
22 minute read
KEY INSIGHTS
Turbine Retrofit Reduces Hot Startup Time, Increases Revenues Revenues
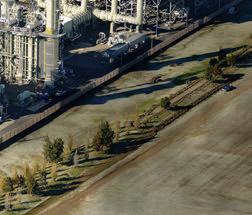
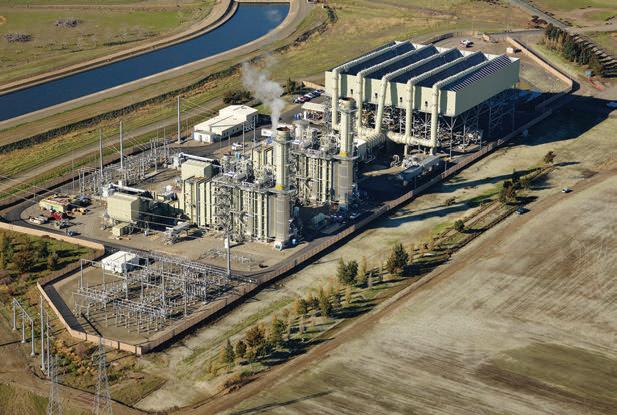

Replacing legacy steam turbine controls with Emerson’s Ovation distributed control system technology enabled a Middle River Power plant to better adapt to fl uctuations in renewable energy generation.

By Jeanne Schweder, Contributing Writer
Middle River Power’s Tracy, Calif., plant.
Any competition runner will tell you that being the fastest off the block is a big boost if you want to be the first to break the tape at the finish line. The Middle River Power plant in Tracy, Calif., took the same approach to producing megawatts of additional power more quickly. The plant’s combustion turbine purge credit retrofit project, managed by Emerson, reduced the plant’s hot startup time by 30%. As a result, it’s expected to generate an additional $170,000 in annual revenue.
A combined-cycle power plant, like Middle River Power’s Tracy plant, combines two thermodynamic cycles to improve the overall efficiency of gas-fired generation. The first cycle (Brayton) is completed in the gas turbine engine. The resulting thermal mass in the exhaust, which might otherwise be vented into the atmosphere, is captured in a heat exchanger called a heat recovery steam generator (HRSG) where steam is produced and sent to a steam turbine (Rankine Cycle) to produce many more megawatts per unit of fuel burned with a significantly reduced heat rate. The Tracy plant, located 80 miles southeast of San Francisco, is owned by Middle River Power LLC and operated by NAES Corporation. The retrofit project was initiated in response to fluctuations in renewable energy generation, which was causing the 323MW, 2x1 combined cycle plant to start frequently— typically 250 to 300 times per year. Wind and solar assets are typically placed into the power grid whenever they are available, but since they are intermittent, power plants are cycled in to balance the grid.
“Many combined cycle plants were designed for baseload or traditional generation. Cyclic operation increases the thermal stresses on plant equipment, which can lead to premature failures and forced outages,” explains Emerson’s Brett Benson. “Market changes necessitate the need to bring units online faster to balance the variability of renewable, intermittent energy sources. The ability to rapidly bring a unit online can mean the difference between being dispatched or left idle by the system operator.”
Making the change
Unless it is addressed, cycling can both reduce unit availability and increase costs. According to the U.S. National Renewable Energy Laboratory, “A major root cause of
increased operations and maintenance costs for many fossil units is cycling.”
Prior to the retrofit project, the gasfired Tracy plant was required to perform a 20-minute, fresh air pre-start purge cycle to remove potentially explosive residual fuels from the combustion system. The purge cycle extended overall startup times, putting the plant at greater risk of a delayed or failed start and missing its power purchase agreement (PPA) dispatch obligations, which could potentially trigger substantial financial penalties.
To reduce that risk, NAES took advantage of a change to the National Fire Protection Association’s “NFPA 85: Boiler and Combustion Systems Hazard Code,” which gave them the option to eliminate the prestart purge by modifying fuel and monitoring systems. Emerson’s turnkey project scope included mechanical, electrical, and control system design, as well as installation and commissioning.
