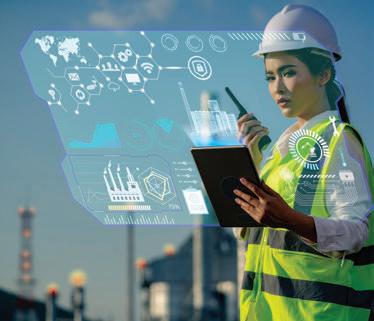
35 minute read
NEWS
Bringing Artificial Intelligence to Remote Access
By David Miller
Senior Technical Writer
IBM announced a new collaboration with engineering consultancy firm Black and Veatch to combine IBM’s Maximo Application Suite of software products with Black and Veatch’s experience in the field of realtime data analytics.
Remote access use has boomed over the past few years, as companies have sought to maximize productivity with fewer onsite workers. According to Automation World’s 2021 remote access survey, 67% of respondent companies are currently using some form of the technology (awgo.to/1264).
However, while pulling so much more data out of plants than in the past can provide new opportunities for optimization, it can also introduce unwieldly complexity. As the volume of data grows, software dashboards can become so overwhelmed with updates, signals, and alarms that important information winds up being ignored entirely. AI (artificial intelligence) can solve this issue by helping end-users sort through the many incoming datapoints more efficiently.
The collaboration between IBM and Black and Veatch will allow intelligence from Black and Veatch’s monitoring and diagnostic centers to be delivered to end-users via IBM’s Maximo Application Suite, which includes applications for predictive maintenance, worker safety, visual inspection, and an assortment of other tasks performed on the plant floor and in the IT department.
As an example of how AI can assist in optimizing maintenance procedures, consider that much maintenance work currently being carried out is preventative in nature. This means it is performed at pre-determined time intervals or in conjunction with pre-selected events believed to precede equipment failures. While this method can be effective, it can be inexact, and may lead to either too much or too little maintenance work being done. In addition, the rigid guidelines preventative maintenance schedules employ fail to take into account contextual factors.
By contrast, AI can help operators shift to a predictive model of maintenance that couples large, complex datasets with contextual information such as weather conditions to construct real-time analytics that can greatly increase the efficiency of maintenance procedures. Without AI, the utility of the additional data may go to waste, as its uses could be limited by the narrow expertise of individual operators.
“Organizations in every industry need to figure out how to use the vast amounts of data generated within their own systems,” said Kareem Yusuf, IBM general manager for AI applications and blockchain. “Monitoring insights that combine AI and machine learning technology with deep industry expertise can help organizations make better sense of their data and use it to manage their assets better. IBM and Black and Veatch are collaborating to deliver insights that can be applied to improve the performance of assets and extend their lifespans."
The Maximo Application Suite is a cloudbased platform, which means maintenance crews, plant managers, and other staff can share a unified view of all operational data across multiple sites. According to IBM, having access to this single source of truth is imperative to achieving optimal results.
To further this drive for unified data, IBM is also adding Black and Veatch’s digital twin asset models to its Digital Twin Exchange, an online resource available to IBM customers that allows them to attain information made available by asset providers. Types of data shared on the exchange include: Bills of material, parts lists, AI models, maintenance plans, user manuals, and 3D computer-aided design (CAD) models for digital twin visualization.
Adaptive Manufacturing Gets Real with New Materials Handling Tech
By David Greenfield
Editor-In-Chief/Director of Content
Adaptive manufacturing is a concept that centers on a manufacturer’s ability to rapidly change production operations to meet the need for demanddriven products—an increasingly important capability for manufacturers as more products are designed for customizability. Meeting such demands is leading technology suppliers to develop automated material handling systems that allow manufacturers to more easily meet the market’s demand for custom products.
To learn more about how technology suppliers are creating these new material handling systems, we connected with Jeff Johnson, U.S. mechatronics product manager at
“By generating electromagnetic fields, the coils float and propel the mover above the surface. And then, by varying these electromagnetic fields, we’re able create free 2D motion, which allows for six degrees of freedom, enabling the mover to travel in any direction we want.” — Je Johnson, Beckho Automation
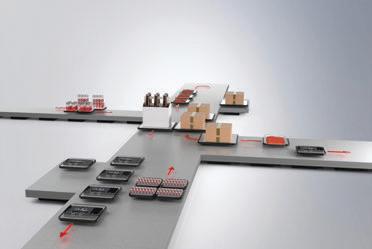
ONE source.
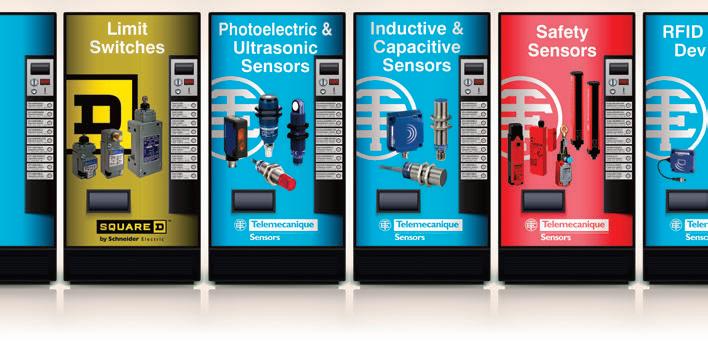
Simply easy!
