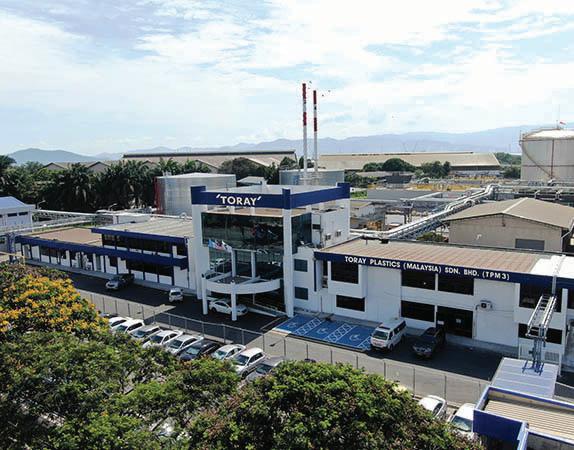
57 minute read
Engineering Plastics
Growth and sustainability with a new breed of plastics
Engineering plastics suit the design and structural innovation in a variety of industries since they are high-performance materials with greater features than traditional materials and commodity plastics, says Angelica Buan in this report.
Advertisement
Bullish market for engineering plastics
The engineering plastics market is massive, and it has remained unaffected despite the disruption caused by the Covid-19 pandemic. Indeed, market forecasts for engineering plastics remain bullish.
According to a Mordor Intelligence report, adoption of these high-performance polymers is expected to rise in major industries such as automotive, aerospace, building and construction, mechanical, and medical. The applications will be driving a market that is expected to grow at a CAGR of more than 6% from this year to 2026. As well, as the light weight trend spreads across major industries, engineering plastics will effectively replace traditional materials.
In today’s era, comparing engineering plastics with commodity plastics is like comparing oranges to apples.
Engineering plastics outperform common plastics such as polystyrene (PS), PVC, polypropylene (PP), and polyethylene (PE) in terms of mechanical and thermal properties, and have largely replaced wood and metals in a variety of applications due to their excellent weight-to-strength ratio, ease of manufacture, design versatility, and other characteristics.
Expansions on ABS growth
A recent report by Global Industry Analysts cited that the global engineering plastic market will reach 24.6 million tonnes by 2026, up from 19 million tonnes in 2020. One of the segments examined in the report, acrylonitrile-butadiene-styrene (ABS), is expected to grow at a 4.4% CAGR and reach 10.4 million tonnes by the end of the forecast period. Meanwhile, Brandessence Market Research’s report says the ABS market will be valued at nearly US$47 billion by 2027.
ABS is frequently utilised in electronic housings, automobile parts, consumer goods, pipe fittings, and toys, among other applications. Chemically and impact resistant, the opaque and amorphous thermoplastic has a low melting point. The material is relatively safe and has appropriate mechanical properties like toughness and rigidity. Citing the Brandessence Market Research report, the increasing adoption of ABS in the automotive sector, as well as in construction, electronics, and other industries, is a major factor driving the market forward. Having said the above, resin makers’ capacity expansion throughout this time has been both risky and strategic. Taking advantage of this market growth, Toray Plastics (Malaysia) Sdn Berhad (TPM) has commenced expanding its global production and distribution capacity of its Toyolac ABS resin transparent grade at its new facility in Penang, Malaysia. The new factory will increase production and distribution capacity by 75,000 tonnes/year to 425,000 tonnes/year. Toray Group currently produces 497,000 tonnes/year of ABS at its Chiba Plant in Japan. The company says it is expanding its global manufacturing, including its TPM plants, to increase sales in important Chinese and Southeast Asian markets, as well as meet increased demand in Europe, the US, and India.
Toray Plastics has expanded its ABS resin facility in Malaysia
Toyolac ABS grades include clear ABS grades with improved anti-static, scratch, and chemical resistance. According to TPM, they are lightweight, durable, and easily processable, with mechanical, chemical, electrical, and colouring properties.
Invista envisages nylon growth in China
The need for nylon (PA) 6,6 polymer has risen drastically in recent years. The estimated CAGR for nylon 6,6 through 2029 is approximately 2% globally and 4% for China*.
In view of this, Invista Nylon Chemicals (China) Co. plans to double its current nylon 6,6 polymer production at Shanghai Chemical Industry Park (SCIP) and signed a memorandum of cooperation with SCIP recently. Following a 40,000-tonne/year capacity increase in 2020, this new increased production, with an investment of US$230 million, will double the plant capacity to 400,000 tonnes/year and strengthen its integrated nylon 6,6 value chain in China. The new capacity will also enable Invista to more quickly respond to the growing demand for engineering plastics in automotive, electrical and electronics, and other application fields. To say the least, industry leaders are tackling the challenge of developing lighter car parts. As an example, roof frames built using Germany-based BASF’s Ultradur High Speed polybutylene terephthalate (PBT) material were developed in collaboration with Grupo Antolin, a Spain-based supplier of vehicle components. According to the firms, using Ultradur High Speed in the roof structure resulted in weight savings of up to 60%, compared to traditional solutions, and reduced carbon emissions.
The easy-flowing PBT is BASF’s first engineering plastic to be TÜV-certified for eco-efficiency. This new material’s good flowability also reduces the cost of producing injection-moulded components.
The partners’ newly created panorama roof is integrated into the car’s ceiling trim (called the headliner), which is composed of BASF’s Elastoflex E 3943/134, a light PU material. A structural bracket supports the actual sunroof opening in the headliner. This was previously made of heavy steel, but it has since been replaced with Ultradur PBT. The engineering plastic demonstrates mechanical qualities in addition to its high dimensional stability.
Meanwhile, compatriot materials firm Lanxess has developed a hollow-profile hybrid technology to help advance vehicle interiors with lightweight solutions. Metallic hollow profiles can be functionalised on ordinary injection moulding machines with plastic compounds using this new lightweight design technology.
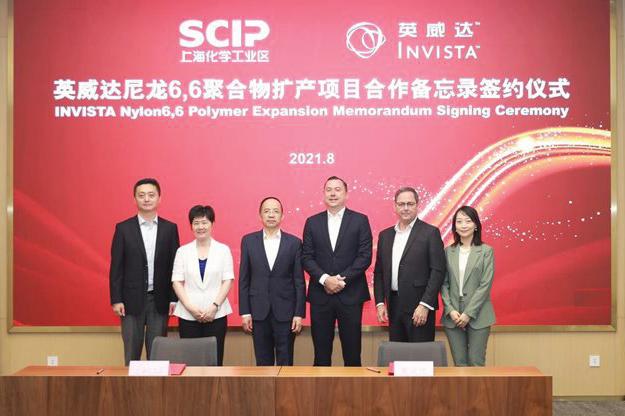
Invista plans to double its nylon capacity in Shanghai
The company expects China’s demand for nylon products will account for more than half of the total production and consumption of nylon in the Asia-Pacific region and is expected to become the world’s largest nylon consumer.
The additional capacity will support the development of engineering polymer, industrial and apparel segments, and satisfy the downstream application requirements for nylon 6,6 products and solutions, including stronger mechanical properties, higher temperature resistance, and higher heat resistance.
Automotive applications for fuel efficiency
The automotive and transportation industries employ engineering plastics to meet their needs for reducing vehicle weight to improve fuel efficiency, recyclability, and ease of processing. Thus, these industries are projected to be the largest end-use industries for engineering plastics.
EnginEEring Plastics
Lightweight and emission reduction roof frames have been made with BASF’s PBT
Lanxess has launched a new hollow-profile hybrid technology
Cross car beams, coupling rods, stabilisers, and seat elements are some of the potential applications in the automotive industry.
The hollow-profile hybrid technology is a step forward from the conventional plastic-metal composite technology (hybrid technology) that uses sheet metal. The new technology’s main advantage is that it allows processors to produce with short cycle times, which is typical of injection moulding in high-volume efficient production.
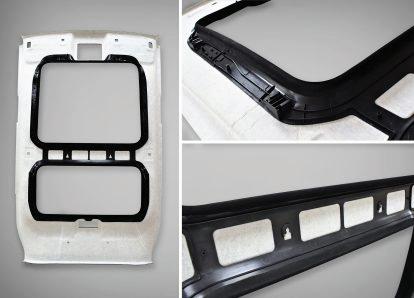
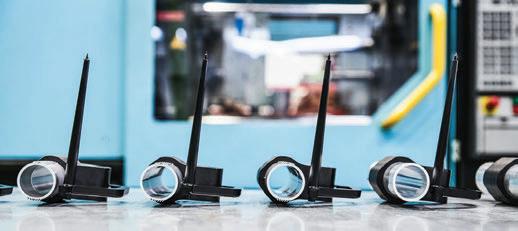
EnginEEring Plastics
Lanxess offers highly reinforced PA6 types for hollowprofile hybrid technology, such as the easy-flowing Durethan BKV60H2.0EF DUS060, which has a short glass fibre content of 60% by weight.
Lanxess evaluated how employing the compounds pay off in the construction of an automotive cross car beam, made 30% lighter than an all-steel construction. Typical load situations and component attributes, such as vibration behaviour and steering wheel stiffness in the direction of gravity forces, were calculated. Additionally, the component also demonstrates the technology’s potential for implementing cost-saving functional integration.
New PA6 grades for E&E sector
Meanwhile, in the E&E industry tests are performed on materials to compare their tendency to resist ignition, selfextinguish flames and to not propagate fire via dripping. Glow wire testing is one of the most relevant indirect flame methods where a non-flaming heat source is applied to the material sample. Specifically, the glow wire test is used to simulate heating effects that may arise in malfunctioning electrical equipment caused by an overloaded connection or component that is overheating.
PA6 and PA66 supplier Domo Chemicals, which acquired the Technyl brand this year, says it is driving materials development to meet evolving market needs and is working with customers to select the best base materials for specific applications. not an easy achievement for a flame retardant solution with a glow wire resistance of 850°C down to 0.8 mm, according to Andrea Rizzo, Sales Manager at Domo.
