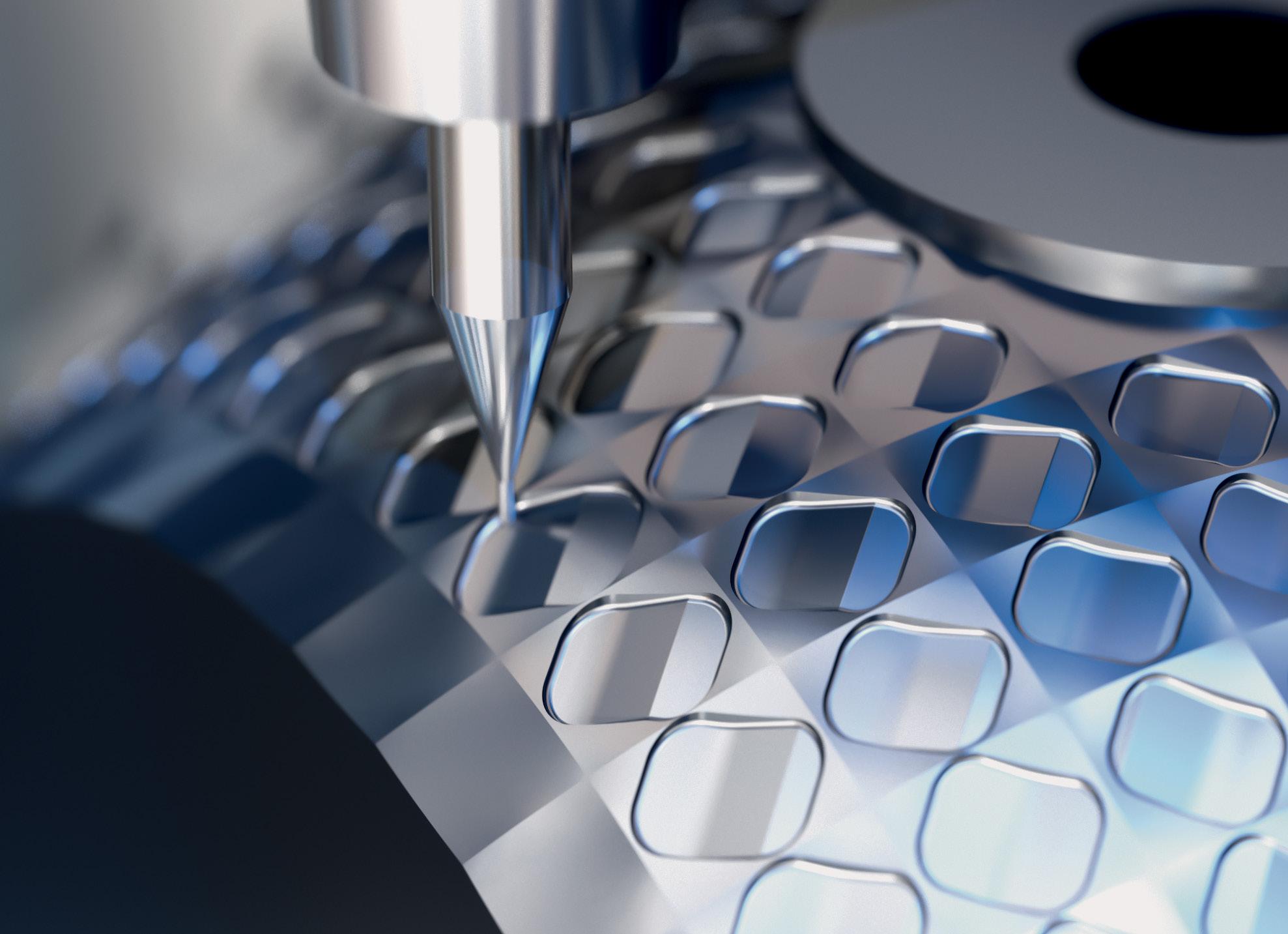
15 minute read
TECHNOLOGY
REDUCING DIMENSIONAL ERRORS IN MOLDMAKING
By Gisbert Ledvon, Director of Business Development, Machine Tool, HEIDENHAIN Corporation
In tool and moldmaking, dimensional and contour errors need to be so low as to be barely measurable and must certainly never be visible. These requirements are increasingly at odds with demands for higher productivity and lower costs. New control options offer possible solutions to the key questions that arise between the conflicting demands of a production process that is highly precise and at the same time highly efficient. The user can take advantage of these functions that bring out the best of a machine in any machining scenario while efficiently meeting workpiece accuracy requirements. HOW CAN I OPTIMALLY TUNE MY MACHINE TO THE GIVEN MACHINING CONDITIONS? Tool builders are finding ways to optimize speeds. As a result, either the cycle is under control or the increased speed causes gouging issues as the machine moves over the 3D surface. When these issues occur, there are basically two options: bring in the machine’s engineering team to fine-tune the machine for the application or – if the machine allows – change the dynamics using embedded cycles to which the operator has access.
Cycle 32 TOLERANCE and the ADP function of the TNC result in perfect molds through the use of a milling machine that has been tuned to the respective machining scenario.