Beckhoff Automation, for a recent episode of the “Automation World Gets Your Questions Answered” podcast series (awgo.to/1260). Beckhoff is well known for its release of two new mechatronic material handling technologies designed for adaptive manufacturing— XPlanar, which uses levitating tiles to move products or components in any number of directions for processing, assembly, or packaging; and the eXtended Transport System (XTS), which provides for independent control of magnetically driven movers along a customizable, guided path.
In our discussion for this podcast, we focused on XPlanar and how it allows manufacturers to more quickly and easily adapt product flow to meet changing demands because it has no mechanical track to follow. With XPlanar, “you have free motion for quick process changes,” said Johnson. “You can add processes or skip processes simply by changing the path that the movers follow.”
Johnson explained that XPlanar can do this because the movers on the system that transport materials float above the tiled surface based on magnetic levitation principles. These principles are well known and have been used for years in transportation, such as with maglev trains. “With XPlanar, the mover is passive,” said Johnson. “It has permanent magnets arranged in a Halbach array, where you’ve got really strong magnetic fields on one side—in our case on the bottom of the mover—and very weak magnetic fields on the top. The tile contains all the electronics for powering the coils to create electromagnetic fields, as well as all the feedback and diagnostics. So, on the surface of the tile, there are a lot of very flat coils; and that’s where the name XPlanar comes from—these very thin, planar coils in the surface of the tile. By generating electromagnetic fields, the coils float and propel the mover above the surface. And then, by varying these electromagnetic fields, we’re able create free 2D motion, which allows for six degrees of freedom, enabling the mover to travel in any direction we want.”
The XPlanar movers can levitate zero to five millimeters above the surface, with a two-millimeter height being the sweet spot, said Johnson. “At a two-millimeter flying height, we can move up to two meters per second with a 1 g acceleration. We have different mover sizes, and the payloads range from 0.4 to 4.2 kilograms. But they can also be linked mechanically or via software to carry even heavier loads.”
Collision avoidance is handled automatically by Beckhoff’s TwinCAT software, which is the only platform needed for XPlanar configuration, programming, and runtime.
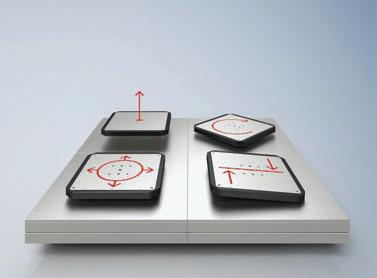
Why levitating movers?
As fascinating as it can be to watch XPlanar in action, practical manufacturing requirements tend to bring cutting edge technology ideas into an understandable and easily deployable form. So how did the futuristic idea of using levitating movers evolve into a material handling reality?
According to Johnson, the idea began not long after Beckhoff’s creation of the XTS more than eight years ago. “We started developing XPlanar six years ago because we were seeing lots of applications that would benefit from free 2D motion,” he said. “With XTS, we have done lots of applications with it, but that’s 1D motion—where we can do very fast, highspeed applications with heavier loads. We saw that need for free movement capability, and XPlanar allows for six degrees of freedom. We can move in the X-Y plane over the entire surface, raise and lower the movers from zero to five millimeters, tilt the movers plus or minus 15 degrees, and we can also rotate plus or minus five degrees while in motion, and perform up to 600 RPMs while stationary. So, the six degrees of freedom opens up the door for many different applications.”
In terms of getting manufacturers to use such a new technology rather than sticking with more well-known material handling systems like conveyors or track systems like the XTS, Johnson said, “if you’re just trying to move product from point A to point B, standard conveyors are probably the right solution. But we’ve found that when you design your process around the XTS or the XPlanar, you can reduce your [materials handling] footprint by 30% to 60%. And from an end user standpoint, XPlanar with the free 2D motion opens up the door to new and innovative designs because your tooling becomes simpler.”
Describing how XPlanar makes tooling requirements easier for end users, Johnson offered an example of processing a carton on which you want to place a glue pattern. “Typically, you’d have a three-axis glue head come over the carton and lay the glue pattern down. That glue head tool can now become a one-axis tool because we can bring it out and drop it down the Z-axis to dispense the glue, and then do the X-Y motions using the mover. That’s how XPlanar enables your tooling to become simpler.”
This even applies to the positioning of tools. “Your tooling doesn’t have to be perfectly level to function because we can tilt
“Every mover can follow a di erent path or go to di erent stations, which delivers on the goal of lot size one. Di erent products can even be running at the same time on the same machine because you’ve got the freedom to layout your machine in any X-Y format.” — Je Johnson, Beckho Automation
the mover so that the material being moved is level in relationship to the tooling. Plus, every mover can follow a different path or go to different stations, which delivers on the goal of lot size one—as every tile does not have to index and follow in line. They can jump out of line to perform any task. Different products can even be running at the same time on the same machine because you’ve got the freedom to layout your machine in any X-Y format.”
And because the 9.5-inch square XPlanar tiles can be grouped in any grid pattern, users can form rectangles, lanes, squares, or even U-shapes with the tiles. “It gives you this flexibility to assemble your transport system around your machine and around your factory,” Johnson said.
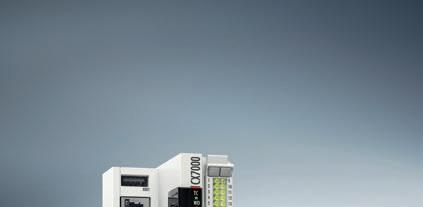
Integration
Because material handling technologies need to integrate with other systems for processing, assembly, and/or packaging, Johnson explained how XPlanar is designed to work with other systems in a manufacturing environment.
