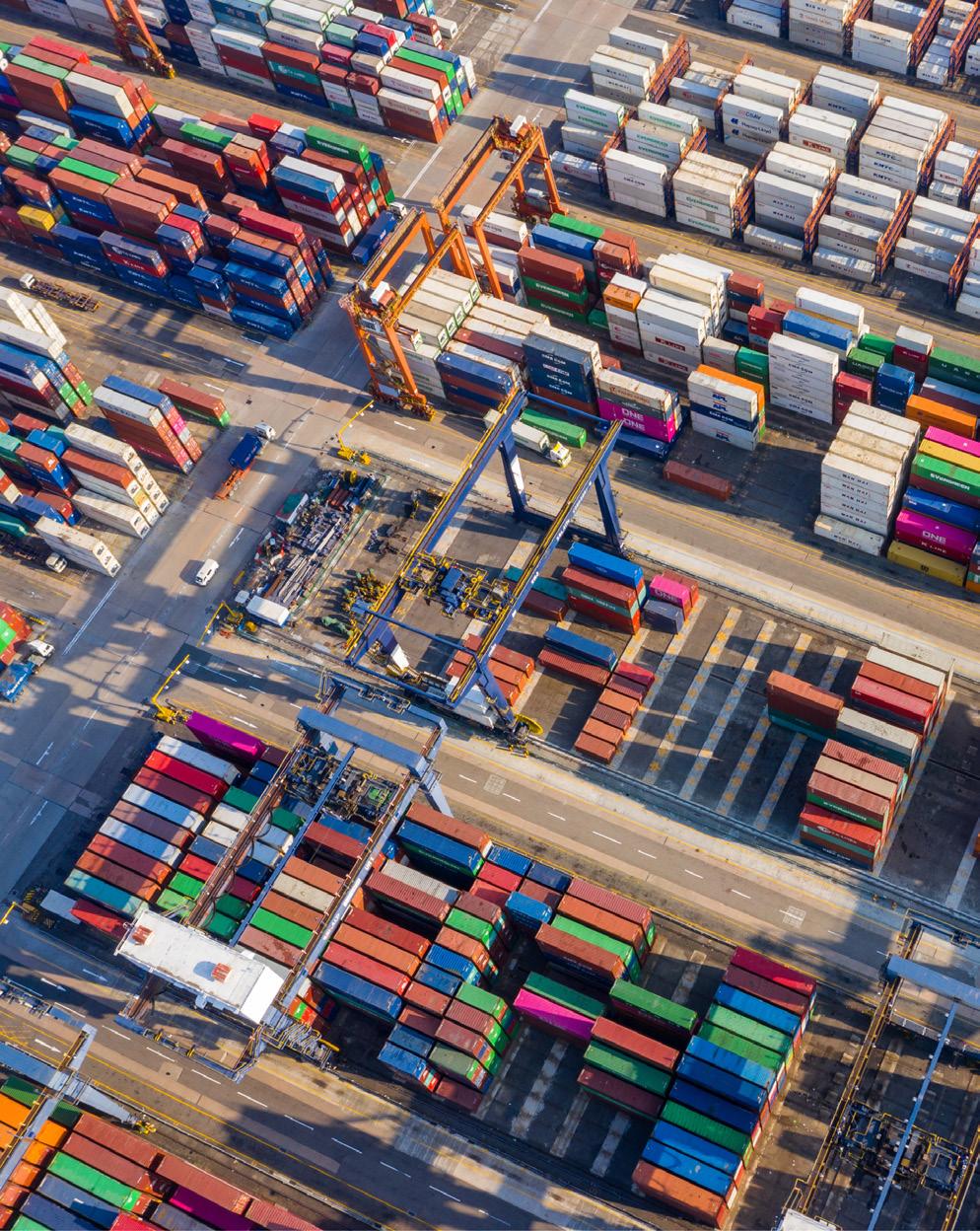
WRITTEN BY
TONY RICHTER, PARTNER, BASTIAN
When the COVID-19 pandemic first hit, the global economy came to a grinding halt. Supply chains that had been the invisible backbone of industries worldwide were suddenly thrust into the spotlight—and not for positive reasons.
From shortages in essential goods and delays in production, it became clear that many supply chains were woefully unprepared for such a widespread disruption. Terms like "supply chain crisis" became part of everyday conversations, and businesses quickly recognised the need for urgent upgrades across their physical and digital infrastructures.
The pandemic exposed weaknesses that had been festering under the surface for years. Overreliance on certain regions for manufacturing, outdated technology, and a lack of agility were just a few of the problems supply chain leaders had to contend with. As people began returning to work and businesses tried to regain their footing, there was a significant push to modernise and transform these critical networks. This phase, which we can call the "first wave of supply chain transformation," saw companies invest in everything from digital infrastructure to talent and workforce development, in an attempt to future-proof their operations.
However, as with any large-scale programs of change, the transformation of supply chains came with considerable costs. Just as businesses were starting to gain momentum in their efforts, the economic landscape shifted yet again.
The First Wave: Post-Pandemic Rush to Upgrade
The initial post-pandemic period was marked by an urgency to fix the vulnerabilities laid bare by COVID-19.
Many businesses, having experienced the consequences of poorly managed supply chains, began to invest heavily in technology. Digital transformation became a key buzzword, with companies adopting cloud-based platforms, realtime tracking tools, artificial intelligence, and automation to improve visibility and efficiency. There was also a focus on creating more diversified supply chains, with businesses reducing their reliance on single sources of raw materials or production to mitigate future risks.
