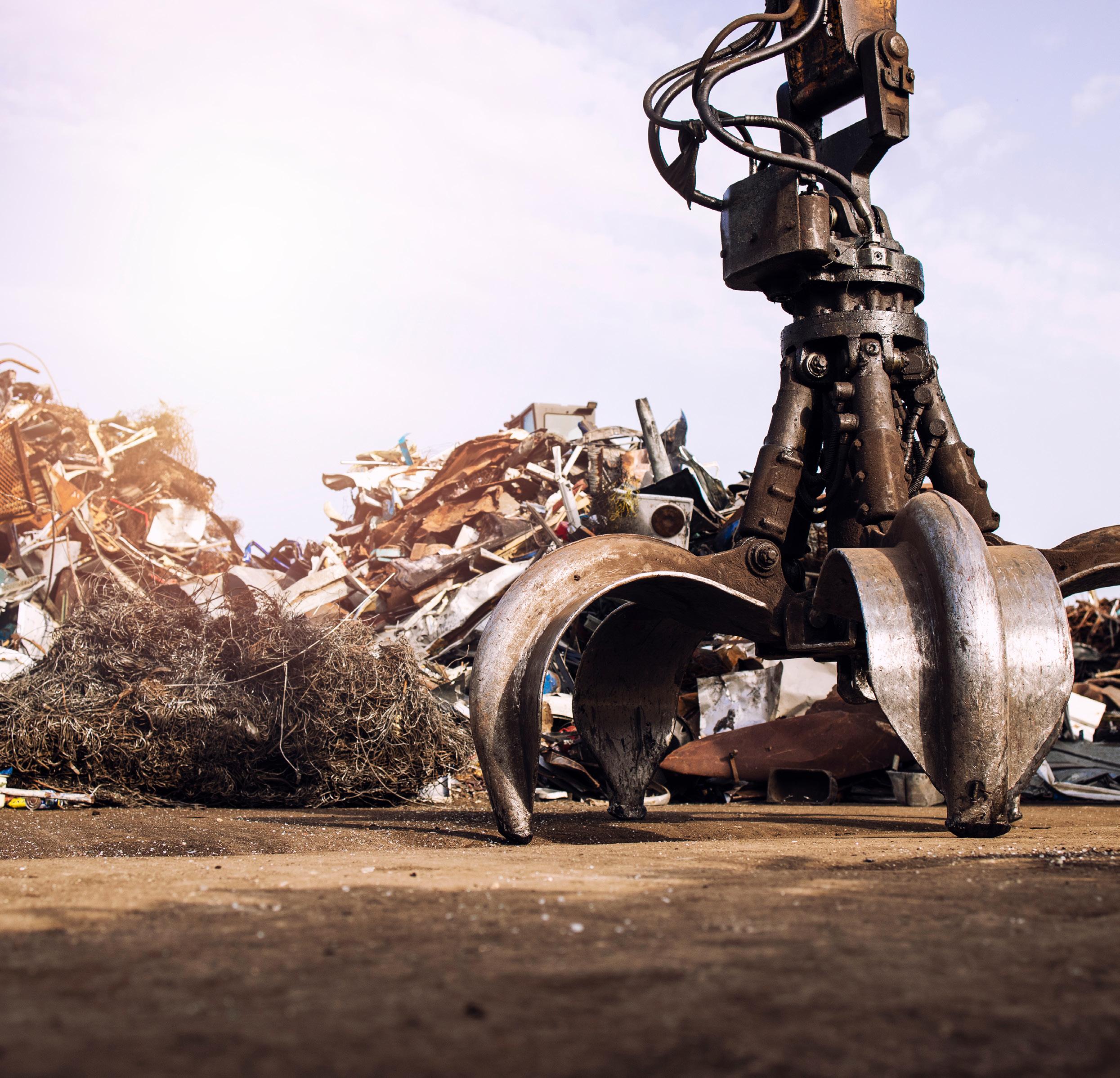
4 minute read
The Lowdown on Loaders
For years, loaders of all varieties have remained a key piece of equipment for construction projects around the world. As the world evolves, so do the projects, and the range of loader options available continuously changes.
The uses of loaders remain highly variable, with many companies such as CAT and Liebherr continuously pushing the limit on what can be achieved. So, what are they about? And what does the future of loaders look like?
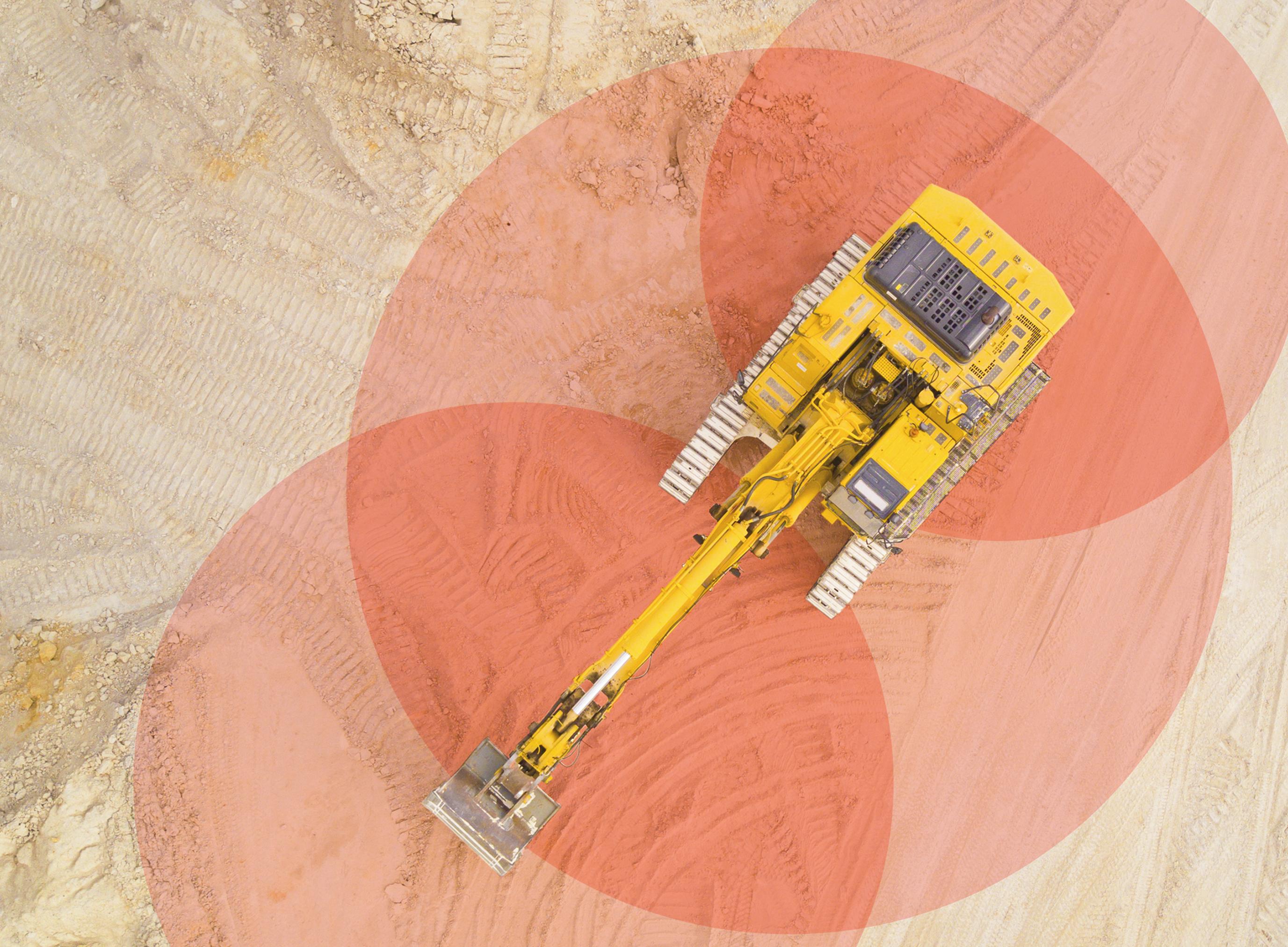
In recent years, the focus has been on how to improve the carbon footprint of this site staple.
