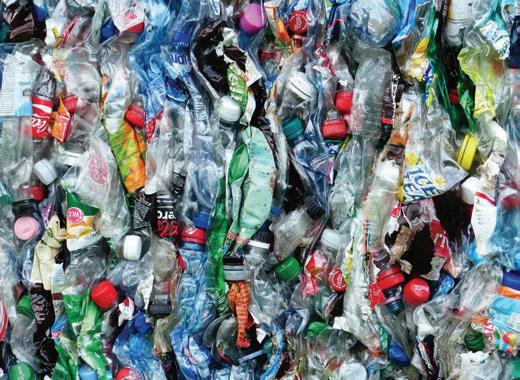
10 minute read
Recycling
Recycling Scaling up the recyclables
New technologies and programmes are the linchpin of the global plastic value chain to expanding recycling and enhancing the quality of recyclates for product applications in order to reduce global carbon emissions, says Angelica Buan in this report.
Advertisement
Adversity creates opportunities, and for the plastics industry, the pressure to increase plastic recyclability or contribute to plastic waste reduction has opened up opportunities to use recycled plastic content in their products. As a result, there is a growing preference for recycled plastics over virgin plastics in a variety of new applications in the packaging, automotive, and electrical & electronics industries, as well as a slew of favourable initiatives promoting the use of recycled plastics around the world.
Even so, odour and colour issues with recycled resins persist, sometimes making it difficult to find a comparable substitute for virgin resins. As a result of these limitations, the quality of recyclates needs assurance, with the use of recycled resins overcoming technical challenges.
Majority of plastics are made from chemicals and nonrenewable resources, and by 2050 will account for 20% of total global oil consumption Europe’s timeline for recycling stepped up
Globally, the volume of plastic waste is estimated to be 300 million tonnes/year and growing, but only 9% of all plastic waste produced is recycled. The majority of waste plastic is either incinerated (12%) or disposed of in landfills (79%). The majority of plastics are made from chemicals and non-renewable resources, and by 2050 will account for 20% of total global oil consumption.
The industry is now taking a different perspective on the situation: why not use the massive amount of waste and turn it into a resource?
Recycling of plastics is an important factor in the transition to a green, circular European market, according to Plastics Recyclers Europe (PRE), a Belgium-based organisation of European plastics recyclers. Technology advancements, product design, and an enhanced system of collection and sorting, as well as optimised recycling procedures, are key to transformation, PRE said.
It’s unsurprising then that Europe, as a driving force behind the circular economy agenda, is taking more aggressive steps with trade associations backing the statute for increasing to 30% the recycled content target for plastics packaging by 2030.
Members of the Brussels-based organisation are already working toward this goal, investing billions of euros on expanded high-quality recycled plastic supplies and technology solutions, it adds.
Meanwhile, PlasticEurope said that by 2030, it plans to invest EUR7.2 billion into chemical recycling, which it says will keep plastic waste out of landfills and incinerators. Significant amounts of recycled material with virgin plastic characteristics will be produced using this process. The technology complements mechanical recycling and can help Europe achieve a climate-neutral and competitive circular economy, it adds.
Utilising data for effective recycling outcome
Meanwhile, data collection is required to track the progress of the uptake of high-quality secondary raw materials. Thus, PolyREC, a non-profit organisation formed by PlasticsEurope, PRE, Petcore Europe, a European PET value chain association; and VinylPlus, an initiative by the European PVC industry, will monitor, verify, and report the plastics recycling and uptake data in Europe, using a common data collection platform (RecoTrace).
