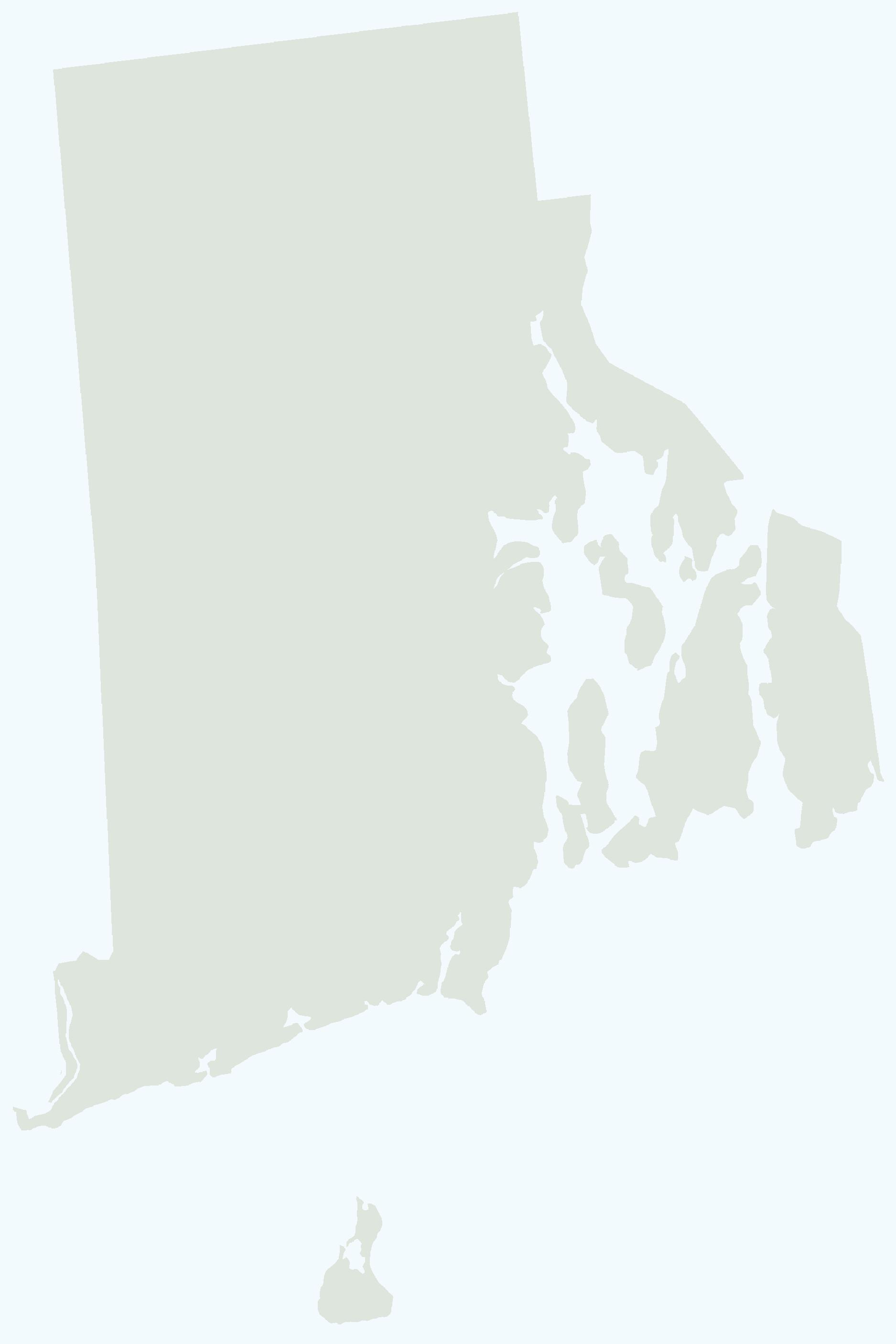
23 minute read
THINGS MADE HERE
Taking pride in ‘Rhody-made’
From the beginning of the American Industrial Revolution in the 18th century to the crisis-driven response to COVID-19, Rhode Island has produced an array of interesting and needed products and materials. And while the pandemic affected production and services for some companies, for others it served as the impetus for new designs and products. Many manufacturers and construction companies have worked through the pandemic, a testament to the ingenuity and commitment of the state’s makers, builders and designers and the importance of their contributions to the local economy.
Advertisement
JEWELRY
Snow Findings Co. ............................................................................................................................... 27 Herff Jones LLC...................................................................................................................................... 27
FOOD
Edesia Inc. ................................................................................................................................................ 28 Chi Foods LLC ......................................................................................................................................... 28
DISTILLERS
Industrious Spirit Co. ......................................................................................................................... 29 Rhode Island Spirits LLC .................................................................................................................. 29
HEALTH CARE
G-Form........................................................................................................................................................ 30 Subsalve USA LLC................................................................................................................................. 30
INDUSTRIAL
Amtrol Inc................................................................................................................................................. 31 Nelipak Corp........................................................................................................................................... 31
CONSTRUCTION
BOND Building Construction Inc. ............................................................................................... 32 K.O. Steel Construction Inc. ........................................................................................................... 32
CONSUMER PRODUCTS
Lumetta ..................................................................................................................................................... 33 Clean Brands LLC.................................................................................................................................. 33 Crisloid Products Inc.......................................................................................................................... 34 Aargo Environmental Inc................................................................................................................. 34
TEXTILES
Darlington Fabrics ............................................................................................................................... 35 Neocorp...................................................................................................................................................... 35
TECHNOLOGY
FarSounder Inc. ..................................................................................................................................... 36 Ambilabs LLC .......................................................................................................................................... 36
JEWELRY
› The family-owned jewelry metal manufacturer quickly expanded, and the company’s products and services are sold in wholesale quantities to national jewelry brands and manufacturers.
› The bulk of Snow Findings Co.’s business is producing jewelry components called findings. The company handles between 1.5 million and 2 million pieces per year. › Each finding takes one to two seconds to process. › The company also makes finished jewelry as part of its Lovements collection, launched in 2017, which includes various brass and rhinestone bracelets.

› Most of all the products are made of brass, and then electroplated by other
Rhode Island companies. THE STORY: Snow Findings Co. had humble beginnings when William Snow founded the company in the early 1950s inside his garage at his home in Cranston. The family-owned jewelry metal manufacturer quickly expanded, and the company’s products and services are sold in wholesale quantities to national jewelry brands and manufacturers.
COVID-BORN
Demand for jewelry items dropped significantly, hitting zero for a few months, during the COVID-19 pandemic. As an alternative, Snow Findings Co. began making “MasKords,” lanyards that allow a user’s mask to hang around on their neck when not in use, remain clean and pull up quickly when needed. The cords also help children in school in taking masks on and off throughout the day. Jewelry production, after the brief slowdown, has since resumed.

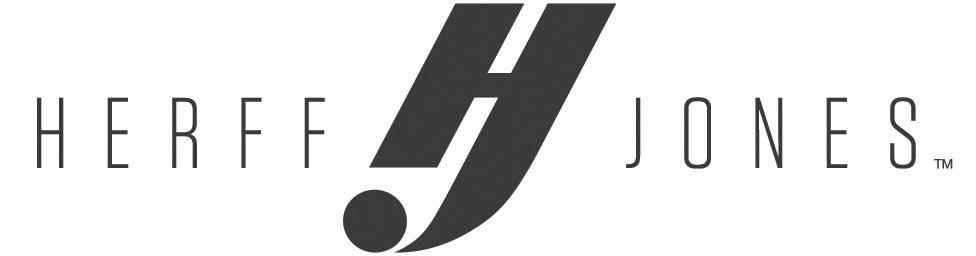
THE STORY: Celebrating high school achievements has a nice ring to it – literally. Herff Jones LLC, which has a Warwick manufacturing facility and is now 100 years in operation, has produced class rings from the very beginning and has since expanded its portfolio to diplomas, caps and gowns, diploma frames and letterman jackets.
› The rings are made from metal, including silver and gold options, with several finishes available to choose from. Additionally, simulated gemstones are used to enhance the ring as desired. › A class ring is worked on by about 20 different individuals in the plant before it is finished. Rings take four to six weeks to make. › The product-development team conceptualizes styles and works with artists for renders. Once adjustments are made, those renders are sent for computer-aided design for a rendering and wax file. Then, the panels are designed for activities and mascots. › Class rings in the new collections begin at $300. › Approximately 250 people are employed at Herff Jones’ Warwick facility.
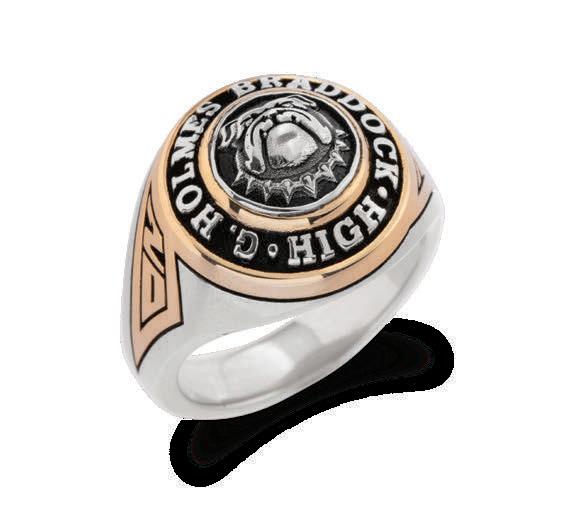
The manufacturing facility has continued producing rings with no interruption during the COVID-19 pandemic.
