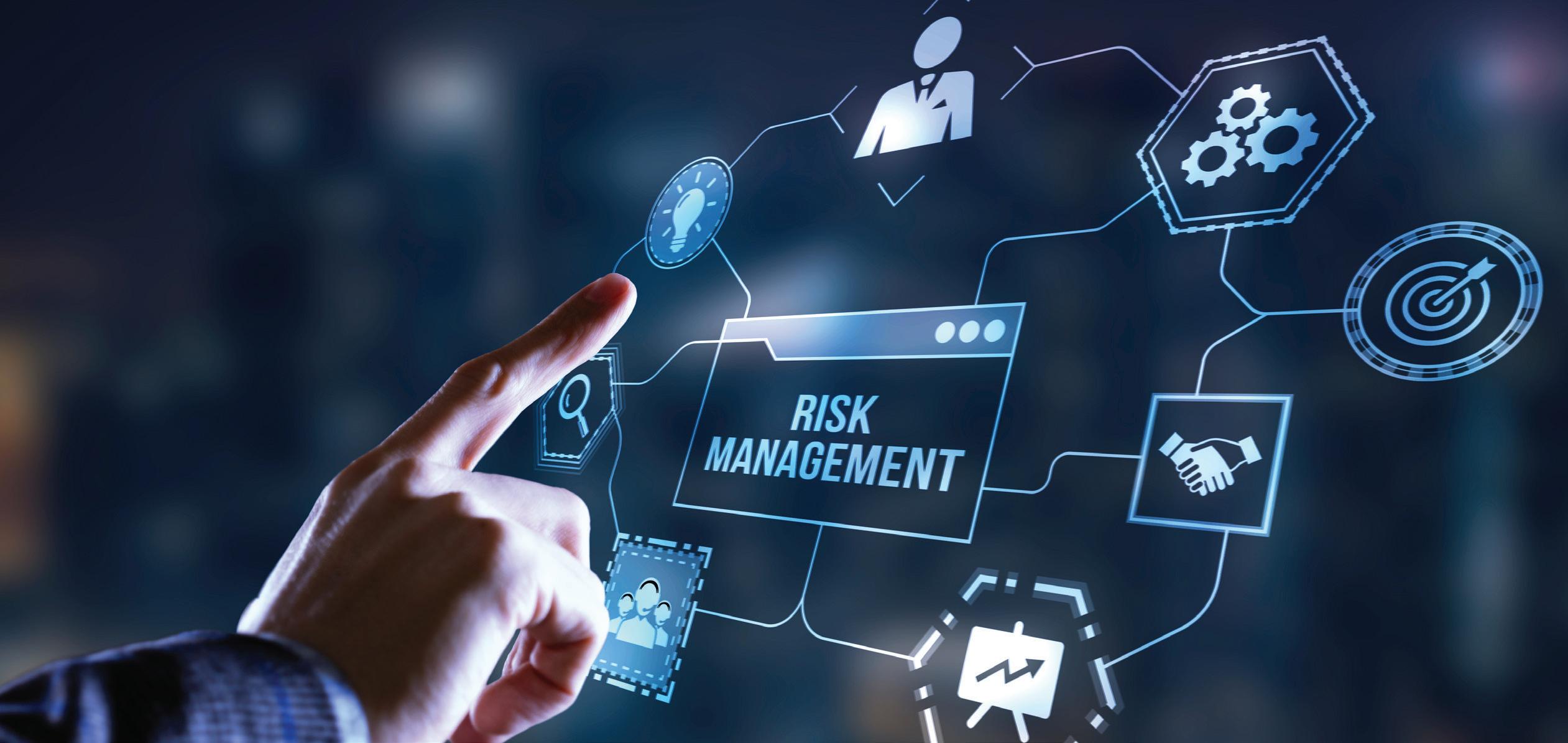
8 minute read
Safety
Risk Management in Process Development
By Perry Parendo, founder, Perry’s Solutions, LLC
The product development process is challenging to execute. There are technical, manufacturing and business considerations to balance. Any issue can cause a significant delay in project completion and the ultimate product launch. Production issues can damage company image and negatively impact financial success. How can companies avoid these delays? How can they anticipate things that they are not expecting? Risk management provides an opportunity for launch predictability. How does this happen?