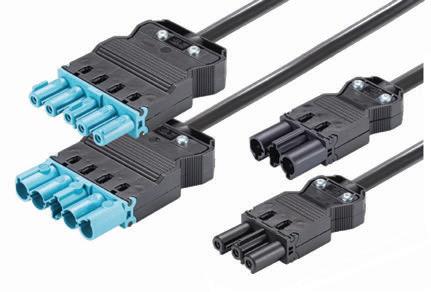
Sustainable solutions line-up for engineering plastics
A key player in the engineering plastics sector, Ineos Styrolution has introduced the first post-consumer recycled Novodur ECO specialty ABS solutions and Novodur ECO High Heat grades being the result of mechanically recycled post-consumer waste.
The new grades, the Novodur ECO and the Novodur ECO HH will contain up to 70% and 40% recycled material; respectively. The new materials, which are available in standard colours, offer identical mechanical properties as their virgin equivalents making them drop-in solutions for application developers. The new Novodur ECO HH solutions offer a balanced property profile making them sustainable options for automotive applications including centre consoles, radiator grills or mirror housings.
Domo Chemicals’s nylon material was selected by German company Wieland Electric for its installation connectors
Recently, German company Wieland Electric selected Domamid 6LVGT85 for its installation connectors GST18i3 (3-pole) & GST18i5. These make up part of the gesis pluggable electrical installation system for buildings, a flexible, future-oriented, and economic product range that meets all the requirements of modern energy distribution.
Certified to comply with the product specifications for these installation connectors Domo’s material is a low viscosity grade for injection moulding, certified V2 at 0.75mm with a UL Yellow card, matching the PA66 previously used for the housing shells, and top and bottom parts of the product. The property profile with good flow and demoulding characteristics, as well as good particles crystallisation, enables an optimised production process.
The PA66 has a glow wire resistance of 850°C on both test specimens and moulded parts, which were the specific values requested on the material characterisation.
In this case, the PA66 substitution has provided multiple benefits as good flow and fast crystallisation have also resulted in better processability and cycle time reduction,
Meanwhile, South Korean chemical manufacturer LG Chem has teamed up with Veolia R&E, the country’s largest recycler of methyl methacrylate (MMA), to produce ABS from recycled material. MMA is an unsaturated ester with a variety of applications in polymer manufacture, including adhesives, coatings, composites, and industries such as aerospace, automotive, marine, and transportation.
LG Chem has gained the opportunity to commercialise low-carbon transparent ABS based on chemically recovered MMA, after the two firms signed an MOU. The two companies will collaborate to optimise processing and conduct cooperative R&D development to improve the recycled MMA quality.
Veolia R&E, a division of the Veolia Group in France, developed the world’s first pyrolysis-based process for recycling discarded artificial marbles into MMA.
LG Chem is considering using the recycled MMAcontent transparent ABS in its eco-friendly LETZero product line for distribution to global home appliance and IT firms.
Moreover, LG Chem has also collaborated with another South Korean company, TK Chemical, to work together to produce environmentally friendly biodegradable materials, with plans to build a PBAT (poly butylene adipate-coterephthalate) production line that will begin operations in the second half of 2022. TK Chemical, a subsidiary of the Samla Midas (SM) Group specialises in synthetic fibres.
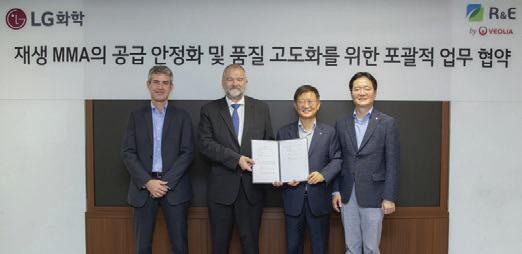
LG Chem has tied up with Veolia R&E to produce ABS from recycled methyl methacrylate (MMA)
The era of human/robotic collaborations
Automation
With human workers and robots beginning to work together in tandem, automation for output-intensive industries has come of age, says Angelica Buan in this report on Industry 5.0.
Modern twist to industrial revolution
Industrialisation has increased overall economic output, creating more jobs and raising living standards. Obviously, the industrial revolution aims to advance technology, socioeconomics, and culture – but at what cost? Workers were displaced by migration throughout the early stages of industrialisation, and they endured low wages, long hours of toil, and exploitation.
The term “industrial revolution,” which was once used to describe economic and industrial developments in Europe and the US between the 18th and 19th centuries, has been given a modern twist. As demand for goods begins to exceed output from conventional machines, the second wave of the industrial revolution aims to boost productivity and efficiency with technologies.
Moreover, the cyborgification of industries, in response to the skilled labour shortage, has sparked an uncanny valley fear that a robot will outperform a human worker. Newer generation technologies, such as collaborative robots or cobots, are, nevertheless, reducing human hostility towards them. It’s only a matter of time before a peaceful coexistence between humans and robots becomes a reality.
Remedy to close the gap in skilled labour shortages
The generational skilled labour shortage has been a barrier to achieving full industrial ambitions. For years, unemployment has been at an all-time high, yet thousands of skilled jobs have gone unfilled, owing to a lack of training and experience, to name a few factors.
The use of robots, artificial intelligence (AI), and smart machines became increasingly important in the latter stages of the technologicallydriven industrial revolution
The use of robots, artificial intelligence (AI), and smart machines became increasingly important in the latter stages of the industrial revolution. This, however, led to the perception that such technologies will eventually infiltrate manufacturing floors, render human labour obsolete, and disenfranchise humans – much like in sci-fi movies.
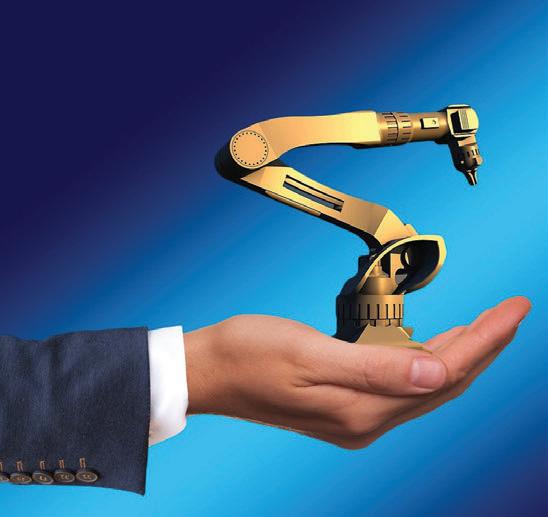
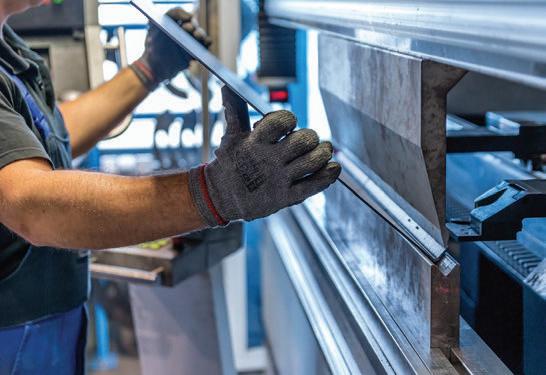
Lack of recruits with proper training and technical experience creates a chasm in the skilled labour market
The recent pandemic has been a disruptive factor to the labour climate. Although deemed to be only a temporary situation, the pandemic has caused an employment crisis with many businesses ceasing operations, or reducing capacity. Indeed, the pandemic has put to the test not only the manufacturing sector’s resiliency, but also its ability to recover.
In the US, the manufacturing industry lost more than 500,000 jobs in 2020 during the pandemic, according to findings by Deloitte and The Manufacturing Institute, which polled an online research of more than 800 US manufacturers across all sectors, between December 2020 and February 2021.
The Deloitte study revealed that the pandemic cost the US manufacturing industry 1.4 million jobs, but 820,000 of those jobs were rehired by the end of 2020.
Automation
The irony, according to this report, is that there were roughly 500,000 positions available, mostly for qualified people that could not be filled. By 2030, the US manufacturing industry is expected to have 2.1 million skilled labour vacancies.
This opinion is also echoed by US advocacy group National Association of Manufacturers (NAM)’s recent Manufacturers’ Outlook Survey, which had 453 responses in August. Recruiting and maintaining qualified employees, as well as supply chain and logistical difficulties, and healthcare expenses, were cited as top challenges by respondents.
Meanwhile, the expanding skilled labour gap is being exacerbated by digitalisation, automation, and an ageing population.
In a recent article titled “Creating pathways for tomorrow’s workforce today”, Deloitte stated that the rapid digitalisation of the manufacturing industry will almost certainly continue to reshape human labour, adding that it will be a challenging factor over the next ten years.
The reason for this is that the skills required to perform jobs in a smart factory will most likely differ from those required today. Unfortunately, many of these talents are lacking in today’s manufacturing workforce and if this issue is not addressed, vacancies will increase, affecting productivity, innovation, competitiveness, and the GDP.
Automation as a disruptive force
Worker safety and efficiency remain central to technologically-driven industrial shifts. Worker safety has improved as a result of automation. Furthermore, the introduction of AI-connected technologies and robotics has improved manufacturing efficiency and productivity, particularly in major industries such as the plastics industry, where manufacturers are focused on lowering costs while increasing capacity and output.
The application of software-integrated machines that either stop or alert the operator when it detects a defect or self-adjusts to ensure that processes are not disrupted is on the rise. These machines allow for greater precision and less wastage on the factory floors.
While machines and robots will never completely replace humans in the supply chain, they help relieve employees of redundant, highly technical, and physically demanding tasks while assisting organisations in improving their bottom lines.
Thus, does automation create more jobs? According to an article published by Forbes and World Economic Forum (WEForum), automation will result in a 58 million increase in employment. Automation is anticipated to turn two-thirds of occupations into higher-skilled jobs, while the remaining one-third will become lower-skilled jobs.
Cobots in the plastics industry
The plastics industry, which every year has new technologies being launched, has also borne the brunt of a gap in skilled workers. While robots are generally used to augment this shortage, especially in areas that require precision and consistency, they do not necessarily disregard human interaction.
