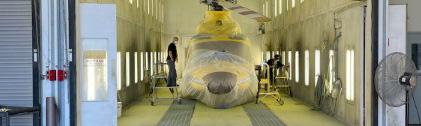
4 minute read
145 REPAIR STATION
by PHI
OUR UNSUNG HEROES
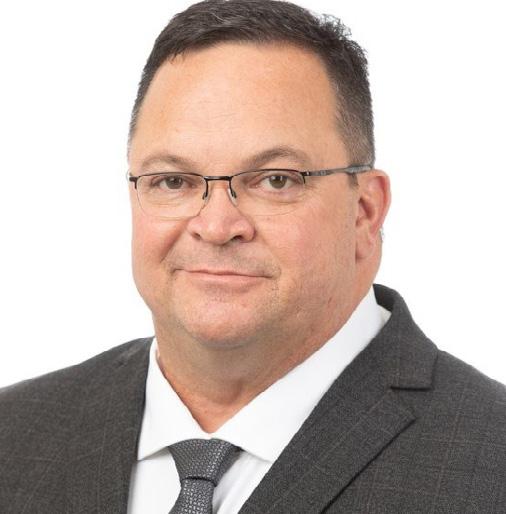
JOHN ELLYSON, DIRECTOR OF MAINTENANCE - PHI AMERICAS
Resiliency—the ability to recover from challenges and push forward in the face of adversity—is a hot topic, especially during the COVID-19 pandemic. But over the years, our teams have shown much more than resilience. They’ve shown courage, compassion, adaptability, selflessness, innovation and strength.
In a time when most businesses were experiencing a drop in demand, PHI was able to strengthen partnerships with our customers and continue to build our position as a leader in aviation—a feat that would not have been possible without the commitment of our teams and their dedication to our core values: safe, efficient, quality, service. And while our success as an organization requires all our teams working collectively together, our 145 Repair Station has always been there to support the operation.
Based at our Lafayette, Louisiana, facility, our 145 Repair Station has always been a critical part of our welloiled operations, but their recent efforts have pushed them further into the spotlight. Over the past 12 months, our Repair Station team has successfully returned 14 aircraft to service in support of our customer contracts and operations. Although the journey wasn’t always easy, the 145 Repair Station rose to the occasion, facing every challenge head-on to support our teams and ensure the success of our operations along the way.
BUILT TO LAST
After emerging from Chapter 11 bankruptcy in 2019, PHI underwent significant operational restructuring so that we could better support our teams, customers and future growth. Our priorities were moving forward with the right-sized capital structure, streamlining our operational footprint and ensuring proven teams were in place to meet our customers’ needs. As part of our strategy, we focused on more appropriately sizing the organization for our current and planned operations.
Then came 2020.
When the COVID-19 pandemic became a global reality, our customers forecasted a 50 percent reduction in flight hours and aircraft, and our business, like so many others, had to once again restructure in response to the impacts of the pandemic. As a result, we decided to park aircraft based on our customer requirements. Our teams worked to identify which aircraft to park based on age, total time and time since last visit to repair station. Together, our fleet of parked aircraft increased by more than 20 helicopters. Once parked, we proactively removed aircraft components that had time remaining from parked aircraft and reallocated the components to operational aircraft. We also reinstalled the components on parked aircraft, allowing us to maintain long term preservation on the parked aircraft and continue operating if needed.
Our Repair Station managers worked with our Materials department to develop a strategic plan to meet our component forecasts. Our teams closely monitored the planned forecasts of components coming due and worked collectively to meet those requirements. The hangar staff also created a schedule to perform ground runs on parked aircraft to maintain longterm preservation status. Those ground runs still occur monthly on our remaining parked fleet which includes less than 10 aircraft.