Employees, too, became a focal point of this first wave of transformation. With the rise of remote work and the need for new skills in a digital-first environment, many companies were forced to
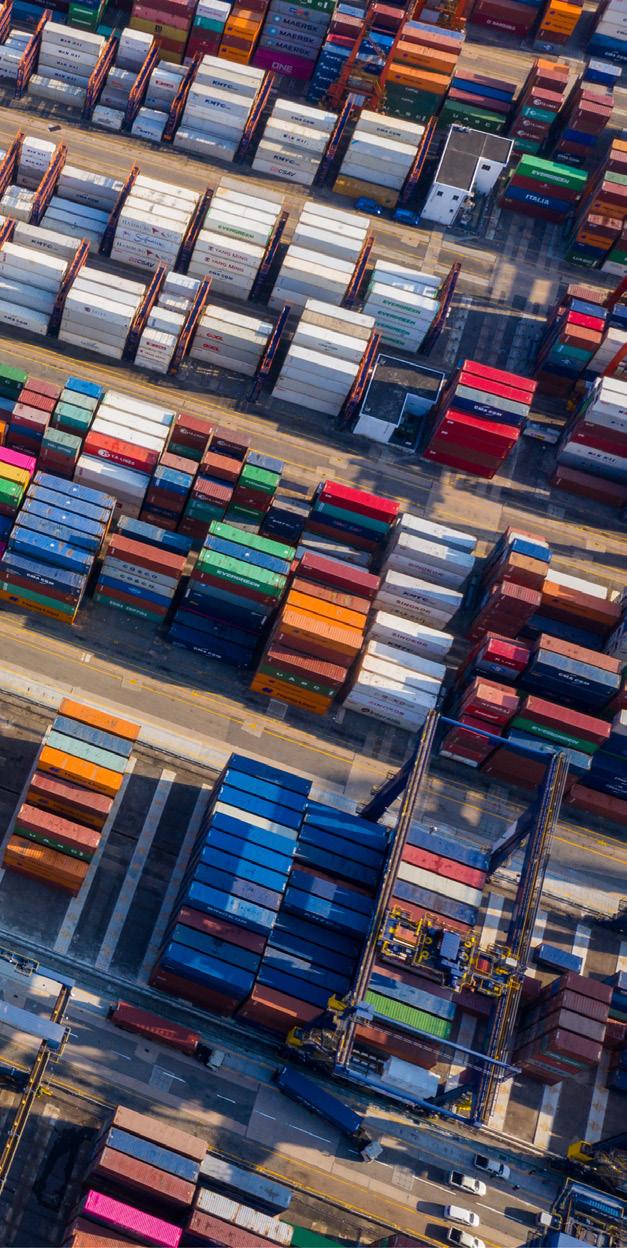
upskill their existing workforce or hire talent that could help drive the change. Supply chain leaders, data analysts, and IT specialists suddenly became crucial hires as businesses scrambled to build a more resilient network.
But these efforts were capital-intensive, requiring significant financial outlay. Unfortunately, the economic environment soon became difficult to continue steaming ahead as cost of materials, labour increased, challenging the validity of businesses cases.
Rising Interest Rates: A Sudden Slowdown
In early 2023, interest rates began to rise, making borrowing more expensive and reducing the availability of cheap capital. The rate surge was likely a response to inflationary pressures, in part driven by the massive investments made in infrastructure, technology, and workforce development during the first wave of supply chain transformation. Suddenly, companies that were in the middle of their upgrade efforts had to hit the brakes.
The rising cost of debt put pressure on businesses, especially those with tight margins, to slow down or even halt their transformation projects. What was once a rapid and aggressive push to modernise supply chains turned into a more cautious, wait-and-see approach. Companies that had been on the cusp of major breakthroughs in supply chain visibility and efficiency had to scale back their plans.
Despite the slowdown, the need for supply chain upgrades did not disappear. The pandemic may have highlighted the vulnerabilities in global supply chains, but the underlying challenges remain. And while many businesses had to pause their efforts in the face of rising costs, it’s only a matter of time before we see the resumption of supply chain transformation. This next phase, or "second wave," is poised to bring about even greater changes.
The Second Wave: Preparing for the Next Transformation
As we wait for the global economy to stabilise and interest rates level off and eventually reduce, we can expect a second wave of supply chain transformation to unfold. This wave will build on the foundations laid during the pandemic, but it will be shaped by a new set of factors.
One of the most important drivers of the second wave will be the geopolitical landscape. The ongoing conflict between Russia and Ukraine as well as the Middle East continues to disrupt global trade and logistics. As affected supply chains include everything from energy to agriculture, businesses are being forced to rethink their sourcing and logistics strategies. Diversifying supply chains will once again be a priority, as companies aim to reduce their exposure to geopolitical risks.
The upcoming U.S. elections will also have a significant impact on supply chain transformation.
The election results could influence regulatory policies, trade agreements, and economic stability, all of which will affect the ability of businesses to invest in their supply chains. Companies will need to keep a close eye on political developments to anticipate how future policies may impact their global operations.
The status of the investment markets will also play a critical role in determining the timing of the second wave of transformation. If markets recover and investor confidence returns, businesses will have easier access to capital, making it more feasible to resume their upgrade projects. Conversely, continued market volatility could delay the second wave as companies remain cautious about spending.
Despite these uncertainties, one thing is clear: the second wave of supply chain transformation will be even more comprehensive than the first. The focus will likely expand beyond digital infrastructure to include greater automation, advanced analytics, and artificial intelligence. These technologies will enable businesses to anticipate disruptions, respond more quickly to changes in demand, and optimise their operations for efficiency and sustainability.
When Will the Second Wave Happen?
The exact timing of the second wave remains uncertain, as it will depend on a complex interplay of economic, political, and technological factors. While the interest rate hikes of early 2023 have temporarily slowed progress, the need for supply chain upgrades remains critical.
In the coming years, businesses will be under increasing pressure to modernise their supply chains to stay competitive in an ever-changing global market.
The second wave will likely unfold gradually as companies regain financial stability and geopolitical tensions ease. Once the economy shows signs of sustained improvement and interest rates come down, we can expect a resurgence of investment in supply chain transformation.
Ultimately, the second wave of supply chain transformation will be a necessary evolution, driven by the lessons learned during the pandemic and the new challenges of the global economy. Companies that can navigate this next phase successfully will be better positioned to thrive in the future, with more resilient, agile, and efficient supply chains at their core. ●
How Retailers Can Overcome Warehouse Workforce Challenges During Peak Season
WRITTEN BY
GEORGE PECCHIAR, EXECUTIVE DIRECTOR CONSUMABLES, TECHNOLOGY, SOLUTIONS, PEACOCK BROS.
As retailers prepare for peak season, managing supply chain workforces becomes one of the most critical yet complex tasks. With half of Australian consumers expected to begin their holiday shopping by October, the rapid changes in demand require retailers to scale operations quickly and efficiently.
From hiring seasonal staff to optimising equipment usage, every level of the supply chain feels the pressure. The key to navigating these challenges successfully lies in effective preparation, careful forecasting, and the strategic use of equipment to enhance warehouse and back of store operations.
