
9 minute read
材料新聞
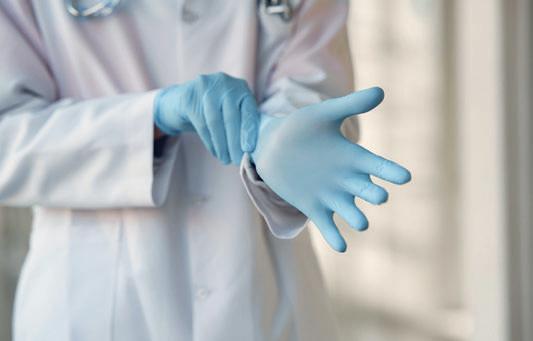

Advertisement

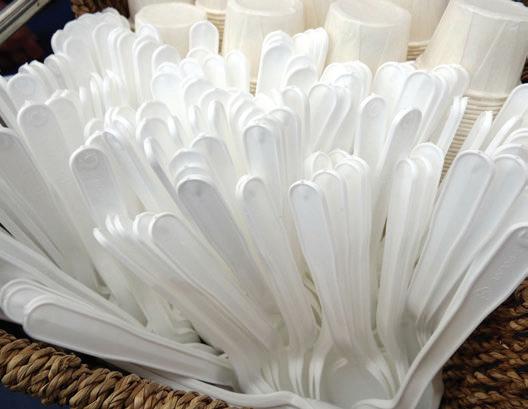
Packaging Sector
Packaging with benefits
The packaging industry has notched up brownie points in the issue of recycling, with increasing use of post-consumer recycled (PCR) plastic content in their outputs, according to Angelica Buan in this report.

Mondi has launched its EcoSolution, which offers recyclability benefits to food retailers such as Austria's Rewe's cheese brand packed with Mondi's patented solution
Less packaging is a new normal for brands
As brands fight for consumer attention, manufacturers are riled up over making their products stand out on shelves. Whether it is good or bad, packaging gives the initial impression to consumers. That is why designs now vary to cater to aesthetics and usage preferences. But when it boils down to it, the fierce shelf competition results in a design overkill, and this may do more harm than good to the brand.
According to an online survey conducted by Ipsos MORI and packaging firm Mondi, British consumers are more likely to switch to products with less packaging. More than 2,000 UK respondents aged 16-75 participated in the survey, which revealed that packaging can make or break brands.
More than half of the surveyed individuals said that when shopping for food and everyday household items, they would switch to a different brand if it used less packaging. What this means is that sustainability in packaging has become a crucial determinant for purchasing decisions.
Mondi commented that the survey results highlight the importance of incorporating sustainability in their packaging development and production. Mondi works with its customers to create EcoSolutions – an approach that creates bespoke packaging solutions that will ensure businesses can protect the product, promote the brand and deliver on their sustainable packaging commitments.
Meanwhile, taking a cue on the importance of using materials sustainably, US flexible packaging maker ProAmpac has joined the Association of Plastic Recyclers (APR), a trade association representing companies responsible for more than 90% of the postconsumer plastic processing capacity in North America. Through APR, ProAmpac says it aims to advance its ProActive Sustainability platform towards a more circular economy.
From waste to resource
In an era of speed and convenience throwing away what no longer serves its purpose makes sense. However, this trend also gives rise to a culture of wastage.
Packaging Sector
According to the Asian Development Bank (ADB), global plastic waste, which represented 12% of all municipal solid waste (MWS), racked up 242 million tonnes in 2016. At the time of the audit, East Asia and the Pacific had yielded 57 million tonnes.
Together with Central Asia, Europe yielded 45 million tonnes. Against the back of this, the region launched the Plastic Waste programme in 2018, which aims to make all plastic packaging recyclable by 2030 and ensure that waste generated on ships is returned to land (EU 2018b).
In India, plastic waste generation takes up nearly 7% of the MSW, according to the Central Pollution Control Board (CPCB). Thus, in 2015 it hatched a programme called Plastics for Change, which takes a shot at ethically sourced recycled plastics to reduce plastic pollution and poverty in the region through recycling.
India's Plastics for Change says it enables global brands and manufacturers to source high-quality plastic from responsible supply chains

hese and similar drives are benefitting the post-consumer recycled (PCR) plastics market to increase the utilisation of materials derived from recycled waste. Projected to exceed US$10 billion by 2024, the growth of the PCR market, according to a Markets and Markets research, latches on the brisk demand for sustainable packaging.
Asia: mining for PCR packaging materials
We have heard it before: some countries in Asia are among the worst plastic polluters in the world, according to a 2017 report by Ocean Conservancy and McKinsey Center for Business and Environment.