“The standard TwinCAT software that comes with XPlanar handles all the functions necessary to synchronize the movers to robots or any other external device for loading and unloading on the fly,” he said. “We can even handle transfer of materials coming in on a conveyor, where the tooling allows for the product to drop into a pocket on the mover. The position and speed of the movers can be sent to external devices to either follow a robot or have the robot follow the XPlanar movers. We could also send speed and position data to cameras for inspection applications. And if you want to do printing on the fly, the position and speed of the mover can be shared for printing in a stationary position or as materials move through the process.

New capabilities
Further highlighting Beckhoff’s new capabilities for XPlanar—the ability to rotate 360 degrees and continuously operate at up to 600 RPMs—Johnson said: “This allows us to apply labels to materials as they are moved, do 360-degree inspection of a part so that the cameras used can be simpler, and orient parts for loading and unloading. The movers’ rotating and tilting motion can be used to create a controlled wobbling motion that’s useful for mixing applications.”
Johnson pointed out that Beckhoff is preparing another new update for XPlanar around a new mover bumper with a unique ID to further enhance mover identification. “This unique ID allows you to track your products even through an XPlanar power cycle,” he explained. “This means you can recover from a power cycle and still know exactly where the movers are to determine if you can continue production as is or if operators need to make adjustments.”
| | EC11-17USA
I/Os built in, powered by TwinCAT: Ultra-compact CX7000 Embedded PC
100 mm 480 MHz ARM processor
Support the most versatile applications: safety technology compatible with EJ system motion control explosion protection EtherCAT
www.beckhoff.com/cx7000
The CX7000 Embedded PC delivers the efficiency and performance of TwinCAT 3 software in an ultra-compact controller format. This further enhances the scalability of PC-based control technology from Beckhoff ranging from DIN rail mounted mini-PLCs to many-core Industrial PCs. Equipped with a 480 MHz processor and 12 configurable multi-functional I/Os, the CX7000 offers an attractive price-performance ratio and exceptional flexibility. The CX7000 supports simple system expansions using the Beckhoff I/O terminal system.
ARM Cortex™-M7 processor (32-bit, 480 MHz) Compact dimensions: just 49 x 100 x 72 mm Multi-functional I/Os allow variable use: 8 digital inputs, 24 V DC, type 3 4 digital outputs, 24 V DC, 0.5 A, 1-wire technology fast counter input encoder input 2 analog 0…10 V inputs 2 PWM outputs
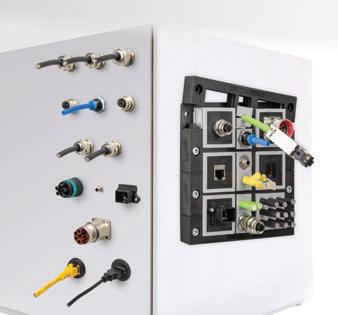
By Sean Riley
Senior Director, Media and Industry Communications, PMMI
The packaging and processing community came together September 27-29, 2021, for perhaps the most important PACK EXPO Las Vegas and Healthcare Packaging EXPO in its history, according to show producer PMMI, The Association for Packaging and Processing Technologies. More than 23,000 attendees, eager to find help with current challenges, engaged with more than 1,500 exhibitors across four expansive halls with more than 740,000 sq. ft. of exhibit space at the Las Vegas Convention Center. It serves as the largest trade show in the U.S. in 2021 so far.
“In a word, PACK EXPO Las Vegas and Healthcare Packaging EXPO was a success,” said Jim Pittas, president and CEO, PMMI. “Exhibitors and attendees alike were energized by the number of people who attended and— more importantly—the business conducted from the moment we opened the doors on Monday.”
As PMMI’s State of the Industry report highlights, 2020 was a record year for packaging machinery, with the total size of the market in the U.S. increasing to $12.3 billion, growing 14.4%. In the case of domestic shipments, growth of 14.7% reached $9.4 billion for this segment, reported Jorge Izquierdo, vice president of market development for PMMI, during Monday’s media briefing at the event. This record year led to the industry’s readiness to come together to see the latest innovations in person.
PACK EXPO Las Vegas and Healthcare Packaging EXPO was more than just a packaging and processing equipment show, with more than 80 free educational sessions. Hungry for new information, attendees took advantage of the opportunities at the Forum and at the PACK to the Future and Innovation Stages located throughout the show floors. Many also accessed digital showrooms and select show content online via PACK EXPO Xpress, which debuted this year to extend the show’s reach beyond the convention center’s walls. All registered show attendees can continue to access PACK EXPO Xpress until Nov. 19.
Thousands of attendees flocked to the North Hall to take a journey through the evolution of packaging and processing at PACK to the Future. The curated exhibit included 26 historic packaging machines dating from the late 1890s. The machinery was surrounded by imagery supplied by museums and manufacturers such as Coca-Cola, General Mills, Kellogg, Hormel, Anheuser-Busch, and Merck. A highlight of the show’s second day came early when nearly 500 industry professionals gathered for the Packaging and Processing Women’s Leadership Network (PPWLN) breakfast. Keynote speaker Tracey Noonan, co-founder and CEO of Wicked Good Cupcakes, reflected on her experience scaling an e-commerce business and managing a growing workforce. She was joined by Yolanda Malone, vice president of global R&D Foods at PepsiCo, and PPWLN co-chairs Jan Tharp, president and CEO, Bumble Bee Seafood Company, and Sharron Gilbert, president and CEO of Septimatech Group Inc., for a candid conversation about the new world of work and what it means for the future of manufacturing.