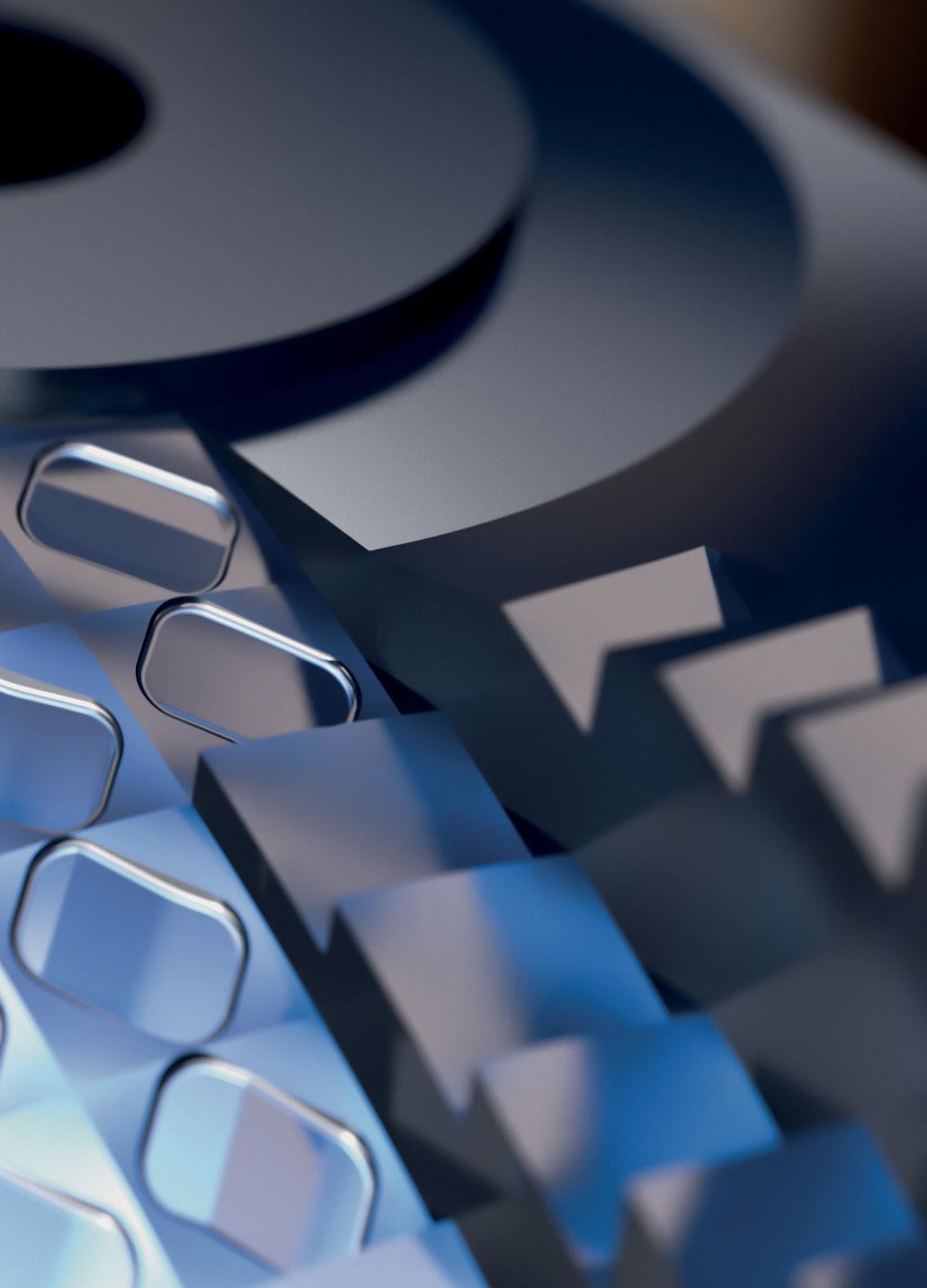
If the machine supplier makes the adjustments, the supplier will send a service or application engineer who will look at the application and measure the behavior of the machine axes. Then the engineer can tune them electronically to optimize the jerk, the speed and the number of axes moving at the same time. This level of control typically is hidden in parameters most operators don’t have access to, which can mean additional downtime and costs while waiting for the service call.
With some systems, the operator can change the dynamics by using embedded cycles to optimize contour accuracy, which individually specifies the path width that is available to the control. The user can directly influence the maximum attainable contouring feed rate and also the machining time, in particular, for contour elements with numerous changes in direction, a common characteristic of freeform surfaces. Optimizing the machining process in this scenario starts with the data quality of the numerical control (NC) program and enables optimized motion control for feed axes in three- and five-axis milling. An insufficient quality of data frequently causes poor motion control, leading to inferior surface quality of the milled workpieces. Some systems can dynamically calculate the contour in advance and adapt the axis speeds in time for contour transitions using accelerationlimited and jerk-smoothing motion control. As a result, clean surfaces can be milled in short machining times, even for contours with highly irregular point distributions in neighboring tool paths. This leads to advantages in the resulting symmetrical feed behavior on forward and reverse paths during bidirectional finish milling and in the form of particularly smooth feed-rate curves on parallel milling paths.