The Unique Nature of Peak Season
Unlike other times of the year, peak season requires rapid scaling to accommodate a surge in orders, both online and in-store. This pressure extends to all areas of the supply chain—stocking shelves, fulfilling ecommerce orders, and managing reverse logistics with returns. Retailers need to prepare not
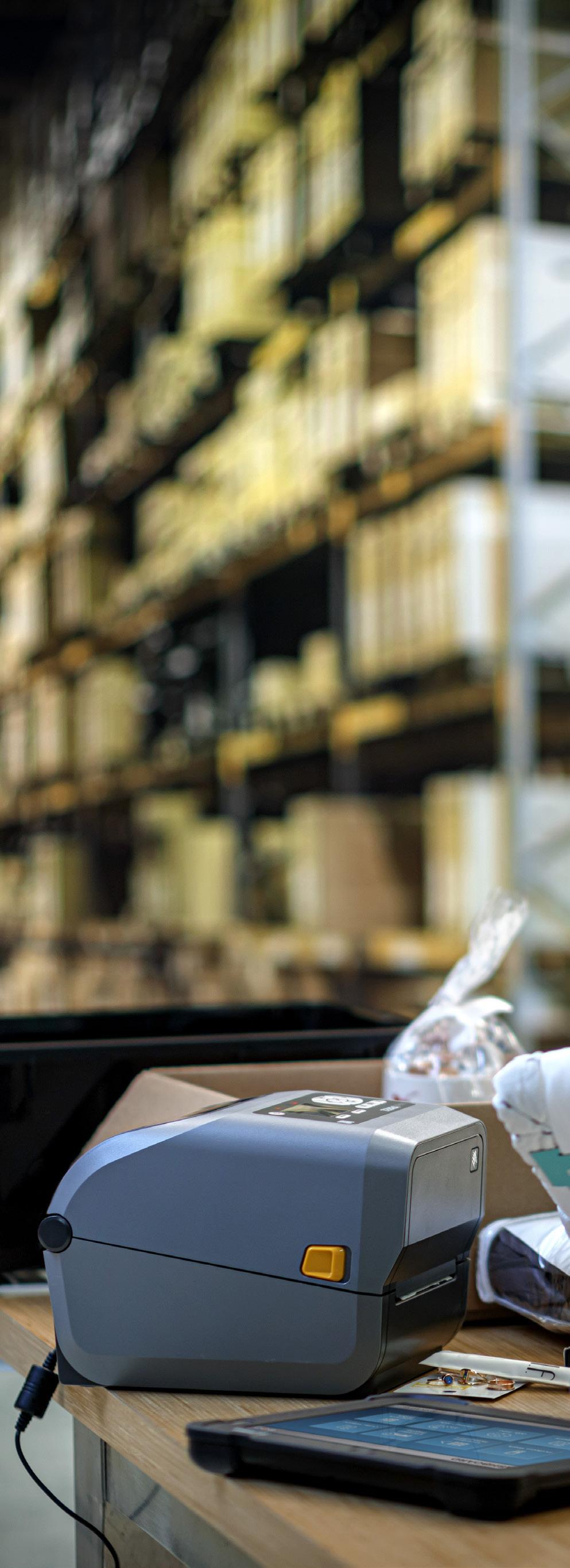
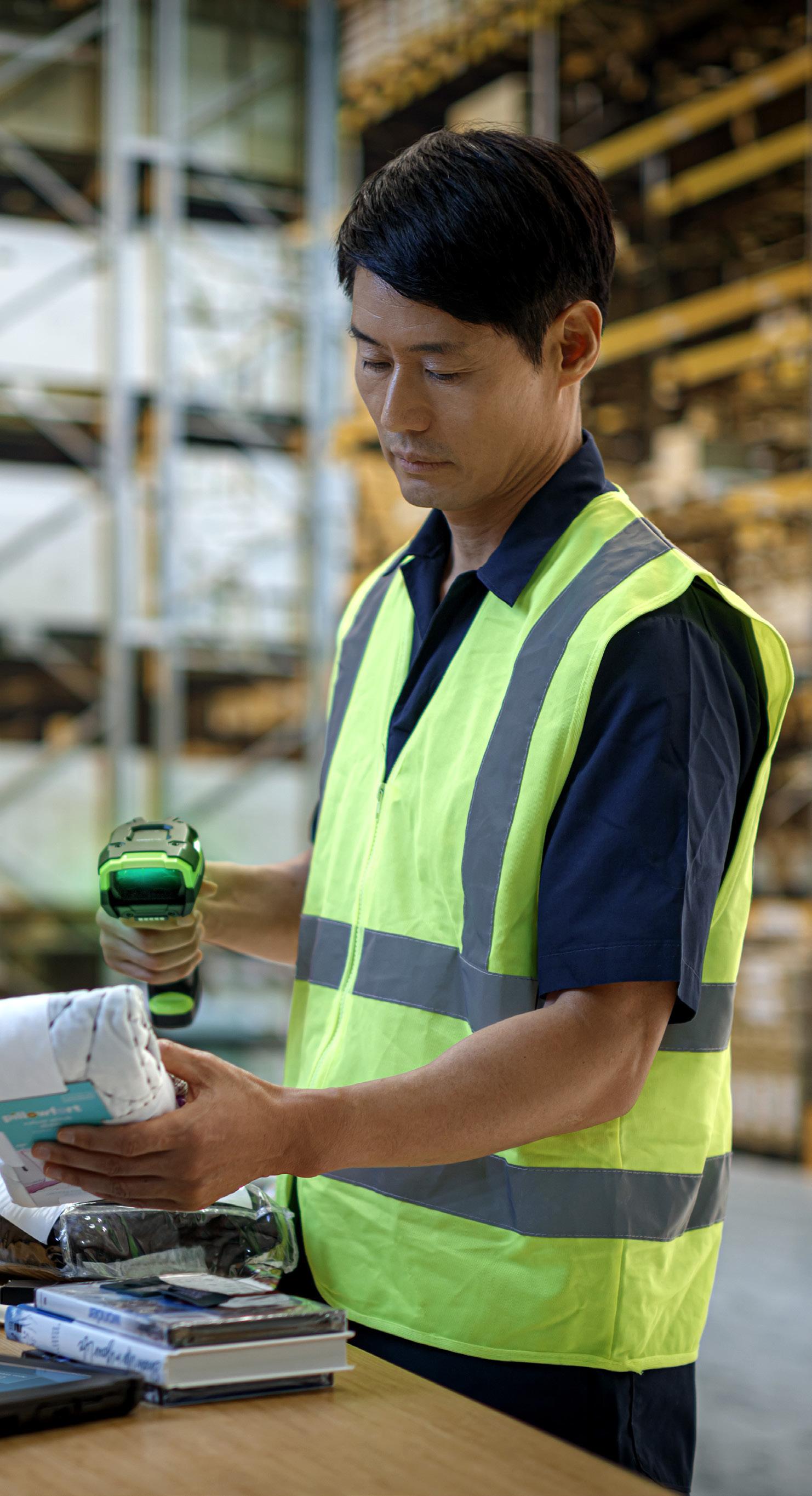
just for a higher volume of work, but also for greater complexity. Multi-channel fulfillment, varied shipping options, and heightened customer expectations require a warehouse and back of store operation that can handle the surge efficiently.
