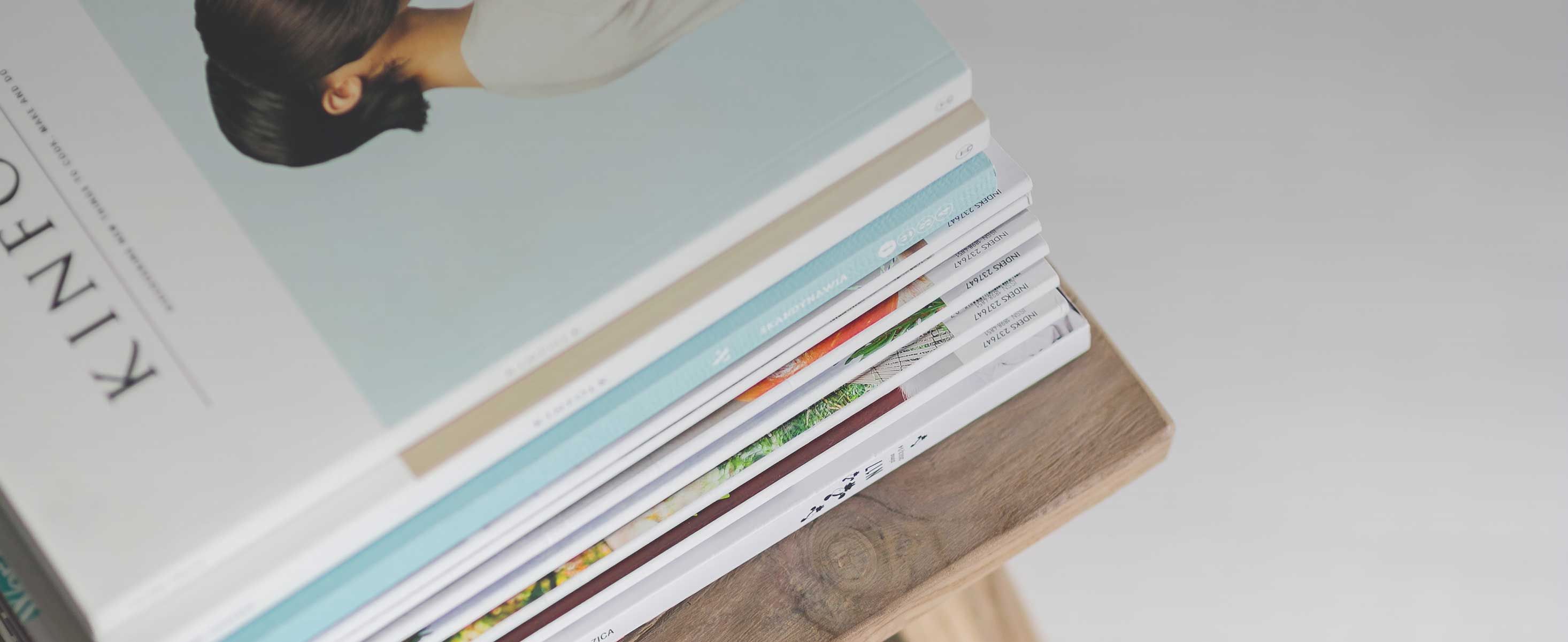
5 minute read
How to Pivot from Vision to Value
Don’t get stuck
By Diane Sacra LNS Research
Industry data analyses conducted by LNS Research indicate that more than twothirds of industrial organizations are committed to an Industrial Transformation (IX) program. LNS Research defines IX as “the proactive and coordinated approach in leveraging digital technologies to create step change improvement across the value chain.”
Despite lingering impacts of the COVID-19 pandemic and current economic uncertainty, IX shows no signs of slowing down. In fact, LNS Research states that 83% of companies say they are maintaining or even increasing their IX initiatives in the face of all of 2023’s economic uncertainties. Why? Early adopters have realized significant return on investment (ROI) from their efforts. These leaders account for the top 20% of companies reporting real success or significant progress in IX—and their results are evident.
