
5 minute read
Q&A
Reducing Production Downtime with Auxiliary Equipment
By Ian Turner, vice president of sales and service, Barwell
Production efficiency always has been important to the manufacturing sector, but with rising energy and raw material costs, combined with worldwide inflation and the effects of the coronavirus pandemic, it probably is more important than it has ever been. As Barwell visits rubber factories all over the world, we are receiving increasing commonality in the issues that have a negative impact on production efficiency and downtime. Here are five of the most commonly raised issues.
We are looking to filter our compound, but this will mean increased downtime and inefficiency due to constant replacing of filters. What are the best options to reduce the downtime and costs of the filters?
A rear-loading preformer machine option is available, which means operators will not disturb the filtering setup or damage the filters when loading the machine. The filters do not need replacing, as they would with a front-loading machine (with a frontloading machine, the filters tear away from the filtering accessories on opening of the head and need replacing, adding significant time to the loading process).
We’d also suggest using a high-pressure machine to help push the compound through the mesh filters that filter the compound. This can provide an increase of up to five times the amount of rubber filtered per minute as the high pressure helps to push the compound through the tiny aperture on the gauze plate and mesh filters.
We are trying to streamline production efficiency throughout our business, but find it difficult to identify areas in which we can improve. How can we ensure our machine and operators are working to maximize efficiency?
The best way to make key decisions is through data analysis; Automation, data collection and instant analysis ensure that the monitoring of machine performance improves production quality and efficiency, as well as enabling predictive maintenance and instant troubleshooting to take place.
Many companies are trying to establish smart factories, and systems are available to help transform rubber processors’ operations by using a safe Internet Gateway and advanced technology, allowing machines, devices, sensors and people to connect and communicate with each other. Process engineers are provided with vital information and data from all points in the manufacturing process to aid decisionmaking and identify key areas that require development. The systems also can provide operators with alarms, production history, error logging, live tracking, service reminders, daily checks and document storage to make daily tasks simple and trouble-free.
Another major benefit to these systems is the ability to allow direct remote access to the machine’s control panel for solving urgent problems from anywhere in the world. Some systems also have the functionality to connect via an IP camera to view the machine remotely, providing instant support to help machine owners. This will help reduce downtime considerably and reduce the need for a service engineer visit.
We waste a lot of time changing the tools on our machine. How can we reduce changeover time?
