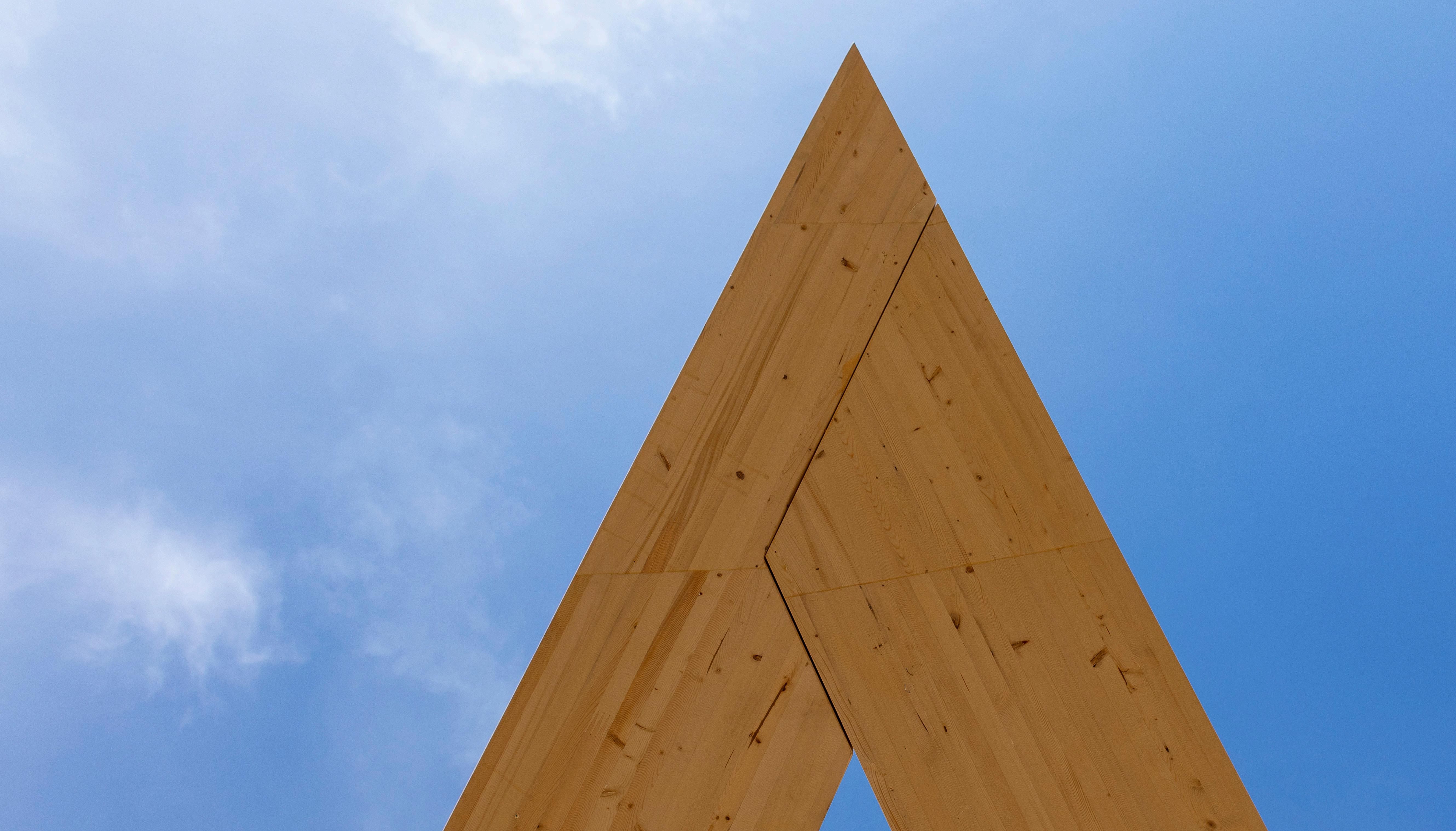
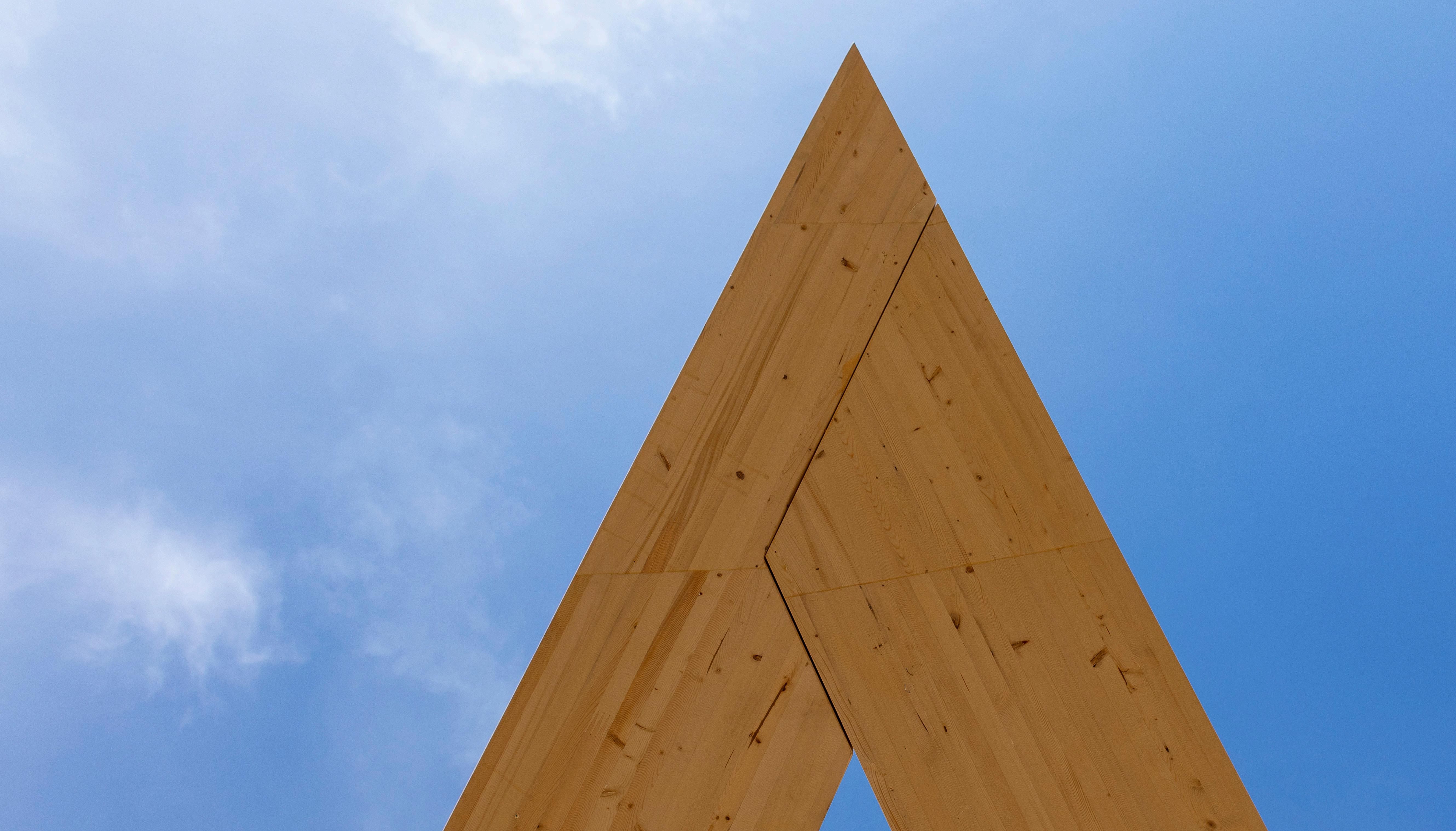
Getting to Craft in Mass Timber Design
A Guide for Project Teams
Prepared by Perkins&Will Building Technology Lab
V3.0 Released October 2023
Cover Photo: 1 De Haro. Image credit: Kyle Jeffers
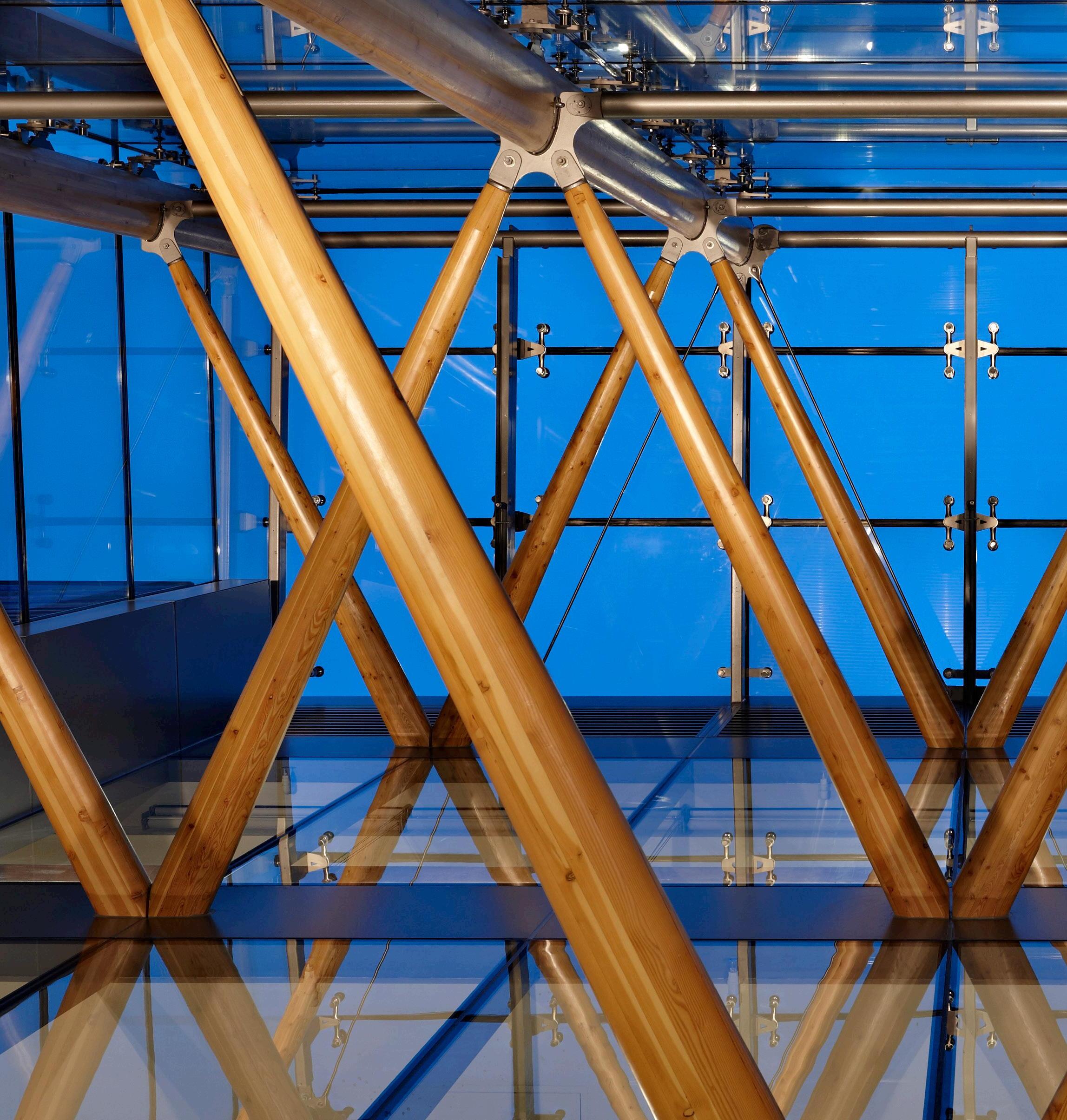
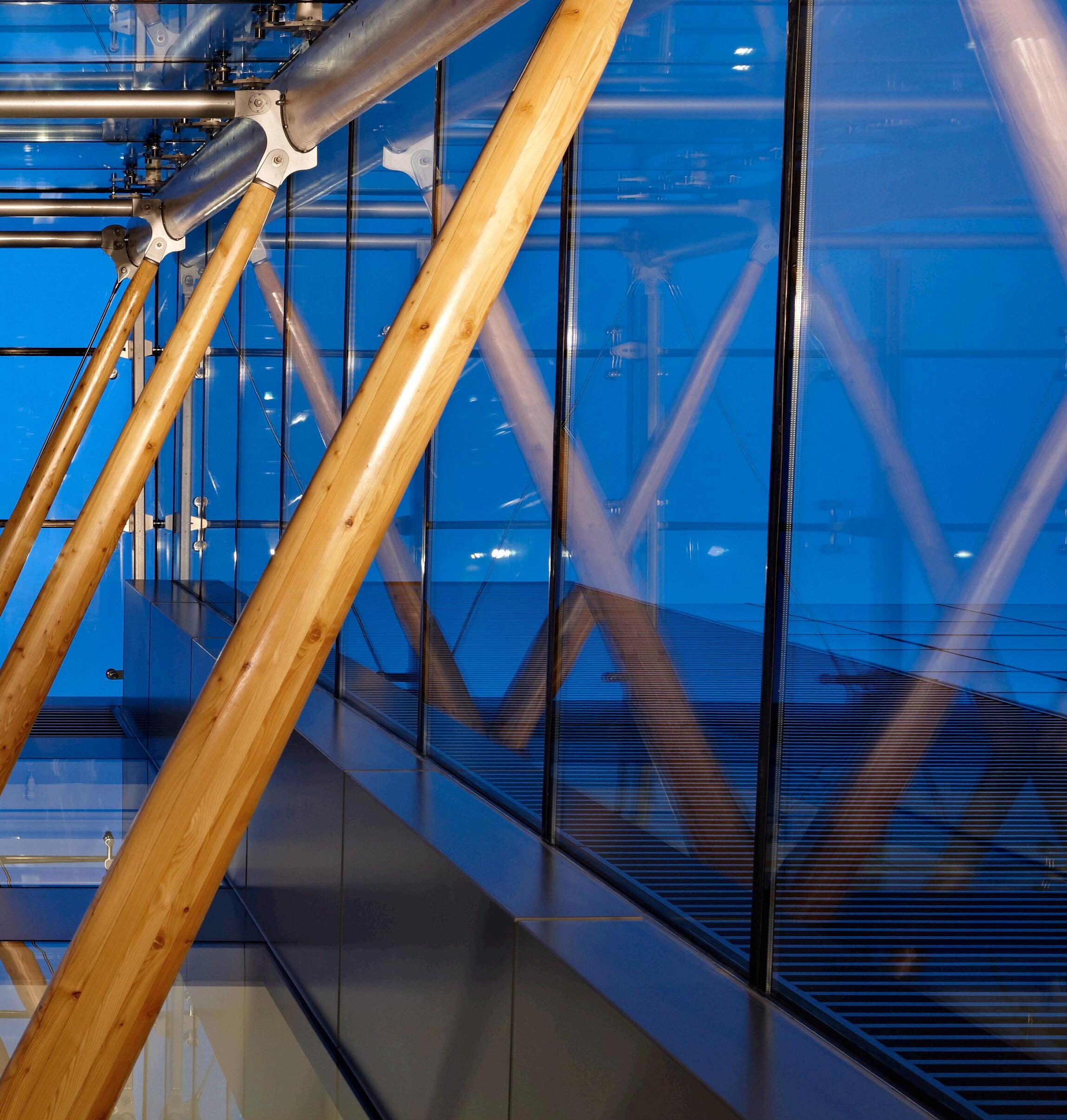
The expanding world of mass timber projects provides stunning examples of built work and offers fertile ground for design innovation. Our clients and partners are eager to work with us on exploring what mass timber can offer.
Getting from the initial excitement of a mass timber project proposal to the completed project requires many decisions to be made, often in unfamiliar territory. The uncertainty that we carry into this territory combined with the risk aversion of our clients and builder partners can hinder our boldest designs and can leave the wood uncrafted, and its potential unexplored.
This guide aims to help you and your project team decide whether mass timber is the right material for your project. In addition, the guide seeks to propel your team past many of the typical stumbling blocks of mass timber efforts so that the team can spend its energy on the design vision and expression of the material rather than on justification of the material to various stakeholders.
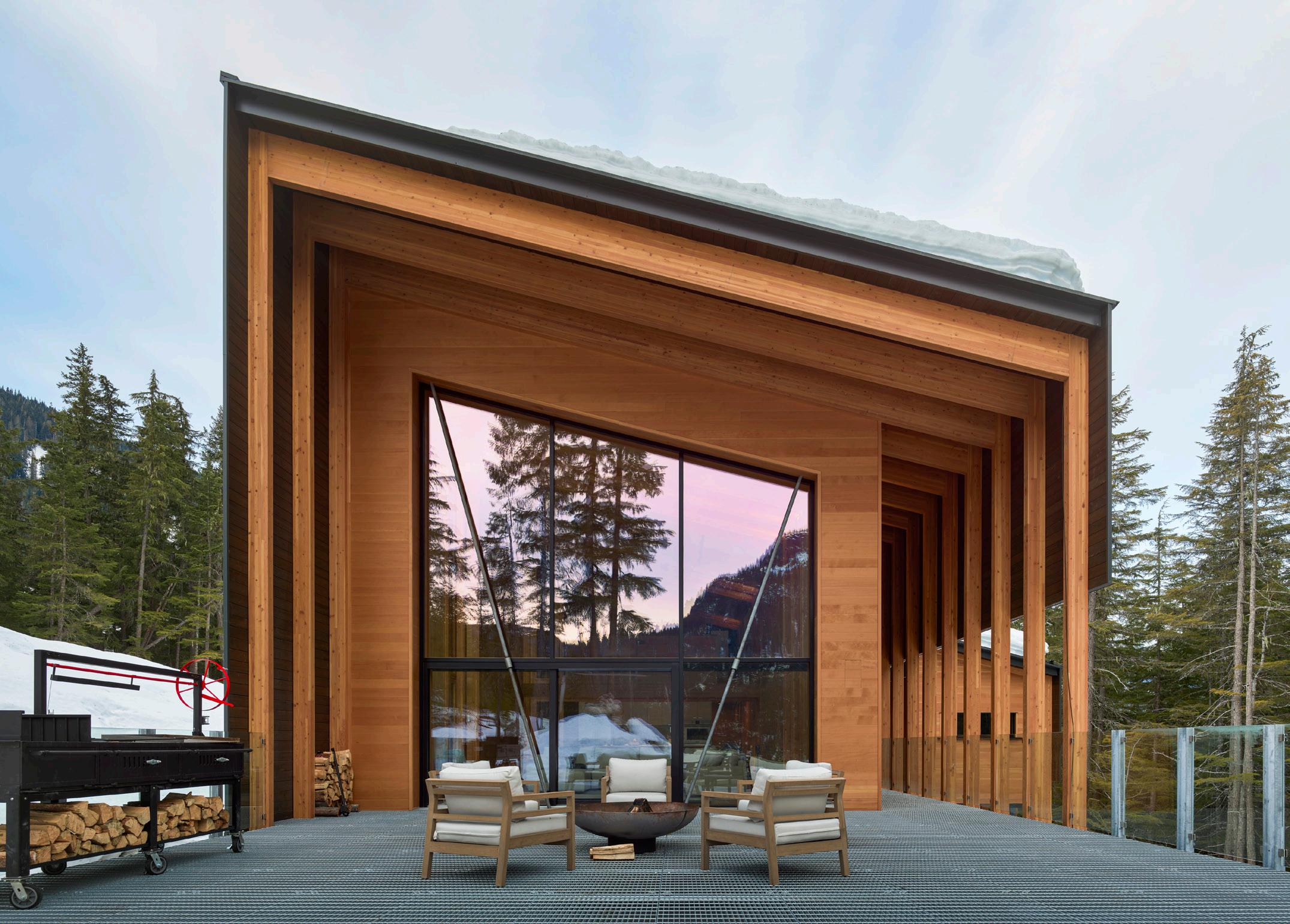
Soo Valley Prototype Home, BC
With over 25 built mass timber projects of significant scale in a variety of sectors, Perkins&Will’s expertise runs deep. We have a team of experts involved in mass timber research and code-writing, as well as a global network of partners. To assist with bringing the unique aspects of mass timber project design and delivery into focus, we have included in this guide case studies from several instructive completed projects.
Recent building code updates reflect the building industry’s bolstered confidence in mass timber. Canada’s 2020 National Building Code allows up to 12 stories of mass timber construction. The United States’ 2021 International Building Code prescriptively allows up to 18 stories of mass timber. The transnational document, NFPA 5000, was ratified in late summer 2020 and allows heights and areas greater than or equal to the 2021 IBC.
Despite the growing energy behind the mass timber industry, we acknowledge that many projects are not suited to mass timber for a variety of reasons - code limitations, delivery model incompatibility, inexperience of local builders, economics, material sourcing, etc. In addition to these factors, our ambition to promote sustainable materials will not always point to mass timber as a preferred material. In fact, without proper forest management, a wood building is no better for the environment than a building made of other materials.
For this reason, we begin our guide with a look at the carbon cycle of wood products and the role we play as designers in protecting the earth’s resources. Our mass timber work can make a difference as we demand transparency from mass timber suppliers and specify products that exist within healthy-earth carbon cycles.
With the right combination of partners, material sourcing care, and design vision, a mass timber project can raise the bar in our portfolios, in the cities in which we work, and in the interconnected ecosystem of our planet.
Let’s craft that future together.
Andrew Tsay Jacobs Ksenia Garrett
Jesce Walz
Mahdiar Ghaffarian
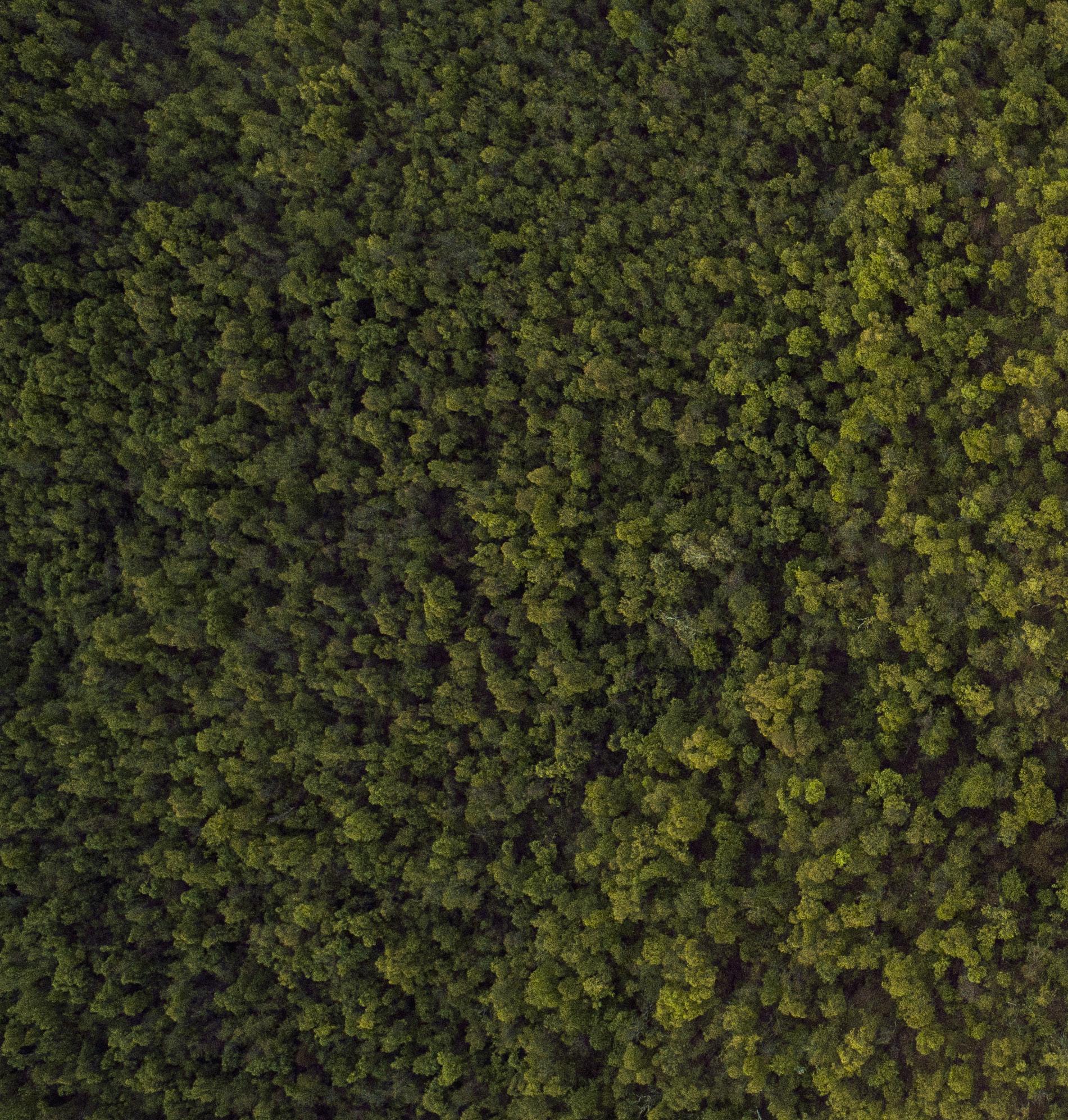
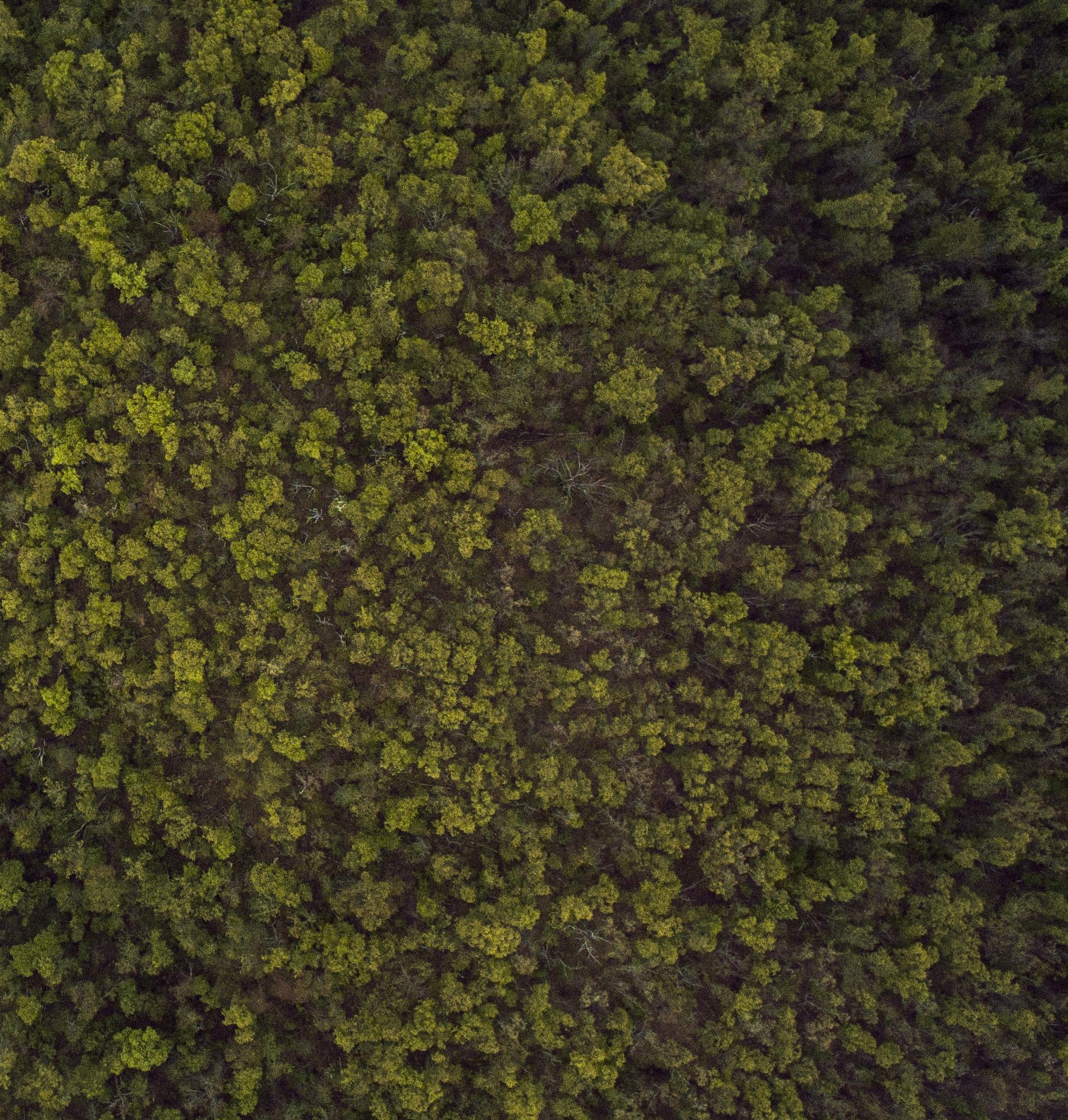
The Cycle, System, and Scale of Mass Timber
Craft in mass timber represents an opportunity to engage the cycle, system, and scale of a living material.
Timber production is intrinsically bound to forest ecology. The forest’s natural cycle is a closed loop: diverse, evolving, growing, decaying, and perpetually providing our planet with life. Humans’ relationship to this ecosystem is ancient. Over time, we have come to understand the forest as a source of life, protection, heat, nourishment, inspiration, and more recently, product and profit.
Today, through a system of harvesting, milling, manufacturing, and distribution, trees are transformed from roundwood into mass timber products. Yet timber is more than a product. It is the only primary structural material approved by the International Building Code that is also derived from a living carbon sequestering resource.
The scale of the building industry’s engagement with mass timber as a structural material is set to increase exponentially in the coming years. As this expansion occurs, transparent and responsible forest management and procurement practices will be crucial to utilizing wood as both a product and a part of a regenerative cycle. The design and development community can exhibit leadership by pairing mass timber design with a holistic understanding of this material’s physical nature and ecological context.
The first step to engaging timber’s regenerative potential is understanding suppliers, the supply chain, and forestry practices. However, the timber supply chain can be complex, so responsible procurement requires time and commitment. Certified timber usually also increases cost, as best management practices and certification require resources to achieve. Project teams must set an expectation in conceptual design that timber products will be derived from responsibly managed sources and follow through with this expectation in specifications and procurement.
The building industry’s collective decisions about how timber is procured today will determine whether we utilize this critical ecological resource in a way that leaves trees with a viable forest and humanity with a viable future.
Designing with Disruption
While the preservation of forest land is crucial to a healthy ecology, disruption is an inherent part of the forest cycle. Human engagement with ecology is also characterized by disruption. The impacts we have on our ecosystems are dependent not on whether but on how we embody our role as disruptors. Disruption is part of life and can instigate new growth, just as it can cause catastrophic failure. When a project team specifies any building material that is extracted from an ecological context, that team has an opportunity to design for a circular pattern of disruption.
Forests are always fluctuating and are both sources of carbon emissions and sinks for carbon storage. Fire, blight, and extraction are all forces of disruption that result in carbon emissions. However, land-based ecosystems currently sequester and store approximately 30% of global anthropogenic carbon emissions (1). The physical area of forested land in any region is impacted over time by various factors that include:
• Age and distribution of trees
• Management practices
• Environmental factors (fire, blight, drought)
• Land use change (development, mining, livestock, agriculture)
There is potential to sequester and store more carbon through the expansion of forest land. The greatest threat to that potential is a linear pattern of disruption: land use change. Land use change and its associated impacts are the second-largest contributor to global anthropogenic emissions after burning fossil fuels (2). Conversion of forest land to other uses is also the primary driver of deforestation.
Teams that procure legal wood from regions with stable or increasing forest stocks and sound land management regulations (e.g., North America) can support a managed forest cycle where the disruptive act of harvesting trees is coupled with replanting and comprehensive planning for ongoing management. Teams that go further, requiring certified wood and/or more information on source forests, can support best management practices to promote biodiversity, watershed health, resilience, and more. In either case, sustainable timber procurement helps to prevent land-use change by providing suppliers with incentives to manage, maintain, and even increase forest land, fostering the forest’s capacity to support life.
Sources of Anthropogenic Emissions Include:
Burning Fossil Fuel, Building Operations, Cement & Other Manufacturing, Transit Construction, and Land Use Change.
HUMANACTIVITIES
Land Plants
BIOSPHERE
Animals & Microorganisms
Soil Formation SOIL
ATMOSPHERIC CARBON
The context of the carbon cycle.
The carbon cycle illustrates an inventory of the location of carbon dioxide (CO2) within our planet's carbon pools. The impact of removing CO2 from the atmosphere depends on exchange and time.
Exchange: Forests sequester and store carbon, cycling it from the atmosphere to the biosphere to soil carbon, and back. Land use change and poor management practices break this cycle. Best management practices and market demand can support it.
Time: One tonne of carbon must be stored for at least 100 years to neutralize 1 tonne of today's GHG emissions (3). Longevity of use and opportunity for reuse are essential factors for maintaining and increasing storage of carbon in timber products.
Can forest land keep up with global demand for materials?
As design with mass timber becomes more common, increased demand for wood products may correlate with a gradual increase in forest land to meet demand. However, this outcome isn't certain. Best management practices and policies will be required to sustain and increase supply of wood (5); it is necessary for project teams to set clear expectations for transparency in mass timber procurement.
The International Organization for Standardization provides one example of guidance to account for wood harvested for products that originates from “sustainably managed forests.” Per ISO 21930, a wood product that wishes to claim carbon sequestration and storage benefits (6) must be sourced from either:
1.
Certified forests or mills.
Certifications offered by Forest Stewardship Council (FSC), Sustainable Forestry Initiative (SFI), Programme for the Endorsement of Forest Certification (PEFC), Canadian Standards Association (CSA), American Tree Farm System (ATFS), and others can provide teams with a base level of assurance that a project’s timber comes from legally harvestable sources with responsible forest management practices (7). Certification supports maintenance and improvement of forested land and is essential if a project is considering procuring timber from a region where forest land is decreasing over time. While many efforts are underway to improve the transparency of timber sourcing, at present, certification is the most direct pathway for teams to validate the sustainability of a project's timber.
2. Stable or increasing forest carbon stocks based on reporting.
Data from the United Nations Framework Convention on Climate Change (UNFCCC) National Inventory Reporting shows that in much of Europe and North America, the net carbon flux from forestry is relatively stable (8). However, forest land is shrinking in many regions of the world, and long-term stability is not guaranteed in any region due to increased demand for timber and confounding factors like wildfire and blight. Additionally, regions the size of a large country like Canada or the US are not reliable indicators of localized forest health or biodiversity.
Either certification or a thorough understanding of where a project’s timber comes from are the most reliable ways to ensure that management of source forests will support continued carbon sequestration and other ecosystem services.
Best practices for mass timber project teams
Significant points of leverage for forest advocacy through mass timber design include:
1. Consider salvaged wood and re-use: Is it possible to use reclaimed lumber or to reuse existing building components before procuring new products? This is the best way to ensure responsible sourcing and reduce a project’s carbon footprint.
2. Promote transparency: Require certification and/or other verifiable information about the management practices associated with each timber product's wood basket or even source stands. While traceability of wood sources is challenging, emerging efforts will make this more possible over time, and well-intentioned advocacy and dialogue can help.
3. Purchase direct from supplier: Some “vertical” suppliers fabricate timber from land that they own or control. Investigate options to purchase from a supplier or from a mill that can guarantee wood from a specific sustainable source.
4. Allocate funds for certified wood: Incorporate an allowance for certified timber in project budgets.
5. Design for longevity and circularity: Maximizing a building's service life and ability to be disassembled and reused in the future are key factors for maximizing the lifespan of carbon storage in timber products, preventing carbon stored in these products from being emitted into the atmosphere.
6. Design with the material: Explore options for fiber-optimized design and hybrid members; utilize different species for outer (aesthetic) and core (structural) laminations; specify products such as wood fiber insulation made of chips, residuals, and pulp.
7. Engage in disruption: Carbon sequestration is not the only factor to consider in sourcing timber. Using wood from forests that have experienced, or are prone to, fire or blight like beetle-kill can support restoration of a vulnerable ecosystem. Sourcing from drier regions may also incentivize development of mills where infrastructure is lacking.
CARBON UPTAKE & STORAGE
Forest + Harvested
Wood Carbon
Pools by Percent
Aboveground Biomass:
Living forest above the soil (~26%)
Belowground Biomass:
Live roots (~5%)
Dead Wood (~5%)
“Natural” Forest Carbon Cycle
Litter Biomass (~6%)
CARBON RELEASE (fire, decomposition)
DISTURBANCE
Soil: Organic (~10%)
Soil: Mineral (~44%) - most of the forest’s carbon is stored in its soil. Even the best biogenic carbon methodologies do not include soil carbon, so this benefit may be under-counted. If forest is converted to other land use, soil carbon may be released into the atmosphere as land is excavated or tilled.
Data on forest and timber carbon pools is rounded to the nearest %, from the US EPA GHG Inventory (8)
RESILIENCE
The forest's carbon cycle extends below the surface. Forest soils filter and distribute water, store carbon, recycle organic matter and nutrients, and provide habitat for a myriad of organisms.
Forest + Harvested
Wood Carbon
Pools by Percent
Aboveground Biomass:
Living forest above the soil (~26%)
Belowground Biomass:
Live roots (~5%)
Dead Wood (~5%)
Managed Forest Carbon Cycle
Litter Biomass (~6%)
Product Stage:
Raw Material - A1
Transport to Mill - A2
Manufacturing - A3
Construction Process Stage:
Transport to Site - A4
Construction / Installation
Process - A5
Use Stage: Timber Products in Use (~3%) - this pool continues to grow as wood products enter and remain in use
Soil: Organic (~10%)
Soil: Mineral (~44%) - most of the forest’s carbon is stored in its soil. Even the best biogenic carbon methodologies do not include soil carbon, so this benefit may be under-counted. If forest is converted to other land use, soil carbon may be released into the atmosphere as land is excavated or tilled.
Data on forest and timber carbon pools is rounded to the nearest %, from the US EPA GHG Inventory (Ibid)
Replanting & Management
Reuse: a second life maximizes timber carbon storage
End of Life Stage:
Deconstruction/Demolition - C1
Transport to processing - C2
Waste Processing - C3
Disposal - C4
Best management practices and demand for sustainable timber can decrease the risk of natural and human induced disturbance and contribute to stable or growing forest stocks.
! Land use change is a disturbance that breaks the natural AND the managed forest carbon cycle and is the second largest contributor to anthropogenic carbon emissions (9).
Impacts from disposal of timber products vary, and include combustion from biomass, emissions from recycling, and methane leakage from solid waste
SWDS: Solid Waste Disposal Sites (~2%) - up to 88% of carbon from landfilled dimensional lumber is stored permanently (10).
Benefits & Loads Beyond the Building Life Cycle (Module D): Reuse, recovery, recycling, exported energy, etc.
Timber Product
Life Cycle
Normalize Dialogue
As design teams work to popularize the use of mass timber, the industry must simultaneously increase dialogue about sustainable sourcing. Conversation between teams, project owners, and timber suppliers is essential to ensuring sustainable wood sourcing, from early cost estimation through specifications and procurement.
While obtaining certified or other sustainably sourced wood will take time and may add to a project’s costs, the gravity of transparency and the importance of keeping forests functioning as forests cannot be overemphasized. Circular forestry practices are in the best interest of project teams, the timber industry, and ecology alike, as they ensure long-standing availability of resources for all.
As a product and a compelling building material, mass timber invites teams to engage in a deep understanding of the forest as a crucial resource and to participate in stewardship to ensure a stable supply chain and ecological health for decades to come.
Resources
The "08 - Sustainable Sourcing" section of this guide provides resources to support sustainable forestry and timber sourcing. In addition, the following resources may be useful:
• Tallwood Design Institute's "Sustainability and Environment" Research (11)
• "Forest Certification Update 2021: The Pace of Change." Dovetail Partners (12)
• "Wood Carbon Seminars," Carbon Leadership Forum (13)
• "Carbon Narratives for Design Planning" series, The Institute for Health in the Built Environments (14)
• The Climate Smart Wood Group (15)
• Work by David Diaz of Ecotrust and partner organizations to assess the carbon and other ecological impacts of forestry management (16)
Climate Responsibility References
1. "Land-Based Solutions Offer a Key Opportunity for Climate Mitigation". UNCCD, 2023. https://www.unccd.int/news-stories/stories/land-based-solutions-offer-key-opportunity-climate-mitigation
2. "Global Greenhouse Gas Emissions Data | US EPA". US EPA, 2016. https://www.epa.gov/ghgemissions/global-greenhouse-gas-emissions-data.
3. Compagnon, Thibault. "Reductions or Removals? Why Science — Not Just Market Forces — Must Shape Our Pathway to Net Zero". Quantis, 2020. https://quantis.com/why-science-not-market-forces-must-shape-our-pathway-to-net-zero
4. "Global forest sector outlook 2050: Assessing future demand and sources of timber for a sustainable economy – Background paper for The State of the World’s Forests 2022. FAO Forestry Working Paper, No. 31. Rome". FAO, 2022. https://doi.org/10.4060/cc2265en.
5. “Sustainability in buildings and civil engineering works — Core rules for environmental product declarations of construction products and services”. ISO 21930:2017, section 7.2.7. 2023. (Current, reviewed and confirmed in 2023)
6. Certain factors associated with forest management are not well understood, such as the impacts of logging on soils, ideal time spans between planting and harvest to maximize ecosystem health, and protection of sensitive ecologies like riparian zones. Certification standards are one verified path to address these and other factors.
7. “United Nations FCC International Council on Climate Change, National Inventory Submissions 2023”. Unfccc.Int., 2023, https://unfccc.int/ghg-inventories-annex-i-parties/2023.
8. Data on forest and timber carbon pools pulls from the EPA's "Inventory Of U.S. Greenhouse Gas Emissions And Sinks: 1990-2018 | US EPA". US EPA, 2020. This data and forest carbon are also well explained in this report: Hoover, Katie, and Anne A. Riddle. "Forest carbon primer." Congressional Research Service: Washington, DC, USA, 2020. https://crsreports.congress.gov/product/pdf/R/R46312
9. "Global Greenhouse Gas Emissions Data | US EPA". US EPA, 2016. (n 2)
10. "Documentation for Greenhouse Gas Emission and Energy Factors Used in the Waste Reduction Model (WARM)". US EPA, 2019. https://www.epa.gov/sites/default/files/2019-10/documents/warm_ v15_management_practices_updated_10-08-2019.pdf
11. “Sustainability and Environment”. TallWood Design Institute, tallwoodinstitute.org/sustainabilityresearch/. Frequently updated timber research repository featuring topics like design for disassembly and reuse, carbon studies, and explorations of innovative assembly and manufacturing techniques.
12. Fernholz, Kathryn, et al. "Forest certification update 2021: the pace of change". Dovetail Partners, 2021. https://dovetailinc.org/upload/tmp/1611160123.pdf
13. "Wood Carbon Seminars - Carbon Leadership Forum". Carbon Leadership Forum, 2020, https:// carbonleadershipforum.org/wood-carbon-seminars
14. "Carbon Narratives for Design Planning". Institute for Health In The Built Environment, 2020, https://buildhealth.uoregon.edu/carbon-narratives-for-design-planning.
15. Climate Smart Wood Group, 2023, https://www.climatesmartwood.net. Includes guidance for sustainable wood procurement in North America. The group includes representation from FSC, but as of this publication, does not include representation from other forest certification entities.
16. Diaz, David D., et al. "Tradeoffs in timber, carbon, and cash flow under alternative management systems for Douglas-Fir in the Pacific Northwest". Forests 9.8 (2018): 447.