Cobots are robotic assistants to human workers that help them be more productive. They are less expensive than traditional industrial robots used for automation, costing less than a quarter of the price. They are safe to use and are equipped with sensors and other devices to ensure that they behave appropriately, particularly when working in close proximity to humans. In many industrial settings, cobots work alongside humans, but they accomplish tasks independently or sequentially.
Industrial robots are mostly used in injection moulding applications in the plastics sector, automating processes without requiring human interaction. They are required in environments where human error is to be avoided.
Cobots, on the other hand, are designed with human safety in mind (unlike traditional industrial robots) and to function in close proximity to employees, preventing workplace risks by being disabled with just a light touch. For industries, cobots can increase productivity in the manufacturing line and the ability for businesses to expand.
It can be recalled that German multinational chemical company BASF, in 2017, showcased its prototype cobot for industrial use, made by Siasun, one of China’s largest robotics manufacturer. The cobot, showcased at a Guangzhou-held plastics event, is built with BASF’s Elastollan thermoplastic polyurethane elastomer (TPU), Ultramid glass fibre-reinforced PA and 3D-printed PA6. The partnership is part of BASF’s Trio project, which brings together prominent designers and brand owners.
BASF and Siasun cooperated on an industrial cobot prototype made of Elastollan TPU and Ultramid PA

Automation
According to BASF, its Elastollan TPU and Ultramid PA are easier to process than standard materials and allow for more colour and decorating options, while allowing for flexible manufacturing. Because cobots are only employed when they are needed, a lightloading cobot will be easier and faster to move about the manufacturing site.
Sepro’s Visual Control System will be integrated with Universal Robots’ cobots as part of a collaboration
Meanwhile, Swedish industrial robot supplier and manufacturer ABB offers its range of cobots, which feature the speed, robustness, and precision of an industrial robot while also having the safety features and ease of use of a cobot. Early this year, ABB introduced its CRB (Collaborative Robot) 1100 SWIFTI, which combines a payload of 4 kg and reach of up to 580 mm; and GoFa CRB 15000. The latter features intelligent sensors in each joint to support close human and robot collaboration, enabling reach and speed for payloads up to 5 kg. These new cobot versions of ABB’s IRB 1100 industrial robot joined the YuMi and Single Arm YuMi (introduced in 2015) in the company’s cobot portfolio for applications ranging from less than 0.5 kg to 5 kg. According to ABB, SWIFTI has a maximum Tool Centre Point (TCP) speed of more than 5m/second, which is more than five times faster than other cobots in its class and comparable to industrial robots. Easy
BASF adds that cobots made with its elastic to use and install, safe working zones for the robot material solutions allow for good insulation and can be configured using SafeMove’s simple fast setup elastic properties, providing greater shock absorption tools, such as the SafeMove Configurator App on the and thus making flexible manufacturing safer as well ABB FlexPendant. Users can programme the cobot as more user-friendly for humans. either via a clip-on lead through programming device,
Similarly, cobot innovation is the focus of a tie-up or ABB’s new Wizard easy programming software. between French manufacturer of robots Sepro Group Both SWIFTI and GoFA have capabilities that and Universal Robots (UR), a Danish manufacturer allow them to function alongside humans without the of smaller industrial collaborative robot arms. need for physical barriers or fences, saving both space
Sepro’s Visual Control System will be integrated and money. with UR’s cobots as part of the agreement. Sepro Thereby, allowing a robot and a human to work created the Visual Control Platform specifically for together in the same space and on the same tasks, robots used in injection moulding equipment and without sacrificing speed or safety, results in is featured in all its products, including co-branded maximum flexibility and efficiency; and above all, lines, with the same user interface of any robot types. harnesses the combined power of a human mind and
Sepro adds that it will be able to offer a machine. comprehensive range of automation solutions to injection moulders as a result of the new cooperation. Cartesian robots, six-axis articulatedarm robots, and now cobots are all part of this portfolio, according to Sepro. It added that cobots, like the sic-axis robots, are well-suited to peripheral operations that are in high demand in the plastics industry.
The integration also allows processors to build safe, open configurations for a variety of processes, such as peripheral operations or advanced automation cells, Sepro furthered. Both the partners’ solutions enable faster process creation and installation, resulting in easy to deploy and testing of post-processing operations and ABB”s GoFa CRB 15000 features intelligent sensors in each joint and turn-key automation systems. enabling reach and speed for payloads up to 5 kg
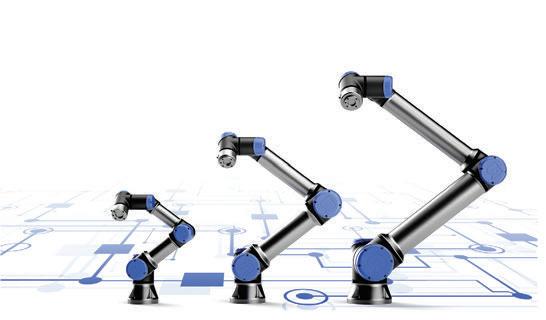
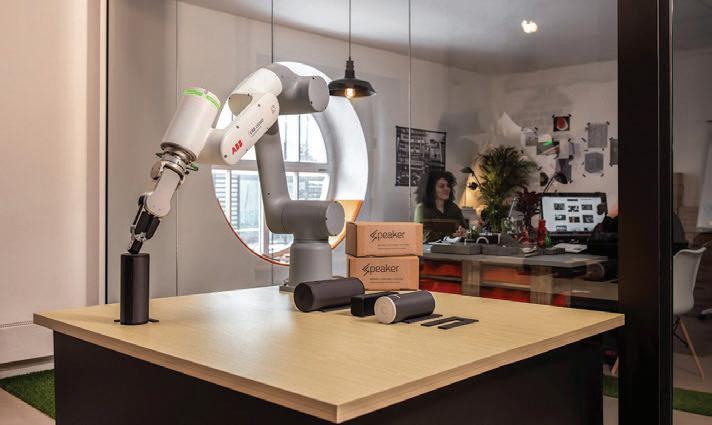
Advertorial
LSR Technology Conference 2021: a conference jointly organised by SIGMASOFT ® , Arburg, Momentive & Ewikon
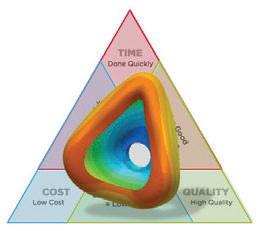
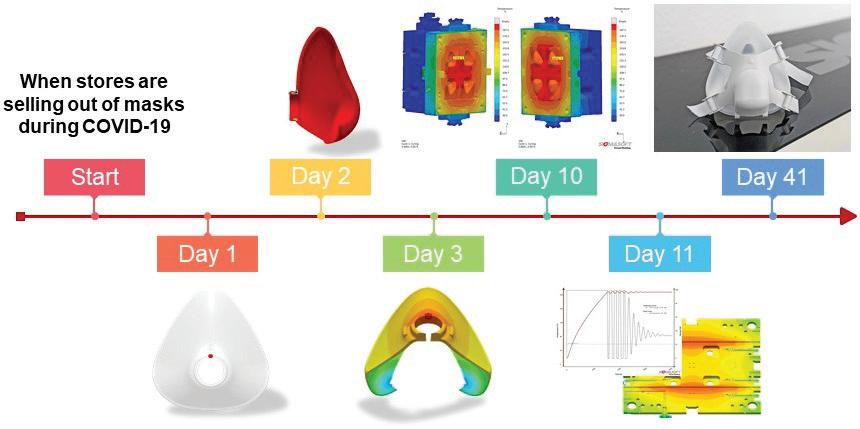
With the focus being set on trends, technology advancements and challenges in many aspects The case study he showcased in the conference was about an initiative to help fight the spread of the of liquid silicone rubber (LSR) part production, coronavirus – it focused on a face mask production SIGMASOFT® and its partners held a LSR Technology project whereby 15 companies partnered together and Conference on the present & future of LSR injection managed to get a the product ready from scratch to series moulding, material innovations, virtual moulding and production in only 41 days. efficient production solutions. The presentations were aimed at presenting invaluable insight to the industry players, ranging from product and mould designers, polymer end users, moulding and tooling experts, to QA/QC, CAD/ CAE specialists or R&D personnel.
Although the focus of the conference was on the Asian market, it attracted a global crowd. There were attendees from a total of 29 countries and more than 300 participants in this virtual conference that was held on 25 August 2021. The invited keynote speakers were subject-matter experts from the LSR production chain with years of experience and they shared the latest advancements and trends in the LSR arena.
Uwe Haupt from German machine maker Arburg had the honour of starting as the first presenter and conveyed how Arburg, as one of the world’s leading manufacturers of high-end machine technology for plastic processing, has significantly influenced the development of plastic injection moulding worldwide since the 1980s. “One of the reasons is that Arburg was the first company to actively work together with material development companies and mould producers to develop the equipment for the process that has shaped our reputation as a pioneer in the injection moulding technology arena,” said Uwe Haupt.
As the first presenter of the conference, he covered the basics of LSR materials, present and future, as well as the trends in LSR injection moulding. In his presentation, he shared how to achieve better control and monitoring of the process, new trends using micro screws for reproducible dosage for extremely small shot weights and how electric drives for LSR processing from Arburg can help to lower overall energy consumption, generate lesser noise while achieving higher precision and better stroke and pressure resolution.
Meanwhile, SIGMASOFT® has established itself as one of the technology leaders in polymer injection moulding simulation. Devadass Vimalanand from SIGMASOFT® presented on how the software was specifically developed to overcome today’s challenges for development, mould design, production and optimisation of the injection moulding process.
Sequence of events of the face mask production project - from scratch to series production in only 41 days
“With a complete set of the mould details, we completed the project within a day and obtained results for thermal balance, filling, cooling behaviour. This is one of the advantages of using the SIGMASOFT® Virtual Molding Approach, apart from the accuracy. Predicting the real thermal behaviour is the first step to optimise the cycle time, which is the strength of SIGMASOFT® Virtual Molding,” said Devadass Vimalanand.