The problem to be solved is a desire for surface quality and consistency, while making sure the machine is running at optimum speeds. If customers have these problems, they should get involved with their machine tool builder or – if their machines have a control system – make sure the operators understand how to optimize the functionality and accuracy.
HOW CAN I TAKE FULL ADVANTAGE OF A MILLING MACHINE’S DYNAMICS? It comes back to what was discussed in the first question: The machine behavior and functionality are critical, which requires a dynamically responding machine tool with high accuracy, linear scales and a closed loop feedback system.
In a typical machine tool for average applications, there is an electronic device that measures the rotation of the ball spool. This measurement relies on the encoder to feed information back to the control – because as the machine is warmed up or runs for a while, the pitch begins to adjust. A closed loop feedback system compares the encoder information with the actual movement, measuring the position of the axes and then evaluating it to the position on the scale. This closed loop feedback ensures accurate positioning of the mechanics. Without that information, operators cannot compensate for any deviations.
With some systems, available controls provide functions to combine high accuracies with dynamic motions. These functions minimize not only forces that affect the mechanics of a machine tool during operation, but also the resulting deviations at the tool center point.

ISO 9001-2015 CErTIFIED
Services
• Finishes to all SPE-SPI standards • Diamond Lapping • Textured Surface Prep • Benching • Quoting from Drawings,
Prints, Pictures and Parts • On-Site Support
Capabilities
• 50+ Polishers • 40 ton Capacity • 24 hours –7 days • Pick-up and Delivery • 3-D CAD File Capabilities
Partnerships
• Welding • Plating • Texturing
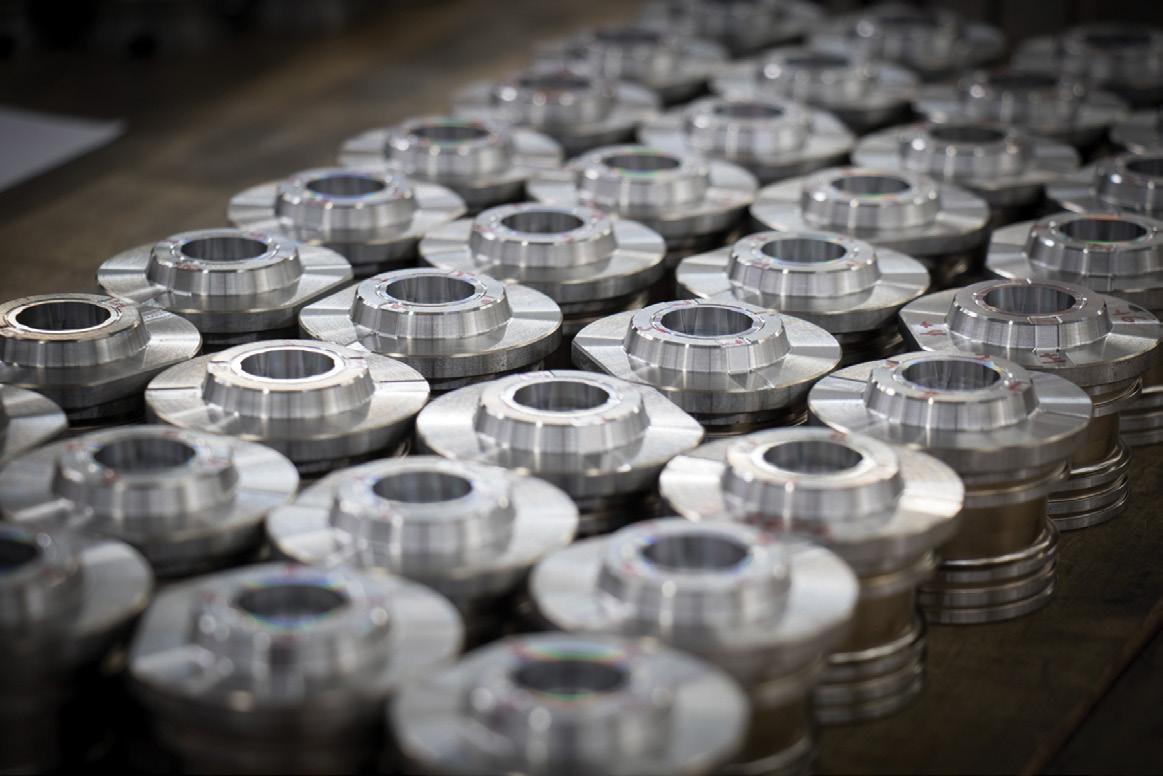
1320 Holmes Rd., Elgin, Illinois
Ph: 847-352-5249
Fx: 847-352-4052 sales@ultrapolishing.com
www.ultrapolishing.com
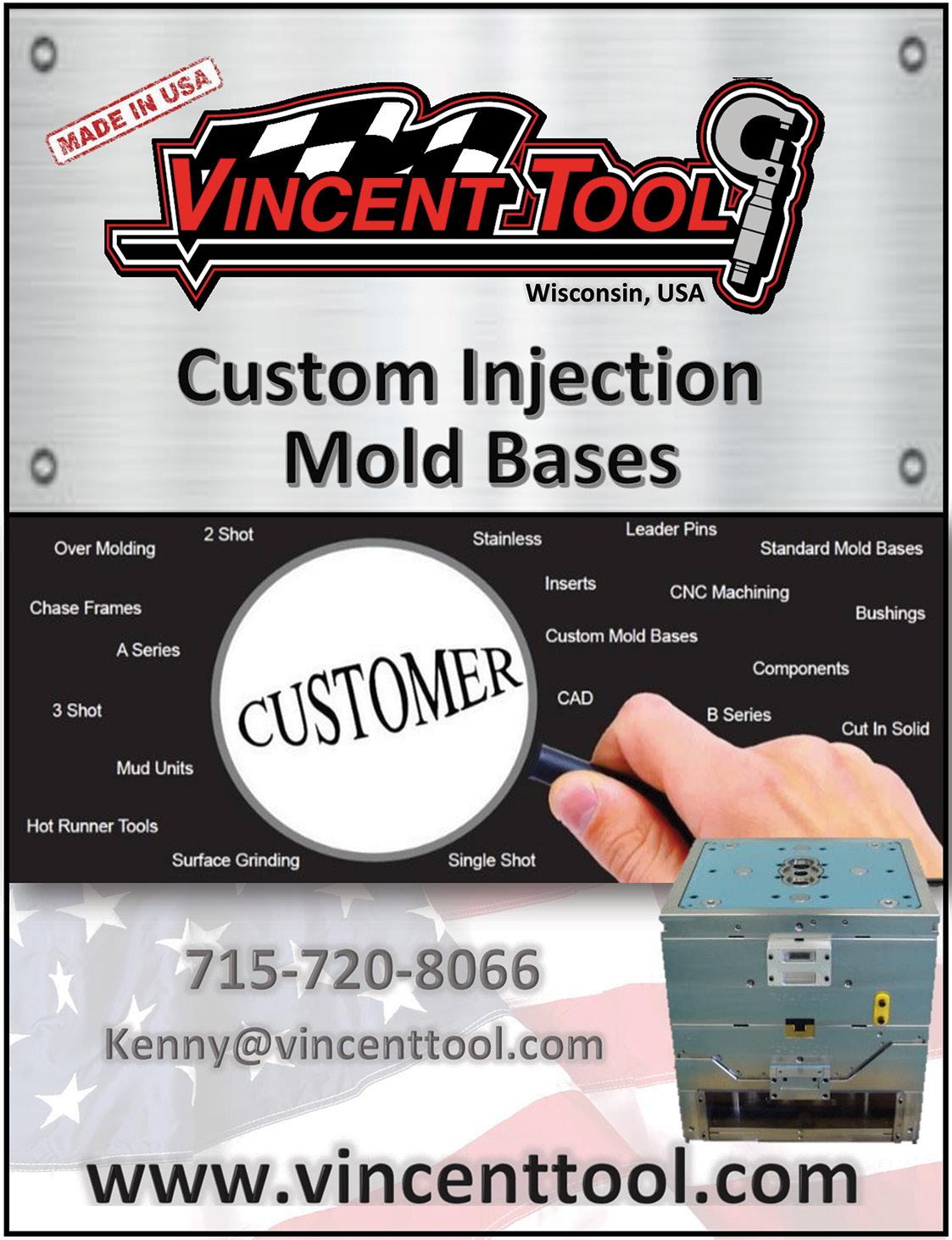
page 9
