
3 minute read
In the News
from ProFood June 2021
To increase your bottom line, start with your frontline
Productivity + People
AMBER BROVAK | SENIOR MANAGER GLOBAL SAFETY OPERATIONS, CHURCH & DWIGHT BERNARD CUBIZOLLES | SENIOR GLOBAL MARKETING MANAGER – DIGITAL PLANT, GE DIGITAL STEPHEN M. PERRY | FOUNDER AND COACH, FSO INSTITUTE
Coronavirus’s Impact, Learnings, and the Value of Discipline
Prior to the pandemic, manufacturers spent most of their time optimizing assets and processes. When the crisis struck, the industry was forced to reinvent day-to-day activities. Refocusing on people is the key to being prepared for future uncertain times.
DURING THE PAST YEAR, the global coronavirus pandemic put pressure on daily manufacturing operations like never before. As these pressures emerged and mounted, members of FSO Institute’s Manufacturing Health Roundtable— representing nearly 30 consumer packaged goods companies (CPGs)—dealt with them in real time and collaborated to identify six of the most significant COVID-19 trends as shown on the opposite page.
As these six COVID trends show, when disruptions of this magnitude occur and uncertainty rules the day, it is easy to lose sight of standard work, process discipline, and the value of predictable dayto-day operations in manufacturing. Maintaining focus and business as usual becomes increasingly di cult. And while most agree that we won’t be returning to normal as we have known it, they also agree that there will be a continual need for discipline and repeatability in manufacturing in the new normal world as well.
CASE IN POINT
Finding certainty in uncertain times
To learn more about how the CPG community is dealing with the turbulence inflicted by the global pandemic, FSO Institute spoke with Amber Brovak of Church & Dwight and Bernard Cubizolles of GE Digital about some of the lessons learned during the past year of uncertainty.
AMBER BROVAK BERNARD CUBIZOLLES
FSO Institute: Amber, as senior manager of global safety operations at Church & Dwight, how has your area been impacted by the global pandemic during the past year?
Amber Brovak: Since most of my experiences with the impact of the global pandemic occurred during my time with my previous employer (Nestlé), my comments are based on that experience.
It is appropriate that “safety first” is listed as the No. 1 trend, as there was a 100% commitment to employee health and safety at Nestlé during this pandemic. In fact, we considered employee health and safety as the gateway to production—without it, there would be a risk of no production. As our leadership team broke into smaller teams leading the COVID process, we immediately began putting safety protocols into place—from social distancing and physical separations to hand sanitizing and PPE (personal protection equipment). That really opened employees’ eyes and showed our focus on and caring about their safety and well-being. We had a small group that spent a large part of each day proactively handling PPE and chemical procurement, including thermometers for each plant. It was di cult, time-consuming, and exhausting, but we had to do it. Initially, the primary focus was at site level, and corporate developed formal procedures quickly

ZSK FOOD EXTRUDER. DUAL USE EXTRUDER FOR PLANT-BASED PRODUCTS.

+ Dual use TVP and HMMA extruder allows fast changeover and high flexibility + Plant based ingredient material handling equipment from source to packaging + Strict adherence to cGMP guidelines and standards, FDA approved materials + High accuracy loss-in-weight feeding of powders and liquids + Proven industry leader with installed TVP and meat analogue systems globally + Worldwide service network
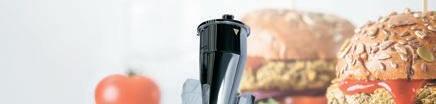
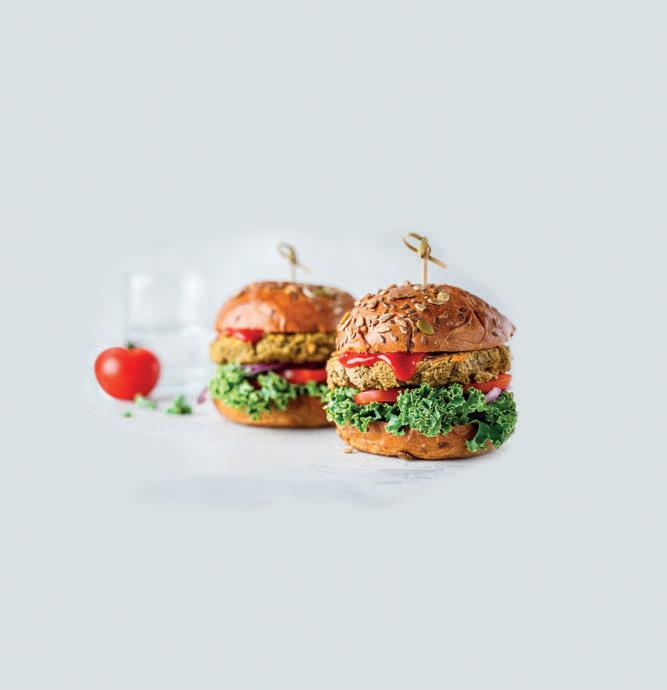
Our dual use TVP and HMMA extruder for plantbased products gives developers and manufacturers of these products the highest flexibility.
John Sheehy Global Key Account Manager Plant Based Foods
Email our expert at: info@coperion.com Learn more at: www.coperion.com/f-news
Video: Extrusion of HMMA
Coperion`s ZSK Mv PLUS food extruder for plant-based proteins in a hybrid design allows dual use for manufacturing meat substitute products. Both TVP and HMMA can be produced on the same extruder, providing manufacturers maximum flexibility and profitably react to changing market demands. www.coperion.com/food-extruders