Golden triangle of project management Level of simulation in different stages of product development
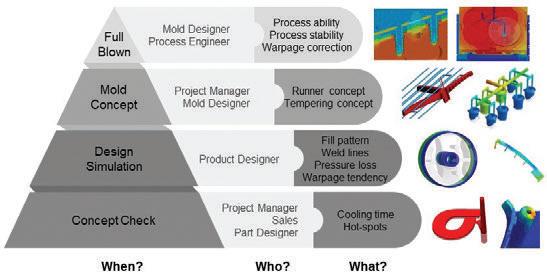
The third presenter, Vivian Tian from Momentive, a global leader in silicones and advanced materials, delivered her presentation on “Innovation LSR”. Her presentation gave insights on how Momentive has created solutions for a sustainable world in the last 80 years as the industry leader for silicone innovation. At the same time, she also shared about the processing benefits of the soft-hard materials such as self-lubricating LSR and self-bonding LSR, and how these innovative materials enable flexibility in the designs that have become valuable in supporting and improving our everyday lives.
The last presentation was about the scientific investigation of the cold runner technology for LSR from Ewikon, a well-known supplier in hot and cold runner technology, founded about 40 years ago in Germany. Stefan Bernhard, who has trained and worked as a toolmaker since young, showcased the innovative COOLSHOT cold runner technology that utilises technologies and know-how from the hot runner sector to improve the LSR injection moulding process.
Rounding up the conference, General Manager of MAGMA Engineering Asia-Pacific, Jan Eilers, said: “Due to the Covid-19 pandemic, face-to-face meetings are delayed to an unknown date. We know there will be a day when most will be back in the office and it will be possible again to have in-person meet-ups and seminars with bigger crowds, but until then, businesses must make the most out of the current situation. To share the ever evolving technology with the industry even during these times is the motivation behind us organising this virtual conference.”
He added, “Thanks to all our partners for bringing their expertise and experiences into this conference and to the attendees for engaging in the fruitful and interesting presentations and Q&A sessions in the live-broadcasted LSR Technology Conference 2021.”
For the full conference programme, please scan here to find out more or follow our LinkedIn to join our upcoming events.

PET Recycling
PET recycling developments
PET recycling in India on the growth
Polyethylene terephthalate (PET) is a high-value material that is on course to take over a key function in the plastics industry’s path toward a circular economy. PET plays an ever more important role in recycling, due to the large volume of packaging materials in use today. PET is a very highvalue material, possessing extremely good properties for reprocessing. It is continuously expanding use in single and reusable bottles, as well as its recovery via deposit systems, add to its value. Correspondingly, it can be lucrative for companies to focus on PET recycling.
Meanwhile, according to the United Nations Development Programme, India generates approximately 15 million tonnes/year of plastic waste but only one fourth is recycled. While more than 10% of this plastic waste is PET and up to 90% is recycled, the recycled material is generally not high quality, resulting in low levels of circularity.
Leading the way, Indian plastic recycling and waste management company Srichakra Polyplast (Srichakra) has officially commissioned its upgraded facility, the first of its kind in India to produce food-grade quality rPET pellets. The company has also commissioned its new polyolefins recycling facility that can produce deodorised bottle-tobottle grade quality polyolefin pellets. The company has invested more than US$10 million to strengthen its recycling capabilities, which allow it to offer recycled plastic to customers in India and global markets such as Europe and the US.
Srichakra says its world-class facility features US Food and Drug Administration (FDA)-approved technology provided by Austria’s Starlinger, which expands the company’s capacity to become the largest solid state polymerised (SSP) PET processor in India. Srichakra adds that it can produce food-grade quality PET pellets, which can be used to produce food and beverage packaging such as water, carbonated soft drink and juice bottles as well as takeaway containers; and high quality deodorised polyolefin pellets, which can be used in home and personal care product packaging such as lotion, shampoo and detergent bottles.
Circulate Capital invested in Srichakra in December 2020 and this has allowed Srichakra to grow its team two-fold to employ 200 workers from local communities. It has also provided upskilling opportunities for employees through training with the Starlinger technology and team.
Bottle-to-bottle recycling with Coperion systems
PET flakes can now be processed without pre-drying into pellets using German machine maker Coperion’s ZSK twinscrew extruders. Next they are condensed in the SSP (Solid State Polycondensation) reactor, and reprocessed back into bottles again with the quality of virgin material.
PET recyclate manufactured using this innovative process has received approval from the FDA for food-contact uses. Thanks to the highly efficient plastification within the ZSK extruder, Coperion systems for this bottle-to-bottle recycling process achieve throughput rates between 2 and 8 tonnes/hour, therefore recycling companies profit from very high product quality, reduced operating and logistic expenses as well as from energy cost savings up to 30% in comparison to conventional PET recycling methods.
Before PET can be reprocessed, it must first be shredded to flakes and then cleaned. Ordinary technologies require pre-drying, crystallisation or agglomeration of the PET flakes following washing. However, using the specialised technology from Coperion, the shredded PET can be fed directly into the ZSK twin-screw extruder and compounded.
The shredded flakes are reliably fed into the ZSK extruder using high-accuracy SWB (Smart Weigh Belt) feeders or gravimetric feeders from Coperion K-Tron. In addition, other regrind materials, new materials, or mixtures can be added. Melting, intensive devolatilisation, and complete homogenisation take place in the ZSK process section before the melt is transferred via a gear pump and filter with an automatic screen pack changer to a strand or underwater pelletizer for pellet production.
Pellets are then condensed in an SSP reactor. The pellets’ quality meets the requirements of virgin material. They have received FDA Letter of Non Objection which certifies that they meet the standards for food-safe plastics and thus, can be processed into bottles once again.
With this direct processing of PET into bottles, recyclers profit particularly from the very high end product quality. Product handling in the bottle-to-bottle process is very gentle. The residence time in the ZSK extruder is very short and dispersion is very good. The ZSK extruders’ high torque enables processing at low temperatures and with almost no viscosity loss. ZSK extruders’ self-cleaning enables rapid recipe and color changes. Thanks to the ZSK twin screw extruder’s very good devolatilisation options, volatile components such as monomers, oligomers, and water are reliably removed and channeled away from the exhaust flow in suitable separators before discharging the process section.
Alongside the high product quality, direct processing of PET flakes offers further advantages including reduced operating costs and energy consumption as well as lower logistic expense.
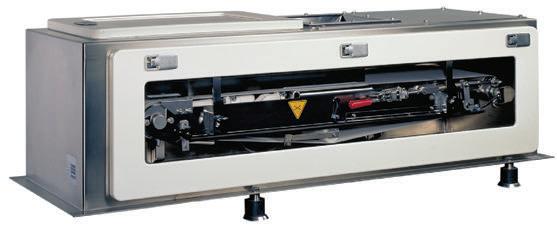
Coperion offers an economical and FDA-compliant system for recycling of PET flakes
PET Recycling
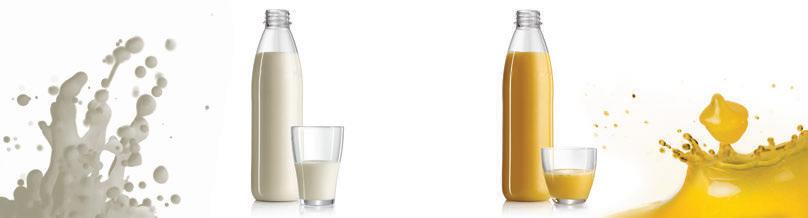
New melt filters cater to higher outputs
Elsewhere, Ettlinger, a member of the Maag Group and a manufacturer of continuously operating melt filters, has unveiled a new generation of ECO products for use in PET recycling. The new features take into account the need for systems with a higher product output and are initially available in sizes suitable for medium-sized recycling lines. The new performance enhanced ECO 350 replaces the former ECO 250, while the new ECO 500, capable of achieving capacities of up to 4,000 kg/hour, replaces the former ECO 250 Twin. The ECO 200 completes this range. Ettlinger’s melt filter technology is based on the principle of selfcleaning with a continuous flow of melt from the outside to the inside of a rotating, perforated drum. A scraper removes the contaminants that are held back on the surface and feeds them to the discharge system. Just like the ERF filters, which are designed for higher contamination, the new ECO filters also have a modular structure, thereby providing a wide range of options for adjusting the filter properties to the respective task.
A new innovative system facilitates an even higher concentration of contaminated discharge, which, in turn, further decreases the already low loss of PET melt, says Ettlinger. Better access to the scraper system reduces the amount of time needed by the operator for maintenance and replacement tasks. The discharge now exits via the front side of the ECO filters, which is generally easier for the user to access.
The new designs combine screen sizes up to 60 microns with a minimum loss of PET through the discharge.
The ECO melt filters are designed to process very low viscosity polymer feedstock (mainly PET and PA) and to facilitate the efficient filtration of contaminants such as paper, wood, aluminium, silicone, etc.
Moreover, the closed discharge system prevents the occurrence of black specks. For this reason, the classic application for ECO melt filters is extrusion systems where PET bottle flake is converted into food packaging films, packaging tape and fibres, as well as PET repelletising and compounding processes.
ECO melt filters are suitable
for single-screw or twin-screw extrusion lines, irrespective of the pelletising system or other downstream units, and can achieve outputs from 150-4,000 kg/hour.