PolyREC will ensure traceability, transparency, and trust in recycled materials along the entire plastics value chain. The partners add that PolyREC’s establishment has been critical, particularly in the context of the Circular Plastics Alliance (CPA);
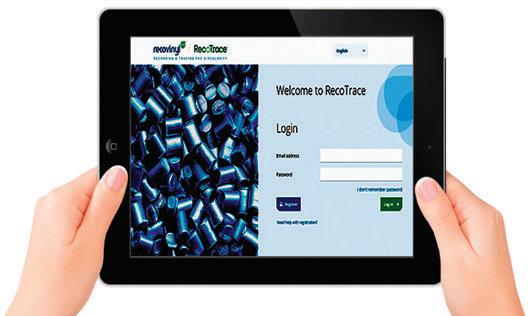
Recotrace is a common data collection platform that is utilised to track and report Europe's plastics recycling and uptake
of meeting CPA objectives, legislative traceability mandates, and industry-wide recycling targets.
PolyREC has recently been joined by value chain initiatives like the Polyolefin Circular Economy Platform (PCEP), Styrenics Circular Solutions (SCS), and European Manufacturers of Expanded Polystyrene (EUMEPS) to leverage the benefits of data systems in the polyolefins, styrenics, and EPS segments.
Project focuses on recyclate quality for packaging use
Meanwhile, a new project funded by the EU’s Horizon 2020 research and innovation programme and coordinated by Spain-domiciled research centre ITENE has been launched. Known as Merlin, which stands for increasing the quality and rate of multi-layer packaging recycling, it is made up of a consortium of 14 European partners and is expected to recover and recycle over 3 million tonnes/year of multilayer packaging waste in Europe.
Sorting technology providers, recyclers, research centres, social innovation experts, and end-users will collaborate on recycling solutions for rigid and flexible multi-layer plastic packaging waste from post-consumer/industrial sources, with the goal of designing cradle to cradle packaging solutions for the food packaging industry.
The EUR4.92-million project, which runs from 2021-2024, will implement solutions for sorting that will involve combining optical sensors, Artificial Intelligence (AI) and robotics; delamination by optimising depolymerisation and using solventbased processes; recycling, which will include repolymerisation and upcycling of polymers; and validation by developing rigid and flexible packaging solutions and demonstrating the circularity of the processes.
US accelerates recycling and recycled content uptake
In the US, increased recycled content in products is also being advocated to alleviate the load of discarded plastics and encourage recycling rates.
Recycling
Led by the American Chemistry Council (ACC), the initiatives will cover such targets as participation of all US manufacturing sites operated by ACC’s Plastics Division members in Operation Clean Sweep-blue. The latter is a programme launched with the Plastics Industry Association (PLASTICS) to assist plastic resin handling operations in achieving zero resin loss by 2020; 100% of recyclable plastics packaging by 2030; and 100% of reuse/recovery of plastics packaging by 2040.
Plastic resin producers plan to focus on six key areas to achieve these objectives, namely, designing new products for greater efficiency, recycling, and reuse; developing new technologies and systems for collecting, sorting, recycling, and recovering materials. Other initiatives include facilitating participation of consumers in recycling and recovery programmes; expanding the types of plastics collected and repurposed; as well as matching the plastic collection and repurposing efforts with goals.
Similarly, the ACC unveiled a five-point plan in July to accelerate the growth of recycling to reduce plastic waste and achieve a 30% recycled plastic content in packaging by 2030. It seeks a comprehensive national policy that will involve the participation of the entire plastics value chain. Furthermore, it states that chemical and mechanical recycling will be expanded, and an “American-designed” producer responsibility system for plastic packaging will be established. That being said, a number of firms have reportedly made voluntary commitments to utilise at least 25% post-consumer resin (PCR) in their packaging by 2025.
Paper-based composites not the answer to less waste Meanwhile, the ongoing criticism of plastic packaging has now led to quite a few companies replacing pure plastic packaging with packaging that contains paper.
