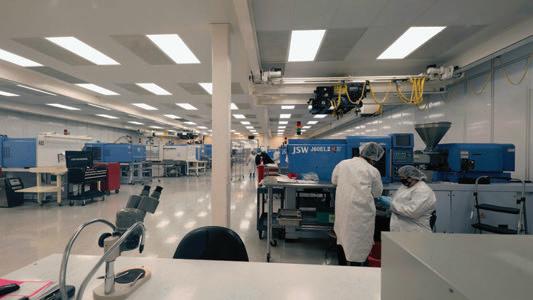
8 minute read
PERSPECTIVES
Trademark Plastics Adapts to Market Changes with ERP
By David Greenfield
Director of Content/Editor-in-Chief
Trademark Plastics Inc. cross-trains machine operators to be the first line of quality by inspecting parts at the molding machine.
Riverside, Calif. based Trademark Plastics Inc. (TPI) is a manufacturer of injection-molded parts. With eight of the world’s top 30 medical device manufacturers among its customers, 85% of TPI’s business comes from the creation of medical components for these customers.
With COVID-19 roiling healthcare operations for nearly two years, adjusting operations to the quickly changing realities facing the medical community has proved to be a constantly moving goal.
Fortunately, keeping pace with its customers during the pandemic did not require extensive adjustments to TPI’s operating processes because of the company’s long-standing investments in automation and related data acquisition and analytics. TPI uses more than 50 machines to create components along with a Zeiss Metrotom 800 computerized tomography scanning machine to conduct x-ray inspections on all products.
Data from the machines in TPI’s facility are fed into the DelmiaWorks manufacturing enterprise resource planning (ERP) system (formerly known as IQMS, which was acquired by Dassault Systèmes in 2019). The information in the ERP software is then used to provide real-time alerts as well as generate nearly 20 different reports in SAP Crystal Reports (which provide detailed data analyses). Data from TPI’s SolidWorks computer-aided design (CAD) software creates the bills of material (BOMs) used by DelmiaWorks system to track materials and the status of each project.
“Everything is connected here at Trademark, from the material to miscellaneous items to robots, injection molding, and machine information, and it’s all located in DelmiaWorks,” says Bryan Barrera, chief operating officer at TPI.
Problem identification
To quickly identify potential issues during production, TPI uses real-time monitoring displays on the shop floor. Color-coding helps employees see whether production is running e ciently (green), running faster than planned (black), or deviating from set parameters (red).
“The system can tell you, for example, if you’re scheduled to produce 100 million components per day and your costs, and it’s going to let you know in real time whether or not you’re hitting your goals,” says David Carty, chief executive o cer at TPI. “Also, when you see a red light pop up, possibly with some audio, you can go to a technician right then to troubleshoot the issue; whereas in the past, it might have been left alone for a couple hours, increasing the scrap ratio.”
“If our scrap report shows that we have a splay issue, the engineers can check if
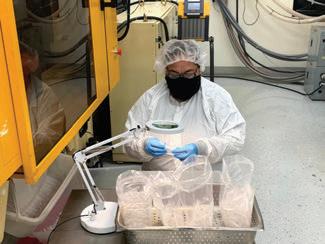
Trademark Plastics Inc. is continually implementing automation within its Class 8 clean rooms with end-ofarm tooling and index conveyors.

A cross-trained machine operator inspecting molded parts under magnifi cation.
there's moisture in the material. If there is a tooling issue, the ERP system will say it needs repair. Burning material, flash, splay—these are all items tracked in a single scrap report,” Barrera says.
Also, because production data is shared with the ERP system’s customer relationship management module, an alert will pop up if there is a delay in production so that TPI can advise the customer early in the process.
TPI also relies on DelmiaWorks to track returns. This data is used to assist in quality control and attract new customers.
“We can say we’re a great supplier [because] with the DelmiaWorks we’re able to show customers and prospects the reports with our metrics. In our case, we’ve had zero returns for the last few months,” Barrera notes. “But if there was a return, we could show them how, for instance, a non-critical dimension was not caught. Having the data for these discussions really helps us out."
Several times throughout the year, TPI is also required to complete audits on behalf of ISO or MedAccred. These organizations want to understand how the manufacturer tracks its metrics, how the quality management system is set up, and how everything is captured and integrated. The company can track and report on much of the data using the ERP system.
Improved customer interaction
TPI also has realized signifi cant e ciencies from using the ERP system to automate its quoting, expanding from hundreds to thousands of quotes without having to increase personnel. Equally important is the strategic advantage that combining automated quoting with production data in the ERP software has provided in creating win-win scenarios for the manufacturer and its customers—enabling TPI to sell more while o ering customers better pricing.
