
4 minute read
MATERIAL DEVELOPMENTS
3 Fast Facts: Cohesive Peel Technology
How might a cohesive peel system help with variability in seal strength?
KEREN SOOKNE, DIRECTOR OF EDITORIAL CONTENT
While many in the medical device packaging industry are familiar with adhesive peels, cohesive peel technology can offer advantages in reducing the variability in seal strength, reducing fiber tear, and offering a consistent peel for the end user. DuPont and PAXXUS representatives held a webinar to discuss the technology.
Adhesive vs. cohesive
Adhesive peel: As the film is peeling, it typically leaves both surfaces in the same state that they were in before they were sealed, explained Doug Dodrill, Chief Technology Officer at PAXXUS. As is shown by the light green section of sealant (next page, top image), it’s strictly separating without transfer of molecules between the surfaces.
Cohesive peel: When the surface peels away from the Tyvek®, the sealant splits in the middle of the layer (see the light green section—next page, bottom image). “Basically, it’s sacrificing the ‘skin layer’ and transferring the skin over to the Tyvek surface, rather than peeling cleanly,” said Dodrill.
1. How is a cohesive sealant created?
The main principle: start with one polymer and add an additional incompatible polymer (or two) to disrupt the polymer matrix. “That weakening of the polymer matrix is actually what creates the cohesive peel. Polybutene is a common one but there are many other combinations of incompatible polymers that will create the same effect,” said Dodrill.
Jose Arevalo, Global Business Development Manager at DuPont, added, “The additive you put in creates a weak point in that film structure, so when you go to open it, it will break along that weak point that you’ve designed into the film layer.” The sealant is designed so that when the bonds within the sealant layer itself are weaker than the adhesive seal bonds, it will split and leave the polymer behind, rather than separating completely from the Tyvek (or other material).
There are various ways to tailor cohesive film behavior to an application. Adding a colorant to the seal offers the ability to see the transfer occurring against the white Tyvek background. A key
element of the new EU MDR is the ability to prove the integrity of the package at the time of use. The colorful cohesive peel technology that transfers to the Tyvek is an example of a visual indicator that allows a nurse to know the package was sealed properly. Pre-opening, a nurse can also inspect the tinted seal for channels or non-uniformities.
2. How is seal strength altered?
Factors that alter the seal strength include (but are not limited to) what chemicals are mixed and the percentages of secondary polymer added to the matrix.
“You also have to look at the viscosities of each of the polymers that you’re blending together. You’re controlling how the islands of the secondary polymer are fi tting into the matrix in the primary
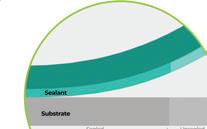
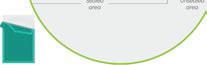
↗ Adhesive peel.
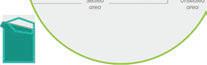
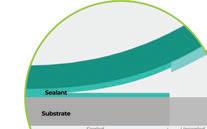
↗ Cohesive peel. polymer. If the viscosity or the melt index of the resins is very similar, then they tend to create a very easy and uniform dispersion, which may or may not be a desirable depending on what type of seal strength you’re trying to create,” said Dodrill. “If there’s a big disparity between the viscosities of the two, then you tend to end up with larger islands of the secondary polymer which would increase the seal strength in that situation.”
He likened it to ingredients we’re all familiar with: if you mix toothpaste and honey together, they mix fairly easily, whereas toothpaste and tar are going to be an entirely diff erent mixture.
3. How might this reduce variability?
With adhesive peel technology, as seal temperatures and/or dwell time increase, seal strengths tend to increase.
In the case of cohesive peel technology, PAXXUS has found that above approximately 265°F, once the seal is activated, seal strength remains consistent up to the limits of the Tyvek at about 300°F. This represents an approximate 35-degree operating window.
Dodrill reported that seal strengths are typically on the order of 1.5 pounds/inch, which can be adjusted up or down. Mark Sundt, Technical Service Consultant at DuPont, confi rmed this estimate in trials with the technology. He added, “Quantitatively, it was nice to see that once you got to a certain threshold point, you saw the seal strength somewhat level off and stay consistent over several degrees.”
After evaluation, Sundt noted that beyond the quantitative results for seal strength remaining consistent over a wide range of temperatures, there were also subjective features to factor in.
“What was also nice—as you went from lower temperature to a higher sealing temperature—how it felt when you opened the package didn’t change. That would obviously make sense as the measured seal strength remained consistent. The opening felt very uniform, so it was a very familiar feel,” he said.
Sundt pointed out that due to the mechanism of the cohesive failure happening within a layer of the fi lm—leaving part of it on the other web surface (Tyvek)—the propensity for fi ber tear to occur is likely lessened. The stress of the peel is essentially moved away from the Tyvek surface, allowing for a smooth peel and less variation.
PACK EXPO Las Vegas and Healthcare Packaging EXPO (Sept. 27-29, Las Vegas Convention Center) will reunite the packaging and processing community. With more than 1400 exhibitors, no other event in 2021 will bring together a more comprehensive gathering of suppliers offering new products, technologies, and solutions. Attendee registration is open at