
8 minute read
BENCHMARKING
AMBA HONES COMPETITIVE EDGE FOR US MOLD BUILDERS WITH SHOP RATE DATA
by Rachael Pfenninger, director of strategic execution, AMBA
At the end of 2021, the American Mold Builders Association (AMBA) surveyed US mold manufacturers on compensation data across 51 unique job positions. At that time, the AMBA benchmarking team discovered that, despite experiencing the highest inflation rate since 1982 (7%), mold manufacturers were continuing to raise wages as they battled a worsening labor shortage. In 2022, mold manufacturers experienced little relief; as of August 2022, the United States faces an inflation rate of 8.5%, after surviving a spike to 9% the previous month.
With this perspective, it is more imperative than ever for domestic mold manufacturers to understand how they can most efficiently compete in the marketplace. For this reason, the AMBA once again surveyed US mold builders on charge rates across over 20 moldmaking, engineering and specialty services. To provide more in-depth data, the AMBA team relied heavily on insights from mold manufacturing executives and was able to provide a deeper analysis of overhead, gross margin, mold build details and both attended and unattended rates (as applicable).
The final report includes survey responses from 70 US mold manufacturers from 21 states, primarily located in the Midwest region. The industries served most frequently by this year’s respondents include the automotive, consumer products and medical/optical/dental industries. For the first time, respondents indicated not just which markets they primarily served, but what percentage of work that industry accounted for over the last 12 months. Of the respondents represented in this data set, only seven indicated that a single industry represented 80% or more of their total revenue; no company indicated that a single industry accounted for 100% of its total revenue (See chart 1).