Additional forestry-related work from EcoTrust can be found at: https://ecotrust.org
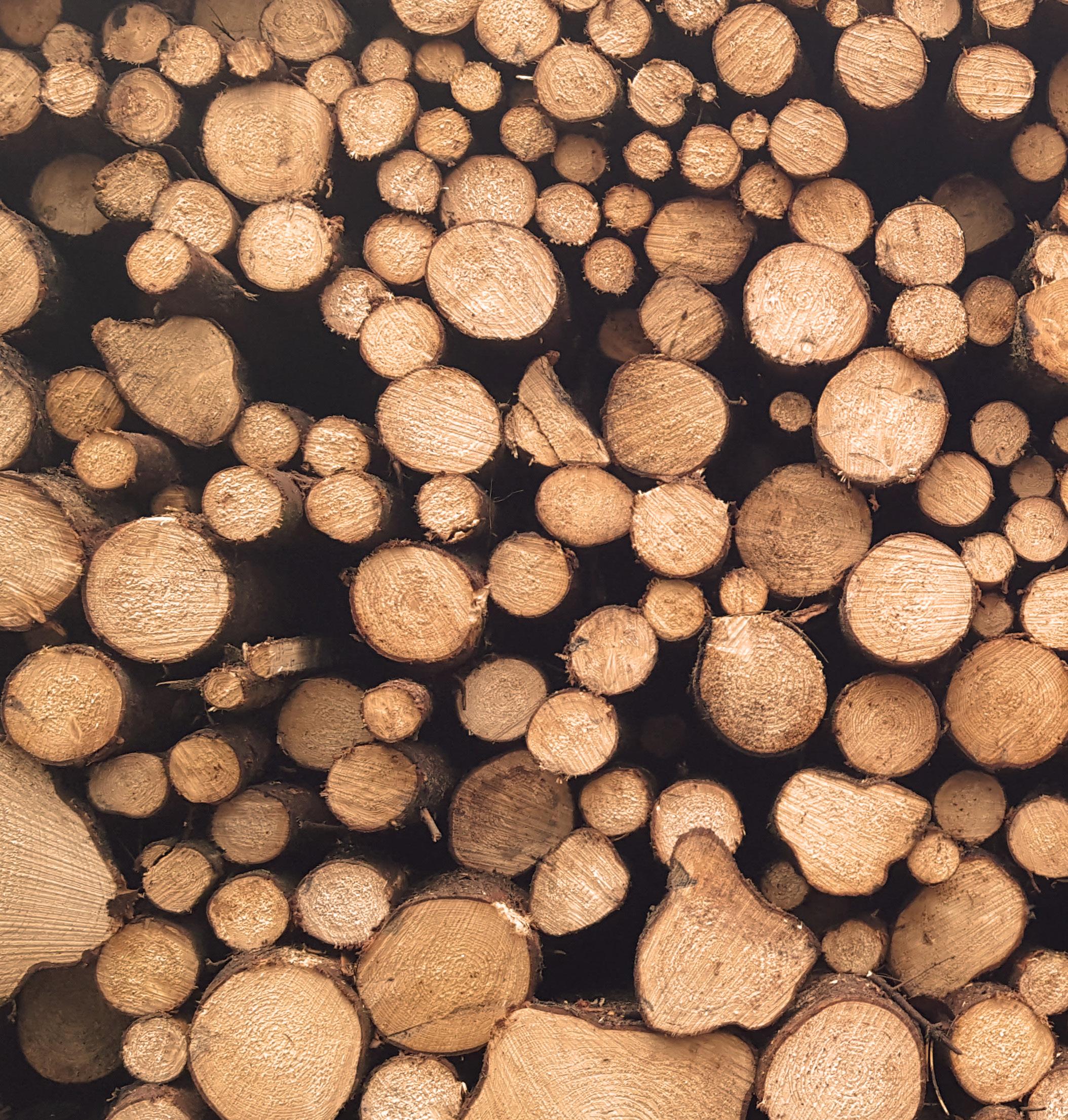
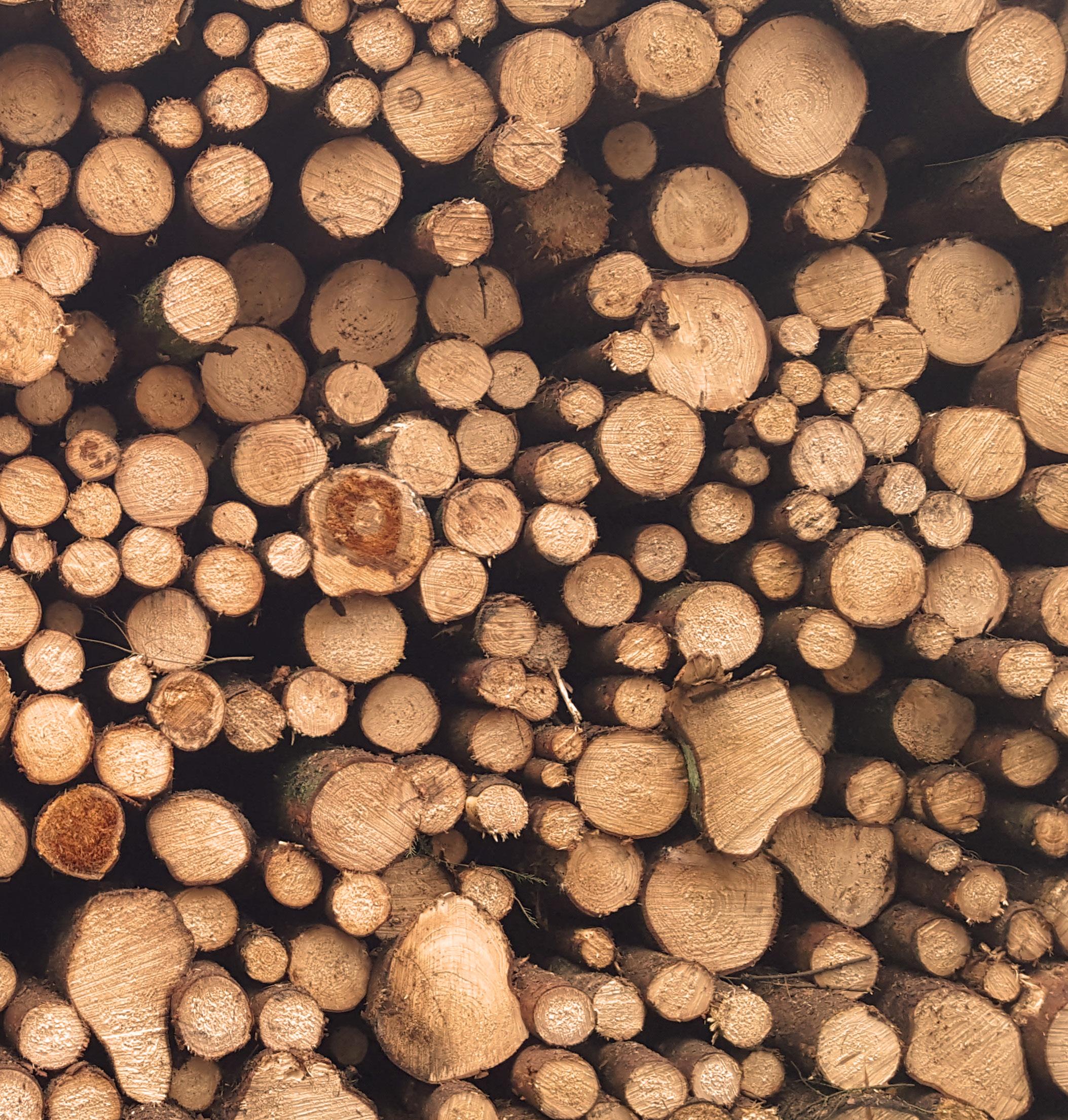
03 FRAMEWORK FOR SUCCESS
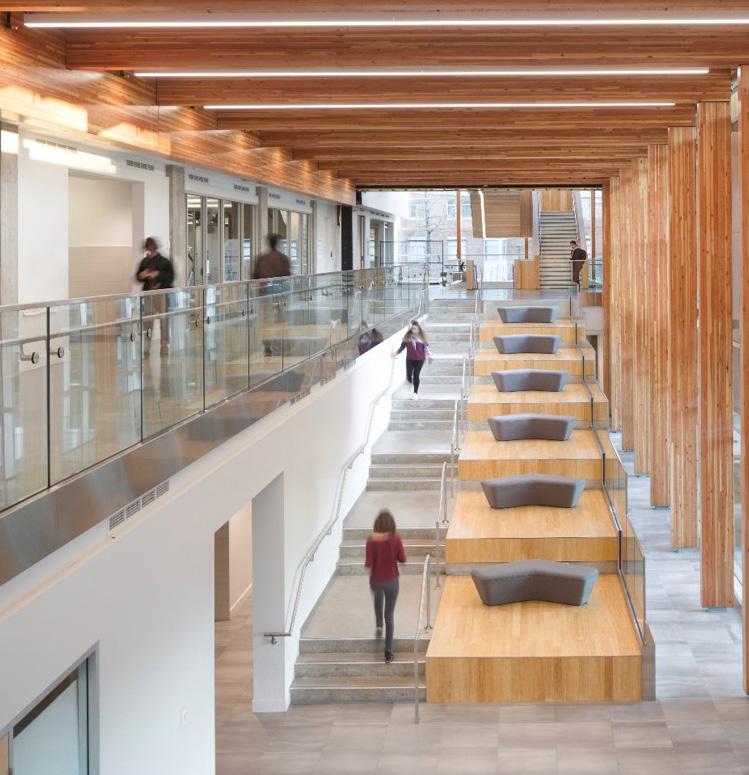
Orchard Commons, Vancouver, BC
Alignment with Mass Timber
Before we can execute a mass timber project, we need to identify a project that has strong potential to be a mass timber project. This identification process is achieved by looking for alignments with the prerequisites of mass timber.
Use the following diagram to help you consider the ways your current pursuit is aligned or not aligned with the typical hallmarks of a successful mass timber project. Where it is aligned, use the diagram to help you leverage that alignment. Where it is not aligned, use the diagram to consider ways to overcome alignment deficits.
The goal of this alignments exercise is to create a mental map of the framework and conditions in which mass timber is likely to thrive on a project. By becoming familiar with these key alignments, we can foster a deeper understanding of when to pursue mass timber.
existing project alignment with mass timber
Is there an opportunity to make mass timber an integral part of the design / design values?
Can SE develop innovative/elegant and cost-effective applications of mass timber?
Can CM and/or timber fabricator help ‘lock in’ mass timber for the project, and avoid the risk of carrying multiple structural strategies through SD/DD/and other phases?
project alignment with mass timber
Which side of the spectrum does your project (mostly) fall under?
Client is interested and/or project values align with mass timber
Structural Engineer has mass timber experience
Client
Client is not aware of mass timber.
Structural Engineer
Project team is able to engage a timber fabricator directly or through a Construction Manager
Are there any key project goals that can significantly align with mass timber? Refer to Section XX for mass timber benefits.
Structural Engineer is unknown, OR, SE is known but has no mass timber experience. If SE is unknown, will the selection process allow for pre-qualification based on timber experience?
If SE has no experience, is there an opportunity to bring on a timber fabricator in a designassist role?
Project Delivery Model
Project is a traditional design-bid-build with limited/no CM engagement
Is there an opportunity to connect with local mass timber fabricators and gauge their (competitive) appetite for a project of this scope?
Can GC describe cost/ schedule/site benefits to client?
What is the code threshold for mass timber on this project? And how far is the project from this threshold?
Is the local supply of mass timber cost-competitive?
GC has mass timber experience
Use of mass timber as the primary structure is allowable under current code provisions for this project
Local mass timber availability is known and understood.
Contractor
GC is unknown, OR, GC is known but has no mass timber experience
Code Compliance Material Sourcing
Use of mass timber is currently NOT allowed under current code provisions for this project
Material sourcing strategy is unclear/undefined
If your project falls mostly on this side of the spectrum, your project is well aligned with mass timber.
If GC is unknown, will the selection process allow for pre-qualification based on timber experience?
If GC has no timber experience, are they interested/eager to learn?
Will any of the upcoming code changes (North America - IBC, NBC) that expand the use of mass timber create a better opportunity for this project?
Have similar projects been completed in mass timber using an Alternative Solution? Is your code consultant aware of alternative solution strategies that fit this project’s criteria?
Are you able to connect with local mass timber fabricators to gauge their interest in this project?
If your project falls mostly on this side of the spectrum, keep seeking key project alignments with mass timber.
Mass Timber
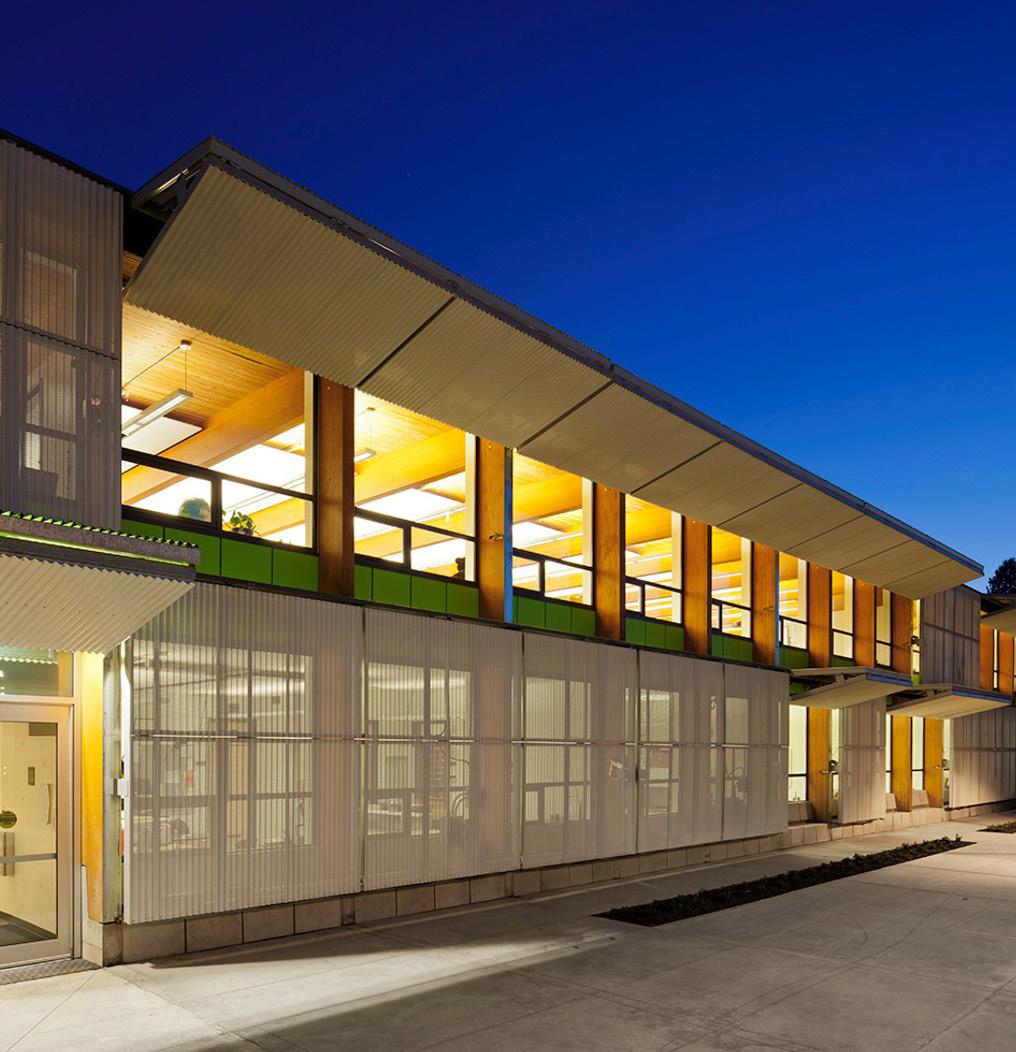
Pitt River Middle School, Port Coquitlam, BC
How do I decide whether mass timber is right for my project?
Assuming the project is well-aligned with mass timber, the shortest answer is that if the client, GC, SE all want mass timber, it is worth pursuing mass timber. If just one of those partners is not a proponent, the project will not likely become a mass timber project.
We as designers have the authority and responsibility to recommend the use of mass timber when it is the right choice for the project. However, the choice to use mass timber ultimately comes down to what you and your client are motivated to pursue. Helping a client select a GC and an SE who are experienced and who will earnestly support a mass timber vision can make all the difference.
The following worksheet comes in two parts. Part 1 is a Mass Timber Go-No-Go checklist that can assist with making a solid decision about whether the project should use mass timber as the structural material. Assuming mass timber is viable, Part 2 will help you ask some tough questions early and get the project off on the right foot. Answering the worksheet questions with your internal project team will establish the framework of strategies and alignments that you can leverage to deliver a successful project.
Go-No-Go Worksheet for Mass Timber
Date:
Project Name:
Project Number:
Project Lead / Workbook Participants:
The purpose of this worksheet is to assist project teams in evaluating if mass timber is a good fit for a project.
Use this worksheet before design starts.
Part 1 provides a high-level Go-No-Go checklist.
Part 2 outlines a list of key mass timber considerations for discussion.
Part 1: Which of the following conditions are satisfied / can be satisfied for your project?
1: Motivated client (min 1 yes) Yes/No Notes
1. Is your client aware of mass timber, and is interested in using it in this project?
2. If your client is not aware of mass timber, are there any key project goals that significantly align with mass timber? Refer to <a section that highlights key benefits of mass timber>
2: Experienced Structural Engineer (min 1 yes)
1. If the Structural Engineer is known:
2. Have they worked on mass timber projects before?
3. If yes, do these projects demonstrate an innovative and elegant application of mass timber?
4. Would they be interested in supporting a timber design on this project?
5. If Structural is not known: will the SE selection process allow for pre-qualifications based on timber experience?
3: Suitable Project Delivery model (min 1 yes)
1. Will this project involve a Construction Manager with mass timber experience?
2. Will this project be delivered in a design-build model?
3. Will the project team be able to engage a timber fabricator in a design-assist role (especially if Structural Engineer does not have significant wood experience)?
4: Experienced Contractor (min 1 yes)
1. If the General Contractor is known: have they worked on mass timber projects before? Would they be interested in supporting a timber design on this project?
2. If the General Contractor is not known: will the GC selection process allow for pre-qualifications based on timber experience?
5:
Ease of Code Compliance (min 1 yes)
1. Is mass timber on this project allowable under current code provisions?
2. If mass timber on this project is not allowable under current code provisions, is your code consultant capable of developing an alternative solutions strategy that meets the client’s project timeline?
6: Material sourcing strategy (min 1 yes)
1. Do you have a strategy to engage a mass timber supplier during design for early costing input?
2. Is your client comfortable with potentially sole sourcing mass timber?
TOTAL (min 6 points)
Work through Part 2 of this workbook and re-evaluate this section again.
PART 2: HOW DO I DELIVER A SUCCESSFUL MASS TIMBER DESIGN?
Have a conversation with your team about the following design and construction considerations:
DESIGN VISIONING:
1. Design vision:
a. List your client’s priorities
b. Do you foresee opportunities to develop a compelling project framework that inextricably links client priorities to wood?
c. When mass timber becomes a necessary element of the project’s values and design vision, you are more likely to execute on a wood project. Briefly brainstorm on a project vision within this framework.
2. Prefab proposition – design considerations:
a. Prefabrication is inherent to mass timber. What other building components can leverage prefab, beyond mass timber?
b. Which of the following potential benefits of prefab serves your client? Quality / tighter tolerances / higher performance / cost savings / schedule savings / off-site labor availability.
3. Co-author a parti with your Structural Engineer
a. Have you discussed the core competencies that are critical for mass timber? Prefab / mass timber product types / supplier know-how / high-level cost take-offs of comparative structural designs / long spans / lateral systems.
b. Design partis that can easily be converted to steel or concrete typically do not represent optimal use of mass timber. Describe how you will work with your Structural Engineer to develop a scheme that leverages the opportunities of mass timber - Refer to Chapter 5. (If mass timber is new to you, make sure you allocate sufficient time for this dialogue).
4. Code Compliance
a. The building code allows for a range of mass timber options. Describe the relevant mass timber code options and opportunities for this project.
b. Is there anything about your project that is not code compliant? If yes, describe simple trade-offs or design moves that can make the project code-compliant.
5. Fire protection – design considerations
a. Are you aware of all the fire protection and control strategies applicable for a mass timber building? Consider encapsulating vs exposing mass timber strategically to bring the most value to the project, and work within the constraints of fire protection requirements.
b. Are there any unique spatial configurations (atrium, interconnected floors etc) that may require additional fire/smoke modeling? If yes, can your code consultant/fire engineer support such explorations?
FABRICATION AND DETAILING CONSIDERATIONS:
1. Prefabrication proposition:
Mass timber structures are almost entirely fabricated off site in a factory setting. Will your General Contractor + Timber Installer team be able to leverage prefab to:
a. Shorten the construction schedule, allowing for early opening?
b. Provide construction cost savings? Or eliminate any construction cost premiums associated with mass timber? Consider impact on General Conditions (reduced on-site labor, reduced length of construction financing, earlier sign-offs, reduced deficiencies and more).
c. Other benefits: Reduce laydown areas on the site using just-in time delivery / quiet jobsite / incentives related to policy.
2. Acoustics
a. Does the project’s program have stringent acoustic requirements?
b. Mass timber floor assemblies do not inherently provide high IIC ratings. Are you aware of all acoustic treatment options that are compatible with your design? Refer to CLT Handbook or NLT Guide.
3. Vibration
a. Is your Structural Engineer aware of measures that can be taken to mitigate floor vibration or sitespecific external vibration? Refer to CLT Handbook.
4. Early Systems Coordination:
a. Mass timber requires integrated design and project delivery. What scheduling tweaks can you implement to allow for early engagement with the timber fabricator and other key trades (Steel connection supplier, Mechanical, and Façade)?
JOBSITE STRATEGIES:
1. Durability
a. Termites are generally not a problem for mass timber. Is your client concerned about termites? If yes, have you considered a concrete base at grade to mitigate this concern?
b. Untreated wood exposed to sunlight may change color over time. Discoloration does not impact the performance of mass timber. Describe how you would weave this aspect of mass timber into the project’s story? (Alternately, if color consistency is important for your client, what finish treatments can you propose to protect exposed wood? Refer to Chapter 5.)
2. Water and moisture management - Design considerations
Will your design team and Envelope Consultant be able to address the following:
a. Sequencing of membrane application to avoid wood wetting on site, or condensation during life cycle of building.
b. Protecting exposed exterior wood elements for the life of the building. Refer to Chapter 5.
c. Protecting mass timber in wet program areas through multiple strategies (For example: floor drains in bathrooms, water monitoring system).
3. Water and moisture management – construction considerations:
a. Do you anticipate construction to occur in a wet weather season? If yes, will your Timber Installer + General Contractor team be able to develop a robust weather protection strategy (For example: factory-applied membrane on timber panels, tape edges and joints during install of panels, rapid envelope enclosure, tenting the site. Refer to CLT Handbook, NLT Guide and Technical Guide to Tall Wood Construction).
4. Fire protection – construction considerations:
a. Is your General Contractor aware of fire protection and control requirements during construction of a mass timber building in the project’s jurisdiction? Consider sprinkler provisions, rapid enclosure of building.
Upon completion of Part 2, revisit Part 1 and re-evaluate your responses.
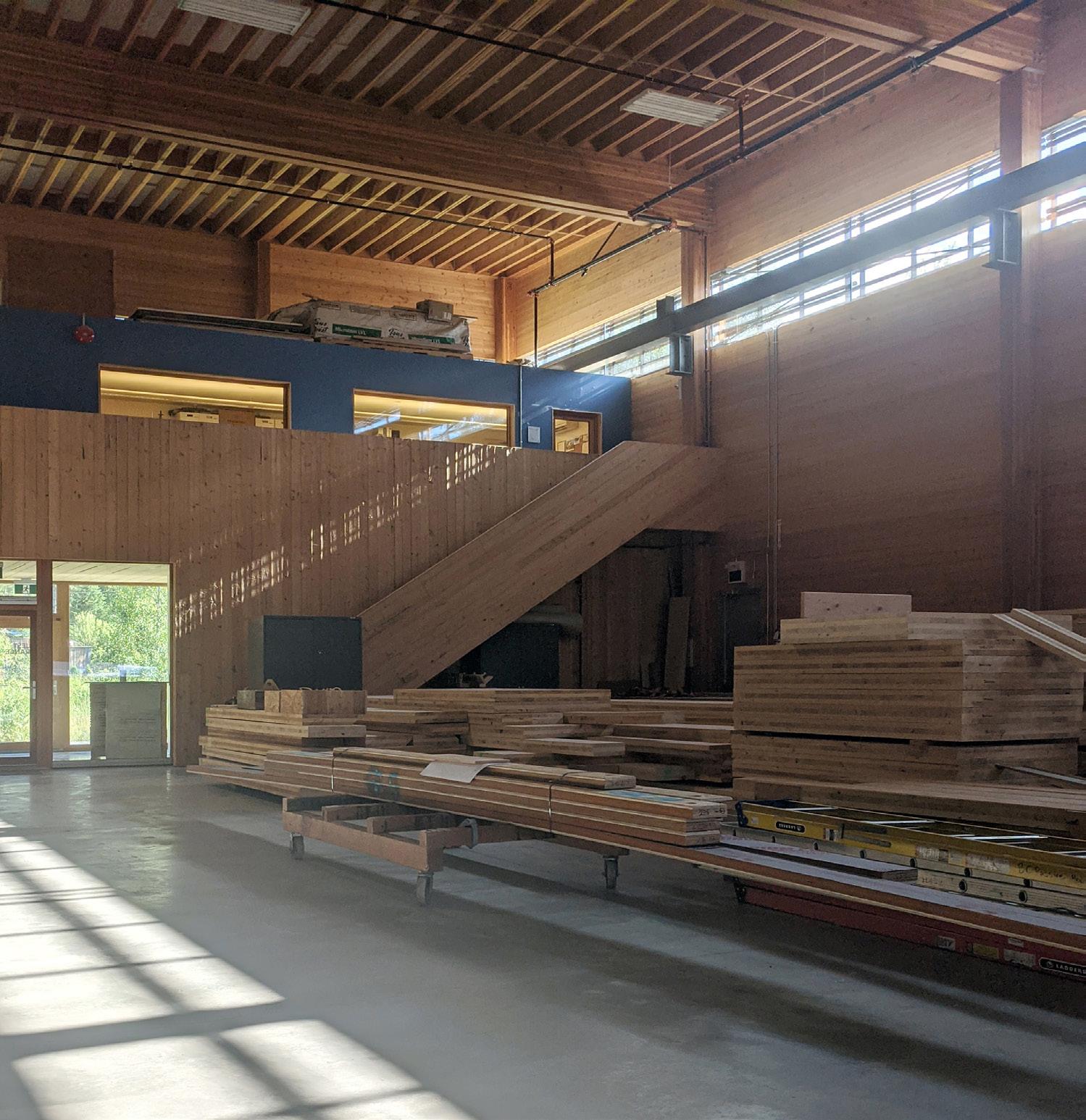
BC Passive House, Mount Currie, BC
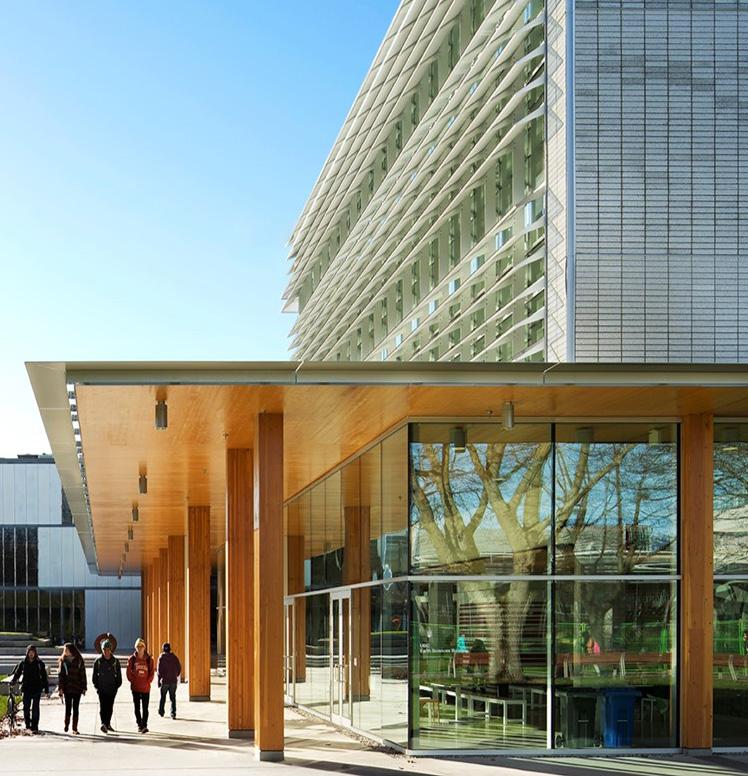
How do I compare mass timber with other structural materials, apples to apples?
When formulating a case for mass timber that you want to share with external stakeholders, it is critical to understand the pros and cons of all potential structural materials. Without this understanding, mass timber can become difficult to promote when pressure or questions from the client, design consultants, code officials, the contractor, or various trades begin to mount.
Take the time to justify to yourself and your team that mass timber is a value add for the project when compared honestly with other structural materials.
The following Structural Material Evaluation Matrix is a useful tool for comparing mass timber to other structural materials in a projectspecific manner. Keep in mind that for each unique project, different categories in the spreadsheet will carry more weight. Establish with your team the relative importance of each category for this client and project.
Structural Material Evaluation Matrix
STRUCTURAL SYSTEM
DESCRIPTION OF STRUCTURAL
FRAMING
STRUCTURAL DESIGN SPANS
STRUCTURAL DESIGN FLEXIBILITY
DEPTH OF FLOOR ASSEMBLY
SEISMIC CONSIDERATIONS
SERVICES INTEGRATION
FUTURE ADAPTABILITY
MATERIAL COSTS
CONSTRUCTION COSTS
AVAILABILITY OF TRADES
Typical structural system
Core structure
Bracing elements
# of stories, other key info
Typical bay size, max achievable spans
Open span (if required), potential for irregular grid (if required), grid size and spacing, future tenant use flexibility, potential for future interconnecting floors (if required)
Typical floor depths, beam depth, floor to exposed structural ceiling clearance, floor to u/s of beam clearance
Seismic approach - describe for each option.
Level of detailing and discussion w/ AHJ
Weight
Post-disaster: ease of inspection, durability, damage potential
MEP coordination in structure
Onsite flexibility
Future tenant flexibility (if required) + rerouting
Drop ceilings vs exposed structure
Alternate layouts
Impact of rerouting services
Potential for other uses
$/unit qty of main structural material
Other requirements s/a connectors
Quantity & weight of material required
Current market trend if known
Onsite crew
Prefab potential
Construction schedule duration
Formwork
Lead times and parallel track activities
Suppliers, fabricators, installers, construction trades
+
CONSTRUCTION TIME/SCHEDULE
CNC, prefabrication potential Just in time delivery
Onsite labor
+ schedule
Offsite work and impact on QA/QC
OPPORTUNITIES FOR PREFABRICATION
IMPACT ON NEIGHBORS
STRUCTURAL FIRE RESISTANCE RATING
NON-STRUCTURAL CODE IMPLICATIONS
APPROVALS
Prefab potential for key structural elements
Preinstalled connectors, service integration
Impact on repetitive systems if applicable
Onsite crew
Traffic impact
Sound + air quality impact
Parking impact
Local by-laws on disruptive activities - impact on schedule
Is structural solution directly code compliant? Is combustible construction permitted?
Alternate solution or Site-Specific Regulation required?
Fire approach - exposed (char method) or encapsulated?
Gypsum/concrete topping impact on FRR
Sprinklers
Any testing to be done?
Flame spread rating
Smoke separation
Fire stopping systems
Any testing to be done?
Is structural solution directly code compliant? Is combustible construction permitted?
Alternate solution or Site-Specific Regulation required?
Building & Fire Department approvals process
Other AHJ stakeholder involvement
Tie-in with other city initiatives (such as Greenest City Action Planembodied energy)
List potential assembly tests to be done
Fire + smoke modeling requirements
MASS TIMBER STEEL
STRUCTURAL SYSTEM
CONCRETE 1 - CAST-INPLACE
CONCRETE 2 - PRECAST
EMBODIED ENERGY
EMBODIED CARBON
END-OF-LIFE
THERMAL MASS
THERMAL CONDUCTIVITY
BIOPHILIA
POTENTIAL TO DIFFERENTIATE
CLIENT MOTIVATION
STRUCTURAL ENGINEER
CODE CONSULTANT
CONTRACTOR
PROJECT DELIVERY MODEL
Energy required for material sourcing, production, fabrication, transportation
Local capabilities - especially if project has regional mandate
Toxic materials in process or end product?
Transportation costs
Carbon sequestration
Fossil fuel dependency
Reuse potential - directly with minimal modification, or with significant modification? Reuse structure again as structure? Or in other uses?
Recycling potential - amount of energy required to recycle, demand
Thermal mass potential if applicable
Thermal bridges / breaks
Cognitive performance, stress reduction, and mood
Potential to benefit from exposing structure
First of its kind?
Precedent-setting for code?
Regional story?
Occupant comfort?
Character space?
Is the client supportive and knowledgeable?
Does the SE have significant experience?
Does the code consultant have significant experience?
Is the contractor a proponent and with significant experience?
Does the project delivery model suit the material?
Engagement with fabricators and installers
Construction schedule
MASS TIMBER STEEL
STRUCTURAL SYSTEM
CONCRETE 1 - CAST-INPLACE
CONCRETE 2 - PRECAST
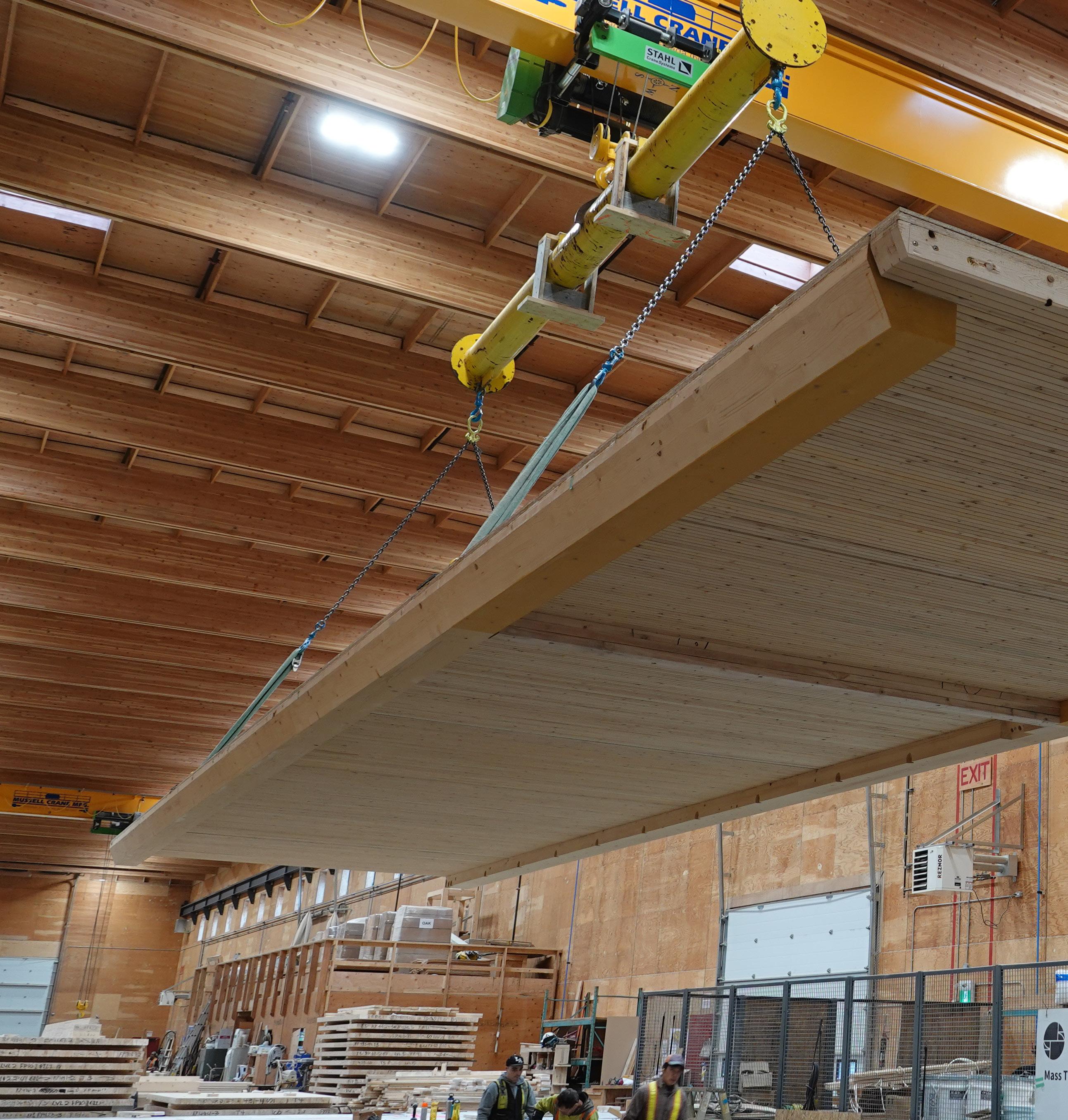
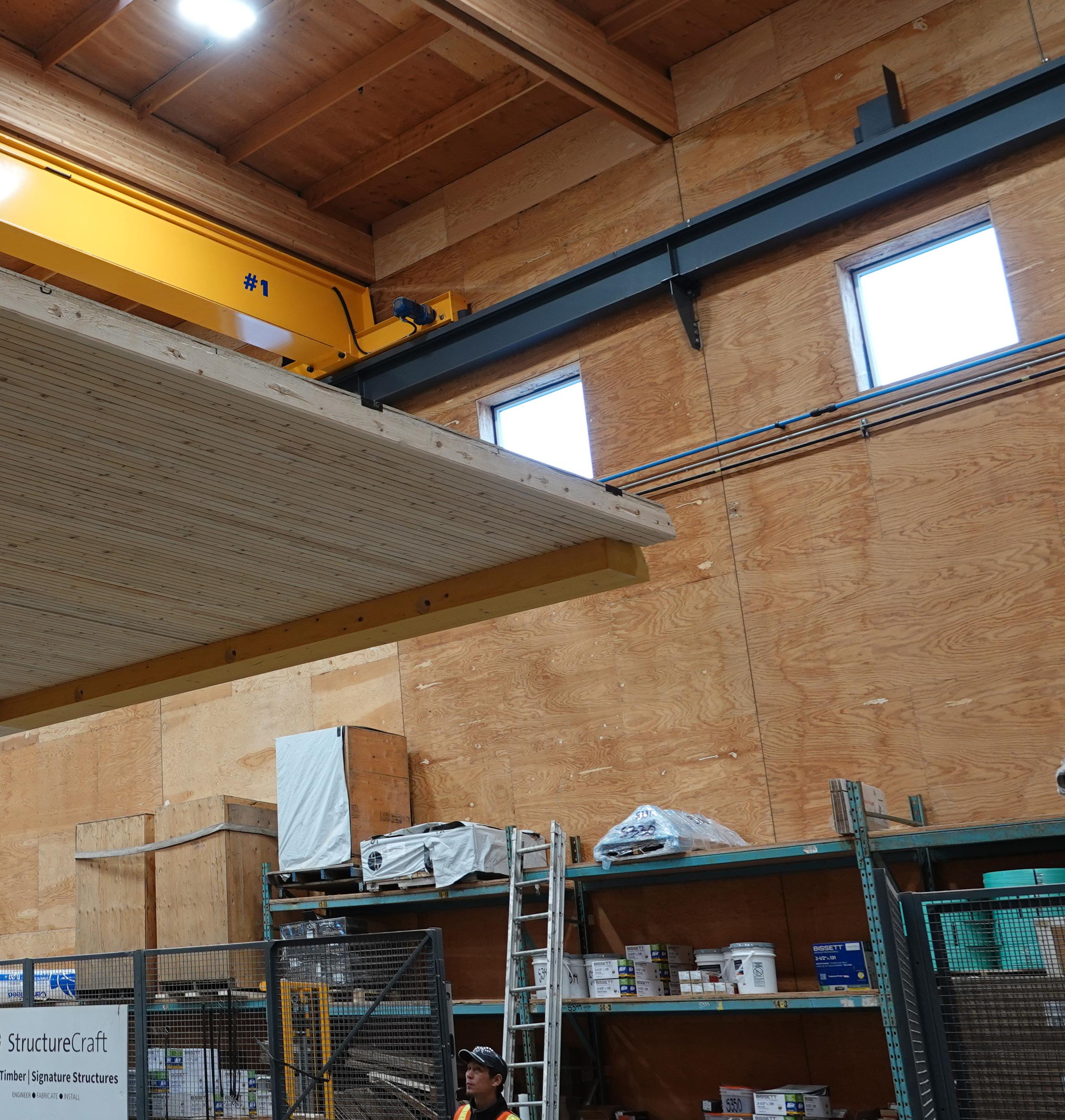
Cost Considerations
When talking about the cost of Mass Timber on a project, it is useful to consider the cost of the whole building rather than thinking of Mass Timber as a substitute for individual structural elements or systems. Building cost depends on square footage and volume, foundation type and size, floor to floor heights, finishes, geometry, and construction schedule. Because mass timber is most often used not only for its structural qualities, but also for its finish, fire resistive and insulative properties, it constitutes more than a structural system.
The cost advantages of mass timber are many. Mass timber buildings require smaller foundations because the structural material is much lighter than its steel and concrete counterparts. While steel and concrete structures may require additional fireproofing and finishing layers, mass timber eliminates or reduces the need for such layers. Wood inherently adds character and warmth to a space, and mass timber ceilings, walls, and columns can be left exposed.
A reduced construction schedule is possible because mass timber components, whose quality benefits from controlled factory prefabrication, are prepared off-site and arrive ready for assembly by a small crew, resulting in reduced on-site labor and overall construction costs. The prefabrication process allows for faster installation of utilities, which are coordinated prior to fabrication.
Mass timber can have a lower carbon footprint and reduced emissions than steel or concrete in most cases. This must be verified on a project-by-project basis, but, depending on the location of the project, mass timber is often the most environmentally responsible building system choice.
To help ensure effective cost control from project start, we recommend that design teams engage a mass timber manufacturer in a Design for Manufacture and Assembly (DfMA) or Design Assist capacity. This collaboration allows the architect to take advantage of the manufacturer's expertise to execute details more efficiently or at a lower cost. Although additional time and effort by both the design team and the contractor may be required at the project outset, the result is improved cost certainty and better coordination, leading to reduced Requests for Information (RFIs) and change orders during construction.
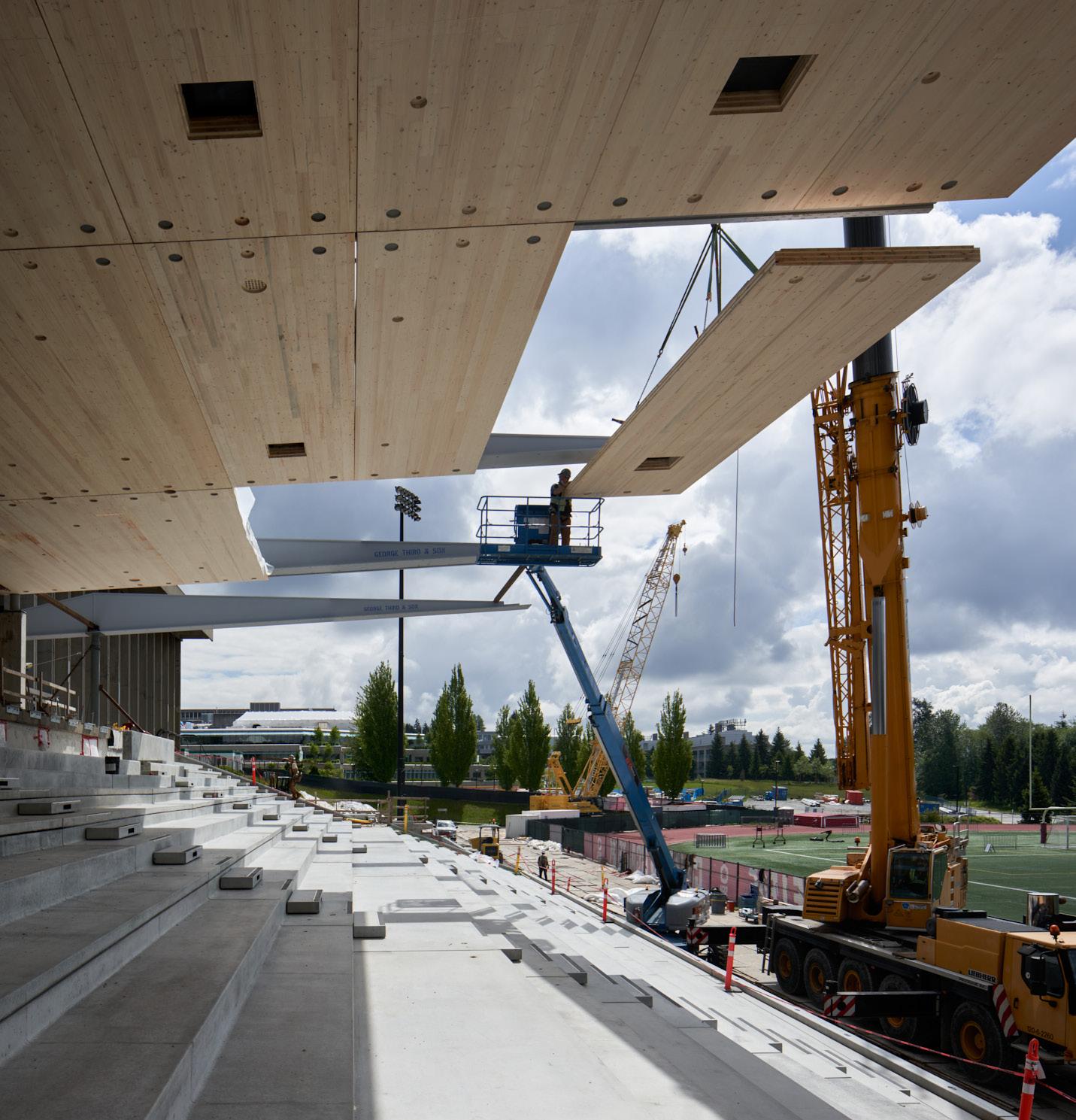
Simon Fraser University Stadium, Burnaby, BC
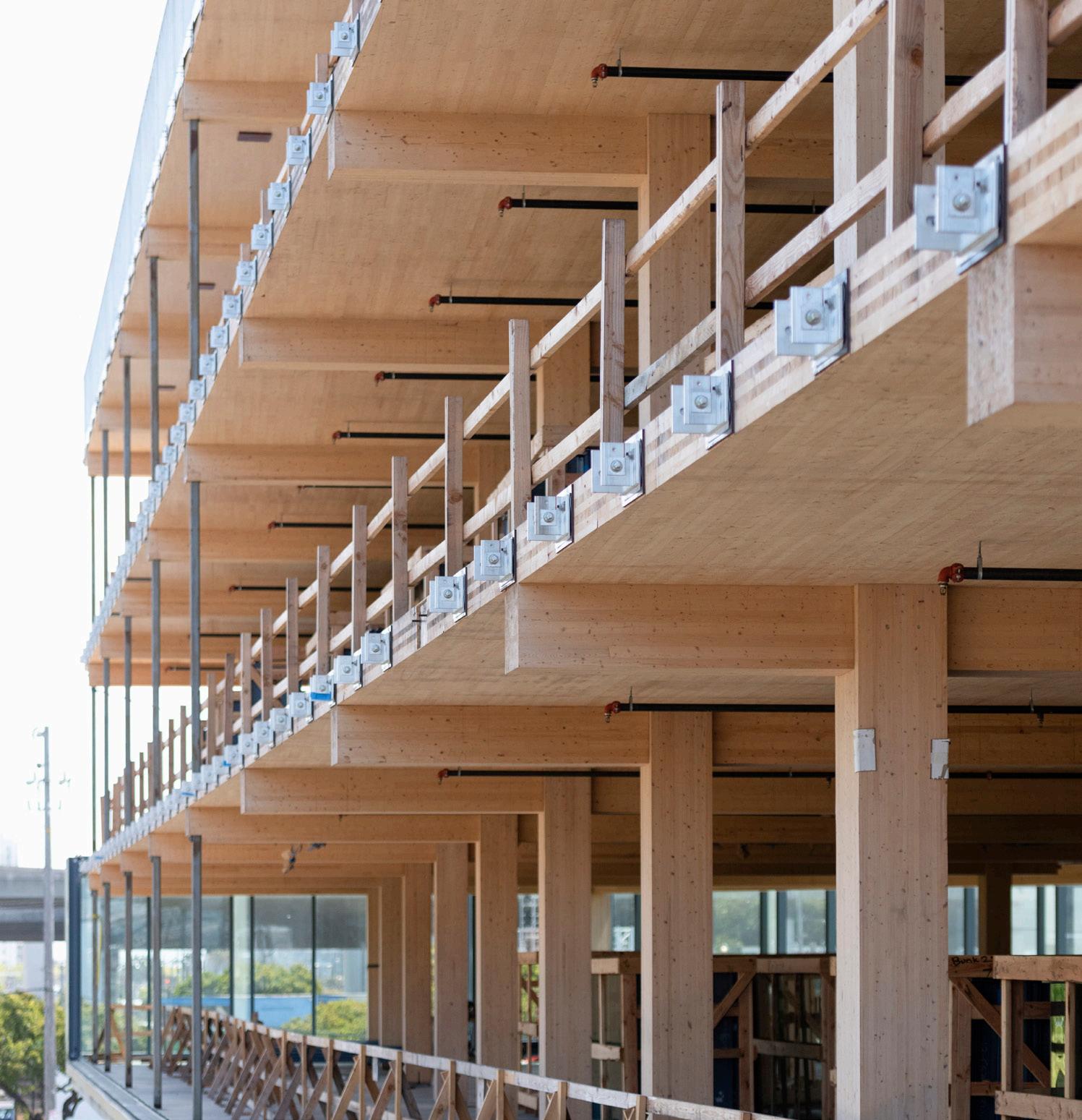
1 De Haro, San Francisco. Image credit: DCI Engineers
Rethinking the Design and Delivery Process
Cost-effective framing layouts for mass timber are non-intuitive when compared to established norms of steel and concrete framing. Designing an efficient mass timber structure requires the leadership of an engaged fabricator and an experienced structural designer from the earliest stages of design conception.
Taking a traditional approach and substituting wood as the structural material will typically lead to cost over-runs, redesign and wasted potential for schedule savings. Sophisticated, craft-centric mass timber projects require a ground up approach that considers how a prefabricated, organic structure influences the delivery model, stakeholder roles, design activities timeline, the structural parti, and the integration of building systems.