This is where the role of forecasting becomes essential. Understanding the anticipated volume of orders, the types of products that will be in demand, and the shipping timeframes can help determine the resources needed. However, even the most accurate forecasting doesn't eliminate the need for flexible solutions that can adjust to real-time conditions.
Optimising Workforce and Equipment Efficiency
One of the most significant warehouse challenges during peak season is workforce management. As operations scale up, so does the need for additional labour.
Retailers often turn to temporary, seasonal workers to meet this demand. However, bringing on temporary staff introduces new challenges, such as training, onboarding, and integrating them into an already fast-paced environment.
To minimise disruptions, retailers need to simplify their processes as much as possible.
Warehouse technology can play a critical role in this regard. By using modern devices—mobile computers, barcode scanners, and printers— retailers can enhance both accuracy and speed in key warehouse operations.
When equipped with advanced technology, warehouses and back of store operations can optimise inventory management, minimise downtime, and ensure orders are fulfilled quickly and accurately.
These devices support barcode scanning, real-time inventory updates, and seamless data exportation, ensuring that products are tracked efficiently from the moment they enter the warehouse to the moment they reach customers.
Tackling Workforce Gaps with Smart Hiring and Tools
Seasonal hiring often brings the challenge of balancing quantity with quality. High staff turnover can increase errors and slow down operations if new hires aren't able to keep up with demand. Automation and equipment that streamline workflows can help reduce reliance on a large number of workers carrying out error prone manual tasks. For example, barcode scanners and printers can cut down on picking errors, allowing workers to focus on productivity instead of

troubleshooting or redoing tasks.
Retailers also need to ensure that these tools are easy to use. The right equipment can speed up training times, as devices with intuitive interfaces make it easier for new employees to hit the ground running.
As the workload increases, equipping the workforce with the best tools for efficiency and accuracy is critical to maintaining smooth operations.
In addition to these strategies, it’s important to select scalable logistics solutions that can adapt to changing operational needs. Whether expanding or streamlining processes, choosing the right barcode labels, printers, and technology is crucial for effective warehouse management during peak season. For businesses requiring short-term storage or seasonal capacity, Peacock Bros. offers flexible rental options for equipment which offers a cost-effective way to manage resources without the need for long-term commitments. Depending on specific requirements, investing in appropriate equipment or opting for rentals can enhance productivity and ensure seamless operations during high-demand periods.
A Sustainable Option for Peak Season Technology Solutions
Once the peak retail season passes, normal business patterns tend to resume at lower levels. This

results in smaller order volumes and lower levels of warehouse throughput, along with a reduction in the number of workers in the warehouse. In this setting, retailers and their supply chain partners may find themselves with surplus equipment they no longer need for daily operations.
This is where flexible equipment solutions, such as rentals and loans, can be invaluable. For example, Peacock Bros.’ equipment hire options includes mobile computers, scanners, and printers that allow businesses to scale their technology needs up or down based on demand. These solutions minimise capital expenditure (CapEx) and ensure that businesses can return redundant devices after the holiday rush, avoiding the cost of maintaining equipment they no longer need.
The logistics behind scaling up a warehouse quickly during peak season often depend on having the right tools available.
Rented devices offer a practical solution for managing this surge. Not only do they minimise costs, but they also allow retailers to maintain flexibility when the peak period ends. By scaling down their device fleet after the holiday season, companies can avoid unnecessary maintenance costs and ensure they aren't paying for unused equipment during quieter months.
Preparing for Peak Season Success
The challenges of managing a warehouse workforce during peak season can feel overwhelming, but with the right preparation and the strategic use of flexible technology solutions, retailers can meet the demand head-on.
By forecasting accurately, optimising both workforce and equipment, and making use of rental options for devices, businesses can manage the surge in demand without overspending or compromising on efficiency.