Sustainability
The core design of wheel loaders has remained largely unchanged for decades; hydraulic loader arms, supporting a wide bucket proved to be a timeless combination. This practical framework has been steadily developed to keep meeting the challenges of modern projects with strides made in operator safety, usability, and extended service.
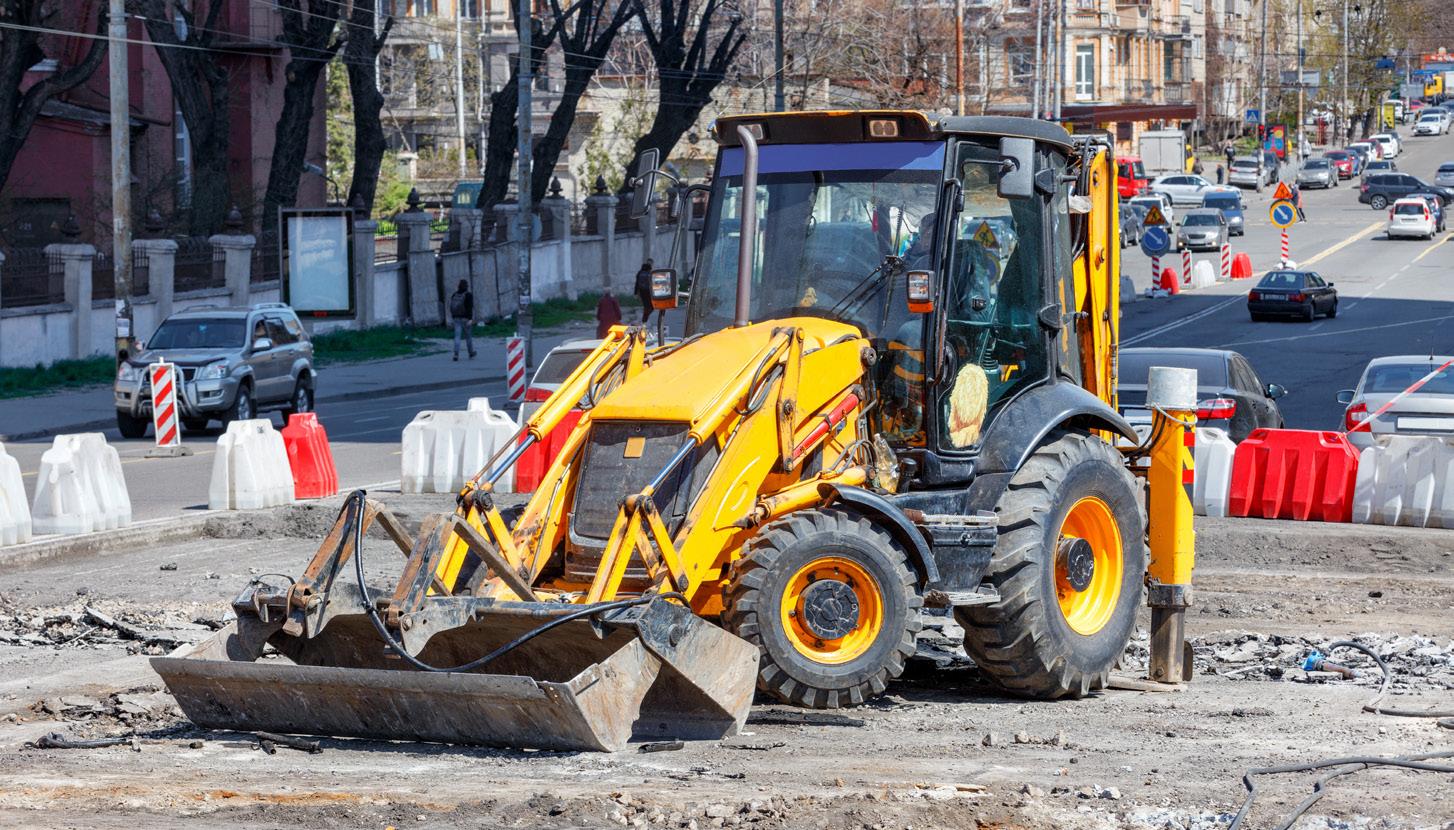
In recent years, the focus has been on how to improve the carbon footprint of this site staple. One way of achieving this has been to prioritise fuel efficiency. Liebherr has been at the cutting edge of these developments, limiting unnecessary counterweight by setting their component mounting position at the rear. This in turn raises tipping loads and handling capacity per operational hour in an impressive design choice.
Meanwhile, Volvo have continued to drive towards environmental excellence through their commitment to electric options. They strive for sustainability and success with the introduction of their Volvo L25 Electric option. Matching the classic compact wheel loader platform to battery power has proven that performance can be maintained or even exceeded whilst producing zero tail pipe emissions and reducing sound pollution. When environmental impact plays an increasingly important role in project bidding, these achievements swiftly show their benefit.
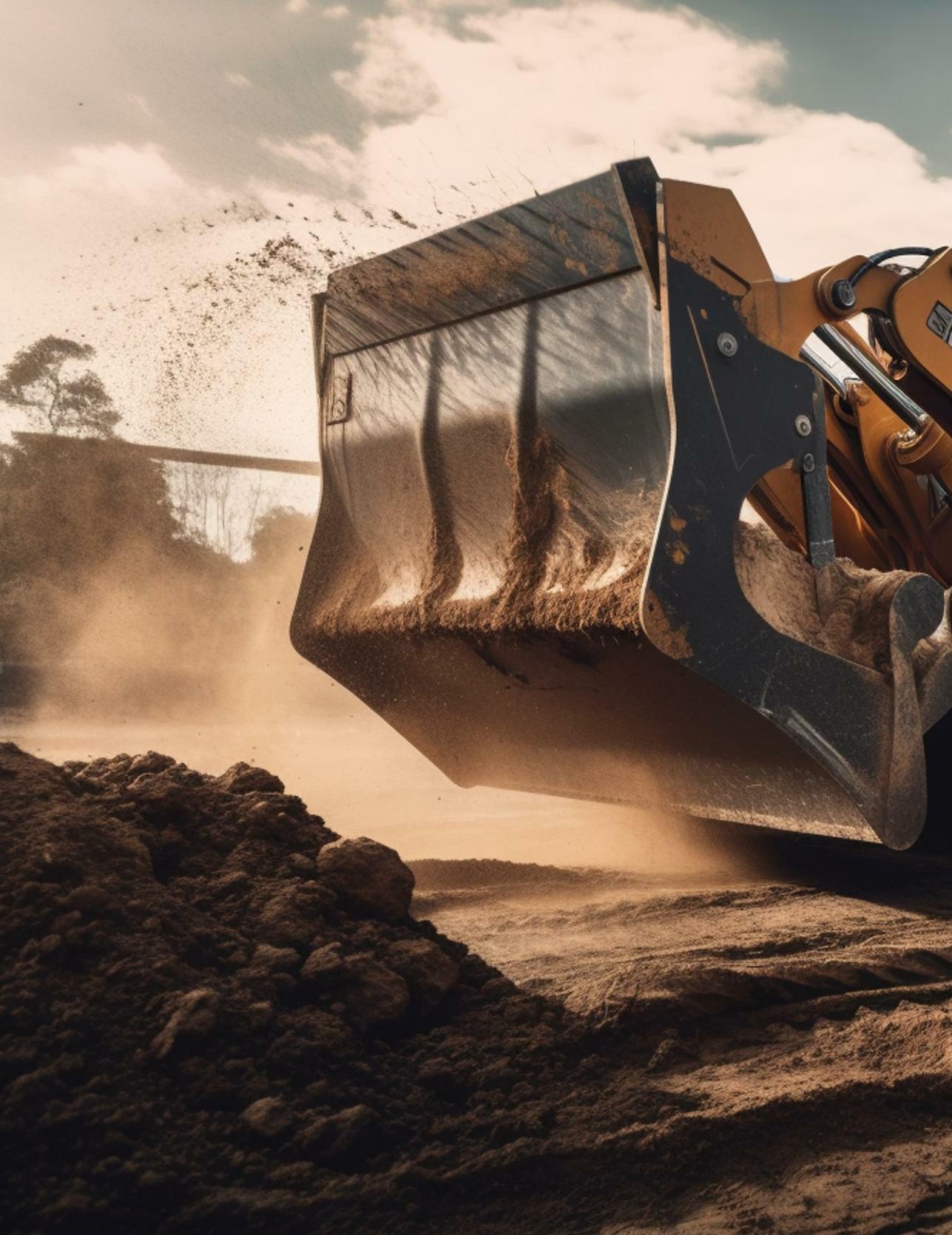
Multi-Faceted
Part of why these machines have stayed at the heart of the industry is the fact that they can be highly customized. Particularly with urban construction sites, where there may be issues with space for equipment or operational limitations, an adaptable loader is certainly preferred.