While replacing steam turbine controls and the excitation system at the Tracy plant with its Ovation distributed control system technology, Emerson also made National Fire Protection Association-compliant mechanical modifications to the fuel train in addition to related changes to the combustion turbine and duct burner control logic.
“[The] Tracy [plant] has seen immediate results following the implementation of the purge credit project, most notably significantly reduced startup time. Emerson’s technology and engineering resources got this project across the line for us, and we are extremely pleased with the results,” says Nick van Haeften, maintenance manager, NAES Corporation.
Additional benefits
Reducing the plant’s startup time may also help the Tracy plant avoid the expense of PPA failed-start penalties, which can exceed $300,000 per incident. Within the first two weeks after the project was completed, one failed start was avoided due to the ability to re-start after a trip and still meet the dispatch.
Other expected economic and operational benefits include eliminating the 20-minute purge of ambient temperature air through the turbine and reducing the thermal stress on the heat recovery steam generation. This is expected to extend the life of the unit by deferring maintenance costs for three to six years, which is beyond the timeframe of the utility’s current PPA. All told, this project is expected to result in a return on investment in only two to three years.
“Today’s power market is more competitive than ever,” says Bob Yeager, president of Emerson’s power and water business. “NAES is a forward-thinking organization that recognized how the purge credit can boost reliability and revenue, thereby putting the Tracy plant in an excellent position to capitalize on future market opportunities.”
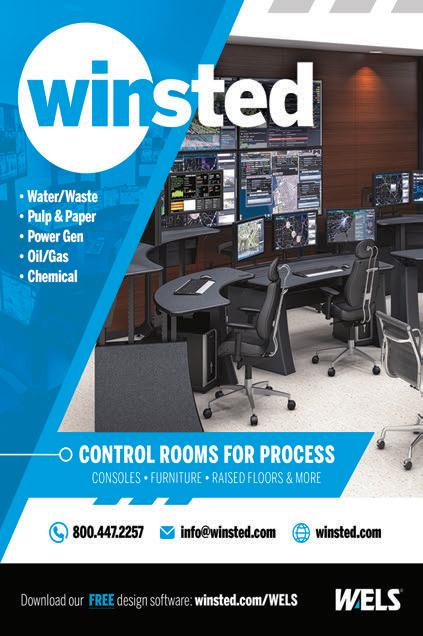
Spitz Digitalizes Its Production with Manufacturing Execution System
To future-proof its operations, which produce more than 1 million products a day, Spitz turned to Siemens Simatic IT Production Suite to increase process stability and product quality while connecting its business and process control systems.
By Jeanne Schweder, Contributing Writer
If you’re charged with making small batches of many different products, ensuring consistency from batch to batch is a daunting task, one requiring precise control of every aspect of the manufacturing process
At the Spitz factory in Attnang-Puchheim, Austria, they’ve turned to digitalization to provide the flexibility, efficiency, and quality required to make a broad spectrum of products.
Every day, roughly 1.2 million products leave the Spitz factory. The company operates 30 process lines and 35 filling and packaging plants. Its automated manufacturing processes make everything from liqueurs, iced tea, and mineral water to wafers, sliced bread, sauces, jams, and honey.
“Automation and digitalization are extremely important for Spitz,” says Walter Scherb, Jr., CEO of the Spitz Group. “The goal is to manufacture new products even more quickly in the future. To achieve that, we’re relying on developing our own recipes as a decisive competitive advantage.”
To make production as efficient and economical as possible, Spitz uses Siemens digitalization technology to convert information from every process used in the factory to a digital format. “Our existing system for production control was no longer able to handle the demands of digitalization,” says Scherb. “We wanted to implement a new, future-ready system that could be expanded over the long term. It was important for us that we be able to control all production processes via one system and process them in real time.”
The end-to-end, integrated system—Siemens Simatic IT Production Suite manufacturing execution system (MES)—not only increases process stability and product quality, according to Scherb, it also minimizes potential sources of error. This software controls production and manufacturing systems, matches the production processes to the delivery chain, and closes the gap between business systems and process control systems. Materials management and operating data acquisition are both integrated in the software.
A production line can be switched to another product practically at the push of a button, and each product changeover is optimized to minimize losses and delays. Although setup time for certain machines must be reckoned with, the actual process control is performed automatically, as is the retrieval of the specified amounts of raw materials required for the particular product and of the materials necessary for the subsequent packaging.