Delivery Model
Mass timber projects are best suited to a project delivery model that allows the design process to include the contractor, fabricator, and structural engineer working together with the architect to establish design goals/vision, framing layout, rough member sizes/thicknesses, erection sequence, and site logistics – including weather-proofing.
Design Build and Design Assist are the preferred delivery models for mass timber. Generally, a turn key fabricator-installer (or better yet, an engineer-fabricator-installer) working closely with the architect and structural engineer during schematic design will yield the best results for the least overall cost.
Stakeholder Roles
The structural engineer plays a more prominent role formulating the design vision than on typical steel and concrete projects. Their expertise in load path options for an isotropic material, such as wood, combined with their ability to facilitate early cost forecasting can greatly assist with establishing a design scheme that will stand up to cost and schedule scrutiny.
The contractor has new risks to consider with mass timber. Logistics of large prefab panels and construction sequencing that suits a well-crafted weather protection plan require an A-team. While mass timber is physically easy to install due to simple field connections, it is not recommended for GCs to self-install without prior mass timber experience due to weather protection risks that are often underestimated.
Mass timber fabricators all have unique constraints on species, lam-stock sizes, members sizes, panel widths, lengths and thicknesses, and span tables. Identifying the manufacturer early and designing to the efficiencies inherent in their offerings can reduce cost, eliminate redesign, and bring precision to the fabrication and construction processes.
Engaging a fabricator so early in the design process requires the support of owners and general contractors, but getting their support as well as the involvement of the fabricator has an enormous impact on the success of the project. In addition, by engaging the fabricatorinstaller early, the contractor can get early support on logistics and weather protection strategies.
Mechanical and fire protection engineers can play a pivotal role in the physical expression of the exposed timber ceiling. Working closely with these partners from an early stage will allow for planned adjacencies and detailing that will impact both aesthetics and cost.
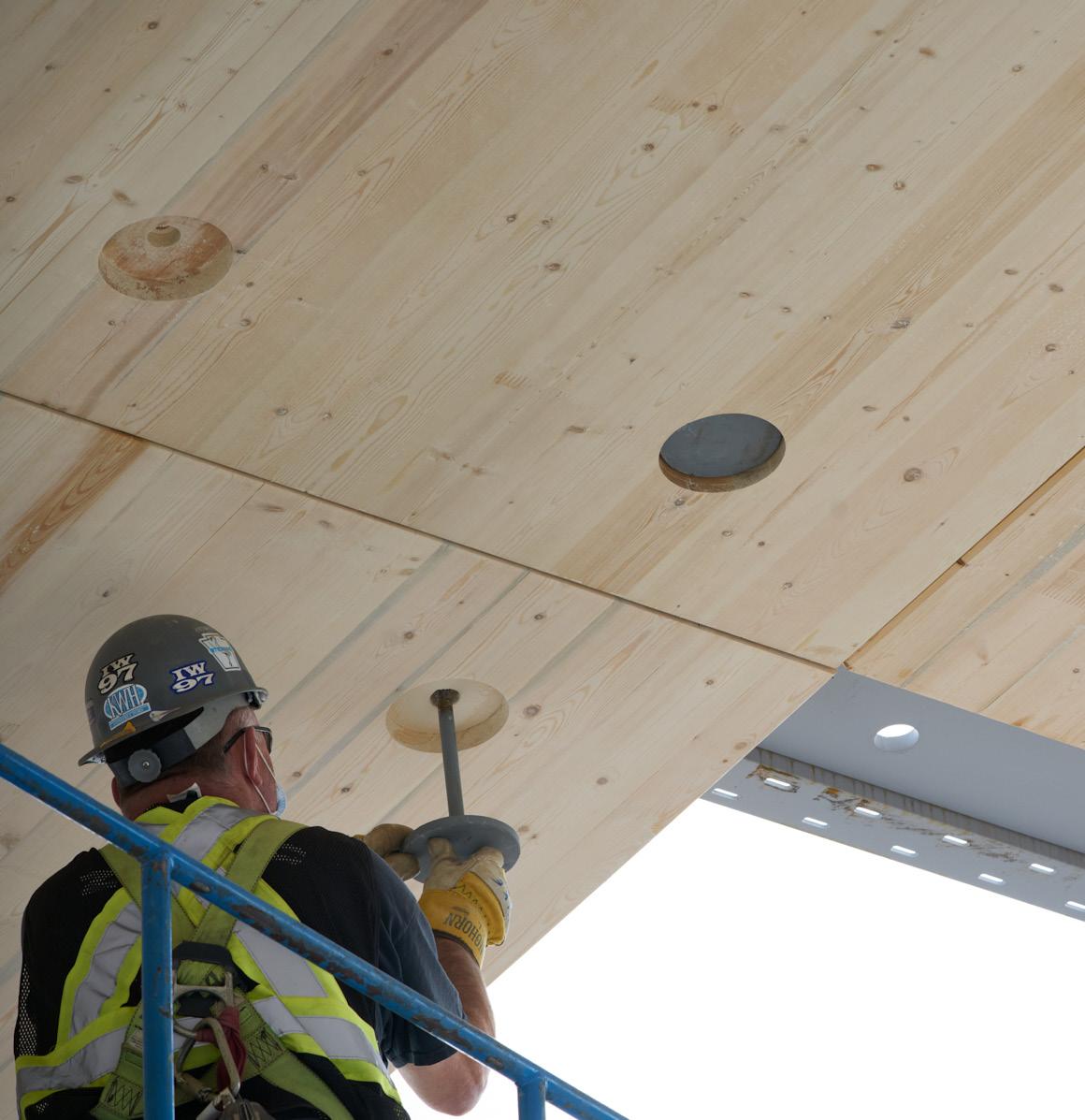
Simon Fraser University Stadium, Burnaby, BC
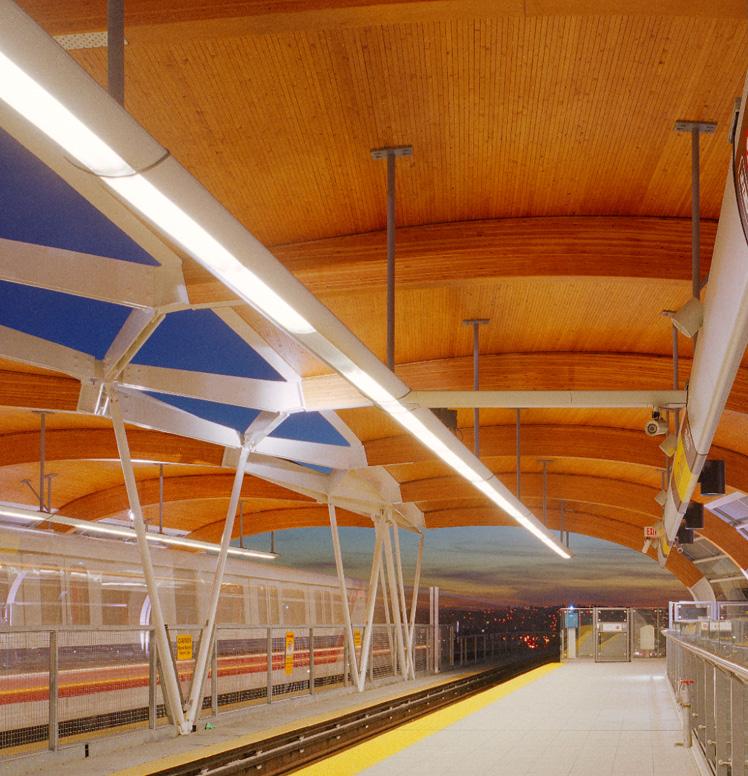
Brentwood SkyTrain Station, Burnaby, BC
Structural Parti Setting
Establishing an architectural parti in a mass timber project is typically influenced by the desire to expose the wood. This requires laser focus on tectonic clarity and careful consideration of minute aspects of the structure that we as architects are at times able take for granted in steel and concrete buildings with concealed structures. Consideration of structural minutiae can be rewarding, but is also time-consuming when we are not intimately familiar with the material.
The parti-setting process for architects is typically done in two parts:
1) Defining objectives – exposing the wood, revealing or concealing steel connections, integrating utilities into the framing and decks, achieving long spans, etc. – and communicating these to the structural engineer.
2) Working with the options presented by the structural engineer with input from a selected fabricator to establish the parti.
Expressing structure as a design goal requires deep attention to framing options, connection details, and the interface between different structural materials. See Chapter 5 for guidance on the basics of mass timber framing and connections.
The beauty of an exposed wood structure is quickly muddled by building systems if the design parti does not take all systems into account. Identify all the building systems and work with your structural engineer to rigorously detail the manner in which they will be accommodated and supported by the structure.
Some of the finest built examples of integrated systems in mass timber projects resulted in new framing typologies. Don't be afraid to reinvent the wheel with your experienced structural engineer. There are still many unexplored territories in mass timber and there is no tried and true framing form for systems integration.
Integrated Systems
Coordinated integrated systems are essential when the structure and utilities will be exposed to view. All uncoordinated conditions will be painfully visible. Aesthetically pleasing field modification to mass timber panels, beams and columns is difficult. With this in mind, all openings - including all penetrations greater than 2" - should be preplanned and communicated to the mass timber fabricator prior to shop drawing preparation, which typically begins in the early construction documents phase. This requires frontloading the MEP design coordination efforts significantly in mass timber projects.
For multi-story mass timber projects, integration of the MEP and structural systems is often critical to achieving a cost competitive scheme while maintaining floor to floor heights typical of a comparable steel or concrete building. This is because beam depths in mass timber buildings tend to be deeper than steel and concrete beams.
In the absence of fabricator-installers at the design table, it is wise to pursue non-integrated systems. In other words, run all MEP below the structure and organize them carefully, leaving no systems unplanned - especially sprinklers.
Systems integration can be successful through careful coordination between the architect and design consultants and with the general contractor. However, because most mass timber projects are design-build or design-assist projects, an MEP subcontractor will likely be involved in the project to engineer-fabricate-install the MEP systems. This subcontractor will have their own strategies to bring to the table to reduce cost and schedule for the GC. In a situation where the architect and/or structural engineer is also subcontracted to the GC, the architect has less leverage to ensure elegant integration of systems. With this in mind, it is best to bring the MEP subcontractor to the table as soon as possible - during SDs, if possible.
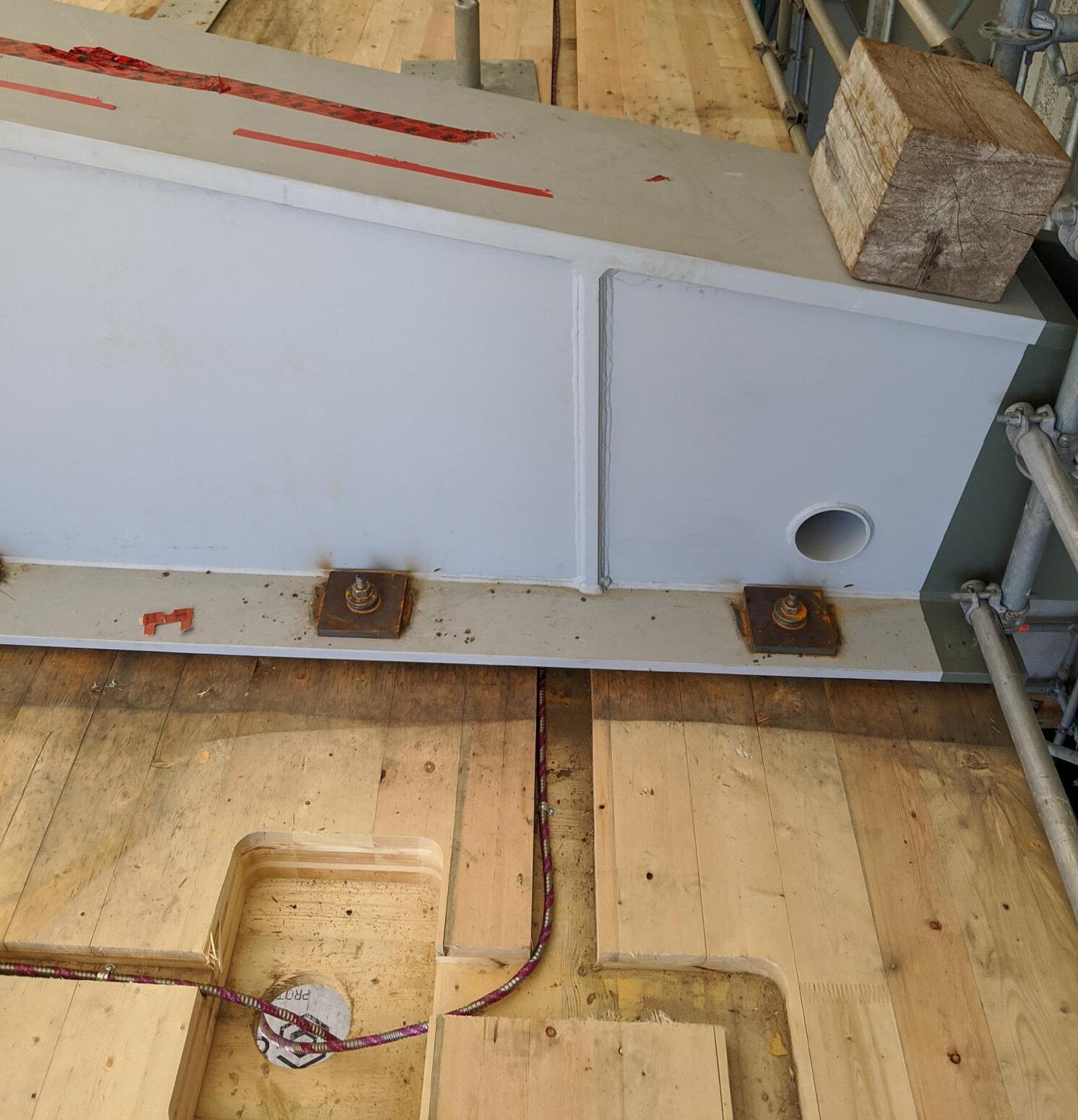
Simon Fraser University Stadium, Burnaby, BC
Project Timeline
Mass timber is prefabricated and is typically delivered through a design-assist model. All aspects related to the mass timber system design are front-loaded in the design process. The following description of design phases provides an idealized sequence of activities for mass timber projects. Use the phased descriptions below to help plan ahead. Use the graphic on the following pages to ask yourself critical questions and develop strategies well in advance of the time you will need them.
Project Kickoff
Ideally, the structural engineer, mechanical engineer and contractor are all represented. Architect presents project design objectives with respect to mass timber.
Concept Design
Working with the structural engineer and mechanical engineer, a framing system is developed that achieves stated architectural objectives. The vision for the role of mass timber and the impact on the architectural expression is clarified. A strategy for systems integration is established to reduce interstitial space and achieve maximum floor to ceiling heights.
Schematic design
The resolution of the mass timber elements during schematic design must go beyond bay spacing and beam depths to include connections, MEP systems integration, and even dimensioned detailing of wood elements (especially panel thickness) to ensure a well-coordinated final product. The reasons for this are three-fold:
1) Mass timber is prefabricated and has a long lead time, often requiring early release during construction document preparation. Identification of the fabricator during SD will ensure that the products offered and production capabilities can support the architectural and structural vision.
2) The expression of the wood as a focal point of the design parti requires early and earnest effort in order to achieve a refined result. This is no different from design teams' approach during SD to any parti-defining element.
3) Fire-proofing mass timber connections, joints and slab edges is challenging because there are no UL listings for mass timber. Hence, engineering judgments are often required and must be identified and resolved early in order to reduce the risk of adverse design effects.
Design development
Design development is typically focused on the systems not related to mass timber – curtain walls, roofing, interiors, MEP systems, etc. Fireproofing details previously identified in SD are developed and validated with engineering judgments.
Construction Documents - Coordination of fabricator-prepared construction documents as well as shop drawings. Project teams working on construction documents need support for CA tasks such as shop drawing review concurrent with design documentation.
Construction Administration
The CA phase on mass timber projects is typically reduced relative to steel and concrete projects. From a project manager perspective, front-loading the design fees to earlier phases is the appropriate approach to mass timber projects for the following reasons:
1) Shop drawing review of mass timber is typically already complete when the CA phase officially starts. The site installation of mass timber is very rapid and the primary CA task is to observe installation with a focus on: moisture protection, protection of exposed wood surfaces that could be damaged by construction activities or UV light, joint widths, fire-protection installation, and any site-cored penetrations.
2) The early coordination of integrated systems and mass timber assemblies/connections leads to a reduced quantity of RFIs and reduced rework on site, leading to less time spent on field observation.
Is the client on board? Have you considered strategic partnerships?
Are you interested in mass timber? CLIENT ENGAGEMENT
Have you identified a target client or partnership?
Have you identified a target building type?
Have you built consensus internally on using mass timber on a potential project?
Have you analyzed the latest local building code? Does it allow mass timber construction for the height and area proposed?
Have you identified staff in your office with expertise in mass timber specifications, design and detailing ?
What is the code threshold for mass timber on this project? How far is the project from this threshold?
What are the values of this client? Are they likely to align with the pursuit of mass timber?
What project delivery method will be pursued?
What are the budget and capabilities based on the regional network and resources of the client and potential team?
Has the owner determined if the GC has mass timber experience prior to signing the owner-contractor agreement ?
Does the owner-contractor agreement require prequalification based on timber experience?
If GC has no timber experience, are they interested or eager to learn?
Have you reviewed your contract language to reflect the specific requirements of mass timber?
Does the Structural Engineer you are considering have mass timber experience?
Will the selection process allow for pre-qualification based on timber experience?
If SE has no experience, is there an opportunity to bring on a timber fabricator in a designassist role?
Have you tapped into the Perkins&Will Building Technology Lab?
If the project is a traditional design-bid-build, is there an opportunity to connect with local mass timber fabricators and gauge their (competitive) appetite for a project of this scope?
Is the project delivery method structured to achieve success for mass timber?
Is your code consultant aware of alternative solution strategies that fit this project’s criteria?
Have you identified a specifications writer at your firm familiar with mass timber that you can engage?
Have you identified a technical architect familiar with mass timber to engage?
Are you aware of which specifications divisions impact mass timber material, process and leverage during construction?
Can the structural engineer develop innovative/elegant and cost-effective applications of mass timber?
Is there an opportunity to make mass timber an integral part of the design ?
How are you designing to the material?
How do you follow through?
How do you build on relationships for future projects?
Are you designing with a prefabrication mindset?
Have you allocated sufficient resources to the design phases to complete all wood design (including fire protection strategies) prior to the start of prefabrication?
Are you using other structural materials where they add the most value?
At dis-similar material interfaces, have you accounted for construction tolerances?
Is your project team able to engage a timber fabricator directly or through a Construction Manager?
Are you able to connect with local mass timber fabricators to gauge their interest in this project?
Have you kept in touch with members of the mass timber construction industry to position yourself for success in future mass timber projects?
Are you protecting the wood from UV and moisture?
Do you have a solid grasp of local mass timber availability?
What is the weather protection plan (UV and moisture)?
Is the local supply of mass timber cost-competitive?
Can your GC describe cost/ schedule/site benefits to client?
Have you done a postoccupancy analysis that could contribute to design decisions on mass timber in the future?
Have you identified awards you would like to submit for?
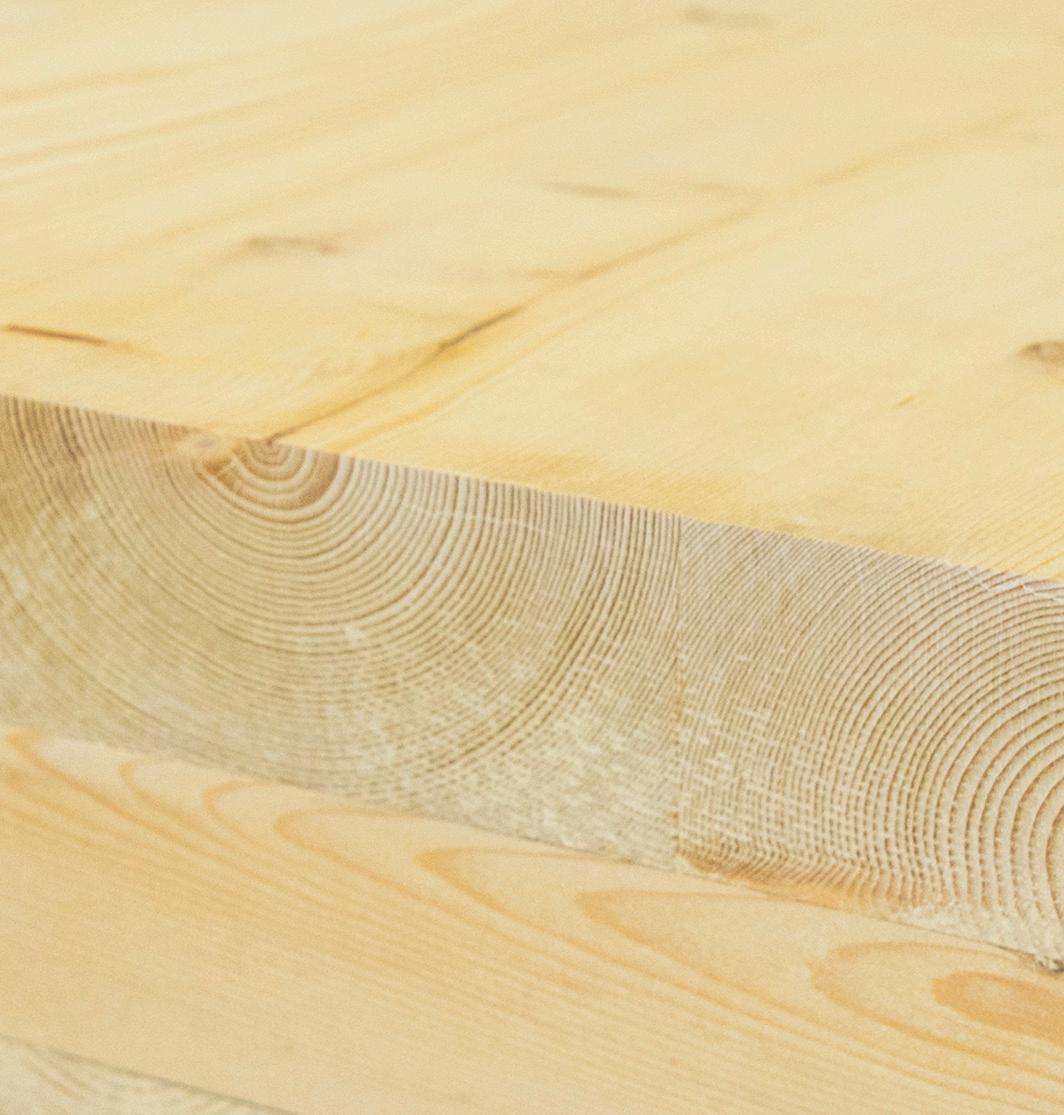

05 DESIGN FOR MASS TIMBER
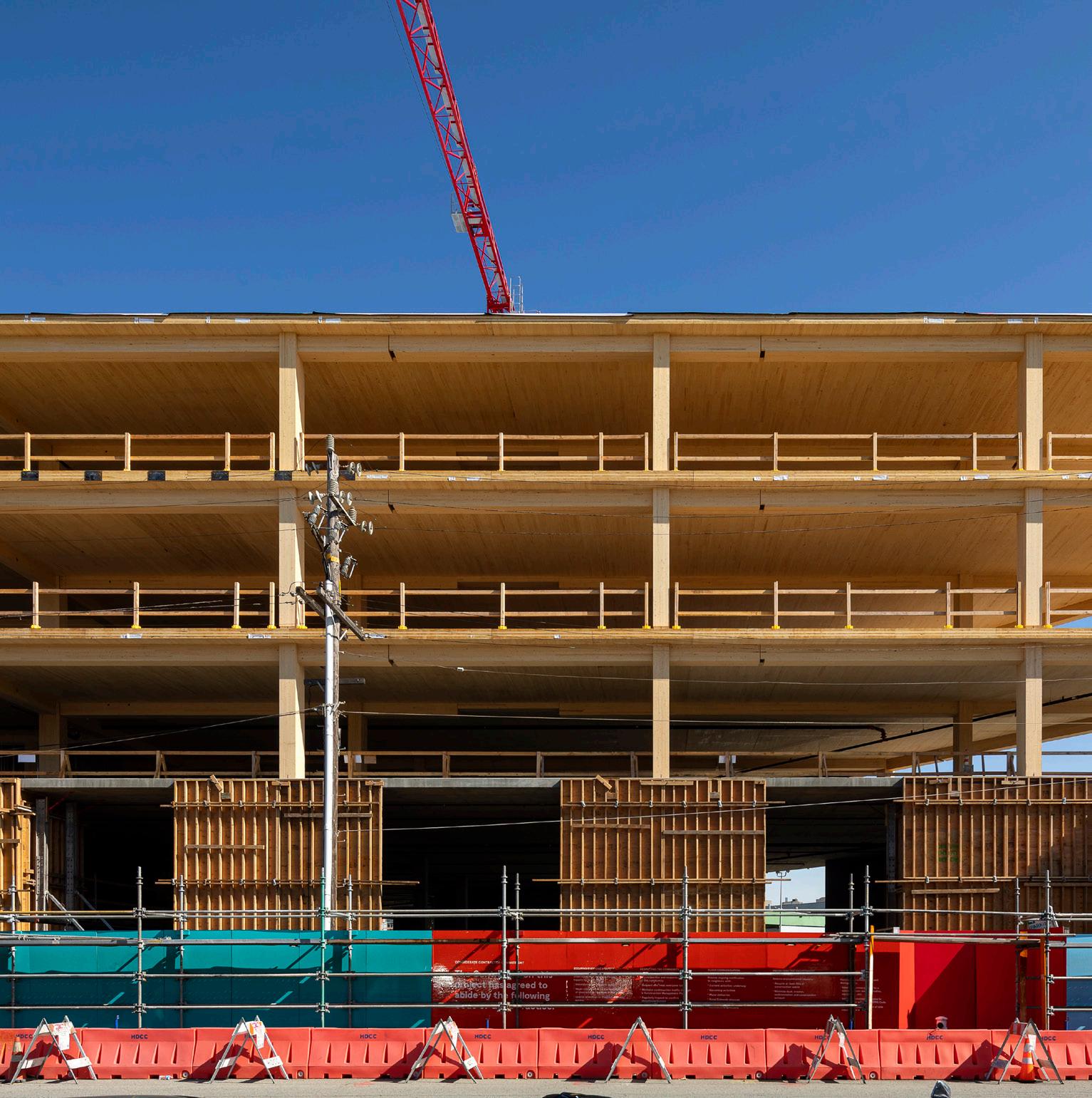
1 De Haro, San Francisco. Image Credit: Kyle Jeffers
Designing from Scratch with Partners
Designing with mass timber is a team sport. Designers depend heavily on the structural engineer's creativity, the wood fabricator's capabilities, and the installer's sequencing strategies. Each of these disciplines must collaborate to obtain a design that carries the team's vision, is cost effective, and is quick to assemble.
Rules of thumb for mass timber are still being established across the industry. However, some basic guidelines have been established regarding structural and cost efficiency. The fundamentals of mass timber design are presented below in text and graphic form for ease of communication within teams and consultants. These guidelines are reliable, but are not meant to constrain. They are best used as a foil against which new thoughts and fresh designs can emerge.
Leverage the diagrams to develop the most economical approach. This will allow you to reserve some budget for moments of craft in design - on even a tight-budget project. On a project with a generous budget, these guidelines are a reliable point of origin from which to break the rules and reinvent the wheel as we progress toward craft.
Mass Timber Design Basics
Mass timber structures can be generally thought of as prefab systems using a combination of panelized and post-and-beam structures. The most similar type of construction from a structural systems perspective - and even sequencing and tolerances -is precast concrete.
Setting Your Grid
Start with a grid that is best suited for mass timber, i.e. 20’ x 20’, and adjust to suit your project needs. Identify the panel size constraints of the mass timber supplier you plan to work with and design toward the panel width they can provide – typically 8’ or 10’. Knowing the supplier panel size before you set your grid can lead to project savings.
Keep the overall building grid as regular as possible, except for architectural moments such as atria. Find the beauty in the module and celebrate it.
Floor to Floor Height
Because mass timber floor and beam structures are deeper than steel and concrete structures, you will need to be creative to maintain head room clearances without increasing floor to floor heights. This can be done in a variety of ways:
Beamless Floors - By resting the mass timber panels directly on the top of the columns, beamless framing can be achieved. The resulting panel thicknesses are significant, but this cost add must be weighed against the savings from reduced floor to floor height.
Beam Placement - By carefully coordinating the program spaces and grids, shallow beams can be used where headroom is critical.
Systems Integration - By stacking beams or stacking mass timber floor decks, utilities can be routed within the structural depth, rather than under it.
Reduced Headroom - By exposing the wood structure, the typical 'ceiling' height will be set by the bottom of the wood deck, meaning that the headroom is actually higher than in a dropped ceiling design. Headroom locally at beams will be lower than for steel or concrete, but an attractive, natural, finished surface is sometimes welcome at closer range.
Floor Assemblies
CLT panel thickness is determined by the number of lam-stock layers, or plys – 3-ply, 5-ply, 7-ply or 9-ply. Try to establish a framing design that uses 3- or 5-ply to significantly reduce cost.
NLT and DLT panel thickness is determined from standard lumber sizes 2x6, 2x8, 2x10, 2x12.
Mass Plywood panel thickness is in increments of 1" (4", 5", 6", etc. up to 2'-0").
Floors and roofs can also be composed of glulam, LVL or LSL beams turned horizontal. Standard beam thicknesses determine the deck thickness.
The most fundamental cost reduction method for mass timber vertical load bearing systems is the following: Reduce the floor deck thickness. A reduced deck thickness can be achieved by adding purlins to reduce deck spans. This leads to reduced volume of wood and, thereby, cost.
Use existing mass timber sizing guides to determine preliminary beam sizes. The structural engineering firm Fast + Epp has developed a useful tool for this purpose which can be accessed at: https://www.fastepp.com/concept-lab/calculator/
A topping slab of 2" or more will typically be used to achieve some of the following effects: sound (impact) damping, reduced vibration, fire protection, lateral diaphragm, composite wood-concrete slab, thermal mass, radiant heating, utilities routing.
Beams
Glulam beams are deeper than steel and concrete beams for the same span. One strategy to accommodate them is to give yourself some extra headroom in your floor to floor height wherever possible. Alternatively, to keep floor to floor heights standard, group utilities/ HVAC in plan in areas with dropped ceilings or close to the building core to allow for unobstructed exposed mass timber structure along the building perimeter.
Structural design of mass timber beams is typically governed by deflection or vibration. This means that from a strength perspective, the beams are always significantly over-designed. This works to your benefit when fire ratings come into play. Because the beams are over-designed with respect to strength, you can typically demonstrate that even after charring, the beam has enough remaining cross section to support the required loads. Thus, there is no need to pad the beam with extra 'char layers' - it is built in to the deflection and vibration design.
Mass timber beams can be combined with other structural materials to create ‘composite’ / hybrid structures that can offer larger spans / shallower beams. For example - mass timber beam + thickened concrete topping will achieve a composite beam capable of increased spans and reduced deflection.
If long beam spans (35+ feet) are required, consider steel or precast beams to support the mass timber deck and reduce beam depth.
Columns
Mass timber columns are very versatile elements of the design. Columns are most typically made of glulam or solid sawn lumber, but PSL LVL, and LSL are also structurally suitable. Mass timber columns may be combined with steel or precast concrete beams.
To get a sense of the size of a mass timber column, the cross section of glulam columns is comparable to reinforced concrete columns for buildings of similar scale.
Beyond Rules of Thumb – Developing Craft
Wood does not flow like concrete. It is not equally strong in all directions like steel. Wood has a visible and structural direction to its grain pattern. Natural tensions in the wood cause it to twist and check. It expands with ambient moisture and changes color when exposed to UV. It has 'imperfections' such as knots, that reflect its former life as a tree. In sum, wood is an organic material and its multiple organic properties can be used architecturally.
Consider how the axial strength of wood can drive the honesty of your framing. Or subvert wood's nature by using heavily engineered products that have strength in multiple directions, such as cross laminated timber, mass plywood panel, and laminated strand lumber.
Unlike steel and concrete, large format panels and linear members are CNC machined for minimal cost. Using machine labor in a subtractive manner to shape the structural elements, mass timber structures become custom-crafted objects.
You can’t weld wood together, but you can bolt it, screw it, dowel it, and glue it. And when you consider that concrete can take any form, just remember what formwork is typically made of. Wood, including mass timber, can achieve many surprising geometries, and current architecture and design work is still very early in the era of mass timber. There is much to explore.
Wood Framing Options
The following framing diagrams provide relative cost icons ($ to $$$$) and relative schedule impact icons (> to >>>>).
To reduce costs, keep floor panels as thin as possible by adding purlins.
To reduce schedule duration for shop drawings, fabrication and erection of the structure, use fewer members and avoid multiple structural materials. Mass timber is quick to erect, so there are no >>>> values shown. This is reserved for steel structures and reinforced concrete structures.
($, >>) 20'x20', 2-Way Glulam Beams, Purlins, 4" Panels
($$, >>) 18'x20', 1-Way Glulam Beams, 7.5" Panels
($$, >>) 20'x20', 2-Way Glulam Beams, 5" over 10" Panels
($$, >) 25'x20', Beamless, 10" Panels supporting 5" Panels
($, >>) 30'x30', 2-Way Glulam Beams, Purlins, 4" Panels
($$, >>) 20'x40', 1-Way Double Glulam Beams, 7.5" Panels
($$$, >) 30'x30', 1-Way Glulam Beams, 12" Panels
($$$$, >>>) 20'xVaries, Mass Timber Walls, 10" Panels
All wood framing with smaller bays will typically provide the fastest erection sequence for the lowest cost. For long spans, reduce cost and beam depth by using steel or precast beams, but be mindful of schedule impacts of mixed structures, as schedule savings is often a major value proposition of mass timber.
Keep the overall building grid as regular as possible, except for architectural moments such as atria. Find the beauty in the module and celebrate it.
Keep in mind that longer spans result in deeper beam depths and impact the floor to floor height. For example: 30' grid = 40" deep glulam.
Hybrid Steel Framing Options
Steel beams can be used to reduce beam depth and provide longer spans. Sequencing of wood and steel trades increases site logistic challenges and reduces schedule savings. A dense field of small steel columns can be used to eliminate beams for buildings with closely spaced partitions. Encapsulation for fireproofing will require additional labor on site.
($$$, >>) 30'x30', 7" Panel, Steel Beams
($$, >), 10'x14', 7" Panel, Steel Columns 1 2 3
($$$$, >>) 30'x40', 12" Panel, Steel Beams
($$$, >>) 20'x45', 7" Panel, Precast Beams
($$$$, >>) 30'x45', 12" Panel, Precast Beams
Hybrid Precast Beam Framing Options
Precast has similar tolerances to mass timber, which facilitates installation. Precast beams can achieve the longest spans with the shallowest profile.
Lateral Framing Design
Glulam braced frames require significant effort through performance based design, but are notable for their aesthetic quality.
Steel buckling restrained braced frames require a clear architectural vision of structural detailing, but can be erected concurrently with the mass timber and have similar tolerances (steel 1/8", mass timber 1/16").
Wood moment frames are possible, but require close spacing: 4'-0"o.c.
Wood structural panel sheathing over light frame studs is possible, but only in low and mid-rise construction types.
Braced
CLT shear walls are recommended if the vertical load bearing system is CLT walls. Otherwise they can be difficult to engineer without becoming very long. Post-tensioned rocking CLT shear walls are possible but require significant engineering and testing.
Concrete shear wall cores are quite common, but the trade sequencing negatively impacts the schedule and the interface of the mass timber with the concrete requires extra design care to achieve a clean aesthetic. Field verify concrete dimension prior to mass timber fabrication.
CLT Shear Wall
Species, Grade, Finishes
Species selection is typically limited to the region where the fabricator is located. First identify your mass timber manufacturer and then identify the spectrum of species they work with.
Grade selection is typically constrained by the budget. Even with the highest grades, it is important to plan for the wood to have imperfections such as knots, checks, splits and wane. Design in such a way that the imperfections are not unwelcome, but rather an expression of the character of the material. Sometimes a field of knots can be less distracting than one or two in surface.
Finish selection for interior wood is a matter of aesthetic preference. Not all finishes are made equal and the off-gassing of the products varies.
Consult Think Wood's Nail Laminated Timber U.S. Design and Construction Guide for more information about species, grade and finishes.
Interior Exposed Elements
Mass timber must stand up to fire, graffiti, mops and fingerprints.
Visually exposed members will typically be oversized when they are required to have a fire rating. The charring rate of wood multiplied by the duration of the fire rating determines the up-sizing of the members. For light charring, sanding and refinishing is all that is required. For deep charring, removal of the char followed by the application of additional wood to rebuild the fire protection thickness.
Graffiti can be sanded out and the wood restained. Steel surface and concrete surfaces in buildings also suffer from graffiti. Thankfully, wood is simple and cost effective to remediate.
In high-traffic areas, consider seals that prevent ingress of grease and oils from mops and fingerprints.
Exterior Exposed Elements
Exterior exposed mass timber must stand up to UV and Moisture. All exposed elements should be set back from the edge of overhanging roofs such that a line extending down 30 degrees from horizontal from the edge of the overhang should not touch any wood. This may seem extreme, but it is the only reliable method for significantly increasing the maintenance period. This deep setback will eliminate all but the most extreme wind driven rain and will reduce UV radiation to only very low angle sun.
When deep setbacks are not possible, the defenses against degradation are the following:
Detailing: Do not allow water to pond on wood or near end grain. Allow the end grain of the wood to breathe in all exterior conditions. Provide at least 1/4" gap between end grain and other surfaces to prevent capillary action from soaking the wood.
Species Selection: Cedar, Cypress and Redwood have high natural durability against the elements. Check if your supplier can provide these woods for the exterior scope.
Finish: Semi-transparent oil-based penetrating stains are the most effective for preserving the aesthetics of the wood over the long term.
Weathered Aesthetic: Work with a species expert who can help you pre-weather the wood with UV or charring to obtain a grayed or charcoal finish. Maintenance cycles can be lengthened when we are not always trying to make the building look brand new.
It is critical to manage your client’s expectations with respect to finishes. Interior finishes shouldn't require any more maintenance than any other material. Exterior wood will require significant maintenance if the wood is not deeply recessed. A 5 year stripping and refinishing regimen is a starting point for conversation. Proper setbacks, good detailing, weather-durable species (cedar, cypress and redwood), and quality finish products can extend this to 10 or 15 years. However, there is no avoiding planned maintenance of exterior exposed wood.
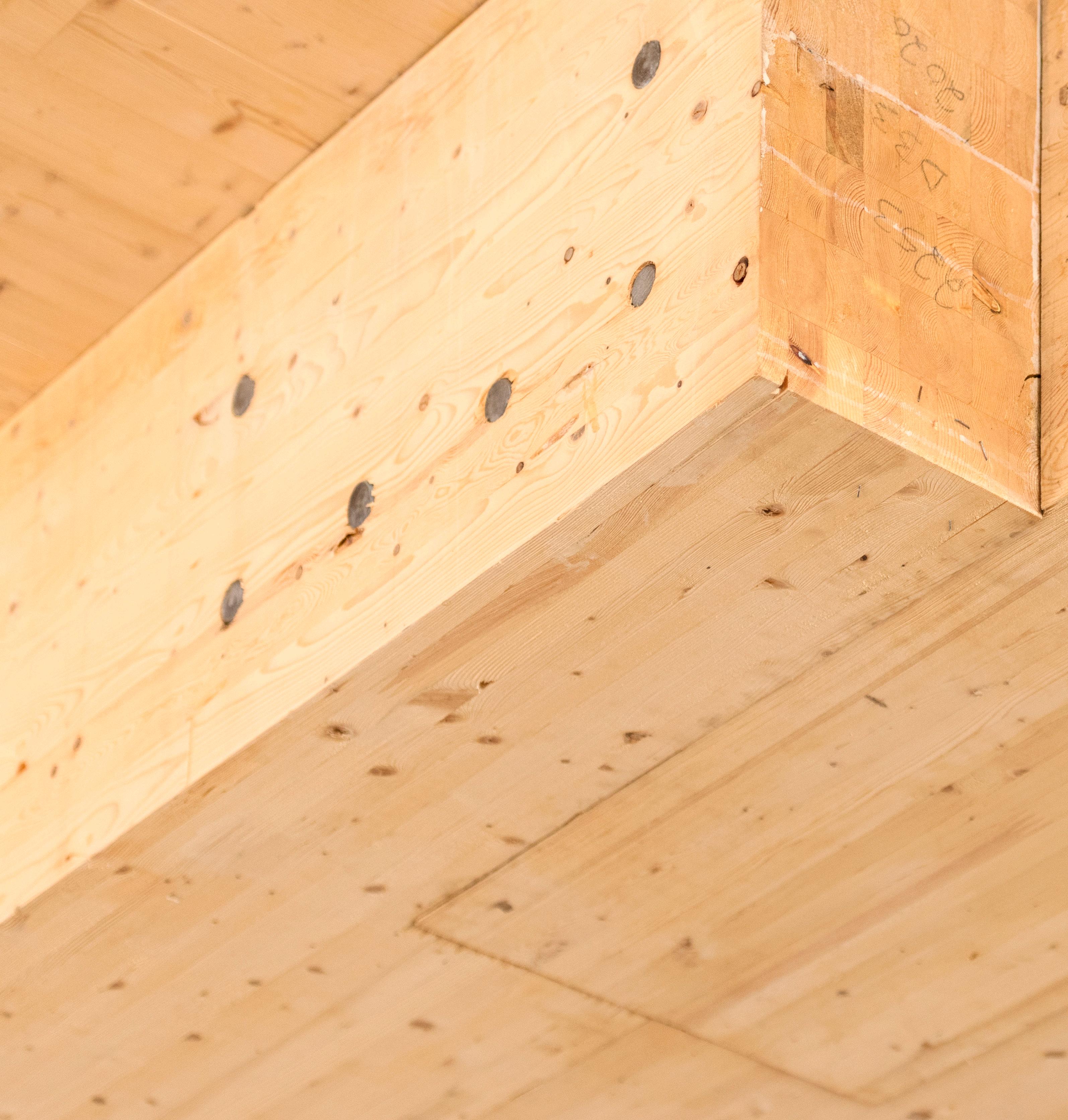
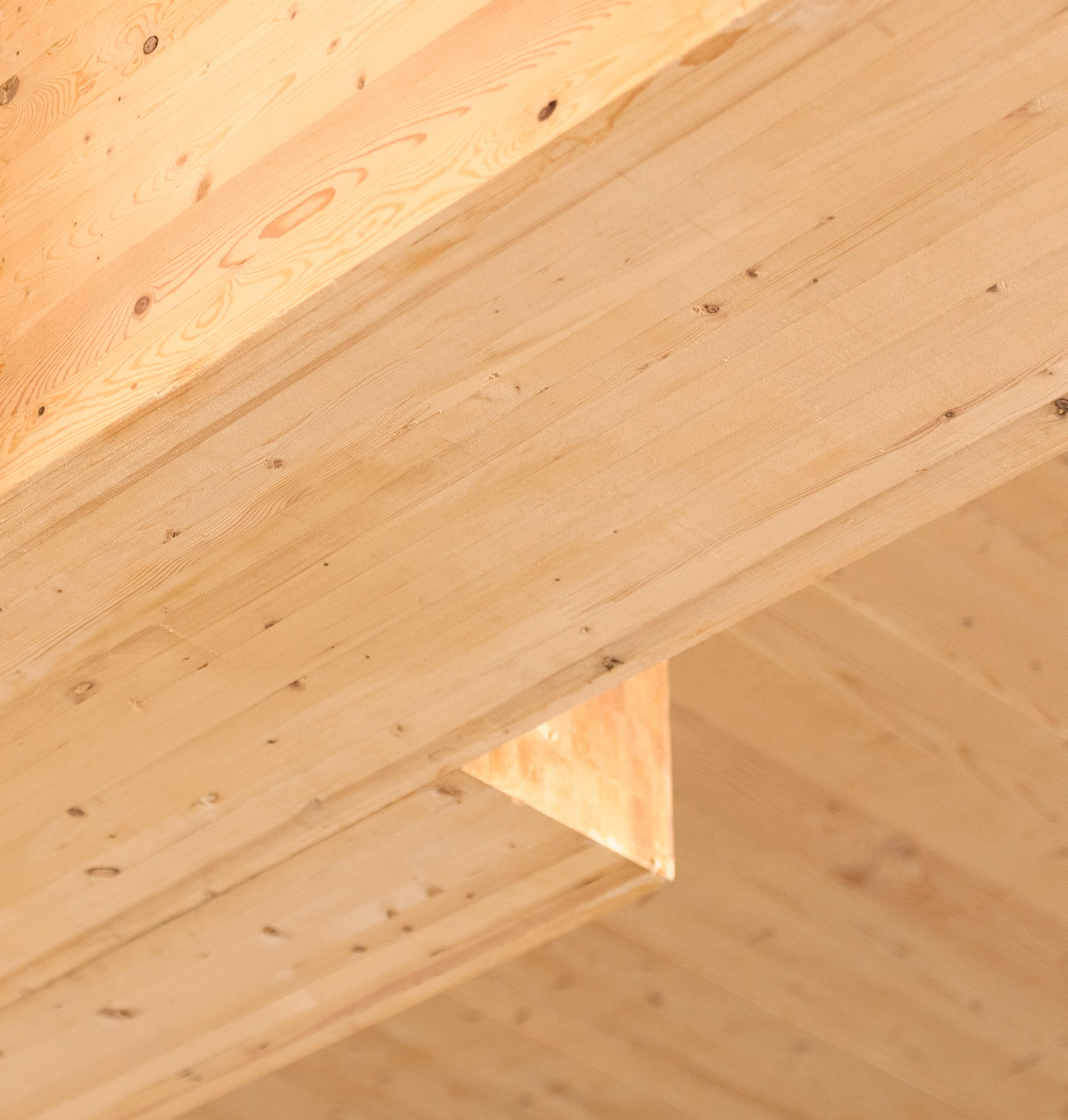
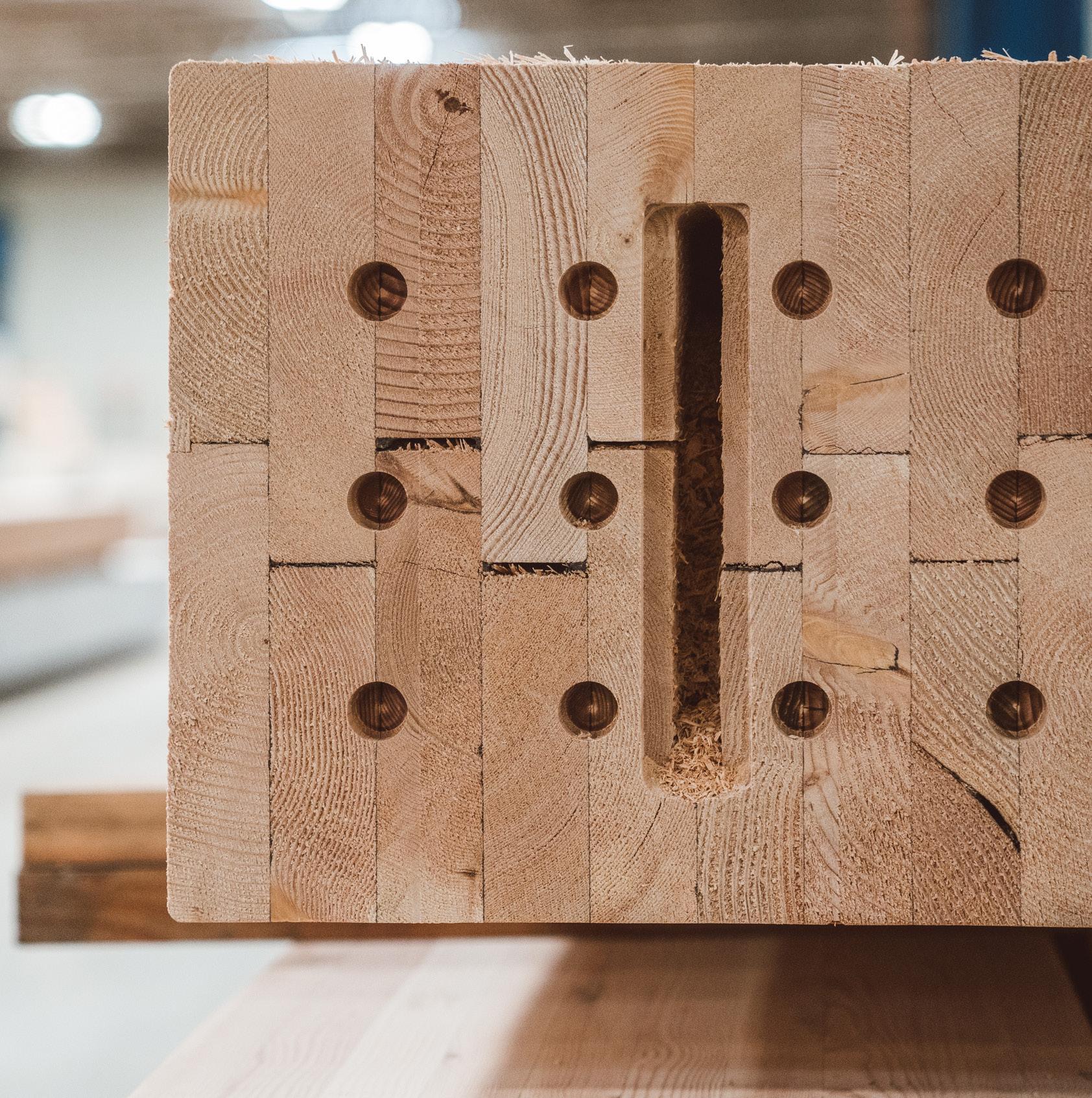
Glulam Column. Image credit: Timberlab
The Basics of Mass Timber Joinery
Mass timber connections are rapidly evolving. New fasteners and connection types are brought to the market each year. Talk to your structural engineer, fire protection engineer and contractor about your aesthetic goals for the connections in your project to ensure that your design efforts do not get negated by load path challenges, fireproofing requirements or site installation logistics.
