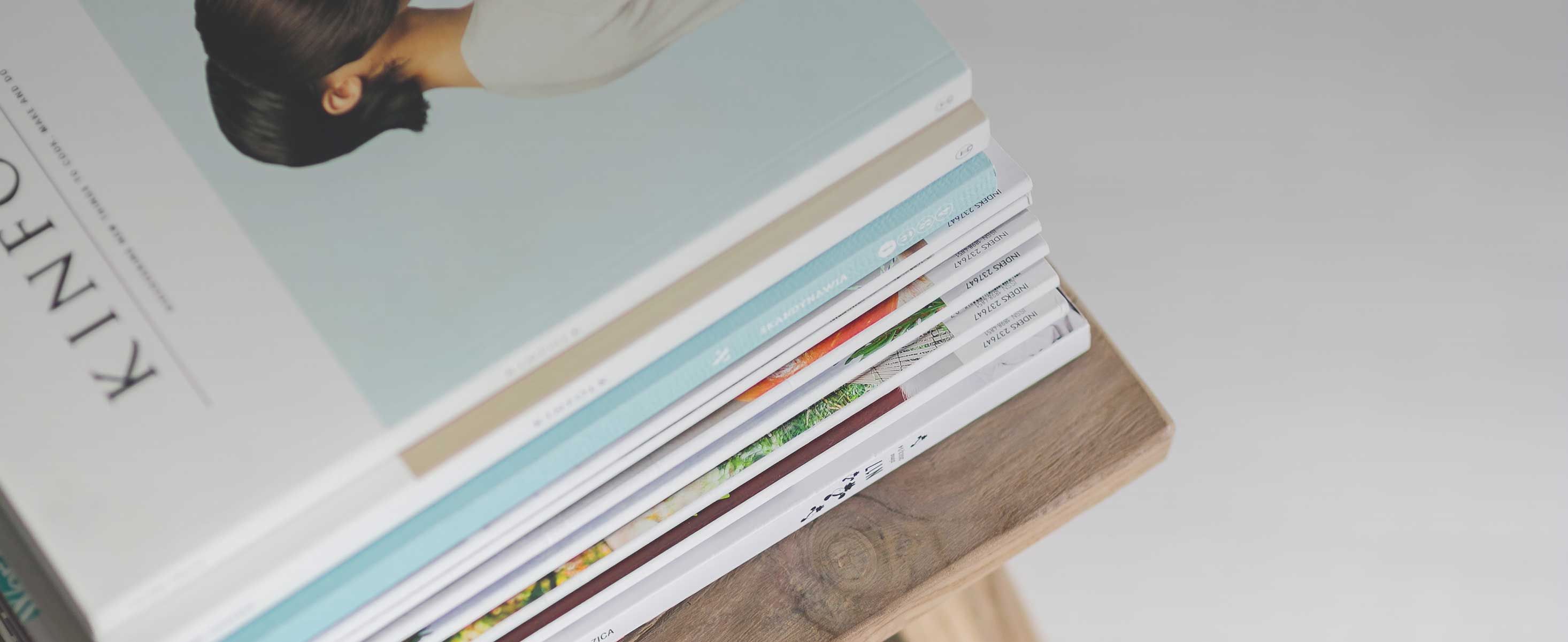
3 minute read
PERSPECTIVES
PRODUCTION POINTS
Overcoming the Cultural Barriers to Digital Transformation
By David Miller
dmiller@pmmimediagroup.com
Senior Technical Writer
It’s often been observed that the biggest barriers holding back digital transformation are related to organizational culture, rather than technology itself. In a recent “State of Industry 4.0” survey from industrial electronics and connectivity technology supplier Molex, 44% of respondents indicated that organizational and cultural issues were the most severe impediments to their digital transformation goals, compared to just 33% who indicated business model issues and 22% who indicated technology issues.
This theme was echoed at Inductive Automation’s 2021 virtual Ignition Community Conference, where experts from Chevron, Stolle Machinery, Chobani, and Amazon Web Services weighed in on the difficulties encountered throughout the digital transformation process at their own companies.
According to Todd Anslinger, Industrial Internet of Things (IIoT) and automation specialist at Chevron, reaching any group of stakeholders and convincing them to change their work processes can be challenging. Some groups can be more difficult to sway than others, he said; in particular, information technology (IT) departments may be more conducive to implementing Industry 4.0 changes merely because digital and software-oriented workflows are more familiar to them. This can be true among younger operational technology (OT) professionals as well. By contrast, older OT engineers tend to be more reticent to change. Moreover, because older workers often serve as gatekeepers to the critical systems that need upgrading, achieving their buy-in is vital to a successful Industry 4.0 deployment.
“They’re doing it the same way they’ve been doing it for years, and in their mind there’s nothing wrong with it, so why change?” Anslinger says.
To shift these attitudes, Anslinger recommends leading them through specific, illustrative examples of how it will impact their day-to-day work processes. More importantly, he advises that, rather than telling them directly how they can do it better with newer technology, asking them questions and letting them come to the answers on their own may be more effective.
“I call it management 101,” Anslinger says. “It’s really about asking the questions that lead them to the answer you want them to have of their own accord. That way it becomes their own answer, and they’re more likely to act on it.”
Corporate executives may also be hesitant, says Pugal Janakiraman, IIoT and automation specialist at Amazon Web Services. In these cases, Janakiraman advises stressing use-cases that will yield the fastest results. Even more importantly, those advocating for IIoT projects should let business outcomes drive technology choices, rather than the other way around.
“Do not look for a machine learning project, but look for a business outcome where something needs to be improved, and then bring in machine learning to drive that business outcome if it works,” Janakiraman says. “Work backward from a business problem and pick a technology to solve that problem.”
Ultimately, those heading up digital transformation projects should be wary of declaring success early. According to Anslinger, Chevron assumed that once all of its data had been moved to the cloud, decision-makers throughout the organization would build their own dashboards to monitor and act on the data points. However, when this didn’t occur, it became apparent that merely putting new technologies in place was not enough.
In response, Chevron has begun implementing low-code and no-code methodologies that allow standardized data objects to be defined and recognized automatically, so that they can be integrated into dashboards more easily. The result has been more scalability and greater alignment throughout the organization.