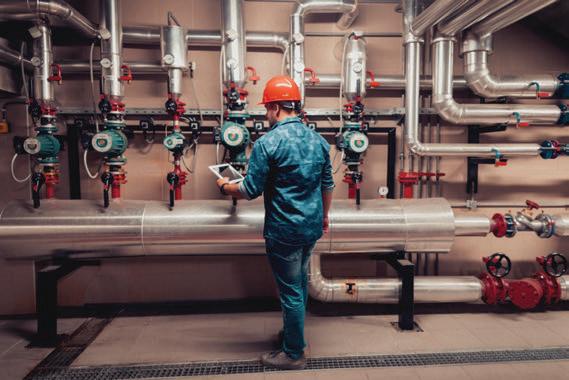
7 minute read
PERSPECTIVES
e aintenance inance afety Connection
By David Greenfield
Editor-in-Chief/Director of Content
Most coverage of computerized maintenance management systems (CMMS) tends to focus on their ability to reduce downtime, guide maintenance teams, and improve production operations. What’s not typically discussed is how CMMS can be used to mitigate physical and financial risks.
Paul Lachance, senior manufacturing advisor at Dude Solutions (a CMMS supplier), noted the following downtime statistics for industrial shop floor operations: • In 2016, the average cost of downtime across all businesses was $260,000 per hour—a 60% jump from 2014, according to Aberdeen Research. In some industries, the cost is considerably higher. In the auto industry, for example, downtime can cost up to $50,000 per minute or $3
million per hour. • The true cost of downtime is unknown.
Consultants believe that 80% of industrial facilities are unable to accurately estimate their downtime. A common estimate is that factories lose anywhere from 5% to 20% of their productivity due to downtime. • Human error causes 23% of unplanned downtime in manufacturing—2.5x higher than other sectors, according to ServiceMax. • A 2017 ServiceMax survey found that 70% of companies lack complete awareness of when equipment is due for maintenance or upgrade. • Manufacturers experience an average of 800 hours of downtime every year.
“There are risks all around us. Life and work are all about balancing those risks,” said Lachance. “Some are financial risks, like unplanned downtime, poor financial planning due to inadequate information, or even compliance gaps. Others are more operations- and team-related risks, such as safety, team ine ciencies, or even poor communication.”
Compliance
Providing an example of how CMMS can be used to mitigate operational risks, Lachance pointed to ISO and OSHA compliance. “ISO 9000 is a way of measuring your quality management systems,” he said. “Failing an ISO audit can lead to extra burdens, increased direct and indirect costs, and loss of goodwill with clients, vendors, and suppliers. OSHA-related violations certainly create financial and operational risks. Team safety is clearly a primary goal, but the secondary costs of an OSHA-
related issue can be significant.”
Lachance said a well-implemented CMMS can be used to address numerous ISO 9000-related needs via features such as: • Automated preventive maintenance; • Well-documented work and safety procedures; • Reporting and record-keeping for audits.
“Having your job safety analysis, safety data sheets, and lockout/tagout procedures alongside your standard preventive and corrective maintenance work order instructions will help mitigate safety issues in the first place and also show an auditor you are serious about that mitigation should an issue arise,” said Lachance.
CMMS software can also recognize a safety-related work order and automatically associate a safety o cer with the order, bump up the priority of the issue, and send an email notification. Likewise, a CMMS can automatically re-alert the team about a work order that’s been sitting around too long.
“Your CMMS can also manage approvals for a project, purchase, or closing a work order,” Lachance said. “Mitigating operational shop floor risks is greatly aided by a CMMS with dynamic routing, notification, and escalation.”
