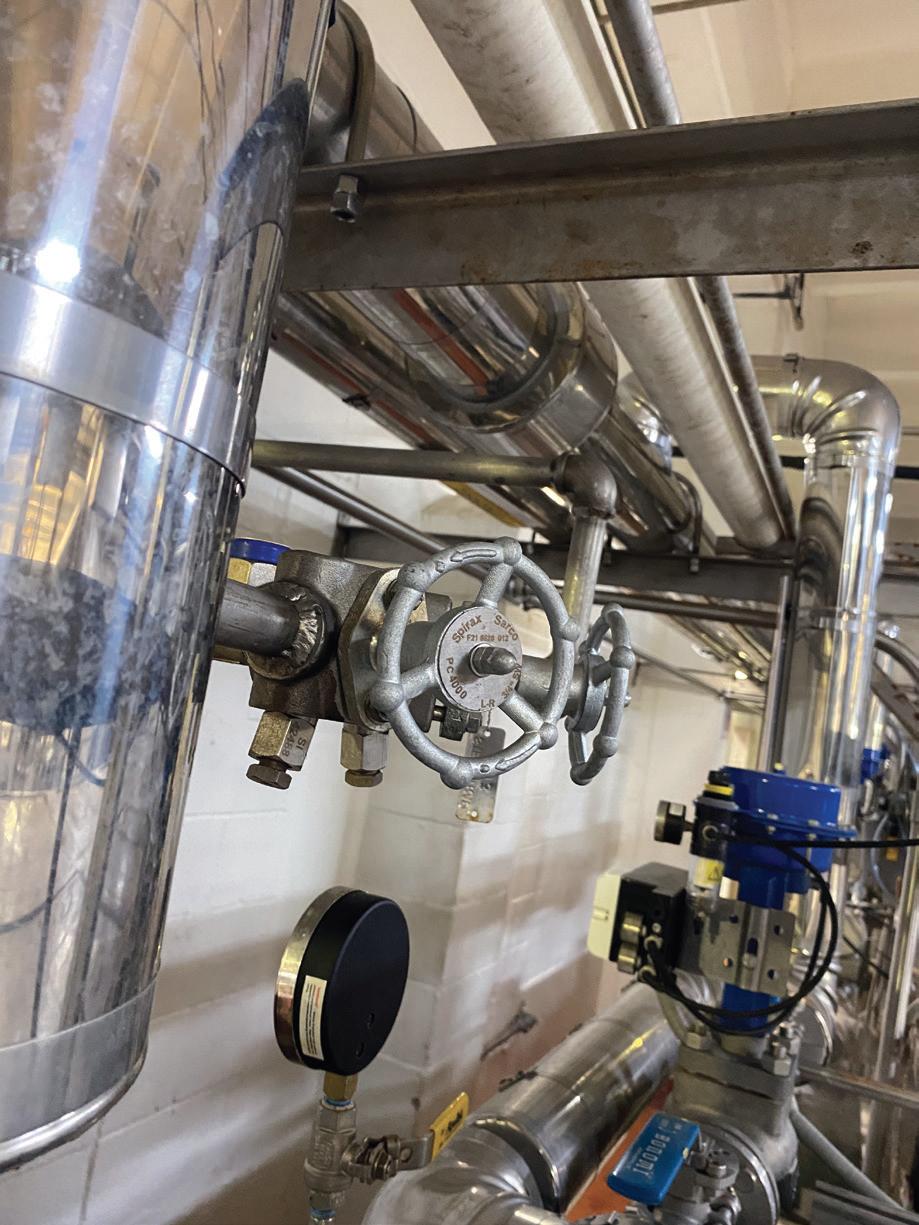
2 minute read
Meet the 2022 Winners at PACK EXPO Las Vegas
The 2022 Sustainability Excellence in Manufacturing Award winners will present more details on their green projects at a special session during PACK EXPO Las Vegas. Join us on Monday, Sept. 11 at 4 p.m. at the Processing Innovation Stage—Booth N-10511 in the North Hall of the Las Vegas Convention Center. Register now at www.packexpolasvegas.com.
ProFood World wants to hear about your current sustainability projects. The submission deadline and eligibility requirements for the 2023 Sustainability Excellence in Manufacturing Awards will be announced this fall at pfwgo.to/sema.
The first phase of the ROC project was implemented in August 2022 on the existing retorts and the final phase in December with the installation of additional retorts. The project reduces water use by about 7.28 million gallons per year. Facilitywide, this is a reduction of about 8% for water use and 10% for wastewater.
“The project is self-sustaining because there is a direct correlation between the amount of steam used in the retorts, ROC water generated, and water needed for process control,” Thole notes. “This process could be transferred to other facilities that have both reverse osmosis filtering systems and steam retorts.”
Although a larger distance between the reverse osmosis filter and steam retorts could cause issues for use in other facilities, there is also potential for ROC water to be used in other heat transfer applications.
SECOND PLACE Project Category Optimizing Steam Traps Brings Signi cant Water and Energy Savings
Steam traps are a significant source of water and energy use, and proactively addressing potential leaks can create more sustainable operations.
Conagra Brands’ facility in Imlay City, Mich.— known primarily for its Vlasic pickles brand—set out to review and optimize its steam traps to reduce steam and water loss, which has the additional benefit of carbon emissions reduction associated with that process.
After an initial analysis by a third party, the Imlay City facility identified 12 trap assemblies with improvement opportunities. With new steam traps, the independent assessment determined that nearly 139,000 gallons of usable boiler feeder water could be saved each year and carbon emissions associated with the 12 steam traps have the potential to be reduced by 78 tons per year.
“Steam has become the new green source for power and heating if controlled and utilized properly,” says Raju Markose, Conagra’s environmental manager in Imlay City. “Keeping a consistent record of the performance of steam traps can increase the system’s reliability and functionality.”
With this in mind, the Imlay City facility installed hardware that gives maintenance the ability to change a steam trap on the system without having to take the system out of production. “The new pipeline connector has a block and bleed function that allows the team to isolate the trap and bleed o the pressure, change the trap, and re-enable the system with full functionality,” Markose says. “This will shorten the time needed to replace traps in the future and also is an increase in the safety factor when servicing the steam system in general.”