For example, LNS Research reports that more than 80% of IX Leaders were able to reduce their cost of goods sold and/or improve operating margins and/or grow revenues by at least 3% as a result of their IX programs.
On the flip side of this are the “IX Followers.” These are organizations engaged in IX that find themselves stuck or stalled in their progress. LNS Research reports that more than 75% of companies are not yet realizing any value in their transformation programs. But why?
According to Tom Comstock, research fellow at LNS Research, the obstacle to realizing value is the “transformation chasm”—the gap between what is required to initiate a program and what is required to sustain transformation. “The staffing, processes, strategies, and methodologies needed to get an IX program going eventually become a burden to long-term success,” Comstock explained.
To prevent getting stuck in the transformation chasm, Comstock suggests that manufacturers cannot simply refine the structure of their program as it matures. Instead, they must rearchitect or pivot within that structure.
“Evidence increasingly shows that IX programs—especially successful ones—must restructure their efforts mid-flight to achieve, sustain, and grow the ROI from their transformational investments,” Comstock said. “At LNS Research, we call this program restructuring the ‘Pivot to Value,’ as meaningful improvement in the financial performance of the company is dependent on these changes.”
LNS Research has found that the benefits of transformation begin to accrue quickly as IX ramps up early on in the “Vision Stage,” but unless the organization pivots dramatically, those benefits will not grow or sustain over time. The IX efforts made early on may be lost long-term, according to Comstock, because “businesses tend to revert to the mean unless the program is restructured.”
Pivoting scales IX with a more holistic approach across the organization. Early on, for example, the organization may be focusing on departmental challenges and avoiding some of the bigger organizational issues that lie ahead. But long-term, this narrow departmental focus will provide dwindling returns. According to Comstock, “IX Leaders pivot and are twice as likely to focus on problematic business models and supply chain restructuring that are too difficult to address in the earlier stages of transformation.
So how can organizations avoid stagnating in the transformation chasm and pivot to value as Comstock suggests?
Confront the bigger challenges
One of the most important shifts a manufacturer can make in their program is to model IX Leaders and not be afraid to tackle the big stuff in your pivot. These leaders are focused on both the bigger picture and problems and are willing to invest in solving these large challenges even without immediate payback.
Another key aspect involves incorporating your IX program into your organization’s culture. This takes a more holistic approach that may include changes such as making digital competencies part of performance appraisals, hav- ing robust IX training programs throughout the entire company, combining IX within continuous improvement programs and teams, and making IX not simply a program but an ingrained, standard way of doing business.
While there are many elements to pivoting from vision to value within IX and avoiding the dreaded chasm, one final area Comstock touches on is technology. He states that IX leaders are not hyper-focused on new digital or emerging technologies; they’ve moved past the new tech testing phase and have already determined what will work best for their needs. This has allowed them to shift their focus to improving business processes via those technologies.
“For leaders, it is about applying technology to reorchestrate business processes, breakdown organizational silos, and innovate agility and resiliency,” Comstock said.