Modern self-tapping screws up to 36" long can be used to secure most structural elements together. Under high loads, the amount of screws can become excessive, resulting in increased labor and material costs.
Concealed slotted fasteners provide an all-wood look, but they have the added benefit of recessing the highly conductive steel elements behind fire-insulating wood. This service of solving the fire-rated joint requirement can help offset the cost of these expensive fasteners.
When fire rated joints are not required, traditional and custom connections using knife plates, angles, saddles, hangers, and HSS elements, etc. can provide an honest aesthetic that is cost effective.
All-wood connections are possible and can lead to intrinsic craft in the architectural expression. These connections are time-intensive to design, but are cost effective to produce because the fabrication of mass timber is a CNC process. Eliminating the cost of steel connections with elegant all-wood connections is a frontier currently under exploration.
The following diagrams illustrate a range of basic mass timber connections. With your aesthetic goals in mind, build on these strategies with your structural engineer. Because the structure is visible in mass timber projects, it is critical that you review each unique structural detail in early design development before fabrication begins. This will help you avoid unsightly and unexpected junctions that reveal themselves in the field.
Floor Supports
Floor decks may be supported by glulam beams or columns, as well as by steel or concrete beams. Provide 1/4" joint between floor slabs for installation tolerance.
Floor to glulam beam
Floor to column shoulder Floor to steel beam (fasten from below)
to concrete beam
Floor to Wall Connections
Floors may also be supported at walls. A clean aesthetic is difficult to achieve without significant forethought. Keep in mind that concrete tolerance (1") is vastly different from mass timber (1/16") and can lead to ugly interfaces if not carefully planned. Consider cast-in anchors.
Floor to Floor Connections
For floors supported by beams and columns, the floor to floor joint will typically need to transfer diaphragm forces. Diagonal screws, plywood splines and lap joints can achieve these objectives. Maintain 1/4" gap between panels for construction tolerance.
Floor Supported by Floor Connections
Floors can support other floors. Thick CLT slabs, for example, can carry lighter ones. Consider how routing utilities above or below thick and thin slabs can help reduce floor to floor height while providing a unique aesthetic.
Column to Column Connections
Columns carry loads parallel to grain. They must not pass their loads through beams or through floor slabs as this would crush the transverse grain of the beams and slabs. Column loads can be passed direct (wood to wood) or they can pass through steel connections.
Column to column with steel knife plate
to column with offstand tube steel within slab
to column with recessed tube steel
to column with pin connection visible above
Beam to column with concealed slotted anchor
Beam through column with bolts
Beam to column shoulder with screws
Beam on column shoulders
Beam to Column Connections
Beams deposit their shear loads at columns. They may terminate at the face of the column, pass through the column, rest on a column ledge, or flank the column.
Beam to Beam Connections
Beams typically terminate at the face of an adjoining beam or girder, but may also pass over when this provides a benefit for utilities routing.
Beam-to-beam with concealed interlocking anchors
Beam-to-beam with exposed plate hanger
Beam-to-beam with knife plate connection
Beam-on-beam with knife plate connection
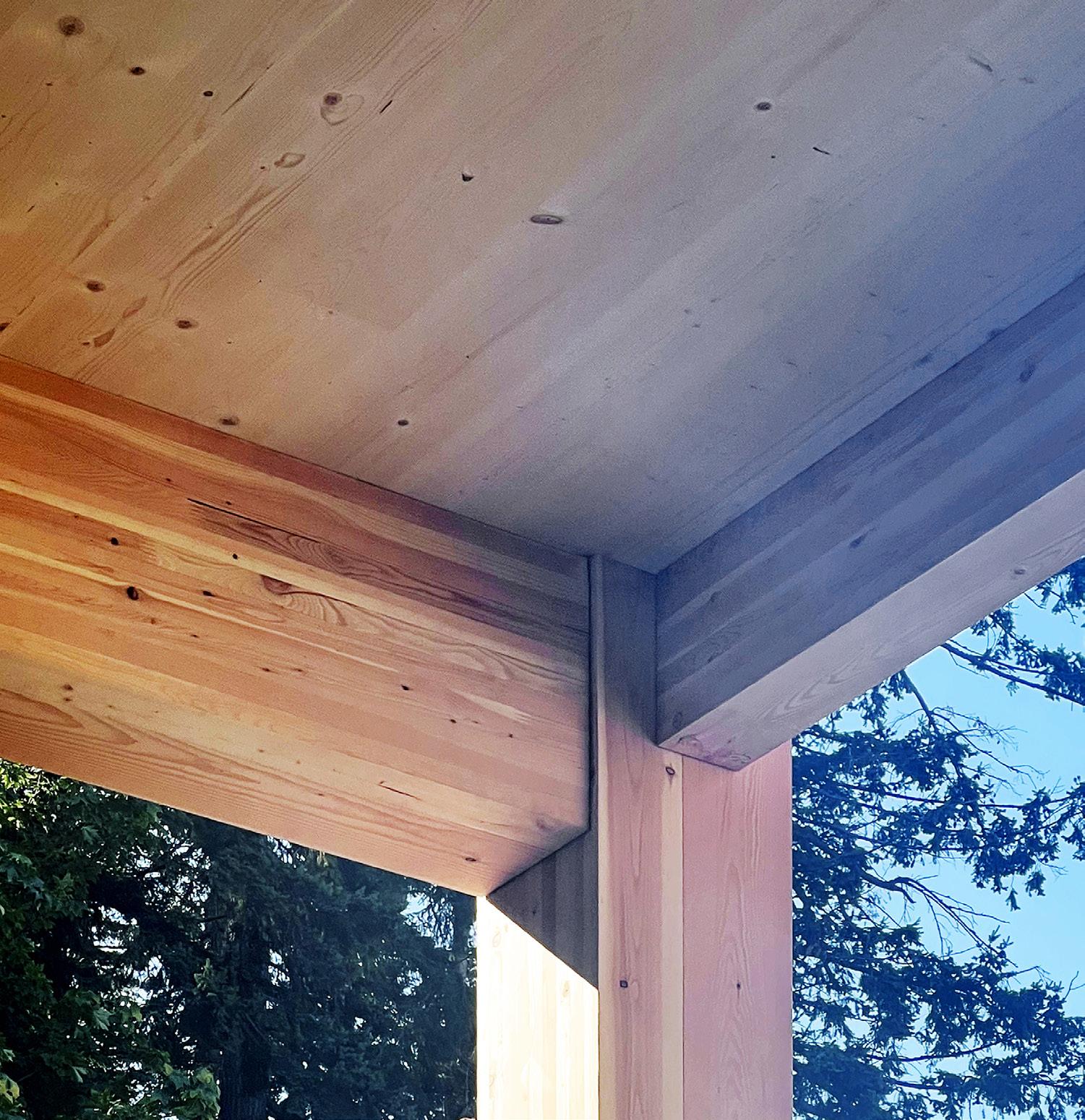
Kaiser Borsari Hall, Bellingham, WA
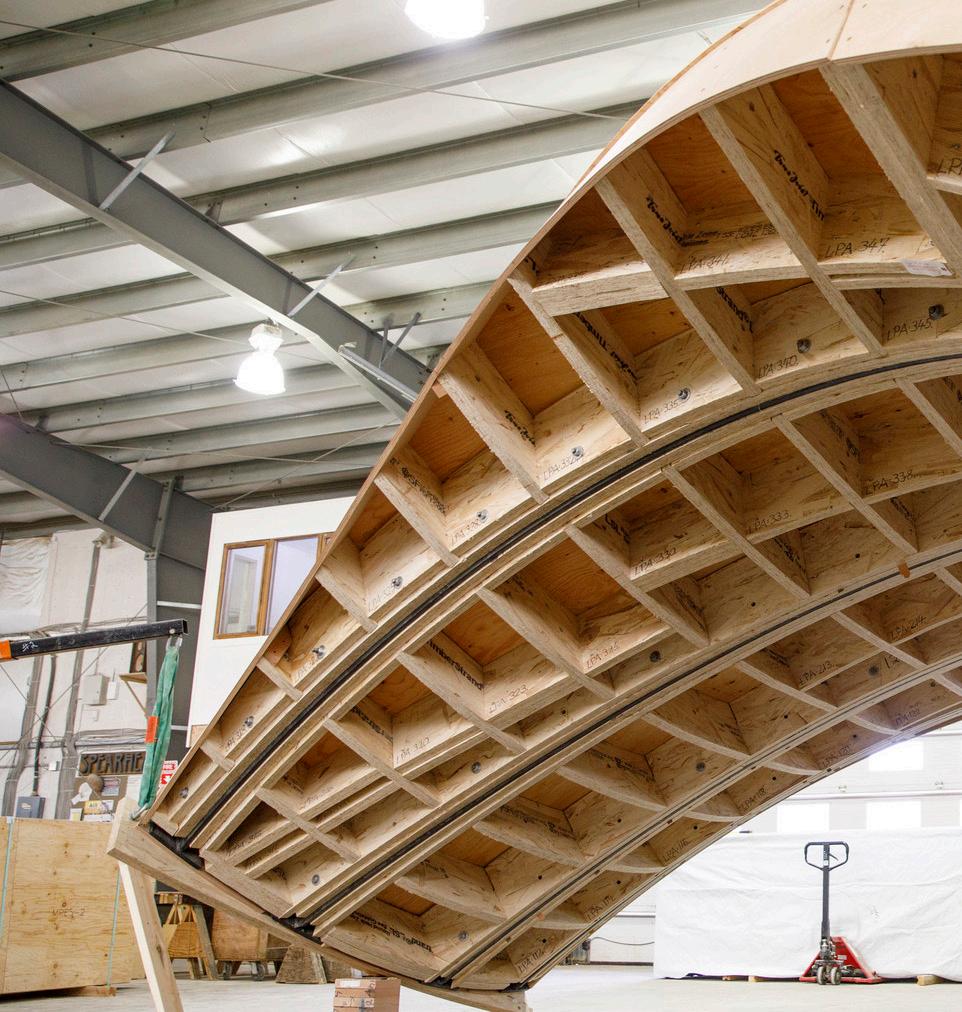
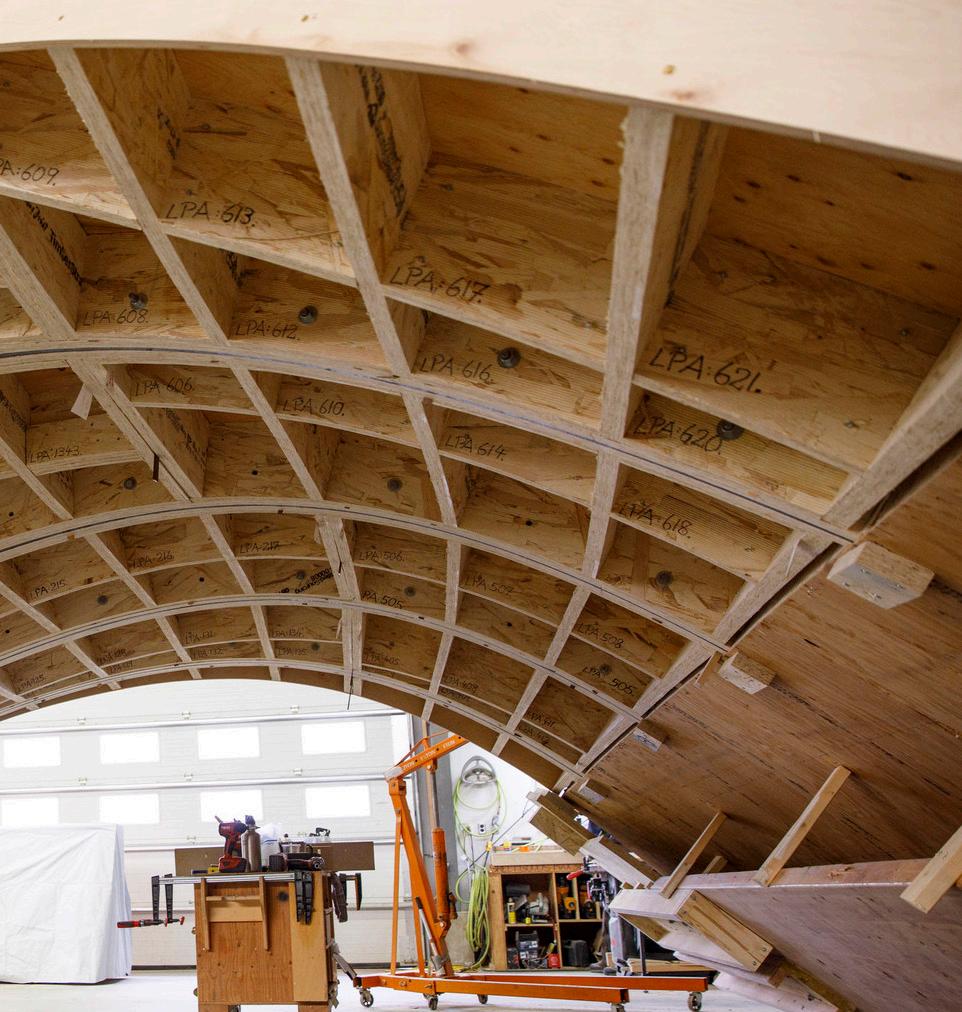
Great Northern Way Pavilion Fabrication Process at Spearhead facility, Vancouver. Image credit: Nick Diamond 07 Design For Manufacture
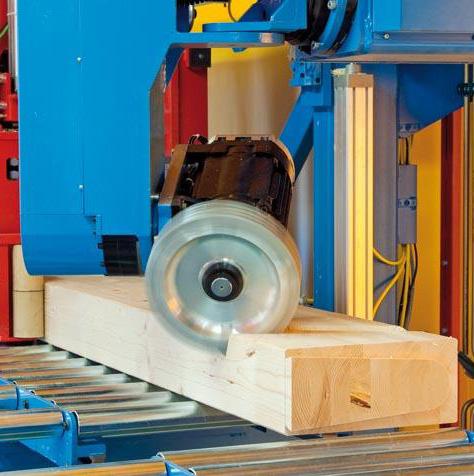
Hundegger 6-Axis Mill Robot Arm. Image credit: Hundegger
Custom is Key
Mass timber manufacturing is a locus where design craft meets digital fabrication at scale. Knowledge of the wood products and equipment that will be used in the fabrication of a project directly impacts the level of design sophistication a team can achieve.
Large format CNC machines process beams, columns, and panels up to 12' wide and 60' long with an array of cutting, drilling and routing tools that allow mass timber to be highly customized for ease of installation, systems integration, and to achieve aesthetic objectives. All panels are passed through CNC machines regardless of how complex the cuts are. Assigning additional cuts, drilling and routing requires deep design and detailing effort, but can save on installation and connections hardware costs, and can elevate the design quality significantly.
Due to risk aversion of multiple stakeholders, many mass timber projects are unoriginal post and beam boxes with little vision put into the detailing. By learning the formal potentials of different mass timber products and discussing fabrication techniques and capabilities of your manufacturer, you will unlock the design potential of wood.
Mass Timber is a Prefab Proposition
More than any other factor, the understanding and appreciation of mass timber as a prefabricated, panelized system will foster the right mindset for success with mass timber fabrication.
Prefabrication is a schedule savings workhorse. The more design thinking you put into the prefabricated elements, the more the savings. This means that deep and regular communication with the fabricator is absolutely essential to generating value through mass timber.
The side effect of deep collaboration with a fabricator is an understanding of the craft of the makers. Understanding the ability of the makers can expand designers' craft.
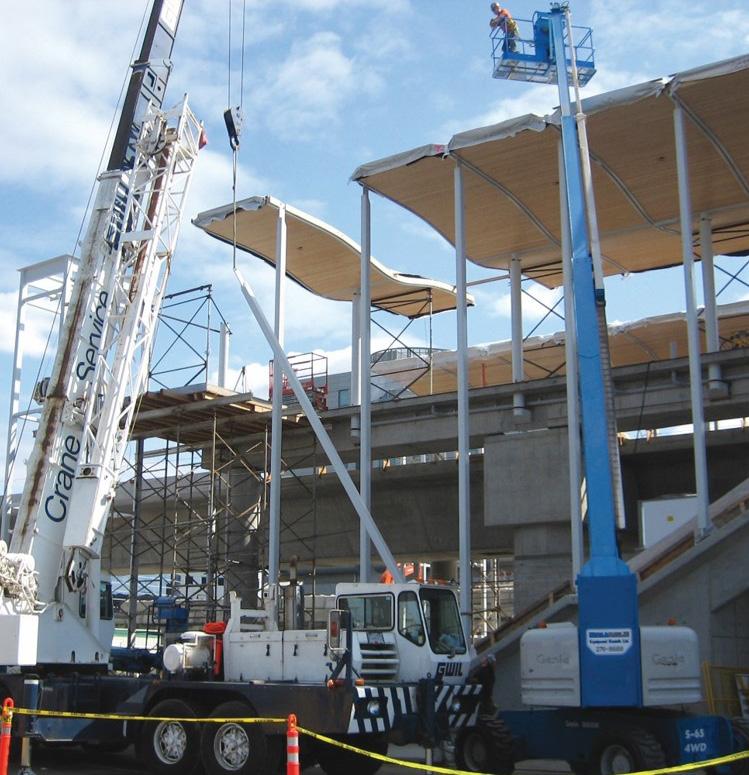
Aberdeen Station, Richmond, BC
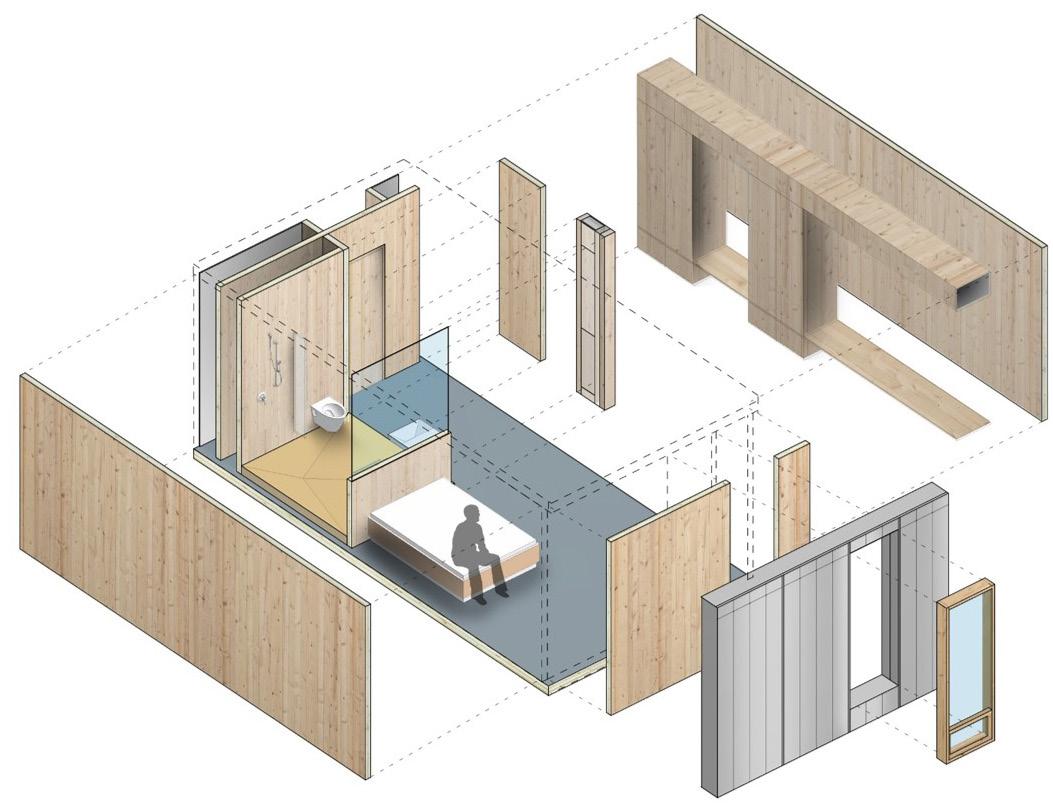
China National Offshore Oil Corporation Worker Housing Module, VAN Studio
Reaching for Prefab Modular
The schedule efficiency of mass timber can be elevated further through the use of volumetric modular fabrication, under the right conditions. If your project is driven by a strong module and has repeated program areas with partitions at regular and closely spaced intervals, consider a volumetric modular approach. Student housing, hospitality, and multi-family projects are all well-suited to volumetric modular mass timber.
Mass timber volumetric modular is uniquely suited to deliver superior performance to other structural materials in the following categories: interior finish quality, structural rigidity, acoustics, insulation, weight, and fabrication precision.
There are relatively few examples of prefab, volumetric modular mass timber buildings on the market, leaving room for much innovation and exploration.
Product Types
When designing for manufacture, consider how your formal objectives lead to specific products, and lead away from others. Structural objectives and formal objectives usually drive the decision, but be mindful of the aesthetic quality of the different products. The composition of each product has a significant impact on the look and feel of the completed design.
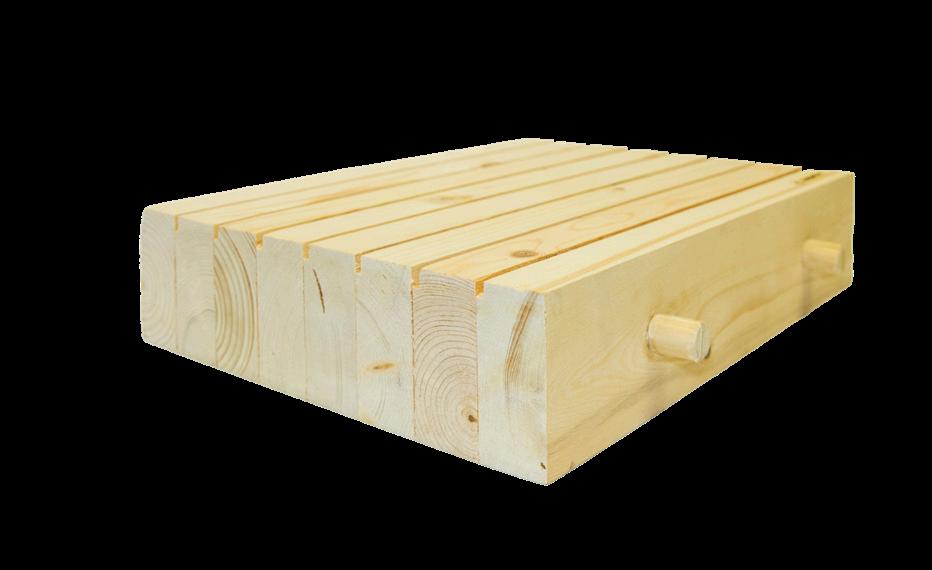
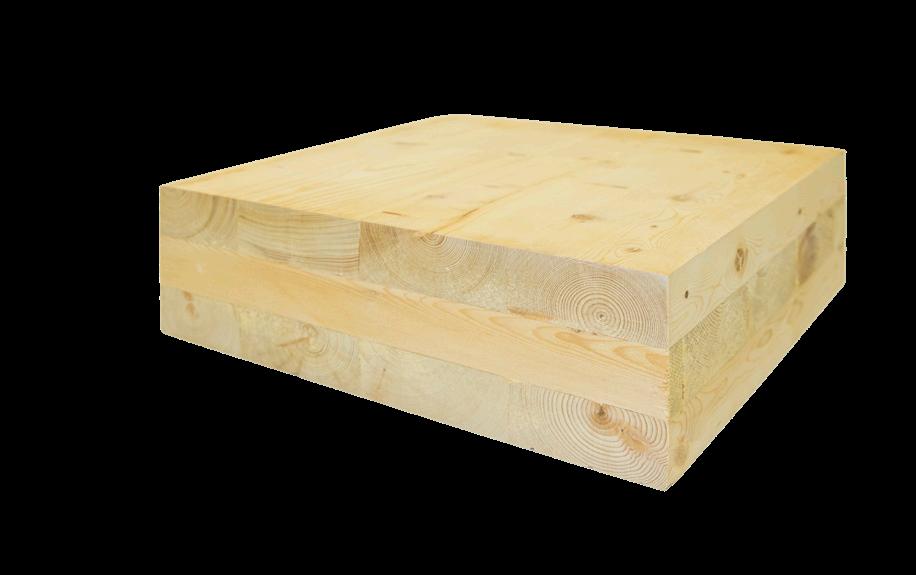
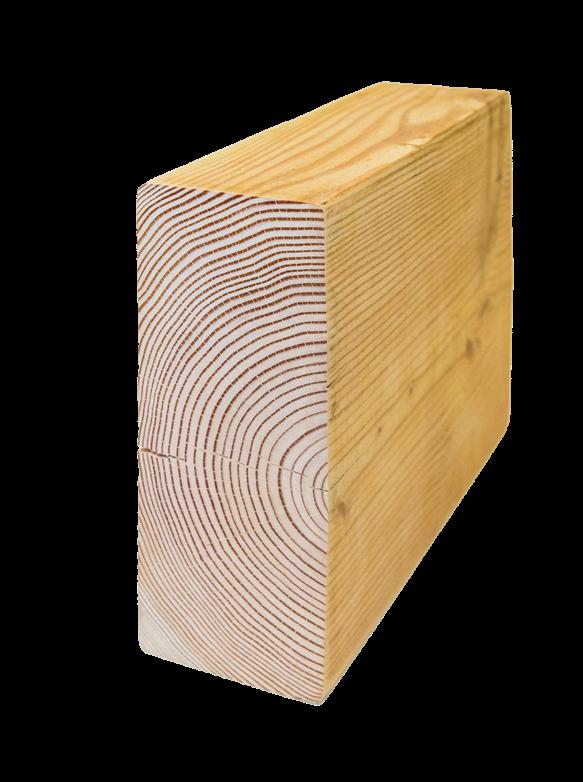
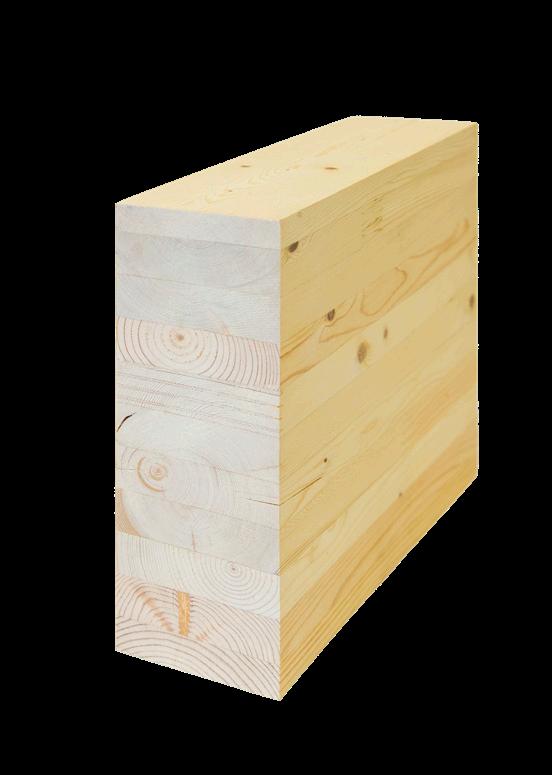
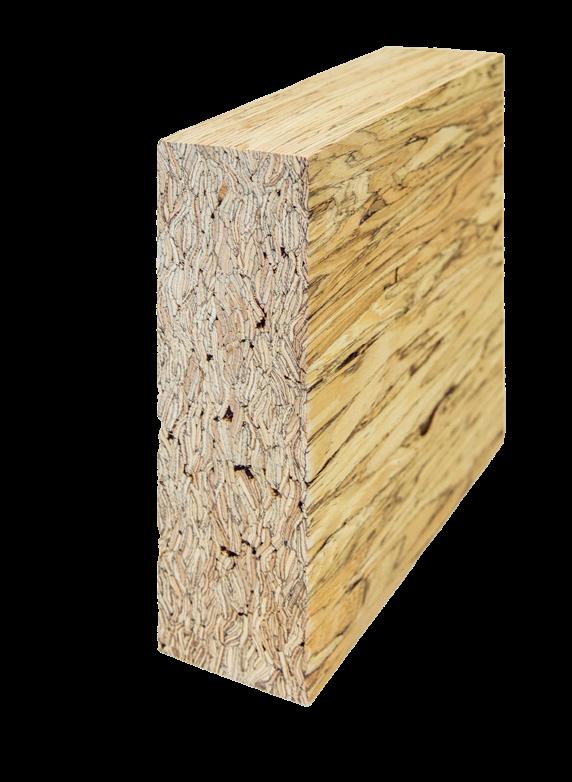
Parallel Strand Lumber
Cross Laminated Timber
Dowel Laminated Timber
Glue Laminated Timber
Solid Sawn Timber
CLT and Mass Plywood panels, while always flat, can be routed, drilled, and cut with miters, dados, etc. NLT is built on jigs and can take complex curvature via ruled surfaces. DLT is always flat but is an all wood product with no glue, nails or screws.
Glulam, heavy timber, LVL and PSL can be cut to accept an infinite variety of off-the-shelf and custom connection types and they can be milled into shapes with varying cross section. In addition, glulam can be inexpensively fabricated with curves, and can even be made with twists.
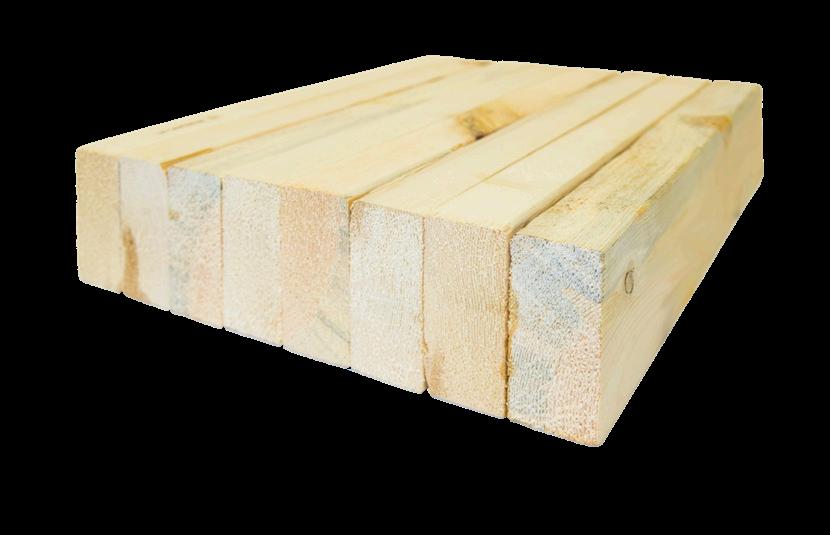
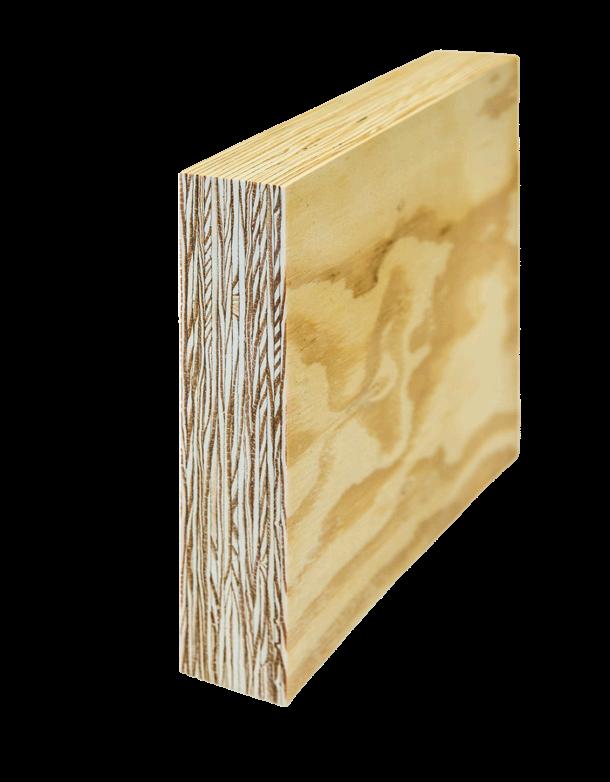
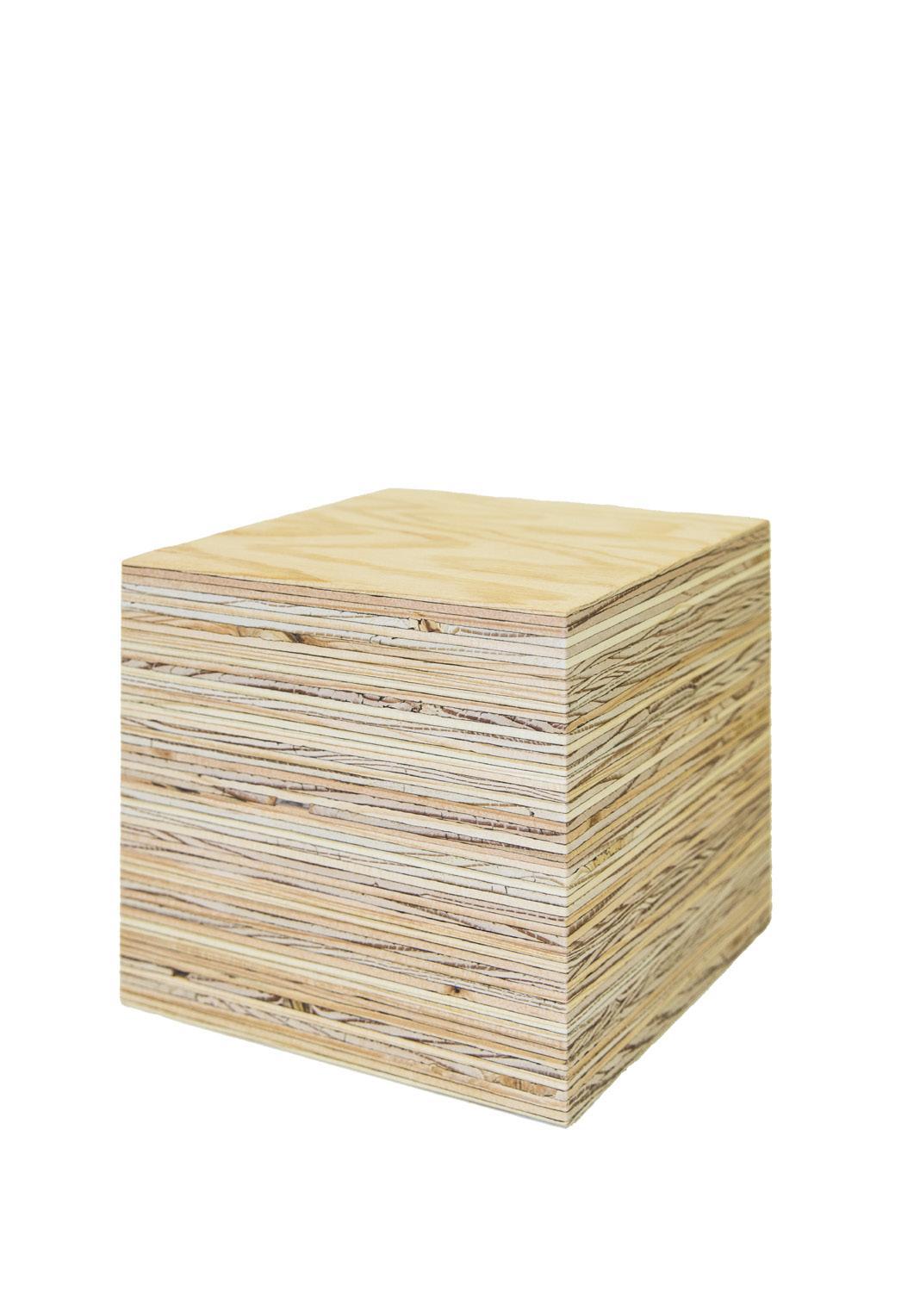
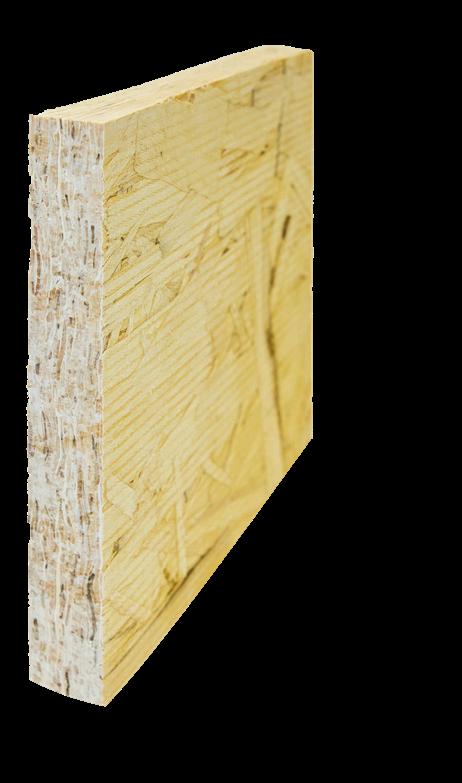
Laminated Veneer Lumber
Nail Laminated Timber
Laminated Strand Lumber
Mass Plywood Panel
Panel Assembly Fabrication
Get to know you fabricator and their equipment. Find out what panel sizes they can fabricate, what angle of cuts they can achieve, what surface textures, routing and milling are possible. Discuss how best to share digital files to clarify precise design intent for custom cuts and routing.
While steel and concrete members can enhance mass timber through hybrid connections and assemblies, fiber-optimized timber connections can also put wood to work rather than depending on other materials to transfer loads from element to element. Design with lap joints, rabbet joints, finger joints, tongue and groove joints and dowels to leverage the inherent strength of the wood.
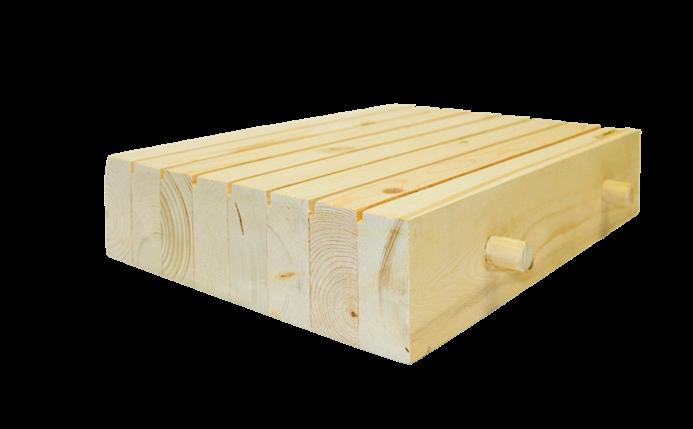
Dowel Laminated Timber (DLT)
2x lumber is stacked on end and then face-drilled and joined with dry dowels that expand with ambient moisture to set the panel. Panels can be post processed through CNC machine.
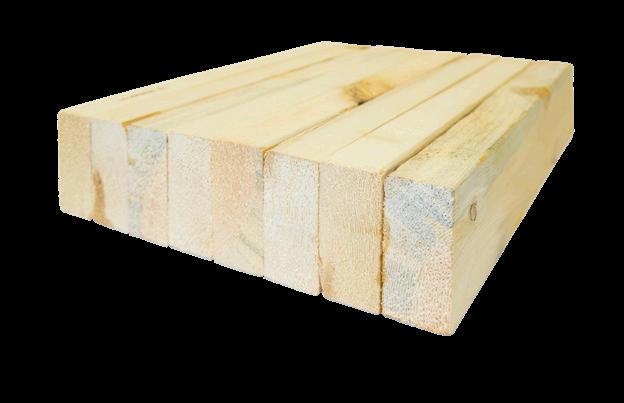
Nail Laminated Timber (NLT)
2x lumber is stacked on end and nailed successively, one board to the next. This allows NLT to be the most formally flexible panel type because each board can be positioned slightly out of alignment with the previous board. Aggregating these offsets can produce twists, curves, etc. Panels are not CNC processed after manufacture due to embedded nails.
Consider using these assemblies as more than floor and roof decks. All of them can be cut to become stairs with treads and risers, load bearing walls or screen walls, and even columns and beams. Consider your structural and aesthetic options with these panel systems and avoid quickly defaulting to glulam post and beam framing for all framing needs. Glulam will always be there for you when you need it. But by using mass timber products in ways that are nontraditional, design and fabrication craft begin to emerge.
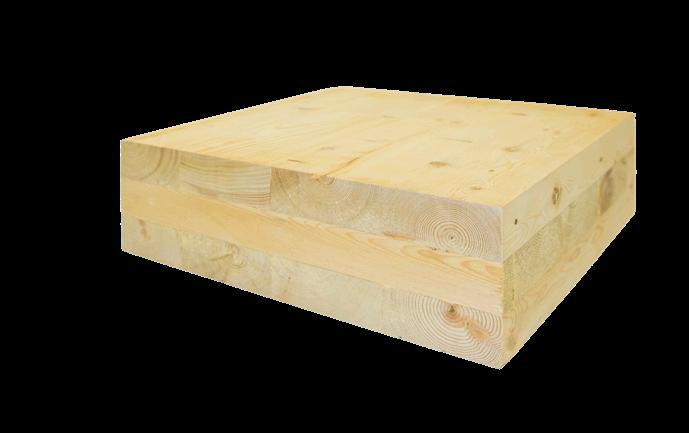
Lam stock is glued and pressed together into large panels (standard size is 10’x40’ with varying thickness). Panel processing is achieved through large format CNC after billet has been pressed and cured.
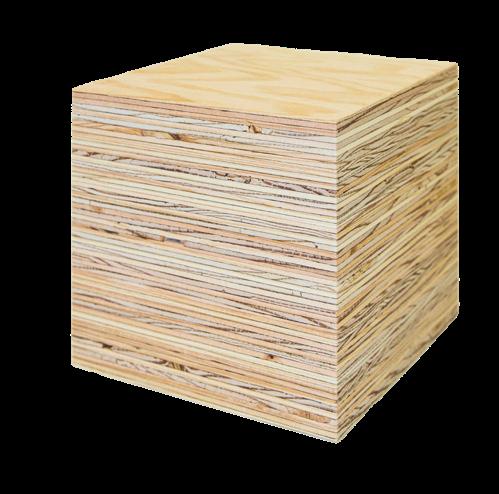
Composed of laminated veneer lumber beams laminated into larger, thicker panels (panel size is 12’x48’ and up to 24” thick). Panel processing is achieved through large format CNC.
Cross Laminated Timber (CLT)
Mass Plywood Panel (MPP)
Column and Beam Assembly Fabrication
Beams and columns can be made from a variety of wood products noted below. Consider the surface character of each of the products and whether or not your members will be visible. In cases where the members are concealed, the strongest member with the lest weight will save cost (LVL, LSL, PSL). In cases where you mass timber is exposed, select products that play well with your material and texture palette.
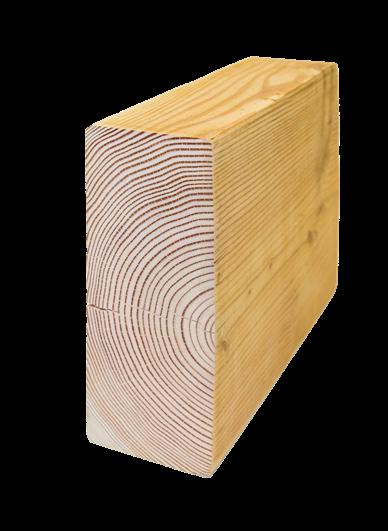
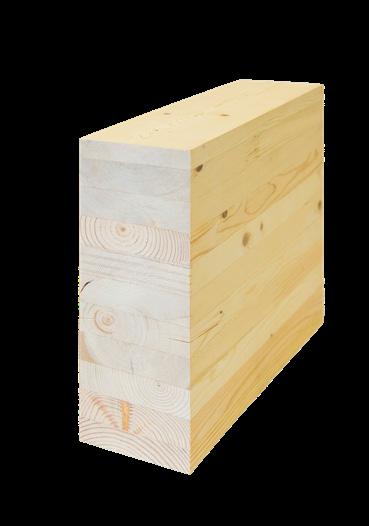
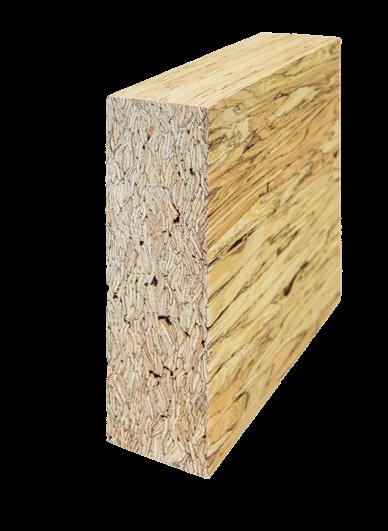
Large wood elements are sawn directly from logs and are dressed to nominal sizes up to 12"x16"x24'.