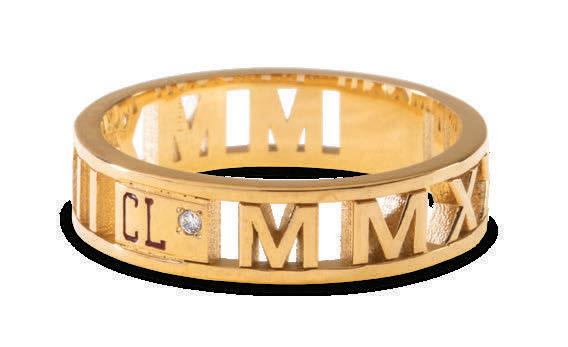
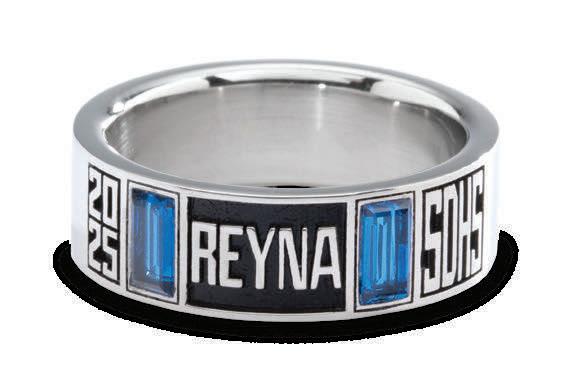
THINGS MADE HERE FOOD
COVID-BORN

MeWe Love Peanut Butter was made in direct response to the COVID-19 pandemic, as Edesia realized lines were forming at food banks across the U.S. The company thought a product that was single-serve, ready-to-eat, protein on the go would be helpful for school lunch programs, food banks and other disconnected populations such as the elderly. THE STORY: Named after the Roman goddess of food, Edesia Inc.’s mission is to save the world from hunger. The North Kingstown-based manufacturer has reached more than 50 countries, and several humanitarian organizations purchase most of Edesia’s products.
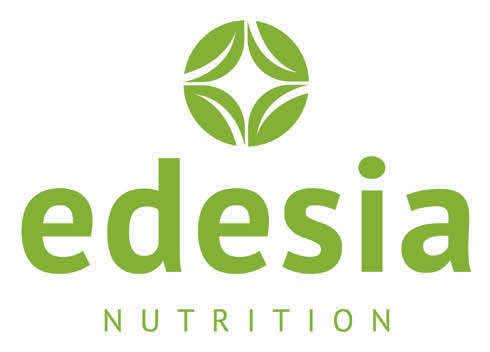
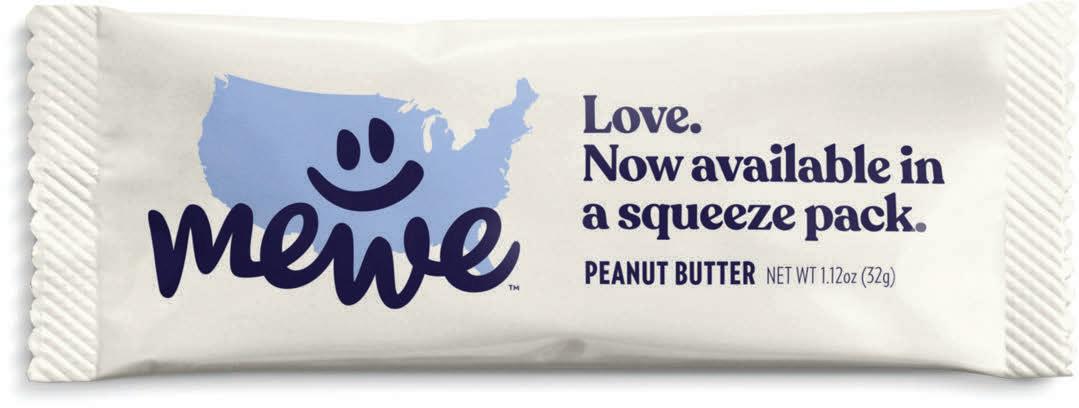
› Edesia’s new product, MeWe Love Peanut Butter, is made with peanuts, sugar, vegetable oil and salt. › Edesia has made approximately 4 million packets of MeWe Love Peanut
Butter from June 2020 to September 2020 and plans to make millions more.
› It takes approximately 18 minutes to produce a batch of peanut butter.
About five production employees work on making a single MeWe Love
Peanut Butter unit in the company’s secondary plant. › Supersacks of raw materials are brought in from Edesia’s adjoining warehouse and funneled into the factory where they go through a process of grinding, mixing and blending before getting directed to the packaging line, where a metalized foil wrapper seals the peanut butter into the packet before getting boxed up and stored in the warehouse. › Edesia employs 105 people.
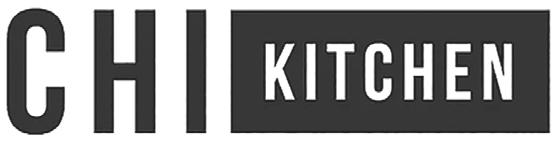
THE STORY: Chi Foods LLC CEO Minnie Luong began in 2015 selling single kimchi jars at a time at local food markets. But the humble beginning resulted in the Pawtucket-based food producer, also known as Chi Kitchen, to sell kimchi jars in more than 100 grocery stores across New England, in restaurants and at various colleges, including Roger Williams University and the Rhode Island School of Design.

› Chi Kitchen produces about 300,000 pounds of kimchi, a Korean delicacy, every year and each jar costs $8.99. It’s a healthy option that can be included with multiple dishes, including burgers, tacos, sandwiches, salads and rice, and noodle bowls.
› The kimchi is made by brining napa cabbage, then mixing red pepper, ginger, garlic, scallions, daikon radish. Then they go into the company’s fermentation room. It is 100% gluten-free. › It takes seven to 10 days to make kimchi from start to finish. › The company has eight employees, and it takes six of them to make one unit of product. › Chi Kitchen plans to introduce fermented sesame slaw and kimchi pickles to the market.
COVID-PROOF
During the COVID-19 pandemic, Chi Kitchen has seen a 50% increase in retail sales due to consumers seeking probiotic, immune boosting foods to be consumed at home. The company has remained in business throughout the pandemic.
DISTILLERS
THE STORY: Bringing a new distillery to Providence has been brewing for five years and not even the COVID-19 pandemic could stop new beverages from being introduced to the Ocean State. Industrious Spirit Co., since opening in spring of 2020, has produced approximately 4,050 bottles of vodka and gin, adding to Rhode Island’s growing brewing industry.
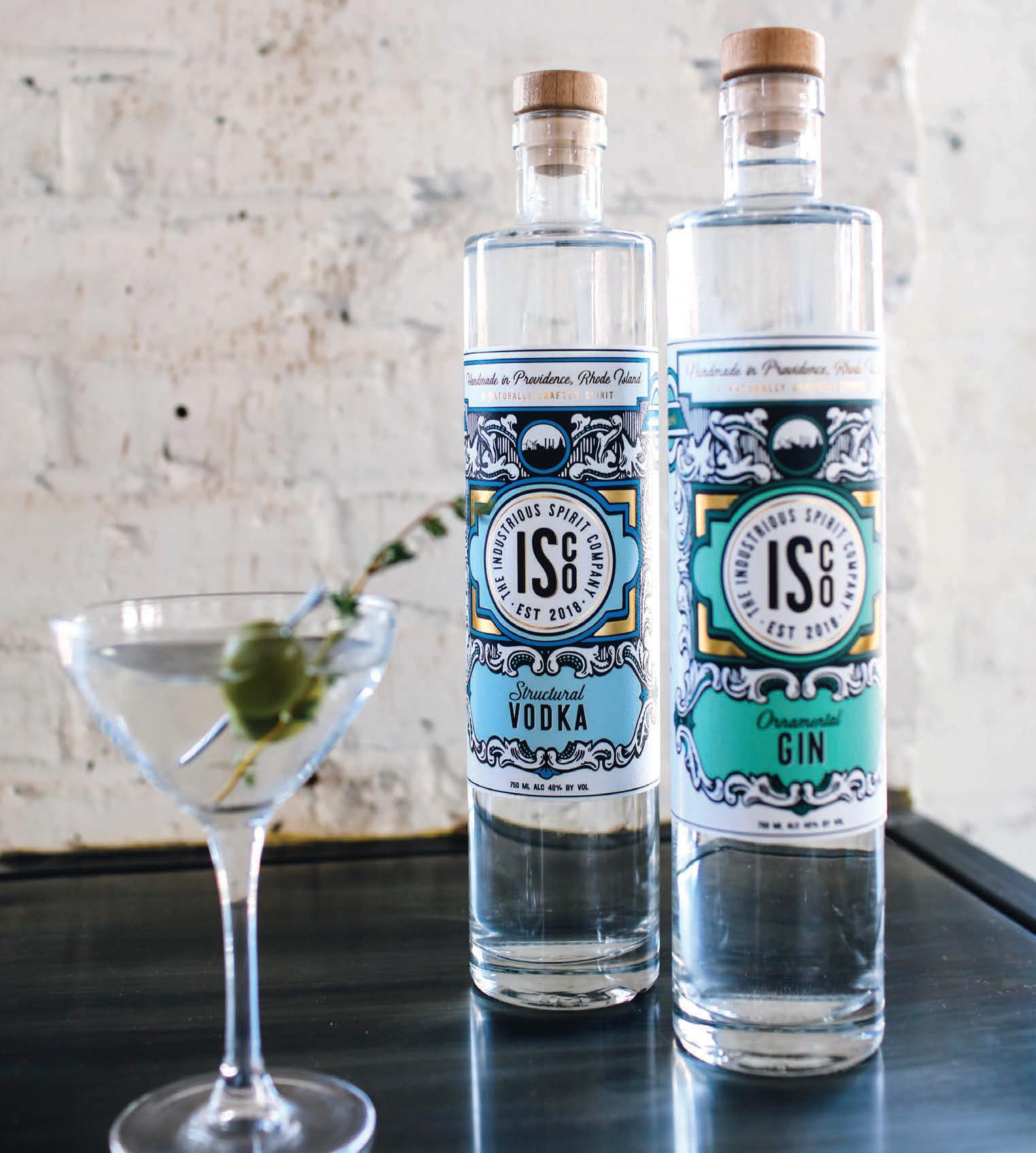
› The vodka and gin are made with 100% organic corn. To make the vodka, brewers cook, ferment and distill corn in small batches. Once the batches are ready, brewers combine them for a further round of distillation, and then everything is charcoal filtered at least 20 times for a crisper experience. › The ornamental gin is also flavored with juniper and a mix of 15 additional botanicals – including elderflowers, passion flower, citrus and hops. › The vodka takes about two months to make from scratch, while the gin takes nearly three months.