For instance, these functions can compensate for forces that are introduced by dynamic acceleration processes and that briefly deform parts of the machine, leading to deviations at the tool center point.
Some controls also suppress dominant low-frequency vibrations and permit fast, vibration-free milling. This makes it possible to set high jerk values. Machining times can be reduced without compromising surface quality. In addition, these controls can continuously determine the current mass for linear axes, or the mass moment of inertia for rotary axes, and adapt the feed-rate control to the values measured at any given time. This improves the dynamic accuracy of the axis for every situation under load, enabling the use of optimized jerk values for the feed axes on the workpiece side. The result is a shorter machining time, since the feed axes reach the desired positions sooner.
HOW CAN I EFFICIENTLY IMPLEMENT THE ACCURACY REQUIREMENTS OF A WORKPIECE? Accuracy requirements are becoming ever more stringent, particularly in the realm of 5-axis machining. Complex parts must be manufactured with both precision and reproducible accuracy, including over extended periods of time. During machining, however, machine components are subjected to relatively high temperature fluctuations. The kinematic transformation chain should, therefore, be adapted correspondingly.
If the machine is not operating in a temperature-controlled room, when a machine heats up, the temperatures will change the kinematics of the machine – the axes, which then changes the pivot point. If that point needs to be held within a few microns of accuracy, the changes caused by temperature shifts – machines expand when it’s hot and contract when it’s cold – cause real problems.
In fact, one meter of steel can grow or shrink by as much as 11 microns when the temperature of the steel varies by 1° Celsius. That could be a big problem when machining parting lines, etc. All of this leads to the necessity for recalibration when there are significant temperature deviations, specifically in 5-axis applications.
