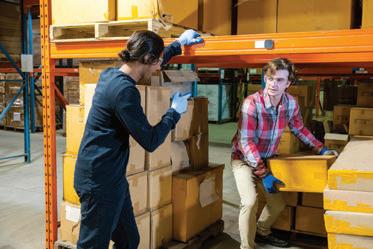
10 minute read
PERSPECTIVES
5 Tips to Get the Most Out of Industrial Wearable Devices
By David Miller
Senior Technical Writer
With examples ranging from 5G connected hardhats to augmented reality (AR) headsets, wearable technologies are on the rise in industry. According to market research firm MarketsAndMarkets, the global industrial wearables market is expected to grow from $3.79 billion in 2019 to $8.4 billion by 2027. Beyond their use in providing AR-enabled remote assistance, another rapidly expanding application for wearables is the data they can provide about the postures and movement patterns of workers to improve ergonomics and reduce the likelihood of employee injuries.
According to ergonomics consultants at financial services provider The Hartford, employers pay an aggregate of nearly $1 billion per week in workers' compensation costs. Moreover, nine of the top 10 most common preventable injuries are linked to musculoskeletal disorders that can be corrected via improved ergonomic practices.
As a result, devices such as smart belts that can be worn around a worker's waist to collect data pertaining to motion, posture, location, and other environmental cues are paving the way for a new approach to risk management.
Based on our coverage of industrial wearables, Automation World sees five key benefits users should be aware of to implement them most e ectively.
Wearable devices streamline on-site moni-
toring. Without the use of a wearable device capable of capturing on-site data in real time, an ergonomic risk assessment would require specialists to spend long periods of time visiting a location, taking measurements, and performing manual calculations. Connected wearables can transmit relevant data gathered in the course of actual work processes and deliver them to a dashboard or other system for analysis. As a result, not only is the data gathered more accurate, but costs and labor hours can be saved.
Wearable devices enable proactive risk
management. According to The Hartford's ergonomic consultants, employers should not rest easy because they have no pre-existing worker compensation claims. If a problem does arise, the company could face multiple claims all at once. To avoid this, management should seek to continuously monitor conditions and implement new processes whenever a potential issue arises. Smart wearables make this possible.
Wearable devices can keep workers health-
ier and improve retention rates. With labor shortages abounding in industry, retaining as many current employees as possible is a priority. While the skills gap may be responsible for the overall labor shortage, employee injuries account for a large share of retention issues. In addition, as the current workforce ages, decreases in flexibility, mobility, and strength may make injuries more likely. Therefore, technologies such as smart wearables that can prevent injuries before they occur can improve an employer's bottom line.
Wearable devices are not a substitute for other personal protective equipment (PPE).
Even though wearables allow companies to monitor employee movements and spot the occurrence of high-risk postures as they occur, that does not mean that other hazard prevention measures can be eliminated. While wearable technologies can help identify where ergonomic improvements need to be made, they cannot replace face shields, cutresistant gloves, and other commonly used PPE. Moreover, traditional workplace safety education and training should continue.
Data gathered by wearable devices re-
quires analysis to produce insights. While wearable devices are a rich source of data, they don’t always direct end users on how to take corrective actions. While employers can use the data from wearables to measure various metrics, they also need to contextualize that information and determine how it is affecting their organization's bottom line. Because of this, it's important to implement a comprehensive industrial ergonomics program once smart wearables have been deployed.
4 Ways to Improve et ork T�reat etection
By David Smit
OT Infrastructure and Security at Interstates
Staying on top of new technology and cybersecurity at aging plants is complicated. Many plants have equipment that is decades old and may be relying on unsupported operating systems or software. These legacy systems often cannot be patched or upgraded, and migrating to a new operating system is not always a cost-effective approach. To help overcome these challenges, following are four ways to bolster your operations technology (OT) network by increasing threat visibility.
1. Baseline Your Network
To help determine which communication activities are normal and which may be threats, it’s essential to have an accurate baseline reading of your entire network. A comprehensive device inventory is necessary to observe when new or unapproved devices connect to your network. It’s also vital to understand which devices communicate to each other and what OT protocols they are using.
