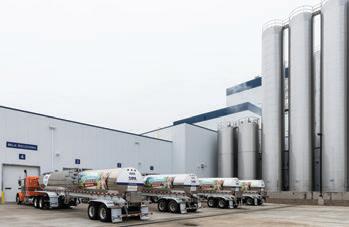
5 minute read
Case Study: Dairy Farmers of America
from ProFood June 2021
DAVID GREENFIELD | EDITOR IN CHIEF/DIRECTOR OF CONTENT, AUTOMATION WORLD
Connected Devices Enable Continuity in Milk Production
Communication technologies accelerate the advance of milk production and help to optimize operations in support of the nation’s food supply during the COVID-19 pandemic and beyond.
DAIRY FARMERS OF AMERICA (DFA) is a cooperative composed of more than 13,000 family farmers from across the U.S. It helps farmers operate their plants, find outlets for their products, and invest in new business opportunities. Brands they represent range from nationally recognized names such as Borden and Breakstone’s to specialty brands like Plugrá and La Vaquita.
The cooperative operates more than 85 manufacturing facilities producing milk and dairy products. Like many manufacturers, DFA members have seen their operations’ safety and productivity impacted by COVID-19. To help support the nation’s food supply during the pandemic, Cisco donated an array of collaboration technologies to DFA to help it develop more flexible manufacturing processes, enable workforce continuity, and increase its ability to collaborate in real time.
Funded by Cisco’s Country Digital Acceleration program, which is active in 34 countries, Cisco supplied Cisco Webex room kits, DX-80 videoconferencing kits, Webex Teams and Webex Expert-on-Demand software, and RealWear HMT-1 hands-free “head-mounted tablet” devices to help DFA connect its teams across the country in multiple manufacturing facilities.
The collaboration equipment and services Cisco donated provides manufacturing workers with secure, remote access to experts and first-line support teams working from home or at other plants. Specifically, it gives DFA real-time visibility into operations through hands-free video devices, which enables DFA’s workforce to remain productive while adhering to physical distancing guidelines. The access to experts these technologies facilitate will help DFA “shift production, optimize resources, and increase resolution time as it adapts to changing demand,” says Carlos Rojas, global manufacturing lead for Cisco Industry Solutions Group.
The first phase of this donation, which was completed in June 2020, was deployed to four sites across DFA’s operations, including its largest processing facility in Portales, N.M. Others included in this first phase are in Ventura, Calif.; Zumbrota, Minn.; and Schulenburg, Texas. The second phase focused on accelerating machine data over the secure Cisco Webex Teams platform for remote diagnostics, according to Rojas.
PHOTO COURTESY OF DFA
Team collaboration
To enable real-time communication between DFA co-workers, Cisco Webex Teams technology is being used to provide workers with access to documentation using RealWear HMT-1 head-mounted devices for routine process evaluations, maintenance, and training. With everyone using Cisco Webex Teams, users don’t need to rely on disconnected methods such as text messaging, phone calls, or emails to connect. Instead, a quick Teams message in a project space allows for collaboration between the necessary resources and keeps all the related data connected and retrievable.
The Dairy Farmers of America cooperative helps farmers operate their plants, find outlets for their products, and invest in new business opportunities.
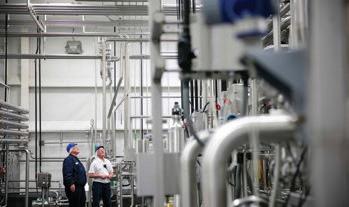
PHOTO COURTESY OF DFA
Cisco donated an array of collaboration technologies to DFA to help it develop more flexible manufacturing processes, enable workforce continuity, and increase its ability to collaborate in real time.

PHOTO COURTESY OF CISCO
RealWear HMT-1 head-mounted devices enable real-time communication between DFA co-workers.
“For example, if a production manager notices that a line is not operating at full health, he or she can directly connect with the plant operator via Cisco Webex Teams to discuss steps to remediate the issue,” says Dan Malyszko, director of operations for system integrator Malisko Engineering, which was involved in the implementation of the Cisco technology at DFA. “Likewise, a maintenance manager looking for status updates on a motor control center issue can be notified by field personnel with pictures, videos, or annotated files showing their progress.”
The combination of a retiring skilled workforce and the social distancing and travel issues created by COVID-19 means that plant personnel will not always have the available experience on hand in every situation. Cisco’s Expert on Demand technology, accessed using the RealWear HMT, can close this experience gap by connecting workers from the plant floor to plant management or experts at other locations while allowing them to keep their hands free to work, rather than having to hold a smartphone or tablet, Malyszko says.
By turning the augmented reality glasses in the RealWear HMT into a voice-activated collaboration headset, the Webex Expert on Demand application can connect frontline workers to knowledgeable experts. This technology allows workers to enhance their productivity through multi-party video calling, Cisco notes. It provides the ability to annotate images, and share the annotations between the expert and frontline worker, as well as share key documentation, all in real time.
Capabilities of the Expert on Demand technology combined with the RealWear HMT include: • Launch two-way or multi-party video meetings hands-free and collaborate with remote experts to resolve problems at the source without requiring workers to be onsite. • Request and receive a call back from an individual expert or an entire team. • Search the company directory to find the right expert or teams to resolve an issue immediately. • Access resources such as documentation for common troubleshooting steps. • Share screens to see more easily what’s being discussed and give an expert the ability to share content live. • Frontline workers and experts can augment live streaming with annotations to help resolve problems faster and provide guidance for day-to-day activities.
These capabilities not only provide plant personnel the means to report an issue, but can also provide a solution without the need for costly travel or trial and error, Malyszko notes. “For example, if an operator notices a deviation in a critical process control point and is unsure of what to do, with a few short voice commands the operator can request help or call directly to the necessary resource to assist in resolving the issue,” he says.
Remote Expert technology can even be used to cross the IT/OT divide. “If plant engineering and maintenance personnel are installing new hardware from corporate IT and need all hands available to rack the equipment, with guidance from either Malisko Engineering or corporate IT, they can safely and properly execute the job with the hands-free assistance of the RealWear HMT,” Malyszko says.
Cisco
www.cisco.com
Malisko Engineering
www.malisko.com