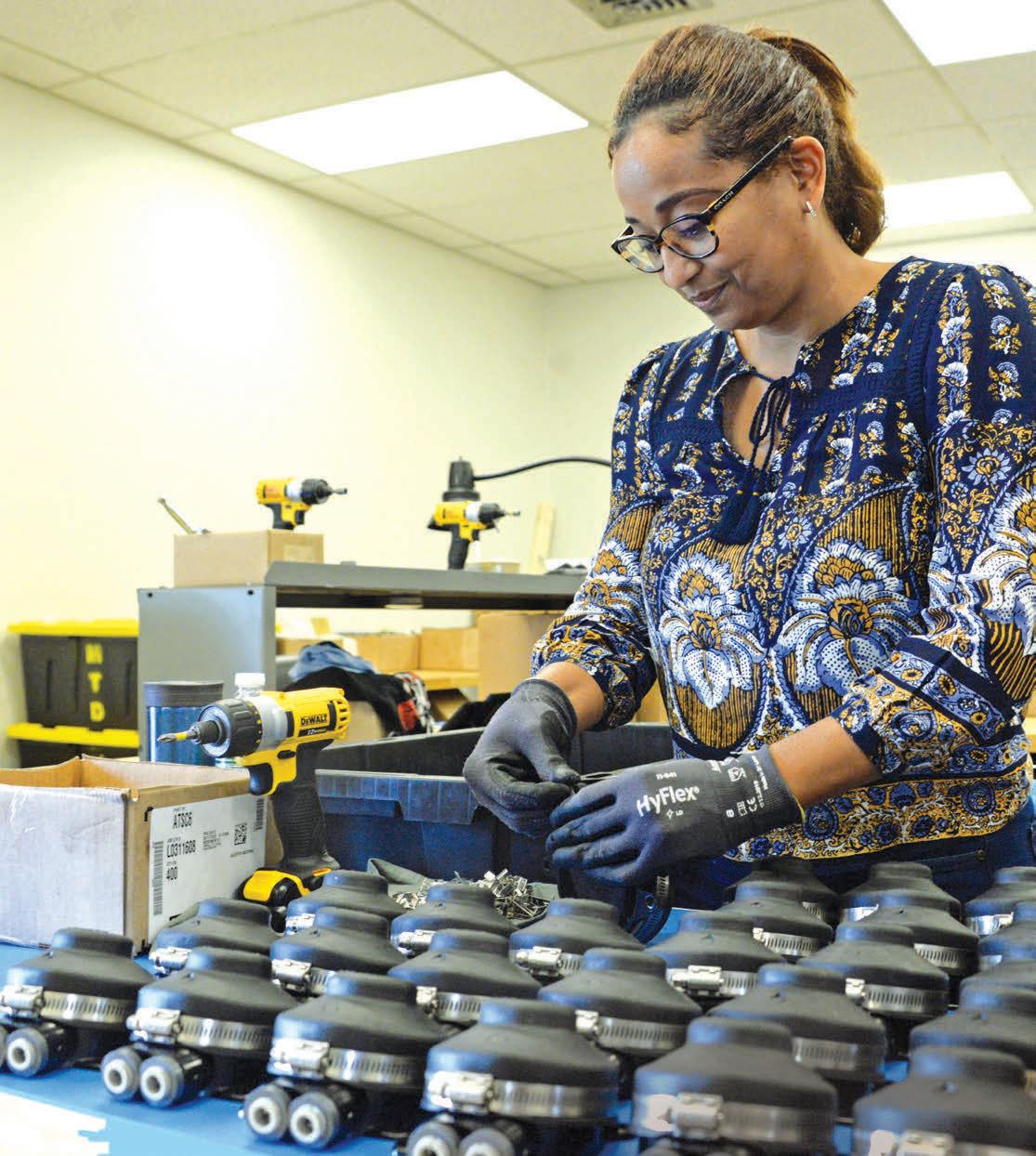
5 minute read
Q&A: Ingridt J. De oleo Morales
Ingridt J. De oleo Morales
The Bosworth Co. pump assembler
Advertisement
Ingridt J. De oleo Morales, a native of the Dominican Republic, began in the state’s Fast Track program for manufacturing at the Community College of Rhode Island a year ago and completed Phase 1. She was supposed to complete Phase 2 in July, but that was delayed by the COVID-19 pandemic. She’s a permanent U.S. resident and began working at The Bosworth Co. in East Providence in May.
