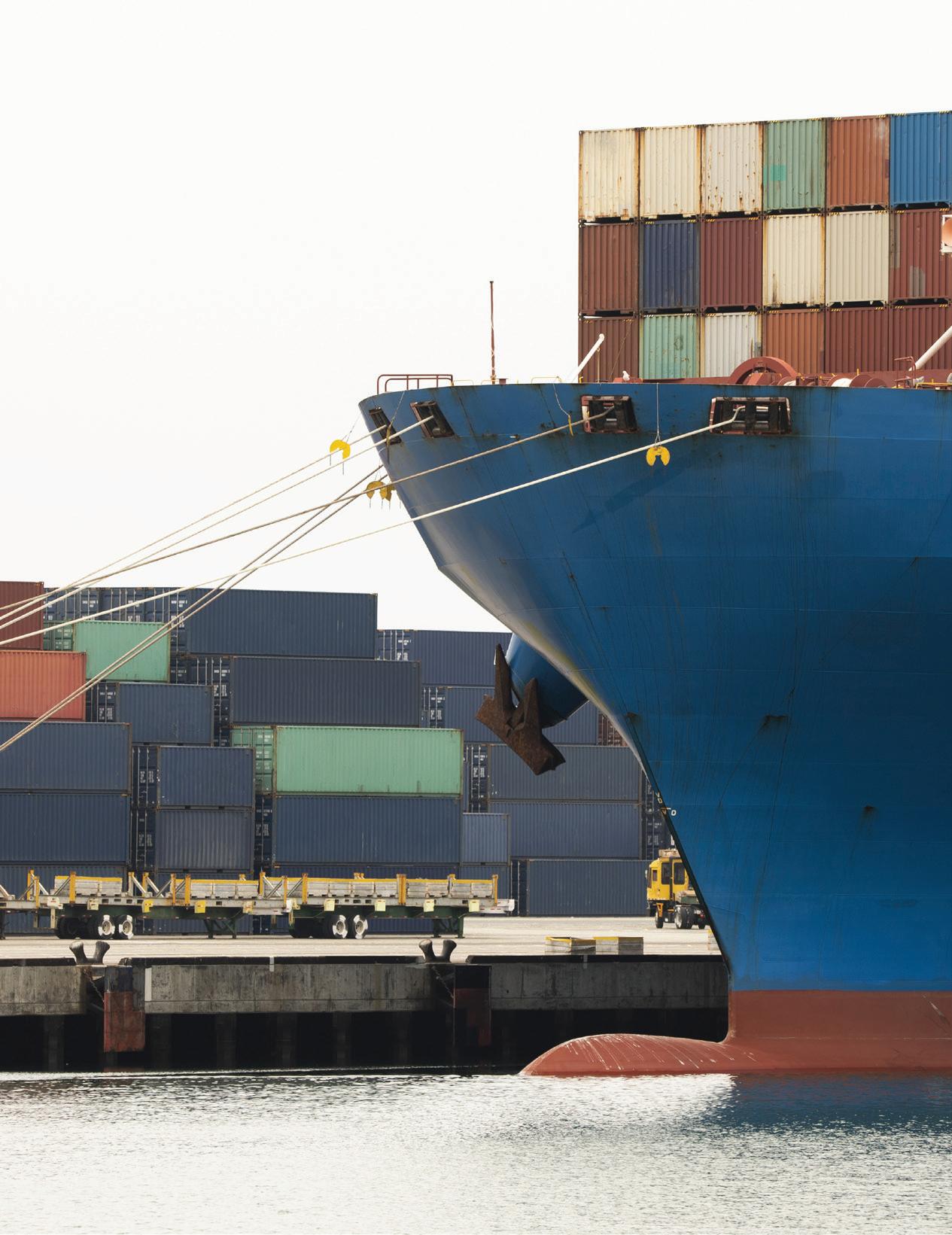
17 minute read
Outlook
Rubber Industry Supply Chain Disruptions
By Liz Stevens, contributing writer, Inside Rubber
As 2022 gets underway, rubber processors are facing enormous pressures. An increased demand for their products is crashing head-on into the lingering worker shortage and a crippling supply chain crunch. Processors have struggled to find trained workers during a period when fewer workers are seeking manufacturing jobs. Add to that the current tight material supply and rising prices, logistics madness and a booming market for products, and it is no surprise that processors are lying awake at night, wondering how to meet these challenges.
How Did the Supply Chain Jam Transpire?
The rubber supply chain quagmire stems from several factors. Prices for imported rubber and ingredients already had risen in 2018 due to the Trump Administration’s trade and tariff wars. Then COVID-19 hit, sending shock waves that resulted in factory slowdowns or shutdowns in China that spread to the US and the rest of the world.