2. Centrally Collect System Logs
System logs can help correlate events across di erent devices and di erent manufacturers. This will provide horizontal visibility across your company. If you’re able, automate the review of these logs with machine learning technology.
3. Implement Incident Response Playbook
With the additional data you’ll collect from various threat detection tools, it’s important to develop an incident response playbook for your company. Collecting logs, baselining your networking, and implementing tools will provide little to no value unless you have a plan in place to monitor and act upon this data. Consider implementing tabletop exercises to role-play the various scenarios.
4. Develop a Central Pane of Glass
It’s crucial to develop a dashboard with specific key points of interest across all your company’s verticals. This will help your operation center teams e ciently parse the data. With the continuing convergence of IT and OT, it is important to have central visibility. This visibility will help close the gap and provide insight into the wide variety of devices that can be seen today.
In manufacturing, security has typically taken a secondary role to production. However, the industry is beginning to see a rapid increase in OT threats. By implementing some of these best practices, you can gain additional visibility into the threats facing your OT network.
Where Can I Learn More?
Interstates has plant cybersecurity experts ready to help. If you have any questions about network threat detection, reach us at (712) 722-1662 or www.interstates.com/contact/.
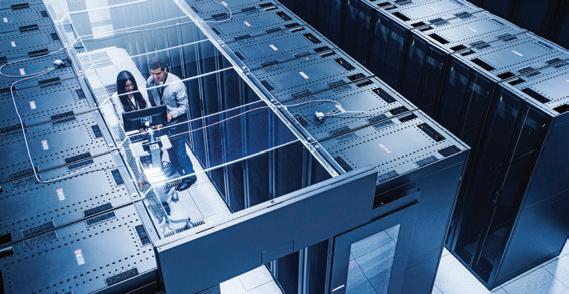
Managing the Risk of Remote SCADA Access
By David Greenfield
Director of Content/Editor-in-Chief
Image source: www.tiga.us
One of the biggest benefits of Ethernet on the plant floor is the ability to remotely connect to plant floor systems. But along with the benefits of remote access comes the heightened risk of cyber-attacks.
Despite this, more and more manufacturers believe the risks are worth managing to drive their operations into the future and ease the process of accessing and sharing data across sites for better decision-making, as well as reducing the cost of onsite troubleshooting and repair—a great deal of which can now be accomplished remotely.
Considering that a key initial Industry 4.0 achievement is remote access to SCADA (supervisory control and acquisition) systems, we spoke with Ben Manlongat of Outbound Technologies, an industrial automation system integrator to learn more about how manufacturers can best manage the risks associated with remote SCADA access.
Protecting against the biggest risks
Beyond the obvious concerns about a hacker taking control of any aspect of your production operations, Manlongat say it’s also important to consider the impact of an outsider gaining access to your SCADA data.
“If someone were to intercept your data, how could that a ect your business?” asks Manlongat. “You have to think about how you could be harmed if your competitor were to get that information. And don't think that because everything [on your SCADA system] is read-only that everything is safe. If a COM (communications) port is open, a hacker could gain access to any laptop on the network to get to the COM port of the device and then start making programming changes. And once those programming changes are made, the hacker can take control of your system. It’s critical to ensure the COM ports on your devices are protected and make sure there are no available device tags that are predefined by the manufacturer for use in controlling the device.”
Core external aspects to consider about SCADA remote access security include: • Do you have a VPN (virtual private network) connection to the plant floor or to your o ce network? If so, Manlongat advises using multifactor authentication (MFA) so that gaining your password isn’t enough to access the system; a hacker would also need your smartphone and its password. MFA sends a special key code to the approved user’s mobile device that can change every few minutes. • Is the connection to your plant floor network encrypted? • Is there any third-party software involved? In this case, Manlongat notes that there have been big breaches of thirdparty software, where the manufacturing site itself wasn’t directly hacked, but the third-party software had been compro-
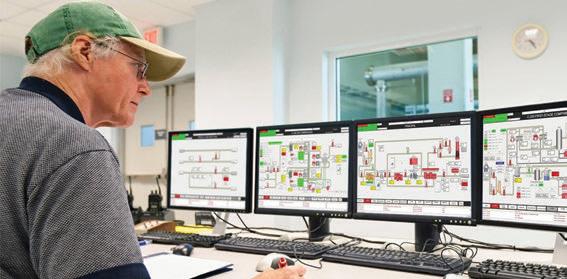
mised. In some of these cases, passwords were leaked, enabling hackers to gain access to the company’s network through that third-party software.