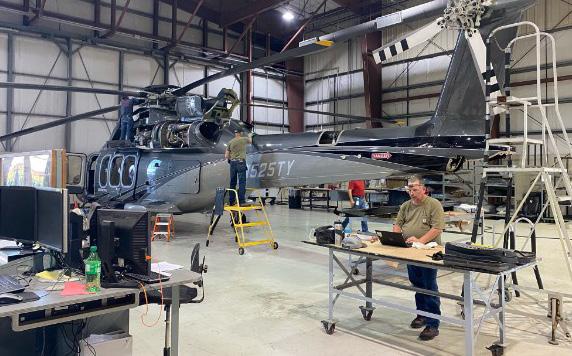
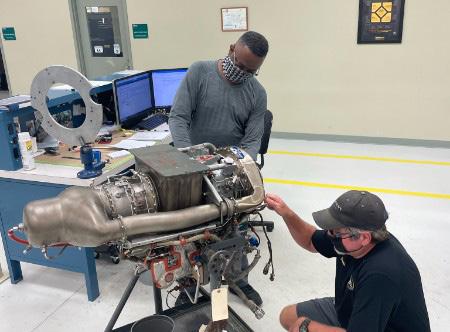

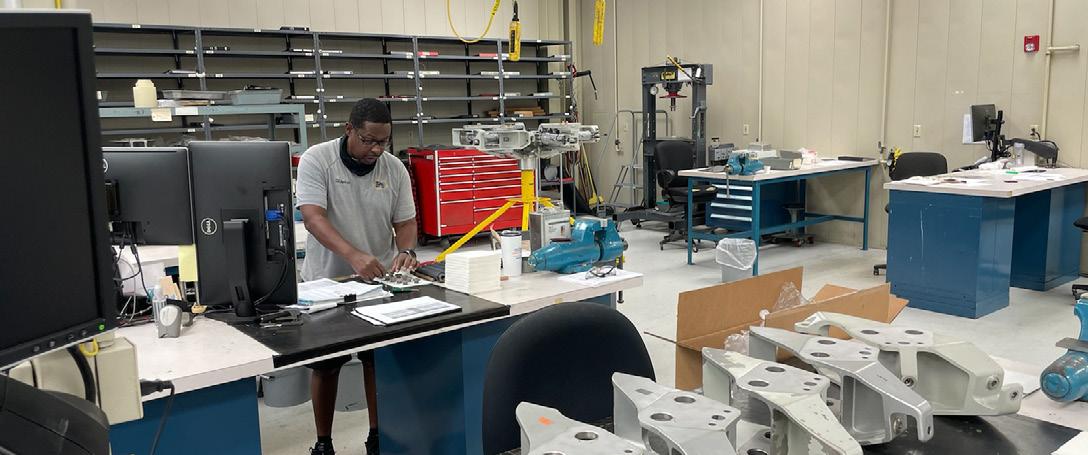
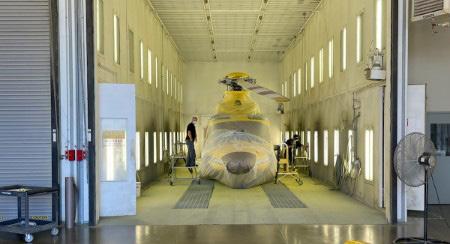
#ONETEAM
As the global economy and aviation industry began to recover from COVID-19, our Business Development team worked closely with our long-term customers and partners to understand their current and future needs. In late 2020, we started to see an increase in activity—I believe, due largely in part to our teams’ dedication to a high quality, high service culture; our availability of aircraft; and our unwavering commitment to safety and reliability.
Our customers’ demand accelerated quicker than the industry anticipated, and we began getting requests to return aircraft to service. For each parked aircraft, the Repair Station team had to comply with all overdue inspections and component replacements prior to returning aircraft to an airworthy state—a significant task, let alone for 14 aircraft. In order to meet our customers’ needs on time and within budget, the Repair Station worked as one team to branch out of their core competencies through a cross-training initiative. This “#OneTeam” mentality has allowed our team to gain deep understanding into the needs and goals of our colleagues for more organizational flexibility and cross-functional collaboration.
Today, not only is the 145 Repair Station team supporting our current fleet in the US Gulf of Mexico, but we’re also providing support for our international aircraft and our partners in PHI Health with manpower, technology support and onsite aircrafton-ground (AOG) support.
At PHI, our people set us apart, and I truly believe that we have one of the greatest—and most resilient—teams. Your loyalty and dedication, combined with your expertise and experience, is unmatched in the industry. So, to the team in the background, showing up to support our operations day in and out, thank you—I couldn’t be prouder to work alongside you each and every day.