Recalibration can be done manually by putting a block on the machine, machining the five sides and then measuring to see if the piece is still in sync. If not, operators can manually shift the datum point. There also are automatic functions that allow the operator to place a measuring board and a touch board on the table, and then the machine runs the cycle and automatically makes the corrections. No matter what, recalibration is necessary when completing high accuracy applications in 5-axis.
Also becoming more popular is 3D tool compensation. A triggering 3D touch probe is used to measure the position of a precise calibration sphere at various rotary axis settings. The result is a
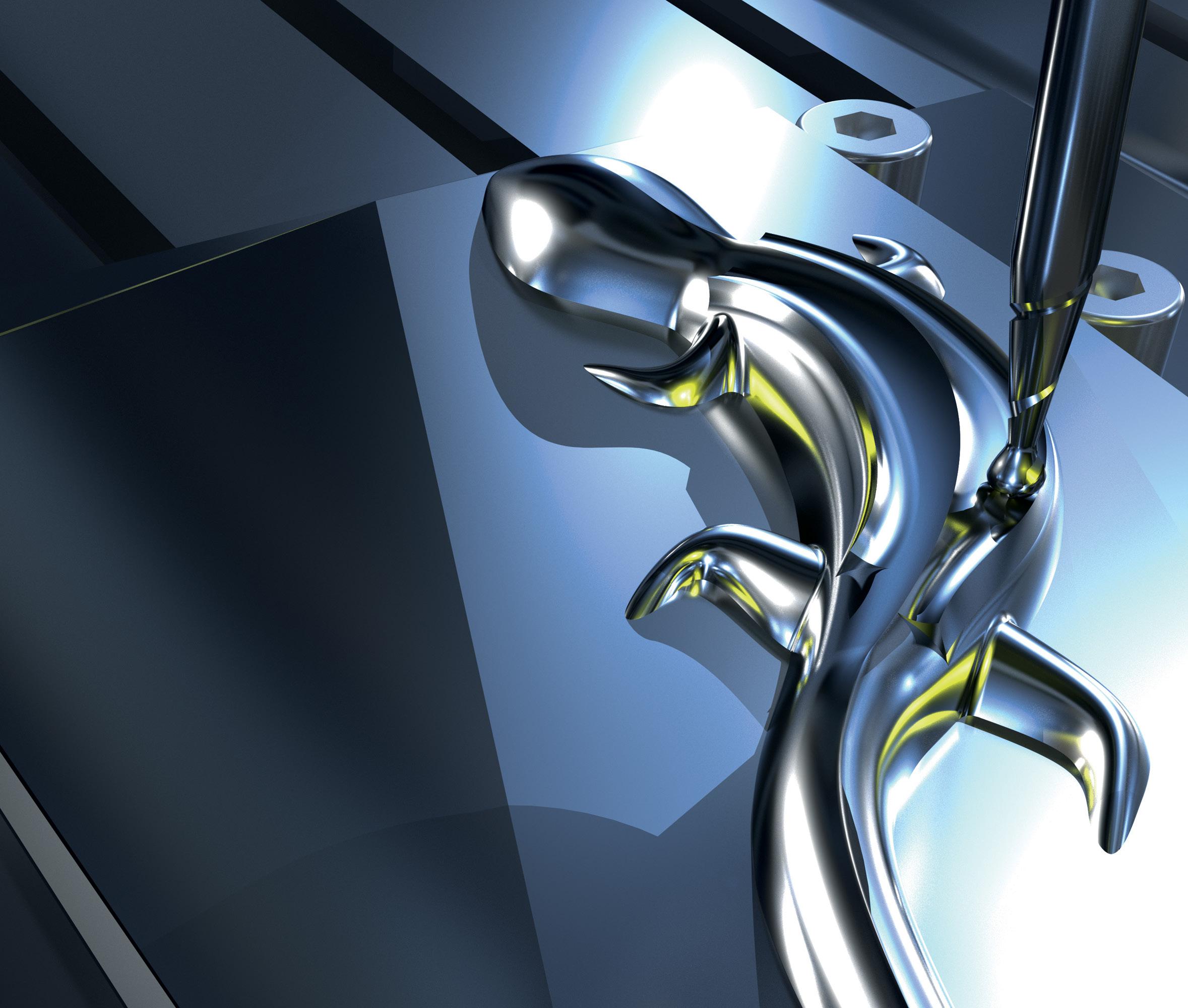
The Dynamic Precision package of functions for the TNC controls combines a high level of accuracy with dynamic motions.
report providing the current actual accuracy during tilting. This 3D tool compensation also automatically can optimize the measured axes simultaneously, and requisite modifications to the machine data automatically can be implemented. The user needs no detailed knowledge about the kinematic configuration of the machine and can recalibrate the milling machine in just a few minutes. If the calibration sphere is permanently mounted on the machine table, then this procedure can even be performed as an automated step between the individual machining processes.