Overwhelmingly, respondents – 86% – identified new mold/die builds as their primary revenue generator. To expound on revenue sources, this year’s survey also asked respondents to identify their second-largest revenue source (only identifiable if it generated 20% or more of total annual revenue over the last 12 months). Of the provided options, mold/die repairs and engineering changes were identified by 61% of respondents as the second-largest revenue source (another 13% also identified this option as their primary source of revenue).
Respondents also were asked to provide their approximate gross

Chart 2
margin percentage, calculated as ((Revenue – Cost of Goods Sold) / Revenue) * 100. Nearly one-third of respondents indicated that their average gross margin was relatively thin (under 15%) while another 27% of respondents identified their approximate gross margin percentage as regularly between 15-24% (See chart 2). who participated in this survey process. AMBA members who did not participate are able to purchase the report for $349. This report will be unavailable to any non-member (regardless of participation). Eligible parties interested in purchasing the report can visit the AMBA publications page at www.AMBA.org.
On average, mold manufacturers reported a current utilization of 72%; anticipated capacity is expected to rise an average of 1% through the end of the year to 73%. Respondents also provided insight into the approximate percentage of their shop’s overhead costs compared to total annual expenses.
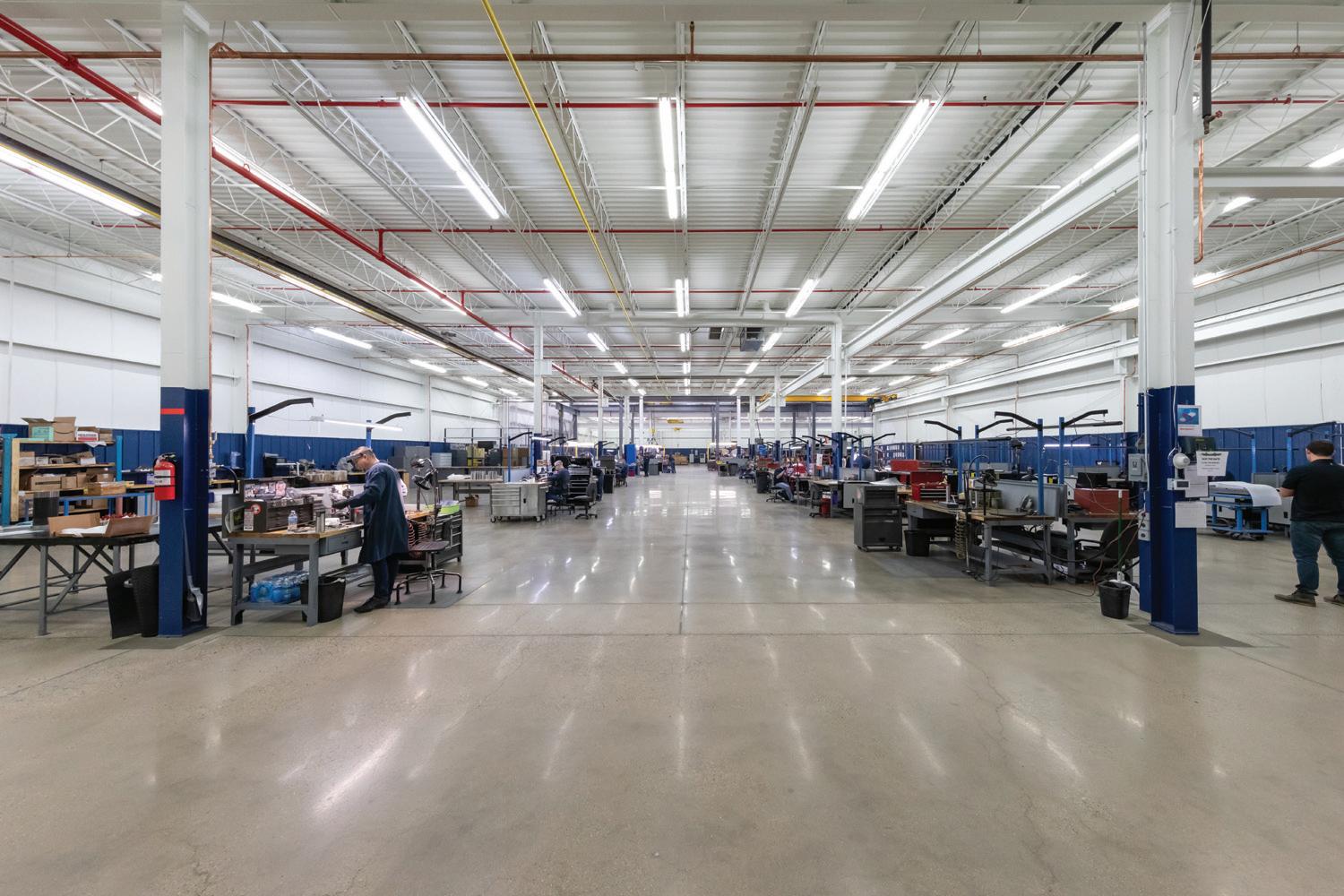
Of the service charge rates studied, no service had only one mode (a single rate that was cited most frequently). For this reason, notable modes – or “peaks” – were identified for every charge rate. To better illustrate this year’s data, all charts were reformatted as scatterplot graphs to better illustrate the frequency and distribution of charge rates for each service area. Additionally, respondents were able to add both attended and unattended rates for the following services: 5-axis machining, 3D printing steel core and cavities for conformal cooling, CNC milling, EDM drilling, gun drill operation, high-speed milling (30k+ RPM), sinker EDM, surface grinding and wire EDM.
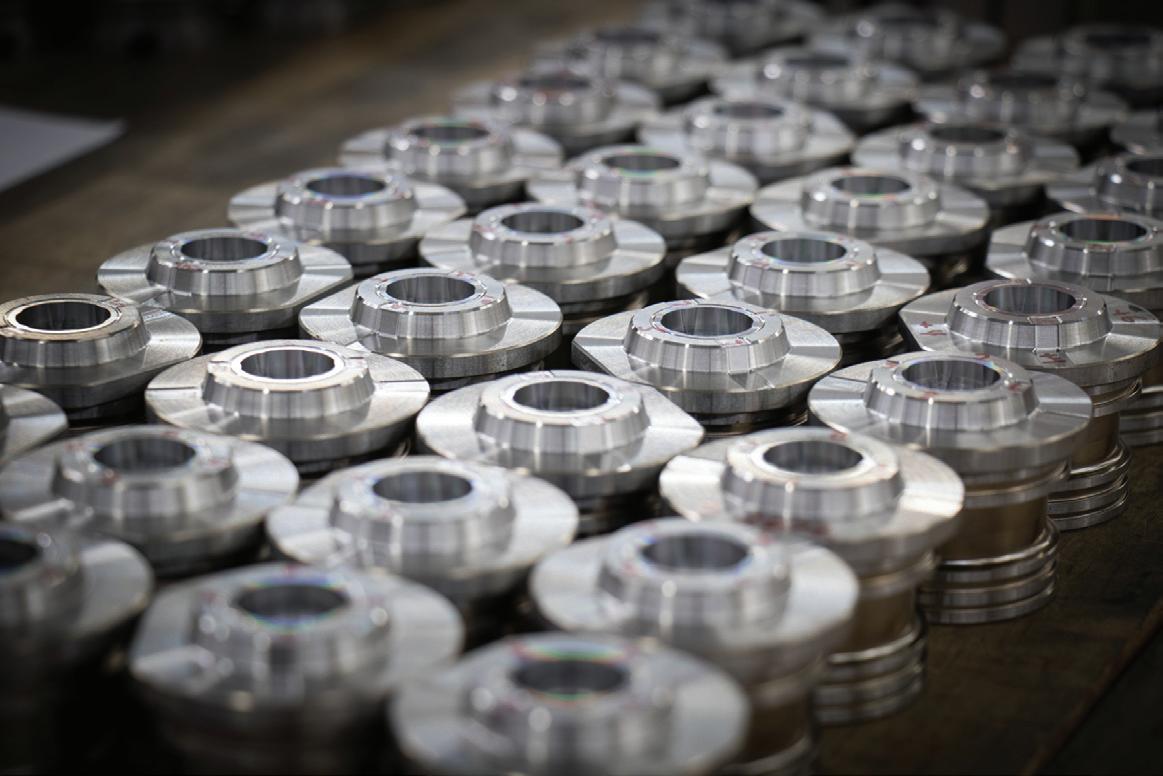
The full 2022 report illustrates additional information on over 20 individual charge rates, as well as further charge rate breakdown by annual sales revenue and/or by the top three primary industries served.
To protect the interests of its members and the competitive advantage of the US mold manufacturing industry, the final report is available at no cost only to AMBA members
Services
• Finishes to all SPE-SPI standards • Diamond Lapping • Textured Surface Prep • Benching • Quoting from Drawings,
Prints, Pictures and Parts • On-Site Support
Capabilities
• 50+ Polishers • 40 ton Capacity • 24 hours – 7 days • Pick-up and Delivery • 3-D CAD File Capabilities
Partnerships
• Welding • Plating • Texturing
Gets you to market faster
ISO 9001-2015 CErTIFIED
1320 Holmes Rd., Elgin, Illinois
Ph: 847-352-5249
Fx: 847-352-4052 sales@ultrapolishing.com
www.ultrapolishing.com

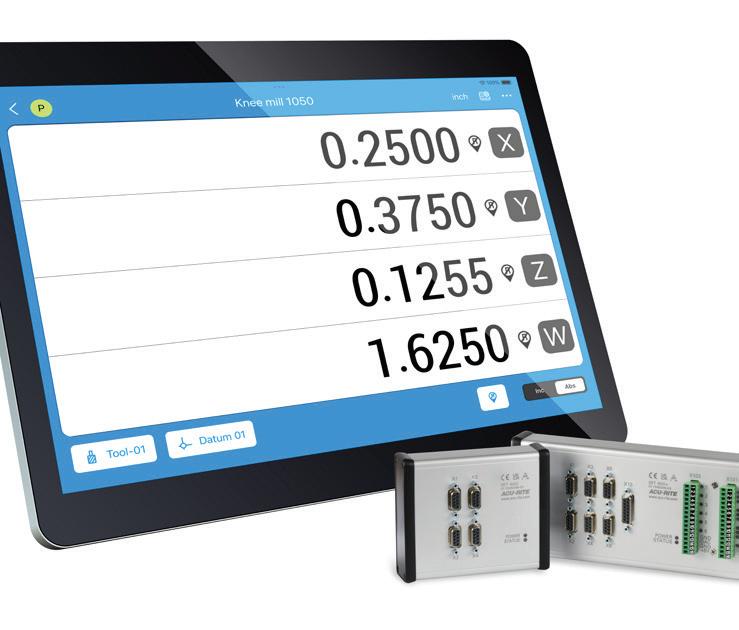
1 2 3
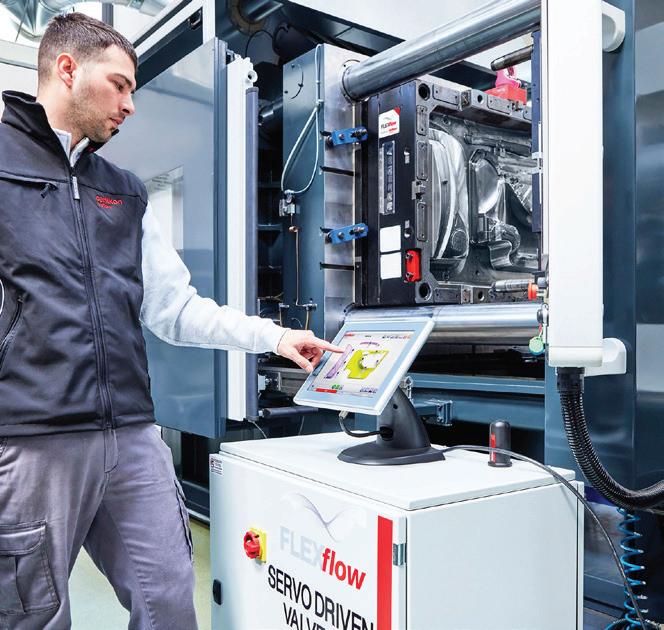
