
17 minute read
Focus
Product Liability in Component Manufacturing
By Greg Vassmer, technical coordinator, ARPM, and Joe Keglewitsch, partner, Ice Miller LLP
There are very few Latin phrases known broadly in America, but – at least to some generations – caveat emptor is one: Let the buyer beware. With that phrase, high school children in the 1960s and ‘70s were taught that, when buying a product, they were responsible to understand any inherent dangers the product might pose. This principle originated in the industrial revolutions of the 19th century where the courts actively worked to make it difficult for injured parties to recover damages suffered due to product defects. Even cases of clear negligence were lost by injured parties because they lacked a written contract with the manufacturers of the defective products.
As products became more complex and technological and the consumer became further removed from the manufacturer, state law began to recognize that there was an “implied warranty of merchantable quality” – in plain terms, if someone sells a product to provide a function, it needs to perform that function. A patchwork of state laws and competing interpretations of implied warranty and contract law confused the issue until 1963, when the Supreme Court of California ruled that liability should not be based on the manufacturer’s warranty, but rather on whether the manufacturer was part of the business enterprise responsible for causing injury. In 1964, this strict liability was extended to all parties in the supply chain, including sales representatives, retailers, subsuppliers and, in 1969, even injured bystanders could collect.
As often is the case, the California laws established the direction taken by the rest of the US. Between 1960 and 1977, 42 federal laws were passed dealing with consumer and worker safety, and most states came to the same conclusion as California and passed similar liability laws during that same time frame. Modern product liability became a legal specialty and a mountain of lawsuits resulted.
The struggle since then has been on how to define “defects” and to decide what constitutes a reasonable effort by the
supply chain to avoid those defects. The US has moved from caveat emptor to caveat venditor: Let the seller beware.
Stated in one sentence, product liability is the responsibility of any or all parties in the supply chain for a product that causes monetary and/or physical damage to a user of the product or random bystanders. Everyone in the supply chain who profited by that product can be liable, even those with no manufacturing or design contribution.
Before continuing, and with some irony, the authors must make this disclaimer: Liability laws are different state to state (and constantly evolving). While most follow the tenets outlined here, their case law is different, and one may see different outcomes though the issue is the same. Be sure to seek legal help from firms with experience in the state or country where the liability issue is being heard.
So, what are the typical approaches taken by injured parties in liability cases?
Warranty, Negligence and Strict Liability
The most straightforward approach is a breach of warranty. Warranties can be either express or implied. A breach of an express warranty is directed at the statements, advertising or other promises (verbal or written) that the product will accomplish a certain action or be capable of a certain function. As an example, a local restaurant buys a mug washing device with multiple rubber seals to exclude water. The device is promoted as safe but with express warnings about dipping the electronics in water. A year later, a worker turns the device on and is injured by an electric shock. Since it was promised the item would be safe, he can claim the company breached the warranty (and, in this case, lost when it was discovered he removed the rubber seal over the switch).
An implied warranty is the indirect promise or promises made just by selling the product or service. A product or service must be under certain circumstances fit for the particular purpose it was sold – like buying paint intended to be used on products exposed to high heat, but receiving paint that flakes when exposed to 100 degrees or more. It must be done with workmanlike quality, meaning that the work meets the level expected of someone with proficiency in the area. And last, the product must be merchantable – that is, it must perform like products sold to do similar things. An icemaker should make ice, an oil seal should seal oil, a new power steering belt should not snap when someone starts her car and so on.
Another common claim is negligence. A manufacturer has a duty to consider potential customer safety issues during the design and manufacture of the product. The manufacturer is expected to take reasonable care and reasonably foresee anything that might cause harm or injury to others using the product or equipment. This obligation extends to include the equipment in which the component might be built. Notice the word “reasonable” shows up several times. In these cases, “reasonable” means “for those who are experts in manufacturing similar products.” Some negligence is obvious – for example, not following a law or regulation. Other types are more indirect, such as not taking sufficient care and protecting against well-known causes of failure.