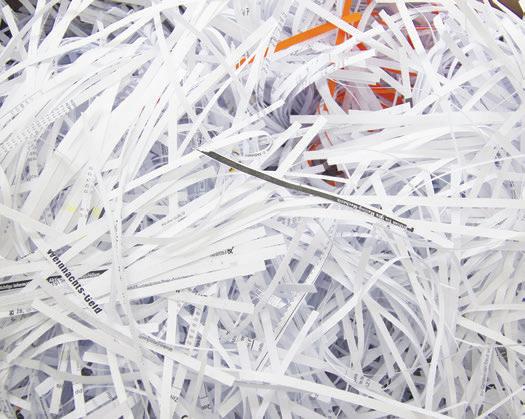
Recycling
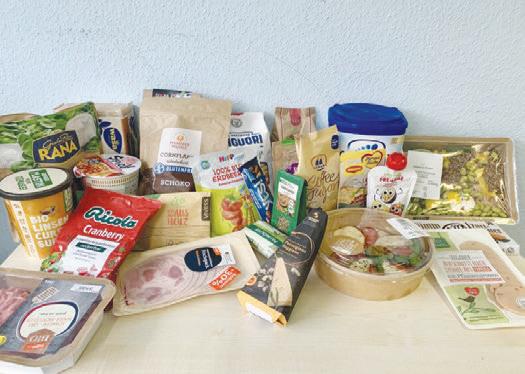
Composite packaging with paper and plastic is not deemed to be greener
This is apparently intended to make the packaging ‘greener’. As a result, composite packaging made of paper and plastic is increasingly replacing pure plastic packaging in shops. However, this is creating an increasing problem when it comes to recycling the packaging, as the German Central Agency Packaging Register (ZSVR) is now warning. This is because such fibre-based packaging with a plastic content can only be partially recycled at best.
Meanwhile, a study carried out for the German Association for Plastics Packaging and Films by packaging market research institute Gesellschaft für Verpackungsmarktforschung (GVM) reveals that paper-based composites tend to be detrimental to the circular economy.
For one thing, paper-based composites cause more packaging waste, as the GVM study shows. To package the same amount of product, the study found that paper-based composites require on average 40% more material than pure plastic packaging, thus generating a total of 25,000 tonnes more waste by 2025. At the same time, however, the amount of non-recyclable packaging is expected to fall by 19,000 tonnes because of the substitution of plastic packaging by paper-based composites.
The GVM study also finds fault with the fact that paper-based composites create problems when it comes to recycling, since only the fibre content of composite packaging is recyclable. This is usually over 70%. GVM says that the only option for the remaining plastic coating is energy recovery. It also points out that the recycling of the fibre content currently falls considerably short of the level that is theoretically recyclable, while the growing proportion of composites is increasingly causing problems for the recycling of waste paper. The authors of the study therefore consider it to be particularly regrettable if plastic packaging that is readily recyclable is replaced by composites.
But that is exactly what is already happening and is expected to increase further in the future: according to the study, it is forecast that around 60,900 tonnes of plastic packaging will be substituted by 85,500 tonnes of paper composites between 2020 and 2025.
All in all, they therefore conclude that substituting plastic packaging with paper-based composites does not represent progress and ZSVR criticises this trend towards composite packaging saying it is clearly at the expense of recycling. From an ecological point of view, ZSVR recommends that recyclable packaging alternatives made of mono-materials are clearly preferable to composite packaging.
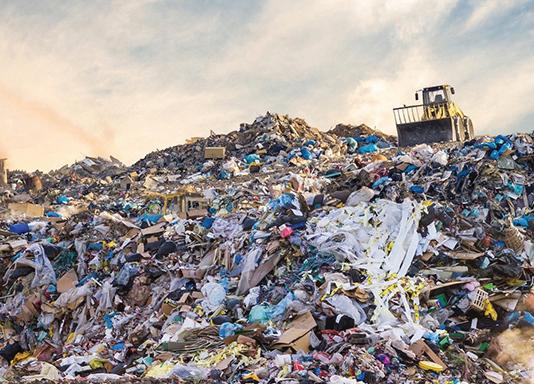
Tie-ups on recycling technology, circularity route
Meanwhile, US chemical company Eastman and multinational consumer goods company Procter & Gamble have teamed up, with P&G using Eastman’s Renew materials, which are produced with waste plastic and molecular recycling technologies, in select products and packaging.