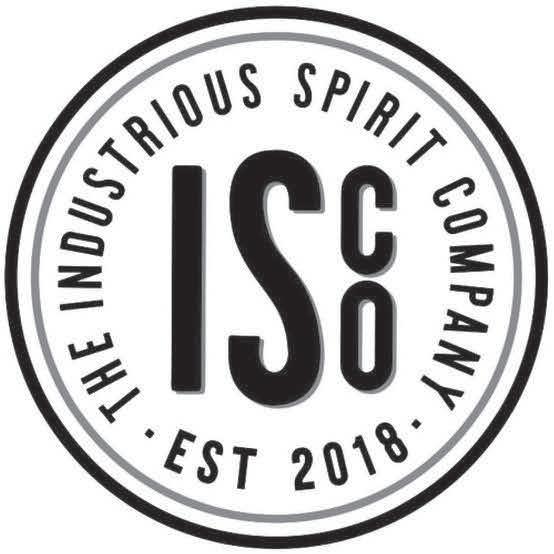
› There are five employees working for the distillery.
COVID-PROOF
Along with still making vodka and gin, Industrious Spirit Co., on a temporary basis, made hand sanitizer in order to help early on during the COVID-19 pandemic and gave it to the public for free.
THE STORY: Rhode Island Spirits LLC co-owners Kara Larson and Cathy Plourde are doing more than just bringing their love of alcohol to the masses; they are local trendsetters. The Pawtucket-based brewery is one of only a few fully women-owned distilleries in the country and produces the only LGBTQ-owned spirits brand in New England – Rhodium.
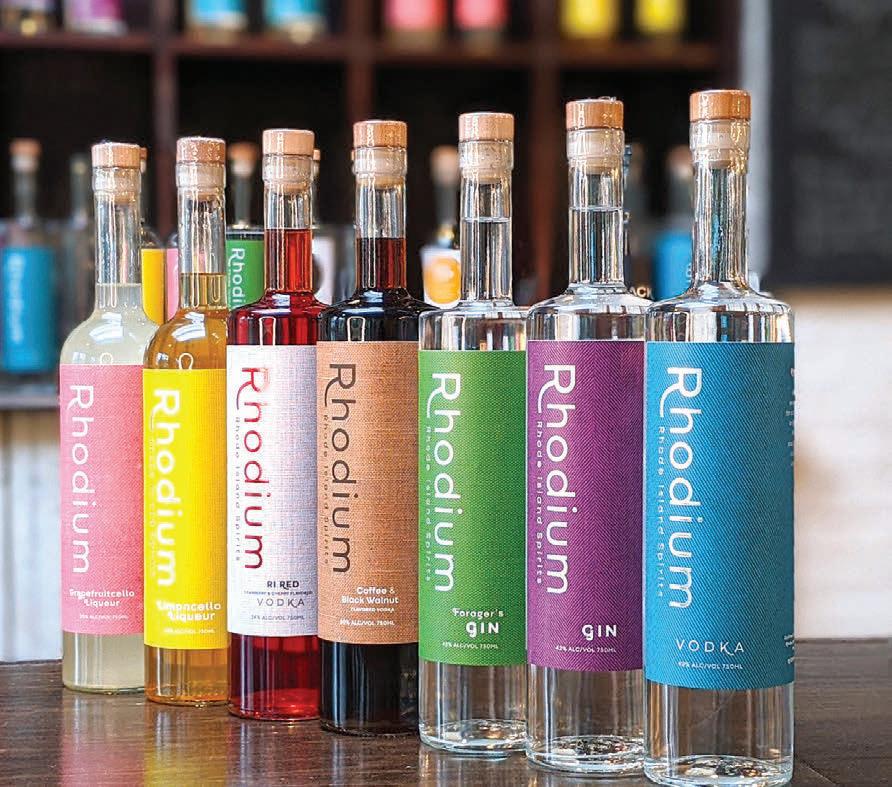
› Rhode Island Spirits has produced more than 17,000 bottles of Rhodium-brand spirits, which are available in stores and restaurants in Rhode Island and Massachusetts. › Larson and Plourde mainly operate the brewery, with six to eight people helping with production and packaging. › Rhodium spirits are naturally gluten-free, organic and vegan, and almost all of the line is certified kosher. › Rhodium Forager’s Gin features wild elderberry, red clover, rose hip and autumn berry, all locally foraged. Rhode Island Red Vodka is flavored with cranberries from local family bogs, plus tart cherry and herbal ingredients.
COVID-AFFECTED
Rhode Island Spirits has had to focus on manufacturing and distribution since the COVID-19 pandemic forced the company’s tasting room to close – 70% of the company’s revenue was derived from private events, tours and tastings in 2019. The company is trying to maximize business by distributing to retail stores, including starting to distribute in Massachusetts.
THINGS MADE HERE
HEALTH CARE
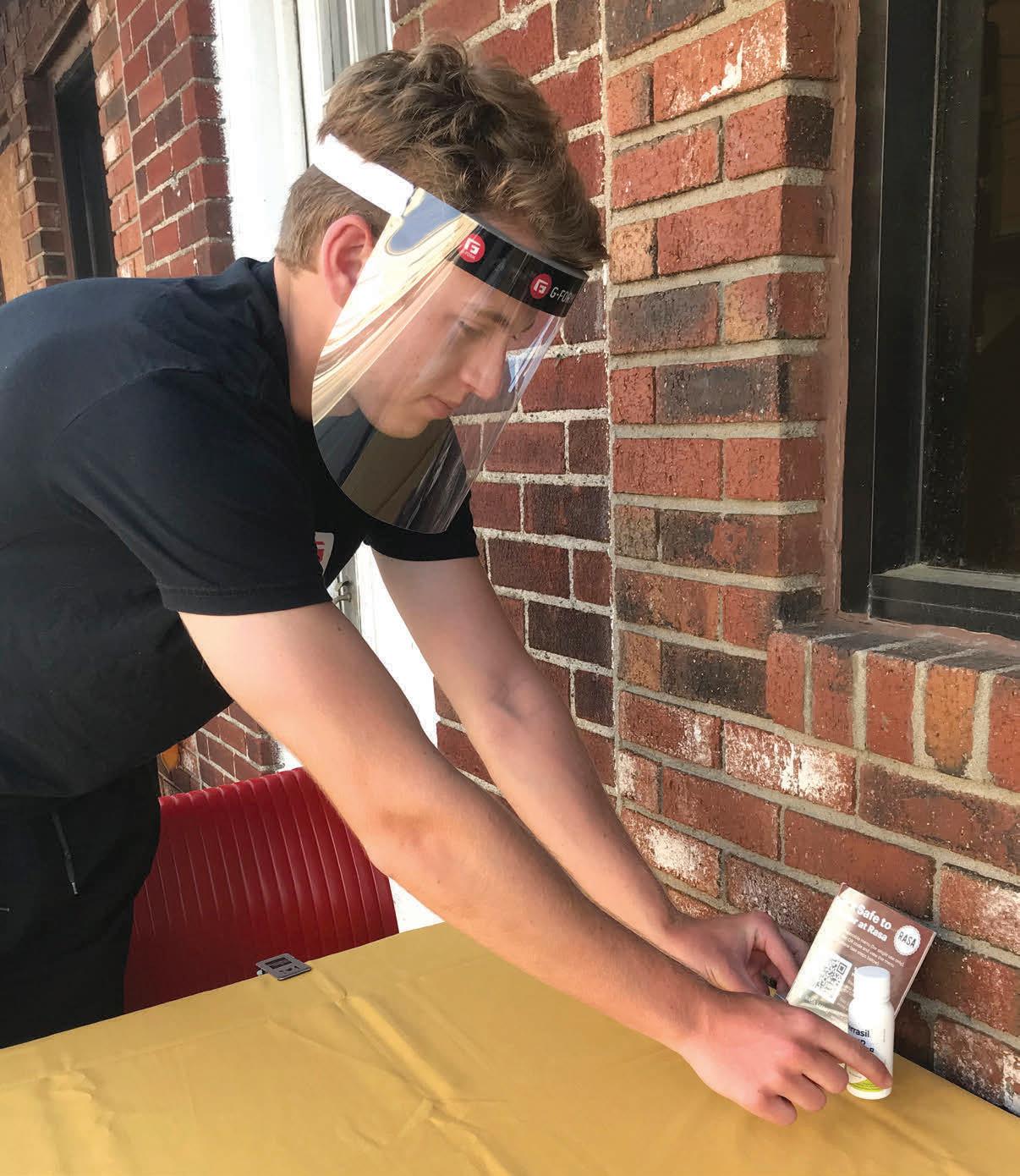
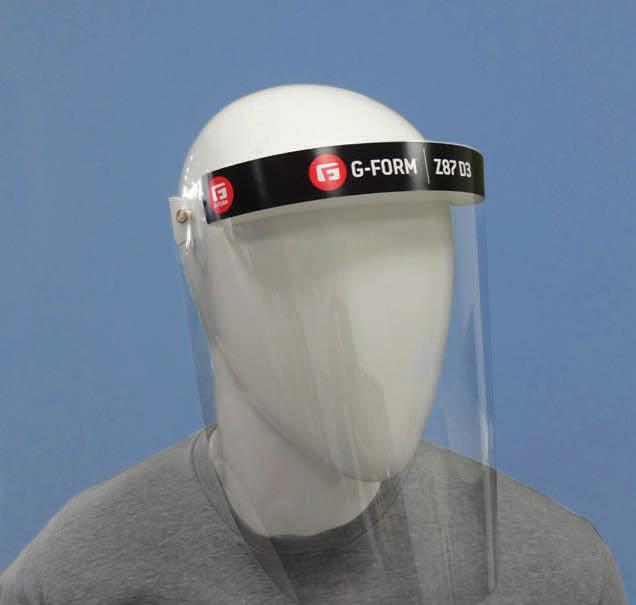
THE STORY: G-Form, founded by former athletes, maintains its focus on protecting people, even now if they are not on the athletic fields in competition. With the COVOD-19 pandemic taking hold of the world in 2020, the North Smithfield-based sporting goods manufacturer began producing face shields to protect the community from virus spread.