PMMI heads east for the next event in the PACK EXPO portfolio of trade shows, with registration officially open for PACK EXPO East (March 21-23, 2022; Pennsylvania Convention Center). Now in its fifth edition, the three-day event returns to Philadelphia after a record-breaking PACK EXPO East 2020 that featured 7,100-plus attendees and its largest show floor to date. For more information, visit packexpoeast.com, and for all show related information visit packexpo.com.
ROUTING ALL KINDS OF CABLES AND CONNECTORS THROUGH 1 KNOCK-OUT WITH IMAS-CONNECT™ www.icotek.com
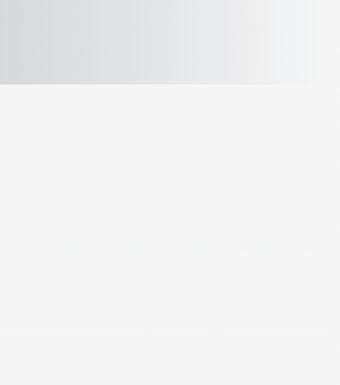
Evaluating Support For The Internet of Things
As manufacturers digitally transform their operations, finding the right technologies can be an overwhelming process. Don’t overlook your supplier’s ability to provide the right level of support when assessing technological capabilities.
By Lauren Gibbons Paul, Contributing Writer
Though the devices used in many Industrial Internet of Things (IIoT) projects may not be entirely new, the architectures used to facilitate IIoT levels of data aggregation, sharing, and analysis tend to be of a more recent vintage. So, even though you may be experienced in working with the types of controllers, sensors, and I/O systems used for IIoT initiatives, having access to quality support from your technology supplier(s) is critical to your project’s success.
But how do you go about assessing the level of support you should expect from a technology supplier for an IIoT project?
First, it’s important to realize that the evaluation should go far beyond knowing who will pick up the phone when you call—though this is an important aspect. The supplier’s support team should also be able to help you figure out the value proposition of the IIoT project you’re looking to implement. They should be
able to help guide you in understanding what you can realistically expect to get out of the project, in operational terms, as well as the return on investment (ROI).
The support you get from your technology supplier should also address the design work typical at the beginning of an IIoT project. Scott McWilliams, vice president of global operations consulting at Emerson Automation Solutions, says, “IIoT opens up a new world and a new approach to how we design [automated production systems]. A vendor on a typical continuous-improvement project might only consider process design issues, but that typically just covers the inputs and outputs of one part of the process. Now, with IIoT, you’ve got to look at the inputs across an entire endto-end process—because some critical inputs may originate in a business system outside of the plant. You’ll need the vendor to sit down and help you think out the whole process from the very beginning with a focus on how to improve both process efficiency and efficacy.”
Swagelok’s experience
Swagelok, a manufacturer of components for gas and fluid systems, was looking for a way to automatically monitor, record, and escalate its assembly process. To do this, the company needed to make information from its Allen-Bradley PLCs more readily available so that its support team could have quicker visibility into its shop floor operations.
Doing this via an Industrial Internet of Things (IIoT) project seemed a natural fit for collecting, sharing, and analyzing the relevant data. Matt DeLuca, quality engineer for Swagelok, says the company selected Opto 22’s groov EPIC (Edge Programmable Industrial Controller) for this project in no small part due to the quality of Opto 22’s support.
“When we first started, they gave us a very in-depth demo to explain the capabilities of the devices. Between then and now, we have done a handful of virtual training sessions and webinars that have helped us take our implementations to the next level,” says DeLuca. “Any time I have a question or issue, I have direct contacts with Opto 22, not an automated phone service. Their team has been more than willing to meet with our engineers and support teams to talk about additional features we would like to see or if a best practice could benefit us.”
Opto 22’s support staff are all engineers with access to an array of test equipment on hand to duplicate customers’ exact issues.
IIoT Vendor Support Checklist
Look for suppliers with support sta featuring engineers and those who’ve had hands-on experience with the products.
Make sure the vendor doesn’t overly rely on the use of scripts. Ask if product support engineers have equipment available in their workspace to emulate customer issues.
Find out if the support sta can share best practices. Support sta should be interested in hearing how the company can improve its products and services.
Opto 22’s groov EPIC (Edge Programmable Industrial Controller). Source: Opto 22 IIoT support: What to look for
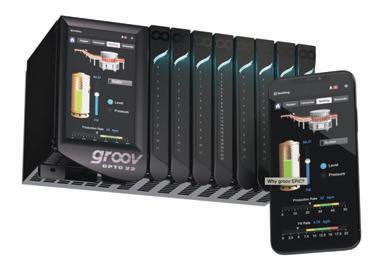
Customers beginning an IIoT project should look to their vendors not just for expertise in the products they sell, but for an understanding of the larger technology landscape, says Garrick Reichert, application engineer at Opto 22.
“They might need help setting up their IIoT solution to succeed,” adds Reichert. “That’s why we engage in these conversations very early on. We get involved in designing the architecture of the system so that when it comes to any support needs they have later, we understand it from start to finish.”
Emerson’s McWilliams advises end users to question how they are supported in three stages of an IIoT project: pre-sale, go live, and post-implementation. “It’s not enough that you can call someone when the green light doesn't go on,” he says. That’s why pre-sales consultations are critical to ensuring you pick the right architecture and support to achieve the benefits you seek.