Development process
First, companies need to consider the development process. Organizations will emphasize different aspects of the process, but the core elements tend to be common for many. A general flow of these core development elements are as follows: y Project Planning y Requirements y Concept Design y Product Development y Manufacturing Development y Validation y Clinical Evaluations (in the medical device industry) y Product Launch
Many organizations consider risk management as a deliverable at project completion, just before launch, vs. a tool to improve project execution. However, to truly help their project, risk management should be implemented early in the process. But how is that done? This article will give tips for each stage of the product development process. During the Project Planning stage, one should consider areas of uncertainty. Are enough resources allocated? Resources can include people, prototypes and time for training. From a process point of view, companies need to consider things they need to be successful. Make sure to ask the right questions and get those questions resolved. Anything not provided is a level of uncertainty for project predictability.
The next uncertainty to address is Requirements. This stage includes technical requirements but also can include business and operational requirements. Examples include product cost, production cycle time and expected yields. As the processing needs are identified, there is a need to assess capabilities. Which requirements are difficult to achieve? Challenging requirements provide uncertainty and risk and a need for a plan and resources to resolve them.
At the Concept Design phase, a functional assessment of the product performance as well as the manufacturing process can be done. New designs can produce production challenges. This can influence fixturing, equipment or finding a process sweet spot. A high-level review of the project can really benefit the later stages of the development process.
During the Product Development stage, the design team will create a detailed assessment of the product situation. The team also should dig deeper into the initial concept level testing and analysis. Design of Experiments (DOE) can be a big help by evaluating multiple input variables and finding optimum performance. Companies want to avoid focusing on the first solution that shows promise. Instead, they need
to understand all options and determine which one is most likely to be stable and repeatable for customers.
Similarly, the Manufacturing Development phase needs to go to the next level of detail. Companies look at their processes in more depth in critical risk areas. Potential issues often are exposed during prototype builds. The more parts produced, the more issues that can be uncovered and resolved. However, budget and schedule constraints mean companies need to learn the most from the test units that are available. Training in new techniques also can happen at this stage to prepare for the expected future production volumes.
After design is complete for the product and process, Validation needs to be done. Validation is a way to confirm all prior development work is accurate and agrees with the final design configuration and manufacturing process. Up to this time, much of the work has been characterized at a low level. These component level bench tests are informational, but it is important to confirm performance after things are integrated together.
In the medical device world, Clinical Evaluations are an important time for feedback. One can learn about new issues and the frequency of occurrence. In other industries, this may be through a beta test with select clients. This can influence the completion of the current project design or provide insights for a next generation of the product.
Finally, during Product Launch, companies gain more information at a faster rate, and they obtain further feedback about production issues and field experiences. Because of this, making risk information into living documents provides a way of capturing this ongoing information. This can be used for continuous improvement, training or for future product enhancements.
Many opportunities exist to influence project execution with risk management to deal with the uncertainties.
During project execution
Typically, project plans include adequate resources for highrisk items. What do companies do with the moderate risk items? Companies cannot afford to provide resources for all of these uncertainties. Many moderate risks will go away with an existing, limited characterization plan. But what about the ones that do not go away? Often, a few high risks will
page 8 u
RUBBER IN MOTION
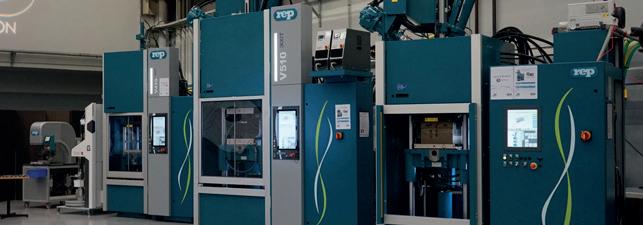
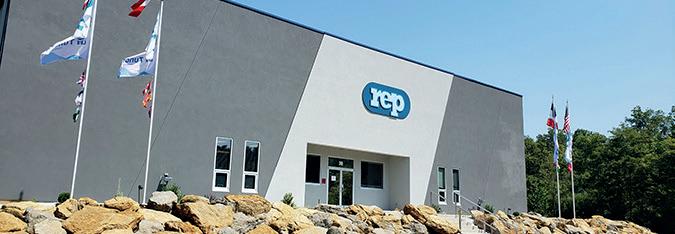
Proud Sponsor of
t page 7
improve faster than expected. When this happens, resources can be transferred to these new areas. As an example, a parallel path technology development can be cancelled, freeing up resources for other purposes. This implies the need to begin a risk management process early, which would need to be reviewed periodically. This can capture new learning and ensure prior items reflect the current maturity level. This does not need to take a lot of time, and it is a good sanity check as the project moves forward.