The start of the COVID-19 crush affected rubber and polymer suppliers but not in the ways that the suppliers expected. In the Spring of 2020, suppliers faced an entirely new and unpredictable future; many (or maybe most) of them feared that the entire US economy would shut down due to the dramatic “shelter in place” orders issued in many states. Suppliers scrambled to sell what stock they had on hand and then radically cut their production. But, at the start of the summer, suppliers were shocked by the unexpected: Consumer demand surged rather than tanking.
The pandemic caused a surge in demand for medical-oriented products like ventilators, rubber gloves, PPE and coronavirus test kits. But the scope of the demand surge was much more widespread than this – nervous citizens began buying up all sorts of household supplies. Then, with the pandemic hobbling activities and travel, home-bound Americans began a consumables and home improvement shopping spree that upped traffic along global trade routes. At the start of 2021, when rubber and ingredient suppliers thought that the balance of demand and supply finally had evened out, along came unprecedented winter storms in the US. A calamitous deep freeze in Texas crippled petrochemical plants and polymers were once again in short supply.
The still surging import traffic flow then was hit by a whammy as cargo shipping was upended after the ship Ever Given wedged itself in the Suez Canal. Meanwhile, the US consumer buying spree continued and the incoming goods – on ships finally able to navigate the Suez Canal – began overwhelming US ports, rail transport and trucking, all of which also impacted the import and delivery of rubber and ingredients to manufacturers. As of January 2022, the Omicron variant of COVID-19 began blanketing the nation with skyrocketing contagiousness but milder disease than the Delta variant. And everyone, in every industry, in every nation, was waiting to see what would happen next.
t page 15
For a look at the current situation, advice for dealing with the challenges and some predictions for the future, Inside Rubber talked to representatives from two equipment manufacturers, along with a custom polymer compounder and a rubber processor. Dave Jentzsch, former chairman of the board at the Association of Rubber Products Manufacturers (ARPM) and now a consultant to Blair Rubber/Hyload, Seville, Ohio, gave us insight from his perspective as a former producer of rubber linings for industrial use in 20 countries. Paul Callitsis, director of purchasing at Chardon Custom Polymers, Chardon, Ohio, offered his view as a maker of elastomeric rubber compounds for North America. Russ Burgert, director of after sales, MAPLAN of South Elgin, Illinois, and Derek Williams, vice president of sales at REP Corporation, Kodak, Tennessee, contributed their insight as equipment manufacturers for the global rubber industry.
The State of the Rubber Industry
From Paul Callitsis’s vantage point at Chardon Custom Polymers, the polymer and ingredient supply chain situation exists in a market that is extremely tight and with numerous significant price increases. “Most suppliers,” said Callitsis, “have instituted some form of volume sales control or allocation – based off historic usage or approved forecasts – which cannot be exceeded.” Already long lead times have been extended, and freight costs have soared. The culprits, Callitsis said, include “strong demand, high energy costs, lack of containers, delays at port, ongoing COVID-related labor shortages and resulting production delays.” In Callitsis’s estimation, the pandemic factors, the skyrocketing demand for rubber-related products, labor shortages and transportation delays are the main factors impacting compounders and their customers. Recent and pending anti-dumping lawsuits also have contributed to higher prices and shortages as well.
Derek Williams, REP Corporation, explained how the supply chain disruptions have affected his equipment manufacturing company’s ability to source parts and materials to build rubber processing equipment. “As all manufacturers utilizing electronic components face delivery issues related to chips and electronic cards, we are not immune,” he said. “Thankfully, we use a proprietary operating system, and our components are made specifically for us. Those impacts have been fairly limited, but nonetheless clearly felt.” REP’s machinery is made in Europe and Asia, and logistics snarls have affected deliveries and installations. “REP machines are made in France,” said Williams, “and our secondary line of machines are made in Taiwan. The shipping from France has been fairly stable, though higher shipping cost is a factor as prices for standard containers have increased.” Williams explained that for equipment shipped from Asia, availability remains a problem and high cost is becoming prohibitive. “Rate increases of 300% for shipping become untenable to “...THE PANDEMIC FACTORS, THE SKYROCKETING DEMAND FOR RUBBERRELATED PRODUCTS, LABOR SHORTAGES AND TRANSPORTATION DELAYS ARE THE MAIN FACTORS IMPACTING COMPOUNDERS AND THEIR CUSTOMERS. RECENT AND PENDING ANTI-DUMPING LAWSUITS ALSO HAVE CONTRIBUTED TO HIGHER PRICES AND SHORTAGES AS WELL.”
our customer base,” he said, “and some projects have been delayed in order to wait out the exorbitant increases.”