Specific benefits
Order data is linked directly to the ongoing process. At the same time, production and consumption data are supplied to the higherlevel system. Thanks to digitalization, the procedure is the same at all the plants, meaning that the data from all production processes is complete, consistent, and comparable.
All silo filling levels are also recorded in the new system on a batch-specific basis, along with the type and quality of raw materials. After a specific raw material has been removed from a silo or pallet, its amount and the path it follows in the individual production lines are precisely documented.
In addition, Scherb says it will soon be possible to adapt the individual recipes to the properties of the raw materials used, such as
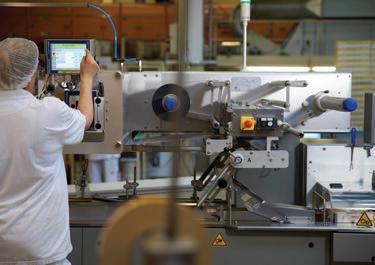
sugar content. The recipe can then be automatically recalculated and modified so that the end product always has the same flavor, texture, and appearance.
A welcome side effect is that there’s no possibility of using the wrong raw material because the system verifies whether the material being supplied should be part of the order. If an error occurs, the system immediately sounds an alarm.
Energy and maintenance applications
To optimize the process in terms of both operation and energy, Spitz also uses the Siemens energy management system. This system shows how much energy is being used as well as where, and whether, unused energy is being lost.
In the future, condition monitoring could also play an important role at Spitz. In this case, sensors will be used to monitor each individual motor for temperature, acoustics, and vibration. Determining the motor condition in this way makes scheduling maintenance cycles easier and ensures high machine availability.
“When it comes to digitalization,” explains Scherb, “I don’t think it’s a matter of ‘whether’ but of ‘when.’ We’ve simply taken early action. We see many opportunities for digitalization, both to improve product quality and consistency and to increase sustainability. It’s making us more flexible. It supports product safety and quality as well as uniformity in production.”
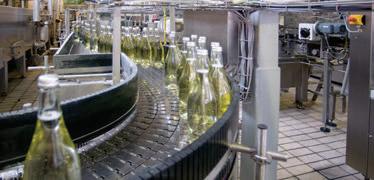
Bottling line at Spitz factory in upper Austria. Source: Siemens
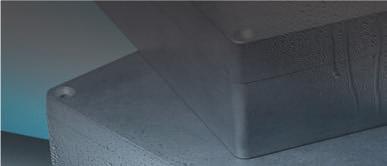
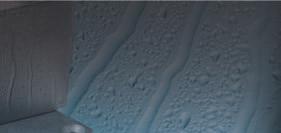
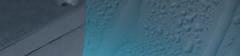
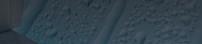
Compact Industrial PC
Beckhoff, beckhoff.com
With the C7015 ultra-compact Industrial PC, Beckhoff combines its expertise with PC-based machine control and IP65/67rated components. The result is an industrial PC (IPC) designed with IP65/67 protection for direct installation on machines or other equipment. The Microsoft Azure certified and Amazon Web Store qualified edge device is suitable for decentralized installation and provides multi-core computing performance. As a control computer, the device also reduces control cabinet space requirements, optimizes machine design, and simplifies subsequent system expansions. The C7015 measures 85x167x43 mm.
Soft Starter for Motors
Danfoss, danfoss.us
The VLT Soft Starter MCD 600 offers a variety of Ethernet and serial-based communication option cards, application-dedicated smart cards, and support for eight languages. It provides the latest in soft start motor control and protection for superior performance in fixed-speed applications wherever drives are used. The product provides all the features and functions of a standard MCD 600 Soft Starter in a compact NEMA12 or NEMA3R enclosure, with circuit breaker, keypad, and operators on the door. Other standard features include: Mains voltage range 3 x 480V AC; inbuilt impeller cleaning assistance with pump clean functionality; advanced start, stop, and protection features; DC injection braking; and multiple programming setup menus.