Another element of negligence deserving comment is foreseeability. Foreseeability is the requirement to reasonably anticipate the potential uses of a product, including damage or injury that may happen if one is negligent or breaches a contract; for example, using an unapproved supplier.
In manufacturing, failure mode and effect analysis (FMEA) tools are used to anticipate exactly those conditions by examining all possible ways a product or manufacturing process can fail when used or executed as intended. Many manufacturers apply FMEA techniques to their operations, but product liability should compel them to understand activities at their customers. For example, this could include handling and installation of the component, and if critical, of the end-consumers potential uses that may impose safety constraints on the component.
The last and most common claim is strict liability. In simple terms, the person who made it can be liable if the product causes injury, even if that person was not negligent in the manufacture of it (in fact, even if the manufacturer exercised great care) and even if the manufacturer did not design it. For instance, if a power tool has an unexpected tendency to kickback and injure the user, the manufacturer would be found liable notwithstanding the fact that it was well-designed and flawlessly manufactured.
All links in the supply chain can be included in a liability case; however, the most targeted companies are the OE manufacturer and its sub-suppliers. They are considered to have the best ability to pay back the injured party and have provided most of the design, manufacturing and marketing material relied on by customers to operate a product.
So, where in an organization are liability issues most likely to be generated?
Liability from Design Defects If the design of a product does not perform the task intended or is inherently and foreseeably dangerous to use, that design can be considered legally defective. Rarely is it as clear cut, and language like “reasonable” and “foreseeable” become the source of most of the arguments. Most products can be dangerous even when used correctly. Proving responsibility
t page 7
for a defective design can be very complex since the materials, components and final assembly each have specifications, testing and management decisions from several levels in the supply chain.
As an example, in the mid-1980s, fluoroelastomer o-rings were used to seal the solid fuel rocket boosters of the space shuttles. The Shuttle Challenger explosion in 1986 demonstrated that the specific fluoroelastomer compound used in these o-rings lost flexibility at about 32° F and did not seal the gap between rocket booster sections during launch, subsequently burning through the wall of the rocket and nearby components, becoming the proximate cause of failure. Ultimately the o-ring joint design failed and was dangerous. But who was liable? NASA made the decision to launch, Marton Thiokol assembled the rocket booster and o-ring joint as well as confirming the o-ring would work under cold conditions and Hydra-Pac Inc. made the o-ring from fluoroelastomer cord provided by Parker Seal Group. The cord met all specifications set by Morton Thiokol, which included performance at cold temperatures. A final complication: A Thiokol engineer anticipated and reported the potential failure mode of the o-ring before launch to his management.
The case was never tried. Morton Thiokol settled with all interested parties. However, a shuttle did not launch again for 32 months and did so with a completely redesigned o-ring joint, new sub-supplier specifications, new test procedures and a new set of application criteria. To establish liability, some jurisdictions now require the plaintiff (the injured party) to show that it was practically and economically feasible to use an alternate design that would have been safer or that the risk was greater than what an ordinary consumer would expect. For example, putting a blade guard on a circular saw is a good, low-cost alternate design considering the high risk of selling a saw without one.
Manufacturing Defects With a design defect, all products coming off the manufacturing line have the defect. If the defect is in the manufacturing itself, then typically the failure is due to poor quality workmanship, mistakes in assembly or raw materials, which fall outside the manufacturer’s specification or design. Products produced outside tolerance, or with sub-standard materials from a new, less costly supplier are examples. Consider a rubber mold that, with age, becomes misaligned between top and bottom. If that alignment affects performance, and the product fails prematurely because of it, the customer can claim (rightfully) that the manufacturing defect was the source of injury.