Despite the challenges, REP has been able to continue installations, training and repairs for its US customers. “REP Corporation in the US has been fully flexible in the field service area and has not missed one installation or service call due to the pandemic in 23 months,” Williams said. The company’s team has traveled to Canada during lockdowns since is it considered an essential service for industry to maintain production levels. “We have been all over the US,” said Williams, “installing, servicing and training new and existing clients to ensure that our products and services keep them running.” Williams credits a team that remained agile, flexible and proactive to maintain this essential part of REP’s business model. “Customers that had a ‘no visitors’ corporate mandate,” noted Williams, “quickly changed their minds when they needed help with a piece of equipment. And we were only too happy to assist.”
MAPLAN’s Russ Burgert spoke for another equipment manufacturer that has stayed busy with installations, service calls and customer training, but Burgert’s company has been hit hard by the semiconductor chip shortage. “It is coming close to shutting us down,” Burgert said. “We are having a hard time getting PLCs and HMIs for the last four months
due to the chip situation. We are taking drives from one machine to the other so that we still can build them, but we can’t deliver because we are having a hard time getting the electronic components, like pressure transducers. Beyond that, everything else is pretty good.”
Beyond the chip situation, everything for MAPLAN is not just pretty good; it’s really good. “This year, we are having an all-time historical year,” said Burgert, “and we sold out 2021 in May. That has never happened before.” Burgert sees this as a confluence of rubber manufacturers having unexpected downtime in which to consider expansion, a surprisingly robust economy and financing that is available at low interest rates. The rebound, said Burgert, has been dramatic. “Machine suppliers – we always are the first to go and the last to come back when we have a situation such as we just went through,” he said. “As soon as the economy shuts down, everybody has extra machine time, so nobody is in the market to buy. We then are usually the last to come back, but this time we came back like gangbusters.” For context, Burgert explained that three years ago MAPLAN exceeded its machine building capacity, and the company opened up new factories in China and the Czech Republic. The company modified its machine building gameplan to meet demand, but it has exceeded capacity once again.
The supply chain issues that have affected MAPLAN, however, are logistics costs and the labor shortage. “Every MAPLAN machine is built in Austria,” said Burgert, “and everything goes by boat. We had two machines coming in for a customer of ours and, because lead times have had to be extended repeatedly, this company actually chose to air freight the machines to meet their project’s start date.” How much did it cost to send two 45,000-pound machines by air freight? “It cost the price of a third machine!” said Burgert. MAPLAN’s challenge for hiring traveling service personnel, already difficult during the long-standing workforce shortage, now is compounded by the pandemic. “It is very difficult just to find somebody who wants to work in this field; finding the person who wants to travel today is even more difficult,” said Burgert. Prospective employees especially are reluctant to sign on with COVID-19 still raging. “A service person who travels puts himself in harm’s way by jumping on an airplane every week,” said Burgert.