Failure Mode and Effects Analysis (FMEA) often is performed at the component level for a Design. How can one do this if a company does not know its components yet? There is an option to perform a concept level FMEA using functions instead of components. They can take a similar approach with the processes. For example, maybe it is a joining function, but it has not yet been determined if it is screwed or glued. The joining options create different risks to help decide on the eventual solution.
Failure Modes and Effects Analysis (FMEA)
A common method to conduct risk analysis in several industries is FMEA. While risk management can and should go beyond this single tool, but discussions in this article are limited to FMEA. For design risks, one might perform a Design FMEA. This assumes the components are “perfect” and that the process is fully capable. The focus is on the ability to design a product (mechanical, electrical and software) and to meet the requirements. The other areas assumed to be free of errors are evaluated in other documents or methods. It is common for people to find risks in other areas of the project outside of themselves, thus the important value of cross functional teams when populating these risk tools.
For the manufacturing risks, a Process FMEA is performed. While the format appears similar, this process version makes different assumptions. First, the design is appropriate and complete with respect to the requirements. Second, companies only look at the specific process being studied. It’s assumed that upstream processes are successful, which includes incoming components. Again, the other error-free areas are evaluated in other documents or methods. Focus is on taking credit for work done to improve the work done and to look for potential areas of improvement.
Companies can drill down as far as needed to become comfortable with the uncertainty. But how do they know where to drill down? And how far do they drill down? Teams should do this in the areas of highest risk. They should explore issues deeper in high-risk areas. This implies that they should schedule with more detail for high-risk items as well. Low-risk areas do not require the same amount of attention.
Business risks/ business impacts
If companies evaluate all business risks, they improve the opportunity for profitability. For example, they can look at their development process, development system and management methods. These impact the ability to execute the project but often are not considered with project risks. Eliminating blind spots can allow people to perform better and avoid big surprises.
Further, companies need to recognize that the technical risks for the product design impact its development cost, product cost and project schedule. These are additional business considerations. While the work required to translate technical risks to detailed business risks is not always done, the thinking process can help to make solid decisions throughout the project. Done early, a company can increase its chances for meeting its cost and schedule performance expectations.
Process validation strategy
Determining an appropriate validation strategy is an important step for predictable project completion. Organizations tend to have a validation approach that is applied to all areas. Should companies apply a similar framework to all areas? Based on the previous discussion, the answer should be no. The level of testing should vary depending on the level of risk involved. Knowing the risk level from early on in the project allows companies to evolve the validation strategy as they go through the development process. Allowing flexibility in the validation approach can speed the end of a project, and increase confidence for product launch. For example, at what level should testing be performed? Do extreme settings need to be included, or is a nominal value adequate? Do companies need a large quantity of tests, or do they have relevant prior testing that helps increase our performance confidence? These are all questions to properly address project uncertainty.
Conclusion
When risk management is used for competitive advantage, it can impact many areas of an organization. Companies can create better plans and improve how they execute them. They can be more predictable. They can have a confident and firm validation strategy. By helping in each key phase of the development process, companies can smooth their project performance. Team motivation will be higher, and financial success will be stronger. Start now and gain the most benefit for the company and for the product development team. u
Perry Parendo is the founder and president of Perry’s Solutions, LLC, a consultancy focused on speed and predictability in new product development, specializing in Design of Experiments methods. Parendo can be reached by calling 651.230.3861 or via www.perryssolutions.com.