Krones/Alpla work on returnable PET bottle
In the beverage packaging market, returnable PET containers currently play a rather small role. Now, German beverage and food industry equipment supplier Krones and packaging firm Alpla are working to develop a returnable PET container that will provide an optimal environment for sensitive ESL (Extended Shelf Life) products such as juices and milk in the cold chain. The partners’ dedicated particular attention to the container cleaning process because “PET is less heat-resistant than glass,” explains developer Ines Bradshaw. “So we had to find a way to ensure both a high level of microbiological safety and a high number of use cycles while cleaning at lower temperatures.” To obtain an objective and meaningful base of data, Krones’ development plant for washing technology in Flensburg carried out an elaborate series of tests, analysing the interaction of different bottle designs and cleaning processes. “The tests provided us with a very clear picture of the respective thermal, chemical, and mechanical factors,” says Bradshaw. “Among the findings: With the right combination of parameters – especially lye concentration, temperature, additive, and mechanical impact – temperatures around 60°C are sufficient to reliably remove even dried protein, fat, and Ettlinger’s new ECO 500 melt filter starch contamination from the containers.” achieves outputs of up to 4,000 kg/hour A direct comparison of returnable PET and returnable glass brought to light another interesting discovery that over various cleaning cycles, the alkaline cleaning medium visibly roughened the surface of the glass bottle, whereas nothing comparable could be observed with the PET containers. “For the filling of sensitive beverages in particular, consistent container quality can be an advantage that should not be underestimated,” notes Bradshaw. Microbiological tests are currently being conducted to definitively establish whether the technology is safe. Initial results confirm the observations made thus far: “Microbiologically, PET bottles that had gone through 25 cycles could not be distinguished from new ones,” says a very pleased Bradshaw. With this proof of concept, the project has reached an important milestone and is now ready for the next major step, with preparations underway for the technical field test.
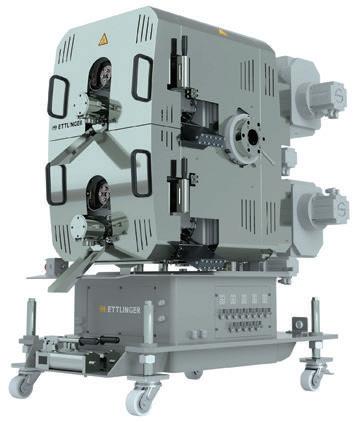
Krones/Alpla have jointly developed a returnable PET container that provides an optimal environment for sensitive ESL (Extended Shelf Life) products such as juice and milk in the cold chain
Automotive
Smart functions integrated with DirectCoating coated parts technology
Car manufacturers and their suppliers face the challenge of integrating smart functions such as display and ambient lighting and touch control, in addition to a wide range of visual and haptic surface properties.
Above all, the aim is to manufacture durable products cost-effectively to achieve broad acceptance in the industry. The goal is car interiors that can easily serve as a lounge, workspace and driver cockpit. In this way, an environment can be created in the car that combines comfort and infotainment with a feeling of safety.
Thus, to allow more design freedom and functionality in car interiors in a cost effective manner, German materials company Covestro worked with a team of three industry partners: coatings specialist Votteler Lackfabrik GmbH & Co. KG, laser texture specialist Reichle Technology Center and pearl effect pigments manufacturer Merck KGaA.
It developed what it says is an effective concept for the production of interior parts with seamless, intelligent surfaces using Covestro’s DirectCoating technology. The coated component is produced in two steps using a polyurethane reaction injection moulding (PU-RIM) process. Puriflow paint systems from Votteler Lackfabrik enable surface properties such as good scratch resistance and a selfhealing effect, but also a feel that ranges from soft leather to hard metal. In implementing the solution, Votteler drew on the manufacturing expertise of Reichle, which operates Europe’s largest laser texturing site. The company provided laser-textured PU-RIM moulds for the project.
Covestro, meanwhile, supplied process technology know-how, coating raw materials from its Desmodur and Desmophen ranges without solvent additives, and Makrolon and Bayblend polycarbonate plastics. Effect pigments from Merck can be used to achieve various colour and transparency effects.
In Covestro’s DirectCoating process, the plastic substrate is first produced in an initial cavity by injection moulding. The resulting part is then transferred to a second, minimally larger mould.
The cavity between the substrate and the laser-engraved RIM mould corresponds exactly to the desired volume of the coating that is injected there. This creates a coated precision part in just two steps. It requires little rework and is highly resistant to chemicals and daylight, adds Covestro. DirectCoating also offers advantages over conventional coating methods, including a shorter and faster process, no overspray and no need for a separate drying step.
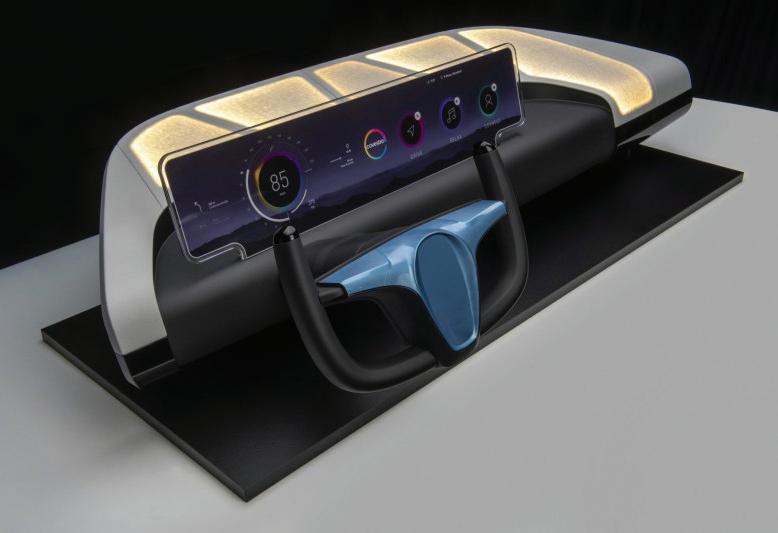
A cooperation between Covestro, Votteler, Reichle and Merck has resulted in the development of dashboards for car interiors being designed with comfort and the addition of infotainment With the help of Covestro’s DirectCoating technology, automotive interior parts with seamless, smart surfaces can be produced quickly and effectively
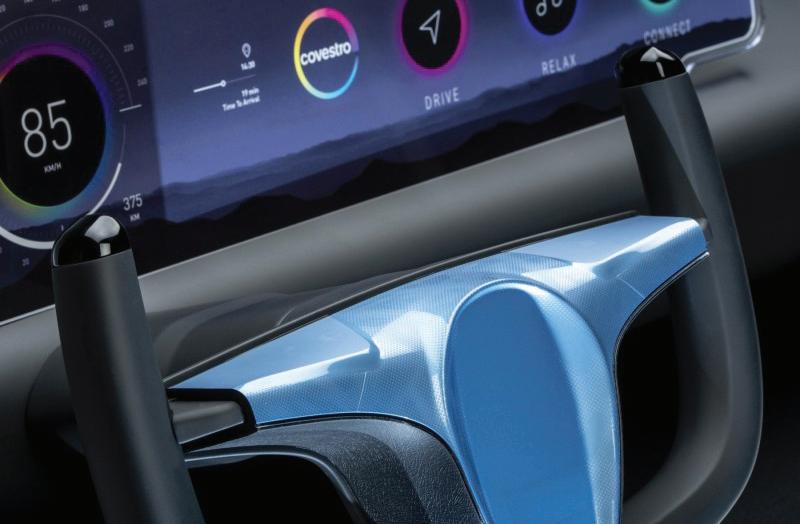
Consortium develops lower-cost and lighter battery for e-mobility
Although millions of electric cars and plug-in hybrids from many manufacturers are already on the road, there are still no generally recognised standards for the individual components in terms of service life or materials used. Moreover, the vehicles themselves are under rapid development.
One way of increasing the range of electric cars is by improving battery storage capacity and through efficient energy recovery. A second approach is to reduce the weight of the individual components, in order to reduce the energy needed to overcome driving resistance (tyre rolling, inclination, and acceleration). The effect of weight reduction on the efficiency of the drive depends on the propulsion strategy of the electric vehicle.
Thus, a consortium consisting of Lorenz Kunststofftechnik, Forward Engineering, Evonik, LION Smart, Vestaro, and Minth (the European headquarters of Chinese automotive supplier Minth Group) has developed a solution to help improve efficiency through lightweight construction.
In late 2019, work started on a brand-independent, lowcost battery housing solution in different sizes for electric vehicles. The result of the cooperation was a significant weight reduction of the battery by about 10% over other commonly
Automotive
A consortium has developed a lower-cost and lighter battery concept for e-vehicles
used material combinations, without sacrificing any mechanical properties. In addition, the glass fibre-reinforced epoxy SMC – purpose-developed for the battery housing – meets all fire resistance requirements and is easy to work, even with complex geometries. The entire concept has been tested and shown to be suitable for series production and is said to be safe even under extreme conditions.
Components used in lightweight construction for hybrid and electric vehicles, such as battery housings, must not only be low in weight, but also exhibit high rigidity and strength. Carbon fibre-reinforced SMC materials can be used for this purpose, but they are very expensive and typically non-recyclable. Beyond that, there were few available materials with the necessary attributes, as they were either too heavy or had insufficient mechanical strength.
For the battery housing, Evonik’s Vestalite S epoxy hardener was used to develop a new SMC with a density between 1.5 and 1.7 g/cm³. It also features a bending strength of > 350 MPa, a flexural modulus of elasticity of > 18,500 MPa, and an impact resistance of > 150 kJ/m2.
By using an epoxy resin instead of the usual polyester resin, it was possible to eliminate other problems that normally arise in working with glass fibre-reinforced SMC materials. The moulding material can be worked into complex geometries without adhering to the mould, the formulation has better mechanical properties than conventional SMC materials and features good fibre course in the moulding process, say the firms.
Moreover, Lorenz has an established process for recycling glass fibre-reinforced SMC materials, which is an important consideration given the sustainability requirements in the automotive industry.
For the supporting structure of the battery housing, the cooperation partners chose aluminium as a proven lightweight material. The general goal for the supporting structure was simple geometries and thus lower production costs.
“The bottom plate is the basis of the entire battery construction and has cross-members that the battery module is mounted on. The carrier plate for the battery management system is also attached to the aluminIum base,” reports Philipp Taschner, Project Engineer of Vestaro.
Two aluminium deformation elements provide the necessary side impact protection through absorption. The module alignment of the battery cells enables separation of the electric poles, which provides higher safety in the event of a crash and enables easy cooling.
