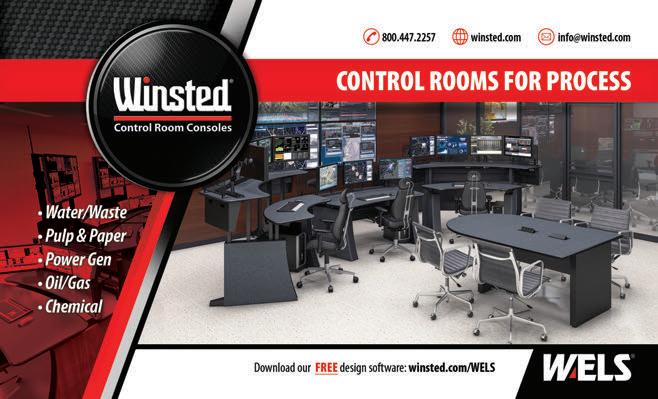
5 minute read
How Automation Advances A ect OEE
How Automation Advances Affect OEE
Overall Equipment Effectiveness is a long-used equation to determine the effectiveness of production machines. But as automation technologies—and their associated analytic capabilities— rapidly advance, what role does OEE serve as industry digitizes?
Few argue about the value of production insights delivered by the well-known OEE calculation. In essence, OEE is a great tool to help understand how well a line is running. This metric can be used to compare similar production systems and determine where improvements can be made most effectively.
If you're wondering whether or not you need to replace or fix equipment on a line or if you can get more productivity out of an existing line through targeted investments, OEE can be very valuable.
But to deliver insights precisely enough to be of real value in determining new investments—especially in light of all the advances that have been made in automation technologies over the past few years—OEE needs context. And to understand how to connect OEE calculations with operational context as industry increasingly digitizes its operations, Automation World connected with Sam Russem of system integration firm Grantek to get a better grasp on this issue for an episode of the “Automation World Gets Your Questions Answered” podcast series.
OEE AS A TOOL
Russem noted that a common mistake he sees manufacturers make when installing software or systems to help determine OEE is that they expect the system alone to drive improvements. “OEE is a tool,” he said. “It's another tool in your toolbox to let you know where you're struggling. But it's not a prescriptive system that tells you necessarily how to fix a specific problem. So for OEE to drive extra value into your business, you need some type of program and the proper funding around it, whether it’s a continuous improvement engineering team focused on identifying and driving those projects for improvement based on OEE data, or the use of more in-depth analysis tools.”
Despite OEE’s inability to deliver prescriptive corrections on its own, Russem said OEE can illuminate a lot of other roadblocks that could hinder a digital transformation program. “OEE can serve as a checklist to see how ready you are for digital transformation initiatives,” he said.
OEE is capable of doing this because of the core production information it provides. “So much of digital transformation is about collecting data and putting the proper context around it to drive more informed decisions,” Russem said. “And an OEE project is going to require you to collect some standard data from each of your lines and machines, which means that all those machines need to be networked or somehow communication-enabled to send the raw data to a server or system that can put information around it. It doesn’t have to require the use of cloud computing technologies or machine learning, but it does need the framework to collect and transmit the data. In itself, OEE is not that type of modern transformative technology that I personally associate with digital transformation or Industry 4.0, simply because it's a metric that's been around on paper for years and years. But it is valuable within a digital transformation initiative as a benchmark to see if you're ready for other data enablement projects and to determine if your digital system [is robust enough to] prescribe changes or identify the key performance indicators to focus on to measure the effectiveness of digital transformation projects.”
For OEE to play an effective role in the digital transformation of a manufacturing business, the data collection and transmission systems supporting it must be installed and used correctly. Based on his work with a variety of manufacturers, Russem highlighted three common areas that tend to create problems for manufacturers when they're installing systems from which they can derive OEE. Those roadblocks are: infrastructure, data integrity, and data contextualization for ERP integration.
Infrastructure is a significant roadblock because of the expense. “If you're not collecting data, because you need to get more machines on the network or upgrade PLCs, you might find that the cost of that infrastructure and hardware is going to be higher than the actual cost of the OEE system,” noted Russem. “To overcome this, manufacturers have to think bigger and consider all of the other value beyond OEE that infrastructure upgrades can bring and how that's going to contribute to the overall digital platform. Any digital transformation project is going to need data, so putting the infrastructure in place to support an OEE program will also support the rest of your digital transformation initiative—and that helps support the financial justifications needed for these upgrades.”
Data integrity is another particularly tough roadblock for many manufacturers, according to Russem. “Maybe your part counters aren't accurate; maybe the downtime code sent to OEE isn't really what stopped the line; maybe the way the system counts rework doesn't align with the way it was formerly calculated on paper. Any of these can cause people to not believe the data going into or coming out of the system, and that can lead to a loss of faith in the systems and hinder buy-in and acceptance of it very quickly,” he said. “For these reasons, it’s critical to include time for data validation and to have a plan in place for what you're going to do if you do find a gap during the validation.”
The third issue Russem noted is data contextualization for use by an ERP system. An OEE calculation should be based on what product is being produced on a given line, Russem said. “This can be really valuable if you're expecting to find di erent evaluations based on what SKU you're running and you want to investigate those di erences. Or maybe you have di erent ideal performance and throughput rates, depending on the product you're running. In either case, the system needs to know that to make sure you're benchmarking against the right thing.”
Russem added that this kind of information isn't always available when starting a new OEE project—and that might mean some level of ERP integration is going to be required. “In that case, OEE becomes your first step in enabling the digital transformation by connecting production systems to enterprise systems as well to lower-level automation technologies to exchange data automatically,” he explained.
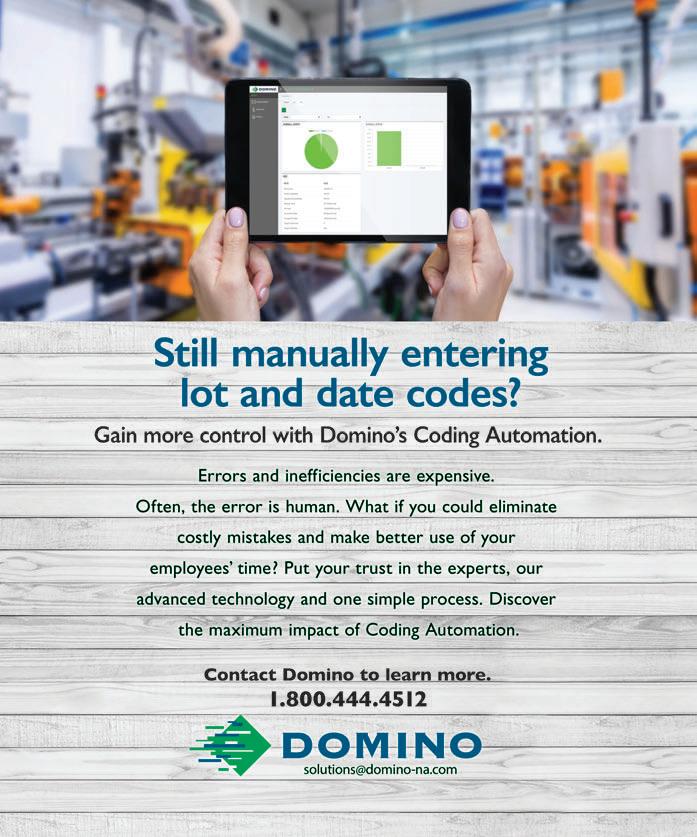