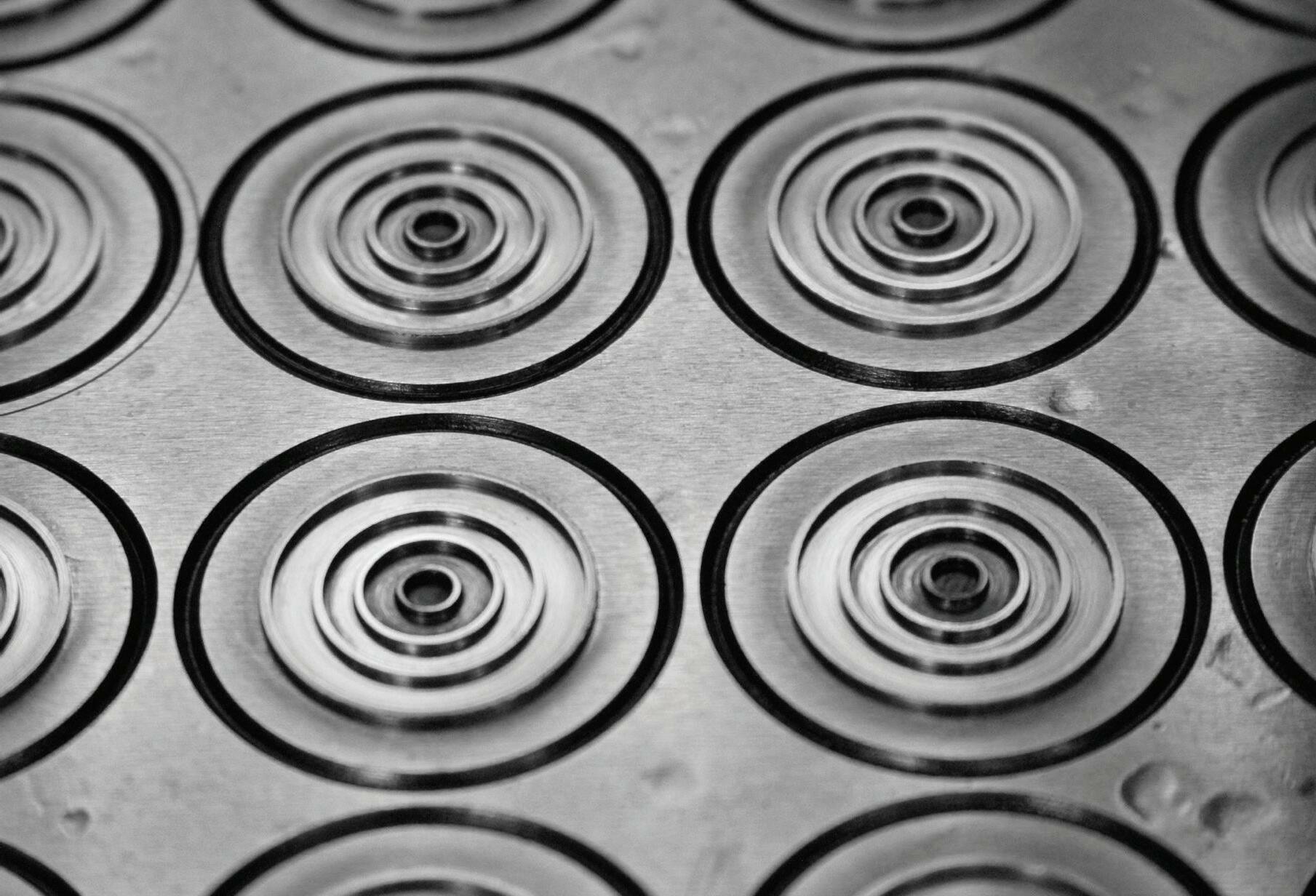
From what Burgert has heard, rubber processors are having problems getting enough compound. “Some of the small and mid-sized shops don’t even know if they can get compound in the future,” he said. “I have heard stories of some shops being told ‘no, we are allocated out and you will not have compound for the next few months’. People seriously are scrambling to rectify that situation.” Dave Jentzsch said that the rubber lining industry has not experienced this type of widespread compound shortage. “Because most processors in this sector of the industry had enough in stock,” said Jentzsch, “they have been able to manage that situation pretty well. Most of these processors try to anticipate four months with the possibility of an uptick of 15% or 20%.” He did note that the extreme weather in Texas, which caused petrochemical plants to shut down, translated into some shortages. “Those processors that produce roofing material using PVC (from Texas) experienced some serious shortages,” he added.
The rubber lining industry’s main headaches revolve, however, around logistics and the labor shortage. “The problem isn’t too much about getting material,” said Jentzsch. “The issue is trying to get the orders to the customers.” Many processors ship rubber linings for storage and transport vessels to customers worldwide. “It really is a struggle to get it out there,” he said. “Some companies are sending via air freight because it can get there a little quicker; sometimes it is easier to get it on a plane than it is to get it on a ship.”
page 10 u
LET US DO THE DIRTY WORK SO YOU CAN QUICKLY MOVE FORWARD.
Performance release agents and mold protectors for rubber molding.
Let us help you stay lean and clean.
CHEMTREND.COM
t page 17
Some processors have reported having outgoing shipments that have been sitting in the port for months. “Los Angeles is all tied up,” he said, “and even Savannah is tied up. A lot of things now have gone out through the East Coast. It just ties up everything, plus you can’t get shipping containers.” Jentzsch also cited difficulty with domestic trucking, especially LTL (less than truckload) shipping.
“The biggest problem, though, is labor,” Jentzsch explained. “If these companies had the labor that they need to run production, then maybe they would have a shortage of materials. Some that usually have a two-week turnaround saw this jump – up to seven and eight weeks – but now it is back to about five weeks.” Jentzsch described the situation as a complicated push-me pull-you situation, or a sort of spring effect in which a strain here translates into a problem there, and a problem there triggers a headache over yonder. “The processors are not having troubles with materials, but they can’t get anything shipped because they just don’t have the labor to fulfill the orders,” he said.