› The shields are made of anti-fog polycarbonate, a contoured foam brow pad and latex-free elastic. › The parts are cut to size and assembled by hand. Multiple operations prepare the materials and one operator assembles the parts. › Each shield costs $4 and more than 1 million of them have been produced since April 2020. › The demand for sports protective equipment was deeply impacted by the pandemic when spring sports were canceled. As a result, demand for face shields drove an increase in the company’s overall business.
› G-Form CEO Glen Giovanucci said: “G-Form has protected athletes against injury for over a decade. However, the mission to flatten the curve of COVID-19 is paramount.”
COVID-BORN
In April 2020, after an intensive effort to identify how to best contribute to the safety of health care workers and first responders fighting the pandemic, G-Form’s Polyworks facility began production on the face shields.
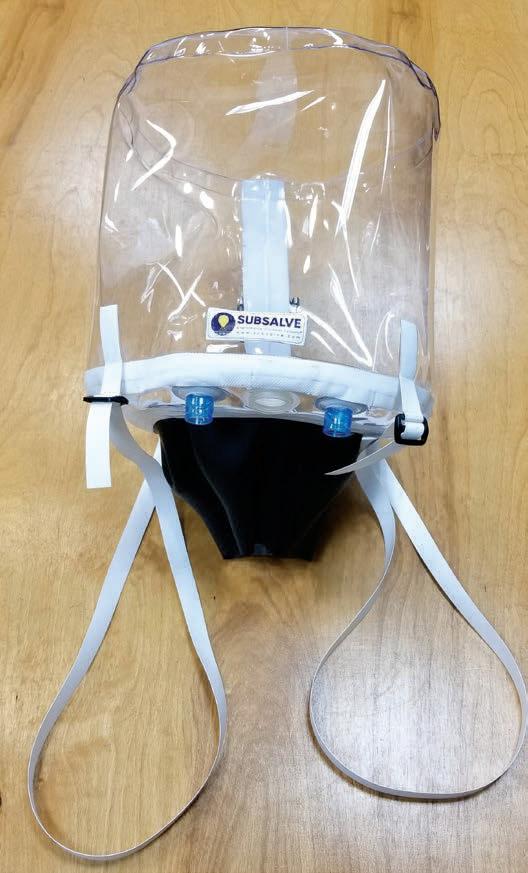
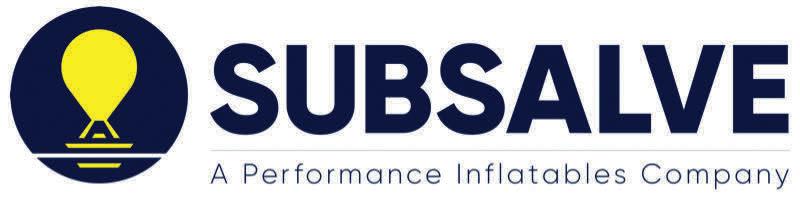
THE STORY: For close to 40 years, Subsalve USA LLC has worked to keep people and vessels above water. The North Kingstown-based manufacturer specializes in making underwater lift bags for recreational, commercial and military purposes to help with various water recovery and construction efforts. But, the company now is making products to help protect people from COVID-19.
COVID-BORN
Subsalve is producing an oxygentreatment hood, first developed in late April 2020. It was given emergency authorization by the U.S. Food and Drug Administration for treatment of COVID-19. › The hood is used by respiratory doctors and technicians in hospitals, and doctors teaching in medical schools and medical clinics in various countries. › The hood is made by cutting raw material, then welding and thermal bonding of the neck seal and clear vinyl body to the vinyl top and inlet ports. The process includes rotary welding the body to the neck seal base. › Approximately 400 units are made each day by Subsalve’s production staff and 30,000 have been manufactured and sold worldwide from late April 2020 through late September 2020. › Each hood costs $135. › Subsalve has 20 employees. › Since manufacturers were considered essential operations – and also given the product the company was producing –
Subsalve never shut down as the pandemic took hold of the state in the spring of 2020.
THINGS MADE HERE
INDUSTRIAL
THE STORY: Innovation has been Amtrol Inc.’s M.O. since the company was founded in West Warwick in 1946. The company set the standard in the well tank manufacturing industry by inventing the first diaphragm expansion tank in 1954 and the prepressurized well tank in 1963, known today as Well-X-Trol. Amtrol invented multiple other water tanks and hot-water makers in its history.

› Amtrol’s well tanks protect the water pump by reducing surge, dampening pressure spikes and offering a point of pressure control. › The Well-X-Trol tanks were first made as a better solution to traditional air-over-water tanks.
Among its features are high-strength steel to deliver 150 per square inch gauge working pressure and a patented Turbulator water-circulator device. › Sizes of the tanks range from 2 gallons to 119 gallons. › Homeowners with well systems use these tanks. They store water from wells and reduce wear on the pump by keeping off the requisite of the pump switching on and off constantly as people in the house use sinks and showers. › Amtrol’s tanks have features that protect water from bacteria in order to address water issues resulting from the COVID-19 pandemic. The Well-X-Trol well tanks feature a patent-pending antimicrobial liner that neutralizes bacteria on contact. Its Therm-X-
Trol commercial-grade thermal expansion tanks feature an Anti-Legionella liner that also neutralizes bacteria on contact.
COVID-PROOF
Production of tanks has not ceased at any point during the pandemic.
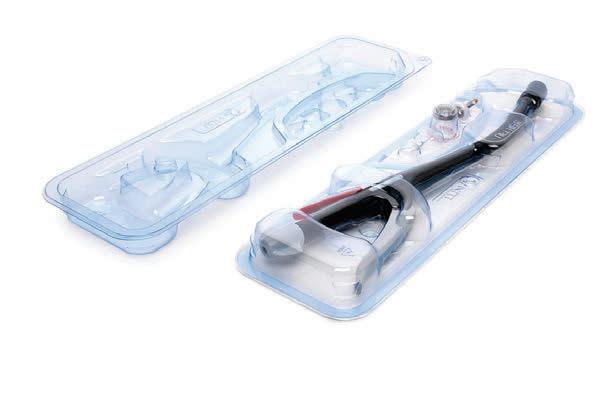
› Nelipak’s packaging is made inside class 8 cleanrooms to reduce the contamination of the packaging by particulate. › The packages are made with polyethylene terephthalate glycol, high-impact polystyrene and polycarbonate, among other materials, and it is heated, vacuum-formed and trimmed in less than five minutes. › Reels of the plastic material are drawn into the machine, heated on both sides to soften it before being moved over the tool with the shape of the tray to be formed, and clamped in the tool to create a seal before a vacuum is applied to pull the material into the tool/mold to form the tray. › About 150 employees work for Nelipak in Cranston. The number of workers varies, based on the product. › Hundreds of thousands of packages are produced annually and the retail cost varies by package depending on size and the thickness of the materials used.
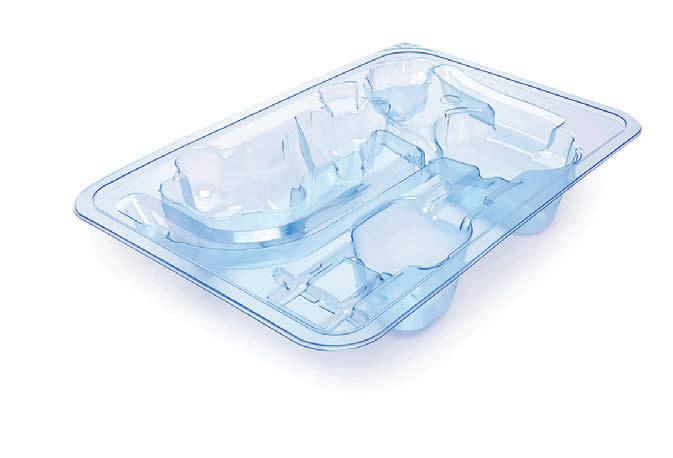
COVID-PROOF
Nelipak has remained operational during the COVID-19 pandemic, since it is considered an essential business to the health care industry. Production did not stop, but some Nelipak customers experienced a slowdown in demand initially. Volumes are starting to recover. THE STORY: Priceless jewelry needs to be kept with care in protective cases, hence why in 1961, Cranstonbased Alga Plastics started making thermoformed rigid plastic packaging for the jewelry industry. The company also saw a need to protect health equipment and, therefore, switched its packaging focus to the health care industry. The company was acquired by Nelipak Corp., based in Europe, in 2007 as Nelipak expanded its operations across the Atlantic Ocean.
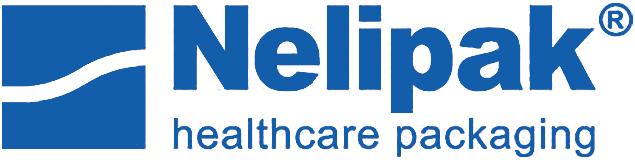
THINGS MADE HERE
CONSTRUCTION
THE STORY: Thomas J. Bond’s mother loaned the upstart entrepreneur $500 in 1907 to start a construction business and he began building sidewalks in Everett, Mass. More than a century later, BOND Building Construction Inc. has built several projects all around New England, with colleges, nonprofits and health care centers among their clients. One of those recent clients was the Providence Public Library, which was seeking a fresh look.