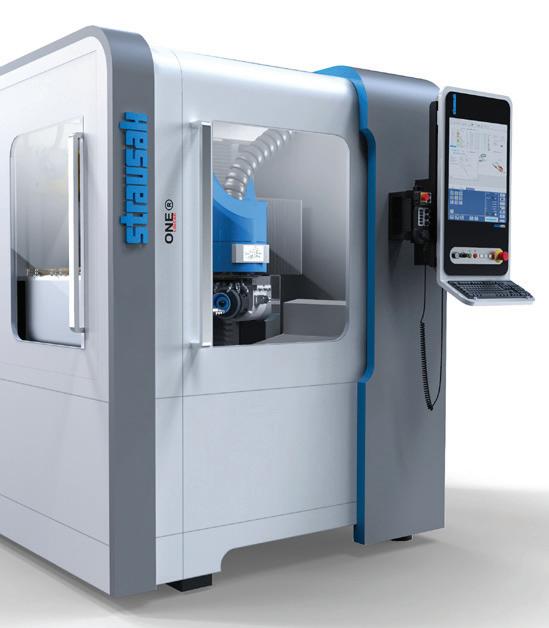
4 5 6 7
[1] BORIDE INTRODUCES WORK FINISHER TOOL BORIDE Engineered Abrasives, Traverse City, Michigan, has introduced a new series of safe and easy-to-use ceramic deburring and deflashing tools. The Work Finisher Tool is ideal for deburring and chamfering non-ferrous metals such as copper, aluminum and brass products and excels on ultra-hard resins like glass-fiber, carbon-fiber and talc-filled plastics, while eliminating the fear of cutting hands, fingers or damaging the molded part in the process. The product is available in three sizes: large, small and micro. For more information, visit www.borideabrasives.com.
[2] CORETECH RELEASES MOLDEX3D CoreTech System Co., Ltd. (Moldex3D), Farmington Hills, Michigan, announced the release of Moldex3D – the latest version of its molding analysis software series. Moldex3D reinforces the system constructure and improves analysis performance, aiming to deliver more accurate molding results for users. For more information, visit www.moldex3d.com. [3] HEIDENHAIN DEBUTS ACU-RITE’S BLUETOOTH DROPWR HEIDENHAIN, Schaumburg, Illinois, presents the new Bluetooth droPWR by ACU-RITE. The droPWR is a firstof-its-kind system to enable an iPad® tablet to become a digital readout (DRO), doing everything an ACU-RITE DRO can except without cables between the tablet and machine tool. Bluetooth technology along with an IBT interface box in the droPWR system allows connection to multiple machine configurations in one tablet including for milling, turning and grinding machines with up to six axes. Designed to be simple and functional, this tablet DRO can be moved and used with various machines. For more information, visit www.heidenhain.us.