The result is a well-prepared, adaptable warehouse and back of store operation that is ready to thrive during the busiest time of the year. ●
Mobile Technology: A Lifeline and a Challenge in Transport & Logistics
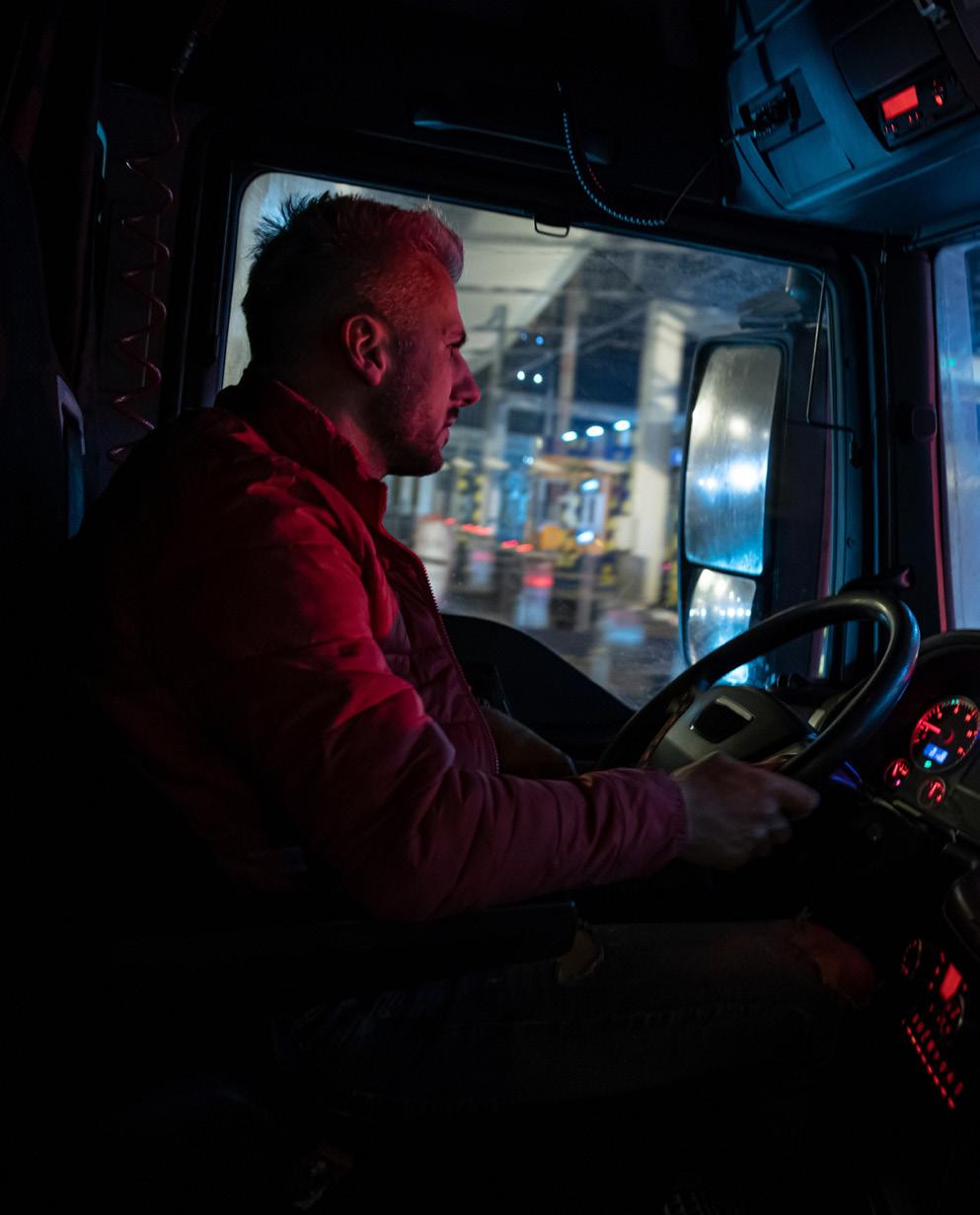
WRITTEN BY
MICHAEL DYSON, VP FOR SALES, APAC AT SOTI
As Australia’s transportation and logistics (T&L) sector becomes more dependent on mobile technology, this digital transformation brings incredible opportunities and complex challenges.
Mobile devices are crucial for everything from realtime tracking and communication to managing deliveries and inventory. Yet, despite their widespread use, SOTI’s latest research reveals ongoing inefficiencies, with Australian T&L employees losing an average of 16 hours per month due to mobiledevice-related downtime.
This issue isn’t just a minor hiccup in the system— it’s a significant bottleneck, hindering productivity, increasing employee stress and affecting customer satisfaction. The research, published in The Road Ahead: Driving Digital Transformation in T&L, underscores the pressing need for more seamless integration of mobile technology into daily operations.
The High Cost of Downtime: A Lingering Problem
Despite advancements in mobile tech, downtime remains a persistent issue. According to SOTI's findings, the sector has made only marginal improvements, with downtime decreasing by less
than an hour since 2021. This limited progress is surprising, given the rapid pace of technological innovation. The result? Thousands of hours are lost annually across the industry, directly impacting business performance and profitability.
For T&L providers, every minute of downtime represents a missed opportunity. With the sector under increasing pressure to meet tight delivery windows, inefficiencies affect timelines and impact customer trust. Downtime also drives up operational costs, as employees are often forced to work overtime to compensate for delays. In fact, 27% of workers report logging overtime hours to make up for tech-related disruptions, while 30% lose their bonuses and 27% forfeit time-off allowances because of these delays.
Device downtime is not only a technical issue, but it’s also a business challenge. Companies are losing productivity, their staff are facing increased pressure, and customer satisfaction is at risk. Reducing downtime and improving troubleshooting capabilities are crucial steps toward better operational efficiency.
Addressing the IT Support Gap: The Need for Real-Time Solutions
One of the most glaring issues in the T&L sector is the lack of immediate IT support when things go wrong. SOTI’s research reveals that 39% of drivers do not have access to real-time IT support on the road, leading to prolonged downtime. Furthermore, 32% of employees struggle to diagnose the problem or identify the next steps when a device malfunctions.

This lack of support causes delays, missed deliveries and ultimately dissatisfied customers.
A more proactive approach to IT support is needed. Solutions such as remote diagnostics and real-time device management platforms can help resolve issues before they lead to downtime. By monitoring battery life, network connectivity and app performance, companies can address potential problems early. For example, remote access tools enable IT teams to troubleshoot devices in the field, significantly reducing downtime and keeping employees productive.
By implementing these advanced support tools, companies can greatly reduce stress on employees, allowing them to focus on delivering goods safely and on time.
Security Concerns in Mobile Technology
Despite progress in training employees on mobile data security, concerns remain high. According to the research, 53% of employees worry that customer data could be compromised if devices are lost or stolen. Additionally, 54% are concerned about data breaches when devices are shared among multiple workers. In an industry where data privacy is paramount, these concerns need to be addressed head-on.
Balancing operational efficiency with robust data security protocols is a challenge, but it’s essential. Solutions such as secure user logins, device tracking and data encryption are critical in mitigating risk.
Integrating Enterprise Mobility Management (EMM) solutions like SOTI MobiControl can ensure that only authorised users access sensitive data, adding another layer of protection against security breaches.
Prioritising security-first strategies, from stronger encryption to better user authentication, can help companies keep both employees and customers safe while maintaining operational efficiency.
Reverse Logistics: An Overlooked Efficiency Drain
Another major time drain is reverse logistics. With 37% of an employee’s day dedicated to returns and only 9% of companies outsourcing this process entirely, the inefficiencies in managing reverse logistics are stark. Yet, this is an area where mobile technology can truly shine.
