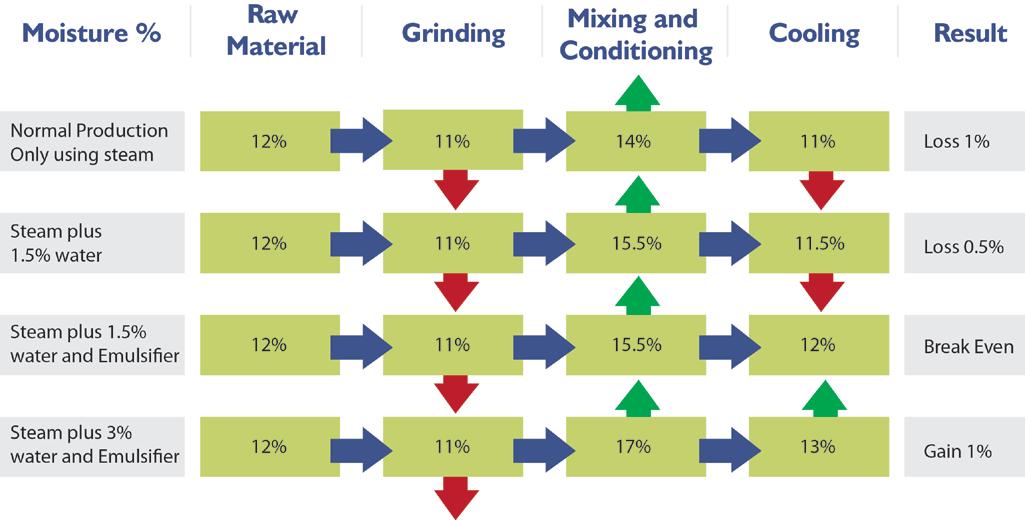
2 minute read
Increasing Production Efficiency by Managing Moisture and Microbial Risk in Feed Manufacture
By Lauren Judd, Product Manager Feed Additives, Trouw Nutrition GB
The use of surfactant additives in compound feed manufacture has the potential to improve efficiency of production and storage while contributing to the drive for reduced carbon footprints. They can be a valuable component of plans to unlock productive efficiencies.
Feed manufacturing businesses should be constantly striving to drive production efficiencies to reduce costs per tonne produced. At the same time, climate change legislation requires reductions in power usage by a further 6%.
Surfactants can have a significant role in three key areas of feed manufacture. By improving moisture retention they can improve the utilisation of raw materials and in addition prolong shelf life.
moisture retention
Loss of moisture is a cause of reduced yield of finished products, with commonly 2.5% moisture losses seen throughout the production cycle that have to be replaced. This means that for every 100 tonnes of raw materials, the yield of finished products is 97.5t.
Moisture in feed comes from the base raw materials, is added at mixing and then molasses and stream can be added at the conditioning stage. Between 0.5-1.5% moisture is typically lost in grinding and cooling. With raw materials accounting for around 80% of total feed production costs, taking action to reduce moisture loss will have an impact on potential profitability.
Adding moisture to compensate for losses can lead to quality issues, particularly if too much is added. If water is reintroduced before pressing, there is a risk of roller slippage resulting in poorer quality pellets.
The addition of Fylax helps to reduce extreme losses postconditioning. As a surfactant, it reduces the surface tension of moisture and helps achieve better dispersion throughout the compounding process. Moisture adheres better leading to reduced losses. While not eliminating moisture loss, Fylax helps flatten the moisture loss curve (see figure 1).
Fylax is a synergetic blend of organic acids and surfactants. It is produced using a technology that creates activated propionates. The activated propionates and organic acids effectively reduce moulds to guarantee the nutrient value and prolong the shelf life of raw materials and compound feed. The surfactants in Fylax have the ability to lower the surface tension of water, improving the products anti-mould effect as well as feed mill efficiency.
It is generally added in the mixer prior to the conditioner but this can depend on the precise set up of the mill.
Figure 1: Moisture losses in different processes
power savings
Feed manufacturers are faced with a continuing demand to reduce energy consumption. On most sites, the quick electricity savings have been made with future changes often requiring capital expenditure to achieve the reductions.
Adding extra moisture in the milling process comes with implications for power usage. Steam is generally cheaper than other methods, vaporising water droplets and gelatinising starch to hold pellets together. If you are unable to use steam then you are reliant on friction and pressure to ensure pellet quality.
By reducing the surface tension of moisture, Fylax ensures water is better dispersed and absorbed resulting in reduced power usage and a better quality product.
Figure 2, based on data from eight commercial trials, shows the effect of the addition of Fylax on energy use and mill throughput with a 22.1% reduction in kW/t.
mould inhibition for increased shelf life
If moisture is added to feed to enhance conditioning, the presence of moulds is inevitable. Mould growth will negatively affect the nutritional