ROUTING ALL KINDS OF CABLES AND CONNECTORS THROUGH 1 KNOCK-OUT
WITH IMAS-CONNECT™
www.icotek.com
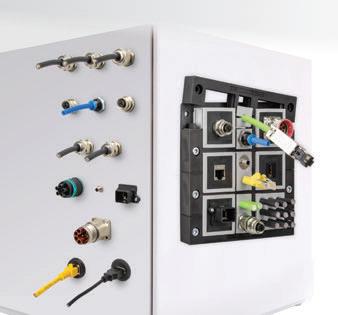

Motor Protection Circuit Breakers
Rockwell Automation, rockwellautomation.com
The Allen-Bradley Bulletin 140MT motor protection circuit breakers from Rockwell Automation offer enhanced Type F combination motor controller ratings when used with Bulletin 100-C and 100-E contactors, enabling assembled starters to be applied without additional branch circuit protection. Tap conductor protection ratings mean these devices can be wired with smaller conductors in group motor installations to save costs. The products are available as motor circuit protectors for three-component starters and motor protection circuit breakers for two-component starters. Special 140MT product variants also address specific applications, like providing protection at output of variable frequency drive (VFD) in multi-motor applications or protection of high-inrush, high-efficiency motors.
A Tale of T�ree Clients and T�eir Journeys to MES
By Tim Gellner
Systems Integration Consultant, Rockwell Automation
T�ey assumed that all of the machines could be connected and integrated into the MES as they were, and therefore made no attempt to validate the assumption leading up to the MES engagement. T�is approach proved to be problematic in that it became necessary to perform a detailed survey of the machines to determine if a data interface could be accomplished in the older machines.
This is a short story about three clients, each in the early stages of an MES (manufacturing execution system) implementation. These clients are in different businesses, but their production processes and shop floor equipment are very similar. They each employ CNC machines and other related equipment to produce their respective products, and each client has plans to connect that equipment to the MES to provide an automated means of gathering critical production data that is, at present, either being recorded manually or not at all.
While each of the three clients face differing challenges in getting their production equipment connected, they each have chosen a different approach to achieve it.
Client #1
This client has tens of machines from which they want to gather data. The machines range in age from 10 to 30+ years old, over half of which fall into the latter category. They have data interfaces to the newer machines and collect a limited amount of data from them. Their approach to the integration and the MES implementation was to eat the elephant in one bite. They assumed that all of the machines could be connected and integrated into the MES as they were, and therefore made no concerted attempt to validate the assumption leading up to the MES engagement. This approach proved to be problematic in that it became necessary to perform a detailed survey of the machines to determine if a data interface could be accomplished in the older machines. The client will have the ability to access machine production data via OPC on the newer machines. For the older machines they are limited to hardwired I/O connections to the controllers which provide running, stopped, and trouble indications to a small PLC which the MES can access. This additional exercise delayed the MES definition phase of the project and added cost.
Client #2
The second client has fewer machines that generally fall into the 20 years old and newer category. This client is also adding new machines to their facility. They currently do not have an automated means of gathering data from the machines they have; they rely on manual collection of production data. They knew up front that they needed production data from their machines to support the MES project. They also knew that it made sense to break up the MES implementation into three phases—essentially a crawl, walk, run approach. The decision was made that as part of the first phase, we would conduct a proof of concept of machine connectivity on a small cross section of their machines. Once the interfaces were proven, the remainder of the machines could be brought online in the second phase of the project.
Client #3
The third client is primarily installing new equipment. They knew that they would need to get data from the machines for the MES implementation and, based on that knowledge, they engaged early with both the OEMs and the MES team to determine how best to get the interfaces defined. This early engagement resulted in machines being delivered to the facility with an essentially plug-and-play data interface preconfigured by the OEMs.
The takeaway from these stories is that, regardless of the approach taken to machine connectivity, it can always be done to one degree or another. The client’s conditions, expectations, and assumptions play a large part in easing the pain and cost of implementation of a MES/IIoT application.