HOW CAN I PLAN AND MONITOR AUTOMATED PRODUCTION? If the machine tool provides perfect machining results, then the associated processes should also run in an optimized manner. Intelligently networked systems for job planning, job management and job monitoring should provide a comprehensive view of job lists, running processes, work progress and any necessary interventions.
There are two components to this: The first is some type of management system to improve flexibility, so that when one program is set up, but another job suddenly becomes a higher priority, a switch can be made efficiently. This management system also provides important information prior to machining, such as when manual interventions will be necessary and how long the machine will be utilized. This allows for precise planning of the machining sequence and facilitates the smooth execution of pending jobs. page 12
μm Accuracy



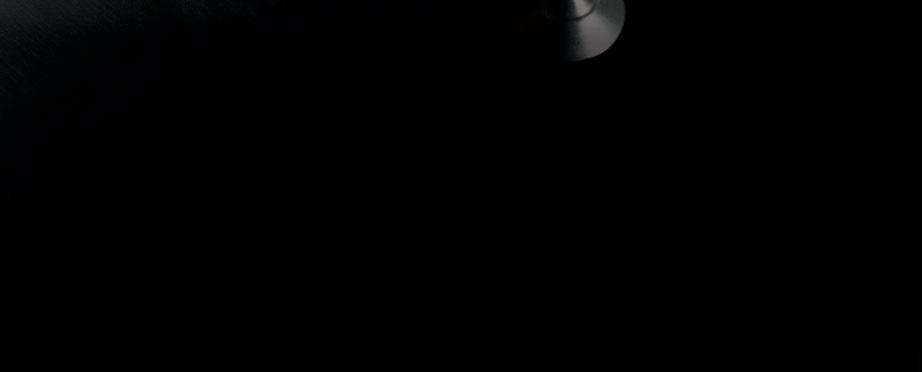
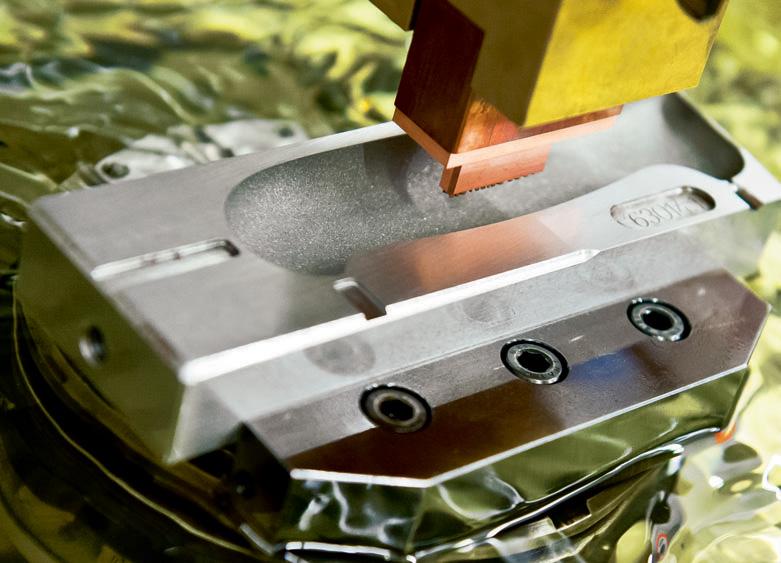
With the EROWA ITS clamping system, workpieces as well as electrodes are held securely and precisely. The guaranteed 2μm accuracy ensures the highest degree of repeatability from one part to the next.
page 11
The second component is a monitoring software that provides a quick overview of what’s happening on each machine. It’s not necessary to invest huge amounts of money – instead, look for plugand-play solutions that provide essential data that can be reviewed easily. Email and mobile device notifications allow operators to monitor processes from home during weekend or evening shifts.
CONCLUSION When it comes to accuracy in 5-axis milling applications the motion control system is a critical part of the machine tool. Mold shop owners and decision makers should take a close look at CNC capabilities and operator training, rather than just relying on CAM data. At the end of the day, the cutting tool has to be moved at high speeds, assuring proper engagement in cutting process, to produce a perfect part the first time. n
Gisbert Ledvon is the director of business development, Machine Tool, for HEIDENHAIN Corporation in North America. With over 25 years of extensive corporate industrial machine business experience, Ledvon is responsible for growing the CNC control side of the HEIDENHAIN business in this region. HEIDENHAIN’s CNC control models are referred to as TNCs and are growing in market share in North America. Ledvon is responsible for developing a strategy to drive technical value and commercial demand for the admired high-end TNC controls at the end user and OEM levels. In addition, Ledvon is charged with leading a team of 5-axis machining, programming and technology specialists at HEIDENHAIN’s North American subsidiary in Schaumburg, Illinois. For TNC control solutions (available for new machines and retrofits), training and application support, visit https://training.heidenhain.com/en_US/.