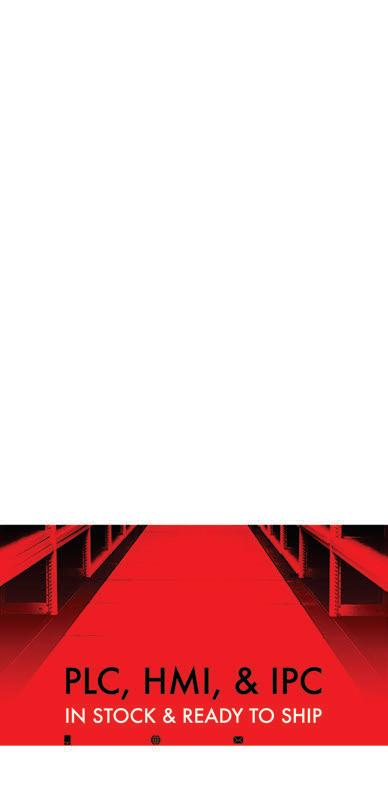
Communication
A CMMS can also be used to help your team, vendors, contractors, and even assets communicate. “Your CMMS dashboard can be setup to show you many KPIs (key performance indicators). For example, improving your ratio of preventive-to-corrective maintenance is essential. To do this, set a goal and publish it on your dashboard. That way it will be hard to ignore if you see it all the time and continue to work with your team to help improve.”
In addition to the safety-related notifications Lachance pointed out above, notifications are another example of how to improve communications with CMMS.
“When you are low on parts, a CMMS can alert you via email or notification on your dashboard,” he said. “This will help you avoid those dreaded stock-outs or missing a key spare part when you need it. Likewise, as work orders are assigned to team members, contractors, etc., you can make sure they get a notification with a quick link into the CMMS. This will help shorten response times and catch problems quicker. All of this is assisted with a mobile CMMS.”
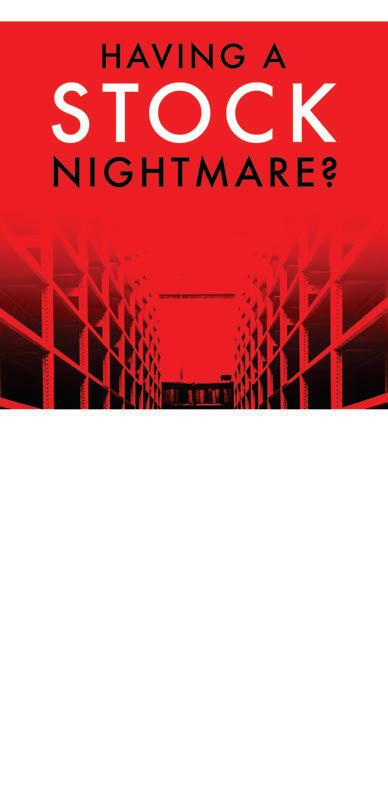
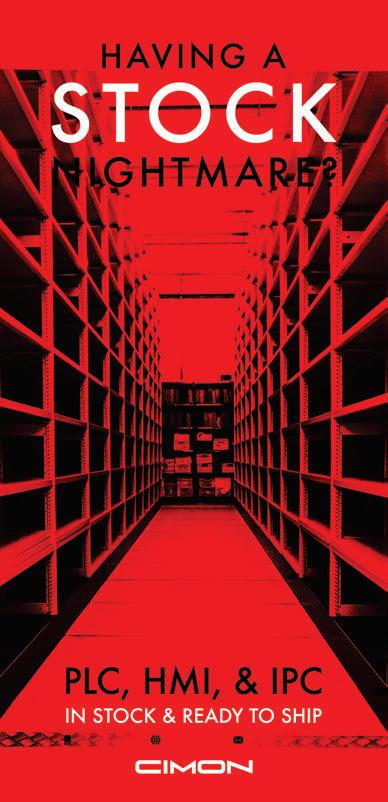
Video Games and the Industrial Digital Twin
By David Miller
Senior Technical Writer
Digital twin simulations that provide end-users with a virtual copy of plant assets and production systems, though not yet ubiquitous in industry, have been used for tasks such as production monitoring for some time now. However, new contributions from the fi eld of video game development may both expand the core functionality of digital twins and extend their use from operations management to other departments such as sales and marketing.