Internal risks include: • Having your plant fl oor network connected directly to the o ce network (e.g., without the use of a DMZ). • Security of Wi-Fi used in the plant and in the o ce (see point above). • Are your devices only transmitting readonly tags? If read-write tags are available, hackers could more easily execute control over portions of your operations. • Are device programming ports available on the network? • Is safety logic programmed in your controllers to prevent against any significant problems?
Is real protection possible?
Given the ever-growing level of risk to industrial control systems, we asked Manlongat if it was even possible to truly protect a SCADA system that has been networked for remote access.
“The quick answer is yes, because there are di erent ways to confi gure an internet-connected plant fl oor network for remote access and read-only viewing,” he says.
According to Manlongat, if you’re looking to do read-only remote access with no potential for remote control: 1) Don’t connect directly to controllers performing operations; 2) use a VPN to connect the plant fl oor to the internet to establish a private, encrypted connection—with tra c on the VPN encrypted. With this setup, even if someone were able to access the network’s tra c, they wouldn't be able to read or understand it; and 3) use MFA so that, in addition to user name and password requirements, you also need access to the authorized person's smartphone or other mobile device.
If you're looking to do read-only remote access and send data to the cloud for artifi cial intelligence/machine learning analytics, Manlongat o ers two recommendations: • Use a device (e.g., an edge computer or server) on the plant fl oor that only receives data from your plant fl oor equip-
ment. This is the device that you would connect to remotely. “This device would not have the ability to do any control operations because it's not connected to anything to do any control,” he says. “It's only reading information from plant fl oor; you’ll connect that to the VPN to send data to the cloud.” • Use a serial connection with the edge computer or server. A serial connection between a data collecting device and a controller is “a lot less risky than an Ethernet connection that could provide access to a controller’s COM port,” says Manlongat.
Listen to the full podcast on remote SCADA access.
Wireless Limit Switches cut out more than just wires...
They eliminate batteries. They eliminate regular maintenance. And, most importantly, they reduce cost; at the time of installation and throughout the life of the switch.
The best part? They do all this while maintaining the reliability of cable-
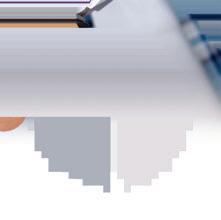
XCMW Wireless & Battery-less Limit Switch:
The energy from the actuator movement converts into the power necessary to send a wireless signal. connected switches. See the FREE
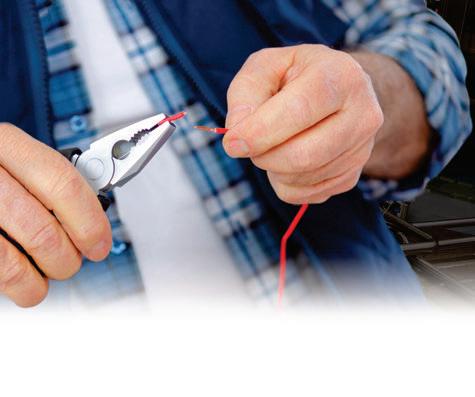
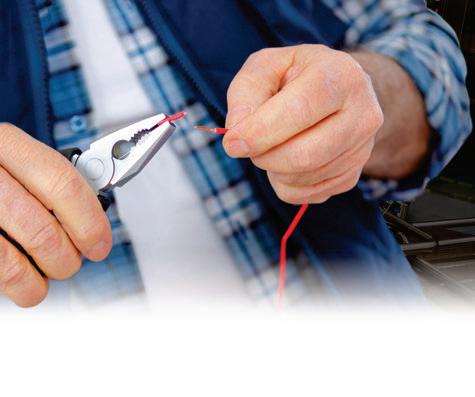
white paper at the link below and cut the Limit Switch wires for good!