› BOND helped transform the Providence Public Library’s 1950s-era wing and auditorium areas with infrastructure and safety upgrades. The building’s Empire Street entrance became a three-story-tall atrium, and glass walls were installed to create a light-filled concept. › A new special collections space was built. The space now houses tens of thousands of historic books, manuscripts and photographs that represent more than 4,000 years of human history and culture. › The project took 18 months to complete and it cost $29 million. › Between 200 and 300 different workers representing various subcontractors, consultants and suppliers worked on the renovation, with daily crews of 75 working on-site. › Frank Hayes, president of BOND Building, said the company felt “privileged to play a key role in this transformation, delivering a modern public learning space in the heart of the city that goes beyond the ideal library facility.”
COVID-AFFECTED
The COVID-19 pandemic began right as BOND’s renovation project was about to finish. The inspection process, the final step, was impeded temporarily. However, the project remained an open job site and was back on track within a few weeks.
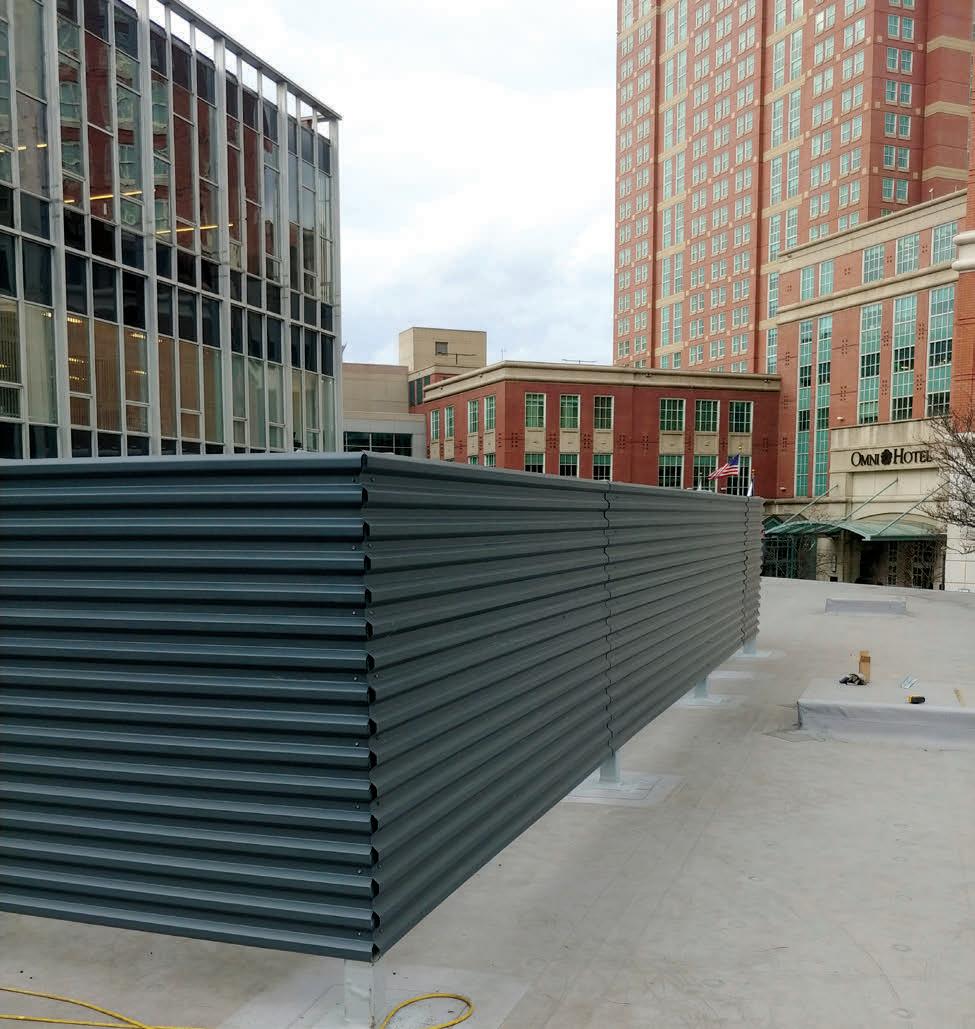
THE STORY: Kent Ormondroyd’s motto has always been: “The road to success is always under construction.” He has lived that mantra for the last 41 years as CEO and president of Scituate-based K.O. Steel Construction Inc., a family-owned job shop that produces custom-finished products for the construction industry.
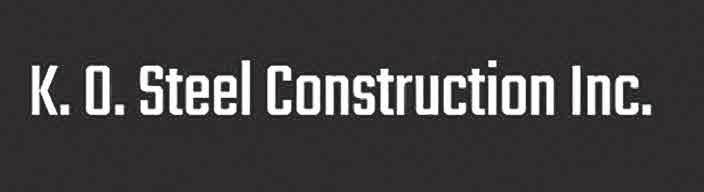
› The heating, ventilation and air conditioning roof screens atop the
Providence Journal building on
Westminster Street in Providence are made of steel, with a hot-dip galvanizing coating on them, and cost $42,000 to install them.
› Fabrication on the roof screen took one month to complete and one week to install. › Commercial and industrial businesses use the screens to help beautify their buildings and hide exterior mechanical units.
COVID-PROOF
Work on the roof screens has been unimpacted by the COVID-19 pandemic.
THINGS MADE HERE
CONSUMER PRODUCTS
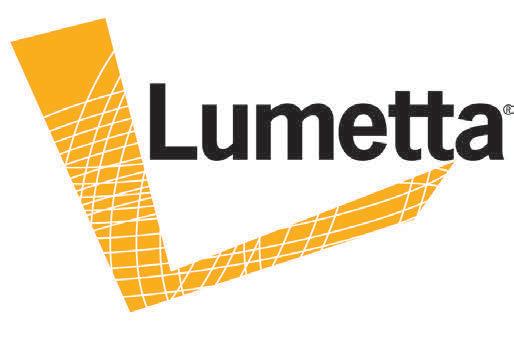
THE STORY: Bill Prichett, while simultaneously doing architectural projects, had also painted and made sculptures for close to 20 years. It was combining those two passions that laid the groundwork for a brighter future when in 1992 he founded Lumetta. Since then, the Warwick-based manufacturer has produced many decorative commercial luminaires with various materials, including with antimicrobial protection technology.
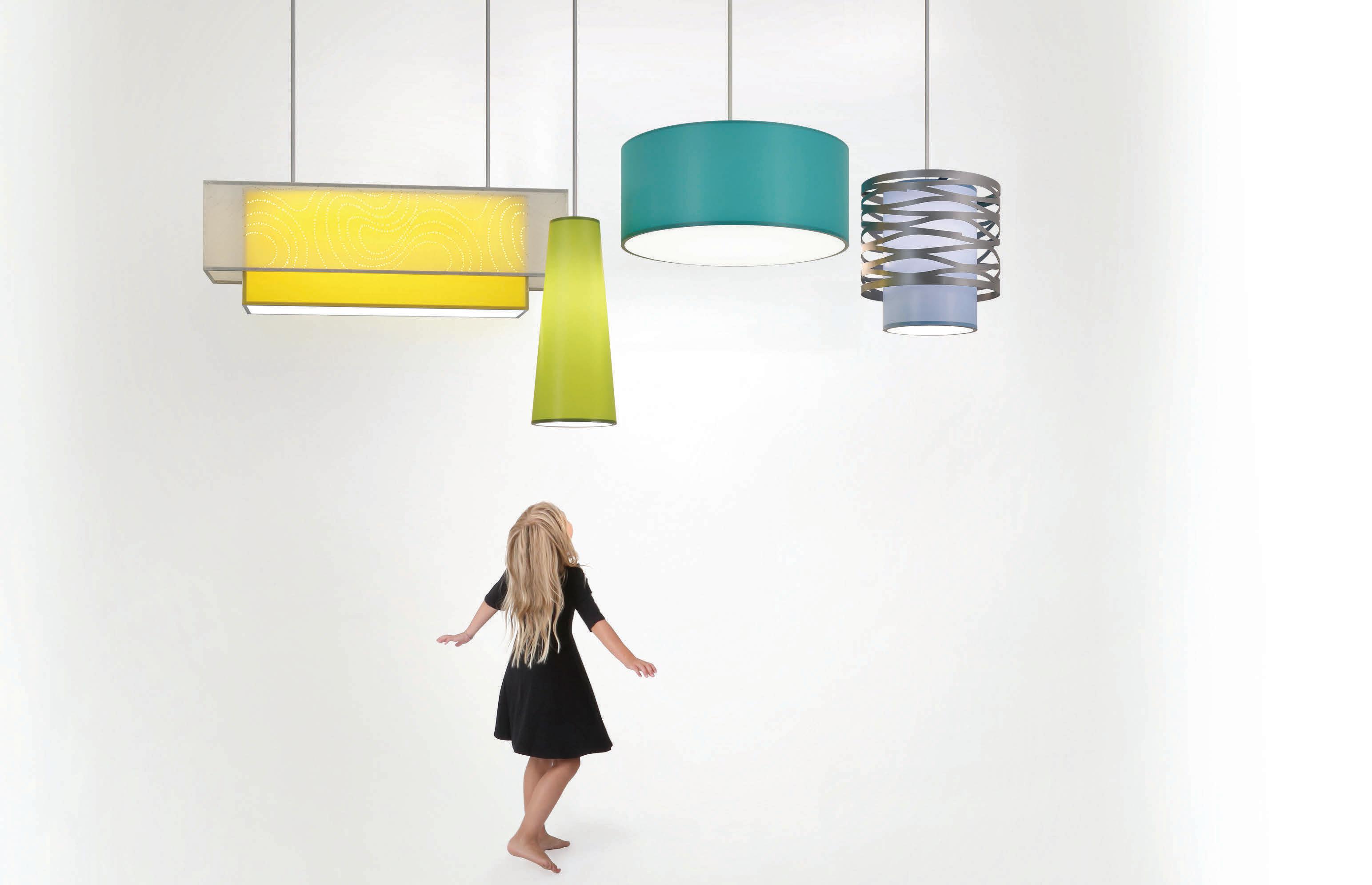
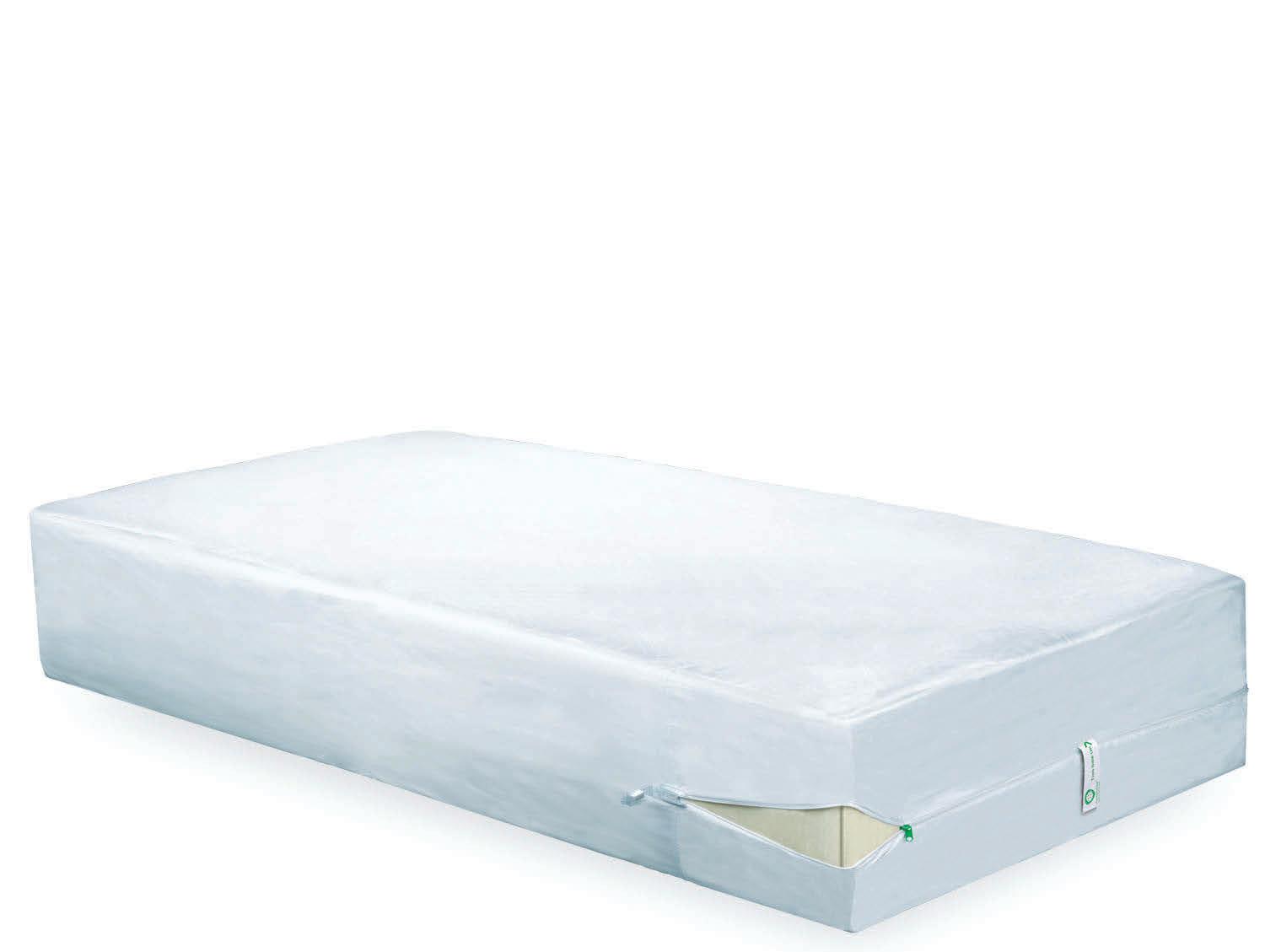
THE STORY: Being free of allergies and other toxins is key to having a good night’s sleep. Clean Brands LLC, based in Warwick, designs and makes beddingprotection fabric, such as the MicronOne and Zip-N-Click closures to keep people free from allergens, as well as from stains and wetness.