Marketing Defects This last type of liability arises from all injury following from poor instructions, inadequate packaging or lack of warnings “THE MORE INTERACTION THE COMPONENT SUPPLIER HAS WITH THE CUSTOMER IN THE DESIGN PROCESS (FOR EXAMPLE, IF THE SUPPLIER SUGGESTS CHANGES FOR MANUFACTURABILITY OF COST REASONS), THE MORE THE SUPPLIER BECOMES PART OF THE END-PRODUCT DESIGN AND CAN BE CONSIDERED LIABLE.”
about potential product dangers. It does not matter how well the product is designed or manufactured. There is a duty to inform the customer of all potential safety issues that are inherent in the product. The result at one end of the spectrum may be warnings, such as, “This drink is very hot” and “Do not trim hedges with this lawn mower.” But for component manufacturers, this can extend to storage and handling instructions, installation guidelines or providing packaging that keeps a product clean or undamaged.
Examples for Component Manufacturers
For a component manufacturer in the middle of a supply chain – such as a gasket manufacturer selling to a hydraulic pump manufacturer that in turn sells to a construction equipment maker – certain liability scenarios occur more often than others. It makes sense to review these variations and how courts have responded.
Consider the situation where the end-customer designs a component and the supplier builds it. The relevant statement from current product liability law says that if the supplier substantially participates in the integration of the component into the design of the product and the integration of the component causes the product to be harmfully defective, the supplier is liable.
When the component supplier is named as liable, two avenues of defense have developed. First, the component manufacturer can argue that it is a bulk supplier, where the product is sold in bulk to a third party and where it is
impractical to know all potential end uses of the product. If the bulk product itself was not defective, the component manufacturer is safe.
The second avenue is the “sophisticated purchaser rule,” which provides that the component manufacturer owes no duty to warn “sophisticated” purchasers where the purchaser has a sophisticated knowledge of the product and of the types of risks associated with the product. The component supplier is not required to monitor the development of products and systems into which its components are to be integrated.
The more interaction the component supplier has with the customer in the design process (for example, if the supplier suggests changes for manufacturability or cost reasons), the more the supplier becomes part of the end-product design and can be considered liable.
Another common situation is the improper use of the component part due to either poor handling and installation or by being put into an application different than one expected. In these cases, the supplier has a duty to provide instructions on use and warnings related to safety. If little or no instruction is given on use and handling and injury occurs, the supplier can be held responsible. Guidelines – such as ARPM OS-7, which outlines best practices with radial lip seals – are an example of instructions that can be used as part of customer documentation.
Additionally, if a customer uses a product in an unexpected way (for example, using a high-pressure seal in a lowpressure application), the supplier could expect an argument that it had a duty to warn the customer of the operating limits of the component, especially if an injury occurred.
Strategies in Product Liability Risk Management
While product liability claims certainly represent the kinds of exposures that keep manufacturers up at night, the good news is that there are strategies that can be employed to manage and minimize the risks of being named in a product liability claim.
Transfer Risk through Management of Suppliers and Supply Contracts A strong sub-supplier network can help strengthen the message that the product design was well executed and that the raw materials came from well-controlled sources. After all, the best defense against a product liability claim is no defect in the first instance, and a well-vetted and supervised supplier is the most effective avenue to that result.
page 11 u
t page 9
When things do go sideways, a supplier network (if responsible in whole or in part for the issue) also can be a source of recovery that allows claim costs to be distributed more widely. However, one must be certain that the relevant commercial terms are well documented. Some items to include in a well-constructed supplier contract are as follows: • Hold harmless agreements, where sub-suppliers are contractually responsible for their own negligence and/or errors. • Indemnification provisions with clauses requiring vendors to reimburse the costs, expenses, obligations and liabilities resulting from product, component or material failure and any associated litigation and claims. These provisions also should address who will handle and how they will handle the actual defense of third-party claims. • Robust warranties of sub-supplier product or component. • Statements of financial responsibility with confirmations that sub-suppliers have appropriate insurance in place. Ask suppliers to name subsuppliers as Additional Insured to allow the supplier’s policy to be primary and the subsupplier’s policy to be secondary. Manage Imported Products, Raw Materials or Components The US-based receivers of imported components may end up being held fully responsible and considered the manufacturer of record. Be sure to gather all design and related information regarding the material or component in advance. Be sure to develop proper warning and instruction documents since foreign suppliers may not be familiar with US requirements. Finally, utilize letters of credit to ensure foreign suppliers have sufficient assets in the US to support their indemnification obligations.