1. Publication Title AutomationWorld
Statement of Ownership,Management,andCirculation (Requester Publications Only)
2. Publication Number
3. Filing Date 1 5 5 3 1 2 2 4 Oct1, 2021
4. Issue Frequency
5. Number of Issues Published Annually 6. Annual Subscription Price Monthly 12 (if any) N/A 7. Complete Mailing Address of Known Office of Publication (Not printer)(Street, city, county, state, and ZIP+4®) Contact Person PMMI MediaGroup,401NorthMichiganAve.,Suite300,Chicago,IL60601 GeorgeShurtleff Telephone (Include area code) 312-205-7890
8. Complete Mailing Address of Headquarters or General Business Office of Publisher (Not printer)
PMMIMediaGroup,401NorthMichiganAve.,Suite300,Chicago,IL60601
9. Full Names and Complete Mailing Addresses of Publisher, Editor, and Managing Editor (D o not leave blank) Publisher (Name and complete mailing address)
KurtBelisle,PMMIMediaGroup,401NorthMichiganAve.,Suite300,Chicago,IL60601
Editor (Name and complete mailing address)
DavidGreenfield,PMMIMediaGroup,401NorthMichiganAve.,Suite300,Chicago,IL60601
Managing Editor (Name and complete mailing address)
10.Owner (D o not leave blank. If the publication is owned by a corporation, give the name and address of the corporation immediately followed by the names and addresses of all stockholdersowningor holding 1 percent or more of the total amount of stock. If not owned by a corporation, give the names and addresses of the individual owners. If owned by a partnership or other unincorporated firm, give its name and address as well as those of each individual owner. If the publication is published by a nonprofit organization, give its name and address.)
Full Name Complete Mailing Address
PMMI
11911WorldgateDrive,#200,HerndonVA20170
11.Known Bondholders, Mortgagees, and Other Security Holders Owning or Holding 1 Percent or More of Total Amount of Bonds, Mortgages, or
Other Securities. If none, check box. None
Full Name Complete Mailing Address
12. Tax Status (For completion by nonprofit organizations authorized to mail at nonprofit rates)(Check one)
The purpose, function, and nonprofit status of this organization and the exempt status for federal income tax purposes: Has Not Changed During Preceding 12 Months Has Changed During Preceding 12 Months (Publisher must submit explanation of change with this statement.)
PS Form 3526-R, July 2014 [Page 1 of 4 (See instructions page 4)] PSN: 7530-09-000-8855 PRIVACY NOTICE: See our privacy policy on www.usps.com.
13.Publication Title
AutomationWorld
15.
Extent and Nature of Circulation
a.Total Number of Copies (Net press run)
b. Legitimate
Paid and/or
Requested
Distribution (By mail and outside the mail) (1)
(2) Outside County Paid/Requested Mail Subscriptions stated on PS Form 3541. (Include direct written request from recipient, telemarketing, and Internet requests from recipient, paid subscriptions including nominal rate subscriptions, employer requests, advertiser’s proof copies, and exchange copies.)
In-County Paid/Requested Mail Subscriptions stated on PS Form 3541. (Include direct written request from recipient, telemarketing, and Internet requests from recipient, paid subscriptions including nominal rate subscriptions, employer requests, advertiser’s proof copies, and exchange copies.)
(3) Sales Through Dealers and Carriers, Street Vendors, Counter Sales, and Other Paid or Requested Distribution Outside USPS®
(4) Requested Copies Distributed by Other Mail Classes Through the USPS (e.g., First-Class Mail®)
c.Total Paid and/or Requested Circulation (Sum of 15b (1), (2), (3), and (4))
(1) Outside County Nonrequested Copies Stated on PS Form 3541 (include sample copies, requests over 3 years old, requests induced by a premium, bulk sales and requests including association requests, names obtained from business directories, lists, and other sources)
d.Non requested
Distribution (By mail and outside the mail) (2)
(3)
(4) In-County Nonrequested Copies Stated on PS Form 3541 (include sample copies, requests over 3 years old, requests induced by a premium, bulk sales and requests including association requests, names obtained from business directories, lists, and other sources)
Nonrequested Copies Distributed Through the USPS by Other Classes of Mail (e.g., First-Class Mail, nonrequestor copies mailed in excess of 10% limit mailed at Standard Mail® or Package Services rates)
Nonrequested Copies Distributed Outside the Mail (Include pickup stands, trade shows, showrooms, and other sources) 14.Issue Date for Circulation Data Below September2021
Average No. Copies Each Issue During Preceding 12 Months No. Copies of Single Issue Published Nearest to Filing Date
49,843 52,840
35,860 35,601
0 0
20 20
0 0
35,881 35,621
13,416 13,780
0 0
0
350 0
1,400
e.