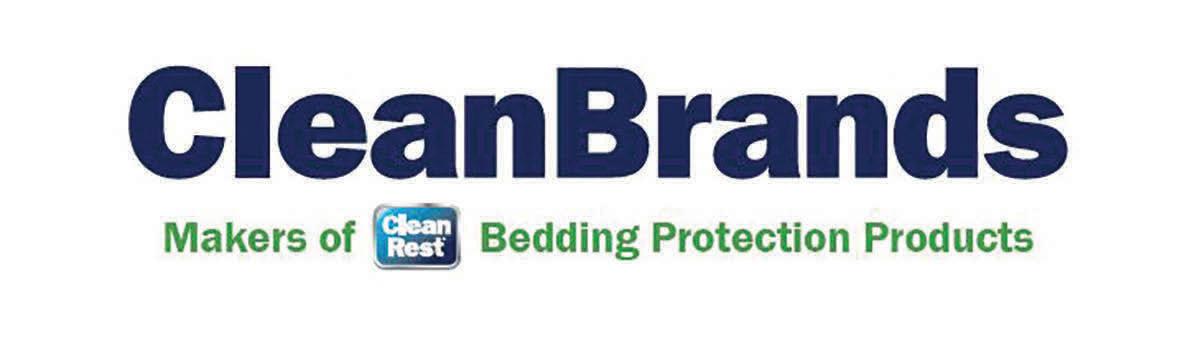
› Lumetta’s Lumenate and TransLumenate material installed in its light fixtures is made with antimicrobial protection to prevent various growths that could potentially cause illnesses and infections.
› Lumenate and TransLumenate are offered in more than 100 colors, and the company allows customers to also create and design their own patterns. › During the COVID-19 pandemic, the company has seen a notable increase in orders with Lumenate because of the antimicrobial properties.
COVID-PROOF
Production on the material has not halted during the pandemic.
› Among the products CleanRest protects are mattresses, box springs, and pillows from spoilage, spills, allergens, bed bugs and regular wear and tear. › Mattress encasements cost between $50 and $70, depending on size. › CleanRest products are designed with a patented
MicronOne waterproof polyester fabric, which is 100% waterproof and more breathable than other such fabrics on the market. › More than 500,000 CleanRest products are made annually. › Hotels and other multibed facilities, such as senior-living facilities and dormitories, use CleanRest products.
COVID-BORN
In April, the MicronOne waterproof fabric passed the U.S. Centers for Disease Control and Prevention’s Level 4 standard for virus protection. The fabric is made to block all virus and bacteria down to 32 nanometers in size, and the list includes COVID-19.
THINGS MADE HERE
CONSUMER PRODUCTS
THE STORY: In 1948 in Brooklyn, N.Y., Alphonse and Lucky Lodato wanted to create games for people to both enjoy and appreciate the high quality the games that are made. More than seven decades later, Crisloid Products Inc., now based in Providence, continues making hand-crafted board games, including checkers, mah jong, dominoes and its trademark game, the Newport Master Backgammon Table.
› The Newport Master Backgammon Table was first made in 2018, and between 50 and 100 are made each year. › The table is crafted from hardwood cherry harvested in the eastern
U.S., stands 30 inches tall, and is 43.25 inches wide and 27 inches long. Game pieces are casted in resin, and cork is both prepared and printed in Portugal. › It takes the company’s 10-plus employees approximately three to five weeks to make each table. › Each table sells for $2,500. › The tables are bought by individuals and clubs all over the world.
COVID-PROOF
The company has remained operational during the COVID-19 pandemic and demand for games has increased, since people have had to stay at home.
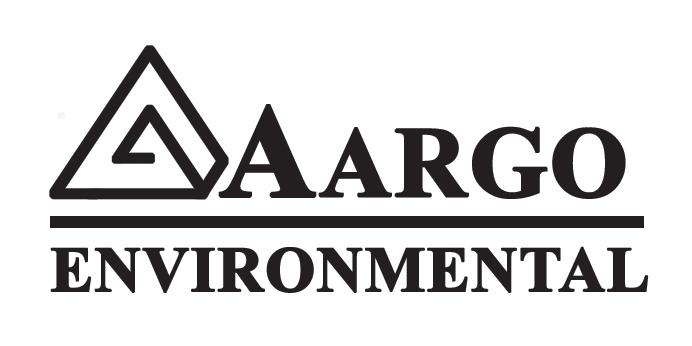
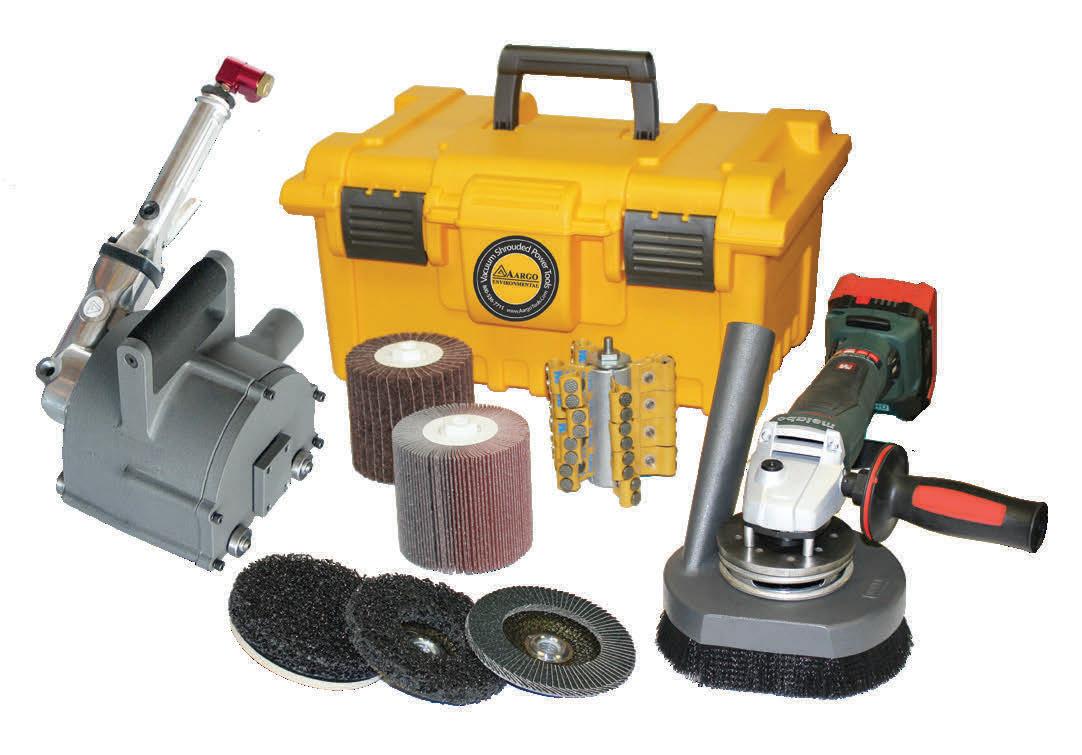

THE STORY: Aargo Environmental Inc. takes “women power” to a whole new level. The North Kingstownbased tool manufacturer is a Rhode Island-certified women’s business enterprise with 45 years’ experience in the industry. The company produces a line of dust-capturing, vacuumshrouded power tools and equipment for the abatement industry across the world.