QA &
1 What is your work like as a pump assembler at The Bosworth Co.? As a water pump assembler, I can prepare, order and put together different pieces and parts to build the pump. We work in an assembly line and in this process, we use different tools and equipment to shape the pumps. … Also, we meet all the company quality standards and make the necessary test to the pumps [and] may work packing and labeling the pumps. 2. How did you learn about the Fast Track program and what initially prompted you to get involved? In my job searching, I was looking in different places, online sources and work agencies. … When I enrolled in this program, I saw potential opportunities not just to get hired when I completed the training, but it would be a good beginning for me to know how college [works] in the United States. I also would be practicing my English and I would have credits at CCRI that could be valid to continue my education. 3. What is the program like and what important job skills have you learned? The program is a combination of hands-on and lecture that prepares you for a manual machinist or start a career in CNC [computer numerically controlled] manufacturing. I attended the classes with lectures and practice at CCRI. Turning, milling and grinding were the fundamental activities we developed there in Phase 1. Furthermore, we learned blueprint reading, geometric dimensioning and tolerancing, and we also developed skills using diverse measurement gages and precision tools. 4. What are some ways companies can promote job training opportunities to their employees? Let the employees know about these programs and the profitable results that they should have improving skills, [following safety] procedures and gaining knowledge. Also, supporting the employees with time for training programs, giving incentives or promotions. 5. Would you consider additional job training in order to advance your career? Of course, I think education and preparation are the keys to getting better opportunities. . . . I would like to continue improving myself, developing new skills, being fluent in English. It will make me able to build a hopeful future for me and my family in this country.
John A. Lahtinen is a PBN contributing writer.
PBN PHOTO/ELIZABETH GRAHAM
Continued from page 9 for this unprecedented virus. I believe the long-term impact on local manufacturing and supply-chain resiliency will be positive for Rhode Island.”
Chenevert acknowledges, however, that smaller manufacturers have struggled with cash-flow issues during the pandemic and, like many other small businesses, are fighting to survive.
WORKFORCE TRAINING
Throughout the pandemic and its aftermath, one area that will continue to be in the spotlight in the manufacturing industry is job training.
According to Margaux Fontaine, interim communications director
for the R.I. Department of Labor and Training, the manufacturing sector lost 2,200 jobs as a result of the pandemic from February to April in 2020. While manufacturers were deemed essential in the state and not ordered to close, workers who needed to at least temporarily leave their jobs as a result of school and day care closures, quarantine orders, or being in an at-risk group contributed to the job loss.
The good news? As of July, the 2,200 jobs lost had all been recovered – making manufacturing the first sector in Rhode Island to at least temporarily regain all the jobs that had been lost since the beginning of the pandemic, when 39,400 were employed, she said. In August, however, that number dipped back to 38,800.
After the pandemic hit in March, 71 participants enrolled in Real Jobs RI manufacturing industry programs, 19 of whom in September were in the Fast Track program.
RIMA’s Chenevert says training employees for multiple positions will be vital for employees and employers alike.
“Whether it is in manufacturing, accounting, engineering or some other sector, we must keep programs like Real Jobs alive,” Chenevert said. “This will be a lifeline for many employees if they lose their jobs. … Employees need to look at their position and where [it] is going. Training is available and there are resources that can assist them.
Chenevert sees a lot of interest [among job seekers] in manufacturing, due to many of those businesses remaining open to this point in the pandemic. One area he believes will grow over the next decade is robotics.
“Machinery is more complex and requires trained individuals to deal with the complexity of these CNC-type [computer numerically controlled] machines,” Chenevert said. “Data analytics is an area that is evolving more, as companies use this data to operate and better understand the market they are currently servicing, but also to expand their sales in new areas.”
Cowan echoed that sentiment, adding better workforce skills will be needed coming out of the economic crisis.