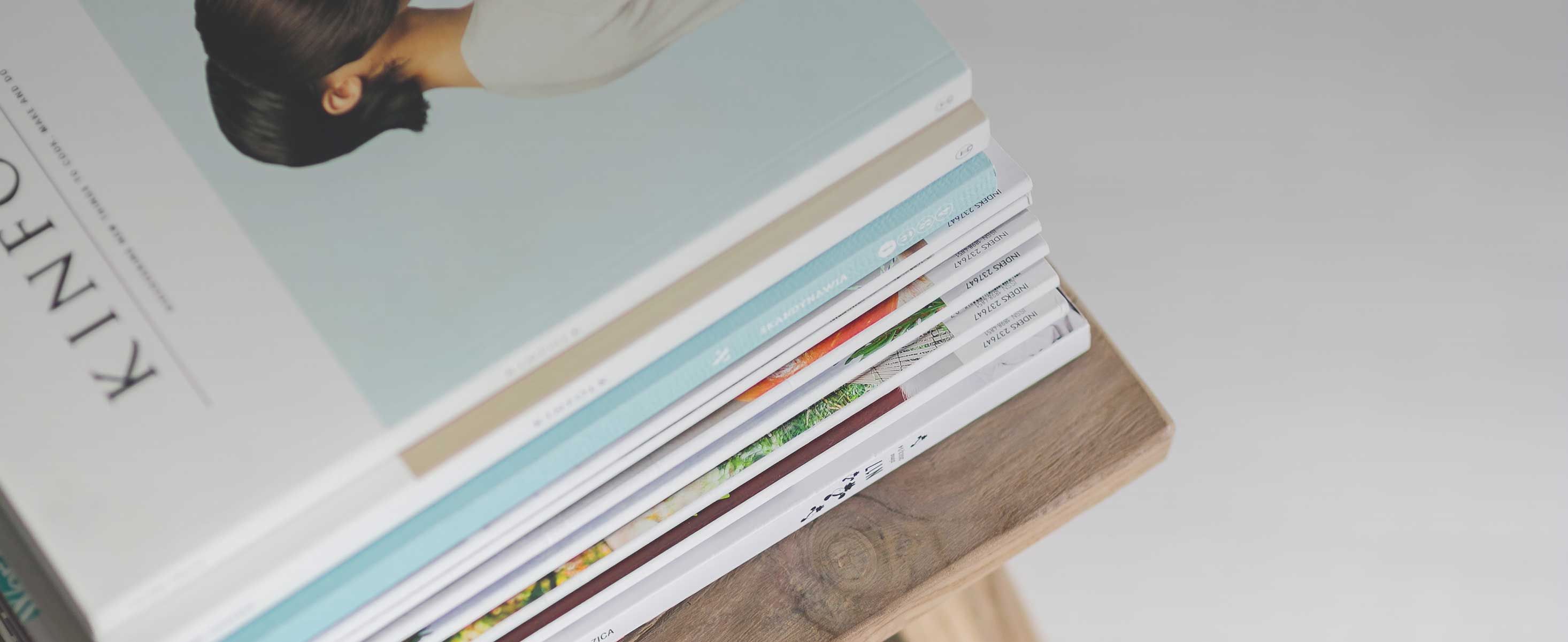
7 minute read
BATCH OF IDEAS
INDUSTRY DIRECTIONS
Moving Robots Into the Matrix
By Stephanie Neil
sneil@automationworld.com sneil@automationworld.com
Senior Editor
Otto Motors is a maker of autonomous mobile robots (AMRs) used to automate material handling in manufacturing and warehouse operations. The robots are designed to bring materials to and from people, equipment, racks, and shelving in a free-movement manner. With collaborative capabilities built-in, AMRs are a highly productive way to optimize workflows.
According to the company, Otto robots have the ability to double productivity, but they have to be installed correctly in the first place. Simply using a spreadsheet to figure out how many AMRs are needed in an operation comes with a cost if there are too few—or too many—robots. Even a 20% variable on a fleet of 100 AMR vehicles means that either a customer is not getting what they need or are spending more than they should to achieve what is necessary, which makes for a weaker ROI.
But there’s a solution to this problem, and it comes in the form of simulation software.
Matthew Rendall, CEO and co-founder of Otto Motors, was at the Robotics Summit & Expo in Boston in May delivering a presentation on the use of simulation for successful AMR deployments.
“We believe simulation is a critical prerequisite in your toolkit for a large fleet implementation,” Rendall said. “And the reason is that you can be highly granular, highly variable, and very catered to the specifics of not only the layout of the facility, but how your operation changes day by day, shift by shift, and minute by minute. And then you can load all of those parameters into a simulation and model it for a full operation.”
It’s basically a way to start with the end in mind and mitigate the risk of failure via scenario analysis. The larger the fleet, the bigger the risk. “If you have 100 AMRs on a line, you are probably integrated into mission critical business processes,” Rendall explained. “And if that system doesn’t work, the plant doesn’t work; and if the plant doesn’t work that is catastrophic. So simulation is important for risk mitigation.”