Automation Direct www.automationdirect.com/vision 2
Automation24 www.Automation24.com 5
AVEVA Software, LLC www.aveva.com/align-your-teams 33
Banner Engineering Corp. www.bannerengineering.com 13
Beckhoff Automation www.beckhoff.com 35
Beckhoff Automation GmbH & Co. www.beckhoff.com 21
Carlo Gavazzi www.gavazzionline.com 99 Cimon Co. Ltd www.cimon.com 101
Contemporary Controls www.ccontrols.com/ctrlink 105
Digi-Key Corp www.digikey.com/automation 7
Emerson Corporation www.Emerson.com/Sustainable-Automation 24
Encoder Products Company www.encoder.com 27
Fabco-Air www.fabco-air.com 41
Festo Corporation www.festo.us 29
Hammond Manufacturing www.hammondmfg.com 103
Heidenhain Corp. www.heidenhain.us 15
Lenze Americas www.lenze.com 17
Motion www.ai.motion.com 9
Moxa Americas, Inc. www.moxa.com 19 Murrelektronik, Inc. www.murrinc.com 28 Norgren, Inc. www.norgren.com 39
Opto 22 www.opto22.com 111
PMMI ProSource www.prosource.org 97
ProFood World Sustainability
Excellence in Manufacturing Awards www.pfwgo.to/sema 43
ProComSol www.procomsol.com 20
SEW Eurodrive, Inc. www.seweurodrive.com 112
SMC Corporation of America www.smcusa.com 23
Telemecanique Sensors www.tesensors.com/XXSonic 25
Uline www.uline.com 26
Yaskawa America, Inc. www.yaskawa.com 11
Automation World ® (ISSN # 15531244, USPS 22435) is a registered trademark of PMMI, The Association for Packaging and Processing Technologies Automation World ® is published 12 a year by PMMI with its publishing office, PMMI Media Group, located at 401 N. Michigan Avenue, Suite 1700, Chicago, IL 60611; 312.222.1010; Fax: 312.222.1310. Periodicals postage paid at Chicago, IL, and additional mailing offices. Copyright 2023 by PMMI. All rights reserved. Materials in this publication must not be reproduced in any form without written permission of the publisher. Applications for a free subscription may be made online at AutomationWorld.com/subscribe. Paid subscription rates per year are $105 in the U.S., $147 Canada and Mexico by surface mail; $250 Europe, South America. $325 Far East and Australia by air mail. To subscribe or manage your subscription to Automation World, visit AutomationWorld.com/subscribe. Free digital edition available to qualified individuals outside the United States. POSTMASTER; Send address changes to Automation World®, 401 N. Michigan Avenue, Suite 1700, Chicago, IL 60611. PRINTED IN USA by Quad Graphics. The opinions expressed in articles are those of the authors and not necessarily those of PMMI. Comments, questions and letters to the editor are welcome and can be sent to: editors@ automationworld.com. We make a portion of our mailing list available to reputable firms. If you would prefer that we don’t include your name, please write us at the Chicago, IL address. Volume 21, Number 1.
Siemens’ Amberg electronics plant has moved away from legacy operational systems used to manage 350 changeover processes between di erent production lines and is now using Red Hat OpenShift to create a more modular, microservices-based IT/OT architecture. This move allows developers at Siemens to apply artificial intelligence-generated data insights for smaller-scope changes to avoid disrupting operations.
David Greenfield on Siemens’ use Red Hat’s OpenShift technology in its manufacturing operations.
The new smart instrument setup measures both ambient temperature and internal temperature, performing corrective calculations to achieve continuous, accurate, and repeatable readings of the gas inside the pipe. Data is sent to the automation system using WirelessHART, and the system gives operators a great deal of intelligence compared to what they had with the singular temperature reading.
Beth Stackpole on how smart instruments are improving operations.
What some users fail to understand about HMI systems is exactly how tightly the software is connected to factory floor controllers. This connection via high security networks, VPNs, and masks, can be tricky to navigate, particularly when the architecture is intentionally complex to provide security.
Randy Otto of ECS Solutions on why web-based HMI technology is ready for industrial use.
While working in one heavily dated facility, we discovered that all their control panels were on one network. They also used multiple versions of various panel devices from multiple manufacturers. The site was in such a state of disarray it was di cult to pinpoint which devices were where and what each panel was specifically controlling.
Melissa Bruno of E Technologies Group on battling obsolescence and risk with technology assessments.
A recent Accenture survey found that 94% of North American companies are now planning to invest directly in onshoring or nearshoring. And more than half of all supply chain and manufacturing executives think building manufacturing capacity closer to home is essential for their companies’ survival.
Brian R. May of Accenture on the next phase of industrial supply chains.