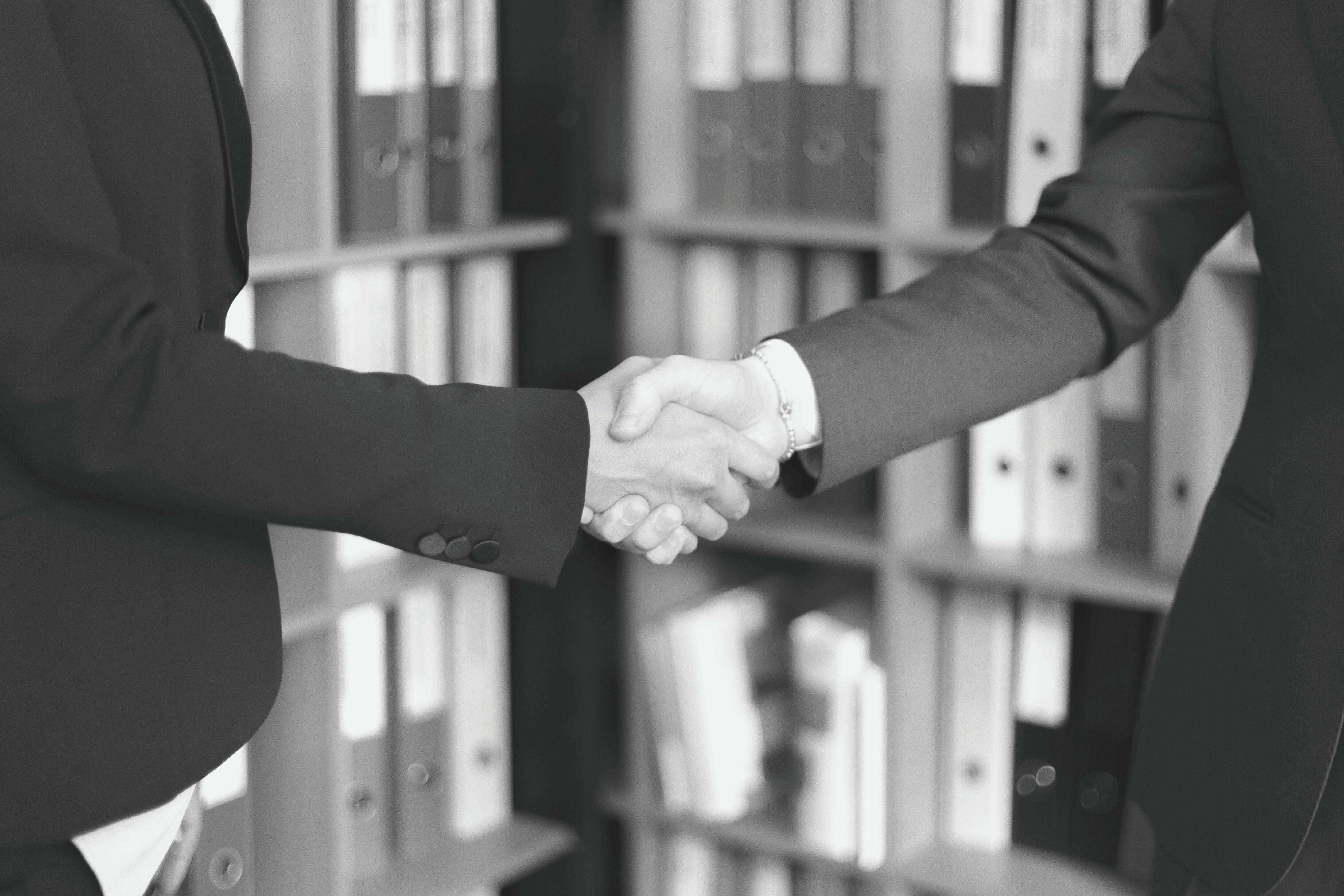
Build in Safety at the Design and Manufacturing Stage Create a product safety policy and, where possible, a committee that builds and oversees corporate culture for safety. These policies encourage operator reporting of potential product defects on the factory floor and ensure the FMEA results lead to mitigation actions. The committee will manage the communication with legal counsel in the event of a product claim