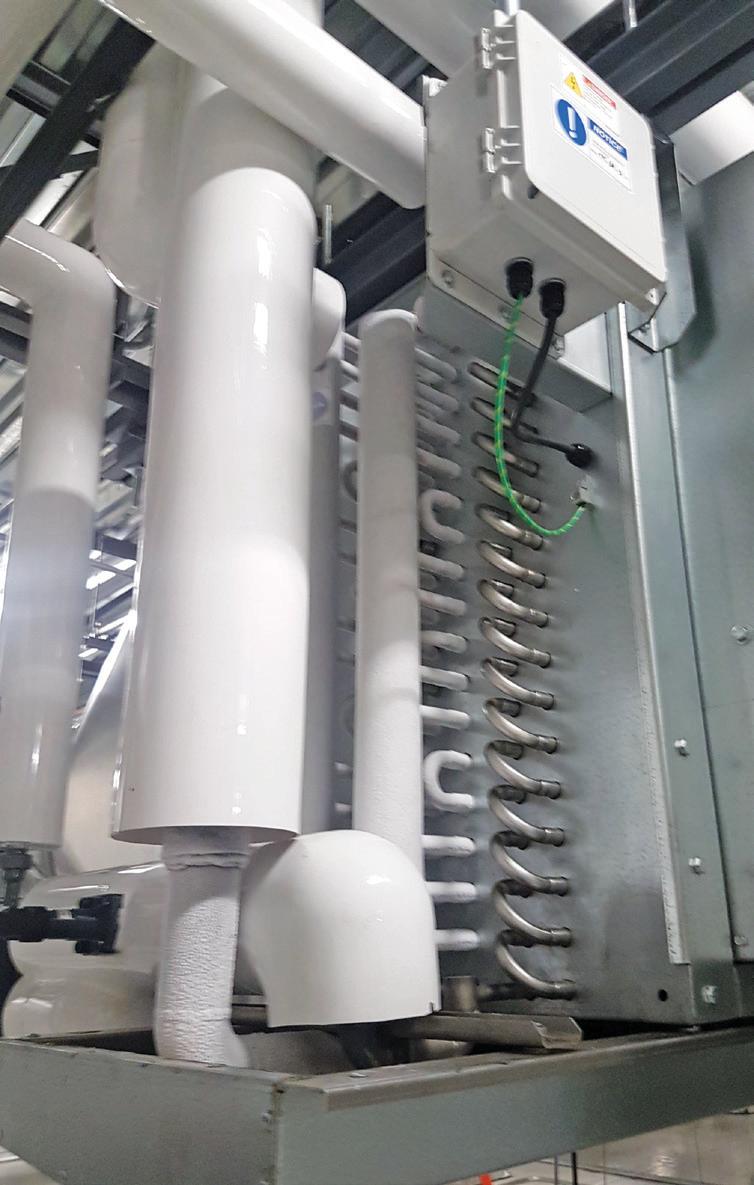
2 minute read
n Refrigeration
from Jan/Feb 2023
The lines between commercial and industrial applications have never been more blurred than it is today.
Continued from page “37” willingness to use industrial-style equipment in civic infrastructure projects, like ice rinks. Ice rinks are not an overly large refrigeration system. You can make ice with anything from ground source heat pumps, commercial style chillers, grocery store racks, CO2 racks, to open drive ammonia or halocarbon systems. While people do employ all these options regularly, the majority of municipal projects are still built with an industrial-style system because municipalities have the desire to build facilities with much longer life cycles than much of the private industry.
Reliability
Another differentiating factor is reliability. I am aware of industrial refrigeration systems that run for years between shutdowns; there are some that have quite literally never been completely shut down in their entire existence except for during a power outage. Repairs and replacement of components, of course, but not shut down. In many large food production facilities, a shutdown is massively expensive, and money put into reliability and long-term operation is much preferred over less expensive investment in equipment.
One example of increased liability is related to the piping design. Smaller commercial equipment is not often built to comply with ASME B31.5 and instead relies on a UL rating for its pressure containing components (other than pressure vessels). This is not bad, but since UL is a test-based method compared to ASME’s much more conservative calculationbased methods, the commercial equipment does experience (in my experience) a significantly higher rate of piping and pipe joint failures. A frequent location for this is discharger headers on compressor rack-style systems. This pipe can get very hot and often doesn’t incorporate appropriate flexibility into the piping design.
I have seen dozens of cracked discharge headers or failed discharge branch piping in commercial rack-style systems in both CO2 and halocarbons. I don’t recall ever having seen failed/cracked discharge piping on a system that complies with ASME B31.5.
End of the day
As with many things in engineering or design, it comes down to lifecycle costs. I once worked on a facility that insisted on planning everything — including the spiral freezer and refrigeration system — on a five year life. They had their business reasons for doing this, and I can assure you it doesn’t make sense to use the most expensive equipment in this scenario.
