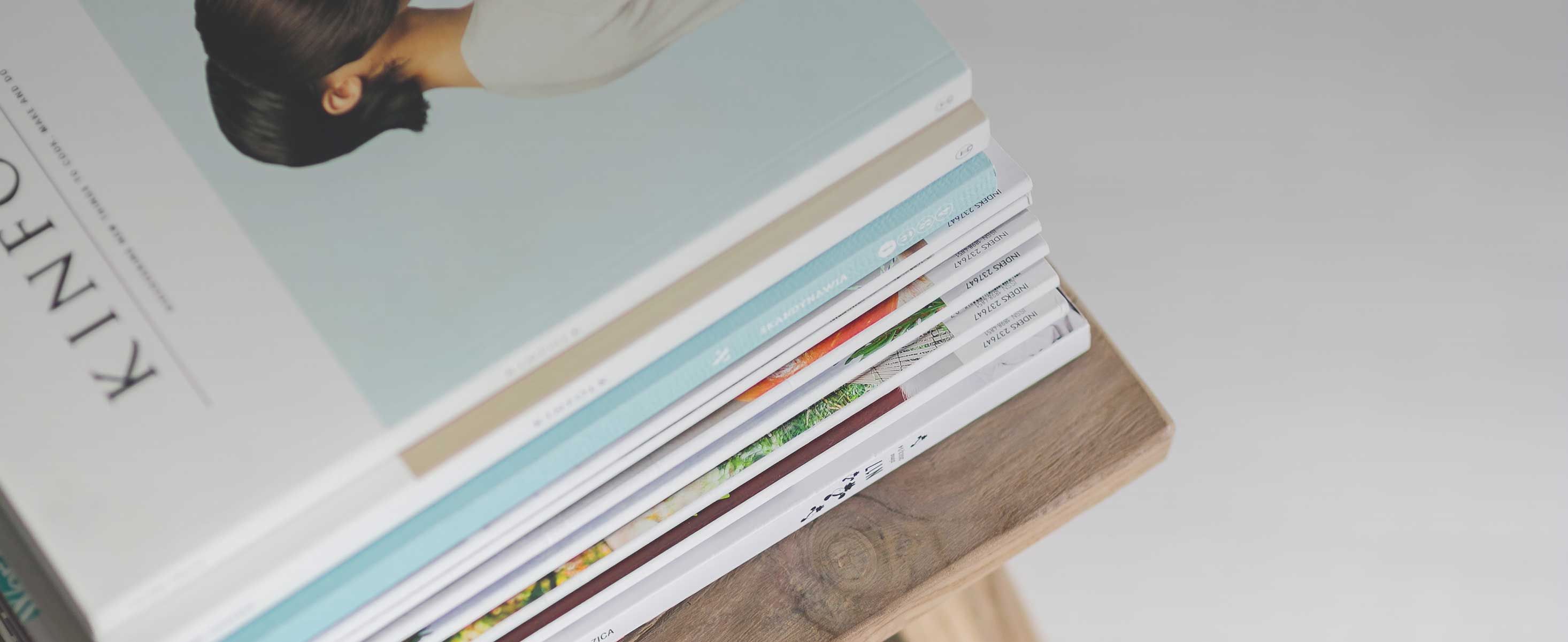
1 minute read
3.1.4 Discussion and Future Work of Automated Vision-based Inspection
3.1.4 Discussion and Future Work of Automated Vision-based Inspection In section 3.1, the methodologies for “Primary Scanning” have been introduced. The GUI for automated vision-based inspection has been developed and tested on BESAT. Here, we will discuss the challenges and future plans for using the primary scanning system.
One of the challenges in the developed vision-based inspection is correlating the image pixels to real-world dimensions and selecting the proper sliding window size. According to camera theory, the ratio between the image pixels and true area needs to be obtained to convert pixel-based areas to an engineering unit. It is common to use the physical target as a marker as well as a sort of calibrating standard in vision-based methods. By measuring the distance between two preselected points on the target in the image coordinate and the world coordinate, a conversion ratio between pixels and engineering units can easily be determined. However, it could be difficult to measure the distance from real-world targets due to the access issue. In this case, the camera theory is utilized as an alternative approach by establishing the conversion ratio R and the distance Z from the camera to measurement locations in terms of camera calibration. As shown in Figure 22, pixel values d can be calculated by equation (8).
d=h/p (pixel) (8)
Where h is the object image dimension in the engineering unit, p is the unit length of camera sensor (millimeter per pixel), which is provided by the camera manufacturer.
According to the triangle similarity, equation (9) is developed:
(9) h/D=f/Z
Where f is the focal length of camera and Z is the distance from the camera to the object.
Substituting equation (8) into (9), conversion ratio R is demonstrated as an inversely proportional function to Z value.
(10) R=d/D=f/(p*Z) (pixel/mm)