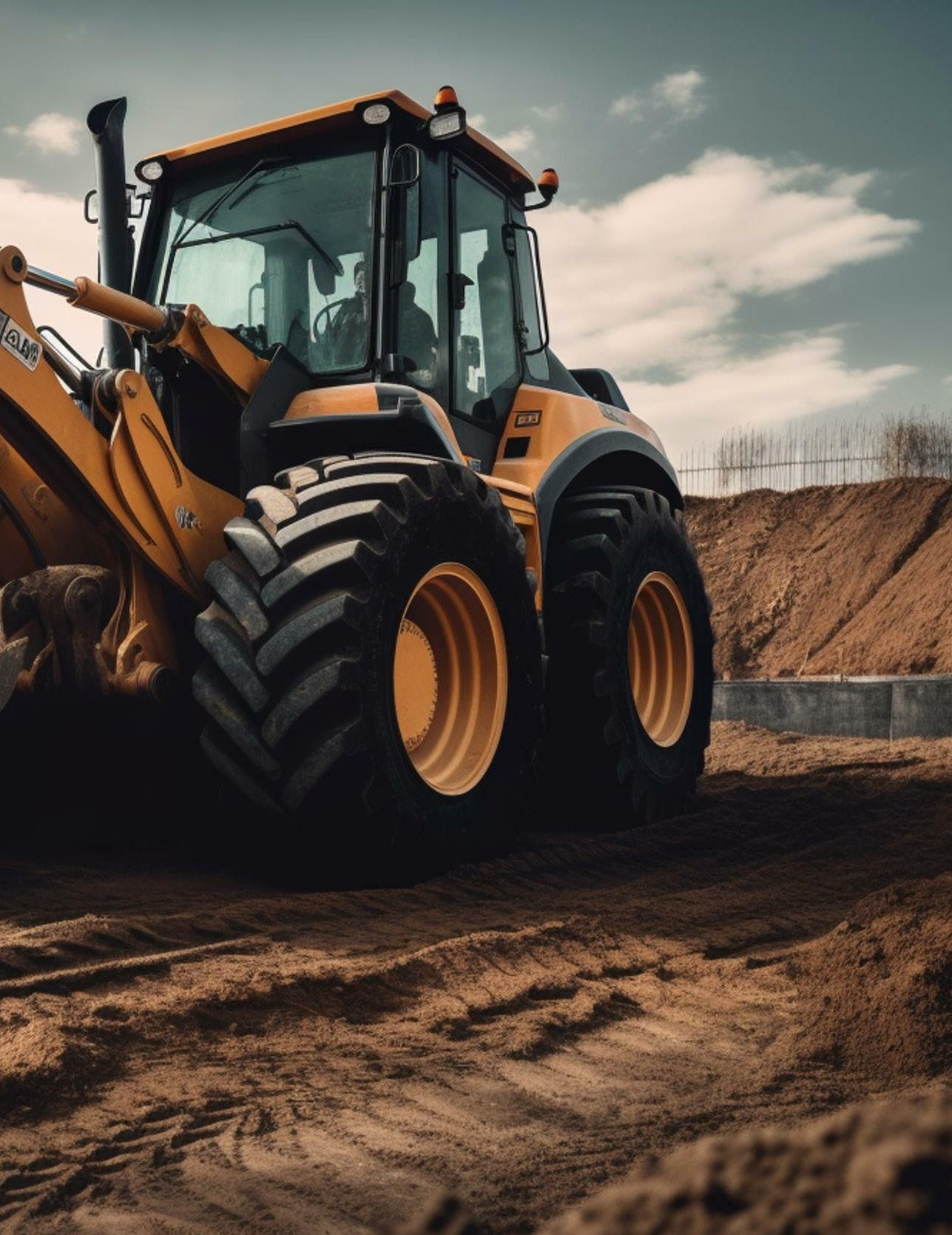
Bucket capacity ranges, fork attachments, grapplers, augers, shovels, brooms, the list of ways that this one machine can be tailored to the situation is truly impressive. However, before getting carried away, it is vital to make sure that you know the details of your attachment system. They are not universal. Manufacturers will tend to have two key styles for couplers: ISO (hook style) and skid steer style. But this can diverge depending on their definition of a wheel loader to include options such as pin-on, fusion, and IT couplers. Each of these in turn creates a variation in breakout force and operating capacity. Before making any decisions be sure that you consider the type and density of materials being handled, as well as whether the attachment chosen could possibly be used by other machines on site.