The customer needs to fully understand IIoT and the implications of the choices they make, says Travis Cox, co-director of sales engineering at Inductive Automation. “That means being transparent about things like data transport—do they own the data or not; and is it transported through an open mechanism where they can use a different cloud service. These aspects are really important.”
Cox adds that customers need to see
that their technology supplier will be a committed partner. “You don’t want to call in and always get somebody different or have a person reading off a script. You need to be able to talk to someone who knows what they’re talking about.”
The vetting process
Labor shortages driven by COVID-19, coupled with increasing retirements in the manufacturing workforce and the relative newness of IIoT architectures, means that finding knowledgeable support personnel can be difficult.
“Many IoT platforms are relatively new to the market, so finding experienced IoT developers and solution architects to work on and maintain a system is a challenge,” says Richard Mizuno, Asia-Pacific principal and regional director at Kalypso, a Rockwell Automation company.
When vetting potential suppliers, keep in mind your need for support will stretch beyond system design, implementation, and maintenance.
Keith Chambers, Aveva’s vice president of operations management software, notes that one of the most critical moments in an IIoT project is when you revisit it to determine if it is delivering on its promise. After finishing a proof-of-concept project is a perfect time to make key adjustments to ensure ROI, he says.
It’s important to realize that “you’ll likely need to fine-tune the solution to deliver real value before you can justify any bigger investments to expand it in one plant or roll it out to others,” says Chambers.
Swagelok production operator. Source: Swagelok
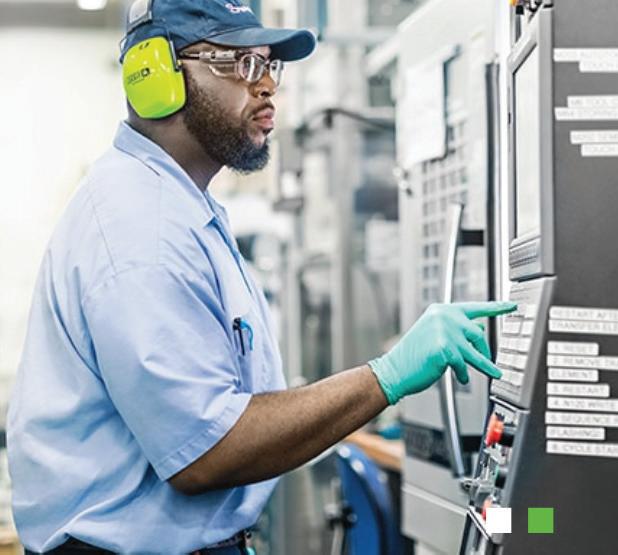
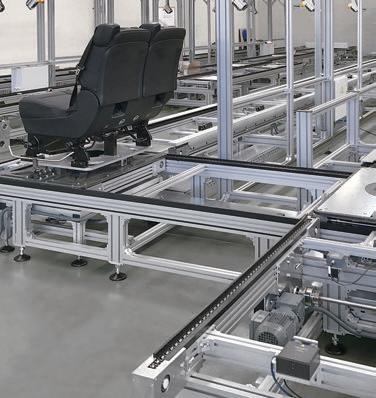
Improve Quality and Output
by streamlining applications with pallet-handling conveyor systems
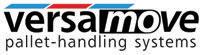
Standard Products for Custom Solutions: Pallet loads up to 800 lbs./ea Pallet sizes up to 1,200x1,200 mm Repeat accuracy ± 0.1 mm Indexing or accumulation Now with ALL ELECTRIC devices
(860) 769-5500 | info@mknorthamerica.com

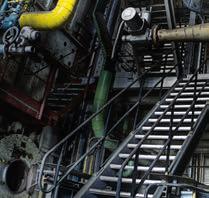
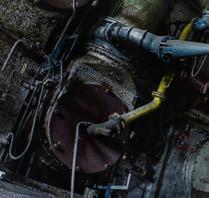

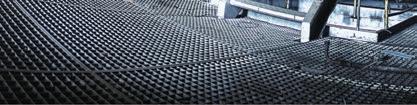
IIoT Retrofits for Legacy Equipment
If you’re like most manufacturers, you’re not operating a greenfi eld site with the latest internet-ready equipment. Nevertheless, you’re likely facing a number of digitalization initiatives. Here’s how you can do it via strategic retrofi ts to existing equipment.
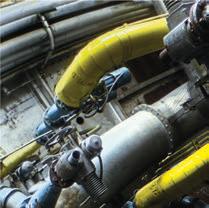
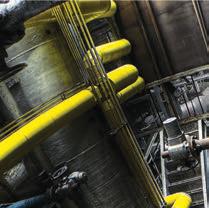
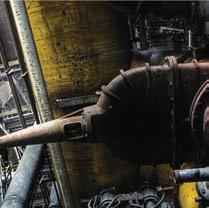
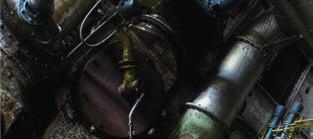
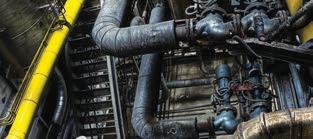
By James R. Koelsch, Contributing Writer
Don’t cry over spilled milk, beer, or anything else for that matter. Why? Because there’s no longer any need to put up with spillage and other forms of waste just because your installed base of equipment is too old. You can solve many of these problems by retrofitting your legacy equipment to give you the connectivity and visibility promised by the Industrial Internet of Things (IIoT) to reduce waste.