Rendall went on to describe two real customer scenarios, one greenfield deployment and one brownfield. They have some similarities, but in a greenfield project—where you are not dealing with existing infrastructure—the benefits of operational efficiency are very high.
The greenfield site was a 1 million sq. ft. facility covering production and warehousing. It had 300 pickup/dropoff locations and AMRs would perform 5,000 deliveries and cover more than 1,000 miles per day. Because they were starting from scratch, Otto was able to partner with the customer to help them rethink how their manufacturing facility of the future would be laid out. Then they could simulate scenarios testing for routing, traffic, location, etc.
The simulation is split into two categories, physics simulation and process simulation, with the output of the physics simulation used as an input into the process simulation. Here is where the fun stuff happens.
“We put the robots into the matrix,” Rendall said. “They don’t know they’re in a simulation as the software is fully emulating the environment. So we teleport the vehicle into the matrix and it’s operating with no knowledge it’s in a simulated environment versus a real environment.”
From there, they can conduct micro-tests to look at interactions and understand how much time an AMR will spend waiting at intersections and pickup locations, for example. These things are validated in the real world and feedback is created in a closed loop micro-simulation to ultimately look at the entire end-to-end process to see how the operation unfolds.
In this case, the manufacturer actually reduced the number of AMRs needed while increasing efficiencies simply by being able to work through each scenario analysis. “It was originally scoped at 102 AMRs, but with the simulation we were able to optimize the design to 83 AMRs,” Rendall explained. So while some customers might balk at the thought of spending more upfront on simulation software, there’s real value on the other side. “Invest a little up front in simulation and save 20% of your fleet size through smarter design and more confidence.”
Brownfield simulations have a similar approach, with the fundamental difference being lower degrees of freedom based on decisions that have been made throughout the facility’s lifespan. It is also often dealing with a mix of traffic including forklifts, AMRs, and people. So the approach here is more about how to phase in AMRs without disruption to the operation to minimize downtime.
In either scenario, however, the use of simulation results in the same outcome. “Our position is that a small amount of investment upfront is so important to set the project up for success and make sure you are spending the right amount of money to solve the right problems and mitigate the execution risk associated with going live with an AMR implementation,” Rendall said.
INDUSTRY DIRECTIONS
Robot Predictions for 2022
By David Miller
dmiller@pmmimediagroup.com
Senior Technical Writer
As labor shortages in the manufacturing industries continue to swell, the uptick in demand for robotics is expected to continue. Moreover, software intelligence is making robots more adaptable, further lowering barriers to adoption and allowing new users to begin automating more easily. The result is a world in which robotic technologies are becoming more ubiquitous than ever before.
“The pandemic accelerated far-reaching global mega trends—from labor shortages and supply chain uncertainty to the individualized consumer and growing pressures to operate sustainably and resiliently—leading new businesses to look to robotic automation,” said Marc Segura, robotics division president at ABB. “As technology opens new opportunities for meeting customer demands, new trends will continue to emerge that will further drive demand in areas where robots have traditionally not been used.”
In particular, Segura identified three key trends that ABB expects to shape demands for industrial robots in 2022.
Trend 1: Electric vehicles will bring changes
to automotive manufacturing. As tighter emissions regulations and fuel economy standards drive automotive manufacturers to decrease the production of internal combustion engine vehicles and pivot toward electric cars instead, automotive supply chains may be thrown for a loop. This is because electric vehicles require many components that internal combustion engine vehicles do not. Most notably, automotive companies will seek to bring the manufacturing of batteries as close to vehicle assembly as possible to meet sustainability requirements. This means new facilities will need to be built. According to Segura, these new facilities will most likely make significant use of autonomous mobile robots (AMRs) to enable more modular and flexible production. Segura sees this shift occurring as automotive manufacturing attempts to become more responsive to rapidly changing demand.
Trend 2: E-commerce will create more
demand for flexible and mobile robots. With mass customization continuing to sweep over the consumer goods markets, companies need to find new ways to adapt their production lines and distribution processes to enable personalization in both manufacturing and delivery. Fulfilling these needs will require the adoption of more mobile, flexible, and intelligent robotic technologies.
“This trend will see the growth of lighter, smaller robotic applications, enabling the expansion of automation into new areas of warehousing and distribution operations. As artificial intelligence in robotics matures and learning robots become mainstream, expect to see these technologies deployed alongside AMR technologies, orchestrated and managed by intelligent software to provide enhanced flexibility, speed, and efficiency,” Segura said.
Trend 3: Robots use will expand signifi-
cantly, requiring worker retraining. At smaller companies that are less-experienced with robot use, more affordable robots that feature collaborative functionality and intuitive programming will continue to proliferate. In particular, highmix, low-volume manufacturers that use CNC machines to produce parts and components for other companies are drawn to collaborative robots because they can work directly alongside human employees to assist in tasks such as machine tending. Moreover, the advances in software intelligence that enable this adaptability and responsiveness could also help robots migrate into new environments such as construction, healthcare laboratories, restaurants, and retail establishments.
According to Segura, as robots become more commonplace in society, widespread education about their use and operation will be required at primary and secondary schools, as well as at colleges and universities.