A front die change solution is available, which is much quicker as the holder ring is unscrewed from the front. This means operators quickly can swap the die out for a different one without disturbing the accessories behind the head, and this has the added benefit of not having to remove any rubber compound, which can be a timely process.
I am concerned about the amount of waste compound during our rubber preform production. How can we reduce waste at the start of a production run?
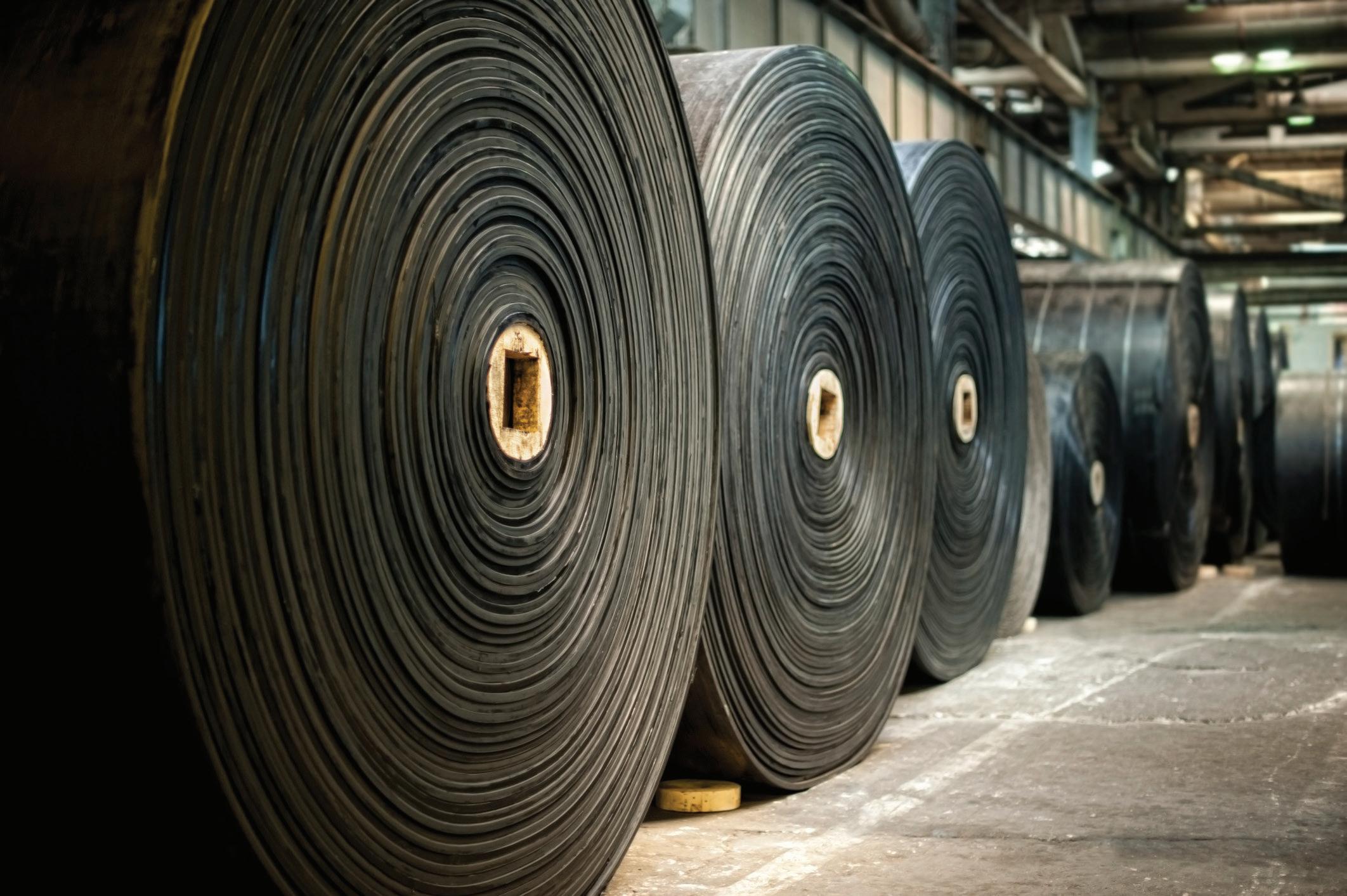
Many of today’s preform machines are highly accurate machines, designed for minimal wastage and consistency during production runs. This firm’s preformers include a scales feedback system for automatic weight adjustment to ensure rubber blank control, which helps to maintain accuracy of up to +/- 1% by volume for many applications. It is possible to access a quick product setup using a product database to save time when programming the machine.
For existing owners of this firm’s equipment, an extended funnel can be used when production solid sections of up to 90mm to further reduce compound wastage, which will reduce leftover compound found within the head accessories after each batch cycle, as the channel within the funnel has been narrowed.
We currently are hand-trimming rubber parts of flash and would like to move to cryogenic deflashing, but we know the costs are high with this process. Is it cost effective for us to switch?
To lower the costs associated with cryogenic rubber deflashing machines, it is important to reduce the level of liquid nitrogen consumption. This firm’s highly engineered chamber construction means that there is no wasted space, which reduces consumption. The inclusion of a 99.99% dryair system to transport the media prevents any unnecessary damage to the polycarbonate media and reduces any downtime, and removes any impurities found within the shop air, when compared to a screw augar. The main disadvantage with a screw augar is that it degrades the polycarbonate media quickly and is a labor-intensive process to clean. A dry-air system also means that gaseous nitrogen is not required, which is another cost savings. u

Barwell’s aim always has been to improve production efficiency and reduce downtime to help maximize an organization’s profitability and production quality, as well as ensure effective and efficient supply and service through the supply chain. Barwell has new machine solutions for customers who do not currently own a Barwell, machine improvements for current Barwell owners or additional machines for Barwell owners to add to their rubber complete processing cycle. Barwell manufactures rubber-processing machines, including batch-fed ram preformers, continuous gear pump preformers, rubber deflashing machines, spacesaving spiral cooling conveyors, strip cutting machines, industrial drying microwave ovens and tire re-treading machines. For more information, visit www.barwellusa.com.
advantage
Practice Advice for the Rubber Industry
Ice Miller focuses on meeting the needs of our clients quickly, efficiently and cost-effectively. Ice Miller attorneys with rubber industry experience can assist with your greatest legal challenges. Contact Josef Keglewitsch at 614-462-2279 or josef.keglewitsch@icemiller.com for more information.
300+ lawyers in Columbus and other offices
icemiller.com

Free ARPM Member Benefit
Save on small package and freight shipping with the ARPM Shipping Program and PartnerShip®
PartnerShip.com/ARPM
Enter 8333 in the promo code field