“They just can’t get people back to work,” said Jentzsch, although he admitted that the real issue could be that the baby boomers retired. “Many are down 25% of their labor force,”
advantage
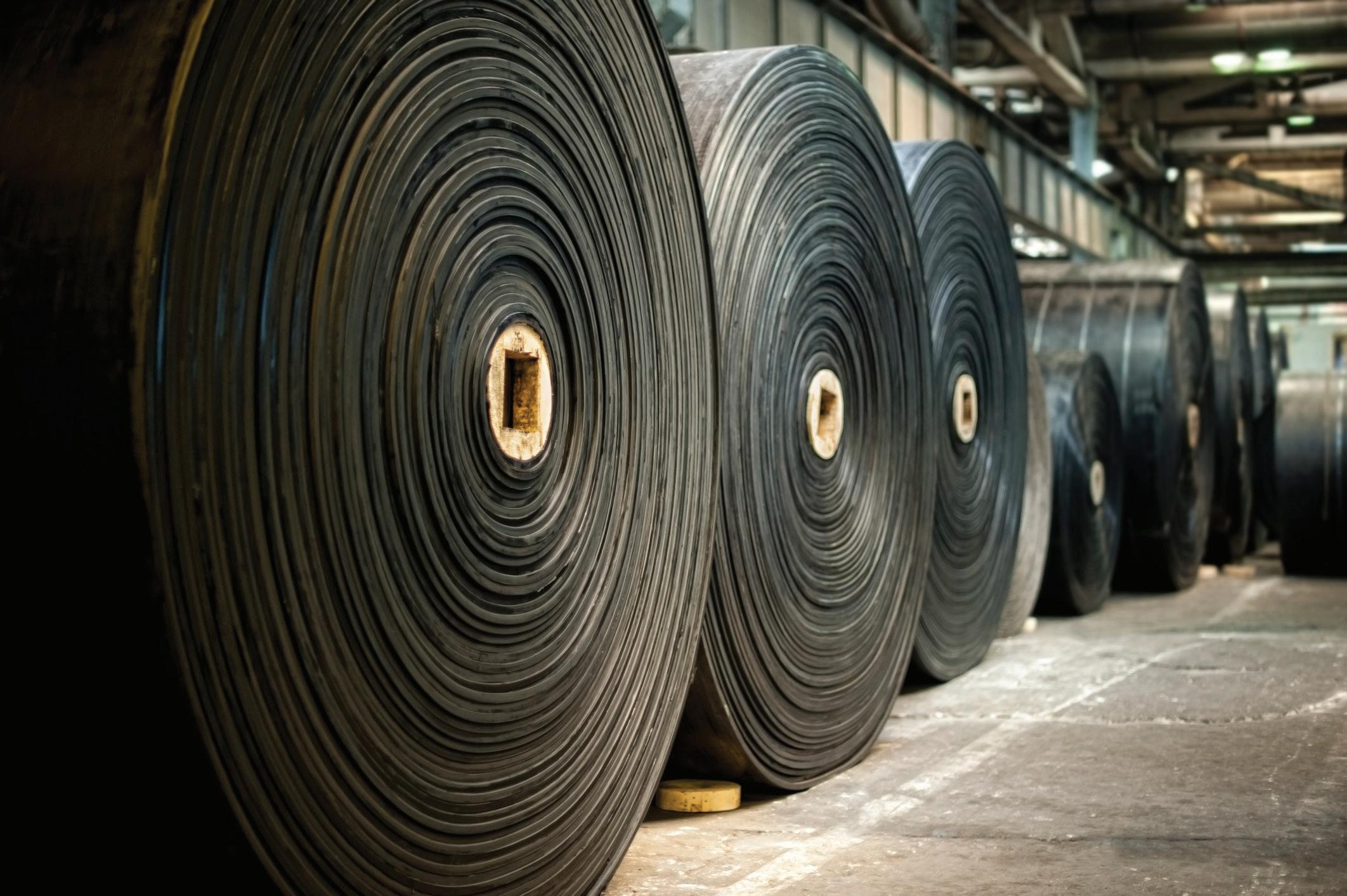
Practice Advice for the Rubber Industry
Ice Miller focuses on meeting the needs of our clients quickly, efficiently and cost-effectively. Ice Miller attorneys with rubber industry experience can assist with your greatest legal challenges. Contact Josef Keglewitsch at 614-462-2279 or josef.keglewitsch@icemiller.com for more information.
300+ lawyers in Columbus and other offices
he said. “If they had all of those employees back, there would be no trouble filling orders.” Some companies have had to cut, for example, from five lines down to only two lines.
Advice from the Trenches
Inside Rubber asked the contributors for advice for rubber processors dealing with the supply chain disruptions and the unpredictable nature of business these days. Jentzsch’s advice centered on materials stock – have plenty on hand and identify usable alternatives, make good choices about production lines and have good relationships with suppliers.
“It is necessary to carry some inventory,” Jentzsch said. “I suggest trying to carry four months’ worth or even probably 20% more. Some processors think that a month is enough, but I would go for more so that a processor has room to surge or taper off.” He also pointed to the wise practice of having alternative ingredient options. “Along with multiple approved ingredients,” said Jentzsch, “make sure to have more than one active supplier.” Jentzsch warned against having multiple approved suppliers but buying from only one of them. If a processor has two approved suppliers but only buys from one, due to cost or some other issue, the “backup” supplier may not be willing to do business in a pinch.
It may or may not be feasible to line up approved alternate compounds, depending upon the formulations used and the performance characteristics required of the rubber. “It is good to have more than one supplier for alternate compounds, or to have more than one grade of rubber compound that can be used because they all will behave the same in the chemical resistance arena,” said Jentzsch. “But that is a tricky situation. For some things, alternatives can be used; for other things, they can’t. Some companies, after running into shortages of crucial chemicals, now stockpile plenty of it so they don’t face another shortage.”