Lam stock is glued and pressed together into large beams. Max size is typically 14”x48” with unlimited fabrication length. Panel processing is achieved through large format CNC.
The strongest of all mass timber products by weight, PSL is formed from small strips of high-strength wood all oriented longitudinally that are glued and pressed into large members Max size is 12"x18"x60'. Panel processing is achieved through large format CNC.
Solid Sawn Timber
Glue Laminated Timber
Parallel Strand Lumber
If your site is constrained and it is difficult to pick large mass timber deck panels or if large format mass timber panels are difficult to obtain in your region, consider whether your project could use these elements to form walls or floor decks by rotating them 90 degrees. We have successfully installed 48" deep glulam members as roof decks on previous projects.
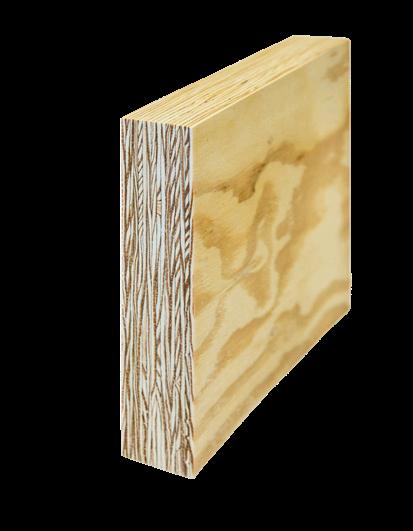
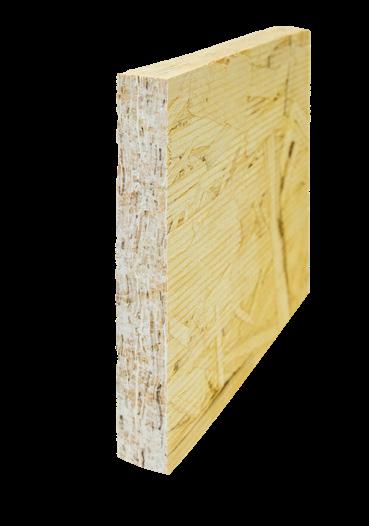
Laminated Veneer is similar to plywood except that all plys are oriented with grain in the longitudinal direction. Plys are glued and laid up and pressed. Max size is 4"x48' and 5.25" thick. Members are CNC processed.
Laminated strand lumber is similar to PSL, except that the strands are not as long and are not all oriented in the longitudinal direction. Panels are glued and pressed into large panels up to 8'x48' and 4" thick. Members are CNC processed.
Laminated Veneer Lumber (LVL)
Laminated Strand Lumber (LSL)
To illustrate the flexibility of mass timber to achieve the complex forms, consider the Van Dusen Botanical Garden roof and columns. The roof is composed of prefabricated panels composed of 2x members spanning between curved glulam beams. The panels are each uniquely curved and fit into a composition that undulates across the site. The columns are machined solid sawn timbers with tapered ends. The joints are expressed in steel.
Van Dusen Botanical Garden, Vancouver, BC 1
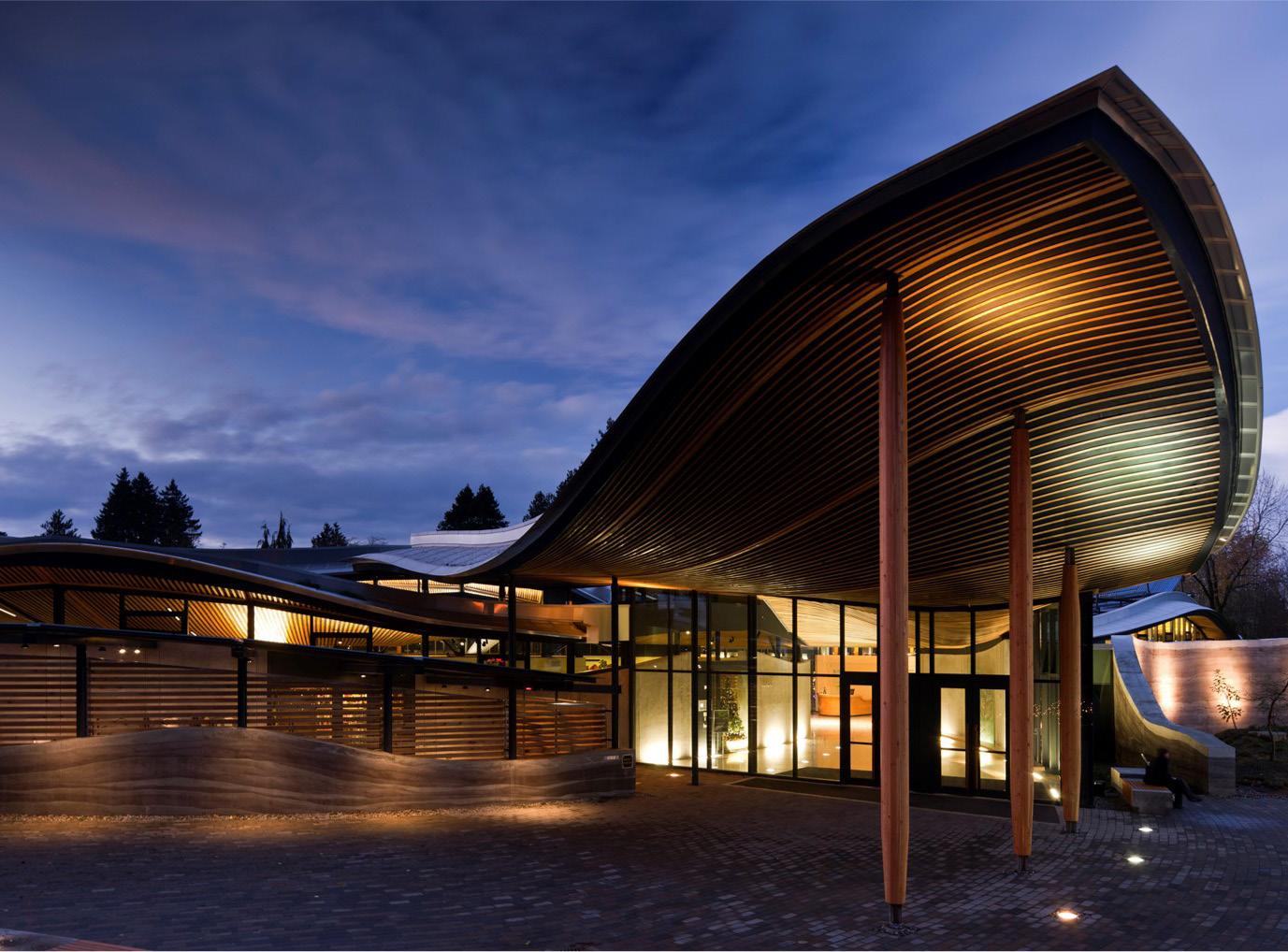
There are many ways to leverage mass timber for formal exploration. Study the products and the fabrication techniques to identify the right products for the look, feel and shape of your project.
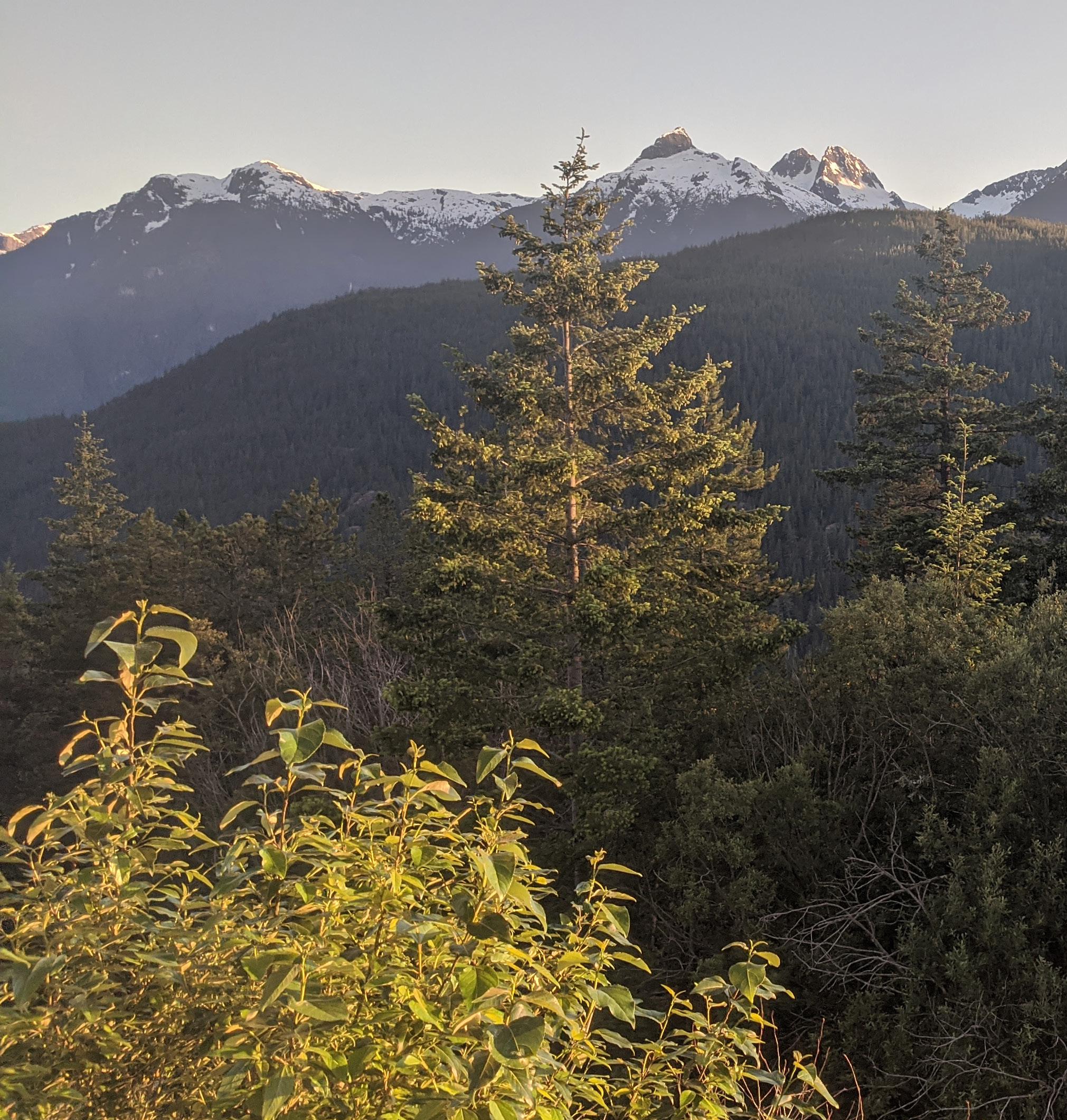
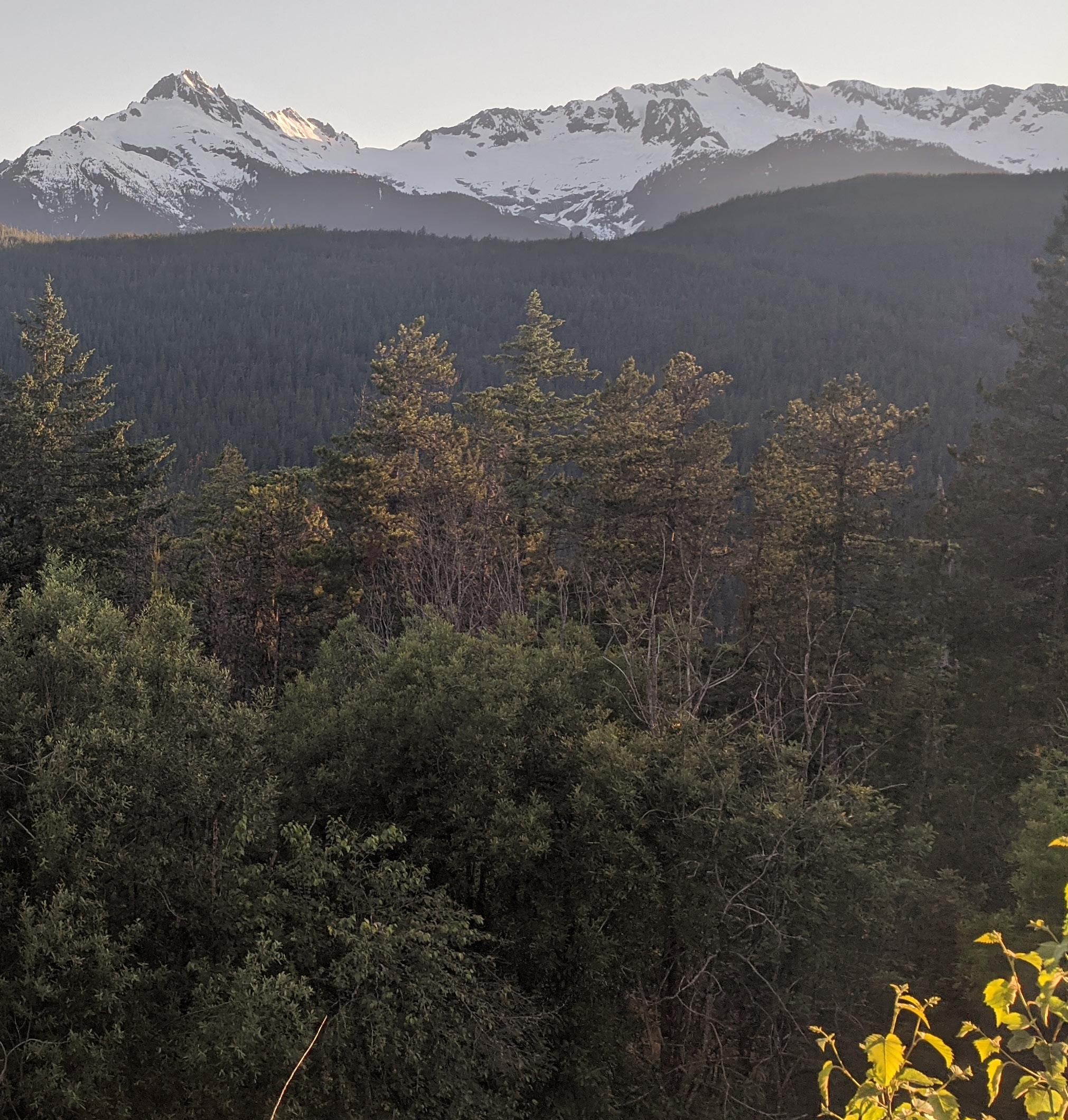
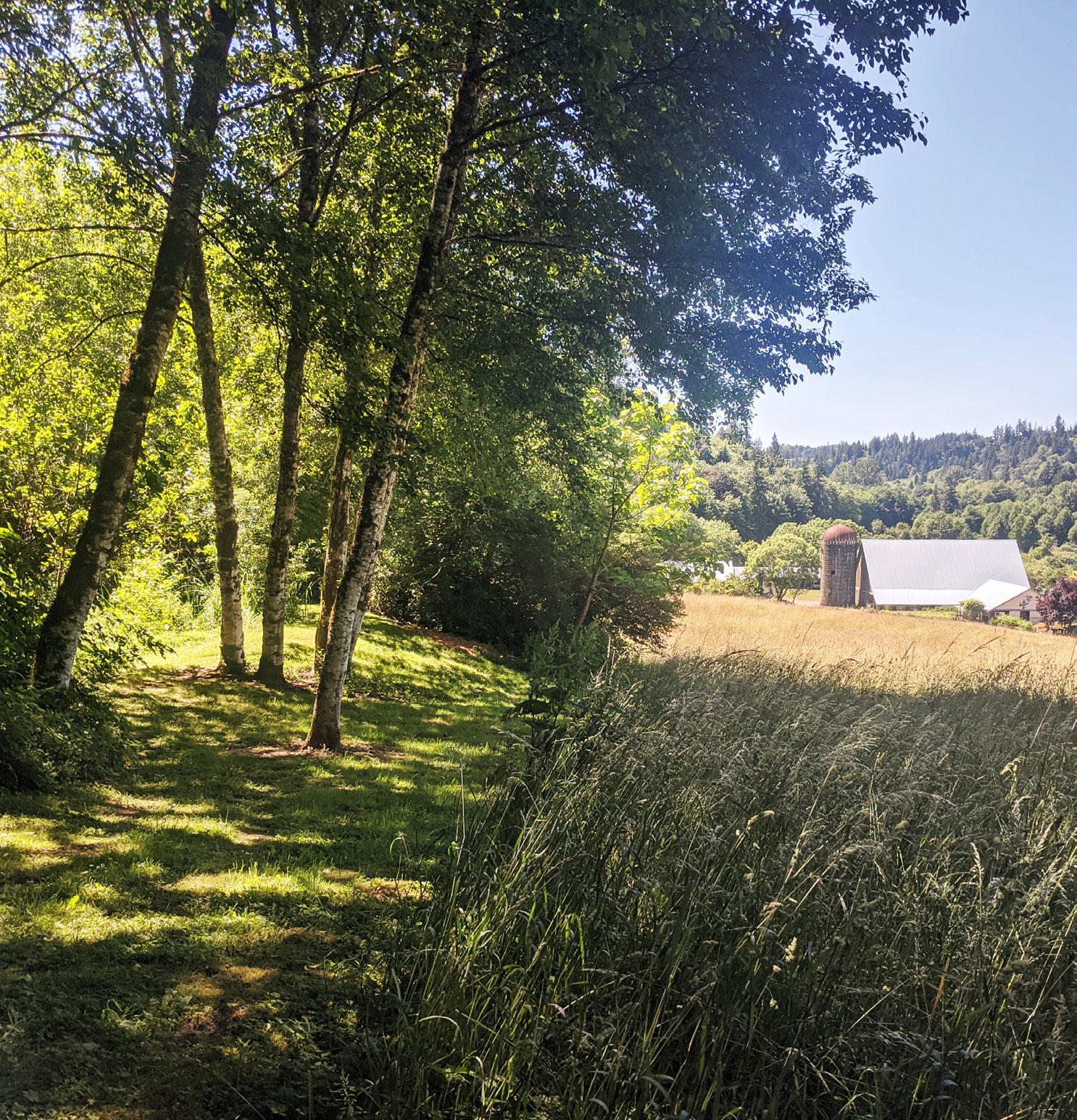
Wild Thyme Farm, Oakville, WA
Forest Management and Responsible Procurement
Sourcing sustainable mass timber can be a challenge. The supply chain is long and has a variety of stakeholder structures. Forestry certifications can be difficult to compare, and the environmental impacts of living systems like forests are challenging to quantify. While industry, forestry, and transparency stakeholders are working toward solutions, designers have a role to play in ensuring that projects use sustainably sourced wood and in promoting change in the industry.
At Perkins&Will, we have advocated for the use of certified wood, highlighting FSC as a gold standard because we trust this promotes a healthy planet. In general, this has served us well. However, this guidance is not the only path to sustainable wood sourcing. FSC 100% mass timber products (where all materials come from FSC certified forests) are uncommon in North America (1). Several suppliers offer FSC Mix, but at varying percentages, and we must consider:
Is the non-FSC fiber coming from responsible sources? If FSC or other certified wood is not available or is not an option for a project team, what are other acceptable paths to sustainable mass timber procurement?
One method to begin answering these questions is to study the region where a project’s wood comes from and understand both forest health and land management patterns. At a broad scale, in the United States, 39% of forest land is owned by individuals and families (2). For many small landholders that are managing their own forests, FSC is not a viable option due to cost and extensive reporting requirements (3). Canada faces a different scenario: approximately 94% of Canadian forest lands are owned by public and governmental entities and are governmentally managed (4). Canada manages 37% of the world’s certified forest area, and PEFC is the most common certification in Canada and many other parts of the world (5).
While the specifics of forestry certifications vary, at a base level, each certification entity is committed to improving sustainability and supporting biodiversity (6). Adoption of biologically based and carbonstoring building materials like mass timber is a core strategy for the building industry to mitigate contributions to global warming. However, this strategy will be most effective if project teams strive for procurement that contributes to stable or increasing forest stocks, more transparency, and continual improvement of forest management practices.
Sustainable Timber Sourcing Objectives
Procurement of legal wood from regions with stable forest stocks and sound land management regulations provides regional incentive to manage and maintain a working landscape. Beyond this, teams can invest in conversations with stakeholders to understand and support the following Sustainable Timber Sourcing Objectives:
Understand Regional Impacts
Only procure timber from sources that can verify harvest from healthy and stable forest stocks, unless procurement is part of an ecologically restorative forest management operation.
Freshly harvested wood is inefficient to transport because it is round and has high water content, so most mills’ “wood baskets” are within a 50-75-mile radius of their source forests (this radius is greater under some circumstances). This region may provide a team with clearer information about which forests a project’s wood may come from.
However, once the wood is dried, milled, and fabricated into mass timber, it may be transported across the world to a project site. Whether wood is procured from across the world or across the street, the project team will need to engage in inquiry to ensure that their timber is not contributing to loss or degradation of forests.
Promote Environmental Impact Transparency
In addition to requesting certified timber, teams can request information to help validate, to the highest resolution possible, the source location(s) of a project's timber buyout. At a minimum, a team could ask for the GIS coordinates of a mill, the radius of the wood basket that accounts for 90% by volume of the material that the mill processes, and the year of harvest for the material supplied. While optimal forest management practices may vary greatly within a radius of this size, this information will allow a team to assess the source region and consider whether additional inquiry is needed.
Additional resources to support sustainable procurement are quickly evolving. These include improvements to product-specific Environmental Product Declarations (EPDs) for mass timber and an array of sourcing and traceability tools (7). These resources are emergent and cannot be explored within the scope of this guide.
Potential Wood Baskets for Two Timber Mills
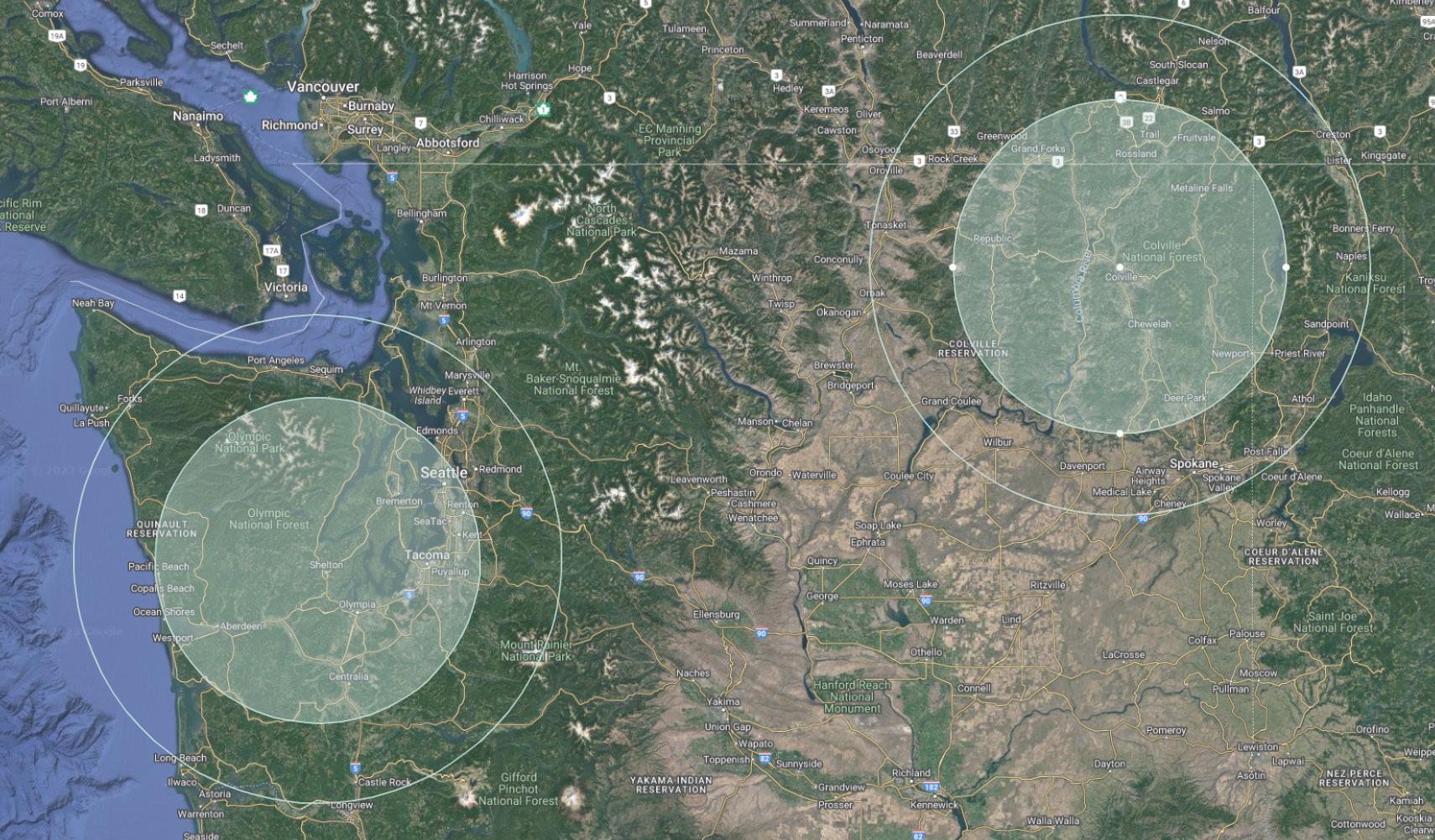
50-mile radius
75-mile radius
For illustration only; does not represent the actual supply area of either mill
Image Source: Google Maps, 2023
50 & 75 mile radii from each: 1) Sierra Pacific Industries Mill in Shelton, Western WA; 2) Vaagen Brothers Mill in Colville, Eastern WA
Riparian Management Zones
Core Zone Core Zone
In certified and sustainably managed forests, management activities near the "core zone" of rivers, wetlands, and shorelines are focused on restoration.
Basal Area Measurements
Diameter at Breast Height (DBH) = Diameter of a tree at 4.5 feet above ground
Basal area of each tree = Cross-sectional area at breast height
The basal area of a stand of trees (before or after harvest) is measured by the area of all species or stems in a stand at breast height per unit of land area.
Increase Carbon Sequestration and Support Biodiversity
Best management practices optimize each stand's harvest frequency to support ecosystem services and increase residual basal area (the density of "leave trees" that remain standing after harvest), as well as riparian buffers and diversity of species in a forest.
Harvest cycles that are optimized for profit may not always align with optimization for carbon sequestration and ecosystem health. Depending on a stand's specific location and species composition, longer harvest cycles may lead to increased wood volume, carbon storage, and resilience against fire (8). So long as seedlings have access to sunlight, increased basal area can support age diversity, supporting healthy soils and mycorrhizal networks (9). Riparian buffers and diversity of species support habitat preservation and watershed health, contributing to healthy environments for fish, land-dwelling creatures, birds, and pollinators. Biodiversity of tree species can also help a forest resist blight.
Additional Objectives
Certification standards share additional objectives for sustainable forestry (10), including:
• Preservation of old growth and primary forest (not previously logged)
• Training and continual improvement of forest management practices
• Restriction of Genetically Modified Organisms (GMOs)
• Support for and promotion of Indigenous People’s Rights
Other objectives for consideration, which may not be captured by certification, include:
• Forest soil health
• Improve resilience
• Rural community equity
• Conservation and recreational access
• Safety and workers’ rights
• Manufactured product impacts on human health (e.g., reduction and elimination of VOCs)
• Waste reduction in the forest through the manufacturing, construction, and installation processes
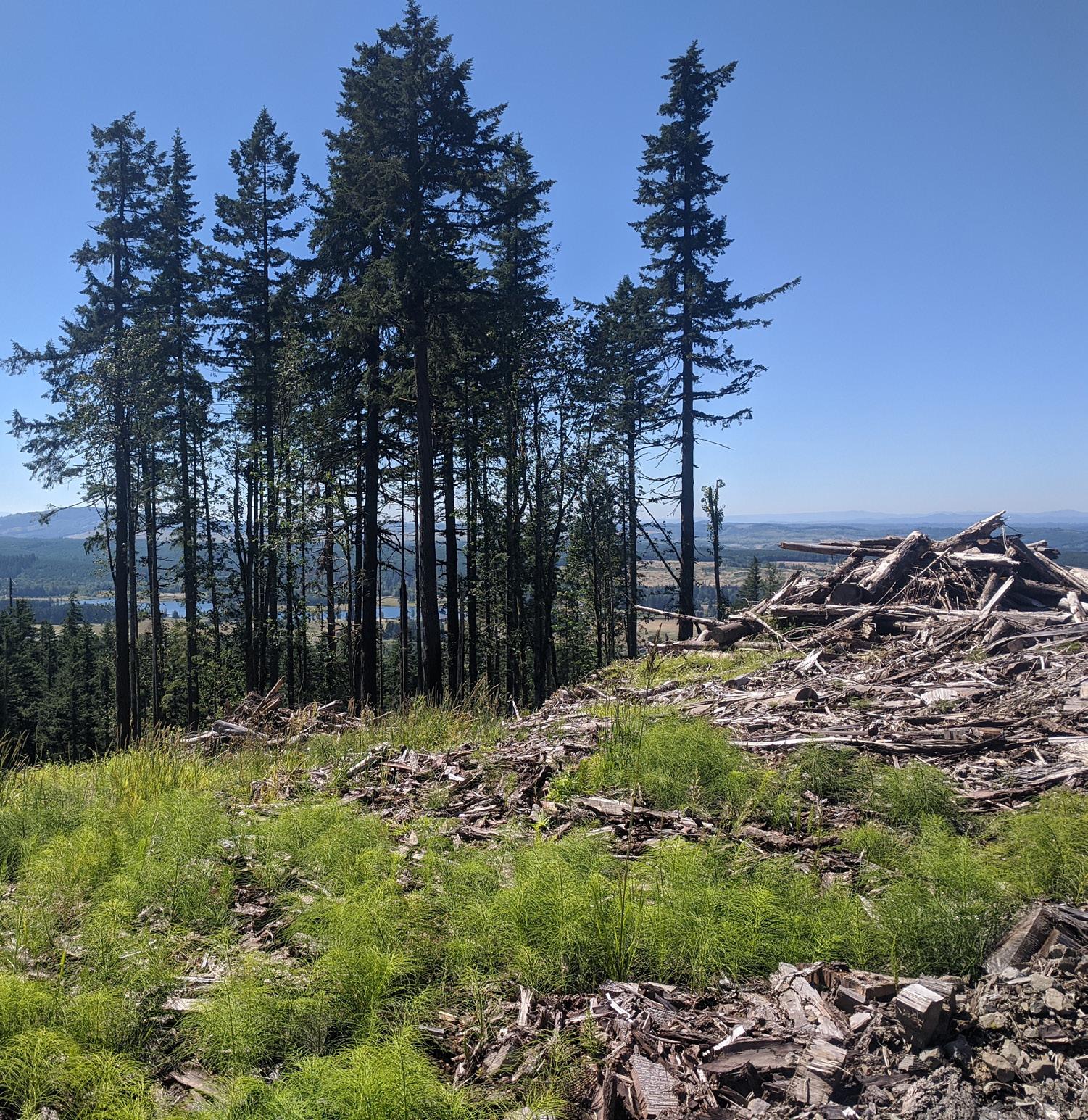
Washington State Department of Natural Resources Tree Farm: "leave trees" and slash after harvest
Wood Souring Stakeholder Engagement
Many players influence the degree of sustainability embodied in the wood fiber of mass timber products and buildings. The primary stakeholders include:
• Certification Entity (FSC, SFI, PEFC, CSA, ATFS, etc.)
• Landowners and Managers (TIMO, REIT, Family, Tribal, Gov.)
• Lumber Mills
• Mass Timber Panel Manufacturers
• Fabricator Subcontractors
• General Contractor
• Project Client
Landowners and lumber mills have the biggest impact on the availability of sustainable mass timber. Landowners decide how to manage their forest (sustainably or not), and mills determine which landowners they will source timber from. It is worth noting that logging companies are not influential stakeholders because they are agents of mills and landowners, following whatever harvest protocol is required by the mill and landowner.
As forests are owned and managed by many types of entities, including federal, state, tribal, private industry, and private non-industry groups, the goals and objectives of each vary. While forest managers are experts in a complex domain, many owners are motivated to manage their land in response to regulations and market demand. A team may be able to secure timber that meets specific requirements through early planning. However, it is important for teams to advocate for an increased budget to account for management practices that add value to timber products. If discriminating owners increase demand and willingness to pay for higher-resolution traceability and specific management practices, suppliers will respond.
Mills do not sort logs by the stand from which they are harvested. They sort them by species and diameter and stack them into the log deck with all the other truckloads of lumber coming in daily or weekly. In addition, mills do not sort outgoing lumber by the stand from which it is harvested. They sort lumber by species, size, grade, etc. Consequently, when a mass timber manufacturer sources lamstock from various mills, the only way to ascertain the sustainability of the resulting mass timber products is to ensure ALL the wood going in and out of ALL the source mills is from sustainable forests. This is not currently a standard offering from North American suppliers.
Questions for Conversation and Verification
To make an impact on projects, teams need buy-in from clients that meeting the Sustainable Timber Sourcing Objectives to the maximum extent possible is a clear goal. From there, they can work with the general contractor to select a suitable fabricator who works with suitable mills. This can only be done by augmenting specifications and having real-time conversations with fabricators and mills, whose upstream supply, certifications, and Environmental Product Declarations (EPDs) represent opportunities for discussion.
The following list of questions for mills and fabricators will help initiate this conversation. Dialogue promotes transparency and helps the team and client develop confidence in the products procured for the project.
Questions for Mills
1. How do you work with landowners to ensure your wood sourcing promotes equity, biodiversity, water quality, and carbon sequestration?
2. What sustainable forest management certification(s), if any, does your company use: FSC, other certification, no certification? What social and environmental advantages does your approach offer?
3. What is your maximum stand-to-mill distance for hauling logs?
4. What type of landowners do you work with, by percentage?
5. How do you sort your logs, and how do you sort your lumber? What is your methodology for timber source accounting? For instance, do you tag logs from different stands, and do you tag lumber from different tree stands?
6. Can you provide lumber buyers with GIS information for the tree stand(s) where 90% or more of a buyout comes from as well as the year of harvest? At a minimum, can you provide GIS coordinates that define your wood basket and the sourcing year for a buyout?
7. Can you certify that no forest conversion or harvesting from prime forest will be included in the source material (unless this sourcing is tied to an ecologically restorative forest management initiative)?
8. As the industry works to develop product and source-specific EPDs (more specific than industry-average EPDs) for downstream products like glulam and CLT, how do you intend to participate?
Perkins&Will has corresponded with several mills to obtain a sense of the state of the industry. Mills have expressed a range of responses.
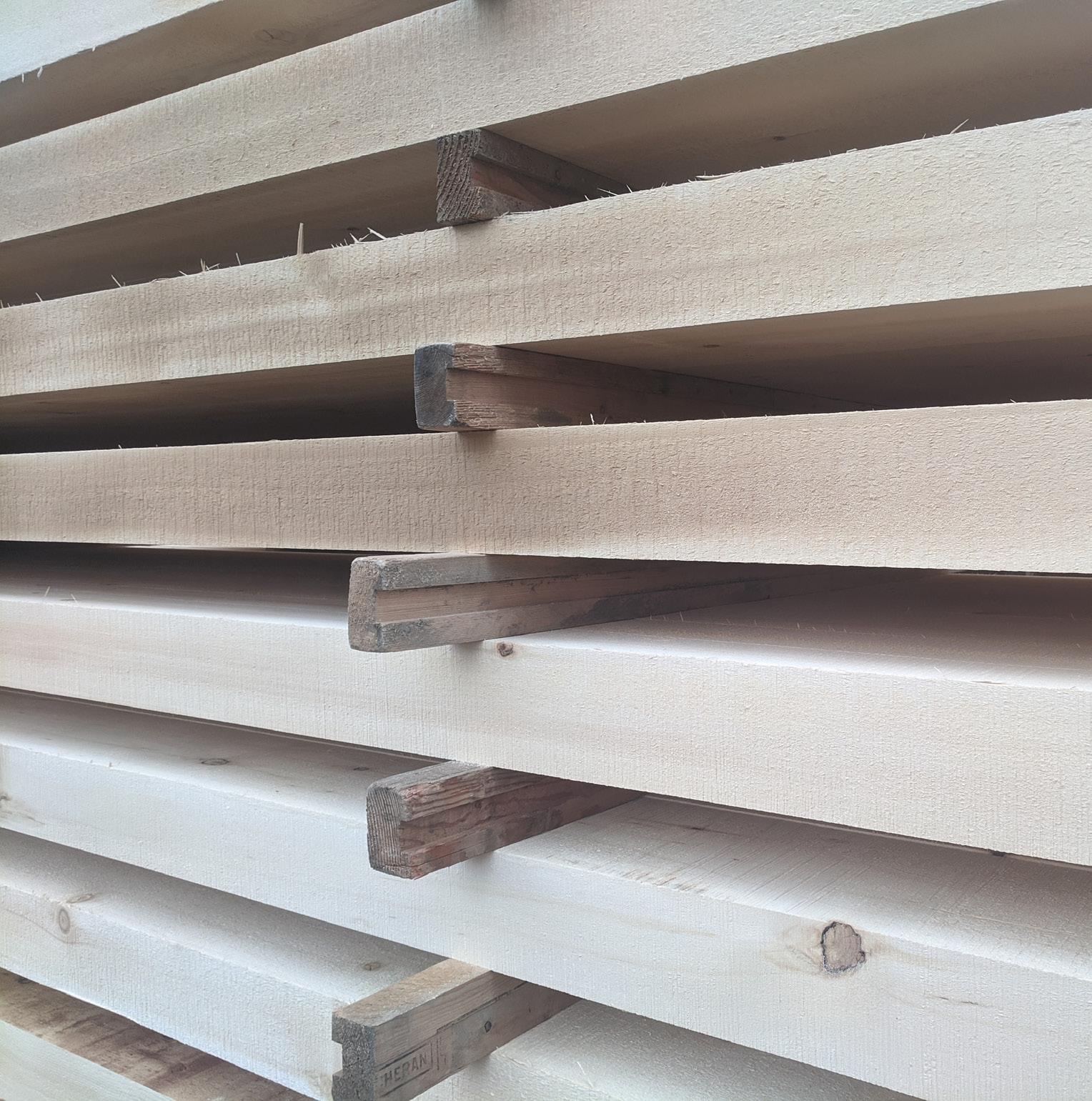
Squamish, BC
Questions for Fabricators
1. How do you work with mills to ensure your wood sourcing promotes equity, biodiversity, water quality, and carbon sequestration?
2. What is your methodology for timber source accounting? For instance, do you require inventory control from your mills?
3. For a specific project, can you provide us with GIS information for the source forests where 90% or more of the lumber used in your products comes from, as well as the year of harvest?
4. Is the lam stock in your products certified? If so, to which standard(s)?
5. Do you have product-specific EPDs that include source-specific data for the timber used in your fabrications (more specific than industryaverage EPDs)? If not, are source-specific EPDs forthcoming?
As with mills, fabricators have expressed a range of responses to the above questions. The fabricators who are most aligned with our Sustainable Timber Sourcing Objectives have expressed that they are currently finalizing EPDs, but some still rely on industry average wood impact data (source-specific data is required to understand localized impacts). They are also limited to the mix of wood that suppliers in their region can provide. Very few fabricators can provide stand locations for their products' timber harvests because they source from multiple mills. Mills should be able to provide coordinates of their wood basket; however, even with mills, stand-specific information is less common. This means that only some of the wood in any given mass timber panel meets the objectives of even the most sustainably minded fabricators.
Apart from certification, one path to sourcing transparency is procurement from a “vertical” supplier (i.e., a fabricator or manufacturer who manages their own land and mill) whose land management practices align with our Sustainable Timber Sourcing Objectives. Another path (though rare) is targeting buyout from specific tree stands, leading to complete chain of custody for every fiber. The latter path requires a mill to be aware of and prepared to collaborate to achieve the intention well in advance and to plan for storage and a dedicated run of milling for that specific wood. This is disruptive and costly for the mill, and associated costs are passed on to the project.
If none of these options are available, a team may need to communicate further upstream to learn more about the forestry practices associated with a wood product.
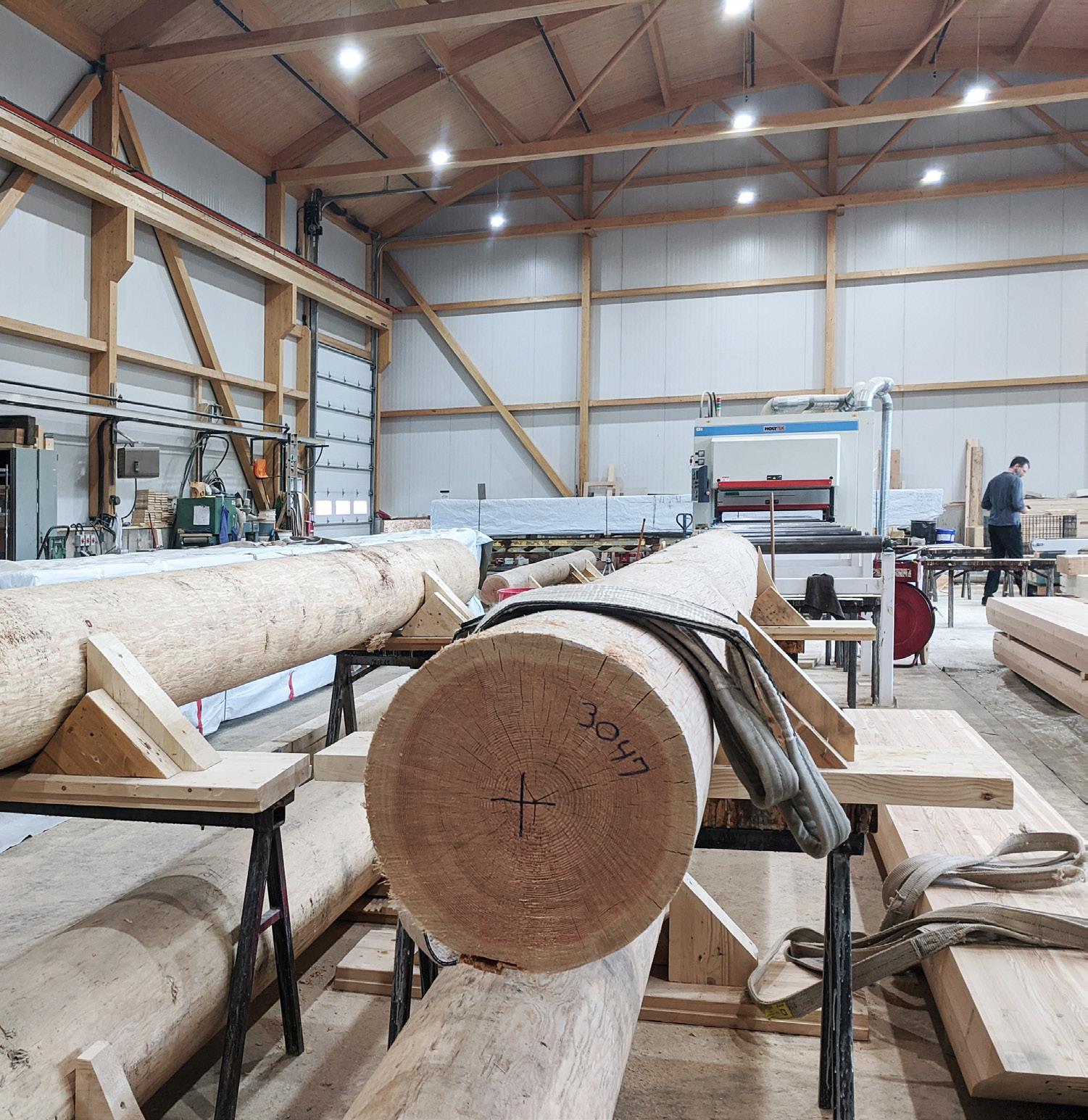
Art Massif Structure de bois, Saint-Aubert, Quebec
Wood Sourcing Stakeholders & Communication
Mass Timber Material Flow
Forest Land, BMP's & Certifications
Landowner(s) and Land Manager(s)
Lumber Mill(s)
Manufacturer(s)
Upstream Communication
Many steps occur between a forest, its management practices, and a finished mass timber project. Depending on how many entities are involved across these steps, a design team may need to communicate upstream, at least as far as a lumber mill, to validate sustainable forestry practices for each mass timber product. The questions presented throughout this section provide a starting point for conversation. Ideally, key requirements to validate sustainable sourcing will be translated into specification and bidding documents. (11)
Increasing the demand for sustainable forest management and harvest necessitates a multi-pronged approach through projects that require certified wood, teams that communicate up the supply chain to improve transparency, and industry collaboration to improve standards and regulations, develop source-specific EPDs, and elevate best practices.
Many steps occur between a forest, its management practices, and finished mass timber project.
Subcontractor or Fabricator
Contractor
Owner & Project
Design Team
Wood
Sourcing Communication Flow
Sustainable Sourcing References
1. Everett, Aaron et al. "Climate Smart Wood Procurement Guide". Climate Smart Wood Group, 2022, 19. https://www.climatesmartwood.net/wpcontent/uploads/2022/11/Climate-Smart-WoodProcurement-Guidance.pdf
2. "Forest Ownership Statistics". National Association of State Foresters, 2018, https://www. stateforesters.org/timber-assurance/legality/ forest-ownership-statistics.
3. "Carbon Narratives for Design Planning". Institute For Health in The Built Environment, 2020, https://buildhealth. uoregon.edu/carbon-narratives-for-design-planning
4.“Forest Land Ownership“. Natural Resources Canada, 2020, https://natural-resources.canada. ca/our-natural-resources/forests/sustainableforest-management/forest-land-ownership/17495
5. Fernholz, Kathryn, et al. "Forest certification update 2021: the pace of change". Dovetail Partners, 2021. https://dovetailinc.org/upload/ tmp/1611160123.pdf.
6. Fernholz, Kathryn, et al. "Differences between the Forest Stewardship Council (FSC) and Sustainable Forestry Initiative (SFI) certification standards for forest management". Dovetail Partners, 2011. https://www.dovetailinc.org/report_ pdfs/2011/dovetailfscsficomparison32811.pdf
7. As an early example, the American Wood Council recently introduced a wood sourcing tool: “How Can I Tell If Wood Is Sustainably Sourced?”. American Wood Council, awc.org/wood-sourcing.
8. Diaz, D.D.; Loreno, S.; Ettl, G.J.; Davies, B. "Tradeoffs in Timber, Carbon, and Cash Flow under Alternative Management Systems for Douglas-Fir in the Pacific Northwest". Forests, 2018, 9, 447.
9. Jabr, Ferris. "The Social Life Of Forests (Published 2020)". NY Times, 2020, https://www.nytimes. com/interactive/2020/12/02/magazine/treecommunication-mycorrhiza.html
10. Fernholz, Kathryn, et al. "Differences between… certification standards for forest management". (n 5)
11. Climate Smart Wood Group is collaborating to design two model specification approaches: “Specification Language.” Climate Smart Group, 31 Oct. 2023, www.climatesmartwood.net/procure/ specification-language.