Packaging Sector
A report found that some countries in Asia were among the worst plastic polluters in the world
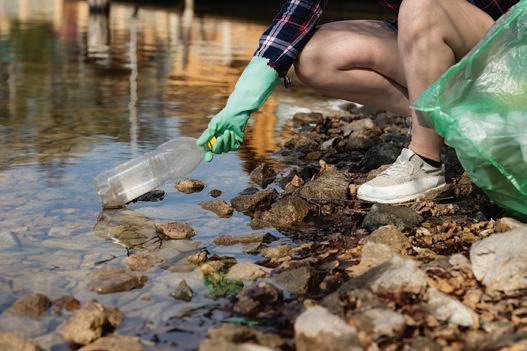
Needless to say, the region is collectively targeting to increase recycling rates to reduce the amount of waste plastics in the environment. With infrastructure for recycling being built and improved, Asia, a ripe source for PCR plastic resins, is poised to corner the US$25.7 billion PCR market size by 2025, based on a report by Grand View Research. It said that the growing demand for recycled films from various end-use industries is anticipated to drive the growth.
Industry majors, like chemical firm Dow, are meeting this demand for PCR films. The company has recently developed and commercialised a new formulated PCR plastic resin designed for collation shrink film applications in Asia-Pacific.
The new resin is designed with 40% PCR content, which creates a film with performance comparable to those made with virgin resins. The product, XUS 60921.01, is made with recycled plastics collected domestically within China through Dow’s strategic recycling partners and is made at Dow’s external manufacturing site in Nanjing, China.
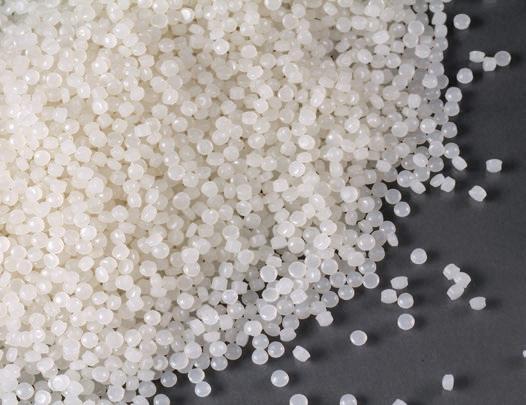
The resin is designed to be used as 100% of the core layer of collation shrink applications and will enable the development of film with 13-24 % recycled content.
Dow, meanwhile, forged a similar venture with Swedish stretch film producer Doxa Plast for biobased stretch films. Called Reborn, this new range of stretch films by Doxa Plast, integrates Dow’s biobased linear low-density polyethylene (LLDPE), Elite 5230GC R Enhanced PE resin, which is produced from renewable feedstock. The feedstock comes from residues of paper production from sustainably managed forests in Finland.
Doxa Plast's biobased stretch films, Reborn, integrates Dow’s biobased LLDPE
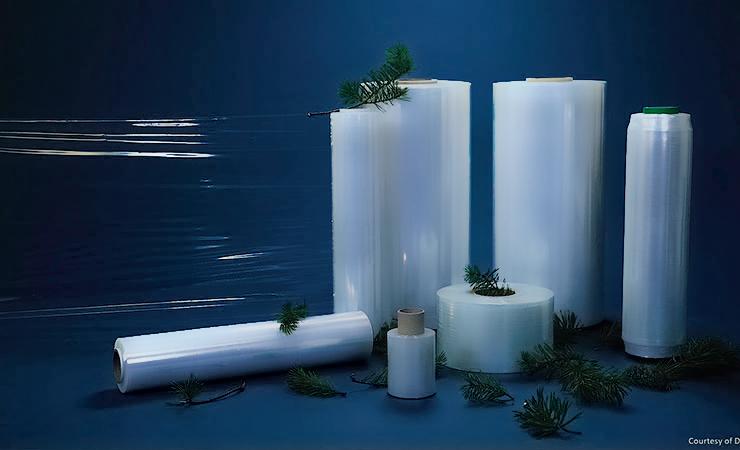
Oceans’ plastics in food packaging
The worst scenario has been predicted for the mounting ocean plastics, which is by 2050 there will be more plastics than fish in the seas if this problem is not tackled soon.
With packaging, the dominant application for plastics, transforming ocean plastics into packaging materials is an appropriate, viable measure to address the above issue.
Plastic packaging, according to the World Economic Forum (WEF) report in 2016, represents 26% of the total volume of plastic applications. This is owing to the materials’ affordability, light weight and high performance. Plastic packaging can also benefit the environment in that its low weight reduces fuel consumption in transportation, and its barrier properties keep food fresh longer, reducing food waste.
Having said this, the material value of ocean plastics are being tapped for packaging applications. Food packaging with ocean plastics is not new but it is hoped that the adoption will increase over time.
UK supermarket chain Lidl has starting offering a supermarket-first food packaging using ocean bound plastic collected from Southeast Asia. It announced that the new packaging will be rolled out across 13 fresh fish products, including white fish and salmon. The packaging, developed in
UK's Lidl has launched its first supermarket packaging made with ocean plastics
partnership with Copernus, Sharpak and Bantam Materials, is made from 80% recycled content and a minimum of 30% of the weight of the tray is made of ocean-bound plastic.