Another partner LION Smart’s supercell concept was used for the batteries. “The design of the battery cells with a low number of components is intended for fully automated, cost-efficient production,” explains Taschner. “In addition, the battery design is particularly safe, as the individual cells are enclosed in a non-flammable dielectric coolant.” This not only provides higher safety, it also ensures a constantly low average temperature within the battery, which reduces cell aging. The modular series connection design of the battery also allows flexibility in the number of modules, with a very low overall height of 90 mm.
Furthermore, to verify the safety of the concept and its viability under conditions of actual use, the Computer Aided Engineering (CAE) department at Forward Engineering performed structural and safety simulations, according to Taschner.
The tests included a simulation of overall torsion and bending rigidity, lateral pole impact of up to 350 kN and short pressure resistance in thermal runaway, all of which were passed without problems. The limited mechanical performance of the base structure resulting from its intentionally simple geometry was effectively compensated by the optimised GF SMC, thanks to the design freedoms provided by the material.
The insulating properties of the epoxy SMC housing came to the fore in the thermal 2D simulation of the battery pack, noted Lorenz, adding that the material can withstand 10 minutes at 800°C without burning through, and its insulating properties protect surrounding components and materials from temperatures over 300°C.
In the past, glass fibre-reinforced SMC materials have been difficult to work with, so this point was likewise thoroughly tested.
Lorenz made multiple complex hardware demonstrators to verify the series suitability of the material and the production process, by using Evonik’s diamine-based epoxy hardener to create a simple and fast-curing SMC material with the required mechanical properties.
The company also adds that it was able to have curing times of three minutes in tests, without workpieces adhering to the mould. Moreover, the SMC with Vestalite S has no styrene emissions and only low VOC emissions.
The cooperation partners have made several configurations of their battery concept.
“Currently, we offer three energy configurations, which are competitive with or superior to current battery models on the market in terms of energy density, safety, and costs,” says Taschner.
“With all-in weights of 412.1 kg at 65 kWh, 527.3 kg at 85 kWh and 789.2 kg for the configuration with 800 V at 120 kWh, and the modularity and flexibility of the overall concept, we consider ourselves in a very good position to compete with other suppliers,” he concludes.
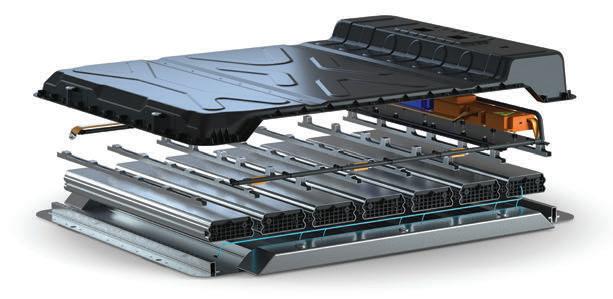
Industry News
• US-based Minnesota Rubber and Plastics (MRP) has acquired
Pawling Engineered Products, a
New York-based custom rubber products manufacturer. MRP, which has facilities across North America,
Europe, and Asia, said that the addition of Pawling’s capabilities will complement its existing offerings. MRP is also building a 9,000-sq ft innovation Centre adjacent to the company’s corporate headquarters in Plymouth. The new facility aims to provide customers with direct access to immersive designprototype-build-test process.
• US-headquartered ExxonMobil
Chemical is to sell its global
Santoprene business for US$1.15 billion to Celanese. The sale includes two world-scale manufacturing sites in the US and
UK. The transaction is expected to close in the fourth quarter of 2021, subject to regulatory approvals.
• Malaysia-headquarteredagrochemical company Hextar Global Bhd is acquiring Nobel Synthetic Polymer
Sdn Bhd and Nobel Scientific Sdn
Bhd, collectively known as Nobel
Group, for RM105 million. The group provides anti-tack rubber lubricants and coatings for the rubber industry.
Its acquisition will be funded through internally-generated funds and bank borrowings, according to Hextar, which is expanding its footprint in the specialty chemicals segment.
• Bridgestone Americas is securing
Azuga Holdings and the Azuga fleet management platform for US$391 million. The acquisition is anticipated to accelerate Bridgestone’s efforts in sustainable mobility solutions as a key aspect of the company’s advanced mobility strategy. The transaction is expected to close by the third quarter of this year.
• Investment firm Altaris Capital
Partners has completed the acquisition of a 51% stake in US biomaterials company Solesis from French tyre maker Michelin, who retains 49% of its stake in
Solesis, which now operates as an independent company. It develops critical components for implantable medical devices and single-use technologies for the biopharmaceutical market, including cell and gene therapies. Meanwhile, Michelin has secured a 20% share in Gothenburgheadquartered tyre recycling company Enviro Systems following the dilution of its holding in May as a result of the completed new issue.
The increase in its holding was via its subsidiary acquiring 2 million of the shares that were issued in May to
Unwrap Finance AB. Michelin has also acquired 100% ownership of Allopneus SAS, a
French firm involved in online sales and tyre fitting. Since 2015, Michelin had held 40% of the capital of the company, founded in 2004 by the
Blaise family. With this acquisition,
Michelin consolidates its e-commerce presence in France. Based in Aix-en-
Provence, Allopneus has had strong growth since 2004, accounting for 40% of the French online tyre sales market to private individuals.
• Swedish engineered polymer solutions company Trelleborg Group is divesting its Czech technical rubber products business to Czech investment group Kaprain. The transaction is expected to be finalised by the fourth quarter 2021.
• US-based polymer firm Trinseo is to acquire Aristech Surfaces, a North American manufacturer of PMMA continuous cast and solid surface sheets, from SK AA Holdings, an affiliate of Falcon Private Holdings.
• US engineered products maker
ILC Dover, a portfolio company of New York-based investment firm New Mountain Capital, has acquired Flexan, an Illinoisheadquartered medical device contract design and manufacturing company that specialises in silicone, thermoplastic, and specialty rubber components and devices. • Tokyo-headquartered Shin-Etsu
Chemical’s Silicone Division will be ploughing an investment totalling
JPY20 billion to curb greenhouse gas emissions (GHGs). The Silicone
Division’s main manufacturing plant, the Gunma Complex, will reduce the volume of GHGs by 14%, by further increasing self-sufficiency in its usage of electric power.
• India-based carbon black manufacturer Birla Carbon is targeting to achieve a zero net carbon emissions by 2050. The company is collaborating with its sister companies within the Indian multinational conglomerate, Aditya Birla Group, to develop decarbonisation initiatives through the Aditya Birla Science and Technology Centre. Recently,
Birla Carbon also announced the availability of Sustainable
Carbonaceous Materials (SCM) through the launch of its Continua brand.
• Japan’s Sumitomo Chemical is to end production at its 40,000-tonne/ year EPDM plant at its Chiba Works and to stop selling EPDM by the end of March 2023 since the expenses of maintaining and repairing EPDM production plants, which have been in operation for more than 50 years, are rising.
• US recycling firm Agilyx
Corporation, a wholly owned subsidiary of Agilyx AS, and South
Korean Kumho Petrochemical, a manufacturer of synthetic rubber, are collaborating in a chemical recycling project in South Korea. It will use Agilyx’s chemical recycling technology to produce pure styrene from post-use PS. This would be used as a virgin equivalent raw material to produce solution SSBR for the large volume, high-performance tyre segment.
• Carbon black maker Orion
Engineered Carbons is constructing its second plant in Huaibei, Anhui’s eastern region, China. The factory will be able to produce a variety of carbon
black with an initial production capacity of 65-70 kilotonnes/ year. The new facility, which joins Orion’s first Chinese factory in Qingdao and Orion’s production facility in Yeosu, South Korea, will convert waste heat into steam to be supplied to the local industrial park.
Meanwhile, Orion has tied up with state-owned RISE Research Institute of Sweden to produce renewable carbon black. Luxembourg-headquartered Orion said that it plans to convert the biomass oil into carbon black using its small-scale furnace reactor in Kalscheuren, Germany. Additionally, using a pilot-scale reactor at its site in Piteå, Sweden, RISE will evaluate the use of electrofuels, such as plasma or hydrogen from electrolysis, as sustainable heat sources for the carbon black process.
• US materials science company Dow has launched MobilityScience Studios, which are aimed towards providing faster and more effective solutions for acoustics, sealing, powertrain, and fluid system components.
The first two studios, located in
Midland, Michigan and Lake Jackson,
Texas, will be used to support the development of transportation technologies, Dow said.
• Vizient, a US healthcare company, and Sri Trang Gloves, a Thailandbased glove manufacturer, are to improve supply of chemo-rated nitrile exam gloves as part of the
Vizient Novaplus Enhanced Supply programme. Vizient members will be able to commit to a monthly purchasing volume for nitrile gloves at any level as part of the arrangement with Sri Trang, and Sri Trang will keep a 90-day onshore supply particularly for that provider organisation.
• Texas-headquartered McDermott
International has been awarded a Front-End Engineering Design (FEED) contract from the Michelin
Group for a waste tyre technology enabling large-scale production
Industry News
of recycled carbon black. This award follows a similar FEED announcement in April, which is focusing on the production of regenerated styrene to make synthetic rubber for tyres. In the implementation of this, Michelin will use Scandinavian Enviro Systems’ licensed pyrolysis process.
• German technology firm
Continental is to use reprocessed polyester derived from recycled
PET bottles in its tyre production by 2022. The new sustainable polyester yarn will be obtained from PET bottles by a mechanical process and will be used in the construction of the tyre carcass, to completely replace conventional polyester.
Together with its cooperation partner/supplier OTIZ, a fibre specialist and textile manufacturer,
Continental has developed a special technology to recycle PET bottles without previous intermediate chemical steps and to make the polyester yarn functional for tyres.
• South Korean chemicals maker
Kumho Petrochemical has developed a sustainable rubber compound, by producing silica from rice bran extracts. The ecofriendly silica is used for improving the fuel efficiency, braking power and wear resistance of synthetic rubber for tyres. In view of this development, Kumho Petrochemical is planning to double its synthetic rubber production capacity from the current 63,000 tonnes to 123,000 tonnes by the end of next year.
