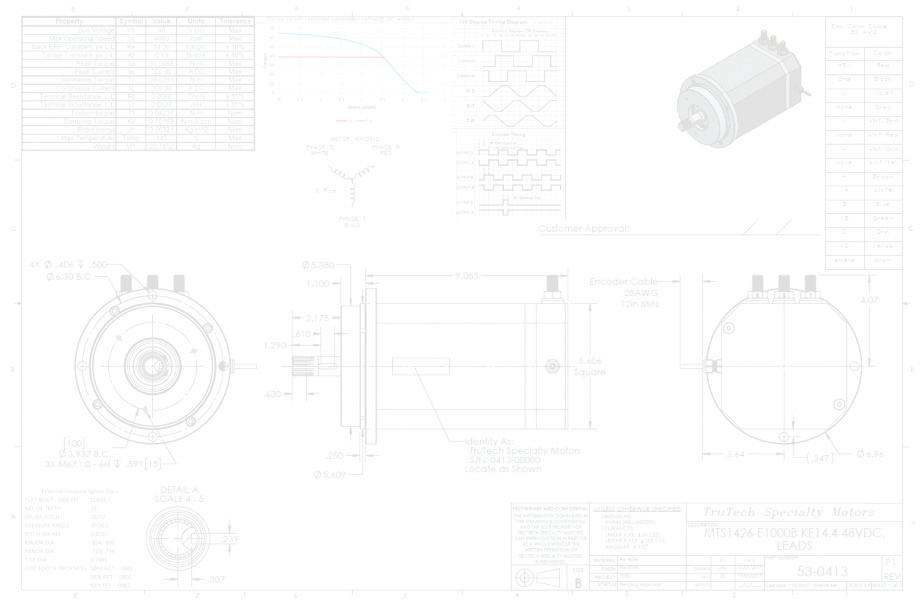
4 minute read
Want Better Performing Equipment to Stay Ahead of the Competition?
Learn how easy it is to optimize servo motors to increase your machine’s performance.
This brief introductory focuses on those OEMs looking to increase machine performance and already utilize or intend to incorporate motion control as the main forces for axes in motion.
It is commonly accepted that today’s machinery depends on performance deliveries that outpace previous methods. However, designers and engineers of tomorrow’s machines continue to be challenged and search for new solutions that meet requirements with greater reliability demands, higher quality standards, and increased production outputs. Providing results is expected regardless of existing equipment with projected upgrades or completely new machine designs. Along with the right choice of motion system for controls and drives, servo motors are the key elements that help provide unsurpassed machine performance.
Most machinery and equipment today have competitive equivalents, and each have their following. Many other machines exist that have no equal, and these continue to carve out niches in their respective fields. Servo motors installed on all types of equipment are main components of these machines. Irrespective of the application or industry that equipment is intended for, the machines themselves are purposely designed to produce certain products or process methodologies. Why shouldn’t servo motors follow suit? Controllers and drives traditionally enjoy enclosure comfort, whereas servo motors are directly embedded into the machine itself. Plain and simple, designing the machine around the motor may not provide for best results. Whereas, designing the motor around the machine most certainly does!
Choices for, and implementation of, servo motors have a vast range of possibilities. Market available models come as standard for many suppliers and the applications where they are applied can vary as well. Catalog solutions from suppliers can already fulfill a multitude of needed motion requirements and these are widely acceptable. Where slight motor changes may be preferred, some modifications can generally be accommodated, but many suppliers may request that machine designers alter the machine to fit the motor instead. Where more significant changes to the motor are requested, but standard elements still need to be implemented and applied where possible, more in-depth considerations may be undertaken; but many suppliers simply cannot provide a solution, thus leaving the machine builder to consider yet more machine alterations. Worse yet, when it appears as if the design of the motor is so unique that limited choices, if any, escape machine designers and/or engineers attempting to meet the new requirements, a machine redesign may be necessary. Going the route of a custom motor design is deemed too complicated, assumed to take too long for delivery of prototypes, or becomes too expensive. Well, not anymore!
Partnering with the right servo motor solutions provider can be an extension of the OEM’s design and engineering teams. Working alongside the OEM’s preferred motion control systems manufacturers of controls, drives, feedback etc., machine builders can not only have designs tailored and delivered to exacting needs, but also help the OEM be more than cost competitive overall. In fact, provided motor solutions have resulted in deliverables that exceeded initial projections. In many cases, some mechanical parts can be removed from the machine given the final motor conceived and designed. Some motors can become completely integrated into the machine with various sub-assemblies.
Low voltage, IP67, BLDC motor specifically designed for submersible use.

Better still, and when taking a larger systems approach, many elements providing motion for an axis can be incorporated into a single unit and delivered as a more complete motor system assembly. Just think about it, if one can consider a reduction of machine complexity, it is no longer just a motor conversation but a realization of how to help make the machine exceed expectations or expand to new possibilities!
Armed with new, and more complete information available from TruTech Specialty Motors’ white paper, “Optimizing Servo Motors for Increased Machine Performance,” (awgo.to/dqjgo) machine designers and mechanical engineers can provide their companies with the solutions they seek. Opting for servo motor manufacturers that partner with the OEM to provide overall solutions dedicated to helping maximize a machine’s operation will deliver excellent results. With optimized servo motors that are pure form, fit, and function, a new era in machine performance can be fulfilled.
IP67, 300mm (O.D.) hollow shaft, high voltage and torque, outer rotational BLDC motor used in food processing.
IP67, 330mm (O.D.) BLDC motor used in submersible water pumps optimized for delivering high torque at low speeds.
IP 68 seamless enclosure, stainless-steel housing BLDC servo motor with watertight cable entry glands and customer-specified pitched screw shaft adapter for harsh environment compliance.
There are many ways to detect an object...
By light...by sound... ...by physical contact...

The real challenge is determining the best method; and then becoming an expert in that discipline. For over 95 years, Telemecanique Sensors has been a world leader in detection
technology, making the choice of of a sensor “partner” obvious.
Need to see, hear, feel, or sense an object’s presence? Browse a comprehensive selection of photoelectric sensors, ultrasonic sensors, limit switches, inductive sensors, pressure sensors and more at www.tesensors.com