g.
h. Total Nonrequested Distribution [Sum of 15d (1), (2), (3) and (4)]
Total Distribution (Sum of 15c and e)
Copies not Distributed (See Instructions to Publishers #4, (page #3))
Total (Sum of 15f and g)
Percent Paid and/or Requested Circulation (15c divided by 15f times 100) 13,766 15,180 49,647 50,801 150 639 49,797 51,440 72% 70%
*If you are claiming electronic copies, go to line 16 on page 3. If you are not claiming electronic copies, skip to line 17 on page 3.
PS Form 3526-R, July 2014 (Page 2 of 4)
Statement of Ownership,Management,andCirculation (Requester Publications Only)
16.Electronic Copy Circulation AutomationWorldMagazine
Average No. Copies Each Issue During Previous 12 Months No. Copies of Single Issue Published Nearest to Filing Date
a.Requested and Paid Electronic Copies
b.Total Requested and Paid Print Copies (Line 15c) + Requested/Paid Electronic Copies (Line 16a) c.Total Requested Copy Distribution (Line 15f) + Requested/Paid Electronic Copies (Line 16a) d.Percent Paid and/or Requested Circulation (Both Print & Electronic Copies) (16b divided by 16c Í 100) 4,744 4,796 40,625 40,417 54,391 55,597 75% 73%
I certify that 50% of all my distributed copies (electronic and print) are legitimate requests or paid copies.
17.Publication of Statement of Ownership for a Requester Publication is required and will be printed in the issue of this publication.
18.Signature and Title of Editor, Publisher, Business Manager, or Owner GeorgeShurtleff PMMIMediaGroup ProductionManager 630-329-1967 November2021
Date
10/1/2021
I certify that all information furnished on this form is true and complete. I understand that anyone who furnishes false or misleading information on this form or who omits material or information requested on the form may be subject to criminal sanctions (including fines and imprisonment)and/or civil sanctions (including civil penalties). Automation Direct 800.633.0405 www.ProductivityPLCs.com 2
Automation24 Inc. 800.250.6772 www.automation24.com 36-A
Beckhoff Automation 952.890.0000 www.beckhoff.com 17, 31
CIMON 800.300.9916 www.Cimon.com 12-A, 1 (select issues)
Digi-Key Electronics 800.344.4539 www.digikey.com/automation 7
Endress + Hauser USA 888.363.7377 www.us.endress.com/calibration-usa 19
Galco Industrial Electronics 888.526.0909 www.Galco.com 8-9
Hammond Manufacturing 716.630.7030 www.hammondmfg.com
icotek North America 312.643.2315 www.icotek.com
Inductive Automation 800.266.0909 demo.ia.io/automation 5
MAVERICK Technologies, a Rockwell Company 888.917.9109 www.mavtechglobal.com
PACK EXPO East 2022 www.packexpoeast.com
ROKLive, A Rockwell Automation Event www.rok.auto/roklive
Telemecanique Sensors 800.435.2121 www.tesensors.com/XCMW 21
Winsted World Headquarters 800.447.2257 www.winsted.com 39
NOVEMBER 2021 INDUSTRIAL ETHERNET OF THINGS
Fabco-Air 352.373.3578 www.fabco-air.com 22
Festo Corporation 866.GO.FESTO www.festo.com/VTEM
Opto 22 800.321.6786 www.opto22.com
PI North America 480.483.2456 www.us.profinet.com/go-digital 25
Tadiran Batteries 800.537.1368 www.tadiranbat.com 11
Wago Corporation 800.DIN-RAIL www.wago.us/systemfield 15
Automation World ® (ISSN # 15531244, USPS 22435) is a registered trademark of PMMI, The Association for Packaging and Processing Technologies. Automation World ® is published 14x a year by PMMI with its publishing office, PMMI Media Group, located at 401 N. Michigan Avenue, Suite 300, Chicago, IL 60611; 312.222.1010; Fax: 312.222.1310. Periodicals postage paid at Chicago, IL, and additional mailing offices. Copyright 2021 by PMMI. All rights reserved. Materials in this publication must not be reproduced in any form without written permission of the publisher. Applications for a free subscription may be made online at www.packworld.com/subscribe. Paid subscription rates per year are $105 in the U.S., $147 Canada and Mexico by surface mail; $250 Europe, South America. $325 Far East and Australia by air mail. To subscribe or manage your subscription to Automation World, visit AutomationWorld.com/subscribe. Free digital edition available to qualified individuals outside the United States. POSTMASTER; Send address changes to Automation World®, 401 N. Michigan Avenue, Suite 300, Chicago, IL 60611. PRINTED IN USA by Quad Graphics. The opinions expressed in articles are those of the authors and not necessarily those of PMMI. Comments, questions and letters to the editor are welcome and can be sent to: editors@automationworld.com. We make a portion of our mailing list available to reputable firms. If you would prefer that we don’t include your name, please write us at the Chicago, IL address. PS Form 3526-R, July 2014 (Page 3 of 4) PRIVACY NOTICE: See our privacy policy on www.usps.com. Volume 19, Number 11.