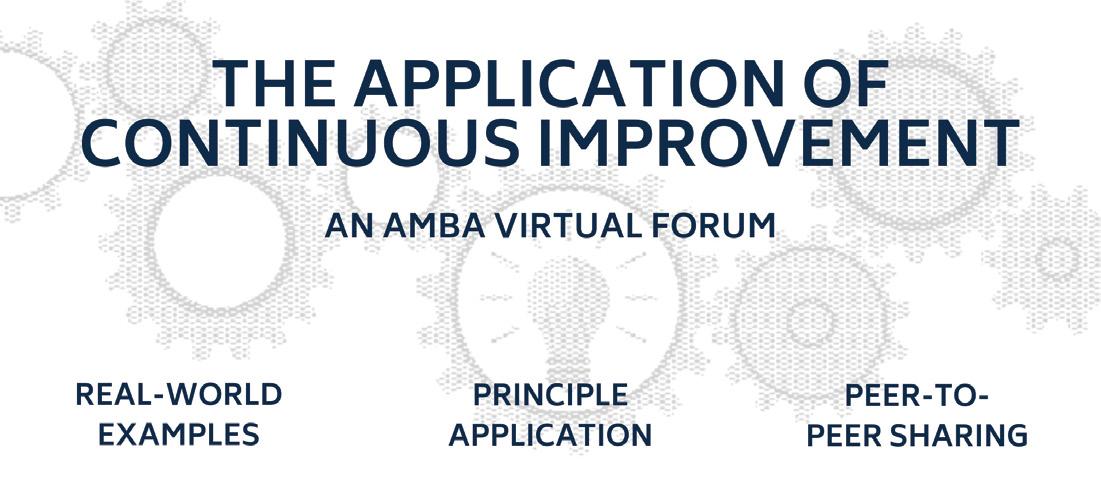
AMBA LAUNCHES VIRTUAL FORUM: THE CULTURAL APPLICATION OF CONTINUOUS IMPROVEMENT NOVEMBER 4-5, 2020 | 10AM – 3PM ET While economic uncertainty introduces stress and forces change, it also presents a unique opportunity for business leaders to renew their focus on the application and evaluation of continuous improvement in their facilities. Through incremental process improvement and reduction of waste, manufacturers can increase their output and efficiencies, while decreasing their footprint in an ever-increasingly competitive global market.
During the AMBA’s upcoming virtual forum, “The Cultural Application of Continuous Improvement,” attendees will hear case studies, presentations and real-world examples of continuous improvement and the ROI achieved. Programming will include peer-to-peer interactions, best-in-class panel discussions and expert keynote presentations. Learn more and register at AMBA.org/Events. This is a members-only event.
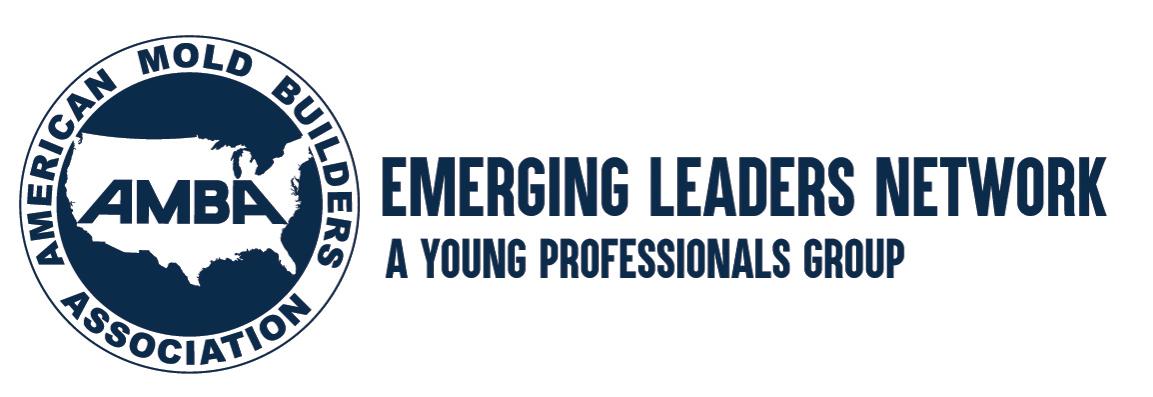
EMERGING PROFESSIONALS EXPLORE PROCESS IMPROVEMENT DURING UPCOMING SERIES Industry knowledge meets critical thinking in the newest series offered by the AMBA’s Emerging Leaders Network: Get Lean – A Project-Based Application. During this multiple-part series, attendees will be coached through the “why” and “how” of quality principles, problem-solving/process improvement methodologies and the application of lean manufacturing principles.
The series will include multiple 45-minute sessions and will address a wide variety of session topics, focused specifically on problem solving and process improvement approaches. Each session will include the opportunity for attendees to practically apply these principles within their own facilities. Cost: $99/person. Includes all session curriculum, instruction and project feedback and review. Learn more and register at AMBA.org/ Events.
NEW FORMAT INTRODUCED FOR AMBA ROUNDTABLE DISCUSSIONS AMBA continues to offer its next series of roundtable discussions specific to current sales and marketing challenges, as well as continuing business challenges. Although the intent of the calls – to share common challenges with one another and learn best practices from peers – remains the same, participants now will kick off the call with a new, small-group format, followed by a larger group discussion. Visit AMBA.org/Events for upcoming session dates and further details.