› Among the tools Aargo produces are shrouded roto peens, sanders, grinders and needle guns with pneumatic, electric or cordless power. › Originally exclusive to the industrial sector, variations to these tools are increasing their popularity among residential contractors for their ability to grind, plane, resurface or remove paint, rust and other coatings. › The tools are made with aluminum shrouds that are powder-coated and machined to fit corresponding motors. › Each tool is hand-assembled by a single employee, taking one hour to assemble each tool. › Tools made by Aargo are used by industrial, commercial and residential contractors, as well as homeowners. › Aargo, responding to textile shortages due to the
COVID-19 pandemic, is currently working with Polaris
MEP, Rhode Island Small Business Development Center and R.I. Commerce Corp. to reposition and increase its manufacturing to establish a Made in the USA supply chain of nonwoven polypropylene material, needed to produce personal protective equipment.2020.
COVID-AFFECTED
While the company had an inventory of tools for sale, tool production at Aargo temporarily stopped due to the COVID-19 pandemic for several months. The company resumed production in fall 2020.
THINGS MADE HERE
TEXTILES

THE STORY: Athletes, along with being at their peak physically, need apparel to keep up with them at the same time. Westerly based Darlington Fabrics creates nylon and spandex fabrics for athletic attire, including team jerseys for prominent sports leagues.
› Darlington Fabrics produces a 100% recycled polyester warp knit tricot fabric that goes into NFL replica team jerseys. The company knits and dyes the fabric in every NFL team color. › The fabric has been in Darlington Fabrics’ line for eight years and between 3 million and 4 million yards are produced annually. › It takes approximately four weeks to make the fabric.
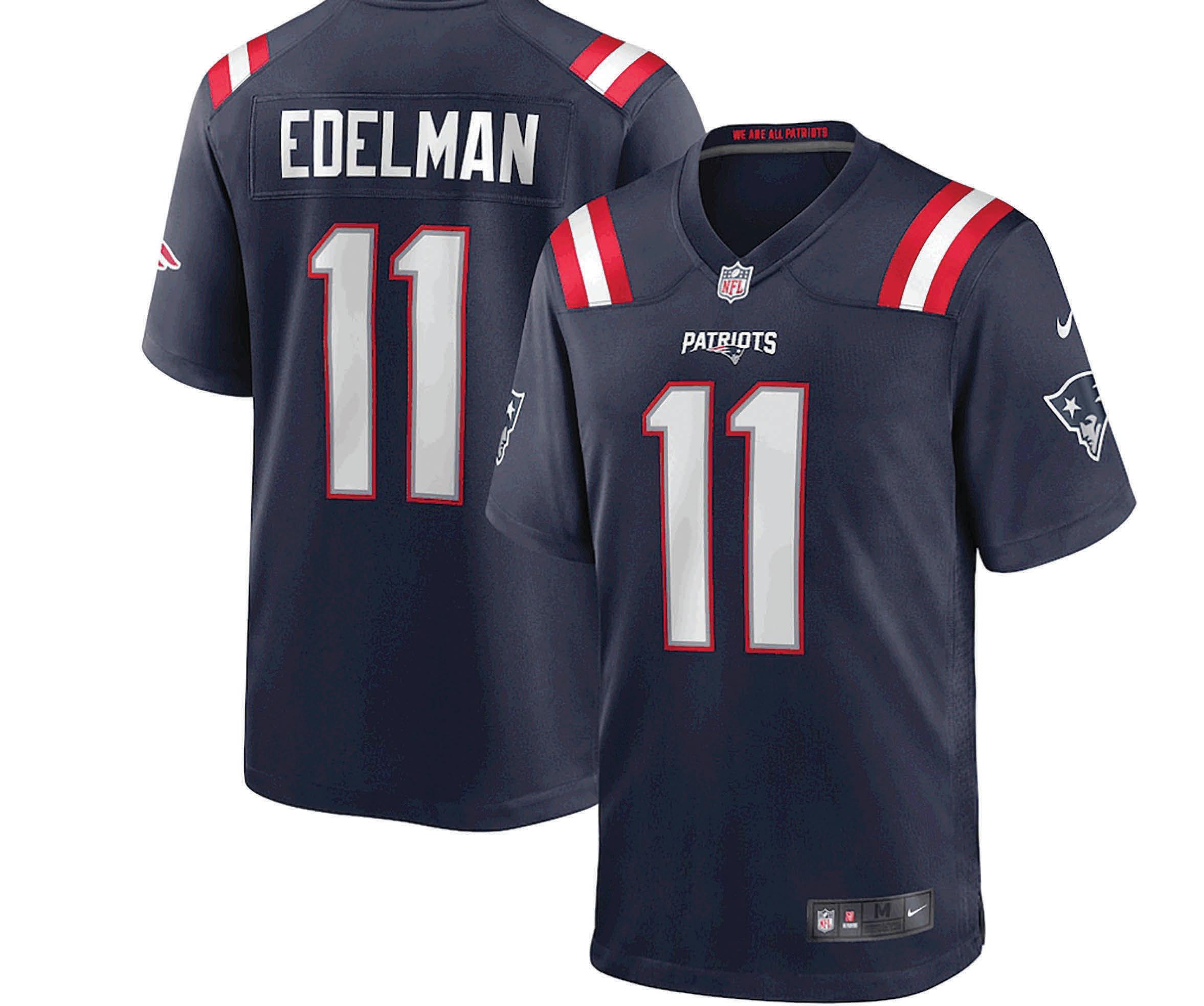
› Darlington Fabrics employs 150 people. › The company’s fabric is used in respiratory head gear that is used in conjunction with respirators for patients being treated in hospitals. Darlington
Fabrics was in this business prior to the pandemic, but has seen a spike in this business over the last six months.
COVID-AFFECTED
Production of fabric was suspended for two weeks in April 2020 due to orders being lean as a result of the COVID-19 pandemic.
› The SpeckJack Bungee Cord is made with a jacket of polyester or polypropylene. › The manufacturing technology allows greater control over density, stretch and jacket appearance of the ropes and cords. › The cords range in size of ⅛ inch in diameter to as thick as ¾ inch in diameter.
› Bungee cords are also made with a high-temperature neoprene core for such applications. The cords have a temperature range of up to 225 degrees Fahrenheit. › Neocorp has 22 employees working out of the 50,000-square-foot manufacturing facility in
Pawtucket.
COVID-PROOF
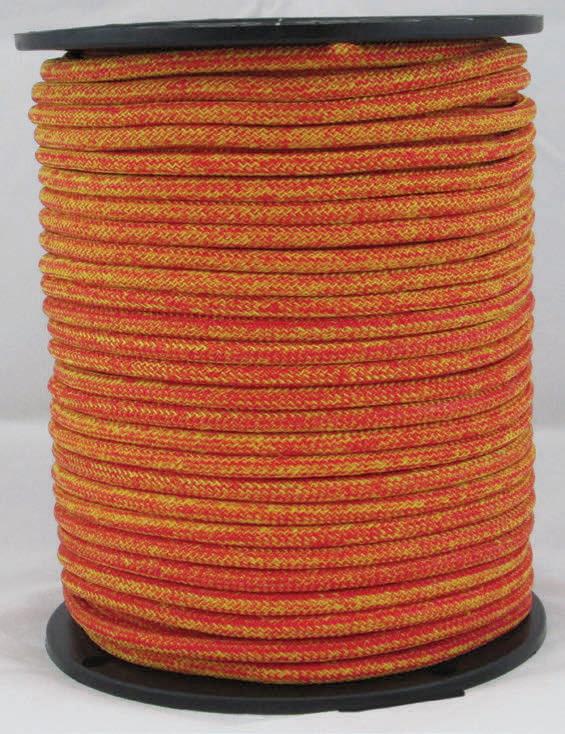
In the spring, Neocorp experienced a surge in orders for its smaller-diameter bungee cords. While not the traditional sizes and materials used for such applications, issues sourcing the usual materials resulted in the company working with numerous individuals and businesses to use its materials in a modified fashion. Through this, Neocorp found its way into masks and other face coverings, including face shields. THE STORY: A manufacturing staple in Rhode Island for more than three decades, Neocorp specializes in making solid braid-style ropes and bungee cords. Along with making hybrid products, Neocorp’s machinery can be reconfigured to fulfill custom orders.

THINGS MADE HERE
TECHNOLOGY
THE STORY: FarSounder Inc.’s products have been out on the high seas – literally. The Argos Forward Looking Sonar, made in Warwick, allows ships to navigate safely through oceans and other waterways.