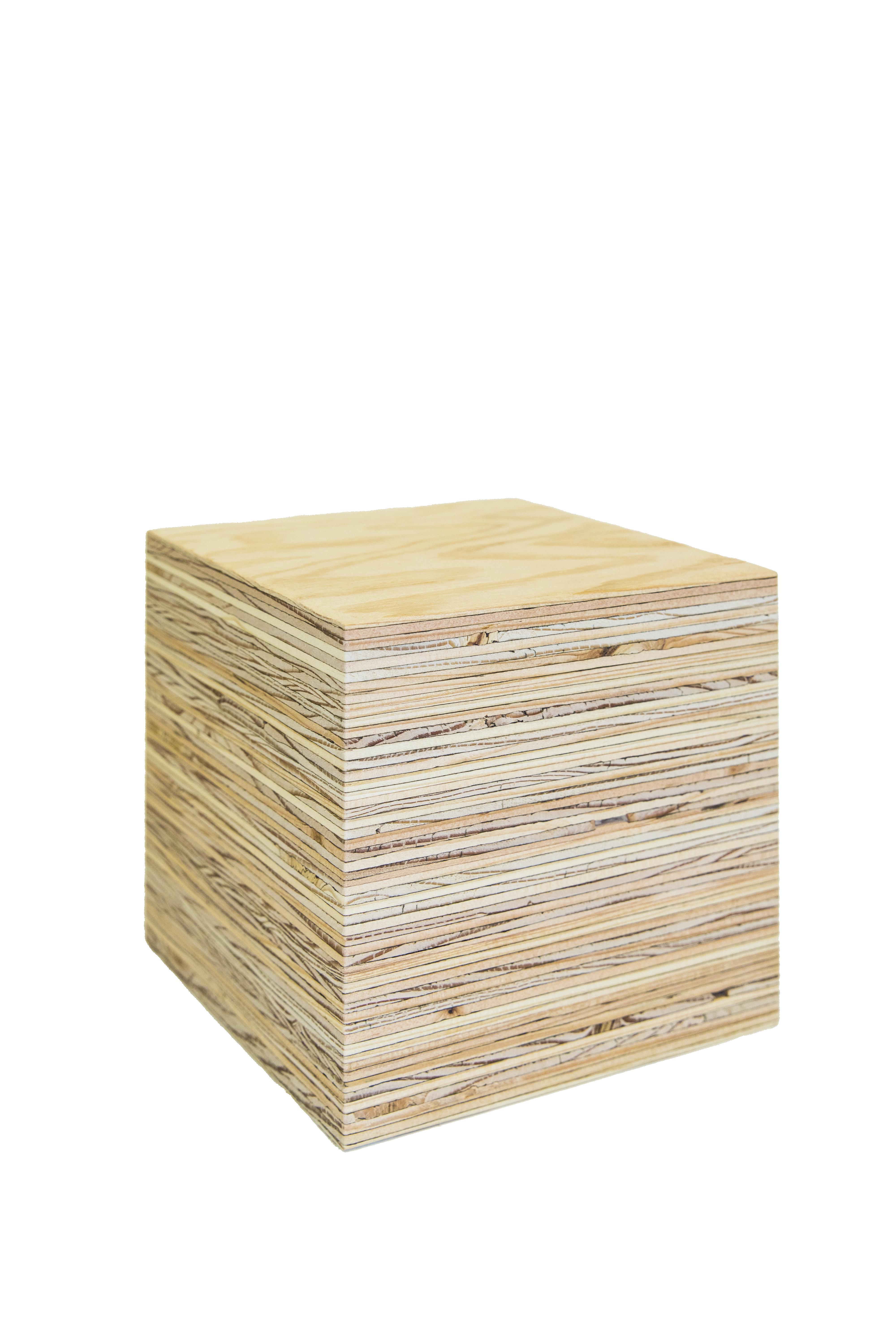
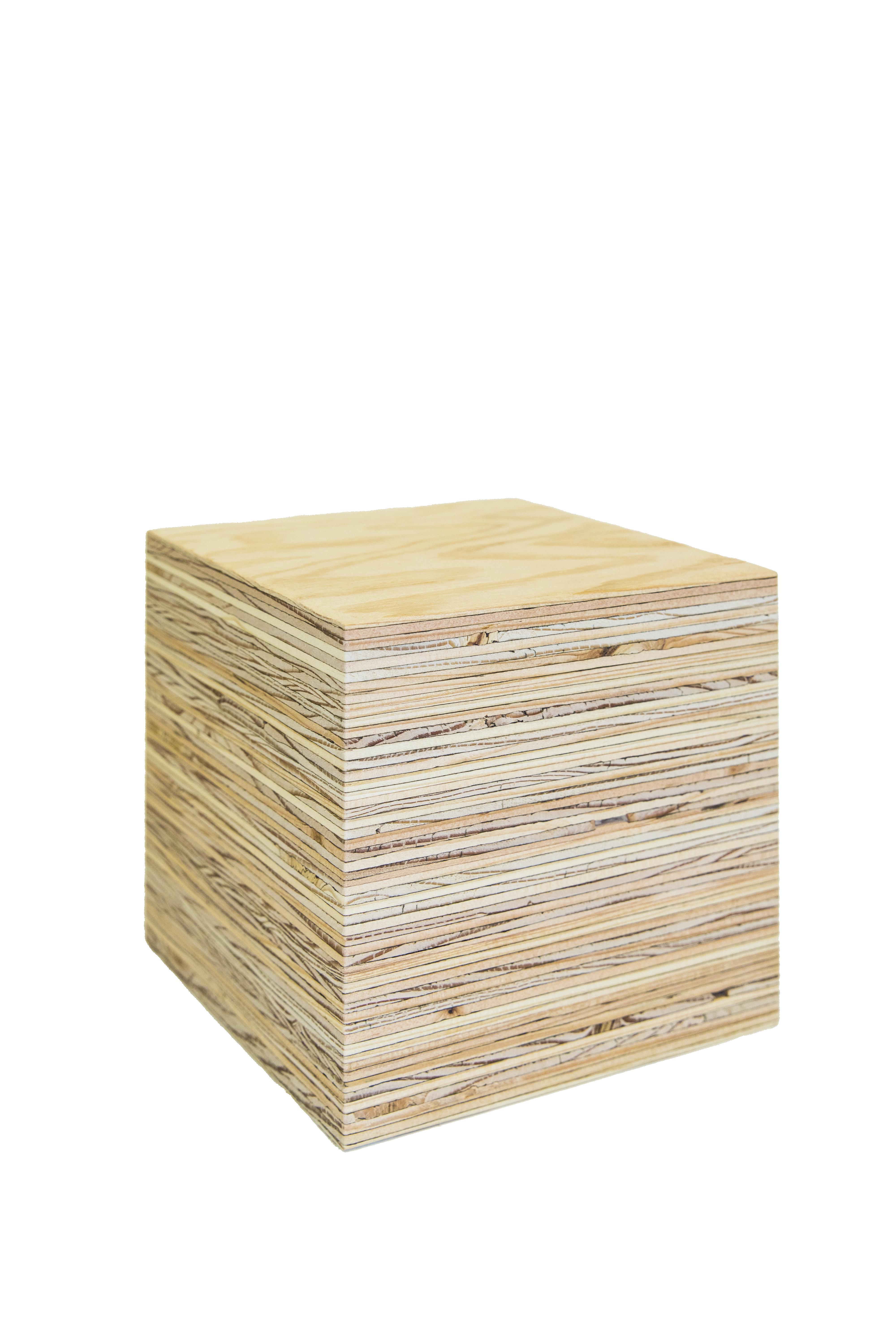
09 CASE STUDIES
1 De Haro (San Francisco)
GNW Pavilion (Vancouver)
Southwest Library (Washington, DC)
Soo Valley Prototype Home (Vancouver)
REM Train Stations (Toronto/Vancouver/Los Angeles/San Francisco)
SFU Stadium (Vancouver)
Camp Lakota (Los Angeles)
1 De Haro
San Francisco, CA
Sector: Commercial Office
Studio: SF
SE: DCI Engineers
GC: Hathaway Dinwiddie
Fabricator: Nordic
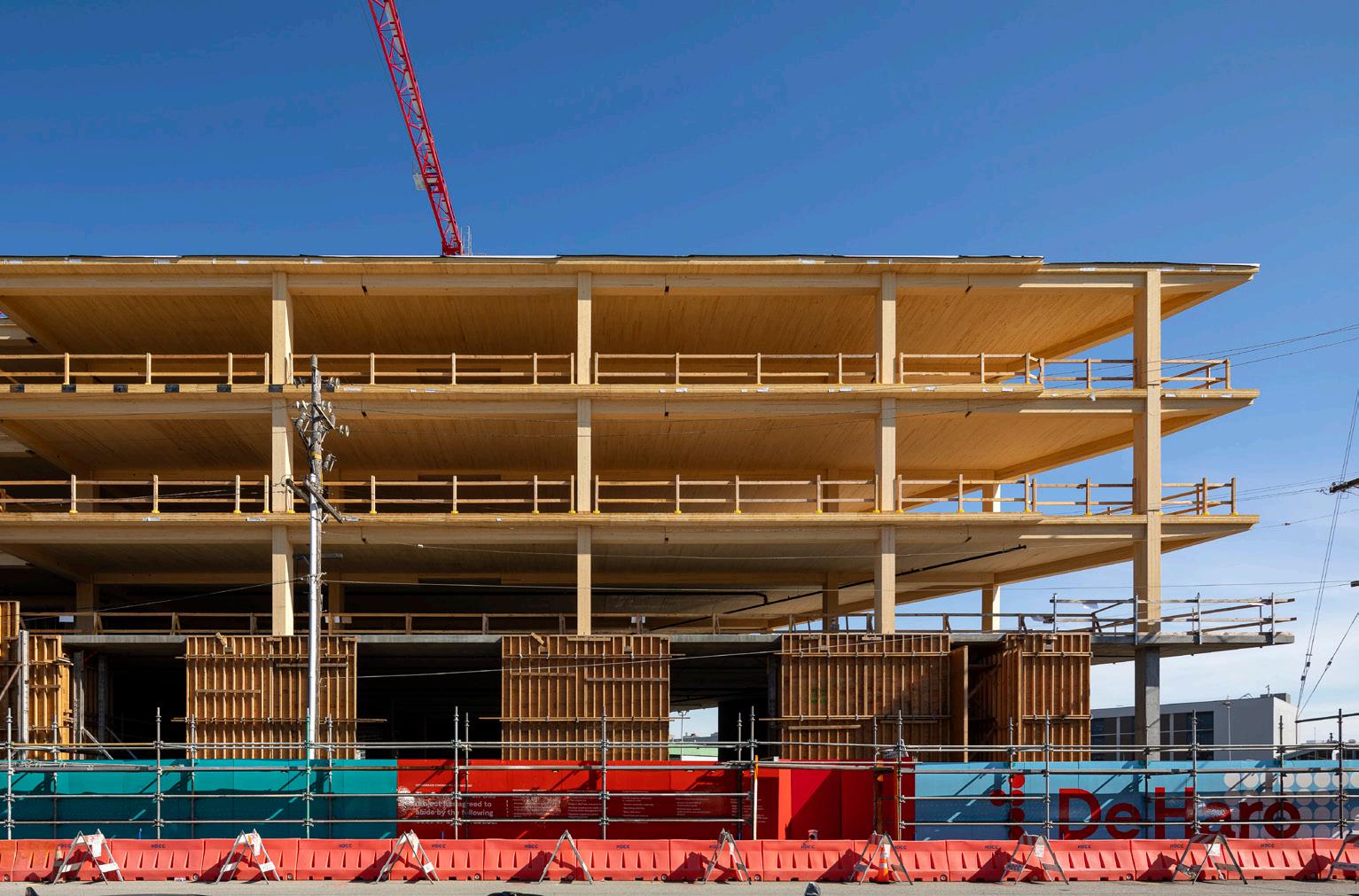
Selecting Mass Timber
Perkins&Will proposed the use of mass timber on this project. Client requested a cost comparison of concrete and wood at the end of DD. After costing, client felt that mass timber was worth the small material cost premium when weighed against other benefits of mass timber, such as a cheaper foundation.
Mass Timber Parti
Unique beam-through-column detailing and beam-to-beam connections draw attention to the material tectonics and craft in fabrication. Exposed wood provides a warm interior without the need for added interior finishes. Mass timber is visible from the exterior through transparent façade and innovative slab edge detail.
Project
Delivery Model
Architect was prime with SE sub. GC was brought on after entitlements as design builder (MEP). Mass Timber was Design Assist/Fab-Install.
View from De Haro St. 1
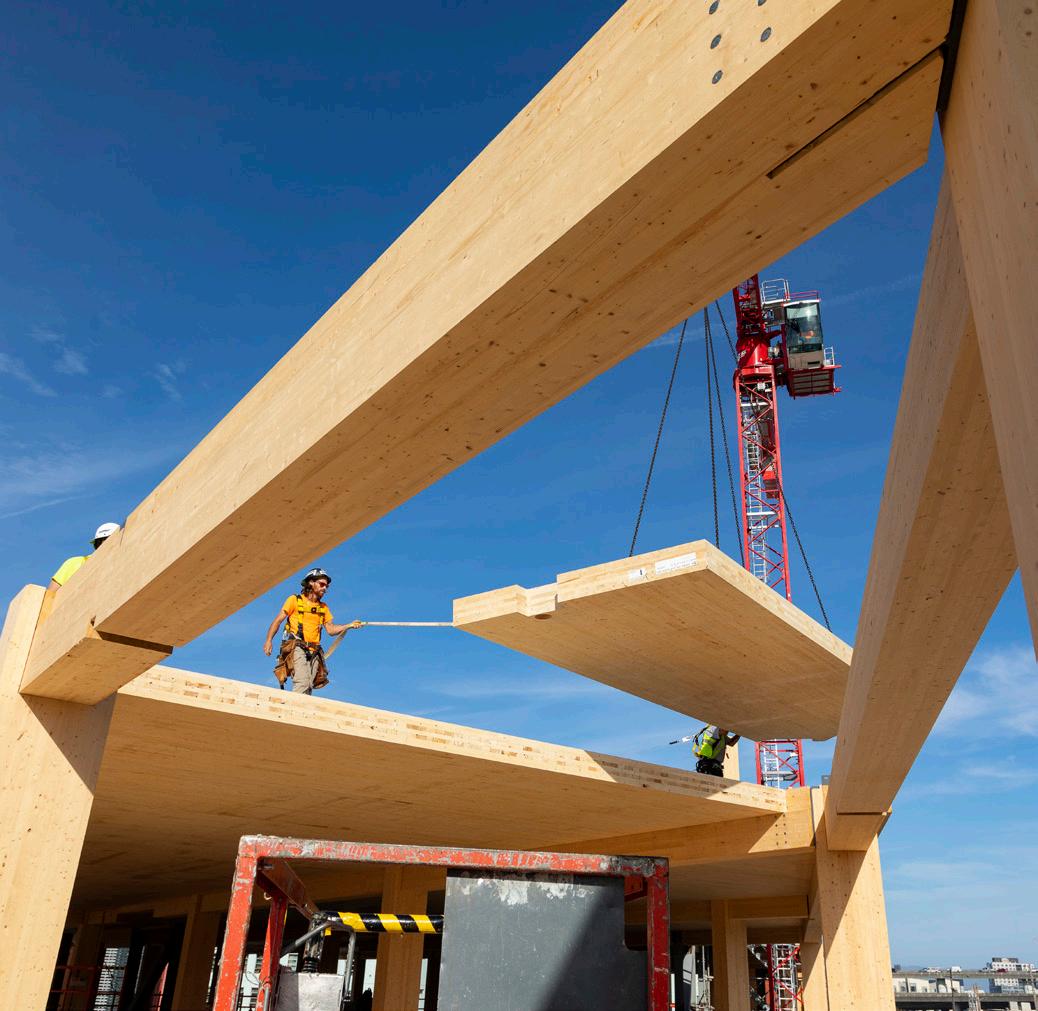
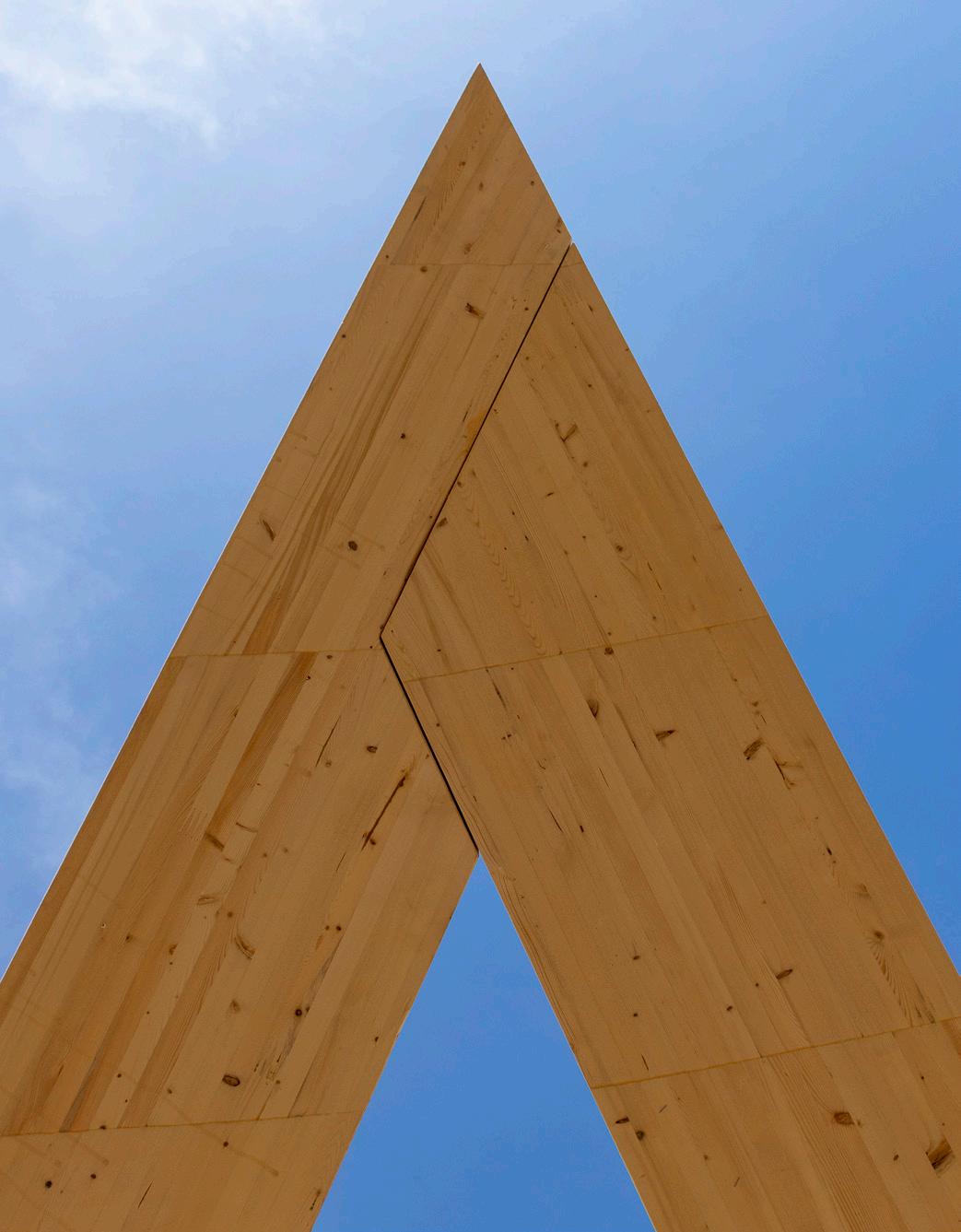
Prior Experience with Mass Timber Design Architect and SE only.
Design Lead for Mass Timber
Structural Engineer was very experienced and took the lead in developing the system.
Systems Integration strategy
Glulam beams were notched to allow duct runs. All mass timber penetrations 2” and larger were prefabricated.
Code and AHJ challenges
Timing and schedule were affected by City Deliberations because this was the first large mass timber project for San Francisco. After entitlements, the permitting process was difficult because the team realized at 50% CDs (structure permit submission) that UL listings
1 De Haro Image credits: Kyle Jeffers
do not exist for mass timber and they had to find fire ratings solutions without changing the structure before they reached 100% CDs. A fire engineering code consultant led the conversations with the AHJ. Hilti supported the process by drawing details and a third party engineer prepared engineering judgments, for slab edge and other conditions.
Cost and Schedule
There was a small premium on mass timber material. Construction achieved schedule savings as a result of careful systems integration during design.
Slab Edge Beam Through Column 1 2
TYP.
What went REALLY well?
Early systems coordination (driven by the need to prefabricate the mass timber) was very effective in delivering schedule savings.
What were the precious lessons?
In the absence of UL listings for mass timber, early identification of required engineering judgments is key to a smooth design process. Construction schedule savings are delivered on the backs of the design team doing early and thorough coordination as well as shop drawing review during design phases. Fitting CA work (mass timber shop drawing review) into the design phase was a staffing challenge.
Typical Framing Bay Size: Mass Timber Elements:
Great Northern Way Pavilion
Vancouver, BC
Sector: Commercial/Retail
Studio: VAN
SE: RJC Engineers
GC: Ledcor
Fabricator: Spearhead
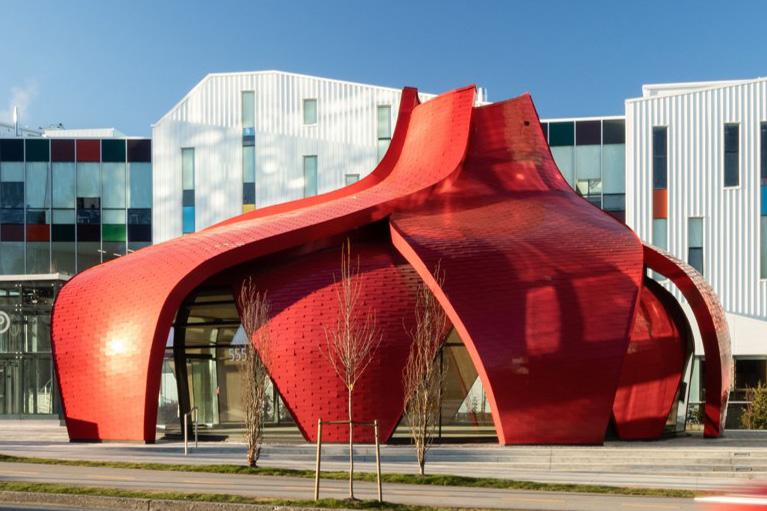
Selecting Mass Timber
Client was material agnostic but wanted an iconic project. Of the many designs we presented, the design that the client felt was most iconic happened to be suitable to mass timber construction.
Mass Timber Parti
The flexibility of mass timber framing and the precise nature of mass timber prefabrication are leveraged to achieve the complex architectural form. Mass timber is concealed by exterior and interior cladding.
Project Delivery Model
Design Assist. GC hired mass timber engineer-fabricator-installer and the project SE reviewed the design.
View from Street 1
Image credit: Ema Peter
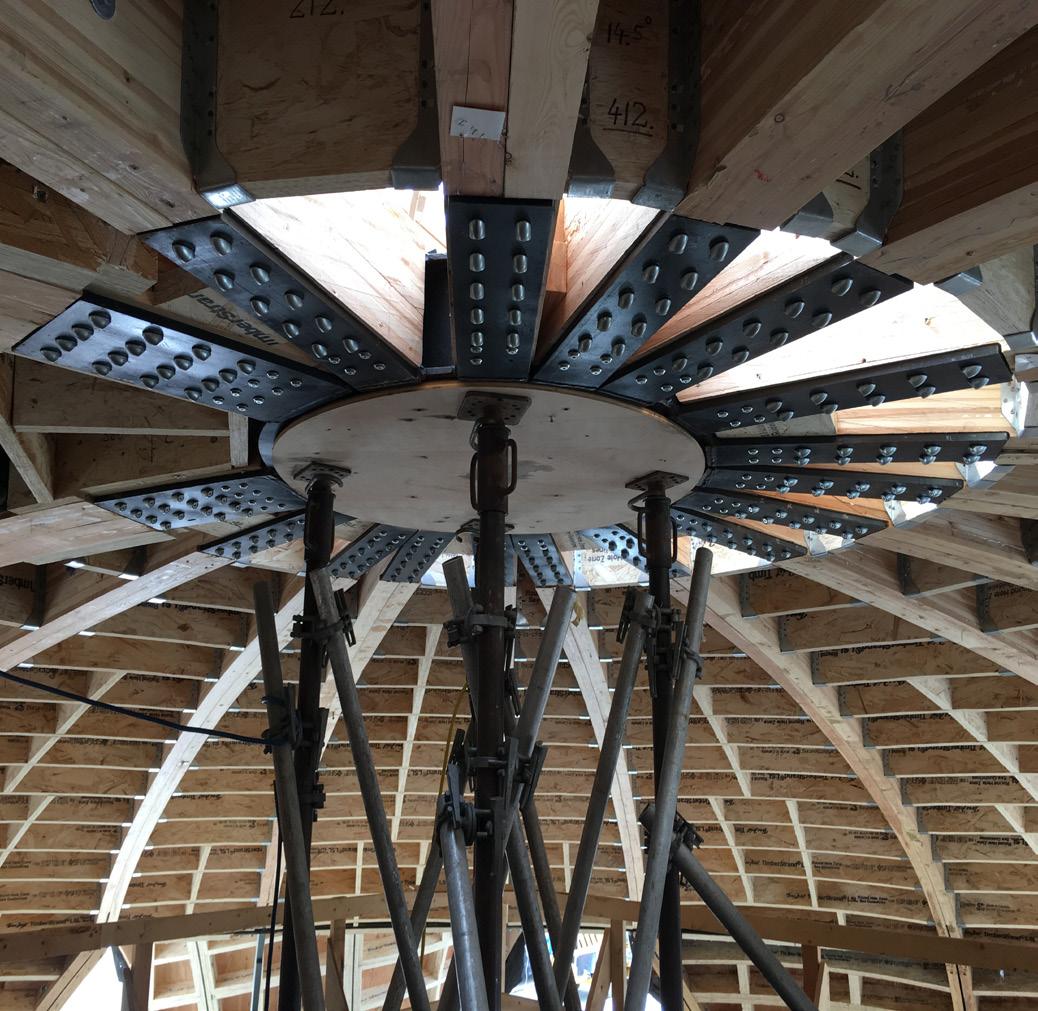
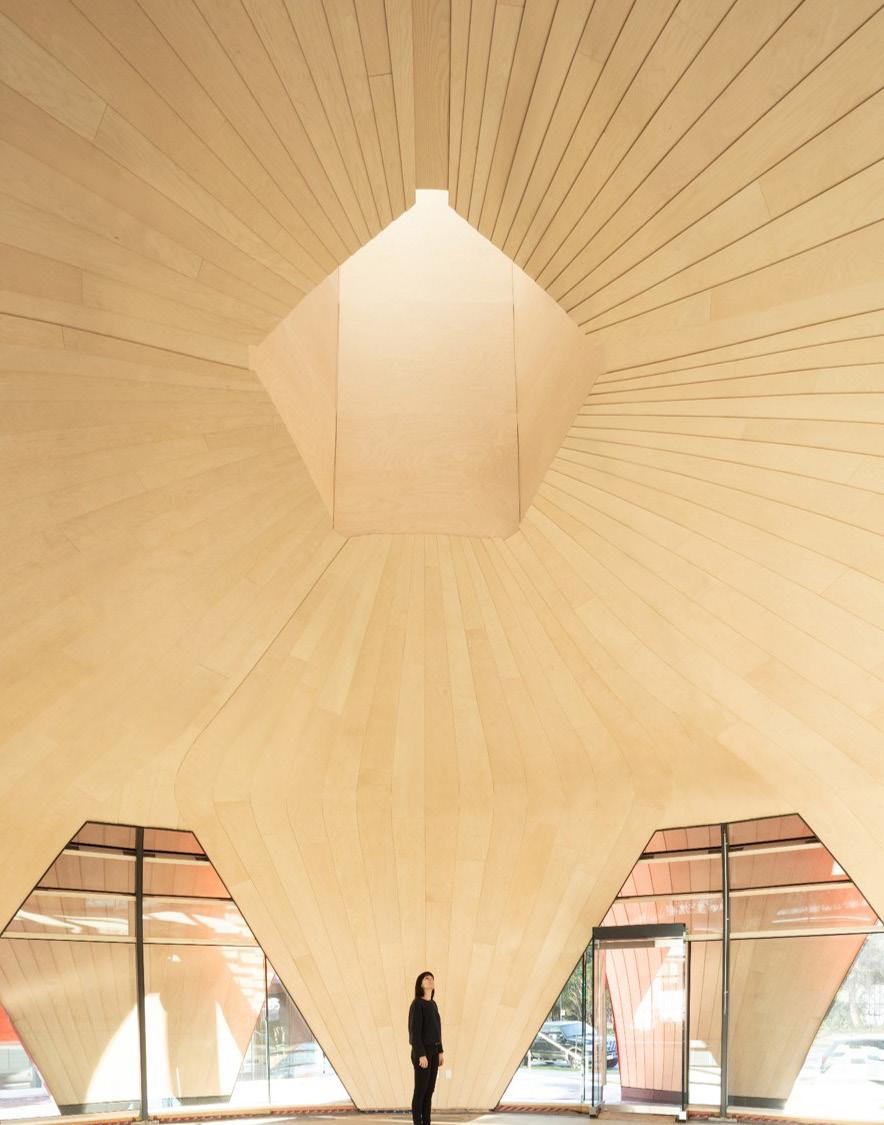
Prior Experience with Mass Timber Design
All stakeholders had prior experience.
Design Lead for Mass Timber
Design Assist Fabricator developed the structural logic to achieve the architectural 'petals' vision.
Systems Integration Strategy
Utilities were routed below the floor slab. Systems were routed in the thickness of the panels when possible. This was difficult due to the curvature and was not feasible for sprinkler pipes, which were ultimately hung in the interior.
Code and AHJ Challenges
No Significant Challenges.
Image credits: Ema Peter
Cost
and Schedule
Cost and schedule savings were realized by rationalizing the petals to all be buildable on one jig, without being identical in shape. The selection of curved laminated strand lumber ribs and 2x blocking was an economical approach to curved petals.
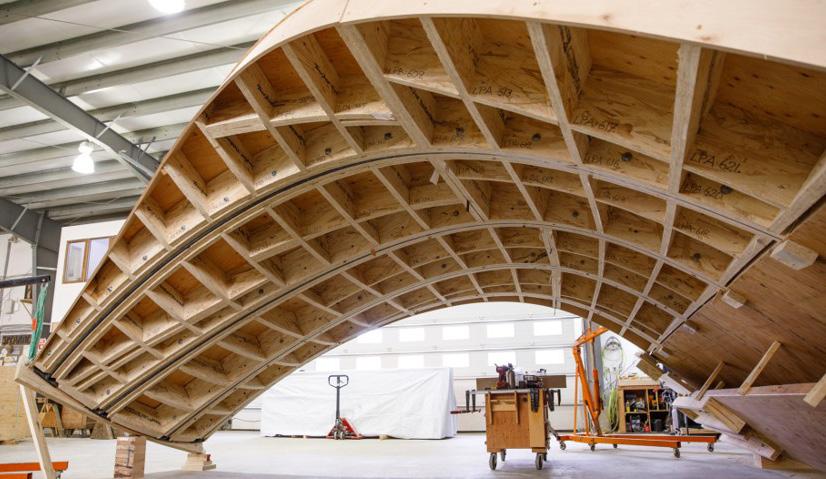
Upper petal connection to lower petal. Prefabricated petal in the shop 1 2
Image credit: Nick Diamond
What went REALLY well?
Coordination with the fabricator went really well because the design team and fabricator team were both using Rhino to share geometry and no 2D drawings were prepared by the designers to assist the fabricators. Installation went very well because the panels were all preassembled and test fit in the shop before being installed at the site.
What were the precious lessons?
Systems integration is very difficult on complex geometries and should be studied as part and parcel of the irregular structural geometries.
Southwest Library
Washington, DC
Sector: Civic
Studio: DC
SE: StructureCraft
GC: Turner
Fabricator: StructureCraft
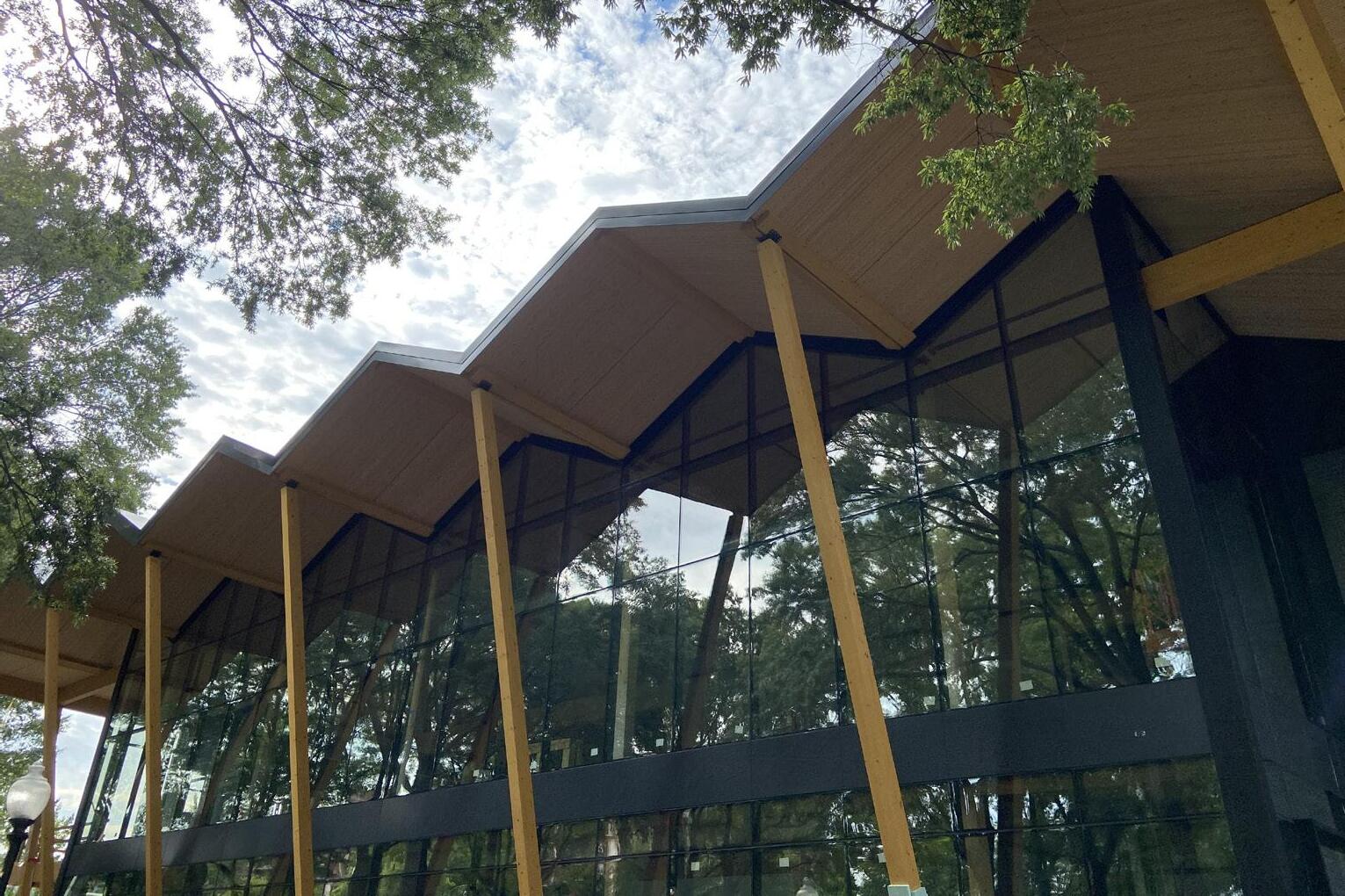
Selecting Mass Timber
Client was material agnostic. Project was won through RFP process. Proposal was a mass timber project using design build delivery to reduce cost and design fees.
Mass Timber Parti
Mass timber plays triple duty as a finish, a form generator, and a structural system. Exterior exposed columns and DLT roof soffit. Interior exposed post and beam frame and exposed DLT decks. Mass timber visible from exterior through transparent façade.
Project Delivery Model Design Build.
North Elevation 1
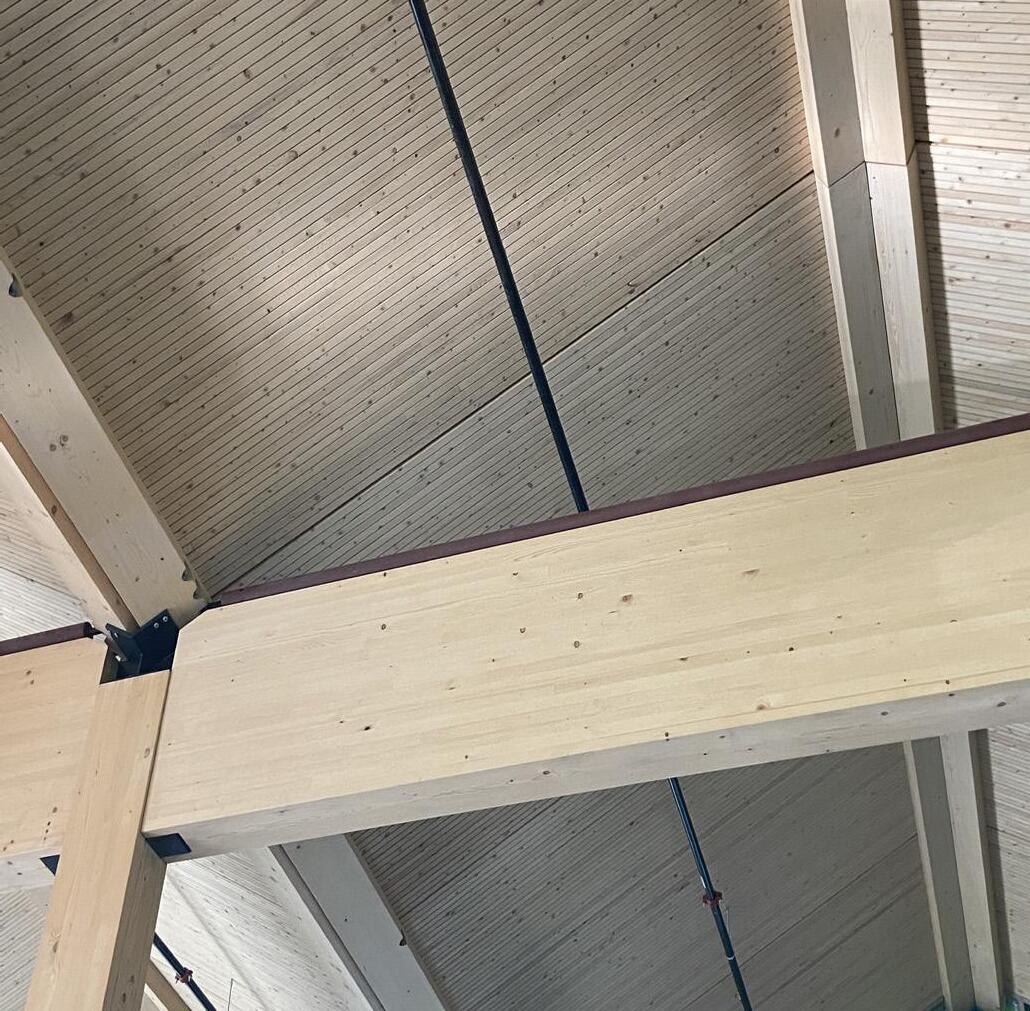
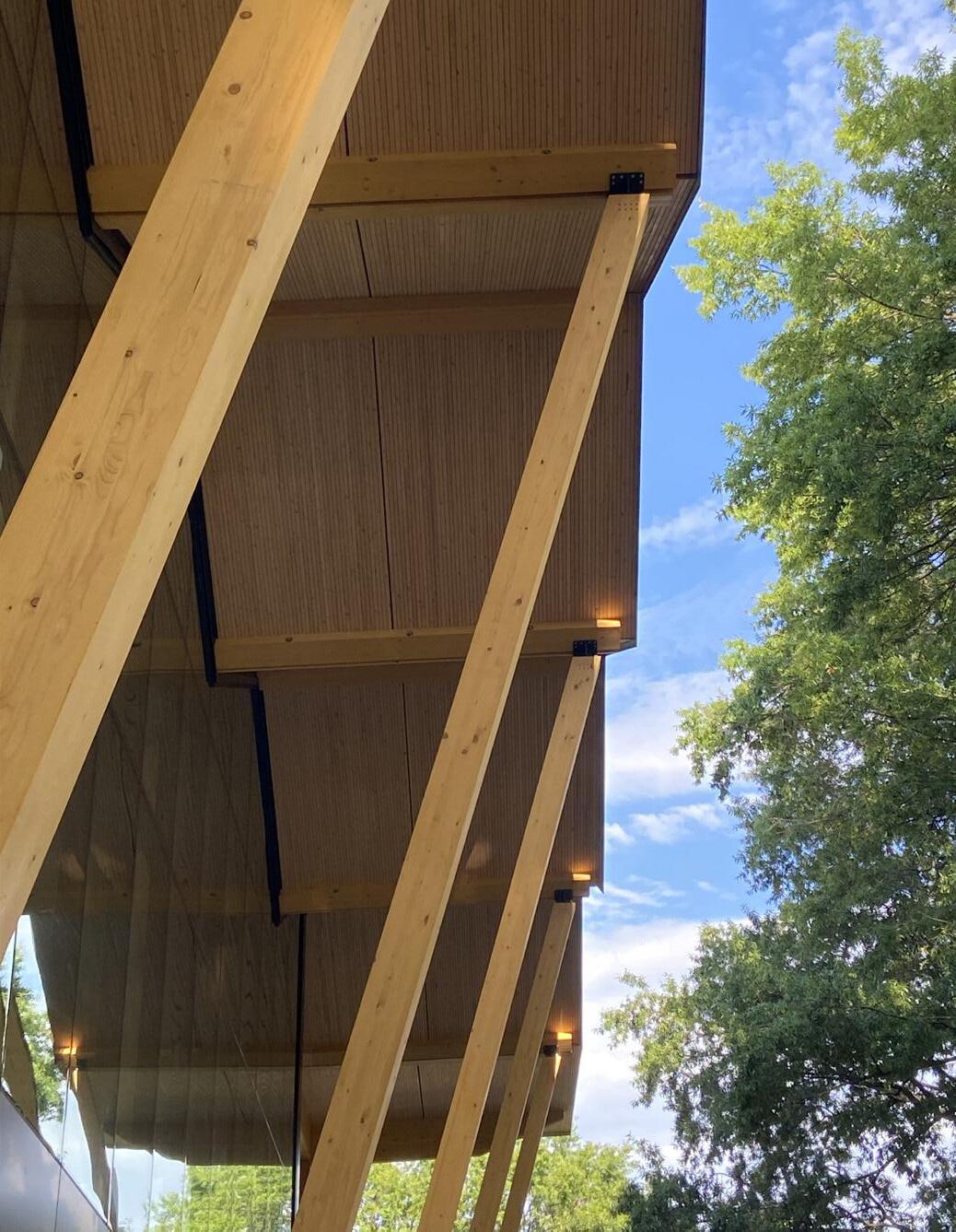
Prior Experience with Mass Timber Design Architect, SE and Contractor only.
Design Lead for Mass Timber Architect and SE-Fabricator-Installer.
Systems Integration Strategy
Expose the utilities and rigidly follow the module.
Code and AHJ Challenges
None. Zero plan check comments on architecture and fire protection.
Cost and Schedule
Mass timber fabrication coupled with design build delivery was used to reduce costs and site errors.
Southwest Library Image credits: Structure Craft
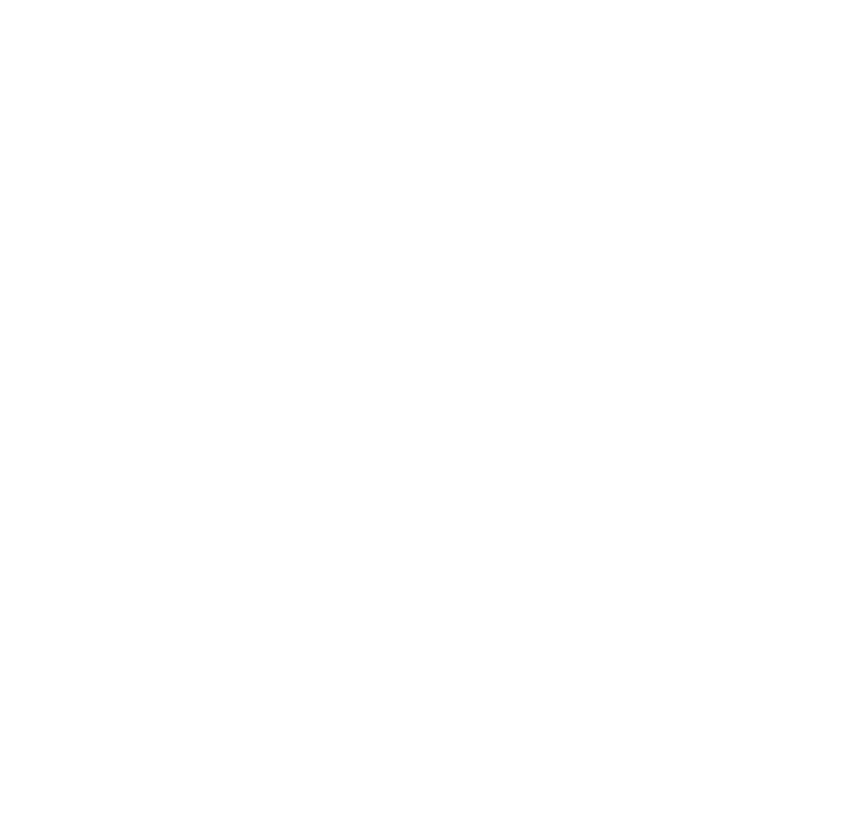
What went REALLY well?
Mass timber was erected so quickly that curtain wall supplier was able to develop shops based on as-builts of the structure. This increased precision of the curtain wall install.