NEW REPORT AVAILABLE: R&D TAX CREDIT USE IN MOLD MANUFACTURING As income taxes continue to rise, it is important for mold manufacturers to identify areas where they can reduce their overall tax burden to maintain profits and remain competitive in today’s global environment. With this in mind, AMBA’s benchmarking team has released its most recent report, R&D Tax Credit Use in Mold Manufacturing, which outlines the frequency with which this credit is claimed (correlated by company size and revenue), the types of qualifying claims that are made and the underutilized tax incentive opportunities that exist for mold manufacturers. The report is complemented with insights from Michael Devereux, CPA, CMP of Mueller Prost, a leading authority on use and application of the R&D tax credit. To learn more and purchase the report, visit AMBA.org/publications.
COVID-19 RESOURCE HUB CONTINUES TO OFFER TIMELY INFORMATION No matter where business is today, the AMBA COVID-19 Resource Hub continues to be the industry’s premier resource for up-to-date information and data. Current areas of interest include: • Trending data via the AMBA Industry Pulse Survey • State-by-state reopening guidelines and restrictions • Manufacturing checklist, toolkits and workplace testing guides (provided by The Franklin Partnership) • Partner resources from Benesch Law, Mueller Prost and more • COVID-19-related state and national grant opportunities • Government resources, including the DOL FFCRA Eligibility
Calculator
The AMBA COVID-19 Hub is open to all industry professionals. To access the hub, visit AMBA.org.
IMPACT THE BOTTOM LINE WITH AMBA WEBINARS Lead Generation and Marketing Strategy in a Virtual World: Tactical “To-Dos” September 23, 2020 | 11AM ET
As all mold builders navigate the second half of the year in the COVID-19 environment, many are realizing the need to shake up their lead generation and marketing strategies, but are struggling to understand how to make personal, meaningful connections when virtual meetings are the new norm. Join Shelly Otenbaker, president at Waypoint Communications, as she shares tactical, immediately actionable “to-dos.” The second half of her presentation will allow for attendees to share situational challenges where Otenbaker will provide case-by-case insights and practical implementation examples.
2020 Race for the White House: Politics, Outcomes and Trade October 27, 2020 | 12PM ET
The outcome of the presidency especially will have a significant impact on manufacturing in America and how the US approaches China, trade and other challenges. Join AMBA’s lobbyist in Washington, DC, Omar Nashashibi withThe Franklin Partnership, as he provides an insider’s insights into the race for the White House, potential Democratic control of the US Senate, Nancy Pelosi’s potential role as Speaker of the US House of Representatives for the next two years and the impact of all outcomes on manufacturing and mold manufacturers in particular.
Register for both events at AMBA.org. ENVIRONMENTAL HEALTH AND SAFETY SUMMIT GOES VIRTUAL The Environmental Health and Safety (EHS) Summit, November 11 and 12, is an opportunity for business leaders to join one another in a virtual environment and share best leadership and safety practices with other industry professionals. This one-of-a-kind experience provides implementable ideas that manufacturers can immediately introduce to their facilities. Potential topics this year include maintaining SHS sheets, OSHA “sticky points,” autonomous robots and automation safety, the Waste Reduction Policy Act and more. Learn more and register now at AMBA.org/Events.

MEMBERS
Vector Tool & Engineering Jake Chambers, Sales Engineer | 816.966.1901 Since 1995, Vector Tool & Engineering has been a leader of plastic injection mold manufacturing by designing and manufacturing highquality molds for the plastics industry. It serves various markets, including automotive, medical, industrial, caps and closures, lawn and garden, home appliance and pet care. Vector relies on quality tools, on-time delivery, advanced technology and quality-driven employees to push the industry boundaries.
Heritage Mold Bennet Franzen | 815.397.1117 Heritage Mold, Inc., was founded in 1978 and designs and manufactures high-quality, plastic injection molds in the small- to medium-size range. The company prides itself on its strict adherence to delivery schedules, offers prototype services and serves the automotive, consumer products, electrical, hobby, personal care and telecommunication industries.
Trifecta Tool & Engineering, LLC Bret West, Engineering Manager | 937.291.0933 With 40+ years of experience, Trifecta Tool & Engineering has the knowledge, skill and wisdom to produce high-quality solutions for its customers. The company designs and builds multi-cavity injection molds for different industries, including aerospace, automotive, caps and closures, consumer products, electrical, medical, military, toys and more. Trifecta Tool is the first, second and third choice for tooling and machining solutions.
PARTNERS
PUNCH INDUSTRY USA
Cheryl Richardson, Sales | 630.625.8080 PUNCH INDUSTRY CO., LTD., is the American subsidiary of a mold and die components manufacturer in Tokyo, Japan. The company offers high-quality and precision metric standard mold and die components with exceptional surface finish, as well as custommade round and special shaped cores, core pins, ejectors, sleeves and punches made per print.
St. Paul Engraving, Inc. John Seiberlich, President | 651.462.9356 St. Paul Engraving, Inc., was established in 1976 to serve the mold and die industry. The company’s services include mold texturing / graining, engraving, tool repair and polishing. As one of the industry’s growing leaders utilizing the latest technology, St. Paul Engraving is committed to quality, customer service and unparalleled lead times. n