Just ask Joe Vogelbacher, CEO and co-founder of the Sugar Creek Brewing Co., a craft brewery in Charlotte, N.C. Retrofitting a bottling line there with IIoT technology has allowed operators to control foaming as beer moves from tank to tank. Even slight variations in pressure and temperature can generate foam, which translates into enough spillage to cost the brewery $30,000 a month in lost revenue.
Operators can now interact with the process in real time from anywhere in the brewery, thanks to help from Bosch Rexroth Corp.
“Together with Sugar Creek, we mapped the value stream and began to analyze specific pain points,” said Armando Gonzalez, Industry 4.0 business leader at Bosch Rexroth. “From there, we were able to determine the amount of waste and how that translated in terms of value.”
Bosch Rexroth engineers then helped the brewery’s staff understand how IIoT technology could help them achieve some quick success.
The retrofit team added not only IIoT sensors to the beer tanks, but also Rexroth’s IIoT Gateway to report fill levels and temperature. Once analyzed, these data points are available to operators on their laptops, tablets, or mobile phones. With information easily accessible and the ability to adjust setpoints remotely, Sugar Creek Brewing Co. saved $120,000 in 2019 alone.
Planning is crucial
Like any other technology, successful IIoT implementation requires a plan that makes good business sense. Developing such a plan helps avoid over-retrofitting, the most common mistake that users make, according to Manish Chawla, general manager for the industrial sector at IBM Corp. “The primary consideration should be clearly identifying what the ultimate goals and business benefits are for retrofitting a given piece of equipment,” he advises. “There needs to be a business purpose for every single sensor that someone wants to install.”
These purposes usually include some benefit for such things as cost, safety, quality, and throughput. “The most impactful place to start one would be to look at where your biggest problems are,” suggests Dave Eifert, senior business development manager for IIoT at Phoenix Contact USA. “Look at one of these aspects in a very granular way and imagine what it would take to eliminate that one problem.” If more data and information about the process will help you to understand and solve the problem, then it could be a good application for IIoT.
Automation experts warn beginners to be selective when deciding what data to collect. “The influx of too much data can create analysis paralysis,” explains Trevor Diehl, vice president of research and development at DelmiaWorks, a supplier of enterprise resource planning software. To avoid this problem, he suggests working with quality professionals to identify three to five signals to start with—and certainly no more than eight.
An oft-forgotten consideration in the planning process is the long-term maintenance of any added sensors. “Making sure that sensors are calibrated appropriately is a long-term difficulty that few people plan for,” observes Diehl. Besides experiencing some drift that occurs naturally over time, sensors also eventually fail in industrial settings because they are installed in hostile environments, such as on vibrating machinery, in electromagnetic fields, and near heat sources.
IIoT with existing controllers
Once the goals and benefits are established, the next step for planning is to weigh them against the value and cost of the technology available to achieve them. The good news is that adding IIoT devices usually does not require replacing the existing controller. One reason is that IIoT is no longer limited to adding discrete sensors decoupled from the traditional control hierarchy. It can now include distributing data already available through PLCs.
“The controls world has been rapidly assimilating more IIoT technology,” explains Diehl. He points to the ability of technology like Rockwell Automation’s FactoryTalk View to connect to an OPC server, which is a common IIoT aggregator of data from a PLC. “So, it’s very possible to get relevant IIoT information from your existing equipment once it’s hooked into the right aggregator.”
“Many older controllers have some way of communicating valuable data, even if it’s over older protocols such as serial or DeviceNet,” adds Daymon Thompson, U.S. software product manager at Beckhoff Automation. Consequently, IIoT and other digitalization technologies can usually read data from these legacy controllers and then transmit it via an IIoT communication standard like MQTT, HTTP, and REST. “However, doing this requires adding a device to the system as a communications gateway.”
These gateways work alongside existing PLCs to send selected data to an on-premises or cloud-based system for the application of analytics. Eifert at Phoenix Contact recommends starting by leaving the existing control system in place and applying edge gateways in parallel. “It’s usually best to start small and learn to avoid potential pitfalls before pursuing projects with higher risk-reward profiles,” he says.
Then, you can weigh the benefits of replacing the
PLCs as it makes sense during subsequent upgrade cycles. To permit this option, Eifert suggests using IIoT technology that can be applied incrementally. An example is Phoenix Contact’s PLCnext, which can serve as both an edge gateway and a PLC. It can be applied incrementally alongside an existing PLC, communicating locally with the PLC via such protocols as Modbus TCP, EtherNet/IP, or even Modbus RTU. Its Linux-based operating system allows using open-source programming tools like Node-Red as a link to the IIoT world.
Thompson reports that most IIoT upgrades involving Beckhoff Automation’s PC-based controls have entailed updating software to add functionality and communications in the controller. “In cases with very old equipment, it is straightforward to add a small gateway device and use our Data Agent software to read data from the existing controller and then map it to IoT communications protocols,” he says.
Such hardware can typically do much more than that, though. “A local IoT gateway can also do some of the computing at the edge before sending any information to the enterprise level or to the cloud,” says Thompson. Processing information at the edge can reduce network traffic and minimize the data being sent to higher-level systems.
An application requiring high-speed data will mostly likely need on-premises or edge computing. “These datasets often also need to roll up into an overarching corporate or enterprise view to assess holistic impact,” notes Chawla at IBM. “So, you need a welldefined architecture that specifies where data needs to be processed.”
