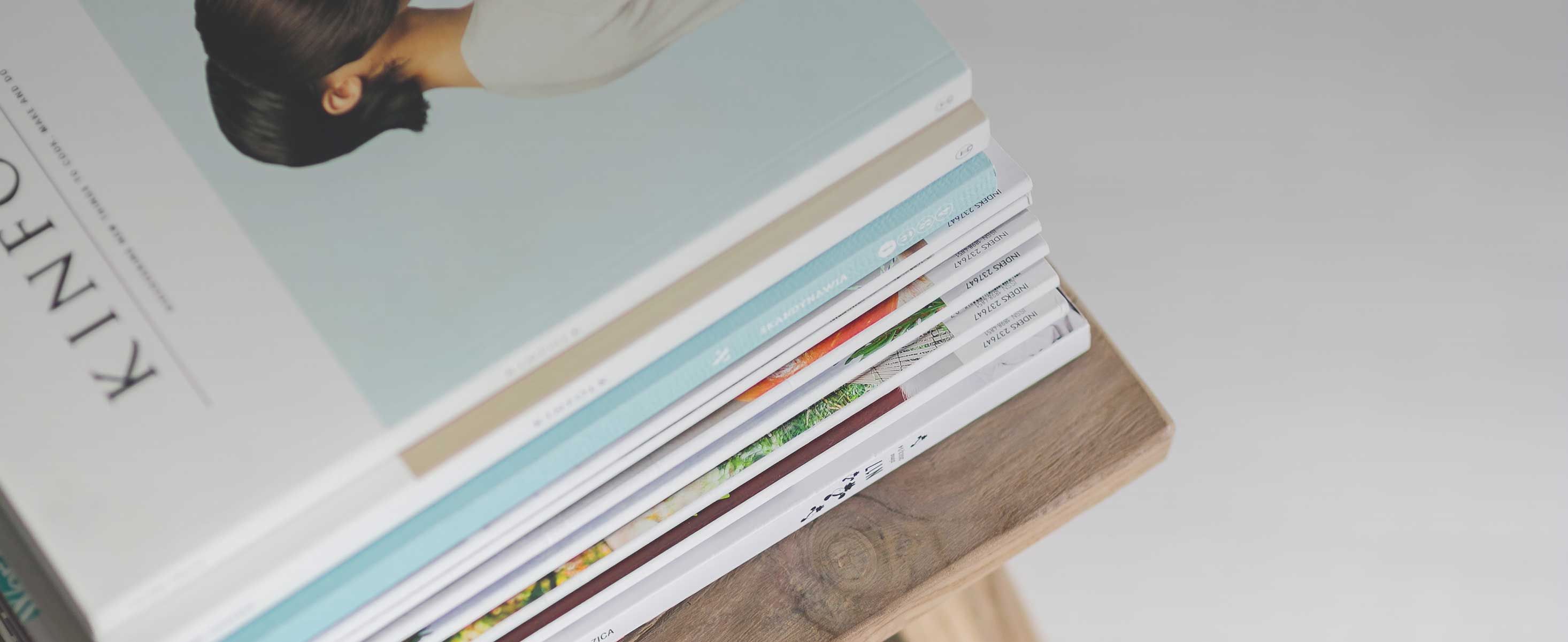
2 minute read
: Agile machines with adaptive automation
Flying 2D product transport with up to 6 degrees of freedom
XPlanar enables new dimensions of freedom in product and material handling: Levitating planar movers fly over flexibly arranged planar tiles accommodating nearly any track layout and path planning.
Individual 2D transport at up to 2 m/s
Processing with up to 6 degrees of freedom
Transport and processing in one system
Wear-free, hygienic and easy to clean
Free arrangement of planar tiles enabling totally customized machine and process layouts
Multi-mover control enables parallel and individual product handling
Fully integrated into the powerful and standardized PC-based Beckhoff control system (TwinCAT, PLC IEC 61131, Motion, Measurement, Machine Learning, Vision, Communication, HMI)
For use across all industries: assembly, packaging, food/bev, pharma, laboratory, entertainment, … operations, all accessible via one pane of glass, the task lies in achieving this broad-based integration.
Rob McGreevy, chief product officer at Aveva, explained the work ongoing at Aveva to achieve this vision.
“We will continue to offer a modular, not monolithic, approach with the intent to create an open, vendor neutral environment to deliver an industrial software platform,” he said, explaining that 30-40% of that data that comes into Aveva’s engineering and operations software comes “from other company’s products. The PI System (acquired by Aveva from OSIsoft in 2020) was a leader in this. And it’s the same with Wonderware InTouch HMI/SCADA (acquired by Aveva in 2018 via the merger with Schneider Electric, which had owned Wonderware since 2014 with its acquisition of Invensys).”
McGreevy said Aveva is essentially blending different user interfaces to connect systems from the edge to the enterprise. Based on this approach, Aveva plans to release the “first-ever coordinated HMI/SCADA release in 2023 via the integration of the Aveva Historian and PI systems to the cloud-based Aveva Data Hub,” McGreevy said. “This takes the HMI concept and applies it to the enterprise.”
To optimize both equipment assets and operational processes, McGreevy said the combined forthcoming system will be able to schedule work based on data-driven performance plans and asset maintenance predictions. This will involve the integration of Aveva artificial-intelligence-powered analytics and the PI system to connect operational processes and analytics.
As an example of what will be possible for industrial companies with these combined technologies, McGreevy noted Thai petrochemical company SCG now saves 40% on maintenance costs after digitalizing its equipment and processes data through application of the PI system. “SCG achieved a 9x return on investment (ROI) in 6 months using predictive analytics, mobile operator technology, Unified Operations Center, and the PI system,” he said.
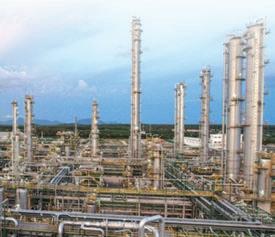

He added that Aveva’s vision is to create a connected community where users still own all their data but can securely share it with equipment vendors, suppliers, and customers. “Digitizing this value chain—from design to operations—helps identify and minimize costs,” said McGreevy.
The ability to access a digital twin of assets, processes, and sites gives users information needed to improve operations and maintenance as well as training. With digital twins built on this coordinated data, engineering efficiencies can be increased by 30%, McGreevy added. “It’s more than linking documents for access, its’s about delivering additional information to a worker as it’s presented; for example: Do you need a ladder to access the equipment [to perform the required maintenance]?”