Nowadays, there are also a range of mini or compact loaders; small versions of the original loader that work for niche markets where larger equipment is simply implausible. Compact Loaders paves the way in the mini market, innovating the world of loader use by bringing the laboursaving technology to the forefront of people’s minds.
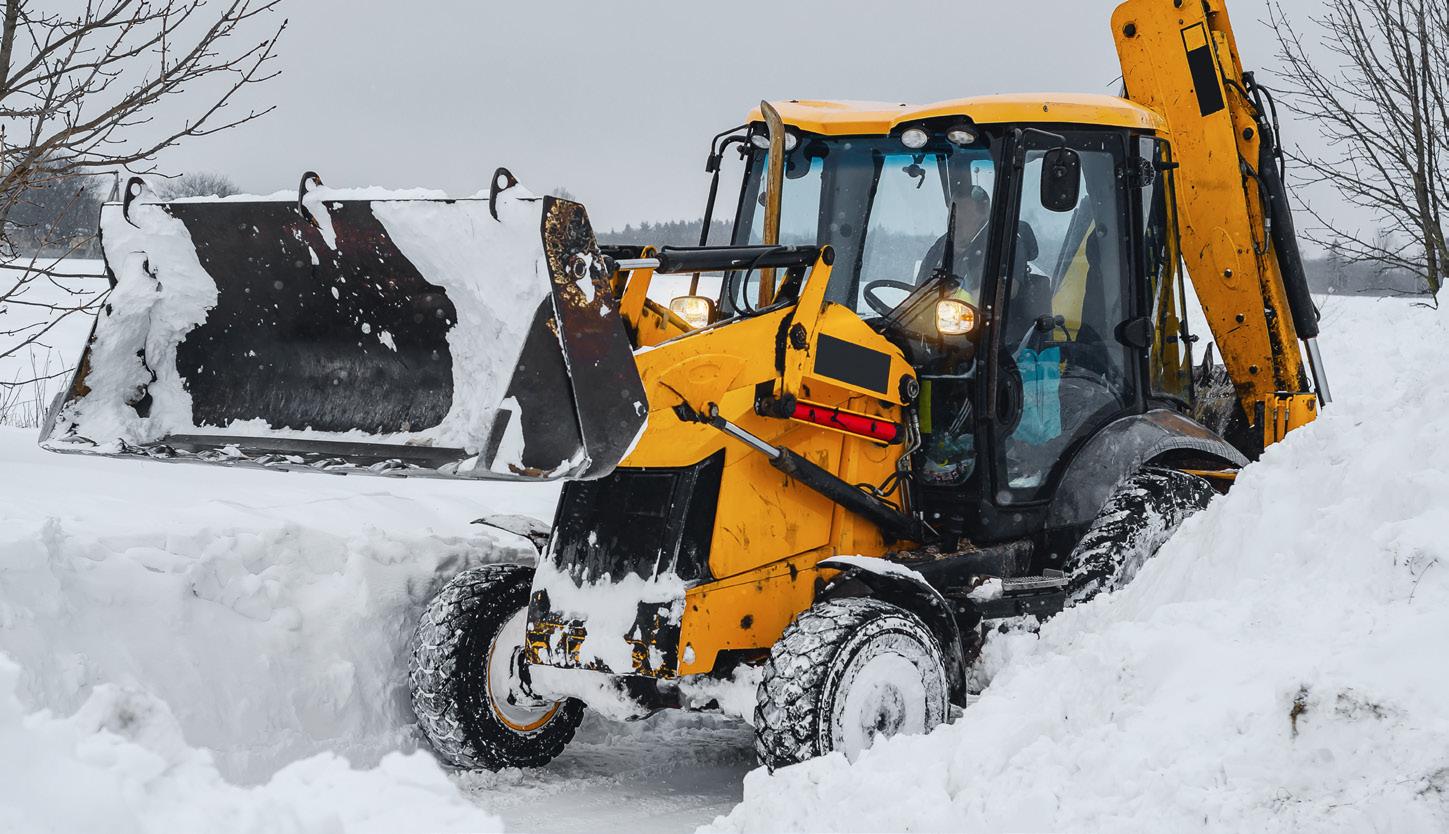
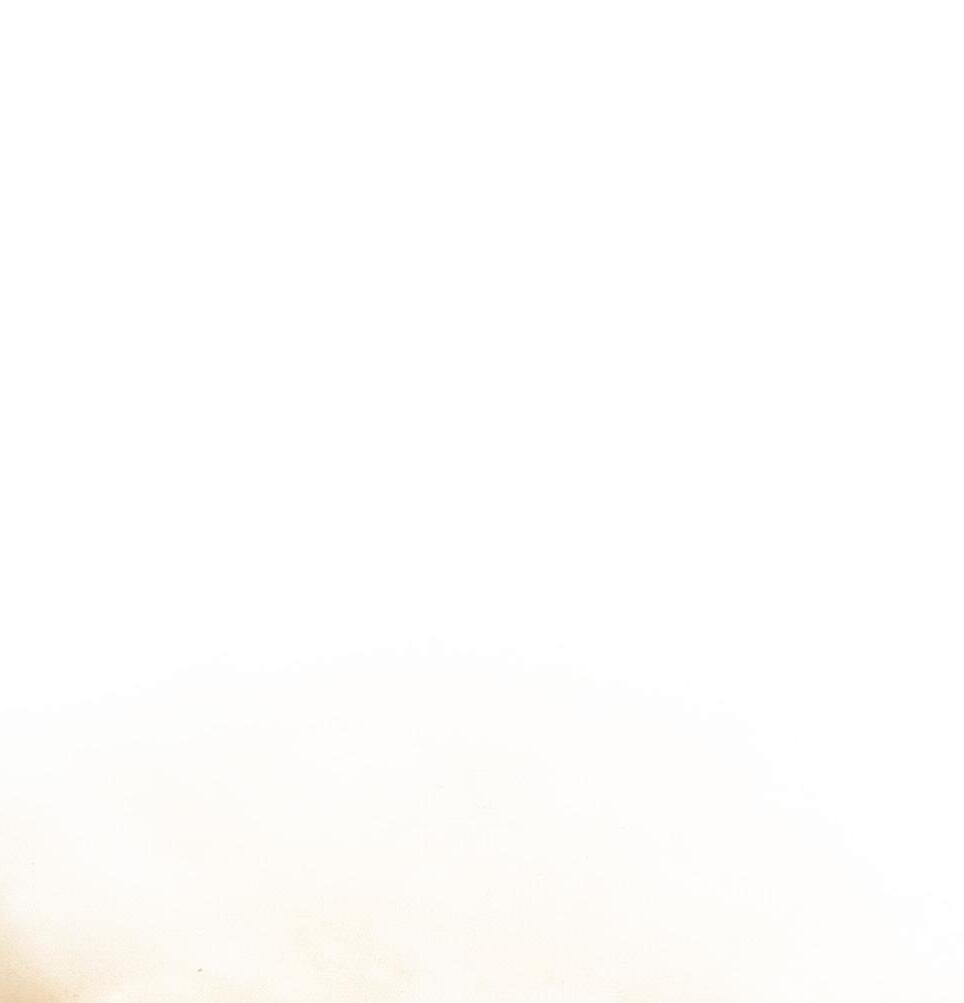
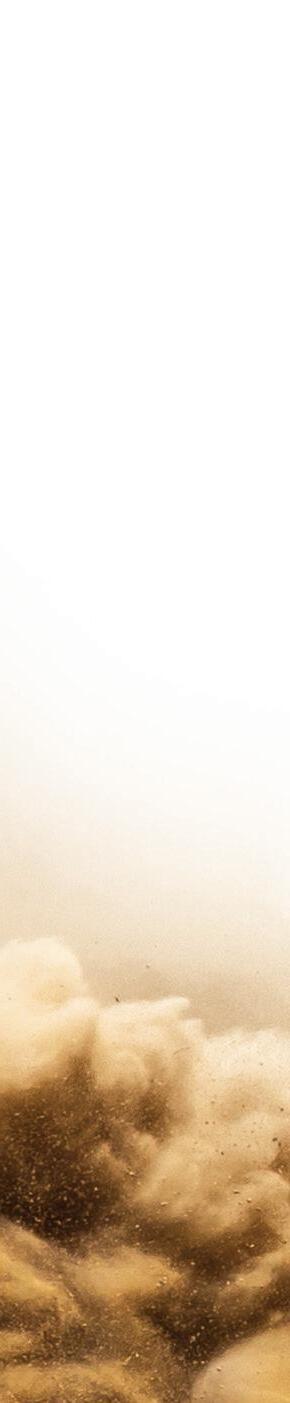
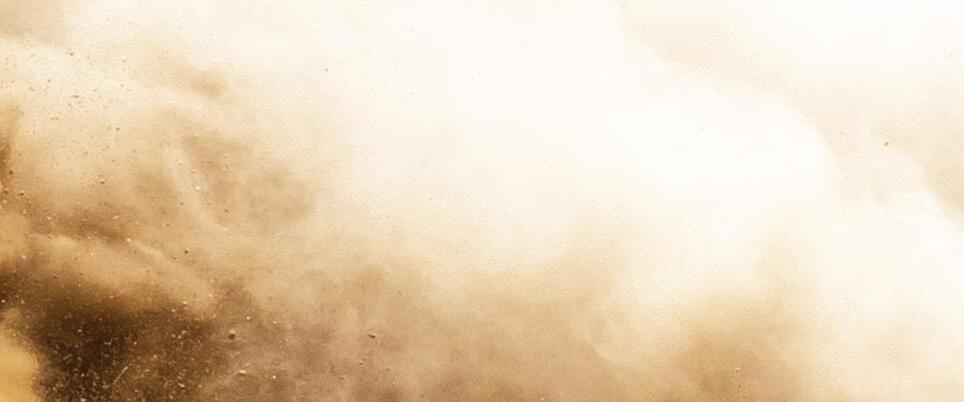
Safety First
Perhaps the most important thing to consider with a wheel loader is the person in control. There has been a greater awareness in the last few years of the role that operator comfort plays in the bottom line. An enhanced environment and integrated technology have become the watch words for improving ease of use and therefore, productivity.