According to Brad Hart, chief technology o cer at Perforce Software, video game engines such as Unreal, which gave its name to the popular “Unreal” fi rst person shooter franchise, boast sophisticated visualization capabilities and complex physics engines that make them the perfect tool for enhancing digital twin simulations. Current industrial digital twin software is, for the most part, highly technical and may require an engineering background to fully comprehend. By improving the accessibility, quality, and realism of the visualizations, game engines like Unreal could help unlock new applications for digital twin technology.
For instance, automotive manufacturer Audi has brought physical data from its digital twin production pipeline into the Unreal engine to simulate the design of new vehicles. Not only can the performance of these vehicles be tested in a virtual environment, but their designs can more easily be exhibited to corporate executives in a highly realistic and interactive manner long before a single unit is actually produced. Similarly, aerospace companies that build private jets can share design blue prints with customers far more e ectively via the use of a digital twin simulation.
“Think about 3D models put out by digital twins in the past. They’re still for engineering minds—not for the sales team, marketing executives, or consumers,” Hart says. “These people want to be as close to feeling the end product as possible. They want to be able to touch it before it’s physically built. These more sophisticated visualizations open up the utility of the digital twin to more people.”
In addition, the use of powerful game engines may make rapid prototyping, digital planning, and virtual commissioning of plants and equipment easier to achieve. Tests that previously involved complex calculations— even with the aid of a digital twin—can be iterated more quickly through the use of a more robust simulation.
Still, those in industry working on digital twin technology need not fear game developers stealing their jobs. While automotive, aviation, and several other manufacturing sectors are seeking game developers to help them build more realistic industrial simulations, the tasks they are performing complement rather than replace those performed by others.
“Without a doubt, some of the biggest manufacturing industries are bringing game developers onto their sta s to assist with this. It really is opening up opportunities for people in game development to branch out into new industries,” Hart says. “But it doesn’t preclude what people already in manufacturing working on digital twins are doing. We’re just augmenting the skillsets that already exist within these organizations.”
Want to watch this story instead? Tune in to our Take Five with Automation World video. awgo.to/1263
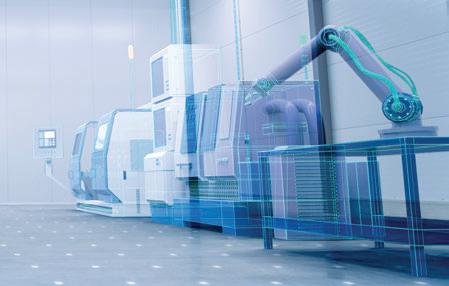
L?34 Û Ãv À vȳ½½³ÀÈË® Èâ to encourage your professional network to stay ahead of the latest trends in industrial automation. Your executive thought leadership is v½³Ü À ˨Üvâȳv½¨ âÈ Ã Û ®ÈƜ®³vÈÈ À ³Üv®â ³¨¨³Ü ÀÃâ³Ë vÛ . As we head into this event we encourage you to share your enthusiasm for the ROKLive event on social media.