By leveraging real-time tracking tools, companies can streamline the returns process, making it easier for drivers and warehouse staff to manage returns efficiently. Real-time updates can help reduce delays, ensure that returned items are processed quickly and improve overall customer satisfaction. Optimising the reverse logistics process through technology frees up valuable time and resources, leading to more efficient operations across the board.
Sustainability: A Growing Priority for Employees
One of the more surprising findings in the report is the link between sustainability efforts and employee retention. The research reveals that 55% of employees would consider leaving their jobs if they felt their employer wasn’t doing enough to protect the environment. While 100% of Australian companies report taking steps toward sustainability, 63% of employees believe more could be done.
Sustainability is not just a corporate responsibility—it’s a key driver of employee satisfaction. Integrating sustainable practices into T&L operations, such as reducing emissions through optimised delivery routes or minimising waste in reverse logistics, can help companies meet both their environmental goals and employee expectations.
Employees are looking for companies that align with their values. By focusing on sustainability, T&L companies can not only attract and retain top talent but also build a more resilient, future-proof operation.
The Future of T&L Is in Digital Transformation
While mobile technology has brought significant improvements to how companies operate, there is still work to be done. By addressing issues like downtime, IT support, data security and reverse logistics, T&L providers can unlock new levels of efficiency and employee satisfaction.
With a greater focus on proactive solutions, real-time support and sustainability, the future of transportation and logistics is bright—for companies willing to embrace the change. ●
For more information on SOTI’s latest report, The Road Ahead: Driving Digital Transformation in T&L, please click here.
The Smart Supply Chain Revolution Begins in the Warehouse
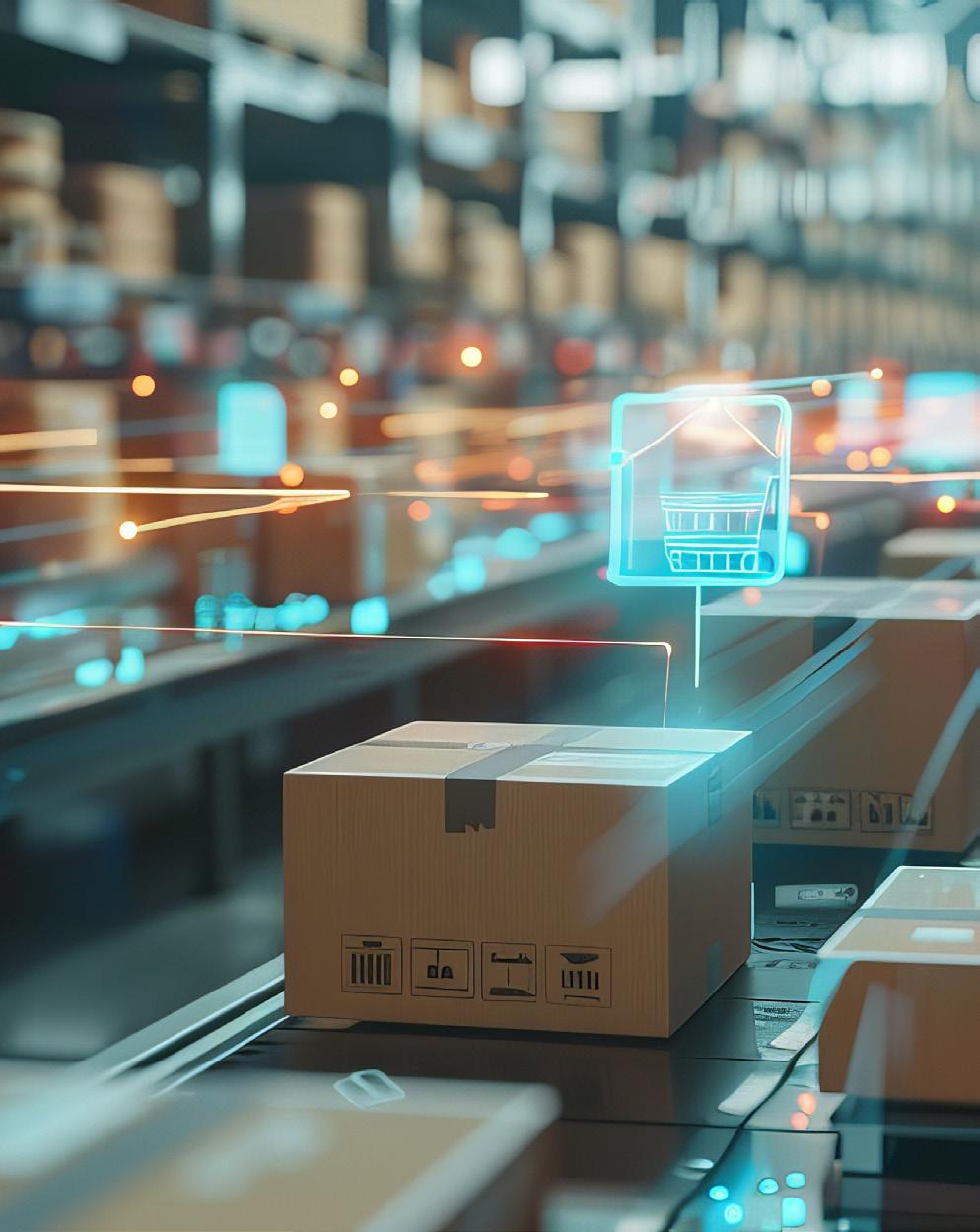
WRITTEN BY RAGHAV SIBAL, MANAGING DIRECTOR ANZ AT MANHATTAN ASSOCIATES
When people talk about ‘smart’ supply chains, it’s easy to imagine futuristic warehouse facilities straight out of an Isaac Asimov novel—fully automated with robot pickers and packers, efficiently receiving, moving, storing, and shipping packages to eager consumers. You might even daydream about fleets of self-driving trucks, planes, and drones, all powered by hydrogen and solar energy.
However, the reality of creating smarter supply chains in 2024 extends far beyond automation alone. While automation is a critical component for optimising operations, true intelligence in supply chains begins in the warehouse. Today’s warehouses are increasingly becoming the epicentre of the fulfillment universe. If we continue with the astrological analogy, much like a solar system with various celestial bodies in different orbits, warehouses consist of numerous elements, processes, and third-party interactions— all interconnected and working in harmony.