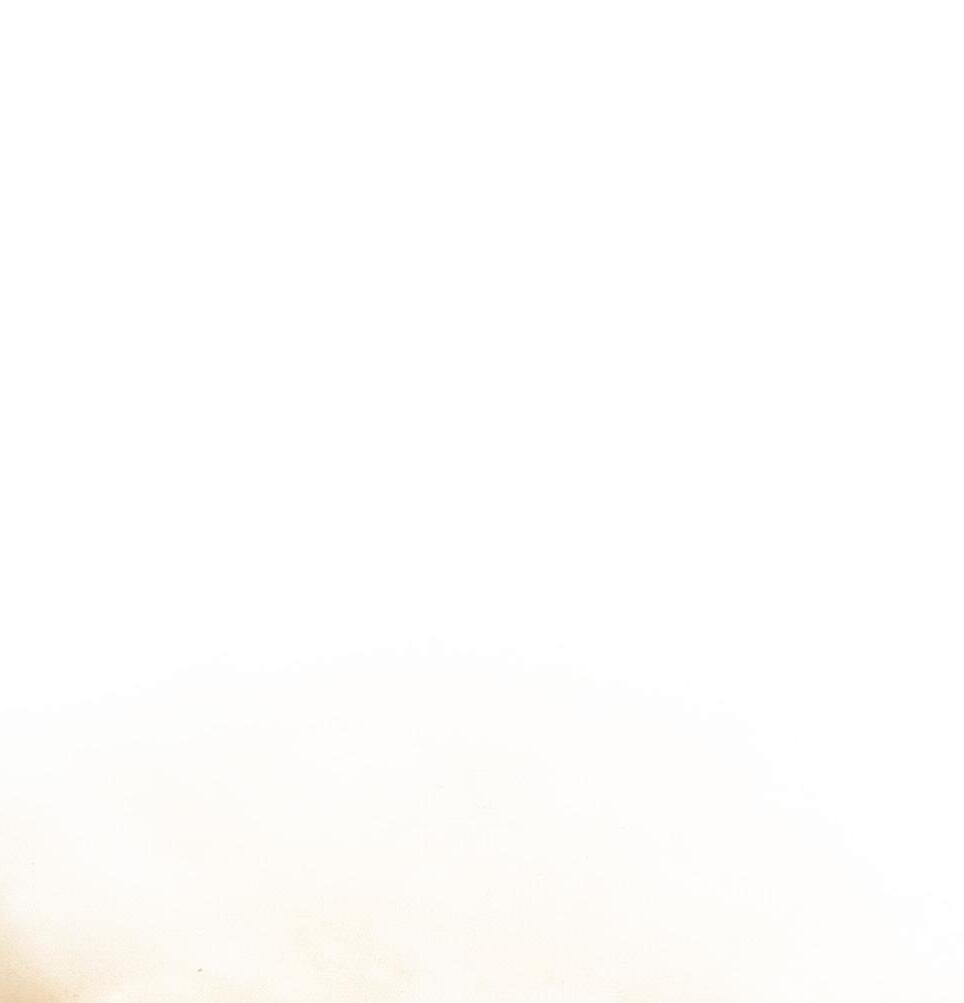
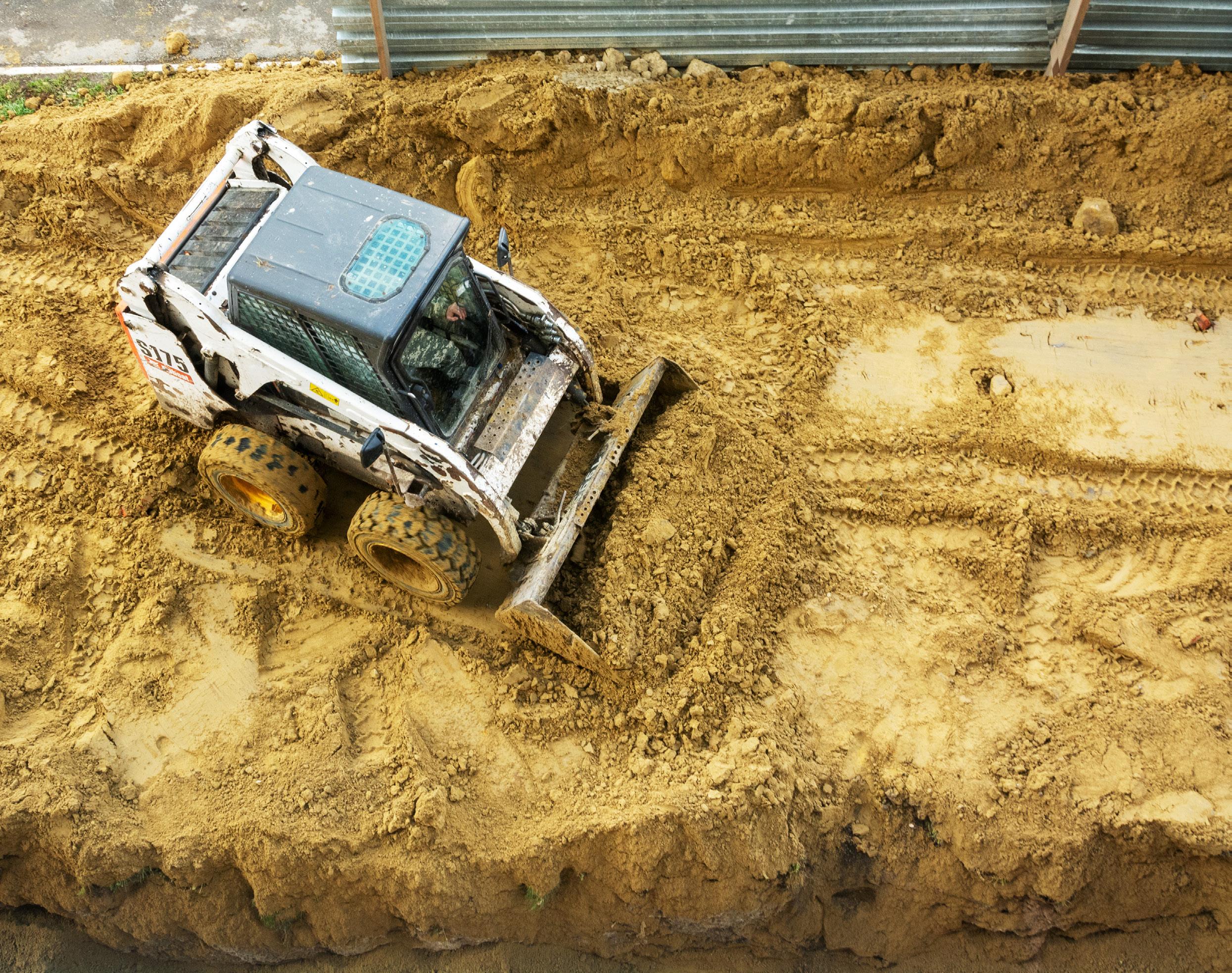
For instance, CASE’s virtual launch in 2021 of the G-Series Evolution was highlighted by the operator cab. Increased forward visibility has been achieved through use of a larger, single curved piece of glass. At the same time, the back received a standard rear grid defroster and optional integrated rear view camera.
DEVELON took visibility a step further with their ‘Transparent Bucket’ technology, where strategically mounted cameras stitch their feeds to show the operator what is beyond the bucket. Not only do these changes boost efficiency, especially during attachment exchanges, but they also have meant huge strides in safety.
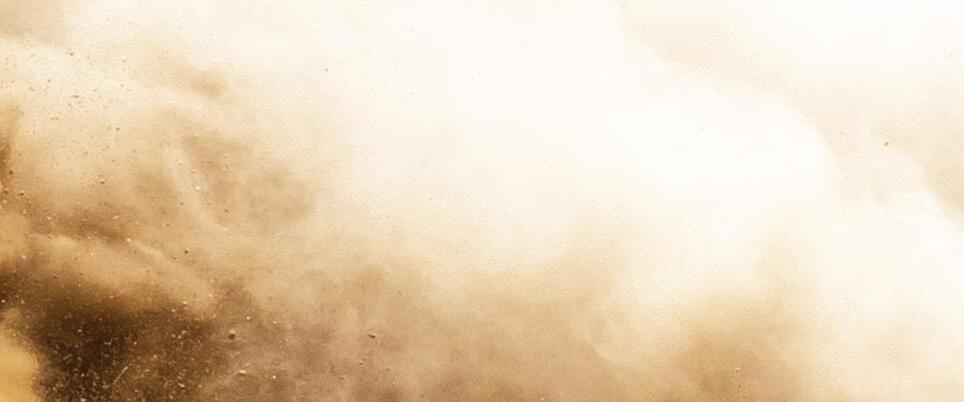
This link between efficiency and safety is echoed across a range of adaptations being rolled out across the market. Object detection alerts are a key feature for improving site safety on a range of heavy machines, with proximity sensors and safety zones becoming an expected standard. Indeed, Zonr have led the way in extending such protection to the individual workers to maximize virtual barrier awareness. No doubt this is an element of design which will continue to be developed to further improve safety standards to the betterment of the industry.
In an industry that works long, tiring hours, it’s good to see that not only things such as driver safety are taken into account, but also their comfort as well.