and ensure all necessary documentation and information is retained for both defense purposes and internal remedial steps to avoid the same issues going forward. In addition to a FMEA of the supplied component, also gather similar FMEA information from the customer on
page 12 u
OUR MACHINES KEEP RUNNING
WE KEEP INNOVATING
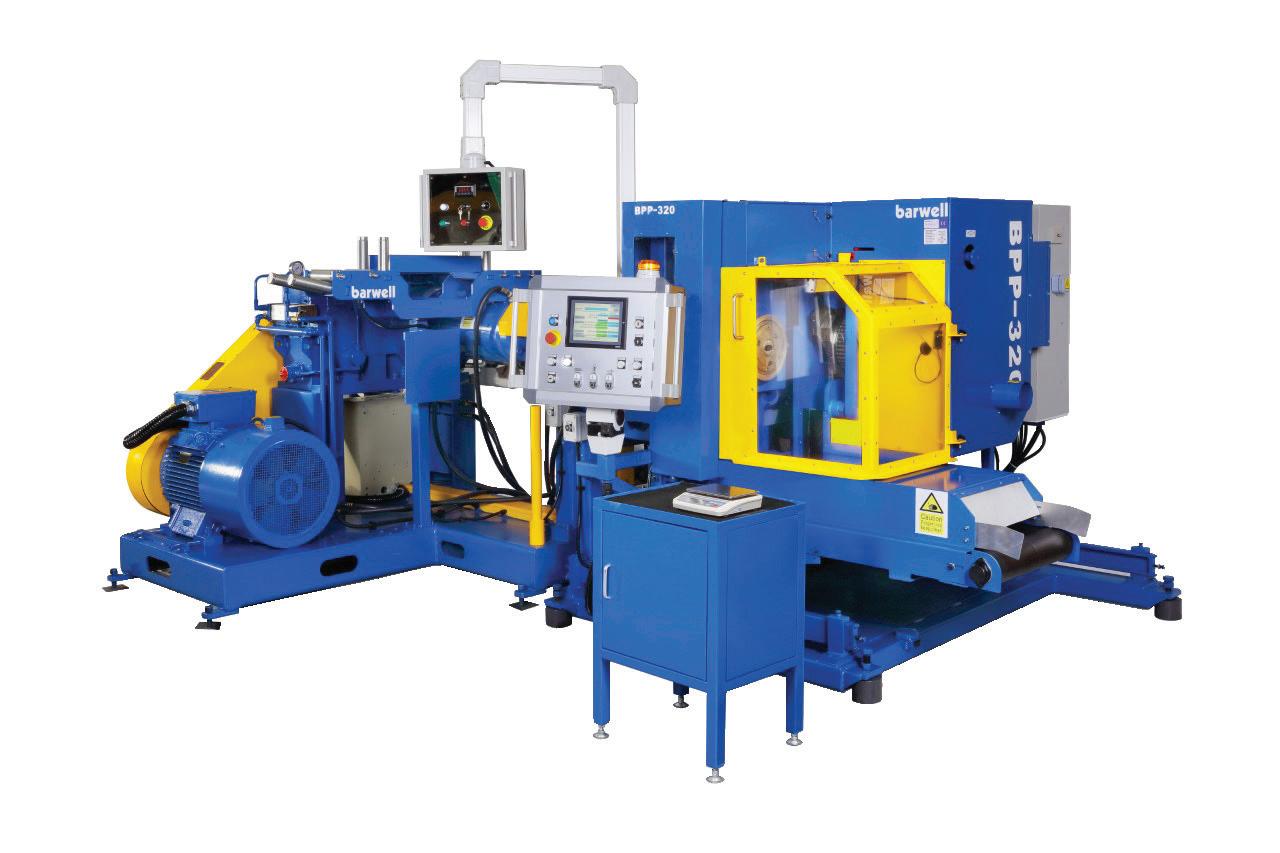
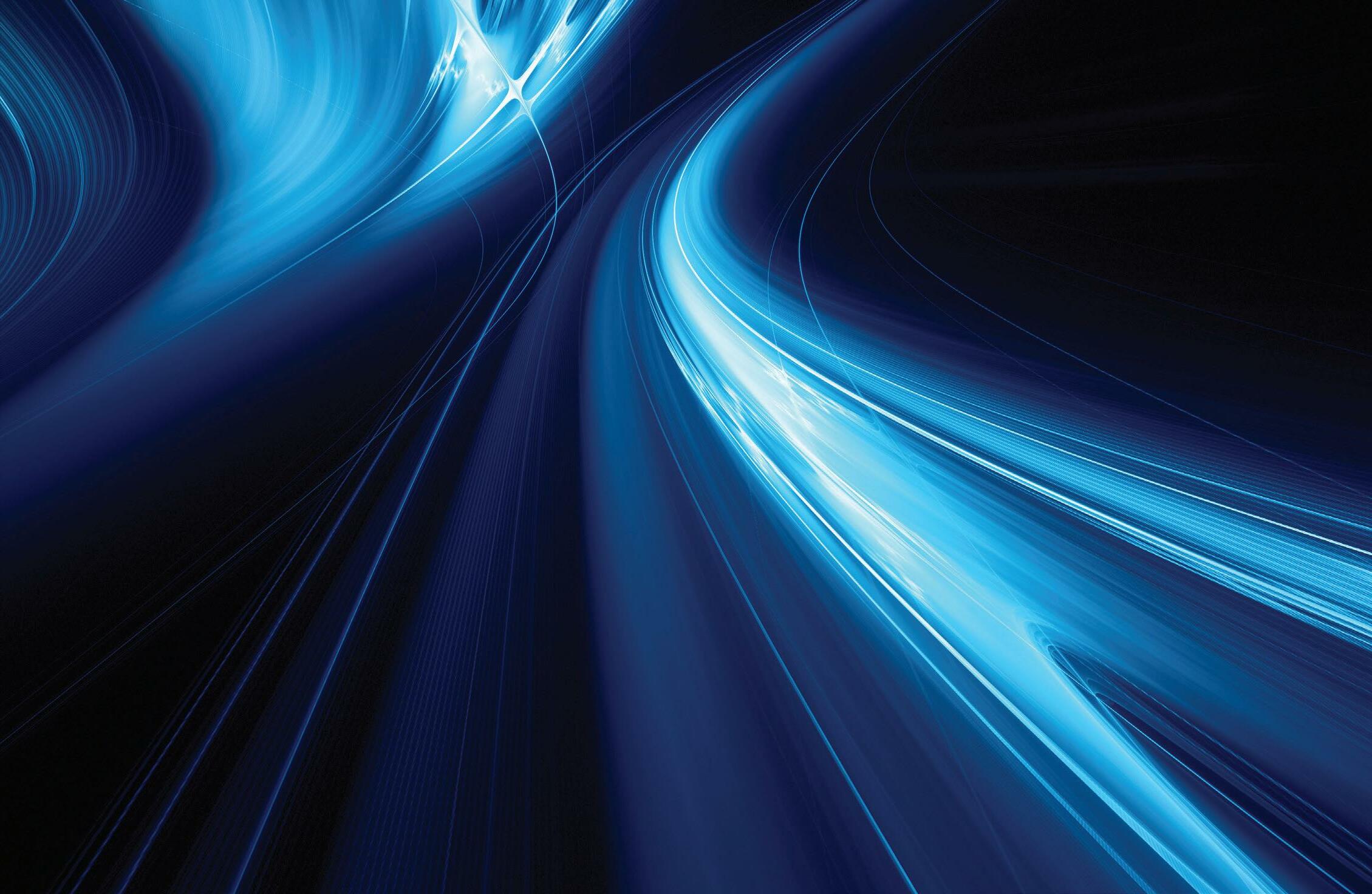
We have machine solutions for all your rubber processing challenges, supported by expert service, commissioning, and genuine spare parts. THE BARWELL FAMILY
info@barwellusa.com +1 330 225 9557 www.barwellusa.com ...a lifetime of reliability and support
t page 11
the installation and handling of the supplied component, as well as the final application of the product. Use the FMEA results to identify risk mitigation actions, such as warning labels, process changes, vendor upgrades and product improvements.