Eastman is building one of the world’s largest plastic-to-plastic recycling facility
In addition, at its Kingsport, Tennessee site, Eastman is building one of the world’s largest plasticto-plastic recycling facility, which is slated to be completed in 2022. In order to create Eastman Renew materials, the molecular recycling facility will consume approximately 90,000 tonnes/year of landfill-bound waste plastic.
Elsewhere, RAMPF Eco Solutions and Spain’s Repsol have reached a mutual agreement that provides Repsol with exclusivity throughout Europe to develop and construct new recycled flexible polyol plants, produced from different sources and qualities of postconsumer PU waste.
This agreement follows Repsol’s announcement last March regarding the construction of the first PU recycling plant in Spain to produce circular polyols from end-of-life mattresses that will be operational by the end of 2022. The plant will be capable of processing over 2,000 tonnes/year of post-consumer waste.
Recycling
Recycled-content resins making their debut
Many resin makers are launching sustainable materials, such as certified renewable products with biobased content or with recycled material content, towards the path to a circular economy.
Chemicals firm Sabic has launched three automotive grades containing mechanically recycled content within the company’s Trucircle circular solutions. The new resins include T2E-3320EH PP compound, a high-flow, low-emission, talc-filled PP. An internal life cycle assessment (LCA) showed that the compound offers a reduced product carbon footprint of up to 24% compared to the corresponding virgin PP compound because it incorporates 25% recycled PP.
Sabic's three automotive grades from its Trucircle circular solutions contain mechanically recycled content


Ineos Styrolution’s first Novodur Eco ABS solution contains up to 70% recycled material. Boasting a balanced property profile, the resin is a sustainable option for automotive applications including centre consoles, radiator grills or mirror housings
It is estimated that 75 million broken windshields need replacing each year. This abundant supply includes thousands of tonnes of PVB, found in the inner layer of the glass, potentially bound for landfills. Instead, the outer glass is recycled and the PVB is reclaimed and reprocessed for various uses, including an alternative raw material source for polymers. Avient says its formulation expertise allows the supply of reprocessed, high-quality, non-toxic PVB to be upcycled into more sustainable TPEs with comparable properties.
Another resin, Xenoy T2NX2500UV resin, is an unfilled, UV-stabilised blend of PC and 21% recycled PET. While Xenoy T2NX5230 resin, a mineral-filled PC/PET blend, contains 16% mineral reinforcement and 29% recycled PET.
Meanwhile, US materials firm Avient’s latest additions to its reSound R recycledcontent thermoplastic elastomers (TPE) portfolio has been developed in collaboration with sustainable polyvinyl butyral (PVB) products maker Shark Solutions. Both new TPEs contain 25% PCR content from PVB reclaimed from broken automotive windshields and laminated architectural glass.
Avient’s new TPEs contain 25% PCR content from PVB reclaimed from broken automotive windshields and laminated architectural glass
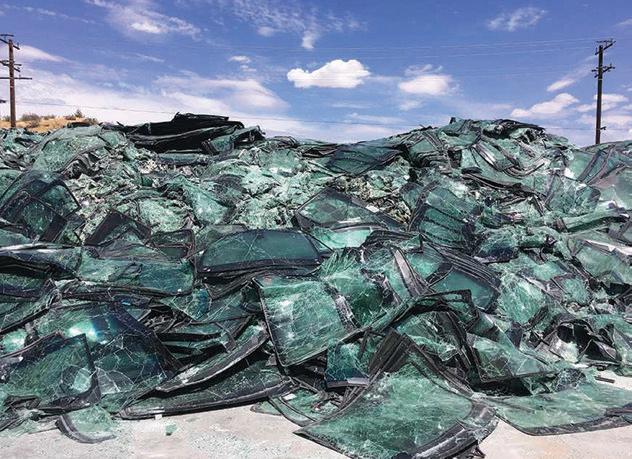