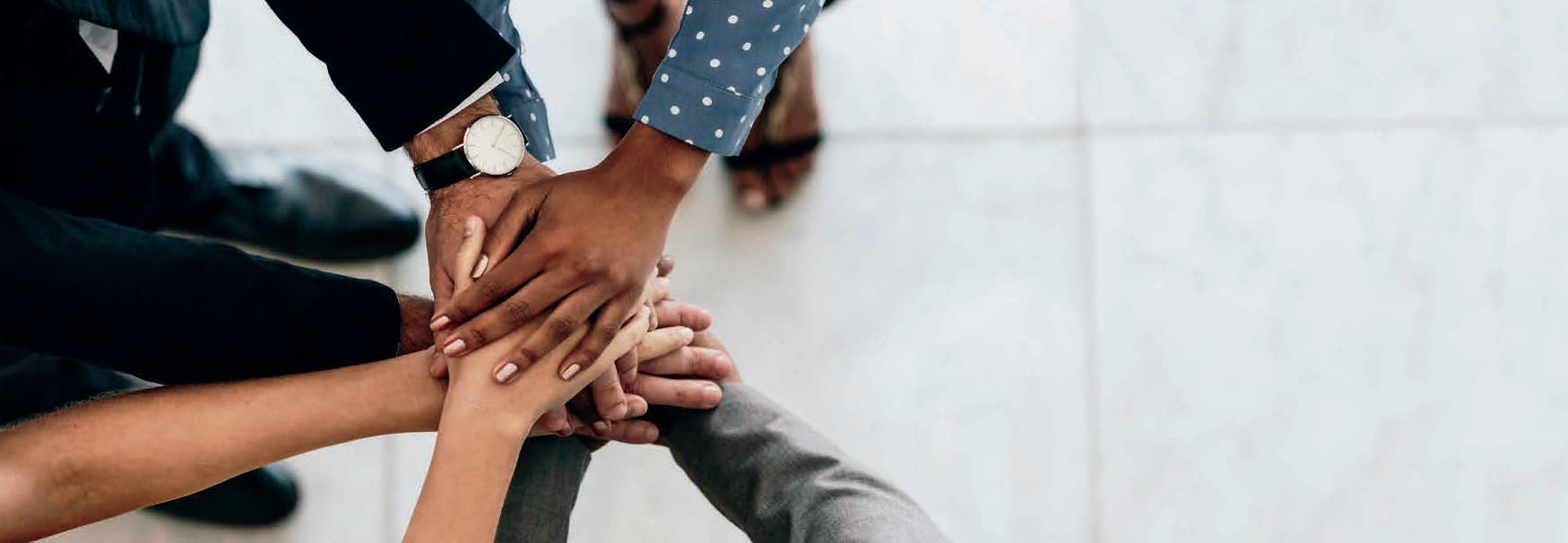
Kubota have launched their new RO70 and RO90 loaders. With their long reach, brilliant lifting power and neat, compact design, they are perfect for a wide range of jobs. They were designed with comfort in mind, maintaining high levels of visibility whilst remaining simple and easy to operate. Their glass cased, spacious cabs are also fully air conditioned, meaning the driver remains content at all times. Such things cannot be overlooked when it comes to safety; a happy operator is far less likely to cause an accident than a tired, frustrated one.
The Future
It is clear to see that over the years wheel loaders have benefitted from a wide range of design and technological improvements, and there is no sign of that changing. Greater productivity, fuel efficiency and lowering service costs continue to be at the forefront of the future of wheel loaders. More responsive hydraulics systems, more accurate camera vision fields, greater stabilization over varied terrain and so much more.
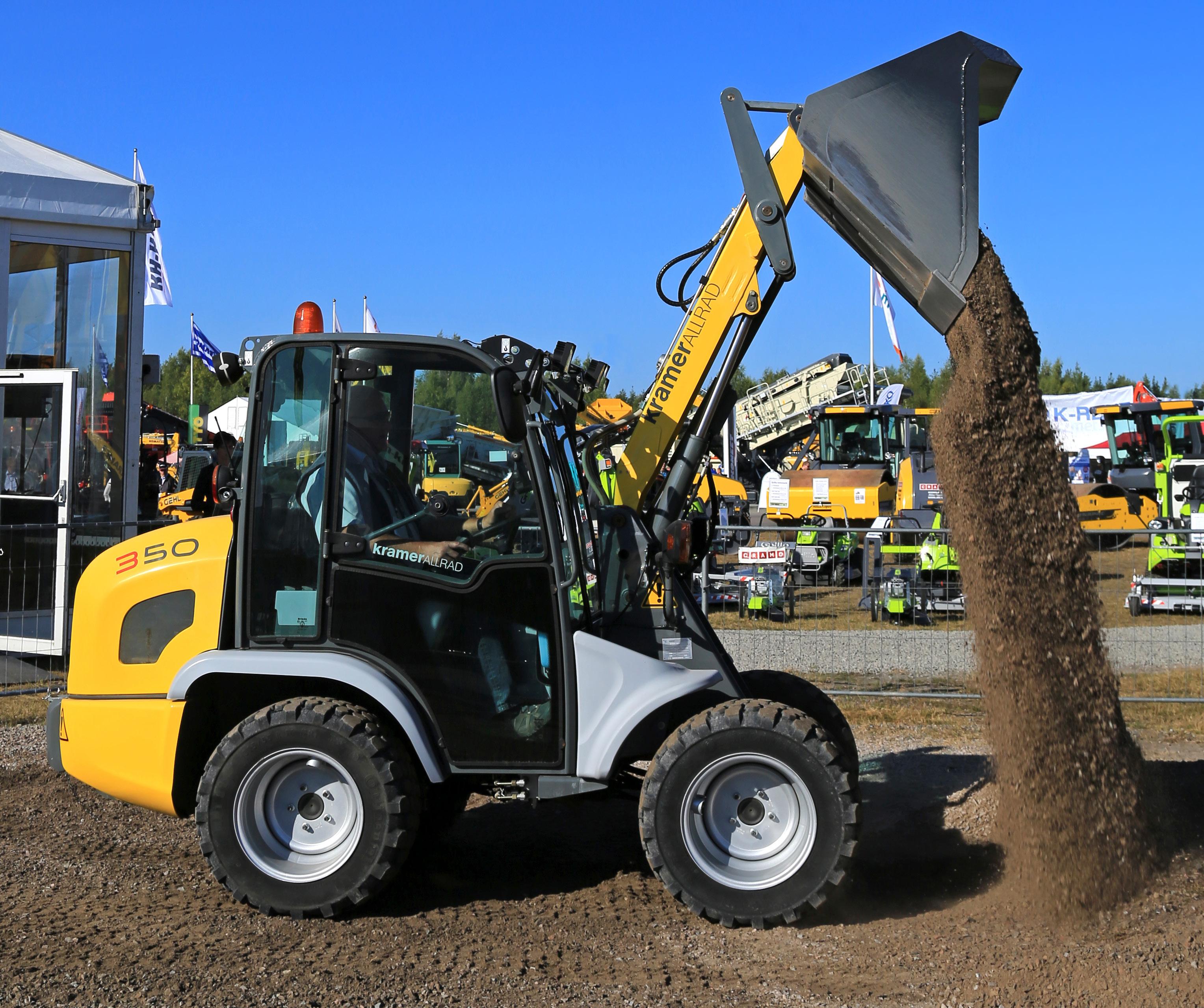
It is as ever amazing to see what can be done whilst the heart of the machine stays true. Volvo completely overhauled the materials, including a more robust upper centre hinge bearing, updating the frames for the new axels and transmission. CASE integrated ergonomic joysticks, optional multi-lever controls and digital touchscreen displays. Attachment options continue to develop to meet the specific needs of modern projects.
Throughout all of this, the humble wheel loader continues to hold its place as an iconic and vital piece of heavy machinery across industrial sectors. We can’t wait to see what the generation has to offer.