• US-headquartered carbon-based products producer Rain Carbon has opened a rubber lab at its distillation and advanced materials facility in Duisburg, Germany.
The US$1.3 million lab comprises a complete processing line, starting with a rubber bale cutter, continuing with a lab station for internal mixing, and concluding with complete analysis employing cutting-edge rubber-process and dynamic-mechanical analysers. 2 • Moscow-headquartered energy corporation PJSC Lukoil has launched its polymer-bitumen binder production unit at its Nizhny
Novgorod refinery, with an output of over 150,000 tonnes/year.
• Wuxi-headquartered tyre maker Jiangsu General Science
Technology (JGST) is building a EUR166 million tyre factory in
Sihanoukville special economic zone, Cambodia. The plant will have a capacity to produce 6 million passenger car tyres/ year. The tyre processing plant, to be completed in 15 months, is expected to start up in September 2022.
• MOL and Tatneft, one of the largest oil and gas companies in Russia, have launched a joint project for a rubber bitumen plant in the Republic of Tatarstan.
The companies are also forming a joint venture that, besides manufacturing and selling rubber bitumen, will also market
MOL’s technology license in the
Commonwealth of Independent
States. The investment is partly financed by the Hungarian Export
Development Agency’s (HEPA) tender funding.
• Indian coal tar derivatives company
Epsilon Carbon Private Limited
(ECPL) has set up India’s first integrated carbon black complex located in Karnataka, South India.
With a capacity of 115,000 tonnes/ year, the carbon black unit is already running close to its full capacity, producing both tread and carcass grades of ASTM carbon blacks for tyre, non-tyre rubber and plastic masterbatch partners globally. As part of Phase 2, ECPL will further expand its capacity by another 65,000 tonnes/year, with an investment of
US$800 million, which will bring the total investment to US$2 billion.
ECPL plans to further expand capacity to total 300,000 tonnes/ year, making it India’s largest single location carbon black plant.
Silicones
Breakthroughs in medical-grade silicones at full speed
To address the need for important medical devices, new silicone technologies are being developed and made available, according to Angelica Buan.
Growth expected for silicone elastomers
As with all global elastomer markets, the silicone elastomers market also suffered a serious setback since the beginning of 2020. However, unlike other elastomer markets, the silicone elastomer market is rebounding rapidly, despite (or more importantly because of) the Covid-19 pandemic, says research firm Smithers in its latest report titled “The Future of Silicone Elastomers to 2026”.
The silicone elastomers global market was 415,000 tonnes in 2016, and increased at a CAGR of 6.15% to 496,000 tonnes in 2019. Due to Covid-19, the global market is estimated to have fallen to 421,000 tonnes in 2020, but expected to grow to 556,000 tonnes in 2026, at a CAGR of 5.1%.
While transportation is the largest end-use sector, with 27.7% of the market in 2020; and forecast to increase to 28.1% in 2026, the medical sector is expected to buoy demand. This is because the advent of Covid-19 has seriously challenged the market for silicone elastomers, presenting positive opportunities in medical and automotive applications, but a reduction in other markets, adds Smithers.
Besides being used as replacements for some thermoplastic elastomers, silicones are also expected to see heightened demand for use in medical applications; automotive under-the-bonnet applications and as a support medium for flexible solar panels, the report adds.
Silicones make the medical grade
Single-use medical devices are in the spotlight as the quest for herd immunity from the coronavirus/Covid-19 continues. While the global situation remains challenging, patient care is focused on the most fundamental needs: hygienic, lightweight, low-cost, and easy-to-use devices. Without doubt, advancements in medical-grade materials such as silicones fit these criteria, making medical treatments more accessible and efficient.
Medical grade silicone has a high market demand for a variety of applications, from single-use disposable devices to more complex, implantable devices, due to its biocompatibility, sterilisability, durability, excellent conductivity, tensile strength, thermal stability, and other desirable properties.
As a result, this elastomer is being used extensively by leading industry players in the development of cutting-edge medical equipment such as dental instruments, prosthetics, pacemakers, and other drug delivery devices. With the increasing preference for medical-grade silicones, the market is set to grow exponentially. According to Global Industry Analyst audit, the market is expected to reach US$1.8 billion by 2027, up from an estimated US$1.3 billion in 2020.
Furthermore, silicones are widely used in the personal care, consumer products, construction, and electronics industries, fuelling the growth of the global silicone market.
Liquid silicone rubber (LSR), a popular material for single-use device parts, is ideal for sealing membranes, electric connectors, seals, and other medical applications due to its high microbiological and chemical resistance, good transparency, gas permeability, clarity, elongation feature, superior dielectric strength, and other material properties.
Concurrently, materials with additional qualities are increasing appeal in application development, in tandem with the rising use of silicone in these major industries. New techniques and technologies are also being developed to improve silicone functionality while also providing productivity and energy efficiency benefits to producers.
Antifungal silicones to curb infections
Antiviral agents, in addition to disinfecting surfaces, play an important role in preventing disease transmission. Taiwanese silicones specialist General Silicones (GS) offers its antifungal silicone sheets for protective coatings, which can be used in applications where surfaces are frequently handled and thus become a source of germ transmission.
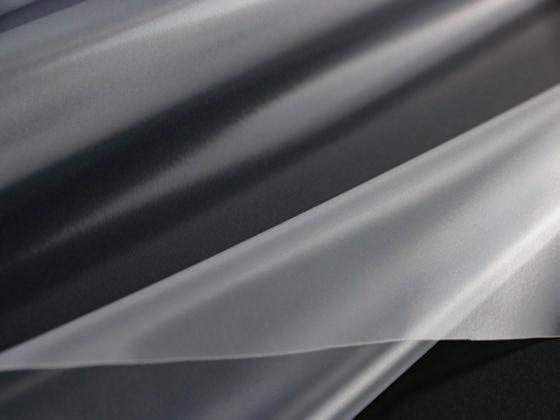
Silicones
Recently, GS’s antifungal silicone rubber sheet for protective coating Compo-SiL obtained ASTM G21 certification from the SGS Hardline Laboratory in Taiwan.
Using standard PU (polyurethane reactive adhesives) and hot melt adhesives, the patented Compo-SiL technology enables ultra-strong and long-lasting adhesion to base materials and surfaces. According to GS, Compo-SiL is the only solution that uses pre-fabricated and cured silicone rubber sheets during mass production and installation work. Furthermore, the colour, texture, and feel can be customised as per customer requirement, and antifungal and antibacterial agents can be added on demand. Customers receive finished sheets in rolls for integration into standard manufacturing processes.
Because of its exceptional resistance to heat, extreme cold, and UV radiation, as well as the anti-slip properties added during manufacturing, the silicone product is suitable for outdoor use in humid environments. Being chemically inert to detergents and alcohol-based disinfectants, Compo-SiL sheets are suitable for giving antibacterial and antifungal protection to surfaces of tables, chairs, handrails, and door handles in public places.
Medical devices and facilities, public transportation, and elderly care facilities are some examples of applications.
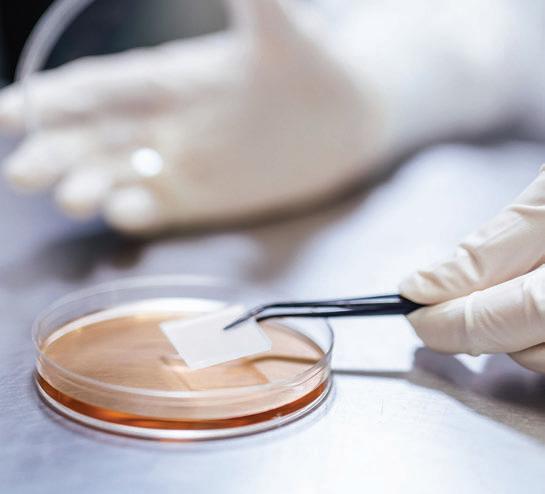
NovationSi’s HCR uses a patent-pending technology that incorporates a revolutionary single-wall carbon nanotube (SG101) developed by Zeon Corporation
Electrically conductive silicone compounds
Elsewhere, high consistency rubber (HCR) healthcare compounds have been developed by Novation Solutions (NovationSi), a materials science company that specialises in silicone dispersions. It uses a patent-pending technology that incorporates a revolutionary single-wall carbon nanotube (SG101) developed by Japanese synthetic rubber company Zeon Corporation.
The electrically conductive qualities of the cured product are considerably improved by effectively distributing Zeon’s SG101 carbon nanotubes with NovationSi’s PURmix HCR compounds. Medical gadgets that perform neuromodulation therapies on the human body are one practical application of this silicone technology.
According to NovationSi, the US FDA has already approved the first clinical application of these silicone compounds in the treatment of essential tremors, a neurological disease marked by uncontrollable and rhythmic shaking that can affect nearly any area of the body. Moreover, the compounds have been introduced to the medical device market for patients’ use under physicians’ care.
Many patients had a reduction in tremors as a result of the therapeutic breakthroughs made possible by this new technology, according to clinical studies related with this study.
NovationSi added that the technology is still in its early stages of development, but it is being improved by integrating with technologies of other companies. The likelihood that its application in medical devices would spur commercial development for wider industrial use is starting to emerge; and strong growth is expected in 2022.
Lightweight solution for enhanced productivity and energy savings
In a variety of industries, including automobiles and transportation vehicles such as airplanes, as well as other fields such as wearable devices, demand for lighter rubber-moulded products is on the rise. Silicone rubber applications are expected to become more common with the development of lighter products.
In this arena, Japanese silicone specialist ShinEtsu Chemical Co has developed a new low-density type of moulding silicone rubber that is lightweight. The company says it is the first in the industry to have developed this type of moulding silicone rubber using LIMS (liquid injection moulding system) materials.

Silicones
A foaming agent was usually applied to millable-type silicone rubber and moulded into a sponge-like form to make lighter-weight silicone rubber. Shin-Etsu adds that its product eliminates the need for a foaming agent.