“The other thing,” said Jentzsch, “is to reduce product lines; go with the most profitable lines.” He advised that if processors cannot meet the demands of all customers during this period of relentless disruption, it is important to identify the most profitable customers – the most profitable lines – and make reductions elsewhere. “You can’t be everything to everybody when things are too tight,” Jentzsch said. He also pointed out the value of close, friendly and collaborative relationships with suppliers. “You are staying close to them because it is harder to say no to a friend,” he said. “You want to keep that relationship strong so that if they can get a scarce but needed item for you, they’ll work extra hard to try to get it.”
Burgert advised rubber processors to keep a close eye on the mixtures being sent out by compounders that are facing raw material shortages. “Lately, unfortunately, my customers
WE’RE ON YOUR TEAM.
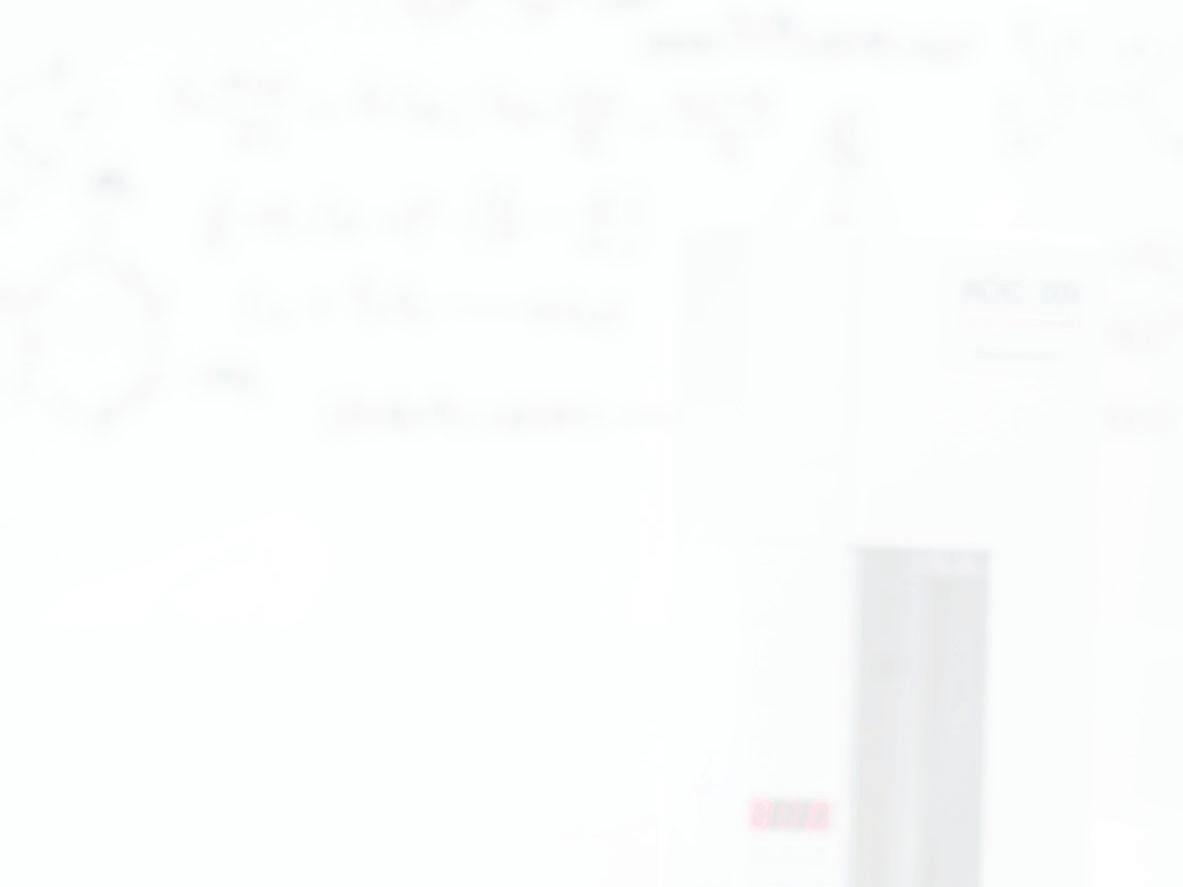
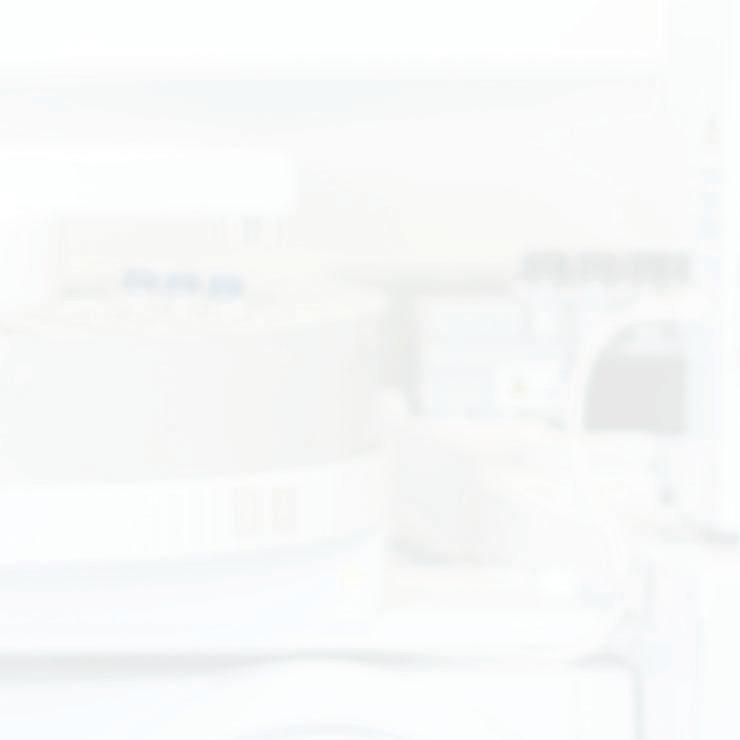
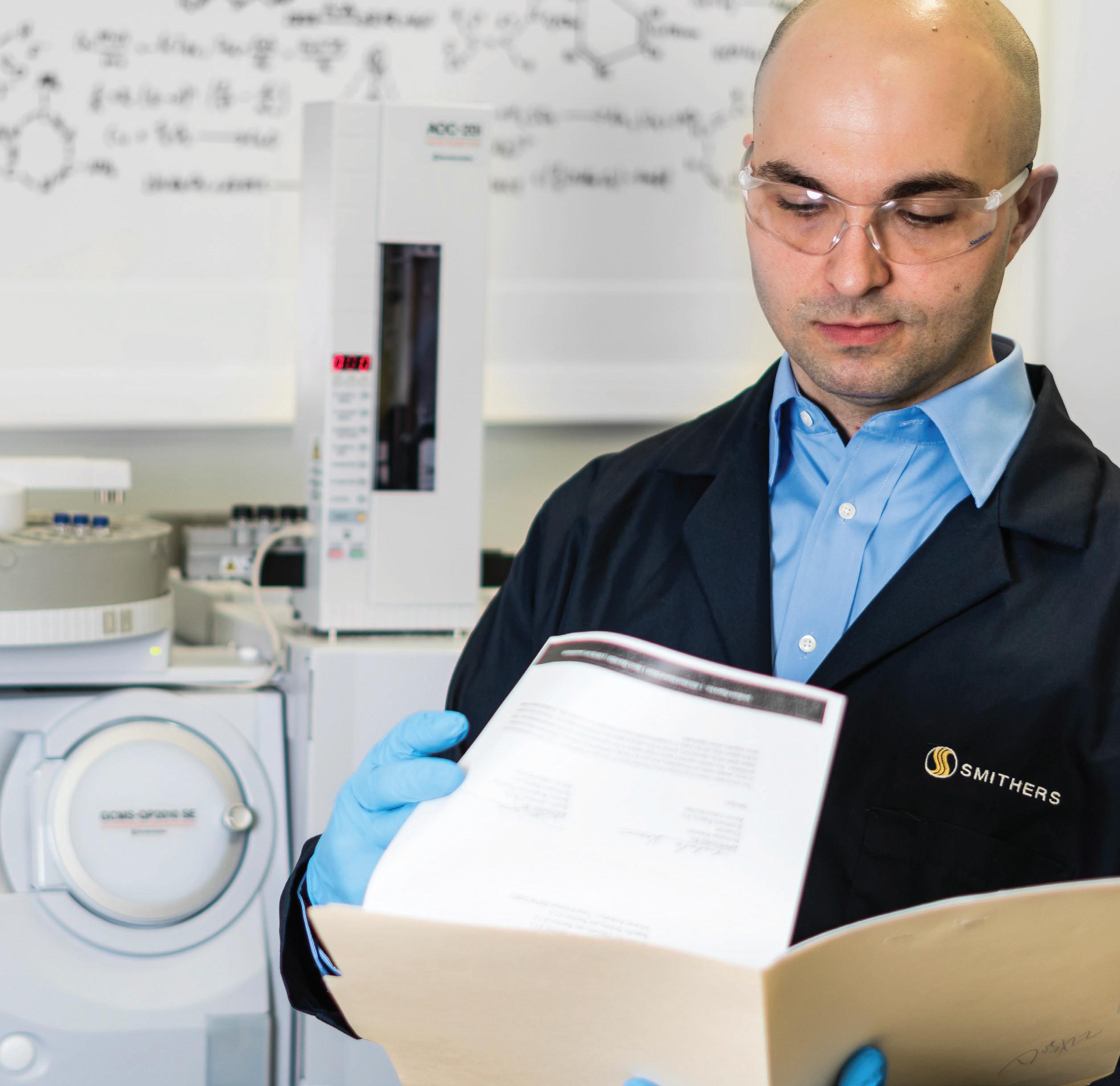
Chart 1. Impact of Raw Materials on Production
MATERIAL CHEMISTRY | PHYSICAL PROPERTIES | PRODUCT TESTING | TECHNICAL CONSULTING
You can always count on our team to conduct your testing programs with care and precision so you can keep your new product development moving forward in a rapidly evolving environment. Our experts have support you. Contact us today to discuss your testing needs.