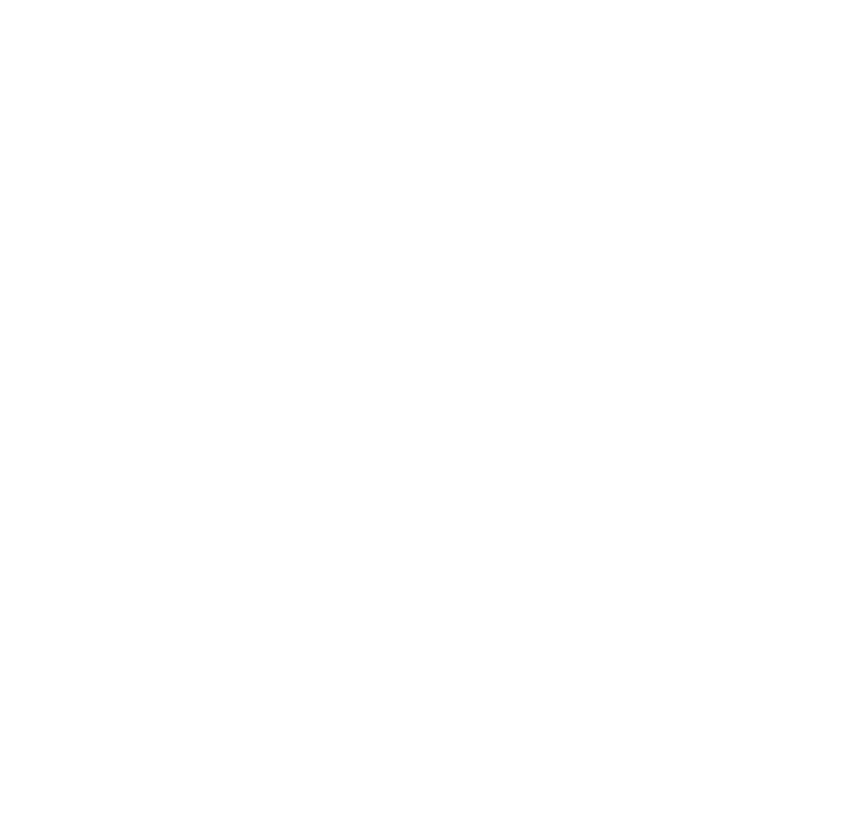
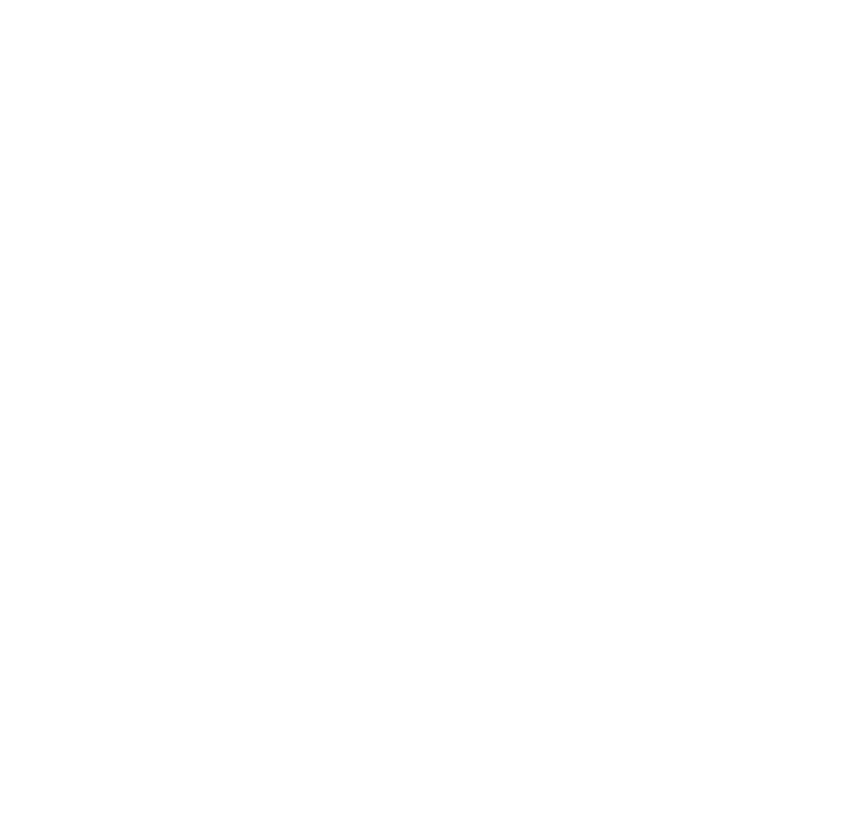
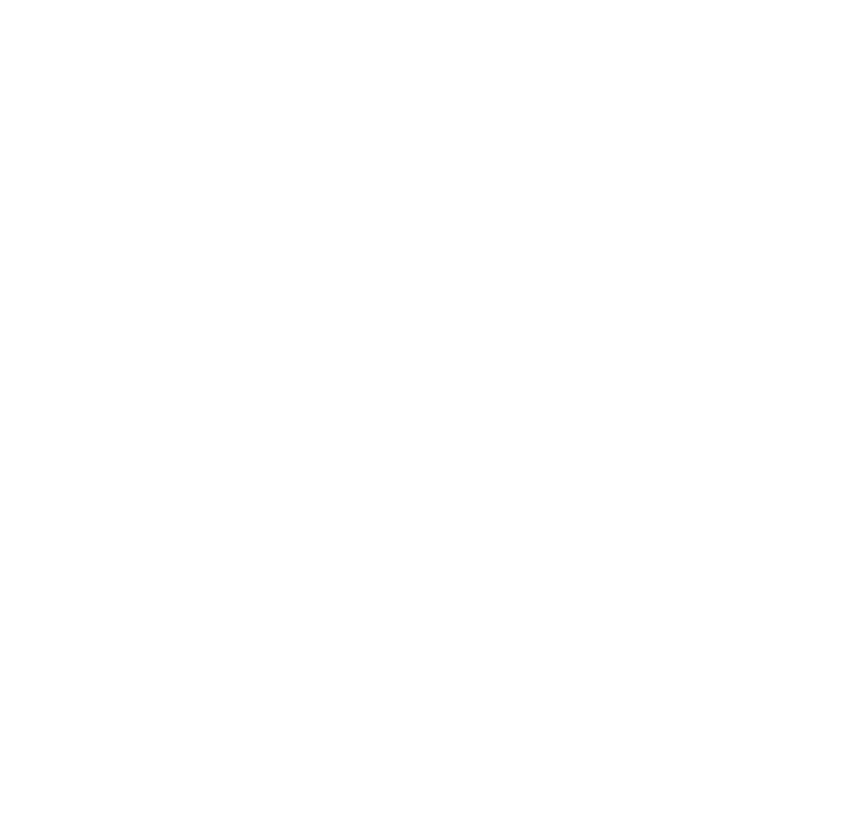
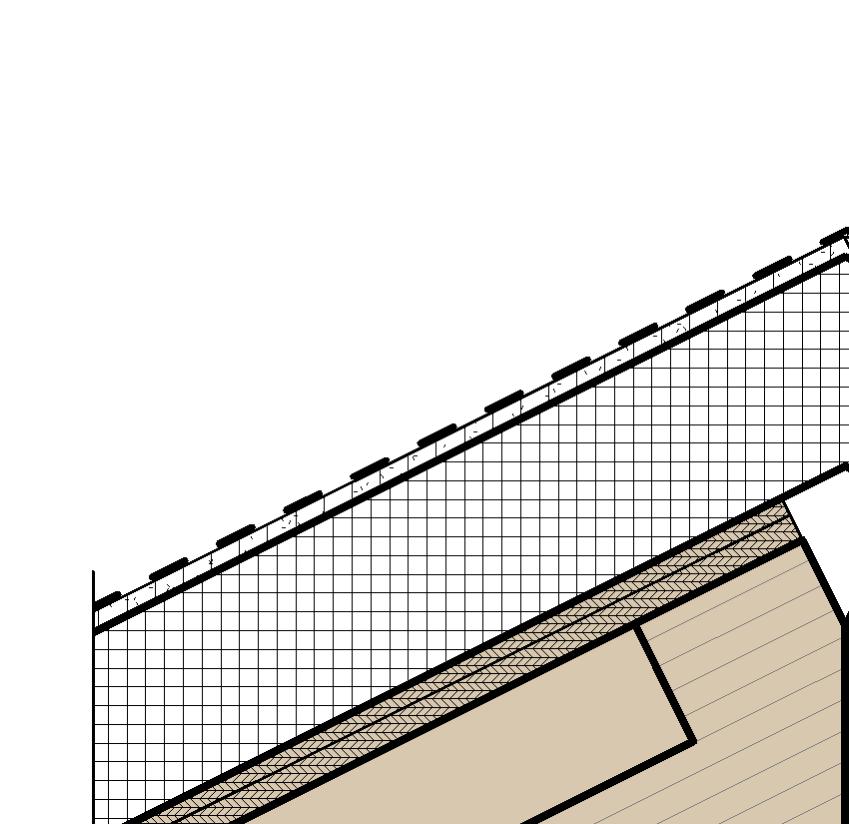
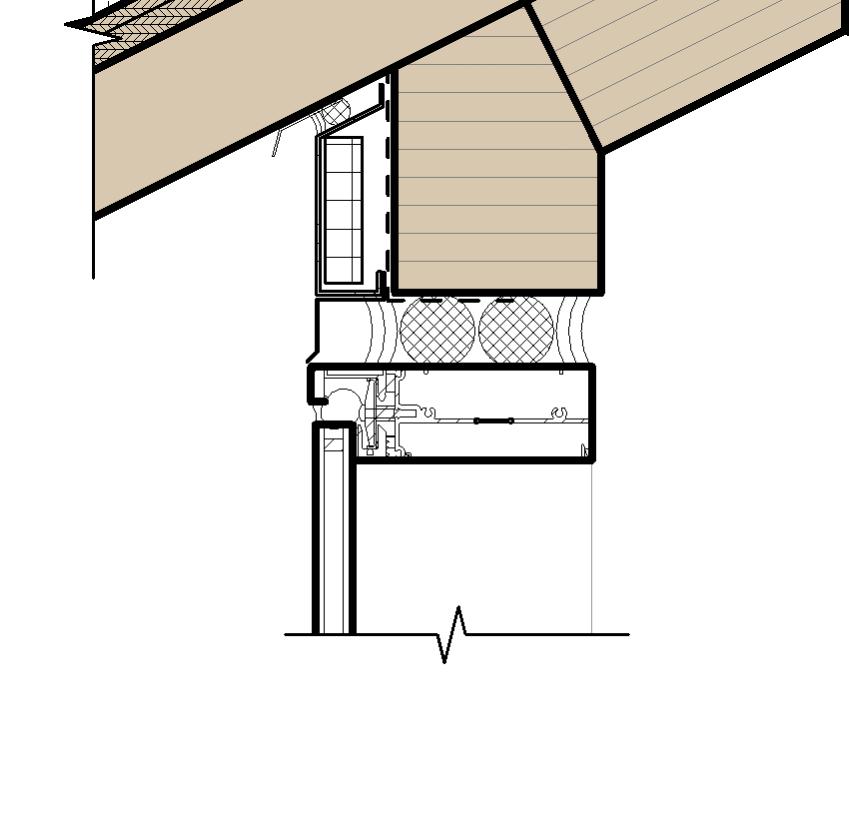
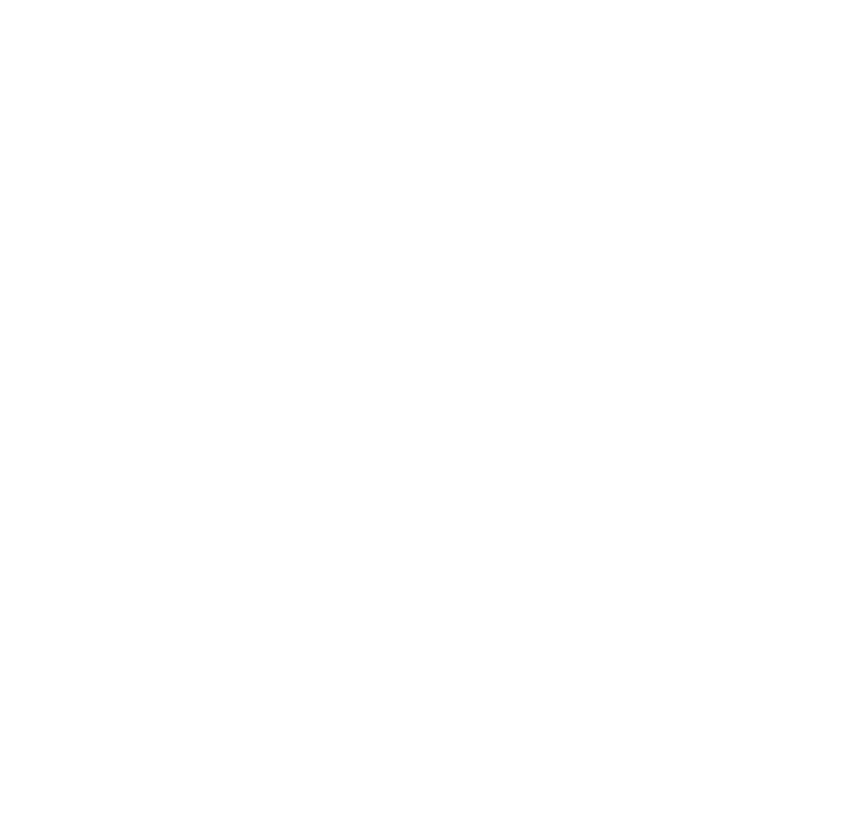
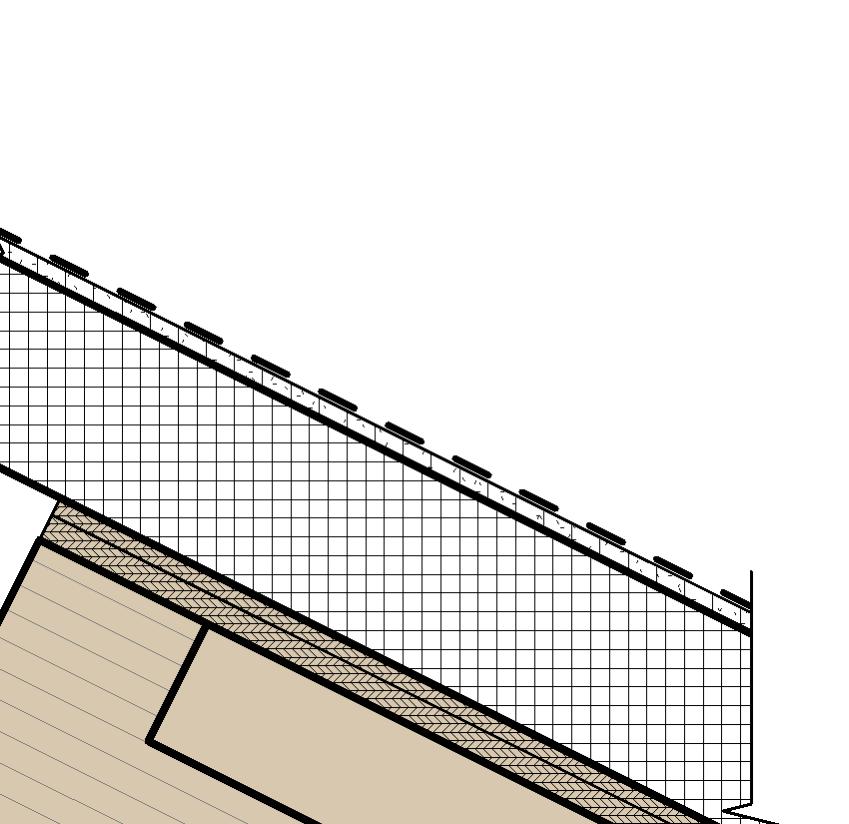
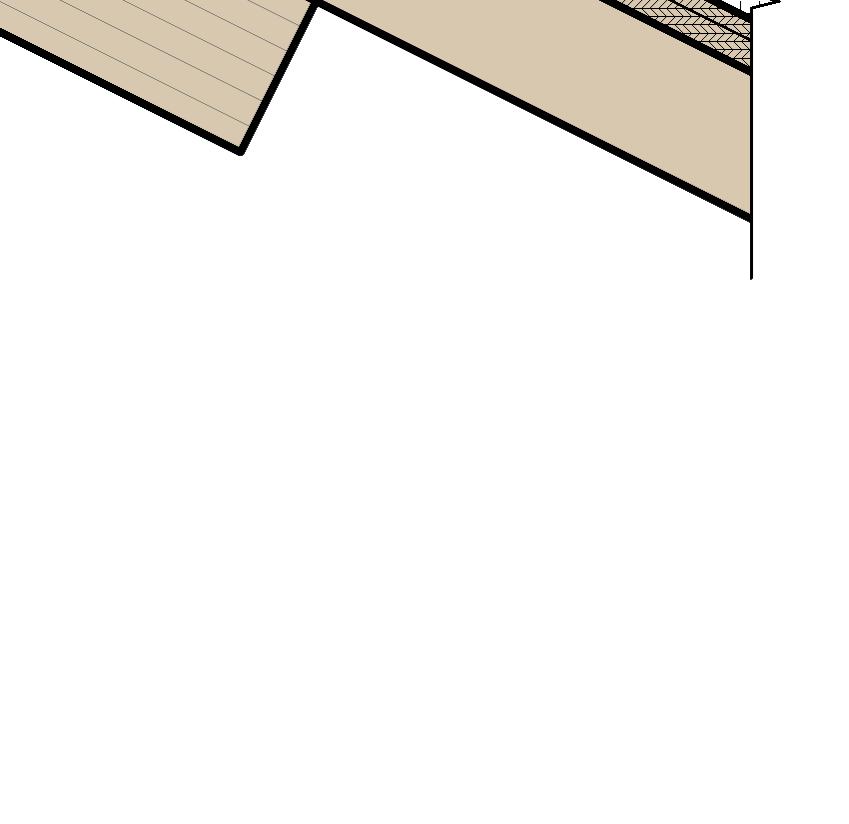
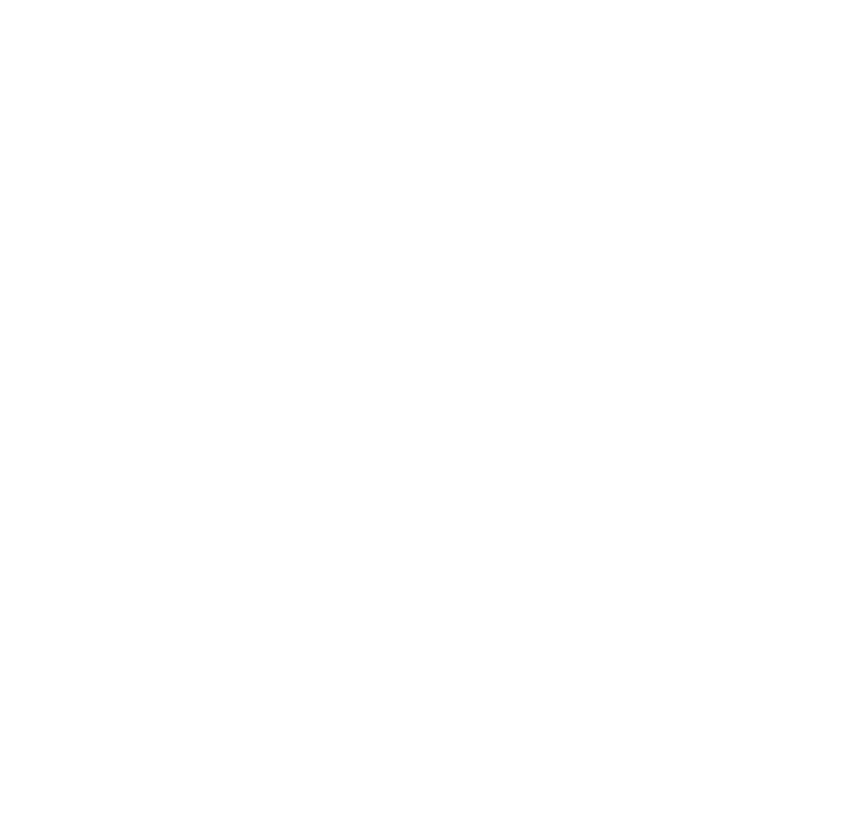
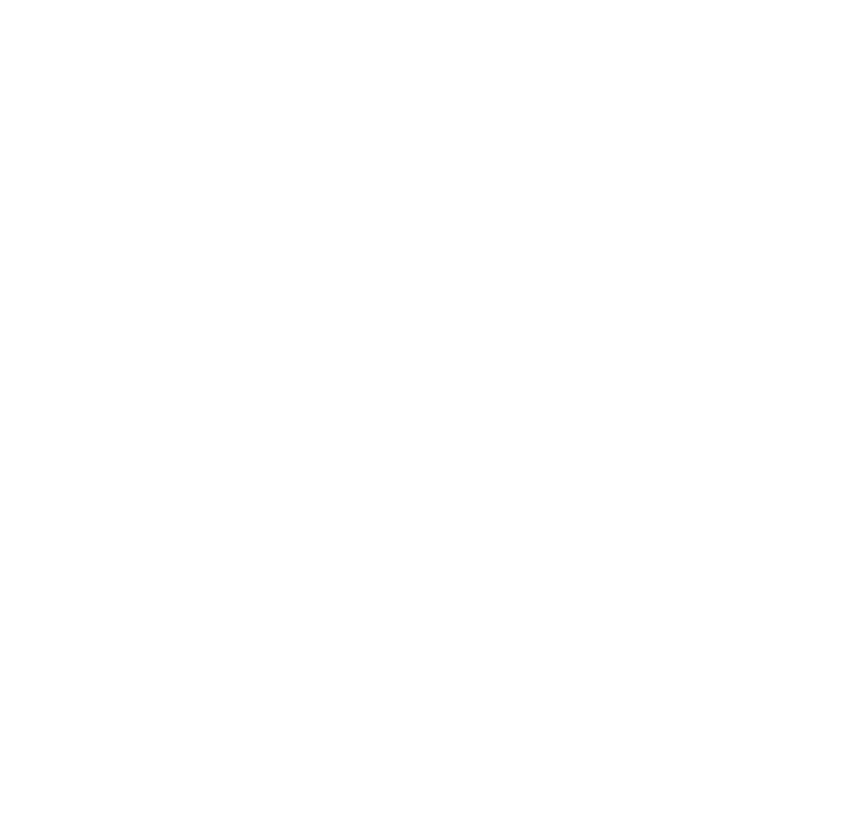
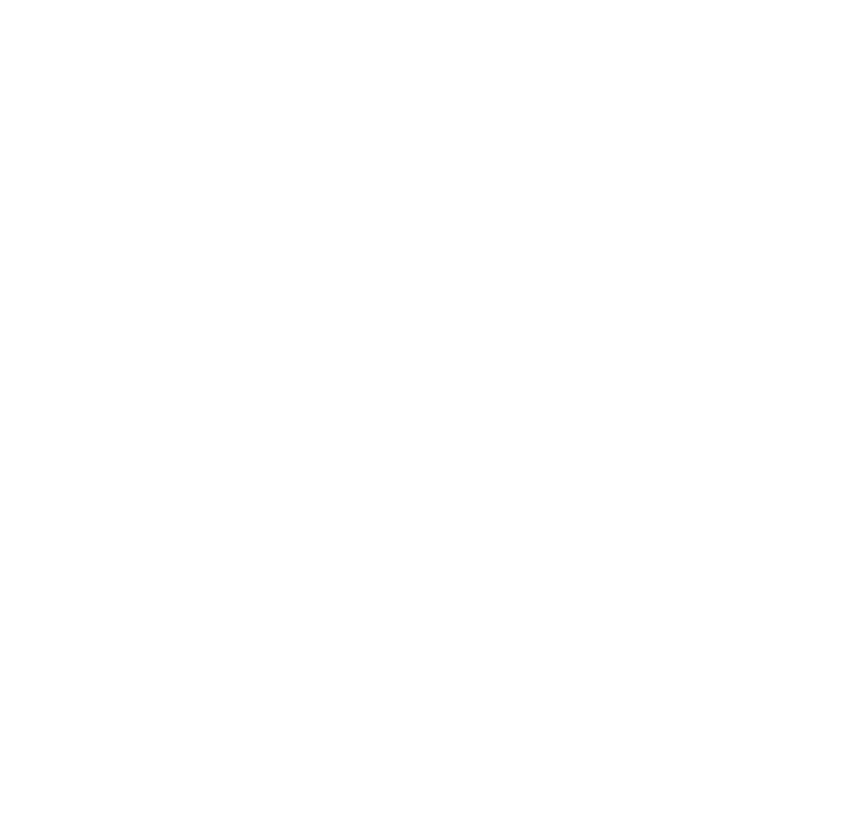
What were the precious lessons?
MEP design builder was brought on too late for meaningful dialogue on MEP integration. Convincing the builder to follow the module instead of the shortest utility routes was a challenge.
SE-fabricator-installer came on board too late and the structural design had to be revised. In addition, SE-fabricator-installer was sub to GC but would prefer to be sub to architect for design services.
Typical Framing Diagram 20'x20' Bay Spacing Mass Timber Elements: 2x6 DLT Roof and 2x8 DLT Floor Panels, Glulam Beams and Columns
SoLo - Soo Valley Prototype Home
Whistler, BC
Sector: Housing
Studio: VAN
SE: Glotman Simpson
GC: Durfeld
Fabricators: Durfeld, StructureCraft, Western Archrib, Structurlam
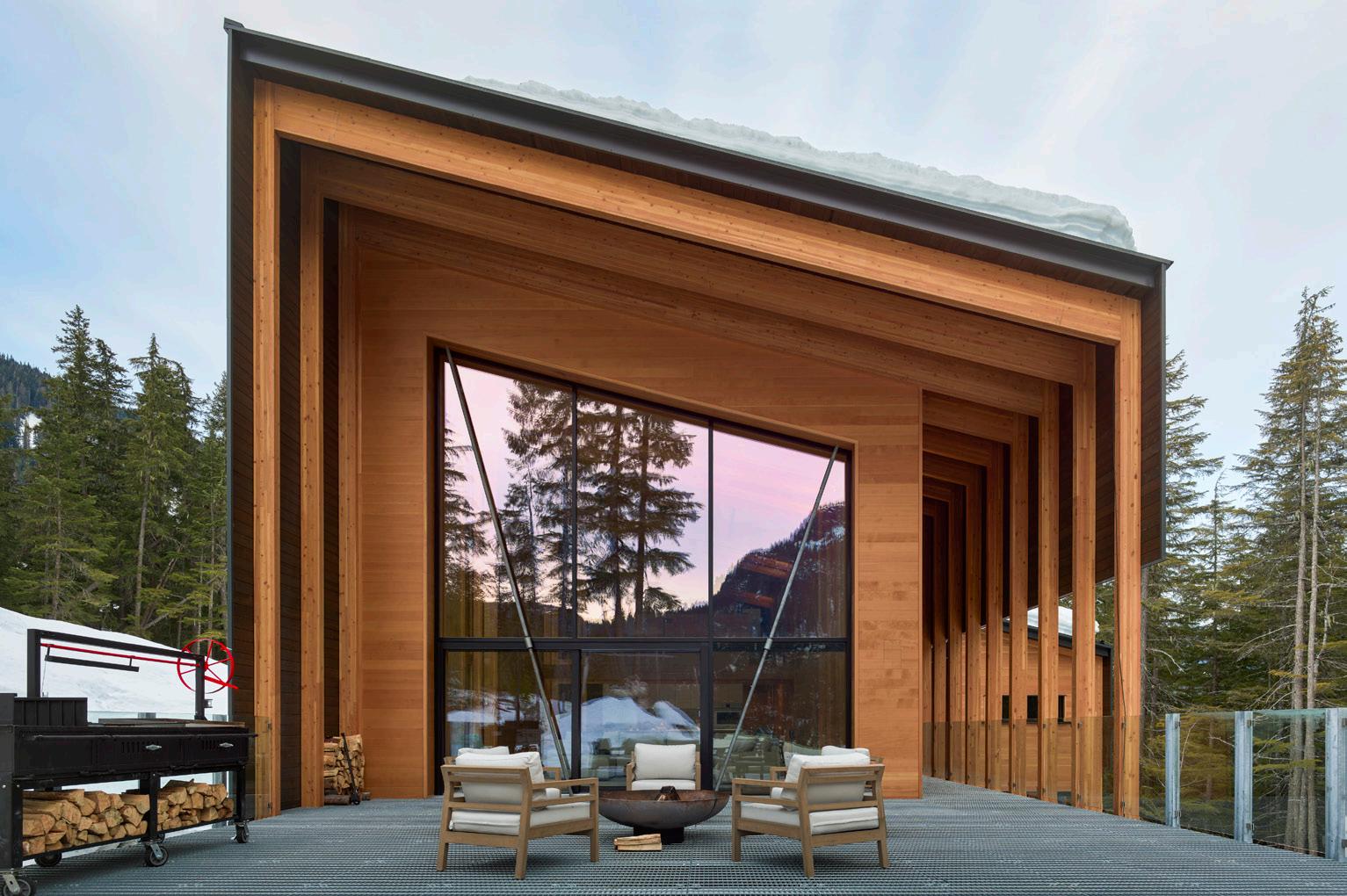
Selecting Mass Timber
Client required mass timber design as part of a vision to build the greenest building possible & support the regional economy,
Mass Timber Parti
Mass timber is the muse of the project. The project is a study in variations on the theme of mass timber with a multiplicity of different structural systems and mass timber products working together on a rigid module. The envelope takes a two-layer approach: mass timber framed ‘shield’, insulated inner layer.
Project Delivery Model
Design Bid Build.
Entry 1
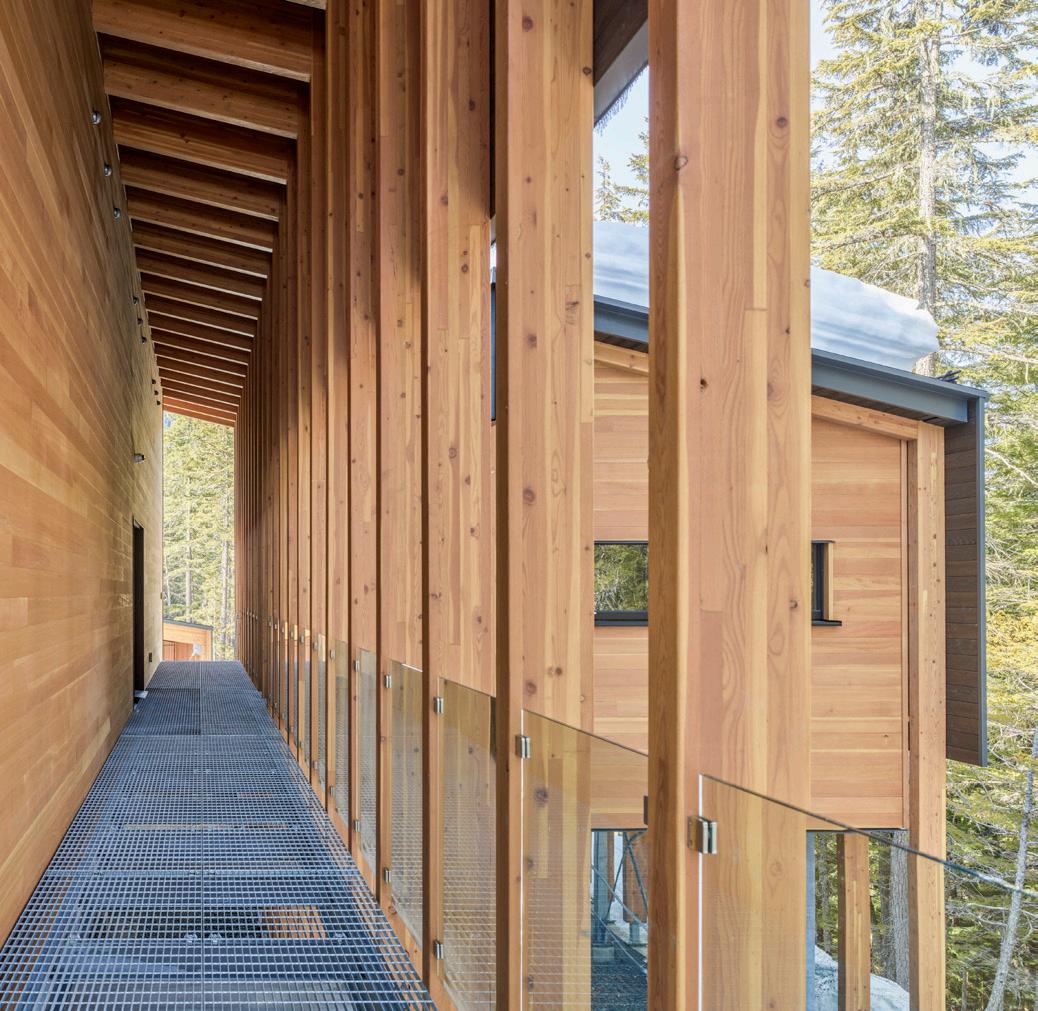
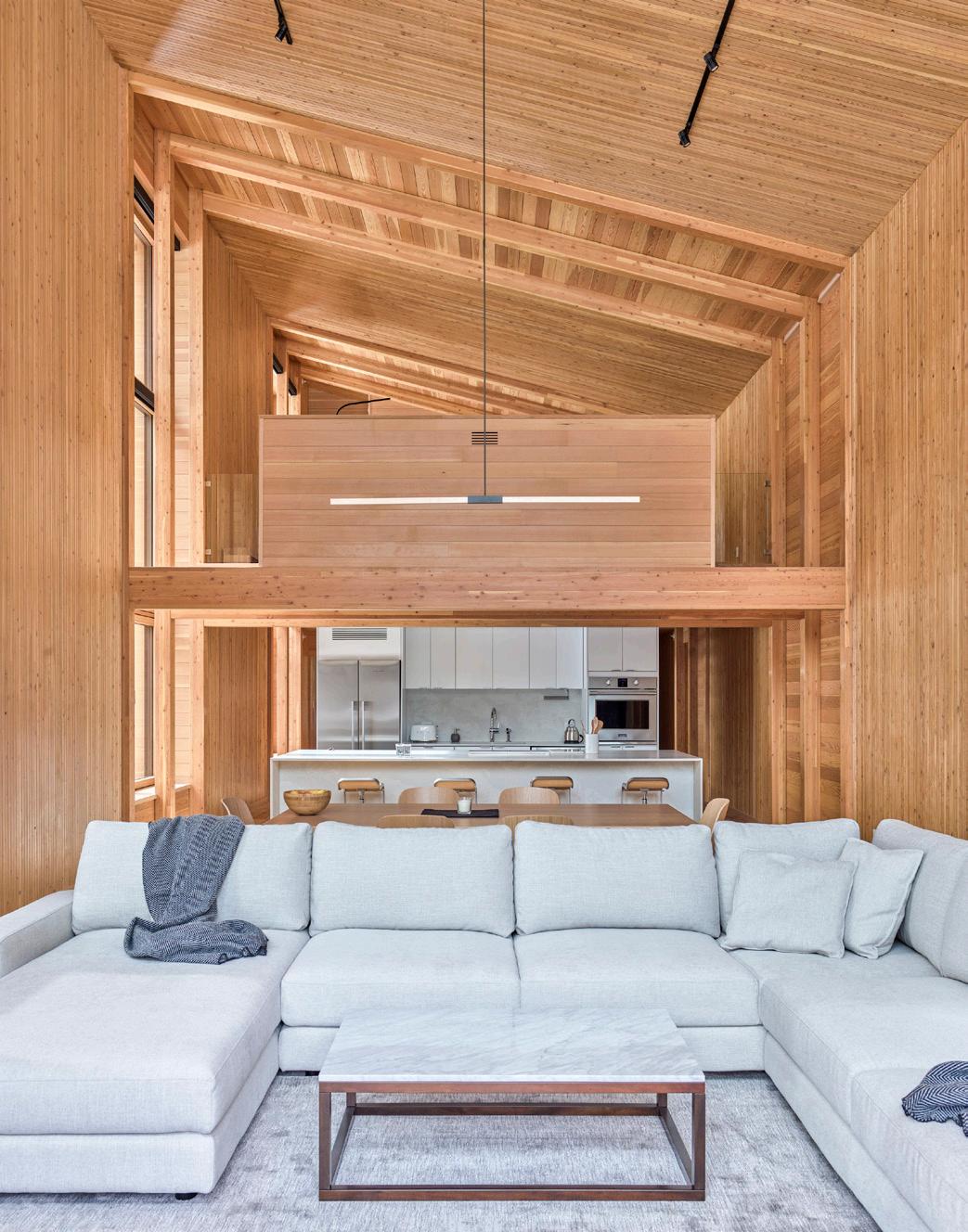
Prior Experience with Mass Timber Design
All stakeholders had prior experience.
Design Lead for Mass Timber Architect.
Systems Integration Strategy
Chases were created in floors/walls to run sprinkler pipe. Routing/ spacing was drawn by PW to demonstrate how to hide pipes. Use of radiant floors reduced visual impact of mechanical system. Sprinkler heads were difficult to conceal with standard mounts.
Code and AHJ Challenges
Project was non-standard from a code perspective and the AHJ needed extra dialogue with the code consultant before approval.
SoLo Soo Valley Prototype Home Image credits: Andrew Latreille
Cost and Schedule
Mass timber was fabricated in winter and the project was built in Spring/Summer to accommodate the seasonal weather.
What went REALLY well?
Precision of mass timber resulted in a tight and clean appearance despite the lack of add-on finishes.
Typical Framing of 2-Story House.
What were the precious lessons?
Sprinklers always need more attention early on because it is difficult to address them elegantly if they are not fully integrated at the beginning. DLT panels are very sensitive. Handling requires an experienced fabricator to understand that hoisting/slinging DLT before it’s settled can result in twisting/racking. It is difficult to make wood look good via patching. Use higher grade of wood if the finish quality is paramount.
It is possible to execute a Design Bid Build mass timber project if all stakeholders have enough experience.
REM Train Stations
Montreal, QC
Sector: Transportation
Studio: TOR/VAN/SF/LA
SE: SNC Lavalin
GC: SNC Lavalin
Fabricators: Nordic
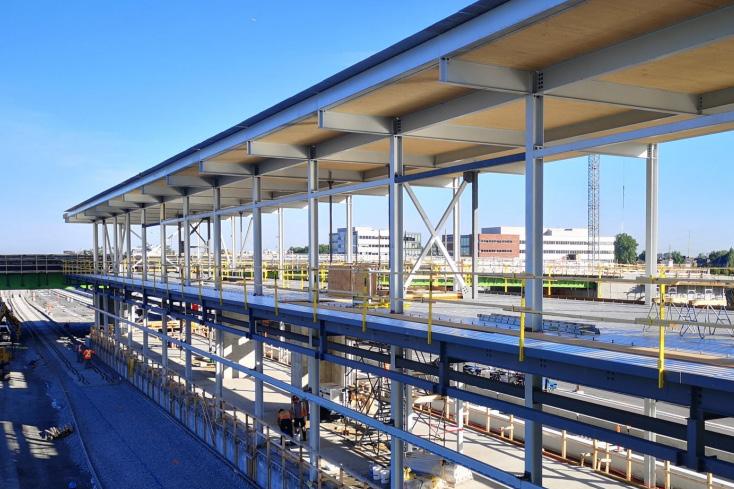
Selecting Mass Timber Proposed by architect during competition phase.
Mass Timber Parti
Roof fascia beams of glulam are legible through the envelope while CLT roof decks provide a warm ceiling surface. The CLT roof deck cantilevers out beyond the facade to form an entrance canopy.
Project Delivery Model Design Build.
Prior Experience with Mass Timber Design Architects and Structural Engineer only.
Station Platform 1
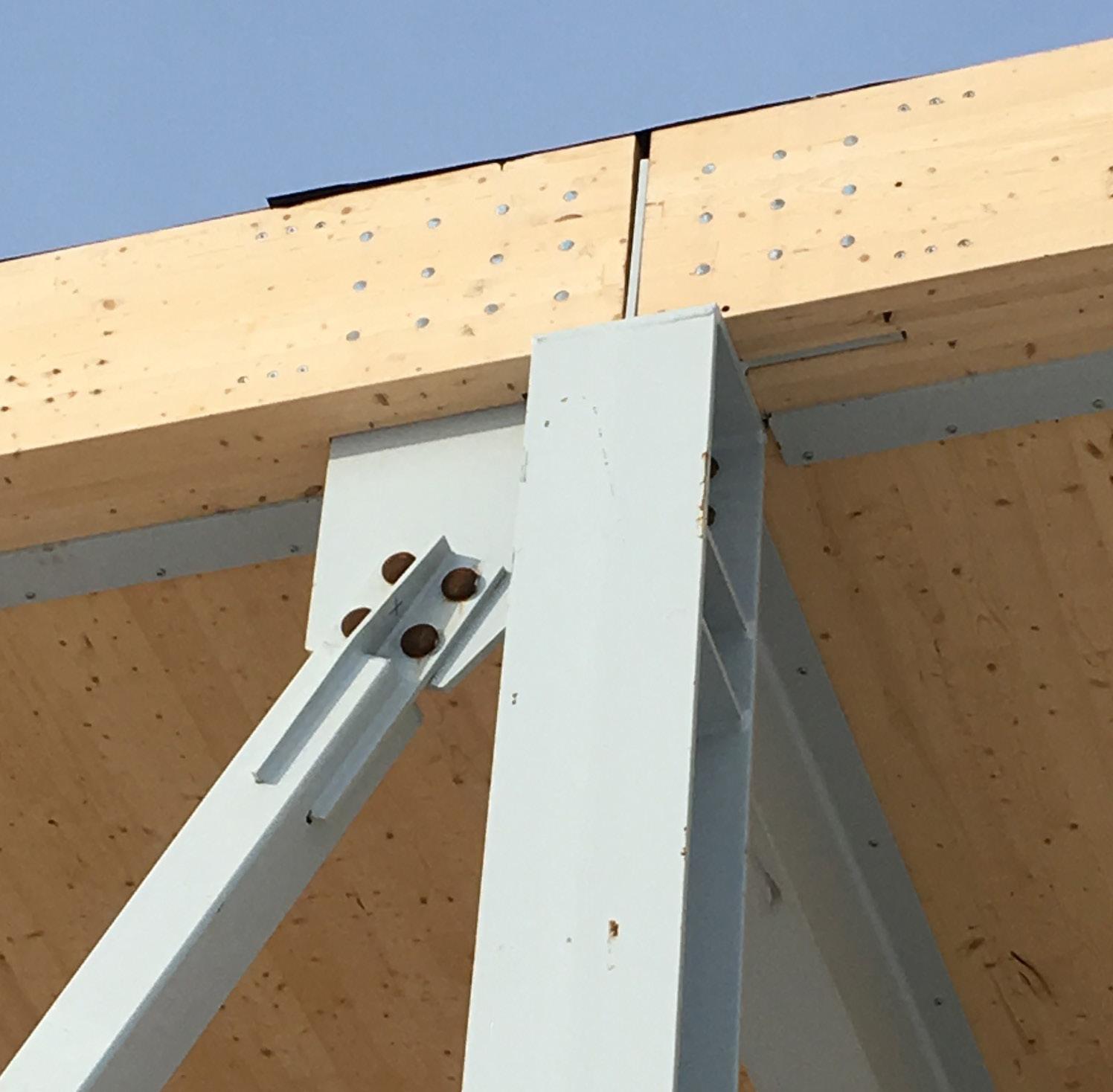
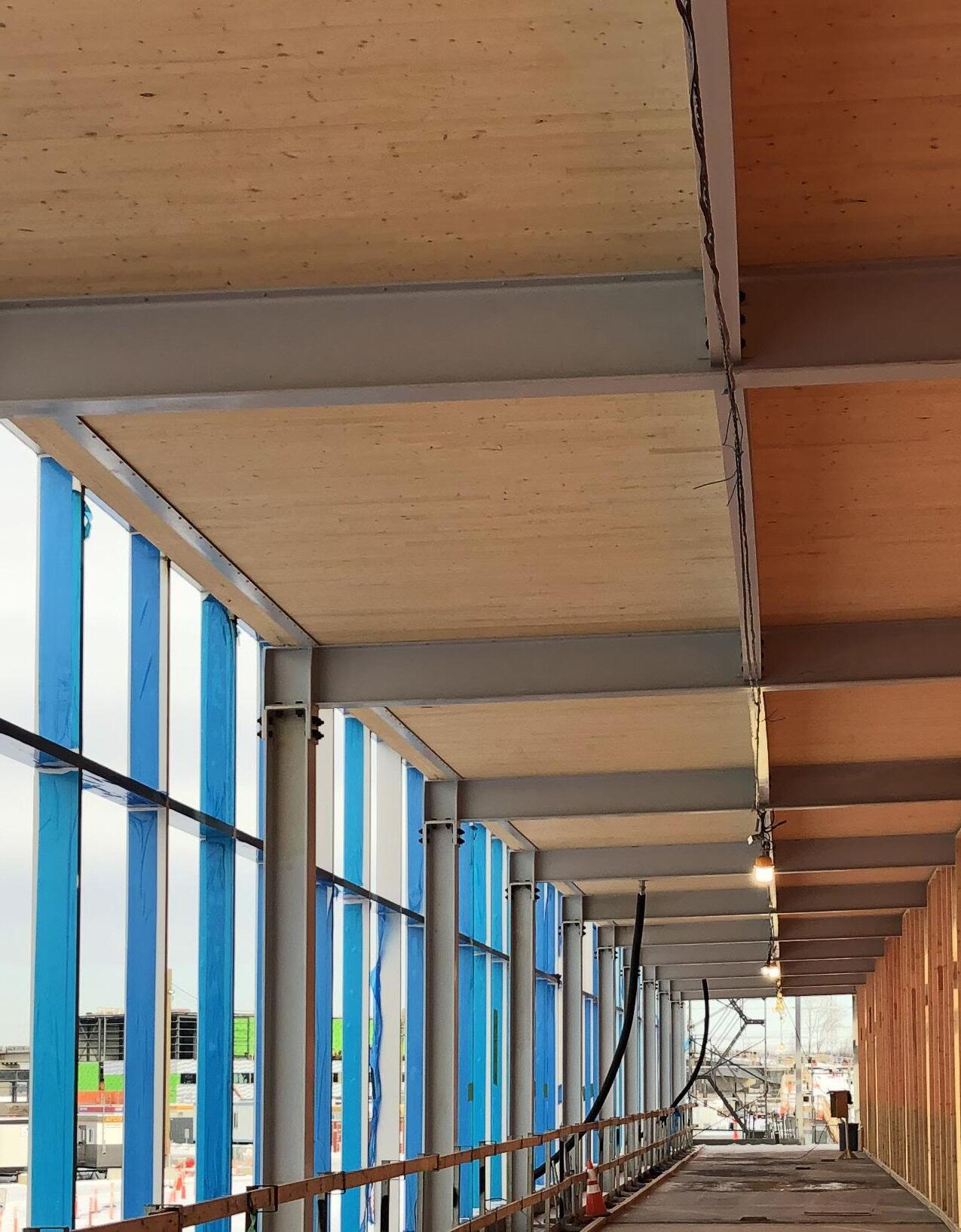
Design Lead for Mass Timber
The client required Mass Timber to be used.
Systems Integration Strategy
Systems were kept independent but design emphasis was placed on reducing overhead utilities to allow the wood to remain visible.
Code and AHJ Challenges
The use of mass timber was limited to the roof decks and beams to minimize the code implications of wood in a project governed by NFPA 130. The alternate means and methods approach was conceived from the beginning of the project and was very successful.
Glulam Beam to Column
REM Train Stations Image credits:
Cost and Schedule
During the shop drawing review process, the contractor proposed the addition of steel purlins to reduce the clear span and thickness of the CLT, and thereby reduce cost. However, the bay width in the 90 degree direction was not coordinated with the panel widths provided by the manufacturer and resulted in field rework.
Parapet Detail with Roof Edge Beam carrying CLT roof deck 1
2 What went REALLY well?
Quick application of vapor barrier immediately after install protected the wood from weather while also providing a dry worksite below.
What were the precious lessons?
Interfaces of mass timber beams and decks with fire rated walls required engineering judgments. These conditions were identified during construction administration and required considerable effort to resolve.