Additionally, it can be moulded utilising its advanced LIMS, thus, it can a meet the demand for improved quality and productivity from moulding producers.
The silicone product comes in two varieties: a lowdensity/high-strength type that saves 20-30% of the weight of regular silicone rubber moulding goods, and a very low-density type that saves 50-60% of the weight of typical silicone rubber moulding products.
Both types can employ an injection moulding machine to perform continuous automatic moulding and, as a result, efficiently make high-quality rubber moulded items, increasing productivity and reducing energy consumption, says the firm.
Faster and higher output with LSR technology
Trelleborg, a Swiss engineering firm, has created and provided silicone tubing, film, and custom-moulded components, as well as elastomer and polymer seals, to biotech and pharmaceutical equipment and medical device makers. To broaden its customer offerings, the company has made significant investments in advanced technology.
Trelleborg Healthcare & Medical, the group’s USbased unit, acquired Switzerland-based SilcoTech in 2011, bolstering its silicone clout by honing Silcotech’s expertise in LSR technology and, in particular, automation of the process to enable high-volume production of precision LSR components.
Recently, Trelleborg demonstrated its advanced polymer solutions, as well as multicomponent and micromoulding capabilities, at a medical device expo in the US. Trelleborg claims that its latest capability will help customers speed up the creation of new products while also lowering production costs, shortening development time, and ensuring high-quality products.
It also stated that combining LSR with plastics is one of its well-known capabilities. Multicomponent injection moulding, often known as 2C or two-shot multicomponent injection moulding, allows its LSR experts to use extremely advanced tool and process engineering to build innovative products.
Trelleborg, which displayed its specialty extruded tubing and hose products in a variety of sizes at the MD&M West show recently, engineers novel extrusion solutions for its customers’ specific tube and hosing applications, which include for example, multilumen silicone foam extrusions and kink-resistant tubing for critical applications such as pacemaker and neuromodulation leads and urological implants.
Furthermore, Trelleborg’s GeoTransTM technology enables the production of extrusion profiles that can change throughout the length of the extrusion, allowing for unique, customer-specific designs.
It also showed off its moulded components, which are used in medical implants. Trelleborg claims that these unique silicone and thermoplastic moulded parts are created with precise tolerances utilising in-house precision tools and know-how, and that short turnaround prototypes match the need for rapid product development.
The company stated that it is motivated to assist customers with manufacturing challenges such as developing devices that incorporate an active pharmaceutical ingredient for targeted therapy delivery, wound-care applications that require waferthin silicone gel films combined with a drug element, or an innovative cancer treatment approach.
Also at the medical technology exhibition, US silicone specialist SIMTEC-Silicone offered its range of critical components used in ophthalmology, endoscopy, respiratory, drug delivery, fluid management, wearable diagnostics, as well as LSR and LSR multi-shot components.
SIMTEC touts its advanced moulding technology, including class 8 cleanroom and automated LSR/LSR two-shot/multishot manufacturing, which it claims provides high precision silicone components with higher clarity, purity, and value. The technologies can be applied in medical devices such as respirator masks, dialysis filters and infusion pump parts, syringe parts, and more – all of which are critical to the medical and pharmaceutical industries.
Trelleborg engineers novel extrusion solutions for its customers’ specific tube and hosing applications
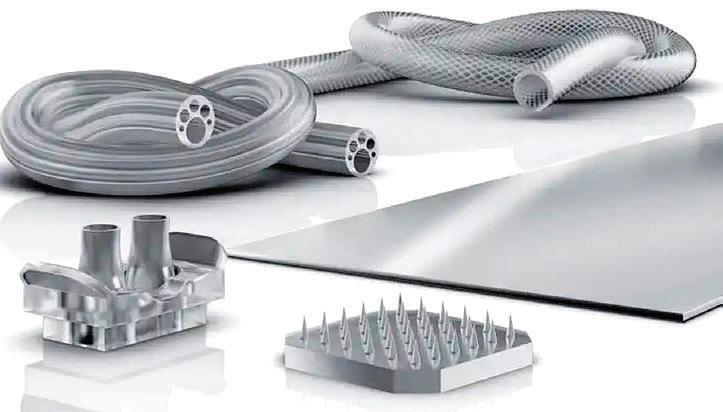
2021
22 - 23 SEPTEMBER 2nd PHA platform World Congress
Venue: Cologne, Germany Tel: +49 2161 6884469 Email: mt@bioplasticsmagazine.com Website: www.pha-world-congress.com
6 - 8 OCTOBER 30th Vietnam International Industrial Fair (VIIF)
Venue: ICE, Hanoi Tel: + 84 904211644 Fax: +84 24 3834 5655 Email: viif@vefac.vn Website: www. viif.vn
12 - 16 OCTOBER FAKUMA
Venue: Friedrichshafen, Germany Tel: +49 (0) 7025 9206-0 Fax: +49 (0) 7025 9206-880 Email: info@schall-messen.de Website: www.fakuma-messe.de
13 - 16 OCTOBER METALTECH & AUTOMEX
Venue: MITEC, Kuala Lumpur, Malaysia Tel: +03 9771 2688 Email: geonice.chong@informa.com Website: www.metaltech.com.my
20 - 22 OCTOBER ProPak India
Venue: Pragati Maidan, New Delhi Tel: +91 98196 15657 Email: sameer.mithia@informa.com Website: www.propakindia.com
20 – 23 OCTOBER Eurasia Packaging Istanbul
Venue: Tüyap - Istanbul, Turkey Tel: + 90-212-867-11-00 Fax: +90 (212) 886 67 48 Email: team@packagingfair.com Website: www. packagingfair.com
10 - 12 NOVEMBER ProPak Vietnam
Venue: (SECC) HCMC, Vietnam Tel: +84 28 3622 2588 Fax: +84 28 3622 2527 Email: propakvietnam@informa.com Website: www.propakvietnam.com
10 - 13 NOVEMBER AllPack Indonesia
Venue: Jakarta International Expo, Kemayoran, Indonesia Tel: +62-21 6345861 Email: info@kristamedia.com Website: www.allpack-indonesia.com
15 - 18 NOVEMBER ArabPlast
Venue: DWTC, Dubai, UAE Tel: +971 55 9555982 Email: rasheed@alfajer.net Website: www.arabplast.info
16 - 18 NOVEMBER UTECH Europe
Venue: MECC, Maastricht, NL Tel: +1 330 608 0231 Email: dhershfield@crain.com Website: www.utecheurope.eu
ADVERTISERS’ ENQUIRIES
Check out the Advertisers' page on our website.
Information is categorised by the YEAR & DATE of publication for easy reference.
For further details, email us at: news@plasticsandrubberasia.com
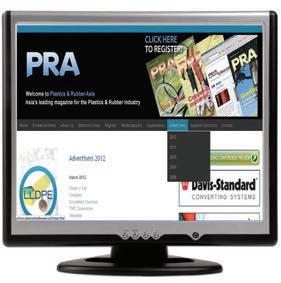
PRA Digital issue is available ONLINE!
www.plasticsandrubberasia.com

INTERNATIONAL OFFICES
Publishing Office/Scandinavia, Benelux & France Postbus 130, 7470 AC Goor, The Netherlands Tel: +31 547 275005 Fax: +31 547 271831 Email: arthur@kenter.nl Contact: Arthur Schavemaker
Regional Office
SQ9, Block A, Menara Indah, Taman TAR, 68000 Ampang, Selangor, Malaysia Tel: +603 4260 4575 Email: tej@plasticsandrubberasia.com Contact: Tej Fernandez
China & Hong Kong
Room 803, No.2, Lane 3518, Road Bao'An, District Jiading, Shanghai Tel: +86 13341690552 Mobile: +86 17751702720 Email: henry.xiao@matchexpo.com Contact: Henry Xiao/Zhu Wei
China
Bridge Media 亚桥传媒 Room 206, #1, 569 Shilong Rd, Shanghai, China 200237 Tel: +86 21 3368 7053 Mobile: +86 138 1643 7421 Email: lagopoah.yang@bridgemedia.cn Contact: Lago Poah Yang 杨旋凯
Southeast Germany, Switzerland & Austria
Verlagsbüro G. Fahr e.K Breitenbergstrasse 17 D-87629 Füssen, Germany Tel: +49 8362 5054990 Fax: +49 8362 5054992 Email: info@verlagsbuero-fahr.de Contact: Simon Fahr
North-West Germany
JRM Medien+Verlag Minkelsches Feld 39 D-46499 Hamminkeln, Germany Tel: +49 2852 94180 Fax: +49 2852 94181 Email: info@jwmedien.de Contact: Jürgen Wickenhöfer
Malaysia. India, Indonesia, Singapore, Thailand, Australia, New Zealand, Korea & Philippines
Tara Media & Communications SQ 9, Block A, Menara Indah Jalan 9, Taman TAR, 68000 Ampang, Selangor, Malaysia Tel: +603 4260 4575 Email: tej@plasticsandrubberasia.com Contact: Tej Fernandez
Italy, Spain & Portugal
MediaPoint & Communications Srl Corte Lambruschini, Corso Buenos Aires, 8, Vo Piano - Interno 9, 16129 Genova, Italy Tel: +39 010 570 4948 Fax: +39 010 553 0088 Email: info@mediapointsrl.it Contact: Fabio Potesta
Taiwan 宗久實業有限公司 Worldwide Services 11F-B, No.540 Sec.1, Wen Hsin Rd., Taichung, Taiwan Tel: +886 4 23251784 Fax: +886 4 23252967 Email: global@acw.com.tw Contact: Robert Yu 游宗敏
USA & Canada
Plastics Media International P. O. Box 44, Greenlawn, New York 117430, USA Tel/Fax: +1 631 673 0072 Email: mjm@4m-media.com Contact: Michael J Mitchell
www.plasticsandrubberasia.com www.rubberjournalasia.com www.injectionmouldingasia.com www.plasticsandrubberasia.cn