` ƺÛ v È vÃâ ³Àâ³Ë â Àv È ® È Ã Ãv½¨ ½³ÃÈà ³Àâ³ËÀ Ë® ¿Ë ½À³ Ãà ³®v¨vË ® ƛ
I?OSŭƝ Join me at #ROKLive to explore the explosion of digital technologies in manufacturing today and learn how industry-leading companies are applying analytics for actual insights. Register now: rok.auto/roklive
I?OSŮƝ The #ROKLive virtual event is your one-stop shop for hot topics in industry. Join us for executive keynotes, exclusive workshops, the DX Idea Exchange and more. Register now: rok.auto/roklive
I?OSůƝ How can we help you shape your digital future? Join us at #ROKLive for keynote discussions on this, digital insights driving innovation, and more. Regster now: rok.auto/roklive
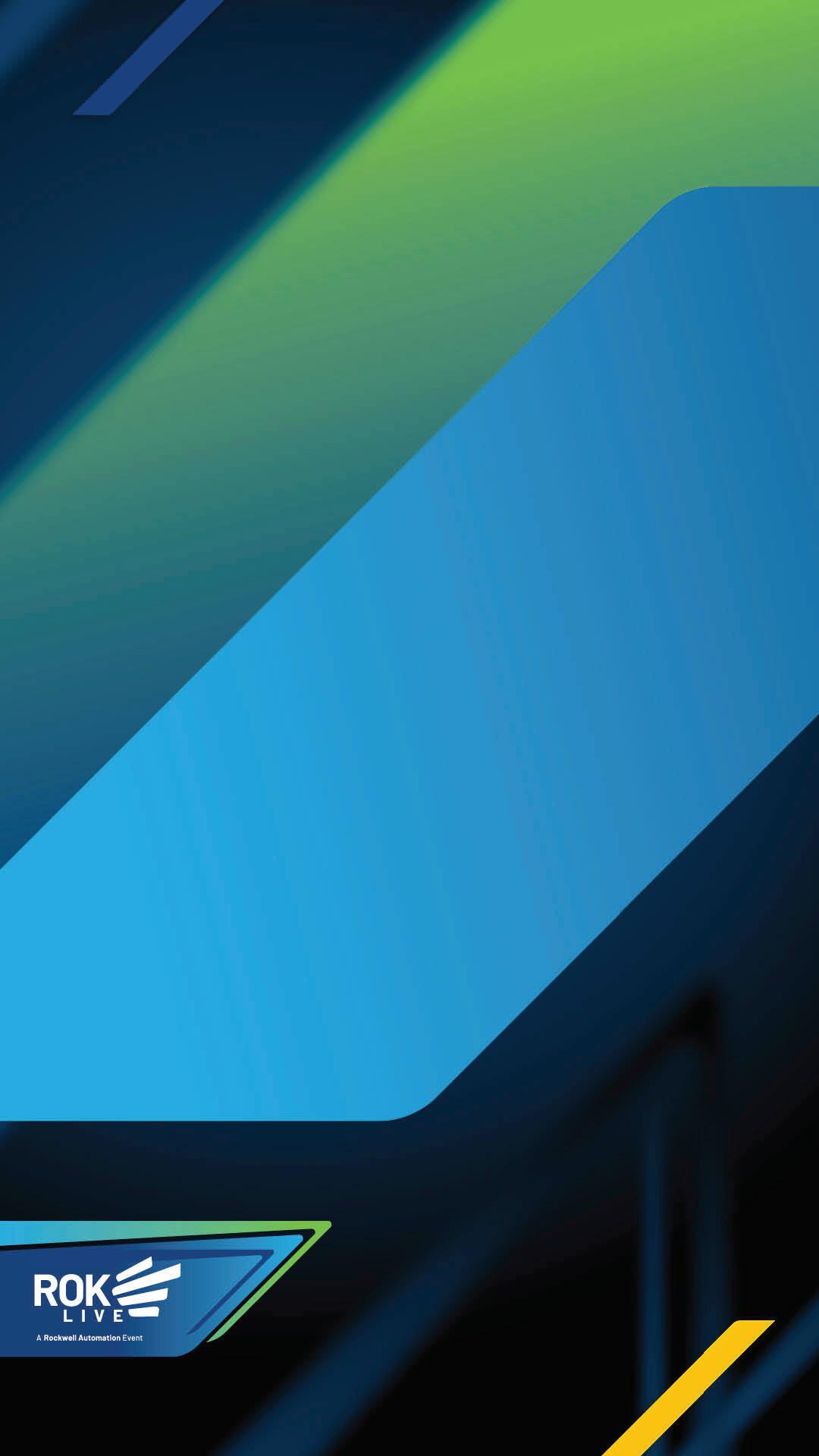