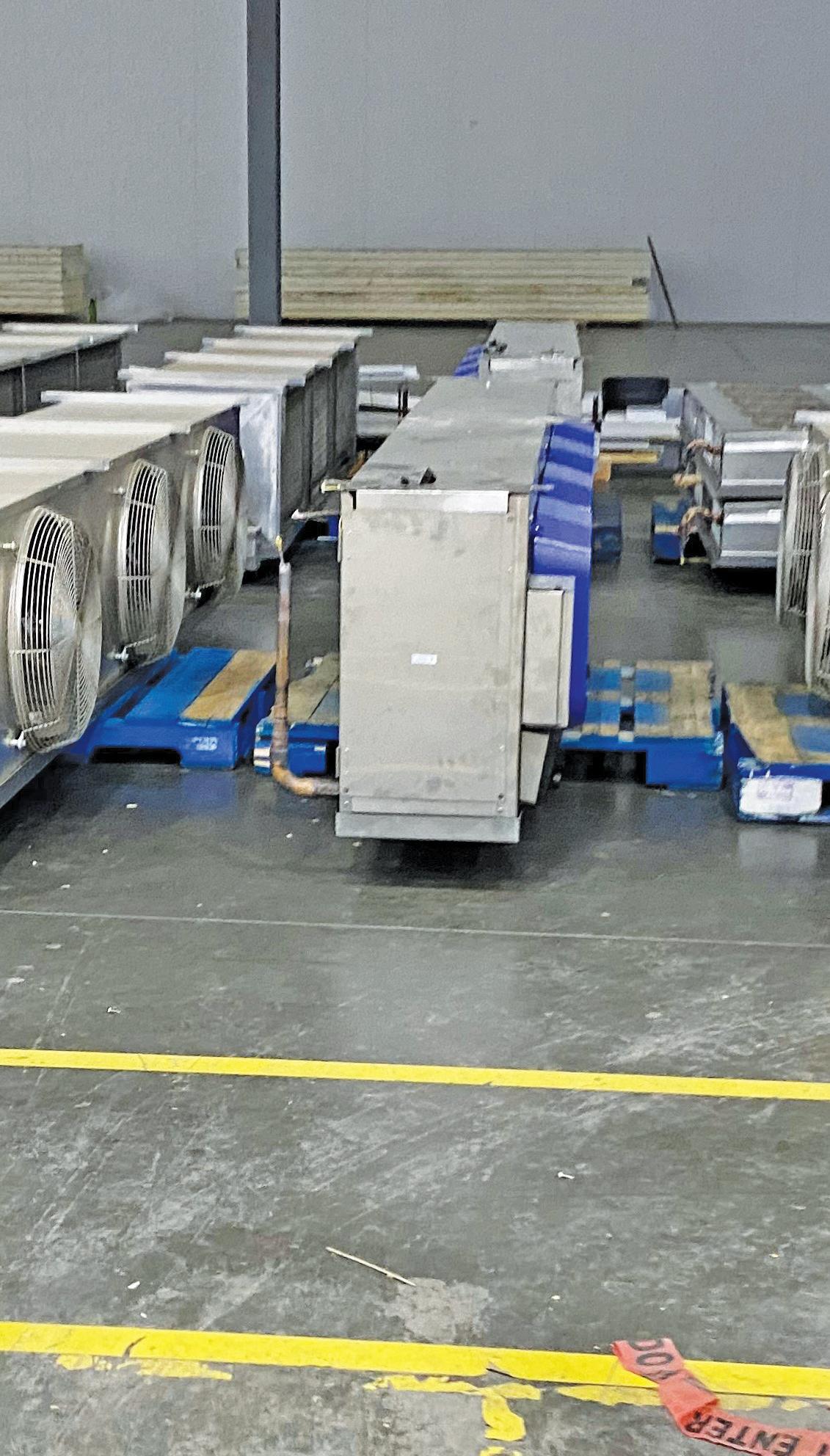
Only a thorough understanding of the owner’s needs can help guide how “industrial” or how “commercial” you make the equipment. The closer you get to the grey area in between them, the harder it is to know what the right decision is. And as I mentioned at the beginning of this article, CO2 is upsetting the long-standing industry balance. There is a huge interest in using CO2 in industrial applications – and we are – but the systems are still often more “commercial” and don’t have many of the benefits that the old stick-built ammonia and R22 systems did. Over time this will change; it is changing. But in the meantime, we should all work together to make sure the word com-dustrial dies. :
Greg Scrivener is the lead refrigeration engineer and a partner at Laporte Consultants, Calgary, and works throughout Canada and the U.S. He is a professional engineer and journeyperson refrigeration mechanic. He can be reached at GScrivener@laporteconsultants.com
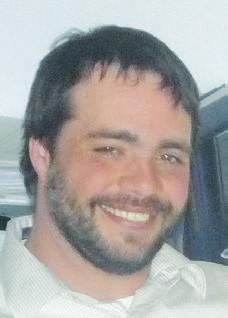