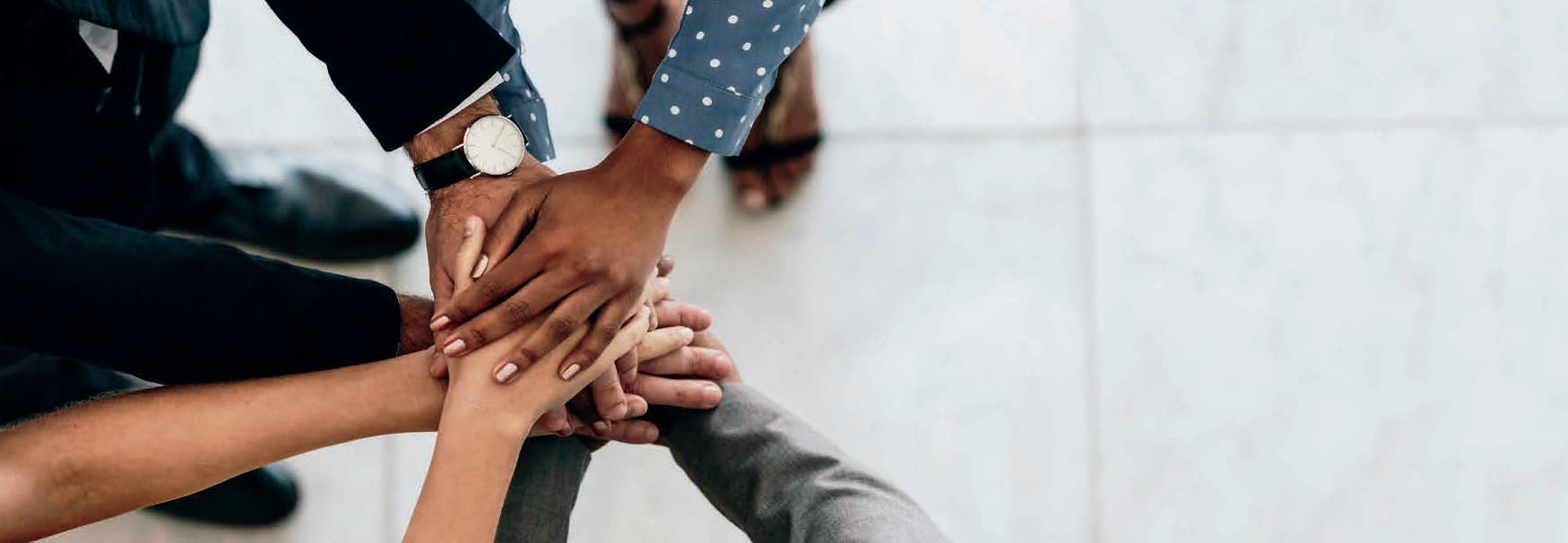
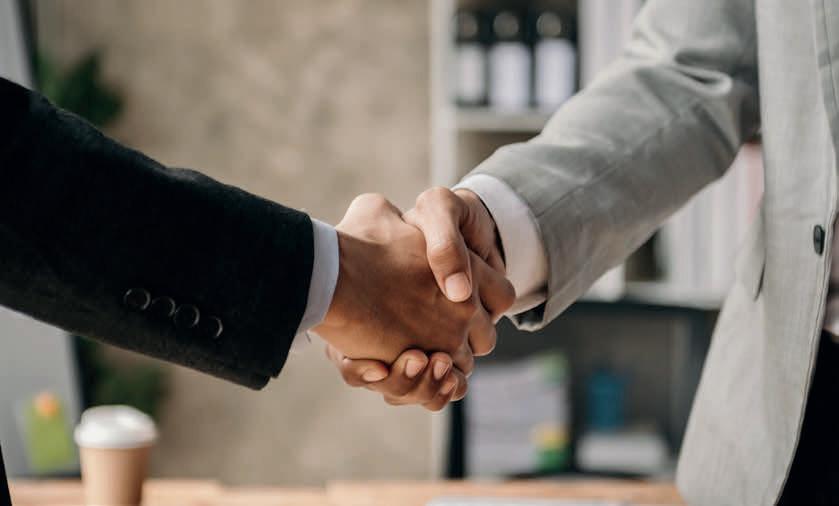
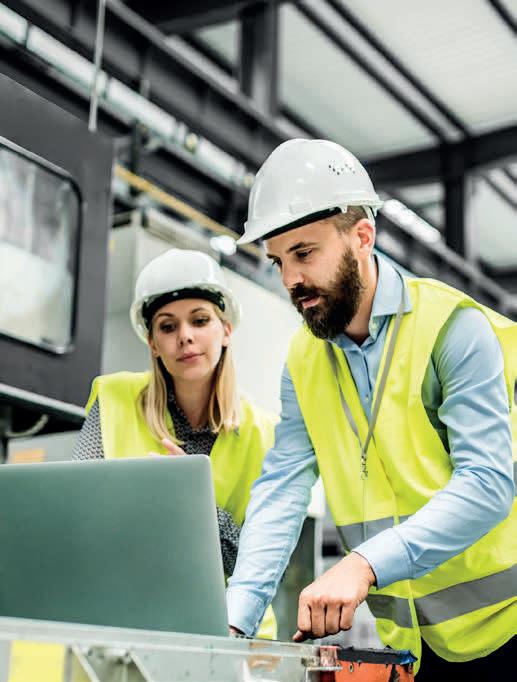
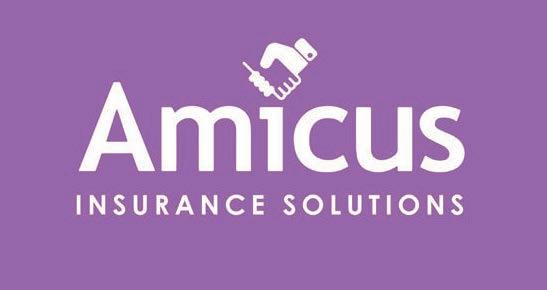
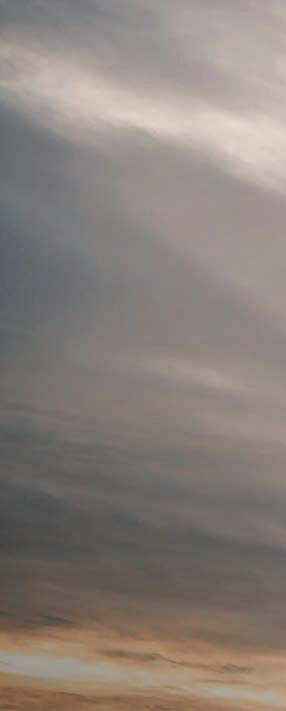