The machine learning and motion planning used in Honeywell’s Smart Flexible Depalletizer optimize the movements of the robotic arm to ensure maximum picking speed. The system’s control logic senses the weight of each item as the robot lifts it and automatically updates its gripping response to transfer each product securely. Because the system uses machine learning to operate, the more picks the robot performs, the more it learns and continues to improve in unloading pallets.
David Greenfi eld on the introduction of Honeywell’s Smart Flexible Depalletizer at PACK EXPO 2021. awgo.to/1270
What this means is that RoBex can build a custom-designed, integrated robotic system based on a manufacturer’s unique needs that RoBex ultimately owns and is responsible for. For example, a palletizing application that typically takes six people to manually operate across multiple shifts can be replaced with an automated robotic palletizing system that creates a signifi cant cost savings on the line—estimated at up to 50% savings—while allowing organizations to redistribute valuable talent to other areas of the factory where they are needed most.
Stephanie Neil on the RoBex Flexx technology licensing program. awgo.to/1271
Once a dashboard is designed and deployed, key performance indicators and other information are available at your fi ngertips. The hassle of manually extracting raw data from a system, manipulating it in Excel, and creating charts for that data is a thing of the past. The dashboard will collect and transform all the necessary data for you.
Ed Miller of Avanceon on the benefi ts of modern dashboards. awgo.to/1272
Bosch Rexroth’s ctrlX Store features applications from Bosch Rexroth as well as third-party providers. According to the company, the primary goal of the marketplace is to help manufacturers speed time-to-market while maintaining the ability to customize their o erings and di erentiate themselves from their competitors. By making an ecosystem of turnkey applications available, the challenges that come along with confi guration, programming, and design when setting up a line or engaging in product changeover can be greatly reduced.
David Miller on Bosch Rexroth’s new ctrlX Store, featured at PACK EXPO 2021. awgo.to/1269
A system failure is the wrong time to realize that you don’t have the internal capability to diagnose and repair the issue. A risk reduction strategy should involve planning a response to incidents and, if the capability isn’t the best it could be within your team, outsourcing can be the best solution.


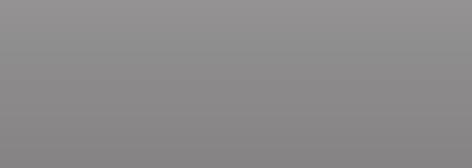
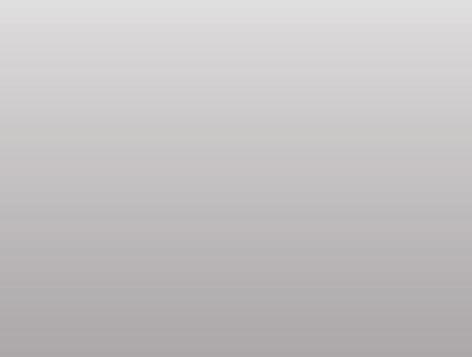