Simon Fraser University Stadium
Vancouver, British Columbia
Sector: Higher Ed / Sports
Studio: VAN
SE: Fast+Epp
GC:
Fabricators: Structurlam
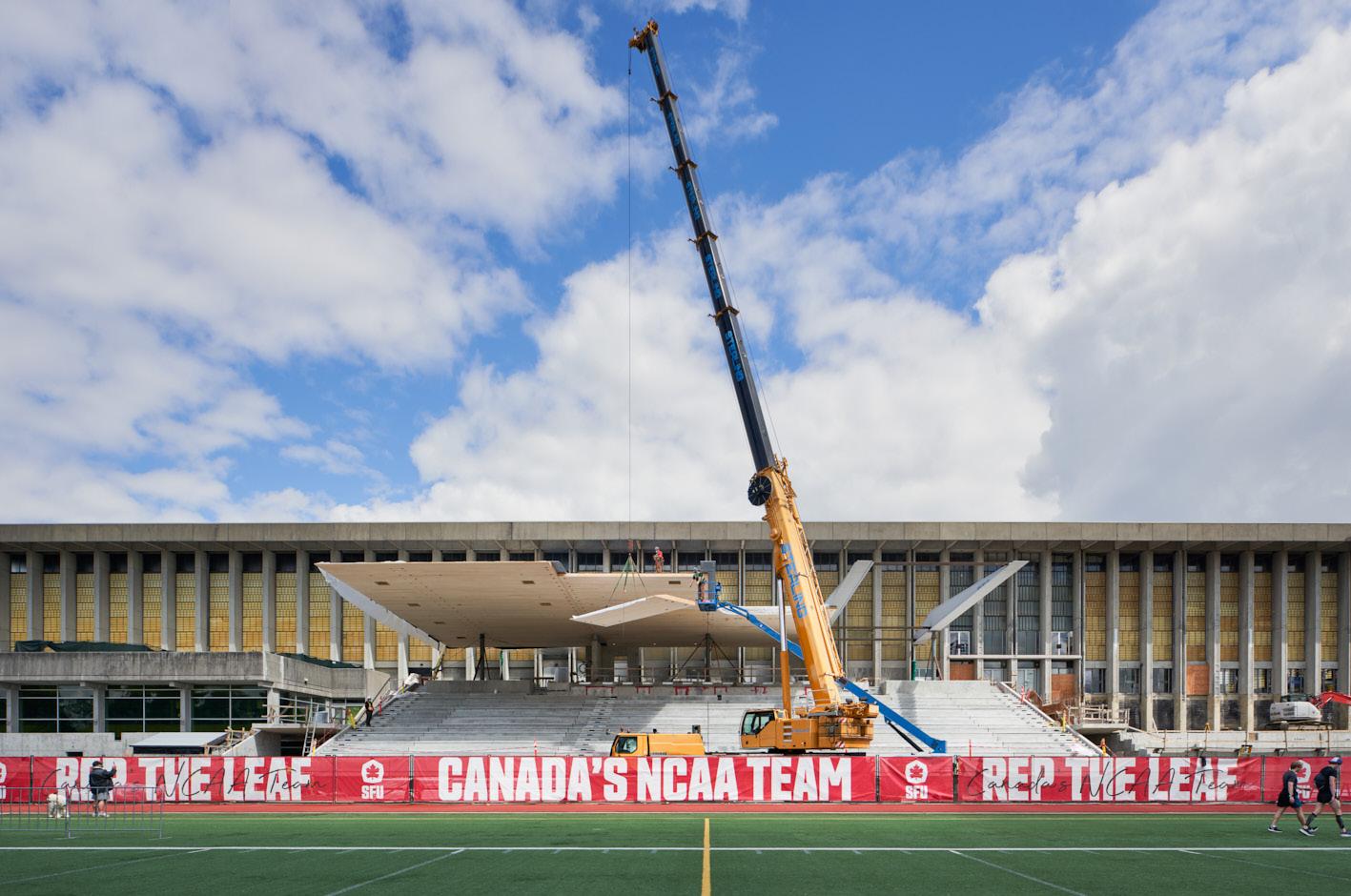
Selecting Mass Timber
Architect proposed mass timber as a contrast to the mostly concrete surfaces of the campus. The client had reservations about durability, but fell in love with the design.
Mass Timber Parti
The goal was to create a clean, uncluttered wood canopy to protect the stadium seating from rain. The CLT decks are hung from cantilevered steel beams with full integration of all MEP, including routing of conduit within the CLT slabs.
Project Delivery Model Design Bid Build.
View from 50 Yard Line 1
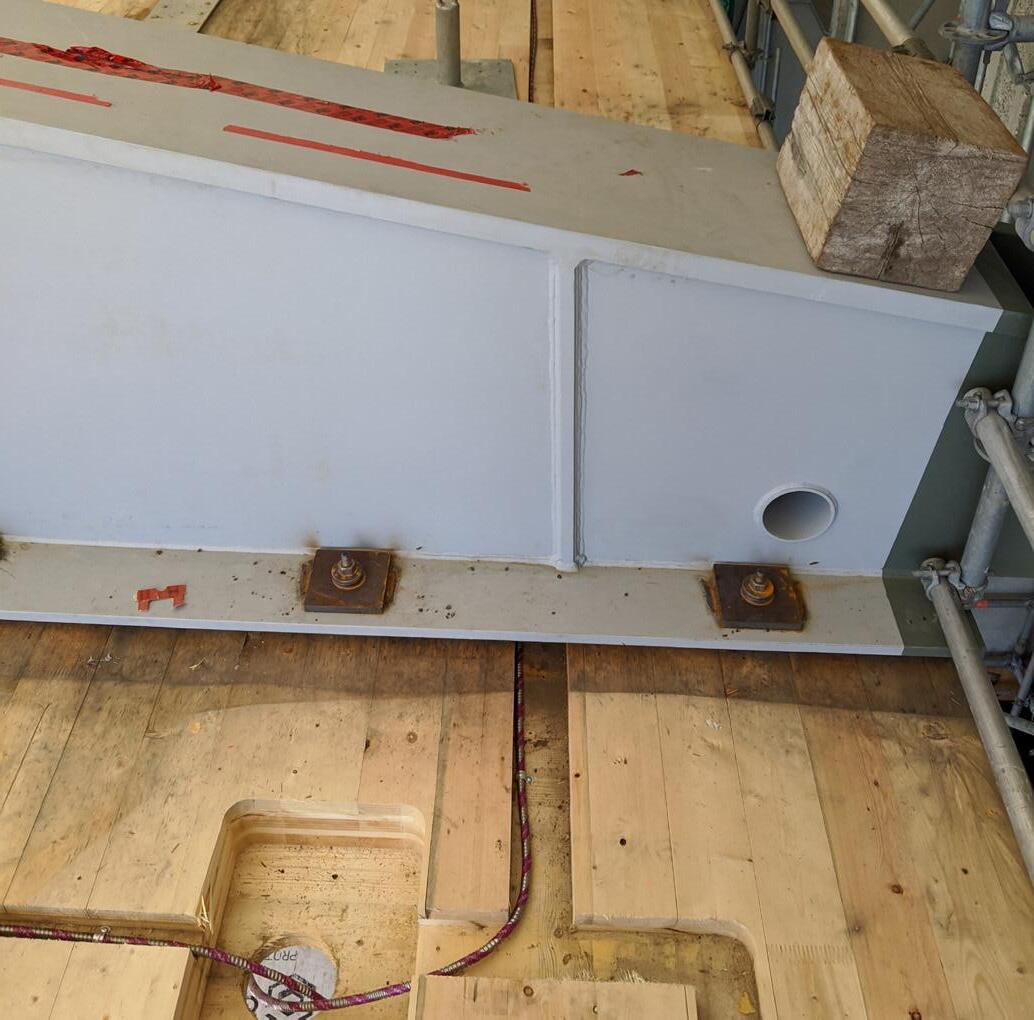
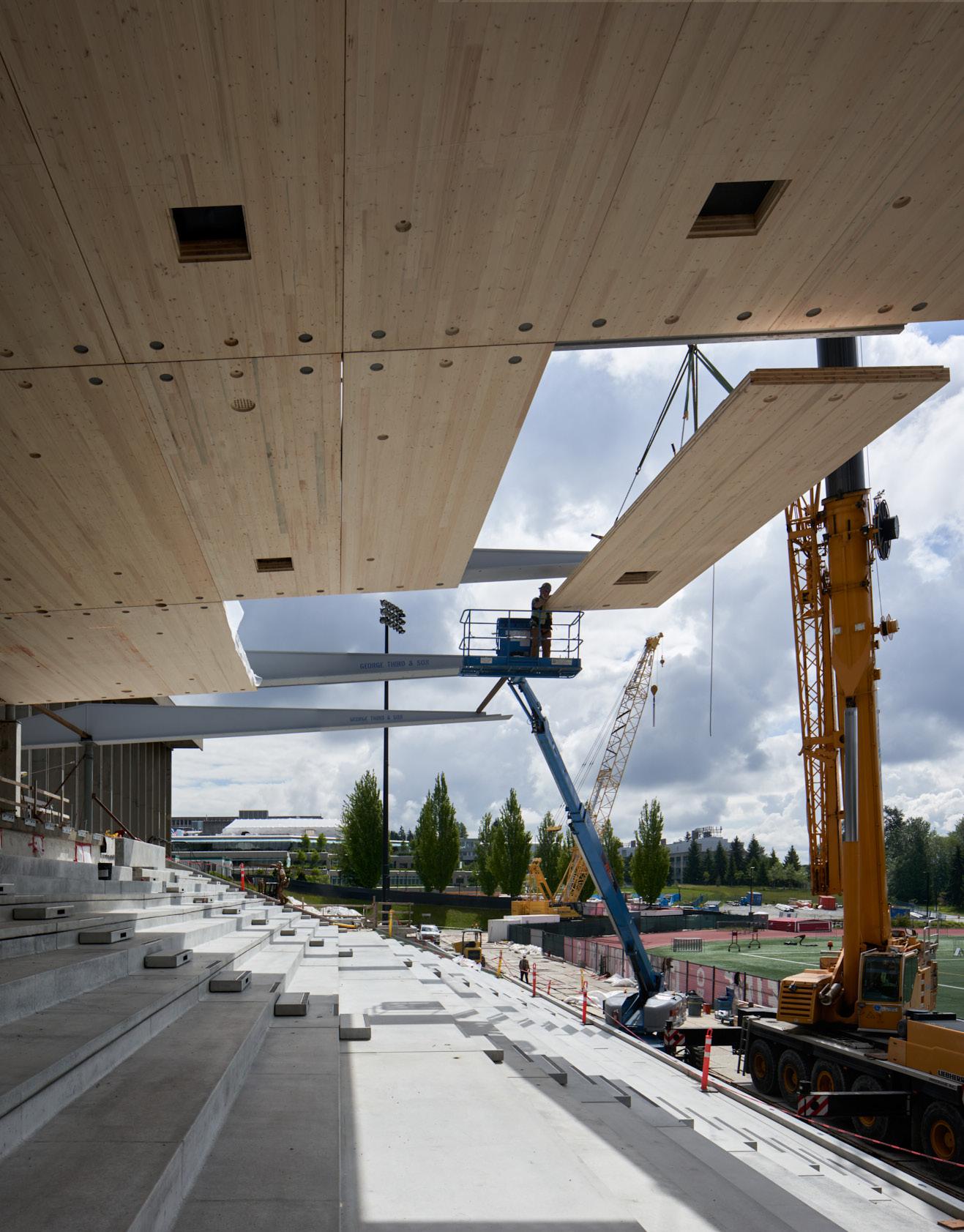
Prior Experience with Mass Timber Design Architect and SE had significant experience, the owner had minor experience while the GC had none.
Design Lead for Mass Timber Architect led the design and SE supported.
Systems Integration Strategy
Deep integration of all systems was required to achieve the design objective of providing an uninterrupted wood ceiling. CLT fabricator was able to precisely fabricate all conduit routes and cores through CLT.
Simon Fraser University Stadium Image credits: Andrew Latreille
Code and AHJ Challenges
The occupancy type below the bleachers did not allow combustible materials. Using mass timber for the canopy required classifying the structures above the concrete deck as a separate occupancy.
Cost and Schedule
The schedule was negatively impacted because the first-time mass timber contractor did not establish a sufficient weather protection plan. In the end, the entire canopy was tented to shield from rain.
3
What went REALLY well?
Joints between CLT panels were expressed as part of the architectural surface. To keep the joint widths consistent, a lot of careful panel positioning adjustments were needed to accommodate the steel construction tolerances without site cutting the CLT panels. Because all parties understood this challenge, the builders held to tight tolerances in the steel erection and the high precision of the CLT panels made the
What were the precious lessons?
UV will change the color of the wood quickly. Provide shade or install all panels quickly to maintain color consistency. Patches and dowel plugs will not match if the mass timber has changed color.
Camp Lakota
Frazier Park, CA
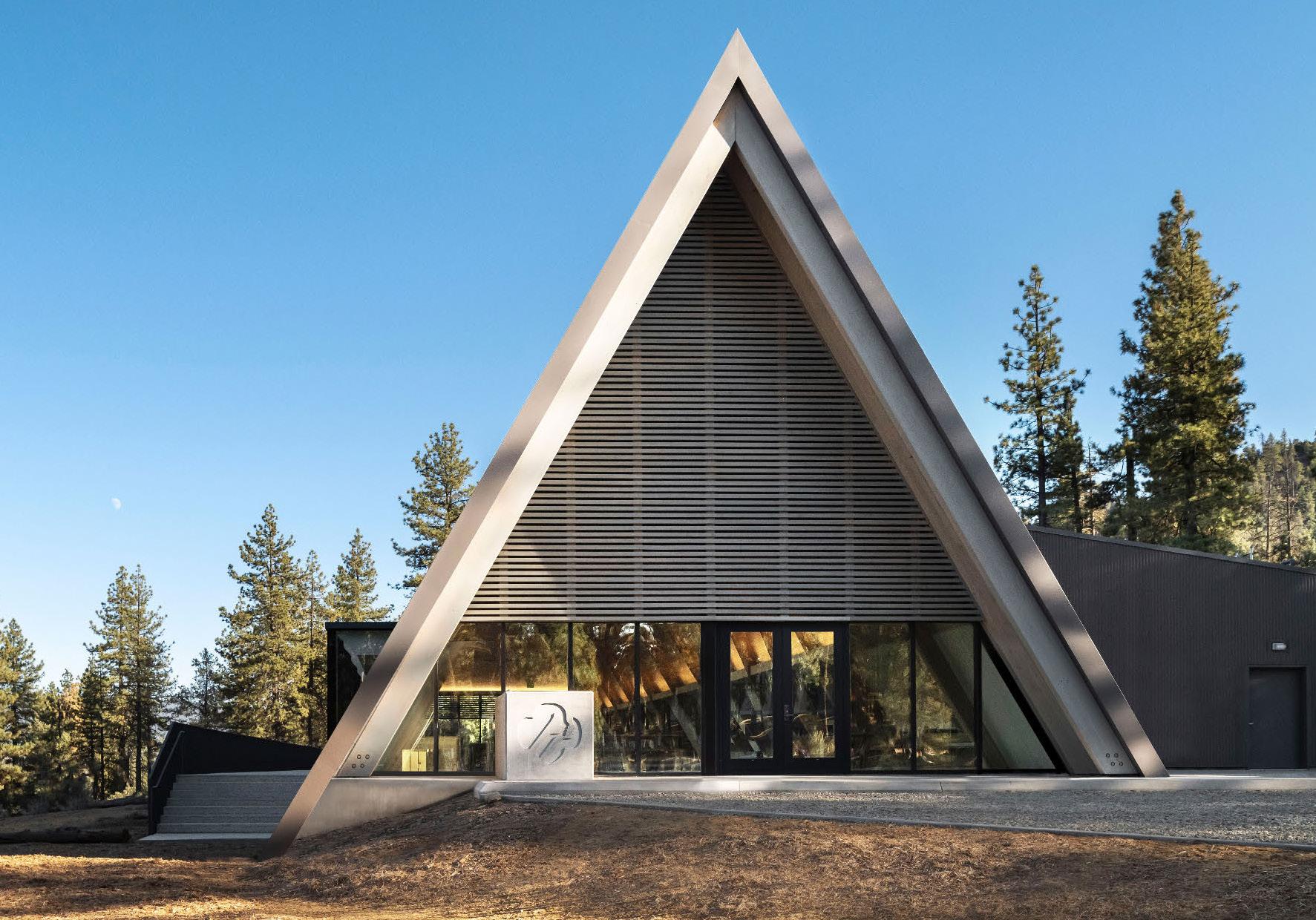
Selecting Mass Timber
We arrived at Mass timber through a cost comparison of different structural assembly options including SIPS, traditional framing, joist framed floors, CLT floors, slab on grade and raised slab with stem wall.
Mass Timber (CLT) allowed for the second lowest cost next to slab on grade but without the extra site grading that a slab on grade would have required.
Mass Timber Parti
The simple triangular geometry of the dining hall utilizes glulam as support for the roof-walls while the cabin floors use mass timber decks to elevate the cabin walls off the ground.
Project Delivery Model
Design Bid Build with preconstruction contractor involvement.
Sector: CCC
Studio: LA
SE: Risha
GC: Illig Construction Co, acquired by Tilden-Coil
CM: Project Development Group
Fabricators: Freres, West Coast SIPs
Dining Hall Exterior 1
Photo credit: Here and Now Agency
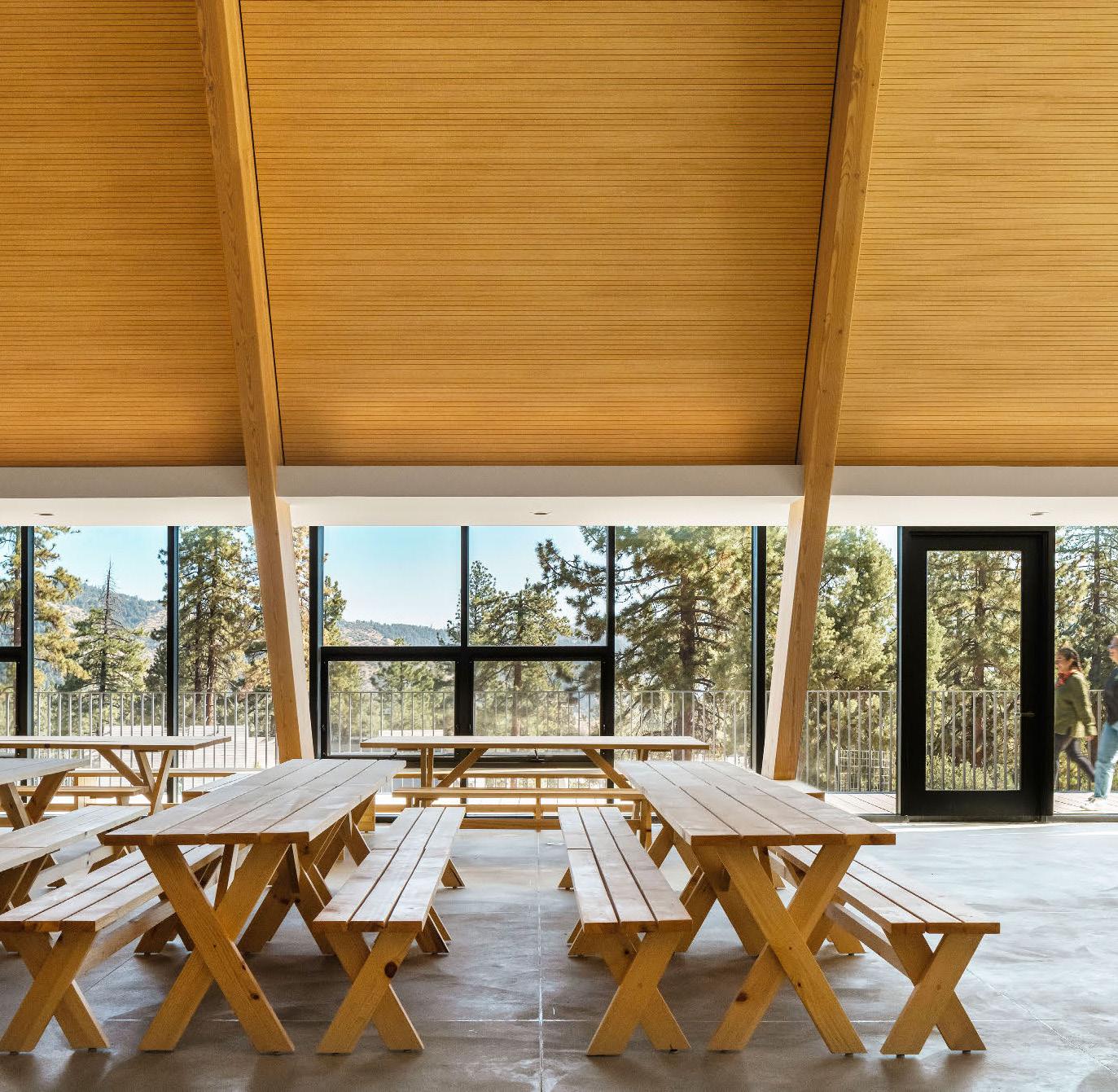
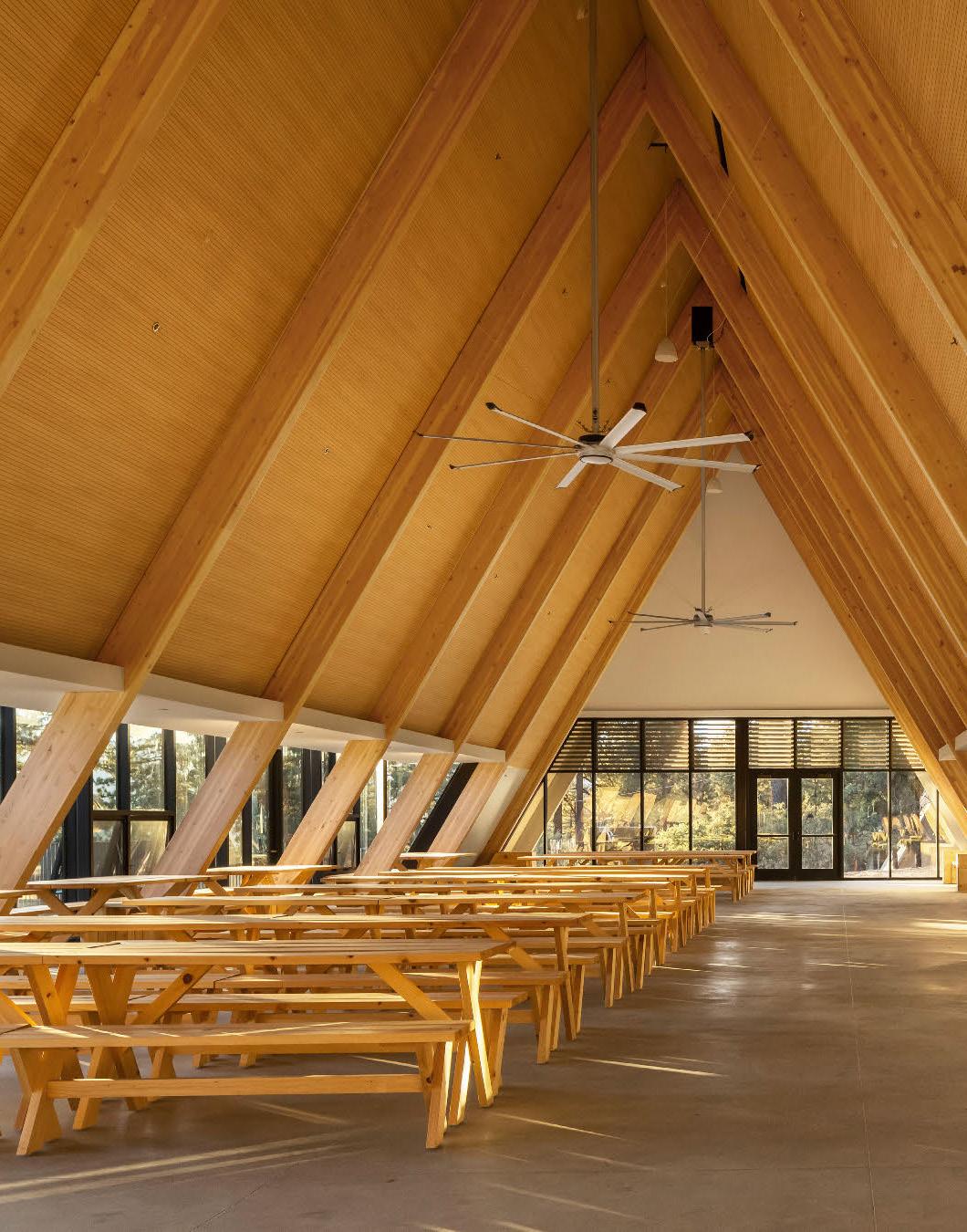
Prior Experience with Mass Timber Design
SE had some experience while the contractor and owner had none.
Design Lead for Mass Timber Architect.
Code and AHJ Challenges
Project was non-standard from a code perspective and the AHJ needed extra dialogue with the code consultant before approval.
Cost and Schedule
Mass timber was put up during winter in the snow, which gave the wood time to dry. Design choices were made with economy of scale in mind. With 36 cabins, prefabrication and construction efficiency had a stronger effect on the schedule than if it were only one cabin.
Camp Lakota Dining Hall Image credit: Here and Now Agency
What went REALLY well?
The floating (4 footing) foundation and mass timber floor framing chosen over a slab on grade foundation for the cabins saved forest floor habitat from disturbance at the wilderness site and resulted in a 29% carbon reduction. The 60 degree shape of the roof/walls of the project allowed it to be classified as a wall that could receive cedar shingles (per the local fire code) and as a roof that met wildfire code requirements. In the dining hall, the concealed connection of the glulams at the ridge is both visually appealing and structurally motivated - an efficient and beautiful design.
Cabin Framing Detail
What were the precious lessons?
After designing the curved awning over the cabin doors to be supported by curved glulams with a 5' radius of curvature, the architect and structural engineer were informed by the manufacturer that glulams with such a tight curve cannot carry the structural capacity needed, so an alternate framing method was used. For the cabin floors, changing product systems due to lead time issues after the start of construction complicated the procurement process. Additional effort was necessary to address the transition from standard CLT to mass plywood.Achieving consistent finishes for the diverse wood and matching finish components within the dining hall posed challenges due to the number and variety of product types, and the nature of the transparent applied finishes.
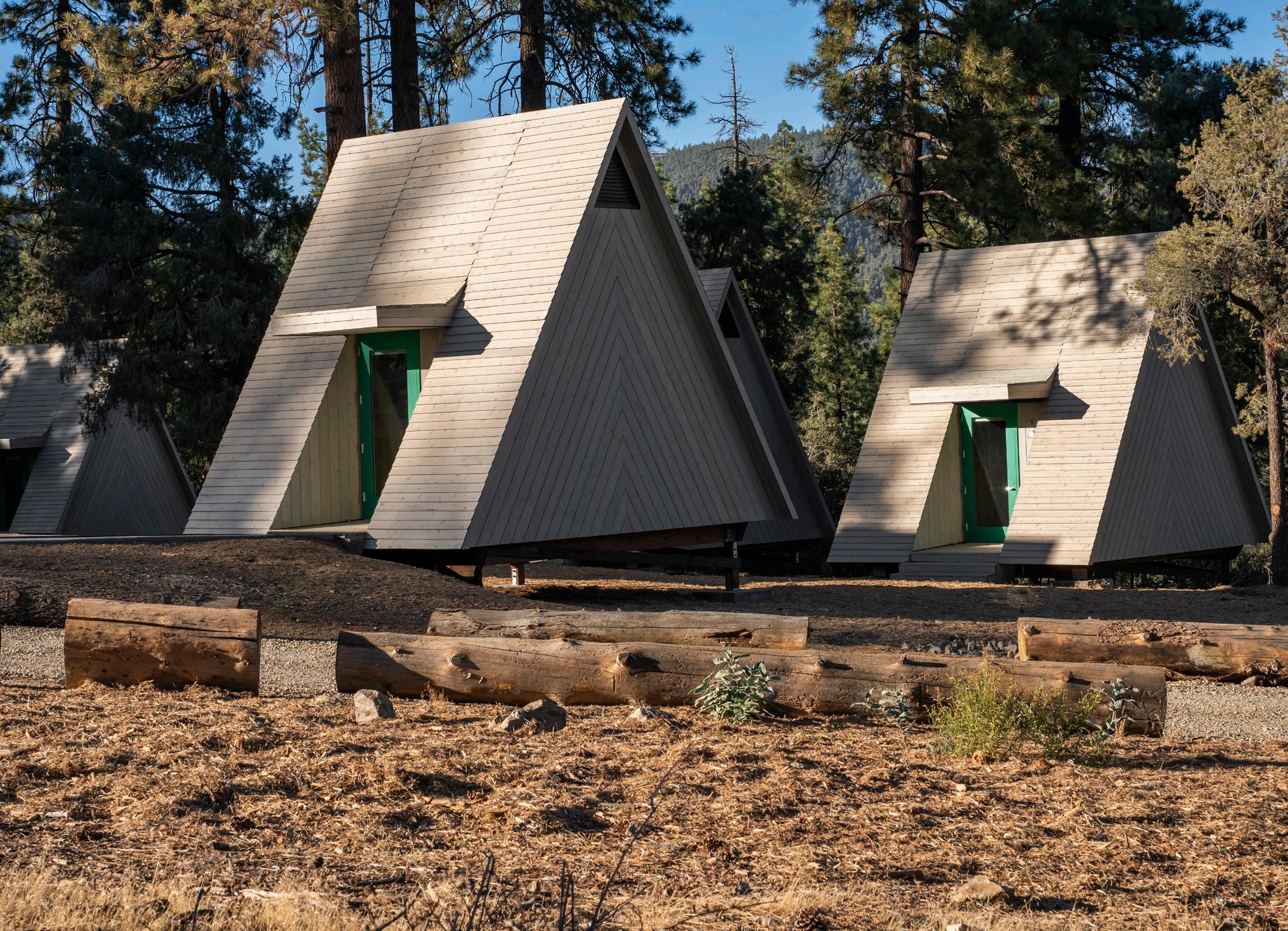
Camp Lakota Cabins Image credit: Here and Now Agency
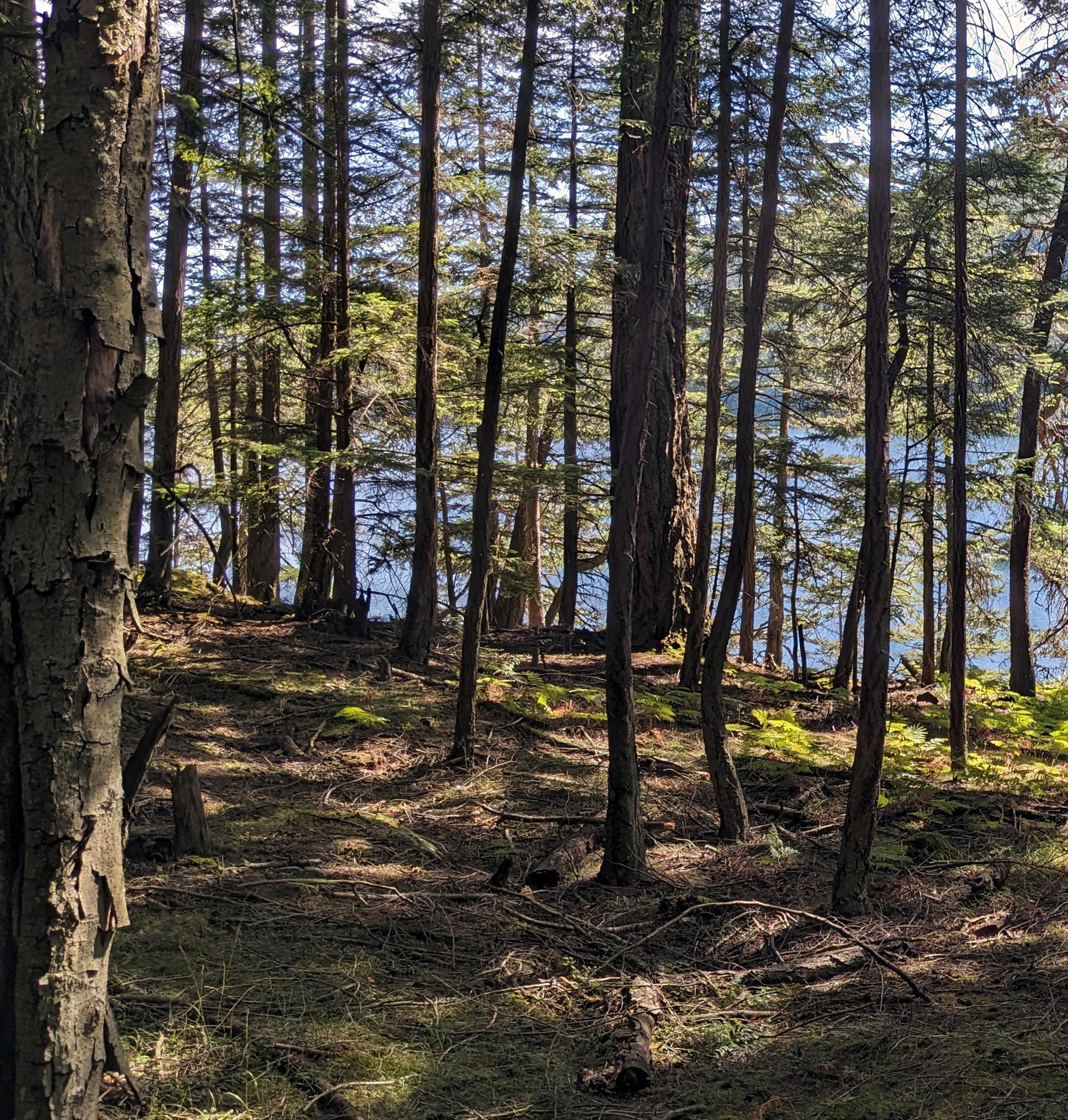
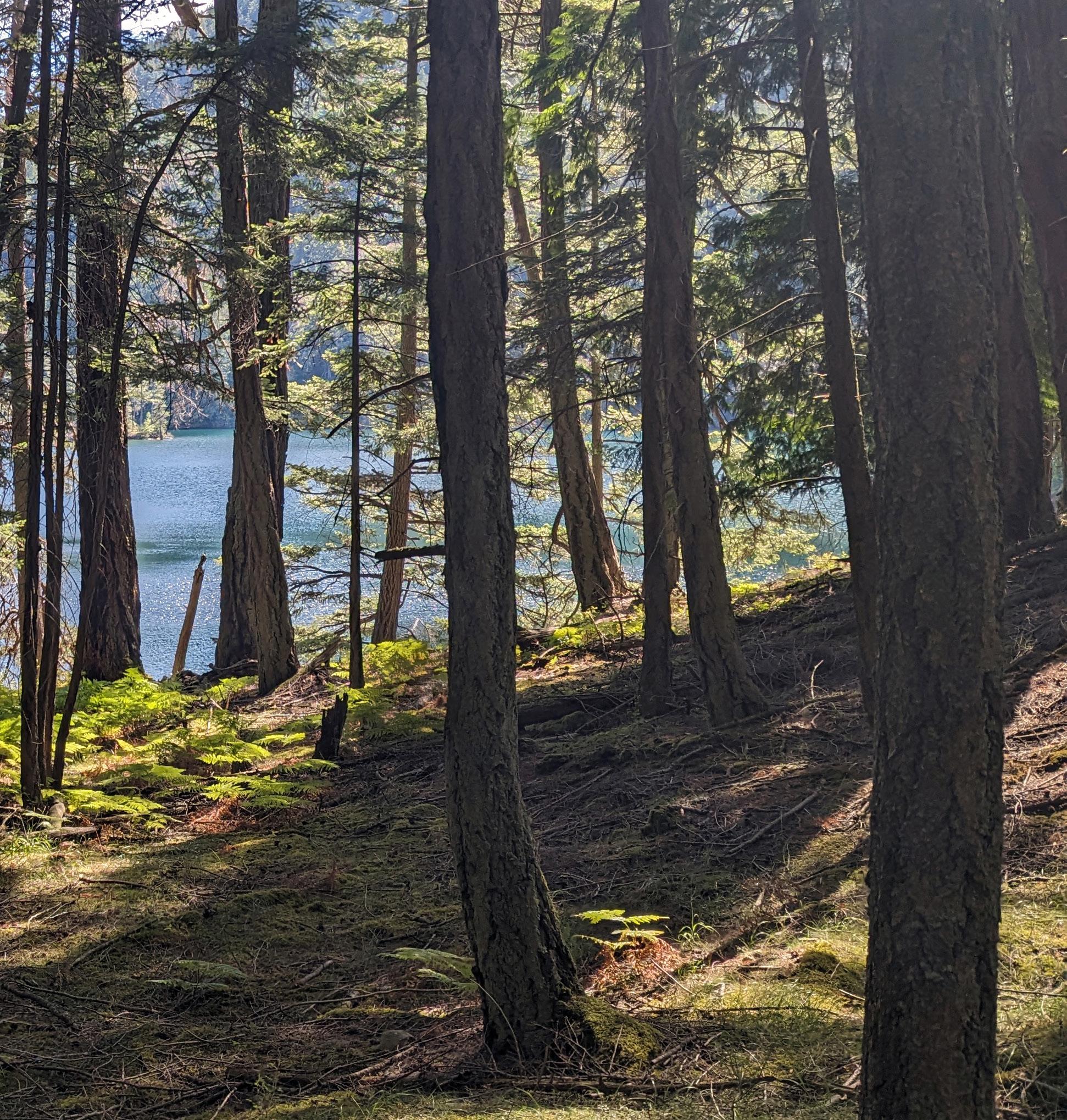
ACKNOWLEDGMENTS
Thank you to these core contributors:
Sindhu Mahadevan
Kelsey McLaughlin
Shireen Khan
Thank you to the following mass timber and forestry experts for your contributions:
Serge Bisson, Art Massif Structure de bois
Ian Boyle, Fast + Epp
Todd Beyreuther, Mercer Mass Timber & Washington State University
Jennifer Cover, WoodWorks – Wood Products Council
David Diaz, Ecotrust
Matheo Durfeld, Kyle Moen, BC Passive House
Lucas Epp, Drew Willms, StructureCraft
Ara Erickson, Weyerhaeuser
Christopher Evans, Swinerton + Timberlab
Brent Davies, Vibrant Planet Data Commons
Don Davies, Davies-Crooks Associates
Eli Gould, Quebec Wood Export Bureau & OffsiteWood
Marie De Guire, Dave Lepage, Nordic
Brian Hawrysh, BC Wood
John Henrikson, Wild Thyme Farm
Mike Jacobs, Idaho Timber
Rachael Jamison, American Wood Council
Keith Murray, Kurt Westerlund, Fraserwood Industries
Ron McDougall, Structurlam
Eric Ortiz, Freres Lumber Co., Inc.
Lee Scott, Element5
Matt Timmers, John A. Martin Associates
Arthur Tsai, Canfor
Mitch Warren, Kalesnikoff Mass Timber
Washington State Department of Natural Resources
Herbert Yancey, International Woodland Company
Thank you to our Case Study Principals, Project Architects, and Interviewees:
1 De Haro - Peter Pfau, Matt Covall, Mansi Maheshwari
GNW Pavilion - Ryan Bragg, Yehia Madkour
Southwest Library - Carl Knutson, Joshua Rubin, Katie Currie, Ben Shealy
Soo Valley Prototype Home - Derek Newby, Alysia Baldwin
REM Train Stations - Jeff Doble, D'Arcy Arthurs, Duff Balmer, Paul Kulig, Yehia Madkour, Mazen Kandalaft
SFU Stadium - Max Richter, Paul Cowcher
Camp Lakota - Yan Krymsky, Ashley Stoner, Nathan Mattson
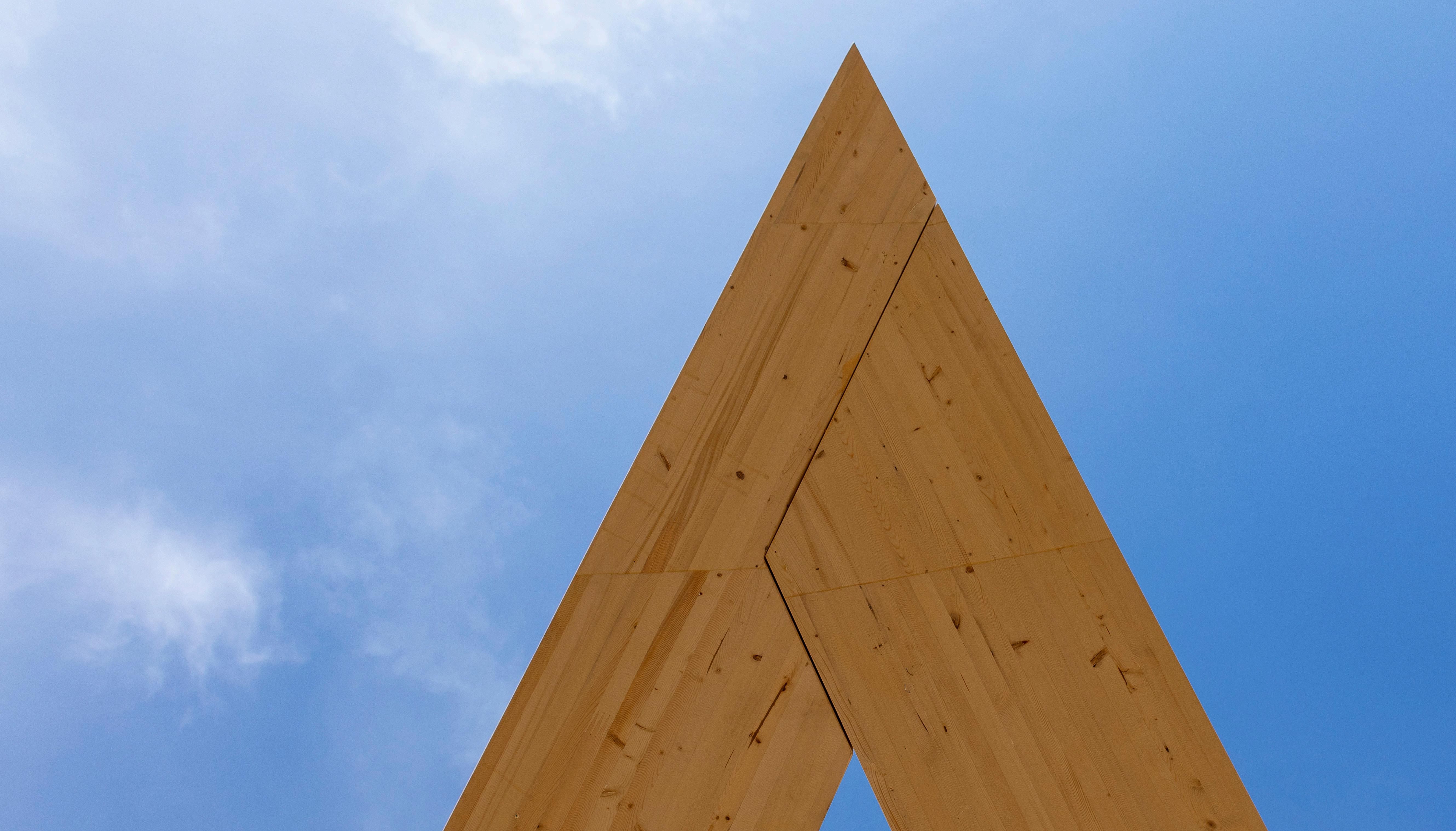
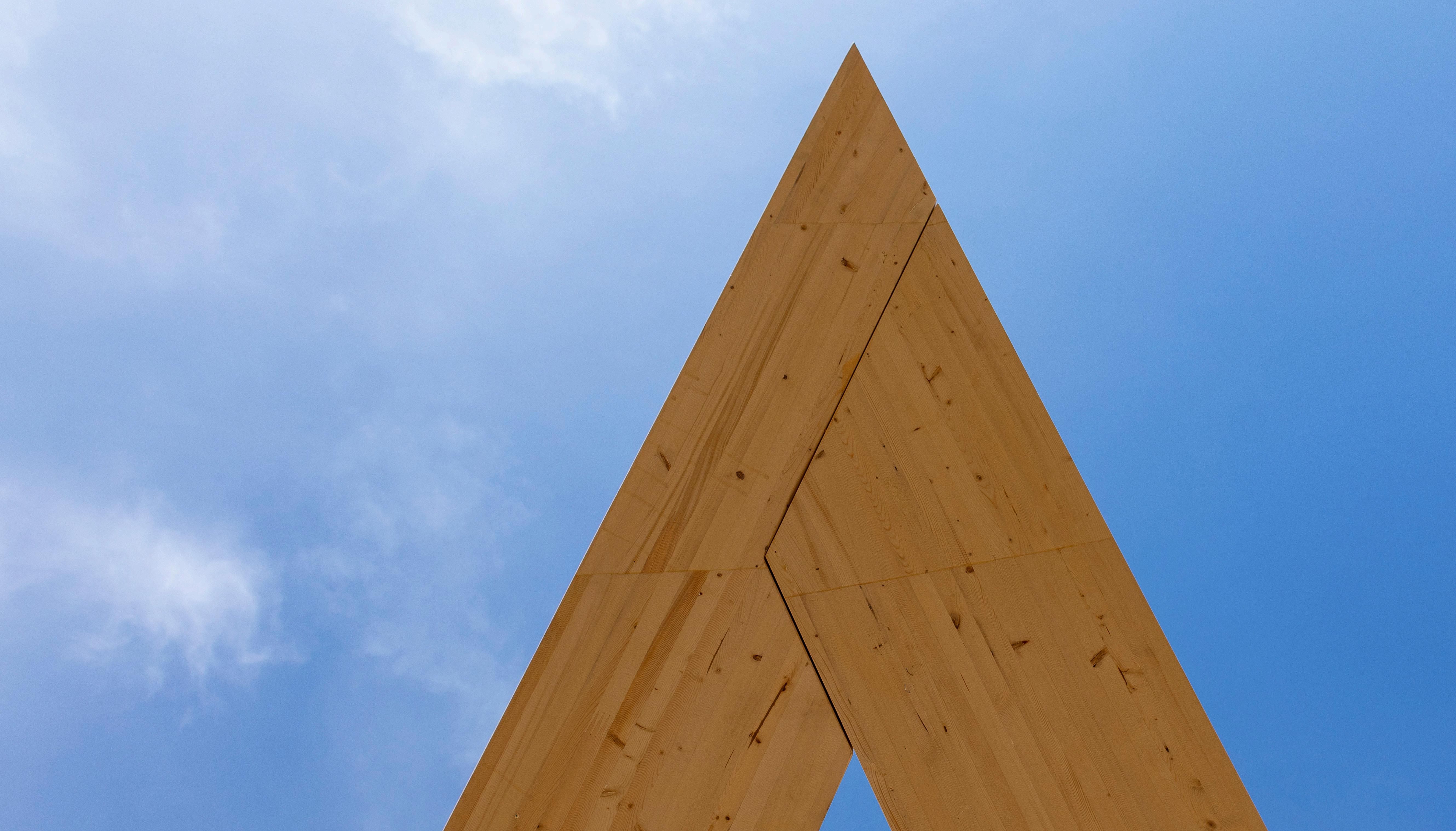