Alongside Copernus, Lidl has also launched this new initiative in conjunction with Bantam Materials, a supplier of ocean-bound plastic via its Prevented Ocean Plastic (POP) programme, and Sharpak, part of Groupe Guillin, a processor that makes Lidl’s new fish trays.
According to Lidl, the initiative will initially prevent more than 60 tonnes/year of plastic from being introduced to the ocean, which is the equivalent of 2.5 million plastic water bottles.
Lidl says it has also improved the recyclability of the packaging with the new recyclable tray, which will divert over 200 tonnes from landfills. This packaging will now be labelled with Widely Recyclable, in line with On Pack Recycling Label (OPRL) guidelines, meaning the majority of customers can recycle at kerbside.
Likewise, this also forms part of Lidl’s commitment to Project STOP (Stop Ocean Plastic), which aims to design, implement and scale circular economy solutions to marine plastic pollution in Southeast Asia.
Along the same vein, Norwegian company ZincIn has also launched ocean waste plastic food trays. It combines the concept of reducing waste plastics and hygienic food packaging, which are much in demand in view of the heightened hygiene measures during the pandemic.
Taking ropes and cages from the fishing industry and converting them into serving trays, Zincin also features a technology that keeps the trays constantly clean. This technology integrates in the plastic a trace element that normally is vital for a body's immune system. The way the element is defending a body against bacteria and viruses is now integrated into the plastic, making the surface of the plastic material resistant to germs and keeping the surface hygienic without the proliferation of germs, ZincIn explains.
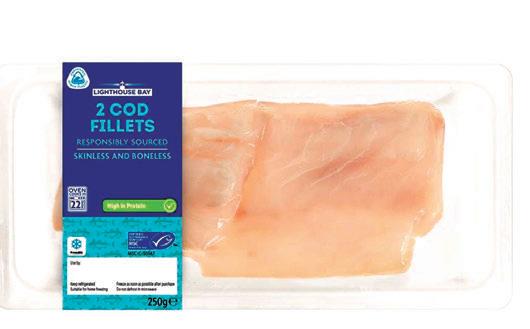
Packaging Sector
ZincIn worked with Parx Materials, which specialises in the development and manufacturing of materials with sustainable anti-biofilm and antimicrobial properties, to integrate its antimicrobial technology in the new packaging. The packaging is also developed with the help of Norwegian Plastic Recycling (NORPEC)’s raw materials that are produced from end-of-life farm cages, feed bags and hoses from the aquaculture industry and ropes, plastic tanks and other plastic waste from the fishing industry.
ZincIn and Parx Materials have developed a sustainable antibiofilm with antimicrobial properties
Meanwhile, Riyadh-headquartered chemicals firm Sabic and UPM Raflatac, a signatory to the Ellen MacArthur New Plastic Economy initiative, have also developed and recently launched a PP label film manufactured from PCR plastic. Now available globally, this label material uses Sabic’s Trucircle solutions that utilise mechanically recycled and certified circular products from feedstock recycling of plastic waste streams and certified renewable products from biobased feedstock.
The UPM Raflatac PP PCR products are made with a chemical recycling technology that uses a mass-balance approach to deliver virgin-like resin feedstock. The chemical recycling process also makes it possible to use recycled plastics in applications that could not utilise recycled materials before, such as food applications. With the same properties as standard PP films, these PP PCR films can be used in different label applications, including rigid food packaging. Customers and brand owners can achieve the same product performance and cut their footprint by decreasing the amount of virgin materials used at the same time, the partners said.