Here, a common mistake is to take a strictly linear approach of processing the data either on-premises or in the cloud. “This approach can limit the value you’re able to gain from the data,” says Chawla. To avoid such limitations, he urges users to consider an open, hybrid architecture because it offers the flexibility to process data on-premises for speed and agility, as well as to reap the benefits of access to the cloud.
A tale of two constraints
Two important constraints for planning an IIoT retrofit are whether the equipment is instrumented and designed to communicate externally. “An application consisting of multiple connected, instrumented systems using controllers capable of communicating with industrial protocols is going to be a lot more straightforward,” notes Josh Eastburn, director of technical marketing at Opto 22. “Basically, you just need some good gateways or a single edge controller to bridge those different automation networks, and then pipe that information to wherever you want it to go.”
He adds, however, that establishing connectivity has been more difficult for un-instrumented equipment not designed to communicate externally. The low-cost option was to add the necessary instrumentation, send the data to a datalogger, and manually transfer the collected data to a spreadsheet. A more expensive option was to invest in a continuous logger, RTU, or PLC—which was pricey for just one piece of equipment and didn’t scale well for multiple machines. A Raspberry Pi was
The slightest change in temperature and pressure can cause foaming on the bottling line at Sugar Creek Brewing. To control this form of waste, the brewery turned to Bosch Rexroth to retrofit its line with IIoT technology. Source: Bosch Rexroth Corp.
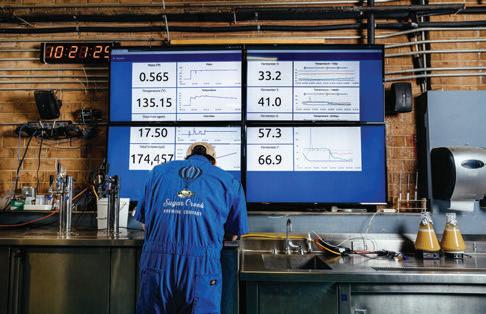
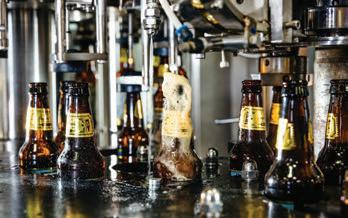
Technicians at Sugar Creek Brewing receive data from the bottling process via IIoT sensors and a Bosch Rexroth IIoT Gateway. Source: Bosch Rexroth Corp.
cheaper, but it tended not to work well with industrial I/O signals and was often too fragile for industrial environments.
For simplicity and scalability, Eastburn suggests an edge-oriented approach, such as that used in a predictive-maintenance program developed for a CNC mill by Enginuity Inc., an engineering firm in Halifax, Nova Scotia. Because CNC machines are usually not designed to collect or publish all of the necessary information for overall equipment efficiency (OEE) tracking, Enginuity’s engineers added sensors for measuring vibration, temperature, and current. They then wired the signals into a groovRIO edge I/O module from Opto 22. Using the module’s embedded Node-Red IoT engine, they collected the signal data, created a real-time mobile dashboard, and pushed data to OSIsoft PI (analytics system) using REST calls.
When either the existing controller is closed or the machine is old enough to be controlled via relay logic, Thompson at Beckhoff Automation says an IoT coupler is another option for reading sensor and motor data directly. In such cases, consider extracting uptime and other OEE data. Beckhoff’s EK9160 IoT Coupler can write sensor or electrical-input data to higherlevel systems in the cloud or on premises using OPC UA or MQTT.
On-machine IIoT
Although IIoT devices are often added at the I/O level, another important place for retrofitting is at the machine level, the same level as an HMI in the control hierarchy, according to Alexander Bergner, director, IIoT product management at TTTech Industrial Automation. This is where TTTec’s Nerve edge computing platform runs.
By operating just above the PLC, the platform is able to draw upon much more computing power than is typically available at the I/O level. And by operating below the SCADA level, the algorithms are still close enough to the operation itself that the data are received in real time and experience no loss of granularity. Consequently, Nerve can support predictive maintenance and other analytics at the edge.
Because the platform has a virtualization function, it can run new applications and services alongside existing infrastructure. In fact, this ability captured the attention of the engineering staff at Fill Gesellschaft, a builder of CNC machine tools based in Gurten, Austria. Nerve now hosts the company’s Cybernetics smart factory software.
Running on edge devices built into each of Fill’s machines, Nerve collects data from the machines and sends it to the Cybernetics applications without any loss of granularity. Fill then processes the data on its software at the edge before sending the information to the cloud.
Fill is also using global datasets to check wear on components across its entire fleet of machines and to offer the results to its customer base as a service. The builder expects as much as 12% of its revenue to come from such services in a few years.
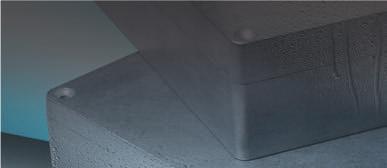
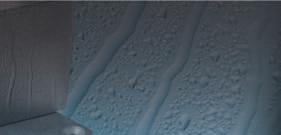
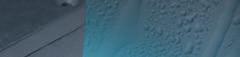
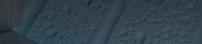
A technician calibrates an Inspekto S70 autonomous machine vision system.