[4] OERLIKON HRSFLOW ADVANCES FLEXFLOW HOT RUNNER TECHNOLOGY Oerlikon HRSflow, San Polo di Piave, Italy, has thoroughly revised the software for the control unit of its FLEXflow hot runner systems. The updated Human Machine Interface (HMI) 4.0 now makes operation even more intuitive and convenient. Systems with different nozzle
types can be integrated and several parameter sets can be saved per mold. Extended possibilities have been added to individually control each servo motor for nozzle needle positioning and to monitor process stability. HMI 4.0 now offers the possibility to control multiple servo motors individually and with specific data. This also enables the handling of systems with mixed nozzle dimensions. For this purpose, the system uses specific mold cards for each tool equipped with the FLEXflow hot runner technology. For more information, visit www.hrsflow.com.
[5] PCS COMPANY EXPANDS CONFORMAL COOLED SPRUE BUSHINGS LINE programming for an unlimited range of applications, both for production, custom tooling and resharpening. A 4‐station wheel changer is integrated into the machine and can be upgraded to an 8‐position or 12‐position system. The Staubli Robot can be pre‐installed or retrofitted to the machine for parts handling. As a cost‐conscious solution, this machine can be equipped with a pick‐and‐place loader that accepts the same cassettes as the range of Rollomatic machines. This machine presents a small footprint with a 32 mm (1 1/4") capacity. For more information, visit www.strausakglobal.com.
HASCO OFFERS NEWLY DESIGNED SUPPORT PILLERS
PCS Company, Fraser, Michigan, has expanded its Conformal Cooled Sprue Bushings product line by adding a 3/4" radius for its U and B Series bushings. These products are designed to reduce cycle times for injection molders by creating faster cooling of plastic sprues. Provided as direct retrofits to the common U (3/4" diameter) and B (1" diameter) series sprue bushings, they are available in 8 (Model U) and 12 (Model B) standard sizes. PCS also provides custom-sized bushings for specific applications. These bushings are constructed of stainless steel for corrosion resistance and longevity. Conformal cooled bushings use curved channels to improve cooling of the sprue, which reduces cycle times, increases efficiency and provides better process control. For more information, visit www.pcs-company.com.
[6] ROLLOMATIC LAUNCHES GRINDSMART® 660XW Rollomatic, Mundelein, Illinois, maintains its global leadership position in the field of multi‐axis CNC grinding by spotlighting the new hybrid model GrindSmart® 660XW for combination grinding of tool geometries as well as peel grinding for neck, plunge grinding or other pre‐fluting or post‐fluting operations. The GrindSmart 660XW is a 6‐axis tool and peel grinding machine. It allows the user to utilize cost‐effective and advanced lean manufacturing principles; termed as “Ultra‐Lean Grinding Process.” For more information, visit www.rollomaticusa.com.
[7] STRAUSAK INTRODUCES 5-AXIS MACHINE MODEL ONE Strausak, Mundelein, Illinois, extends its global position in the field of multi‐axis CNC grinding by spotlighting the new model ONE 5‐axis flexible tool and cutter grinding machine. The machine houses the Numroto software platform offering the user high-performance tool design and intuitive HASCO, Fletcher, North Carolina, introduced newly designed support pillars Z571/…., with clearance hole and thread, give designers maximum freedom in mold design when high injection molding pressures have to be absorbed. The pillars are available direct ex works in the steel quality, 1.1730 in diameters ranging from 25 to100 mm and lengths ranging from 36 to 196 mm. For more information, visit www.hasco.com.
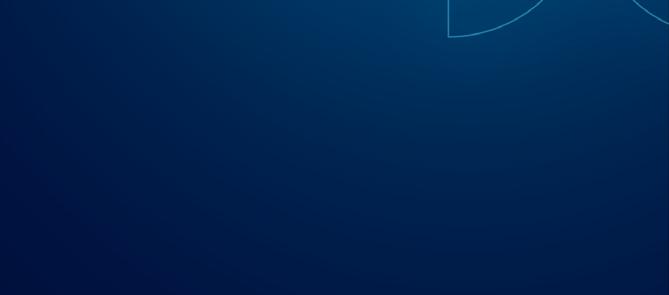
5-AXIS UNIVERSAL MACHINING CENTERS
For the highest accuracy, dynamics & process reliability!
WANT TO KNOW MORE?
CONTACT US AND VISIT OUR WEBSITE! www.grobgroup.com