t page 18
have seen massive variations batch to batch,” said Burgert. “It seems that one day the compounders have this available and one day they have that available. They are mixing as they can, with the materials they can get.”
To address the compound shortages, Burgert urges processors to move toward more waste-free molding. “Processors that are using hot pots or hot runner molds should be looking at going into cold pack technology,” he said “as well as looking at other options where there is no runner or where the runner is reduced by maybe 90%. Try to get as much out of a batch of rubber as is possible.” As processors consider changes to equipment, Burgert notes that MAPLAN offers fully automated equipment cells, which can be extra attractive in light of the workforce shortage. “What we are doing now is creating fully automated cells to take the operator 100% out of the equation,” Burgert said. “We have our own automation department so we can design everything in-house with robots in mind. MAPLAN has expanded into programming, developing the cells, and accommodating the processes that happen downstream from the cell.”
Callitsis had several suggestions to help rubber processors weather the supply chain disruption storms. “Buy safety stock whenever possible, order well in advance and work with suppliers to develop alternative materials,” said Callitsis. “Keep close communication with suppliers on foreseeable shortages or delays, and also keep close communication with customers on their forecasts, and factor in the new required lead times.”
Callitsis stressed the value of strong relationships with suppliers, noting that the price of goods is not the only aspect to consider. “Price always is important,” he said, “but the quality (reliability, customer service, sales support, technical support, communication) of a supply base is just as important, if not more important, than price.” For lining up alternative ingredients and compounds, Callitsis offered this perspective: “Having options always is safer than a single supply source or material. It helps to have a good internal technical staff, and to have capable, reputable suppliers that offer good technical support. Aside from matching the performance, it is important to select viable alternatives from a long-term availability standpoint, too.”
An Eye on the Future
When asked about a prediction for the next year on the availability of rubber polymers and ingredients, the response from Callitsis was succinct: “Very tight with little relief forecasted this quarter or next, and too many pandemic and economic uncertainties to predict beyond that.”
The forecast from Jentzsch for the supply chain to get straightened out in the near term similarly was cautious. “Initially, everybody thought it would happen by the third or fourth quarter of 2021, but it didn’t,” he said. “We are hoping by sometime in the first quarter of ’22 things will start to balance out.” His prediction on improvements in logistics was not optimistic. “The ports hopefully can get a little less congested, but there also is a problem with the shipping containers,” said Jentzsch. “And maybe trucks will be more available or maybe they won’t because truckers can’t find chassis.” Logistics also remain hobbled by the labor shortage. Jentzsch noted that the ranks of baby boomer long-haul truckers have been slashed by retirements, and retirees are hesitant to return to a such a punishing job.
Jentzsch expects ongoing price increases for materials. “At the end of 2021,” he said, “we had not seen prices increase much but from what the industry says, it looks like rubber additives could go up 25% in 2022. Inflation really is going to hit hard in 2022. We haven’t seen much of that; some things went up, but then they came back down. But processors are getting ready for that. They already have told their customers. Discounts that used to be offered probably aren’t going to happen.”
He continued, “Everybody is sitting on their hands, waiting and wondering what the future holds. Projects are on the books and demand is high, but it is just really hard to meet it right now. Prices go up and then back down. Finally, prices settle for a little bit and then we wait for the next market upset.”
Williams offered this forecast about the pandemic and its impact on business. “COVID’s Omicron variant was a surprise to all,” he said, “but as we learn more about its communicability and behavior, we feel this is a new normal and that all of us will be forced to adjust permanently to this normal.” Williams felt that eventually the disruption caused by the pandemic will run its course and businesses will either adapt or get left behind. “2022 will be more of the same,” he said, “and hopefully, by year’s end, we will emerge with a general acceptance of living with COVID-19 and just mitigating the personal risks.”
For Burgert, who was headed overseas to MAPLAN’s Austrian factory during the potentially brief window after the country cancelled its pandemic lockdown and before the next COVID-19 lockdown might be declared, the future for logistics and the workforce looked quite unknowable. “What happens next is entirely up in the air,” he said. “Everybody is scrambling.” u