Autonomous Machine Vision Improves Injection Molding Quality
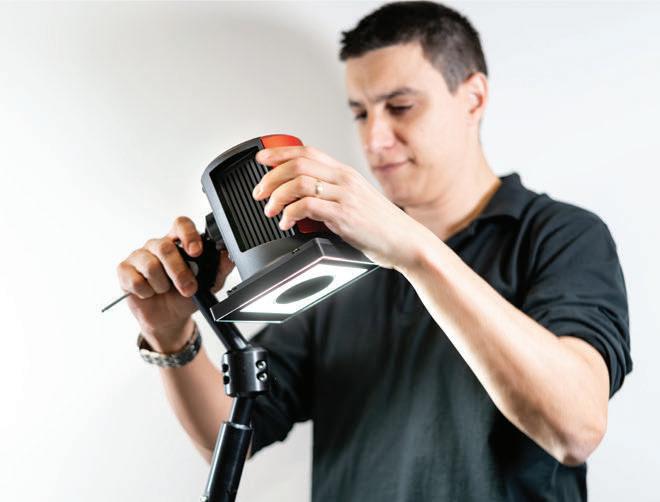
A Bosch plant that produces plastic molded connectors for automotive manufacturers implements Inspekto’s S70 machine vision system, resulting in immediate savings and an improvement in connector quality.
Global competition and market expectations put ever-increasing pressures on automotive manufacturers to enhance their quality assurance (QA) procedures. This is leading manufacturers away from manual inspection procedures and toward automated inspection to reduce costs and improve product quality.
The challenge in making this move is finding and implementing the right machine vision systems for each application. A new trend in automated vision inspection is the use of autonomous machine vision (AMV).
Plastic injection molding, a common component of automotive manufacturing, “poses a lot of problems for traditional machine vision systems,” explains Ofer Nir, CEO of Inspekto, a supplier of AMV technology. “The highly reflective surface of plastic is hard to illuminate correctly. In addition, if the mold and the plastic polymer are a similar color, and the available illumination is anything but ideal, a lack of contrast can make it very difficult for the machine vision system to work. Combine this with the fact that traditional vision systems can only inspect one type of product at a time—though manufacturers need to create product lines in different colors and sizes—and it’s easy to see why a fundamental change in machine vision is needed,” he adds.
This color contrast issue with machine vision technology is exactly the problem Bosch was facing at its plant in Waiblingen, Germany. This plant produces plastic molded connectors for vehicles that are made using multiple production lines and injection molding machines.
The plant uses conventional state-of-the-art machine vision systems, some developed internally, with others created and integrated by external machine vision experts. Unfortunately, these systems aren’t well suited at inspecting black polymer parts on a black background. As a result, it is virtually impossible to set the parameters for a machine vision QA system to recognize defects.
This means that quality inspectors have to check the connectors manually, a tedious and repetitive job. Not only are these defects easy to overlook when inspected with the human eye, but the personnel costs are significant. After reading about autonomous machine vision in an industrial report, Bosch development engineers asked Inspekto to see if the company could provide a solution for its machine vision challenges.
“This [Inspekto’s S70 AMV product] is the first standalone product for visual QA, gating, and sorting,” says Nir. “It is self-setting, self-learning, and self-adjusting and can be used to inspect any item produced with any handling method.” Inspekto claims the abilities of the S70 eliminate the costly integration and customized developments that characterize traditional machine vision technology.
Inspekto’s S70 runs three AI (artificial intelligence) engines in tandem. It merges computer vision, deep learning, and real-time software optimization technologies to achieve plug-and-play vision inspection, according to Nir. “With AMV, light conditions, line vibrations and varying handling conditions have become nightmares of the past. Changes in the inspected object’s placement, tolerance, and orientation will no longer halt production. We’ve essentially Apple-ized visual inspection with this product, which comes out of the box with everything the user needs to start inspecting products. The installation process is designed to be quick and easy. A plant’s own staff can set up and train the system without using an external systems integrator.” More importantly the S70 only requires an average of 20 to 30 good samples to learn the characteristics of a perfect product, according to Nir. “Therefore, there’s no need to set up parameters to train the system to recognize mistakes, like with traditional solutions,” he said. Because of these advantages, Bosch decided to run a pilot project in Waiblingen and see if it would help where traditional machine vision systems had failed. Engineers at the plant have extensive experience in machine vision, so it wasn’t difficult to integrate the pilot system. The initial installation took about an hour, plus less than a day to factor in the small adjustments that were made to optimize the speed of the process. It took another 20 minutes to learn the software program; then, all that was necessary was to plug in the camera so that inspections could begin. During installation, the production line kept running as normal and the plant didn’t experience any downtime. Since the Inspekto S70 can run without any input from the control system, it ran in parallel with the production line. The cost of the initial system was amortized in less than a month, with immediate savings and an improvement in quality. Because the pilot system worked so well, Inspekto says Bosch ordered an additional S70 for an overseas subsidiary and another for an older application in Waiblingen. Manufacturing software that gives you the freedom to change the world one product at a time DELMIAWorks’ ERP and MES software provides the freedom to improve the way you do business to best serve your customers, changing the world with every product you ship.
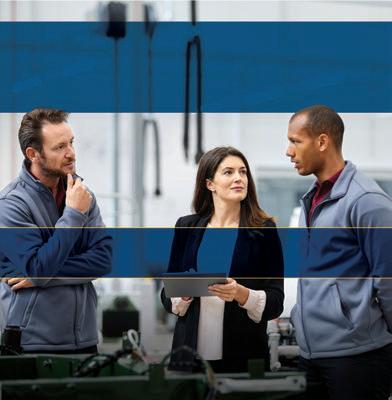