Getting out in front of issues before they occur is the most effective risk mitigation strategy. Make sure that the products and processes strictly comply with industry or government standards, such as those published by oragnizations like ARPM, ASTM and ISO.
Have and follow a certified quality system (such as ISO 9001), with well-structured documentation and product development and engineering change processes. Conduct audits of customer returns, complaints and other feedback. Early action on this information will help avoid claims in the future. Once a field issue is identified, move to contain and limit the issue quickly. Finally, communicate potential safety issues to the customer early to expedite remedial action and mitigate damages. When investigating an issue, follow a systematic root cause analysis as soon as the issue is known, even before there is a liability claim. Industry troubleshooting guides like ARPM OS-17 can assist the investigators through all failure modes and identify the source or sources of a potential issue.
All the analysis of failure modes and causes also must lead to comprehensive warning documentation and clear use and handling instructions.
Warranties and Limitations of Liability One of the most valuable tools available to a manufacturer is a well-crafted product warranty. Tie a warranty to meaningful, objective standards, rather than nebulous concepts like “good quality,” “workmanlike” or alike. Further, disclaim those warranties that are implied by law into the sales of goods, namely, the implied warranties for merchantability and fitness for particular purpose. Also, do not take on risks for which the company is not compensated and be certain when possible to expressly waive liabilities associated with design, material and related guidance provided customers as a gratis, value-add benefit.
Next, be sure to limit the scope of recovery if there is a breach of warranty. When possible, disclaim indirect, consequential, special and punitive damages. This step can take some bigticket exposures off the table. Finally, capping damages under a supply agreement (when the leverage exists to make it happen) to some finite number (such as a certain period of sales) is a meaningful way to create an identifiable and manageable exposure. Keep Important Records As a final point, be sure to keep all product orders, design specifications, customer signoffs and emails. Follow written manufacturing procedures and quality control steps, retaining all quality control information. For example, keep a sample of product used for production part approval for later reference if a deviation from specifications is suspected. Furthermore, establish a document retention policy and structure to reliably have and be able to find information needed in a liability claim.
Summary
Receiving a product liability claim can be disruptive and expensive. It also should be treated as inevitable if a company is supplying components to products that eventually will be used by a public consumer. Simple strategies used by companies to deflect responsibility, such as “I didn’t design it,” or “I made it to their specification,” are inadequate if the supplier could have foreseen the failure with a reasonable amount of diligent effort. The robustness of the design and manufacturing processes can minimize the chance of a claim. Know what the company is making and how it will be used. Ensure the manufacturing processes are well-governed to reduce their variation, and communicate with the customer the limitations of the product.
Even with all this care, claims still may be filed against a company. Be sure to have optimized the relationship with suppliers, financially and legally, to participate in the claim as needed. Assistance is available both through independent law firms and insurance carriers. Involve them early in the claim process. u
Greg Vassmer is a semi-retired engineer and owner at Fluid Sealing Science, a consulting engineering firm for the rubber industry. Vassmer’s long experience in the sealing, hydraulics and brake industry, along with his operational improvement and six sigma practice, allow him to help companies improve their profitability. He also supports ARPM as its technical coordinator on the Dynamic Sealing Committee and writes the Technical Standards Update page for the Inside Rubber. He can be reached at gvassmer@arpminc.org.
Joe Keglewitsch is a partner at Ice Miller LLP and handles complex corporate and business law issues for both private and public companies, with a focus on and extensive experience in the following areas: mergers and acquisitions, general corporate counsel and complex commercial relationships. He can be reached at: 614.462.2279 or josef.keglewitsch@icemiller.com.