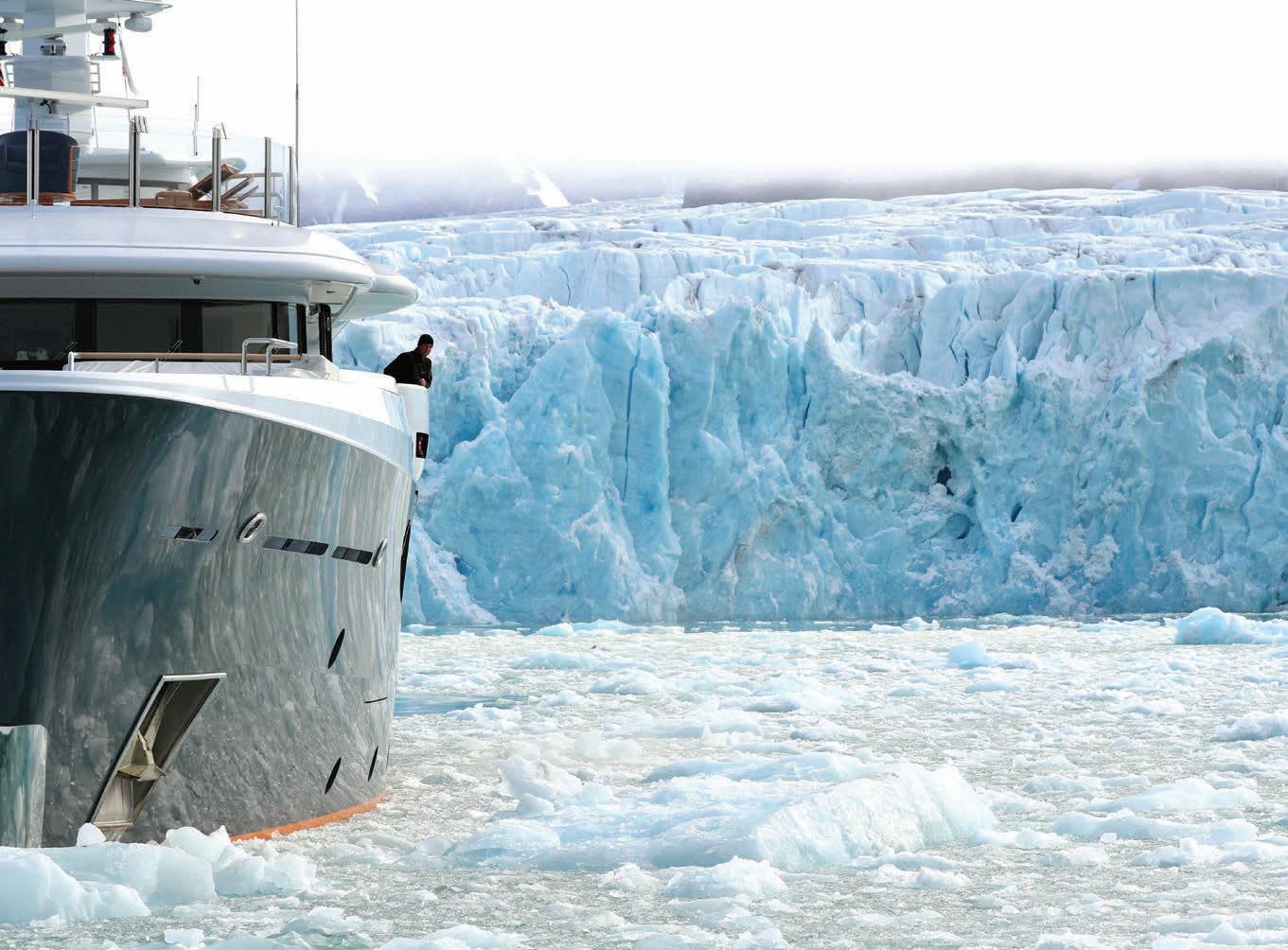
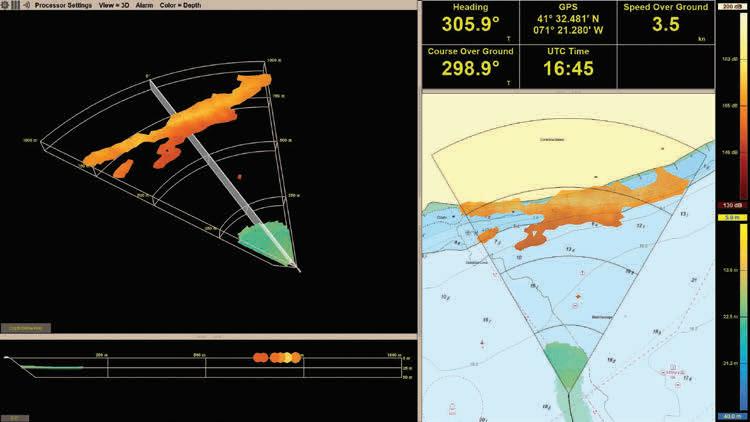
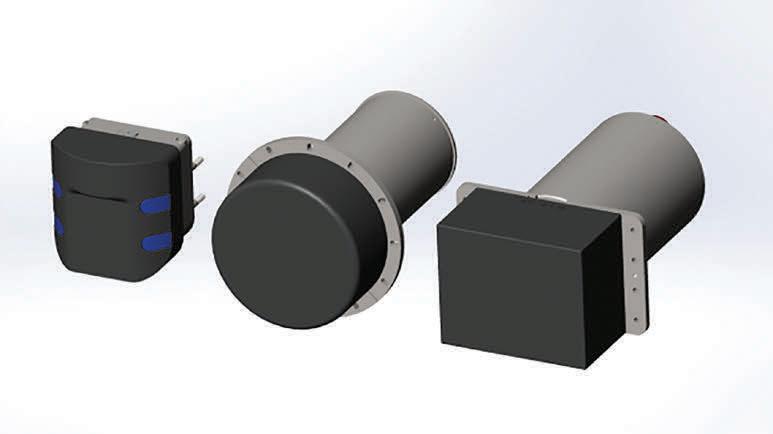
› The Argos series – the 350, 500 and 1,000 – are installed on all types of vessels from large cruise ships and super yachts to commercial vessels, such as survey and research vessels. › Each product costs between $55,000 and $180,000. › The sonar has a user interface showing 3D imagery in up to a 120-degree field of view out to significant ranges. They are made with a transducer module with advanced acoustic phased arrays, advanced analog and digital electronics, a custom cable and a processing computer, among other components. › It takes approximately three to four people about three to four days to assemble and test new sonars.
› FarSounder’s work has expanded into such areas as shipboard and portside security, marine mammal protection, fisheries, ocean sustainability and real-time mapping.
COVID-PROOF
Far Sounder has not closed during the pandemic and production of the series has continued throughout.
› The Two Wavelength Integrating Nephelometer, which is known as 2-WIN and came onto the market in 2016, measures visibility and pollution haze. It also can be used to help identify pollutant types and emissions sources. › The nephelometer is made with an active heating system, which is controlled based on relative humidity levels and warms the sample air and sample cell to keep the relative humidity below a set point to avoid particle growth with moisture. › Ambilabs sold approximately 20 nephelometers over the past year, with each system costing $20,000. It takes between three and four engineers between four and eight weeks to make each nephelometer from scratch. › The U.S. military, mining industry, health care industry, government agencies, environmental organizations, universities and research institutions use Ambilabs’ nephelometers. › The nephelometers could also become useful in the fight against COVID-19. The 2-WIN technology has the potential to help monitor bioaerosols and
Ambilabs is applying to federal government agencies to secure funding for further research and development.
COVID-PROOF
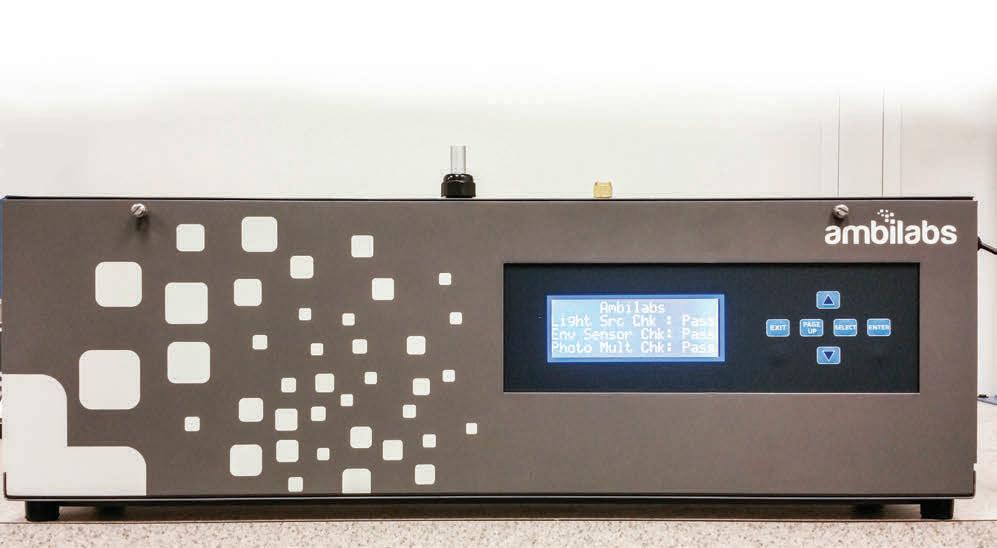
Production of the nephelometer has been uninterrupted during the COVID-19 pandemic. THE STORY: People, philosophically, always want to “clear the air.” Warren-based Ambilabs LLC is producing products to help make that possible. The company specializes in making air-quality instruments designed to provide accurate measurements of particle concentrations in the air. Among those products is the Two Wavelength Integrating Nephelometer.
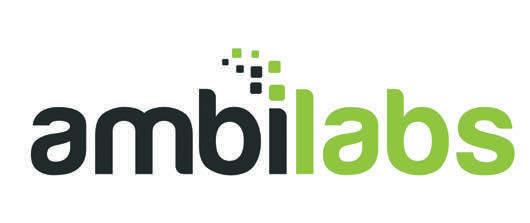