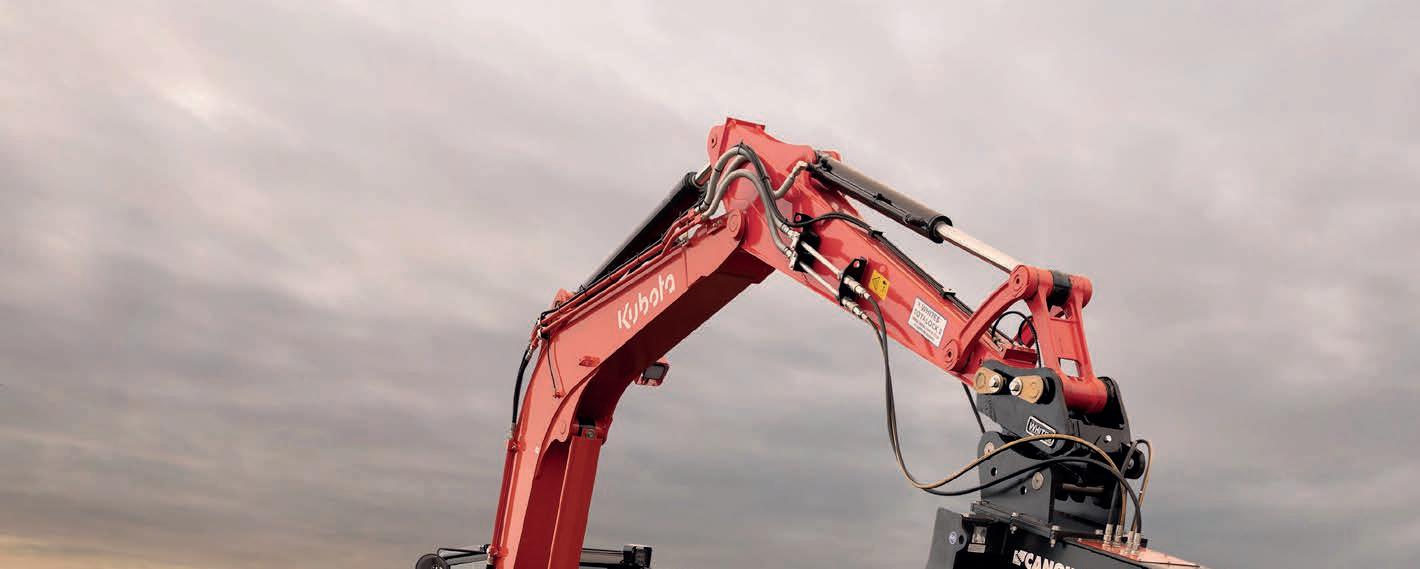
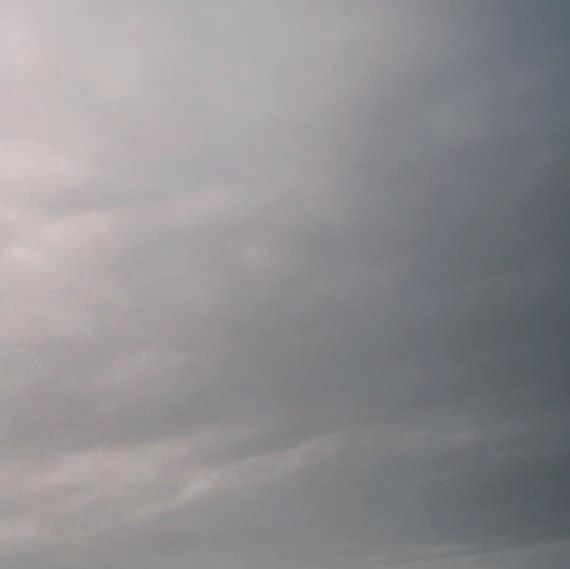

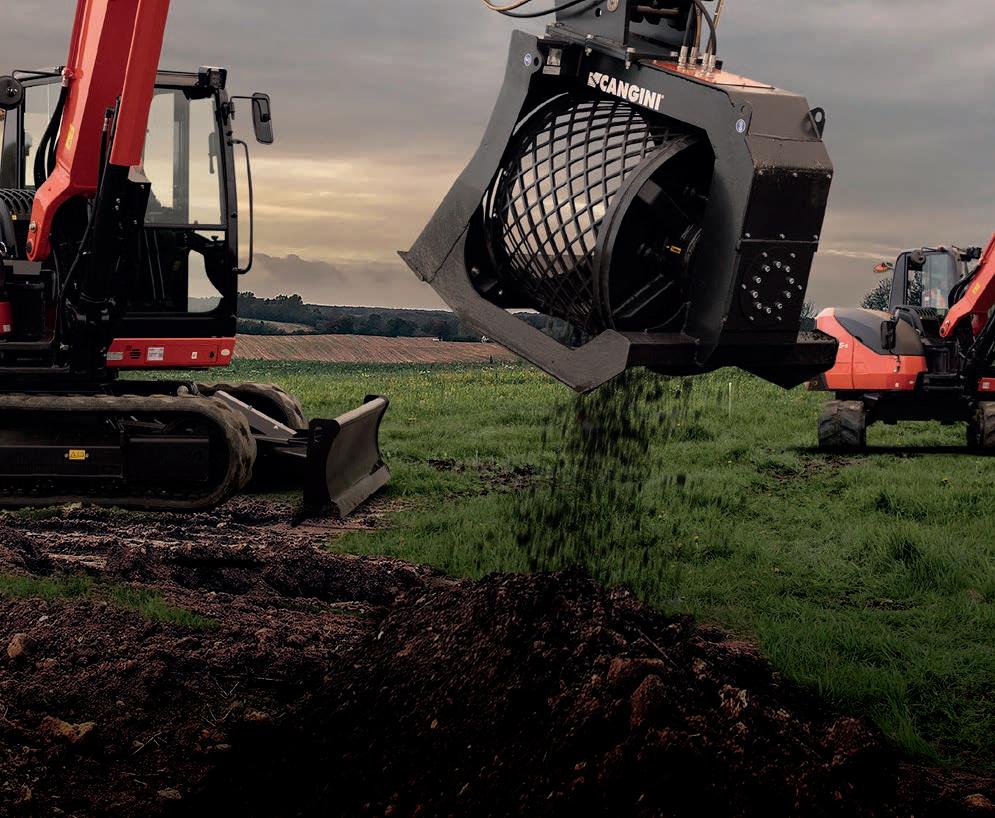
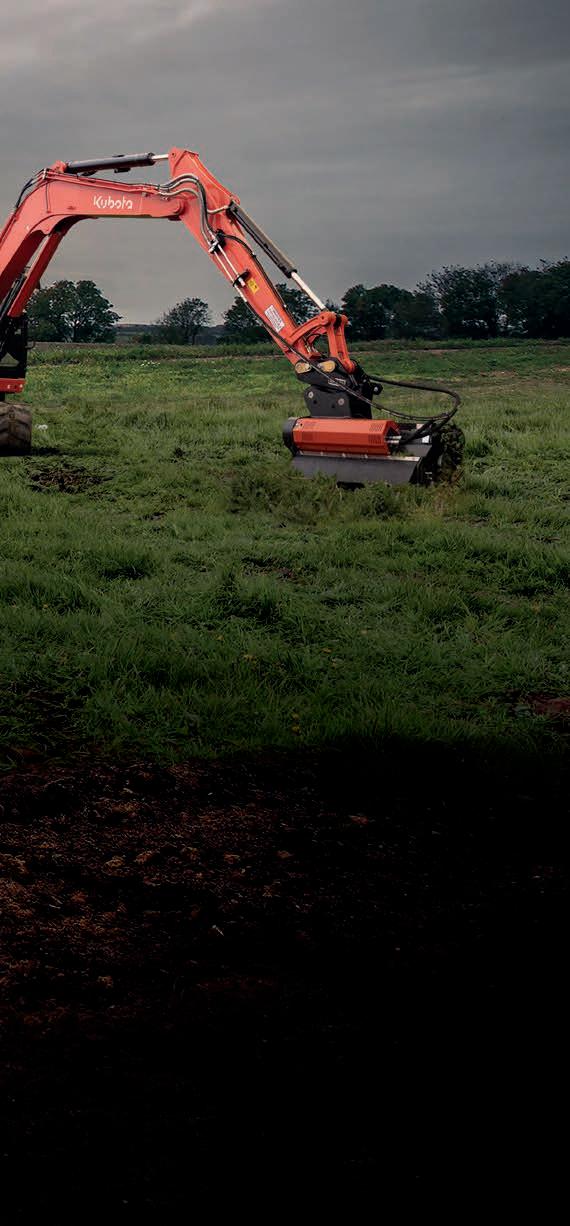
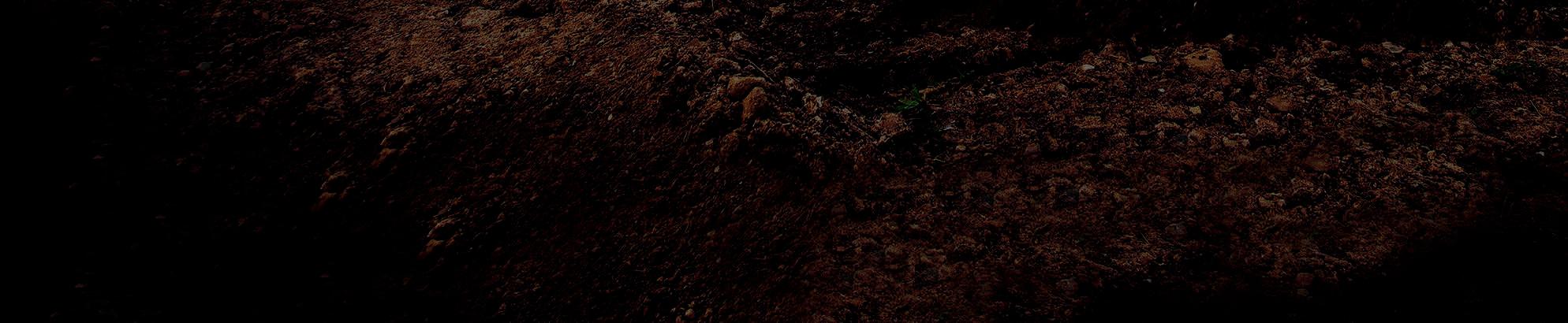