“For example, if we have an order for 1,000 parts and we're able to manufacture 1,100 parts right then, we’ll produce the extra 100 parts, update the quote, and send it to the customer, perhaps giving them a price break,” Barrera explains. “Usually, they’ll accept the o er.”
Alternatively, Barrera notes, “Sometimes the customer reaching out to us doesn’t even know they have a price break, but we’ll reach out to the material manufacturer and get five prices with breaks for 100 pounds, 500 pounds, 1,000 pounds, etc., and put those in the quoting module. Then we can just look at the quoting screen and tell the customer how much they’re saving based off the price breaks.”
A third scenario is when the team gets an automated notifi cation that demand for a product is slowing. If the product in question is a highly profi table one for the company, TPI can use that insight to o er the customer a 5% discount as an incentive to purchase more.
Scan the QR code to read about the use of ERP to help manage operations during a pandemic.
Cybersecurity at the Forefront of Industry Concerns in Early 2022
By David Greenfield
Director of Content/Editor-in-Chief
You’ve likely heard about the log4j cybersecurity vulnerability. Chances are, however, that you’ve mostly heard how this primarily a ects public-facing internet systems. Some of the higher profi le exploits of this vulnerability include penetration of Belgium’s defense ministry, several ransomware hackings, and taking control of computers to mine cryptocurrency, according to the Washington Post.
Though no incursions of industrial control systems via the log4j vulnerability have yet been reported, we do know that the potential exists. According to aDolus Technology, a supply chain cybersecurity provider, several million operations technology (OT) software packages use log4j. Most OT software suppliers use log4j because it is open-source software that e ectively handles required logging tasks. aDolus explains that the log4j vulnerability (called Log4Shell) is “a result of overly-provisioned features enabled by…an insecure default confi guration and the implicit trust of messages.”
The National Institute of Standards National Vulnerability Database reports that Log4Shell has been disabled from log4j 2.15.0 and completely removed from version 2.16.0.
As with most cybersecurity correction measures, protecting your operations requires identifi cation of the vulnerability in your systems. After all, as aDolus notes, if you don't know that the software you use contains log4j, you won't know whether you should patch or block certain tra c, or perhaps do nothing at all.
According to aDolus, a software bill of materials (SBOMs) is the “best tool for uncovering hidden vulnerabilities like Log4Shell.” The FACT platform from aDolus reportedly provides “enriched SBOMs that report all the subcomponents of a software package” and can be a valuable tool for cybersecurity assessments. Source code analysis is another option if you have access to the source code, but that's often not the case in the OT world, according to aDolus.
More detailed information about mitigating Log4Shell and other log4j-related vulnerabilities can be found at awgo.to/1338.

ISA99 update
As 2022 began, the ISA99 Committee on Industrial Automation Control Systems (IACS) Cybersecurity issued an update to stakeholders about its focus moving forward considering the ever-evolving cybersecurity threats facing industry.
Key aspects of this notice from the committee include: • 62443-1-1 (Terminology, concepts, and models)—The fi rst edition of this document was published by ISA in 2007 and later distributed as a technical specifi cation by IEC. Since then, the committee’s understanding of the subject has evolved considerably, as refl ected in the more detailed standards in the series. These changes have been incorporated into the second edition of 62443-1-1 that is currently circulating for review and comment in both
ISA99 and IEC TC 65 WG 10. • 62443-1-3 (Performance metrics for
IACS security)—This technical report defi nes a methodology for the development of quantitative metrics derived from process and technical requirements defi ned in the ISA/IEC 62443 series. It has been circulated for review and comment and further revisions are underway. • 62443-1-6 (Application of the ISA/IEC
62443 standards to the Industrial Internet of Things)—This technical report describes considerations for asset owners when they are deciding on the implementation of industrial Internet of Things (IIoT) technologies and provides guidance on the requirements of the ISA/IEC 62443 series to clarify and mitigate any cybersecurity concerns. It will be circulated for review and comment in early 2022. • 62443-2-3 (Security update [patch] management)—This technical report was published by ISA in 2015 to address the requirements for an e ective automation system patch management program. A second edition has been completed and will soon be circulated for a second round of review and comment. • 62443-2-2 (IACS security protection)—
This document prescribes the requirements to perform a protection level rating during the operation of an automation system. It was recently circulated for review and comment. • 62443-3-3 (System security requirements and security levels)—First published in 2013, this document prescribes the security requirements for control systems and assigns system security levels to the system under consideration. The committee is currently preparing a second edition.