Connectivity is Crucial
In the modern warehouse, connectivity is one of the most vital elements for smooth and efficient operations. This includes everything from ERP systems, automation tools, robotics, scanners, wearable devices, label printers, IoT and RFID sensors, to third-party carrier compliance systems.
The smartest warehouse operations go beyond connectivity; they integrate and unify data sets and insights across a wide range of processes and technologies. With cloud-native solutions, everything is just an API call away, making the seamless convergence and utilisation of data a reality.
However, connectivity is just the foundation. The true power lies in orchestration. For systems focused on execution, such as material handling and robotics, connectivity is only the beginning. The real value is in how a warehouse management system (WMS) can effectively orchestrate tasks across all resources—human and machine alike.
Balancing work between people and machines, optimising picking density, and meeting or exceeding customer SLAs will be the hallmark of the most intelligent warehouse management solutions in the future.
Beyond Integration
From the moment an order is placed to its shipment and delivery, a seamless supply chain relies on systems like warehouse, yard, and transportation management working effortlessly together in real-
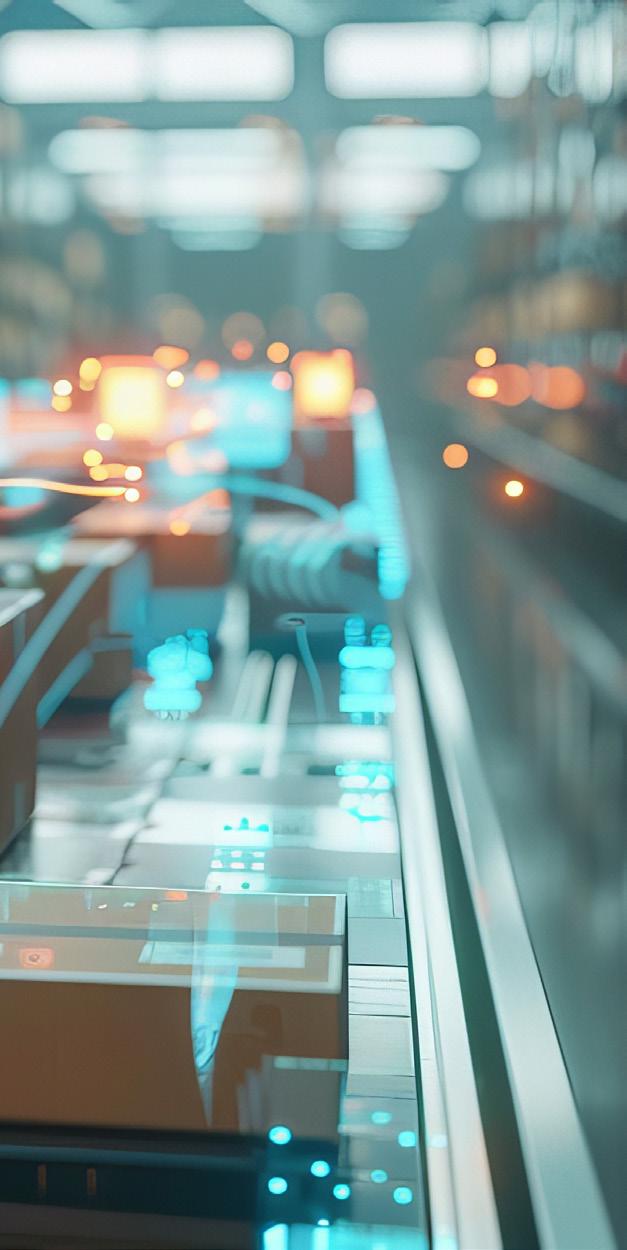
time as part of a unified whole. However, unification isn’t just about integration. It’s about dismantling silos and entrenched processes to address supply chainwide challenges in innovative and creative ways.
With a versionless, microservice-first approach to technology, there’s no need for lengthy hardware or software upgrades. New capabilities are introduced every 90 days, similar to the iOS updates on your iPhone—except with one crucial difference: operations continue without interruption, as these updates require zero downtime.
In the warehouse, this means that when labour management and warehouse management converge into a single application, a gamified employee experience becomes possible. The integration of performance tracking with execution workflows provides workers with complete transparency on their progress, coupled with motivational techniques to boost productivity and satisfaction.
Moreover, a unified approach to warehouse and transportation management enables continuous refinement of transportation plans. Schedules can now be infused with actual weights and volumes from the WMS as an output of cubing and palletising. Previously, the best approach was to optimise shipments at the start, but once the warehouse began execution, adjustments and exceptions would disrupt the plan. Now, shipments can be built and refined based on real-time, accurate data right up to the point of shipping, resulting in more fully utilised trailers and fewer miles on the road. This not only reduces costs but also supports a more sustainable strategy—a clear win-win.
The Infusion of Applied Science
The idea of applying science in the warehouse environment is no longer just theoretical—it’s a reality happening today. Over the last five years, technological advancements in the supply chain space have accelerated at an unprecedented pace. To stay competitive in this rapidly evolving landscape, organisations must embrace the latest developments in AI and Generative AI.
In this continuous technological arms race, having a team of data scientists to ensure the right techniques are applied to the right problems is essential. For example, enhancing business rules with AI-driven intelligence can help warehouse professionals achieve their goals more efficiently.
Consider a scenario where an organisation has numerous rules governing the prioritisation of work associated with orders based on specific characteristics. AI can augment these prioritisation rules by factoring in proximity to shipment cutoff times while integrating lower-priority tasks to boost pick density and efficiency. As the shipment cutoff approaches, AI automatically adjusts, ensuring ontime shipping. In this scenario, AI expertly balances the competing priorities of timely shipping and picking efficiency—something traditional algorithms and heuristics often struggle to achieve.
While we’re only beginning to explore how this rapidly evolving technology will transform daily and professional life, there are already practical applications
for Generative AI in supply chains and warehouses. Need an answer to a complex question? Simply ask the system, and it will provide an ‘instant’ response. Need help writing an extension? Just input some guidance, and the system will generate a starting point for a function that can be refined and used for custom data validation or updates.
Whether you need assistance configuring certain aspects of the system or providing real-time coaching to onboard new hires more quickly and efficiently, Generative AI can support these warehousing scenarios and much more.
Flexibility: The Key to Continuous Innovation
Finally, and perhaps most importantly: if you want to excel, you can’t afford to upgrade your warehouse management system every four to six years and call it a day.
The past four years—marked by global pandemics, multiple supply chain disruptions, and geopolitical unrest—have taught us that change is not only inevitable but increasingly frequent. Supply chains, particularly warehouse management systems, must be equipped to keep pace with this rapid evolution.
To stay ahead, agility and continuous updates are essential. Cloud-native, evergreen, microservicesbased solutions are now the standard. Imagine new capabilities automatically becoming available every 90 days, much like updates to a consumer app or a phone’s operating system.
Today’s warehouse management solutions must be nimble, automatically and continuously updated to remain relevant. But access to ongoing innovation alone isn’t enough.
Customers using intelligent warehouse management systems often have unique demands specific to their business. Therefore, a fully extensible system—where users can easily add data elements, validations, and business rules, and adjust execution workflows—is critical to success.
While the concept of a ‘smarter supply chain’ isn’t new, what is new in 2024 is the holistic approach that integrates high-quality processes, skilled and empowered employees, and cuttingedge technology.
When it comes to supply chain best practices, there’s no silver bullet. However, a strong foundation always begins in the warehouse. Organisations that focus on creating an environment conducive to integration, extensibility, and implementation will transform their warehouse operations from a potential pain point into a competitive advantage.
Ultimately, a more unified supply chain strategy starts in the warehouse, driving efficiency and, in turn, fostering sustainability—both economically and environmentally. This benefits not just the bottom line but the planet as well. ●
For more information: https://www.manh.com/en-au
Look out for the next issue
For all of your latest supply chain industry news, be sure to join our community on LinkedIn
Look out for the next edition of Supply Chain Insights, where we will be exploring “The Future of Smart Warehousing: Embracing Automation and Innovation for Tomorrow's Supply Chains.”
As supply chain demands evolve, the role of smart warehousing is becoming increasingly vital for businesses across the region. This edition will provide a deep dive into how cutting-edge technologies—such as robotics, artificial intelligence, and IoT—are revolutionising warehousing operations.
We will discuss the impact of automation on improving efficiency, reducing operational costs, and enhancing accuracy in inventory management, as well as exploring how smart warehousing is contributing to sustainability efforts and the shift toward more agile, scalable, and resilient supply chains.
For all of your latest supply chain industry news, be sure to join our community on LinkedIn
For more information or story suggestions, please contact: editor@supplychain-insights.media
For advertising enquiries, please contact: advertising@supplychain-insights.media
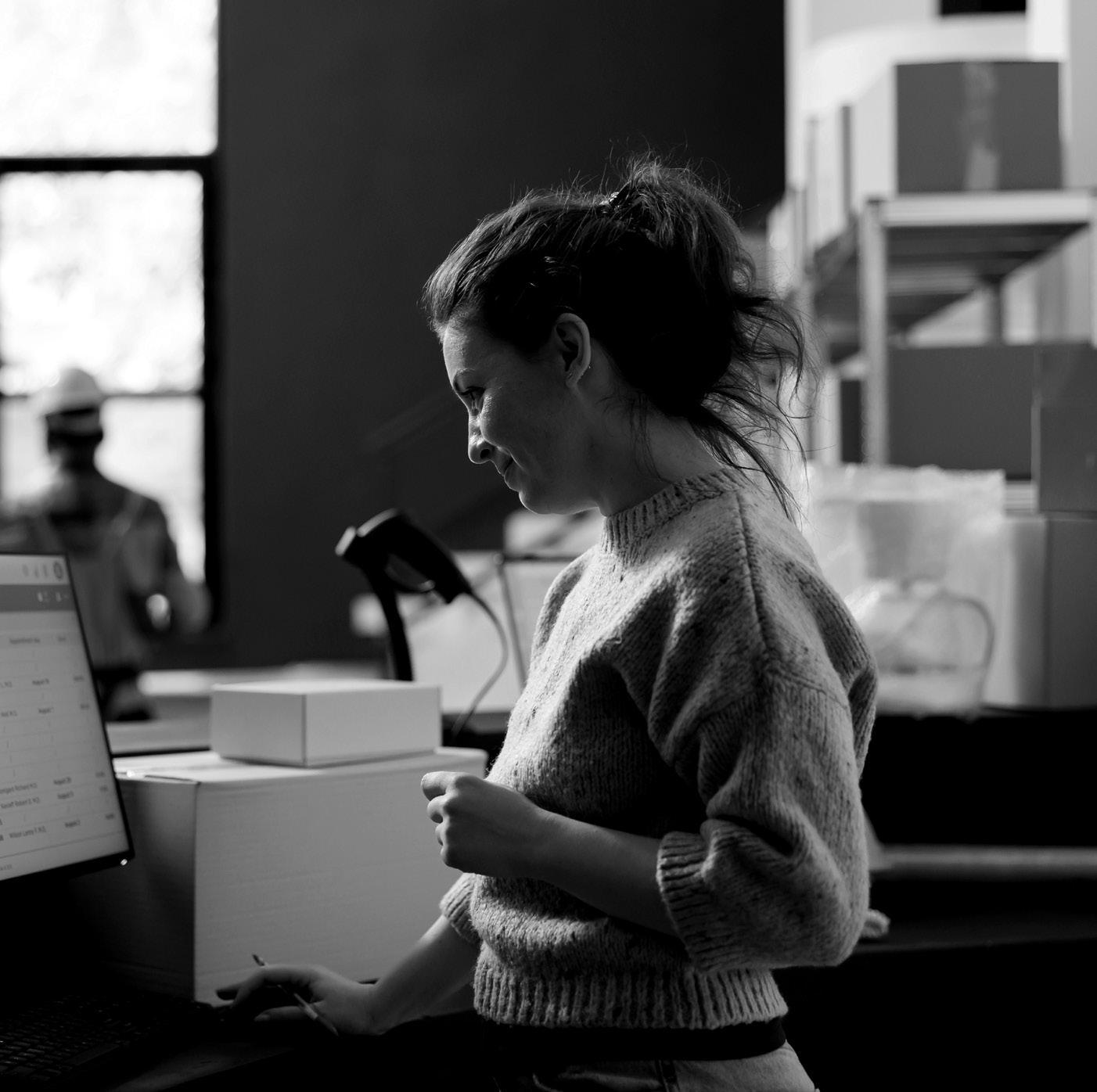